
2802.Трещиностойкость железоуглеродистых сплавов
..pdf
Tк |
критическая температура |
Ткэк |
эксплуатационная критическая температура |
B, % |
доля волокна в изломе |
a |
ударная вязкость, определенная по методу Шарпи |
ai |
ударная вязкость, определенная по методу Шарпи для |
|
одного из образцов, указанных в табл. 3.2 (i = 1…20) |
аз |
часть от а, израсходованная на зарождение трещины |
aр |
часть от а, израсходованная на развитие трещины |
KCU |
ударная вязкость, определенная на образце типа 1 |
KCV |
ударная вязкость, определенная на образце типа 11 |
KCT |
ударная вязкость, определенная на образце типа 15 |
σmax |
максимальное напряжение цикла |
σmin |
минимальное напряжение цикла |
σR |
предел усталости, соответствующий коэффициенту |
|
асимметрии R |
Kmax |
максимальный коэффициент интенсивности напряжений |
|
цикла |
Kmin |
минимальный коэффициент интенсивности напряжений |
|
цикла |
K = |
размах коэффициента интенсивности напряжений цикла |
= Kmax – Kmin |
пороговый коэффициент интенсивности напряжений при |
Kth |
|
|
циклическом нагружении |
Kfc |
критический коэффициент интенсивности напряжений |
|
при циклическом нагружении |
ПНС |
плосконапряженное состояние |
ПДС |
плоскодеформированное состояние |
ЗТ |
зарождение трещины |
РТ |
развитие трещины |
УMP |
упругая механика разрушения |
УПМР |
упругопластическая механика разрушения |
СПЗ |
статическая пластическая зона |
ЦПЗ |
циклическая пластическая зона |
ЯЯмки. Образуются при разрыве в процессе деформации и разрушения стенок между порами, возникшими около неметаллических включений
ППлато – плоские ямки большого диаметра
11

ФФасетка – хрупкий элемент в поверхности излома
ТФ |
Транскристаллическая фасетка (фасетка, полученная в |
|
результате транскристаллитного раскалывания зерна) |
МФ |
Межзеренная фасетка (фасетка, полученная в результате |
|
хрупкого разрушения по границе зерна) |
СТФ |
Субтранскристаллитная фасетка (фасетка, полученная в |
|
результате раскалывания элемента субструктуры |
ББороздки – характерный бороздчатый рельеф, образованный при развитии усталостной трещины
ТБ |
Транскристаллитные усталостные бороздки – развивают- |
|
ся по сечению зерна |
СТБ |
Субтранскристаллитные усталостные бороздки – разви- |
|
ваются по сечению субструктуры зерна |
ДШ |
Дислокационный шнур – критическое скопление дисло- |
|
каций в характерной шнурообразной форме |
КДС |
Критическая дислокационная структура |
ДЦТ |
Диаграмма циклической трещиностойкости |
ОТН |
Относительная термическая нестабильность |
ОТС |
Относительная термическая стабильность |
12
ГЛАВА 1 СТРУКТУРНЫЕ ИЗМЕНЕНИЯ ПРИ НАГРЕВЕ
ИОХЛАЖДЕНИИ ЖЕЛЕЗОУГЛЕРОДИСТЫХ СПЛАВОВ
1.1.Обозначения и терминология
Внастоящем разделе коротко рассмотрим вопросы, связанные с превращениями, которые протекают при нагреве и охлаждении железоуглеродистых сплавов.
На рис. 1.1 представлена диаграмма состояния железоуглеродистых сплавов. Даны все буквенные, температурные, концентрационные и фазовые названия и обозначения, которых мы придерживаемся
входе изложения. Концентрация углерода в точке Е (2,14 %) делит диаграмму на две части: левую – область сталей и правую – область чугунов.
При описании процессов, протекающих при нагреве и охлаждении сталей, важными являются так называемые критические точки, которые обозначаются буквой А. Нижняя критическая точка обозна-
чается как А1 и расположена на линии PSK. Верхняя критическая точка обозначается как А3 и расположена на линии GSE. Когда речь идет о превращениях при нагреве, то к обозначению добавляется ин-
декс с (от фр. chauffage – нагревание) и тогда говорят о точках Ас1 и Ас3 . В случае если рассматривают превращения при охлаждении,
используют индекс r (от фр. refroidir – охлаждение), и тогда говорят об Аr1 и Аr3 . Иногда точка Ас3 , когда она относится к линии SE (заэв-
тектоидные стали), записывается как Асm .
При рассмотрении диаграммы «железо – углерод» используется следующая терминология:
1)феррит – твердый раствор углерода в объемноцентрированной кубической (ОЦК) решетке α-железа;
2)аустенит – твердый раствор углерода в гранецентрированной кубической (ГЦК) решетке γ-железа;
13

3)цементит (карбид железа) – химическое соединение Fe3C;
4)перлит – эвтектоидная смесь тонких ферритных и цементитных пластин;
Рис. 1.1. Диаграмма состояния системы Fe-C
5)ледебурит – эвтектическая смесь аустенита и цементита (при температурах выше А1);
6)графит – кристаллическая модификация углерода.
С помощью определенных режимов нагрева и охлаждения, проведенных с соответствующей скоростью, реализуются различные виды термической обработки, которые в соответствии с классификацией, предложенной А.А. Бочваром, могут быть разделены на следующие виды (рис. 1.2):
отжиг первого рода – термическая обработка, которая заключается в нагреве металла, находящегося в неравновесном состоянии, с целью приведения его в более равновесное состояние;
отжиг второго рода – термическая обработка, которая состоит в нагреве металла до температуры выше фазового превращения с по-
14

следующим медленным охлаждением с целью получения равновесного фазового (структурного) состояния;
Виды
термообработки
Отжиг 1-го рода |
|
|
Закалка без |
|
|||
|
|
полиморфного |
|
||||
|
|
|
|
|
|
||
|
|
Отжиг 2-го рода |
|
превращения |
|
||
|
|
||||||
|
|
|
|
|
|
||
|
|
|
|
Закалка с полиморфным
превращением
Старение
Отпуск
Рис. 1.2. Классификация основных видов термической обработки
закалка – термическая обработка, при которой высокая скорость охлаждения препятствует диффузионным процессам и получаются неравновесные структуры. Различают два вида закалки:
1)закалка без полиморфного превращения. В этом случае фикси-
руется состояние сплава, характерное для высоких температур;
2)закалка с полиморфным превращением. При такой термиче-
ской обработке в результате быстрого охлаждения высокотемпературной фазы возникает новая метастабильная фаза, отличная от той, которая наблюдалась в равновесном сосноянии.
Закаленные сплавы путем дополнительного нагрева могут быть приведены в более равновесное состояние. Такими термообработками являются старение и отпуск;
старение – в этом случае нагреву подвергаются сплавы, которые при закалке не претерпели фазовых превращений;
15

отпуск – при этом виде термообработки нагреву подвергаются сплавы, в которых после закалки образовались промежуточные метастабильные структуры.
1.2.Образование аустенита при нагреве
1.2.1.Превращение ферритоцементитной структуры
ваустенит
Для того чтобы началось превращение ферритоцементитной структуры в аустенит, необходимо нагреть ее до температуры выше заэвтектоидной линии PSK. Закономерности протекания этого превращения зависят от исходной структуры, температуры, скорости нагрева и химического состава сплава.
Поскольку по своему химическому составу аустенит очень сильно отличается от феррита и цементита, для его возникновения необходимы значительные флуктуации углерода в исходном составе стали. По этой причине аустенитные зародыши легче всего возникают на границах между ферритом и цементитом. Схематически на рис. 1.3, а для эвтектоидной структуры показан процесс зарождения (рис. 1.3, б) и постепенного роста (рис. 1.3, в – д) аустенитного зерна вплоть до полного превращения перлита в аустенит (рис. 1.3, е).
Рис. 1.3. Схема превращения перлита в аустенит при нагреве
Чтобы осуществить превращение перлита в аустенит в соответствии с диаграммой состояния (см. рис. 1.1), необходимо, чтобы процесс нагрева был очень медленным. В реальных условиях нагрева образо-
16

вание аустенита происходит при температурах выше линии PSK на диаграмме Fe – C. На рис. 1.4 показано время превращения перлита в аустенит в эвтектоидной стали при различных температурах. Видно, что чем выше температура, тем быстрее протекает превращение, и чем выше скорость нагрева, тем при более высокой температуре и за более короткое время образуется аустенит (скорость v2 > v1).
Рис.1.4. Влияние скорости нагрева на температурный интервал превращения перлита в аустенит. Сталь с 0,82 % углерода [2]
Рис. 1.5. Диаграмма изотермического образования аустенита в доэвтектоидной стали с 0,45 % С с исходной ферритоперлитной структурой (Розе и Штрассбург)
17
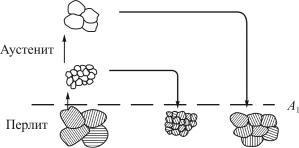
В связи с большой разницей в концентрациях углерода в феррите и цементите только что образовавшийся аустенит имеет очень неоднородный состав, в связи с чем для его гомогенизации необходимо, чтобы он определенное время находился при этой температуре. Несколько сложнее протекает образование аустенита при нагреве доэвтектоидных сталей с феррито-перлитной структурой. Сама диаграмма (рис. 1.5) по своему характеру аналогична диаграмме, представленной на рис. 1.4.
На линии 1 начинается образование аустенитного зерна в основном за счет ферритных участков в перлите, в связи с чем после линии 2 перлит исчезает и в структуре остаются только феррит, аустенит и карбид (цементит). При переходе через пограничную линию 4 структура состоит только из аустенита, который постепенно гомогенизируется.
1.2.2. Размер аустенитного зерна
Вопросы, связанные с размером аустенитного зерна, получаемого при нагреве, исключительно важны, потому что этот размер в значительной степени определяет механические свойства сталей после распада аустенита при его охлаждении. Это схематически показано на рис. 1.6. Из грубой перлитной структуры в результате нагрева до температуры на 30–50 °С выше точки Ac1 получается мелкозернистая
аустенитная структура, в которой при последующем охлаждении образуются достаточно мелкие перлитные колонии. Если же аустенитные зерна образуются при высоких температурах, то они успевают подрасти и при последующем охлаждении образуется крупнозернистая структура с низкими механическими свойствами.
Рис. 1.6. Схема изменения размера зерна перлита в зависимости от температуры нагрева в аустенитной области [2]
18

Для характеристики процессов, связанных с размером полученного при нагреве аустенитногозерна, принята следующая терминология.
Исходное (начальное) зерно – размер зерна в момент завершения превращения перлита в аустенит.
Наследственное (природное) зерно – зерно, которое характери-
зует склонность аустенитного зерна данной стали к росту. Действительное зерно – размер аустенитного зерна, получен-
ного в результате конкретного режима термической обработки. Используемые в практике стали обычно делят на две группы –
наследственно крупнозернистые и наследственно мелкозернистые. На рис. 1.7 дана схема, поясняющая процесс роста аустенитного зерна в наследственно крупнозернистых 1 и мелкозернистых 2 сталях при повышении температуры. Важной особенностью является то, что в наследственно мелкозернистых сталях мелкое аустенитное зерно сохраняется до температуры 950–1100 °С, что, естественно, делает эти железоуглеродистые сплавы более качественными. Однако при
Рис. 1.7. Схема роста зерна аустенита в наследственно крупнозернистых 1 и наследственно мелкозернистых 2 сталях [4]
значительно более высоких температурах аустенитные зерна в наследственно мелкозернистой стали могут оказаться большего размера, чем аустенитные зерна в наследственно крупнозернистой стали. Причиной, объясняющей такое поведение наследственно мелкозер-
19
нистой стали, является так называемый барьерный эффект. При раскислении стали алюминием последний соединяется с азотом и кислородом, создавая большое количество мелких по размеру нитритов (AlN) и оксидов (Al2O3), которые располагаются по границам зерен и препятствуют их росту. Для усиления барьерного эффекта в последнее время стали легируют такими элементами, как ванадий, ниобий, молибден и азот, которые создают дополнительное количество карбонитридов. При достаточно высоких температурах эти частицы растворяются, барьерный эффект пропадает и аустенитные зерна быстро вырастают. Создана специальная технологическая проба для оценки склонности аустенитных зерен к росту. Сравнение производят при температуре tп = 930 °С (см. рис. 1.7).
1.3. Диффузионное превращение аустенита при охлаждении
При охлаждении аустенита (см. рис. 1.1) под эвтектоидной линией PSK (727 °С) начинается его превращение в феррито-цементитную смесь. В зависимости от содержания углерода в стали этот распад протекает с определенными особенностями, которые мы рассмотрим ниже. При содержании углерода 0,8 % этот так называемый эвтектоидный состав превращается в характерную пластинчатую ферритоцементитную структуру, известную под названием перлит. На рис. 1.8 показана схема зарождения и роста перлитных колоний. Роль зародышей могут играть как ферритные, так и цементитные образования, которые появляются на границе с аустенитом. Если зародышем является цементитная пластинка (рис. 1.8, а), при ее росте окружающая аустенитная среда обедняется углеродом и там возникают благоприятные условия для образования двух ферритных пластин (рис. 1.8, б). Они постепенно растут и утолщаются и, поскольку феррит практически не содержит углерода, последний накапливается в соседней области, где создаются благоприятные условия для появления цементитных пластин. Этот процесс повторяется многократно (рис. 1.8, г), и на границах аустенитного зернапоявляются перлитные колонии.
Очень важно отметить, что размер перлитных колоний зависит от двух факторов: от размера действительного аустенитного зерна и температуры, при которой происходит распад. Чем мельче аустенит-
20