
2802.Трещиностойкость железоуглеродистых сплавов
..pdf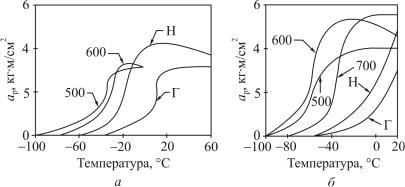
состояний, которые, естественно, имеют минимальные значения при температурах отпуска 500 °С для стали 14ГН и 600 °С для стали 17ГС. Причина в таком неоднозначном изменении трещиностойкости низкоуглеродистых сталей с повышением температуры отпуска заключается в особенностях структуры. После закалки этих сталей получается реечный (пакетный) мартенсит с высокой плотностью дислокаций (рис. 3.28, а). Такая структура придает низкоуглеродистым сталям максимальную прочность, но низкую пластичность, что не обеспечивает хорошую трещиностойкость. Низкие температуры отпуска (~ 200…300 °С) слабо меняют эту структуру (рис. 3.28, б), в результате чего и трещиностойкость существенно не улучшается. При более высоких температурах отпуска (~ 500…600 °С) полосчатый характер структуры сохраняется, оставляя таким образом прочность на довольно высоком уровне. Одновременно с этим, однако, плотность дислокаций внутри мартенситных кристаллов существенно уменьшается, что значительно повышает пластичность (рис. 3.28, в). Это соединение достаточно высокой прочности и пластичности обеспечивает максимальную трещиностойкость.
Рис. 3.25. Влияние температуры отпуска на работу развития трещины, ap :
а– сталь 14ГН; б – сталь 17ГС; Г – горячая прокатка;
Н– нормализация; 500, 600, 700 °С – закалка
сотпуском соответственно при 500, 600 и 700 °С
231
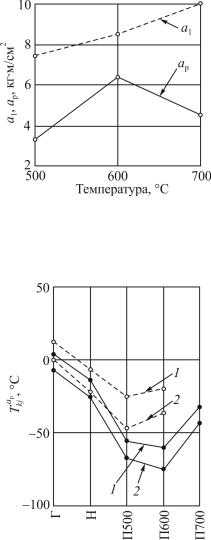
Рис. 3.26. Изменение ударной вязкости a1 и работы развития трещины ap в зависимости от температуры отпуска для стали 17ГС
Рис. 3.27. Изменение критической температуры TKajp
взависимости от структуры стали 14ГН (пунктирные линии)
и17ГС (сплошные линии): Г – горячекатаные; Н – нормализованные;
П– термоулучшенные (500, 600, 700 – температура отпуска,оС);
1 – → ap = 20 Дж/см2; 2 – → ap = 12 Дж/см2
232
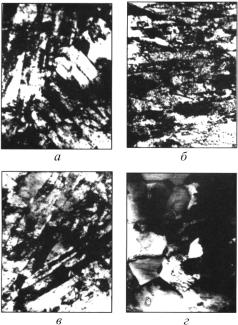
Рис. 3.28. Микроструктура низкоуглеродистой стали (С = 0,12 %) после различныхрежимовзакалкииотпуска: а– закалкаот920 оСвводе, ×18500; б– отпуск
300 оС, ×18500; в– отпуск500 оС, ×18500; г– отпуск650 оС, ×18500
При дополнительном повышении температуры отпуска до 650– 700 °С начинают активно развиваться рекристаллизационные процессы (рис. 3.28, г), при которых реечный характер структуры практически пропадает, а плотность дислокаций резко уменьшается. В результате получается сталь с низкой прочностью, высокой пластичностью и пониженной трещиностойкостью.
3.7. Влияние химического состава на динамическую трещиностойкость низкоуглеродистых нормализованных сталей
3.7.1.Предварительные соображения
Всовременных инженерных сооружениях объем низкоуглеродистых сталей, используемых для их производства, исключительно велик. Наряду со своими хорошими прочностными свойствами и сва-
233

риваемстью эти стали могут обеспечивать и высокую трещиностойкость. Эти обстоятельства являются причиной многочисленных разработок в данной области.
Таблица 3.7 Химический состав сталей 17ГС и 14ГН
Марка |
|
|
|
Содержание элементов, мас. % |
|
|
||||
стали |
C |
Si |
Mn |
Ni |
Cr |
S |
P |
O2 |
H2 |
N2 |
17ГС |
0,19 |
0,43 |
1,35 |
0,36 |
- |
0,014 |
0,01 |
0,003 |
0,0004 |
0,003 |
14ГН |
0,16 |
0,34 |
1,00 |
0,50 |
0,16 |
0,027 |
0,02 |
0,023 |
0,0007 |
0,005 |
Таблица 3.8
Механические свойства сталей 17ГС и 14ГН в зависимости от их структурного состояния
|
|
|
|
|
|
|
|
|
Термическая |
σ0,2 |
|
σâ |
δ |
|
ψ |
T ap |
T ap |
обработка |
|
|
|
|
|
|
ê1,2 |
ê2,0 |
|
МПа |
|
% |
|
|
|||
|
|
|
|
|
||||
|
|
|
Сталь 17ГС |
|
|
|
|
|
Без термообработки |
470 |
|
570 |
21 |
|
57 |
– 5 |
5 |
(горячекатаная) |
|
|
|
|
|
|
|
|
Нормализация |
360 |
|
530 |
26 |
|
62 |
– 25 |
– 15 |
Зак. + отпуск 500 °С |
590 |
|
710 |
16 |
|
65 |
– 65 |
– 55 |
Зак. + отпуск 600 °С |
510 |
|
630 |
18 |
|
65 |
– 75 |
– 60 |
Зак. + отпуск 700 °С |
450 |
|
590 |
22 |
|
68 |
– 45 |
– 35 |
|
|
|
Сталь 14ГН |
|
|
|
|
|
Без термообработки |
500 |
|
550 |
19 |
|
47 |
0 |
15 |
(горячекатаная) |
|
|
|
|
|
|
|
|
Нормализация |
350 |
|
500 |
29 |
|
53 |
– 25 |
– 10 |
Зак. + отпуск 500 °С |
650 |
|
700 |
15 |
|
58 |
– 50 |
– 30 |
Зак. + отпуск 600 °С |
440 |
|
540 |
19 |
|
62 |
– 40 |
– 25 |
В настоящем подразделе обобщены наши исследования, целью которых было проанализировать влияние основных легирующих элементов на динамическую трещиностойкость низкоуглеродистых сталей в нормализованном состоянии. Изучали влияние углерода, бора, кремния, марганца, никеля, титана, ниобия, хрома, молибдена и фосфора. В качестве базового использовали сталь следующего состава: С = 0,2 %, Si = 0,2 % и Mn = 1,3 %. При исследовании роли каждого из этих трех основных элементов его содержание варьировали при неизменной концентрации остальных двух элементов.
234
Опытные плавки выплавлены в 50-килограммовой индукционной печи с основной футеровкой. Металл каждой плавки разливали на несколько слитков. После очередного разлива металла в печь добавляли легирующие элементы, чтобы получить необходимый химический состав следующего слитка.
Нормализацию проводили при температуре на 30–50 °С выше критической точки Ас3 для данной стали. Механические свойства
определяли на поперечных образцах. Величину að определяли по
методике Отани (см. п. 2.9.3). Исследована зависимость работы развития трещины að и критическая температура Òê в зависимости от
содержания легирующих элементов. В качестве критерия для определения этой температуры использовали значения að = 12 Дж/см2
(Тка12р ) и að = 20 Дж/см2 (Òê20àð ). Определяли также номер действи-
тельного ферритного зерна, балл полосчатости структуры, количество феррита, перлита и игольчатых структур.
3.7.2.Влияние углерода
Втабл. 3.9 дан химический состав и соответствующие механические свойства, структурные характеристики и критические темпера-
туры исследованных сталей [158]. Трещиностойкость að (рис. 3.29) с увеличением содержания углерода непрерывно уменьшается.
Таблица 3.9
Химический состав, механические свойства, структурные характеристики и критические температуры опытных сталей с различным содержанием углерода
Усл. |
Химсостав, % |
Механические |
|
|
Структурные |
|
Критические |
||||||||||
обозн. |
|
|
|
|
свойства |
|
характеристики |
|
температу- |
||||||||
|
|
|
|
|
|
|
|
|
|
|
|
|
|
|
|
ры,оС |
|
|
C |
Si |
Mn |
σ0,2 |
σВ |
δ |
|
Ψ |
Nз |
|
БП |
Количество, % |
T àð |
Òàð |
|||
|
|
|
|
МПа |
|
% |
|
|
|
Ф |
П |
|
ИС |
ê12 |
ê20 |
||
1 |
2 |
3 |
4 |
5 |
6 |
7 |
|
8 |
9 |
|
10 |
11 |
12 |
|
13 |
14 |
15 |
У1 |
0,03 |
0,13 |
1,23 |
320 |
400 |
40 |
|
76 |
7–8 |
|
0 |
100 |
0 |
|
0 |
– 60 |
– 35 |
У2 |
0,13 |
0,11 |
1,26 |
380 |
490 |
34 |
|
67 |
9 |
|
0 |
90 |
10 |
|
0 |
– 35 |
– 20 |
У3 |
0,23 |
0,15 |
1,21 |
450 |
600 |
31 |
|
60 |
10 |
|
0 |
65 |
35 |
|
0 |
– 35 |
– 15 |
|
|
|
|
|
|
|
|
|
|
|
|
|
|
|
|
|
235 |

|
|
|
|
|
|
|
|
|
Окончание |
табл. |
3 . 9 |
|||
1 |
2 |
3 |
4 |
5 |
6 |
7 |
8 |
9 |
10 |
11 |
12 |
13 |
14 |
15 |
У4 |
0,31 |
0,13 |
1,25 |
510 700 24 |
50 |
9–10 0–1 |
40 |
60 |
0 |
– 15 |
0 |
|||
У5 |
0,42 |
0,16 |
1,22 |
570 810 22 |
47 |
8–9 |
0 |
20 |
80 |
0 |
+ 20 |
+ 30 |
Примечание: Nз – номер зерна; БП – балл полосчатости; Ф – феррит; П – перлит; ИС– игольчатыеструктуры
Для плавки с минимальным содержанием углерода (У1) при температурах плюс 20 и плюс 100 оС, когда металл достаточно вязкий, образцы с трещиной не разрушаются и соответствующие точки нанесены условно, а сама сериальная зависимость не проведена.
На рис. 3.30 показано изменение критических температур Òê12àð
и Òê20àð , номер зерна Nç и соотношение структурных составляющих
в зависимости от содержания углерода.
Известно, что в доэвтектоидных сталях повышение концентрации углерода приводит к увеличению содержания карбидной составляющей и, как результат, к измельчению зерна. В опытных плавках увеличение перлита от 0% (при 0,03 %С) до 35 % (при 0,23 %С) сопровождается уменьшением размера зерна от 7–8-го номера до 10-го номера. Измельчение структуры повышает трещиностойкость ( àð ) стали, в то время
как появление хрупкой карбидной фазы снижает ее. Объединенное влияние этих двух противоположно действующих факторов ведет к постоянному повышению критических температур с увеличением содержания углерода. Это повышение до известной степени замедляется в интервале 0,13–0,23 % С, когда зерно наиболее мелкое(Nз = 10).
Рис. 3.29. Зависимость работы развития трещины ap от температуры испытания для сталей с различным содержанием углерода
236
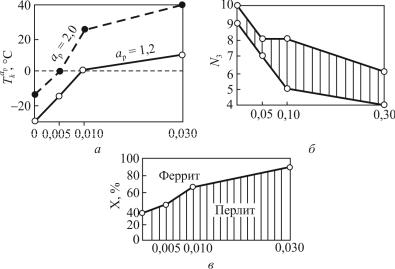
Рис. 3.30. Изменение критической температуры хрупкости Têap (а); номера зерна Nç (б) и количества структурных составляющих в сталях с различным содержанием углерода (в)
3.7.3. Влияние бора
Легирование бором [158] практически не изменяет прочностных свойств стали, только немного снижает пластичность (табл. 3.10).
Таблица 3 . 1 0
Химический состав, механические свойства, структурные характеристики и критические температуры опытных сталей с различным содержанием бора
Усл. |
Химсостав, % |
Механические |
Структурные |
|
Критиче- |
|||||||||||
обозн. |
|
|
|
|
|
свойства |
|
характеристики |
скиетемпе- |
|||||||
|
|
|
|
|
|
|
|
|
|
|
|
|
|
|
ратуры, оС |
|
|
В |
C |
Si |
Mn |
σ0,2 |
σВ |
δ |
|
Ψ |
Nз |
БП |
Объемная |
T àð |
Òàð |
||
|
|
|
|
|
|
|
|
|
|
|
|
доля, % |
ê12 |
ê20 |
||
|
|
|
|
|
|
|
|
|
|
|
|
|
|
|||
|
|
|
|
|
МПа |
% |
|
|
Ф |
П |
ИС |
|
|
|||
1 |
2 |
3 |
4 |
5 |
6 |
7 |
8 |
|
9 |
10 |
11 |
12 |
13 |
14 |
15 |
16 |
Р1 |
– |
0,20 |
0,16 |
1,47 |
380 |
580 |
30 |
|
59 |
9–10 |
0–1 |
65 |
0 |
0 |
–30 |
–15 |
Р2 |
0,005 |
0,18 |
0,18 |
1,60 |
360 |
590 |
26 |
|
52 |
7–8 |
1–2 |
55 |
10 |
0 |
–15 |
0 |
Р3 |
0,010 |
0,21 |
0,24 |
1,65 |
370 |
600 |
26 |
|
50 |
5–8 |
0–1 |
35 |
35 |
0 |
0 |
+25 |
|
|
|
|
|
|
|
|
|
|
|
|
|
|
|
|
237 |
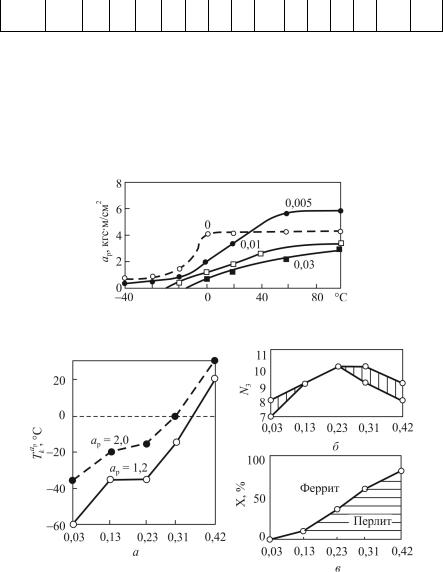
|
|
|
|
|
|
|
|
|
Окончание |
табл. |
3 . 1 0 |
||||
1 |
2 |
3 |
4 |
5 |
6 |
7 |
8 |
9 |
10 |
11 |
12 |
13 |
14 |
15 |
16 |
Р4 |
0,030 0,20 0,21 1,55 360 570 |
25 |
48 |
4–6 |
0 |
10 |
60 |
0 |
+10 |
+40 |
Примечание: Nз – номер зерна; БП – балл полосчатости; Ф – феррит; П – перлит; ИС– игольчатыеструктуры
Сериальные зависимости трещиностойкости для сталей с разным содержанием бора представлены на рис. 3.31. Хорошо видно, что с увеличением содержания бора последовательно снижается сопро-
тивление стали развитию трещины ( àð ), что приводит к повышению
критических температур (рис. 3.32). В этом отношении особенно сильно оказывает влияние легирование бором до 0,01 %.
Рис. 3.31. Зависимость работы развития трещины ap от температуры испытания для сталей с различным содержанием бора
Рис. 3.32. Изменение критической температуры хрупкости Têap (а); номера зерна Nç (б) и количества структурных составляющих в сталях с различным содержанием бора (в)
238
Как было отмечено [159], растворенный в стали бор увеличивает склонность стали к росту зерна и повышает прокаливаемость. Это является причиной появления большого количества перлита при тех же скоростях охлаждения. Следовательно, уменьшение трещиностойкости стали при легировании бором и повышение критических температур связано, с одной стороны, с охрупчиванием феррита в результате роста зерна, а с другой – с увеличанием перлитной составляющей в структуре.
3.7.4.Влияние кремния
Втабл. 3.11 даны обозначения, химический состав, механические свойства и структурные характеристики сталей с различным содержанием кремния [160]. Как видно из таблицы, прочностные свойства
нормализованной стали при легировании кремнием повышаются, а пластические снижаются. Добавление кремния снижает трещиностойкость àð сталей (рис. 3.33) при всех температурах испытания. Ле-
гирование кремнием непрерывно повышает критические температуры Òêàð , но до содержания 0,5 % Si это более слабо выражено (рис. 3.34).
Одной из причин уменьшения пластичности сталей при легировании кремнием является [161] увеличение влияния ковалентных связей между атомами в кристаллической решетке железа.
Таблица 3.11
Химический состав, механические свойства, структурные характеристики и критические температуры опытных сталей с различным содержанием кремния
Усл. |
Химсостав,% |
Механические |
|
Структурные |
|
Критические |
||||||||||
обозн. |
|
|
|
|
свойства |
|
характеристики |
|
температуры, |
|||||||
|
|
|
|
|
|
|
|
|
|
|
|
|
|
|
|
оС |
|
Si |
C |
Mn |
σ0,2 |
|
σВ |
δ |
|
Ψ |
Nз |
БП |
Количество, % |
T àð |
Òàð |
||
|
|
|
|
МПа |
|
% |
|
|
Ф |
П |
ИС |
ê12 |
ê20 |
|||
С1 |
0,03 |
0,21 |
1,4 |
310 |
|
530 |
29 |
|
63 |
6–7 |
0–1 |
65 |
35 |
0 |
–20 |
+5 |
С2 |
0,5 |
0,20 |
1,4 |
350 |
|
590 |
27 |
|
64 |
6–7 |
0–1 |
65 |
35 |
0 |
–10 |
+15 |
С3 |
0,8 |
0,20 |
1,42 |
370 |
|
640 |
23 |
|
61 |
6–7 |
0–1 |
65 |
35 |
0 |
+15 |
+45 |
С4 |
1,8 |
0,19 |
1,5 |
430 |
|
730 |
23 |
|
53 |
6–7 |
0 |
65 |
35 |
|
|
+100 |
С5 |
2,5 |
0,20 |
1,55 |
460 |
|
750 |
23 |
|
49 |
6–7 |
0 |
65 |
35 |
0 |
|
+100 |
Примечание: Nз – номер зерна; БП – балл полосчатости; Ф – феррит; П – перлит; |
||||||||||||||||
ИС– игольчатыеструктуры |
|
|
|
|
|
|
|
|
|
|
||||||
|
|
|
|
|
|
|
|
|
|
|
|
|
|
|
|
239 |
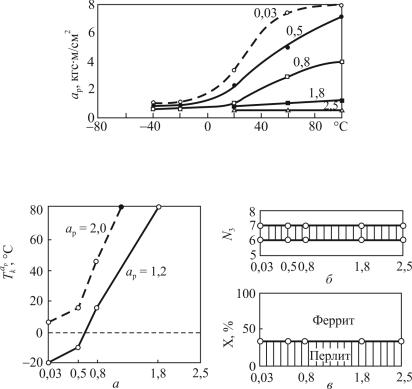
Рис. 3.33. Зависимость работы развития трещины ap от температуры испытания для сталей с различным содержанием кремния
Рис. 3.34. Изменение критической температуры хрупкости Têap (а); номера зерна Nç (б) и количества структурных составляющих в сталях с различным содержанием кремния (в)
3.7.5. Влияние марганца
Химический состав сталей, легированных марганцем, их механические свойства, структурные характеристики и критические температуры представлены в табл. 3.12 [160]. Трещиностойкость стали (рис. 3.35) с увеличением содержания марганца до 1,05 % понижается сравнительно мало. При повышении содержания марганца, однако, резко повышаются критические температуры. На рис. 3.37 показаны микроструктуры сталей с 0,07 % (рис. 3.37, а) и 2,2 % (рис. 3.37, б) марганца. Количественные структурные характеристики представлены в табл. 3.12.
240