
1363
.pdfВ зависимости от крупности дробимой породы и дробленого продукта стадии дробления имеют особые названия: первая стадия — крупное дробление (от 1500 до 350 мм), вторая стадия — среднее
дробление |
(от 350 до 100 мм) и третья стадия — мелкое дробление |
(от 100 до |
5 мм). При подготовке цементного сырья наиболее часто |
используют две стадии дробления — среднее и мелкое.
Для характеристики процесса дробления в целом, а также исполь зуемого для этого дробильного оборудования пользуются показа телем, называемым степенью измельчения. Степенью измельчения i принято называть отношение поперечных размеров куска D, посту пающего на дробление, к поперечным размерам измельченных кусков d:
i — D/d.
Например, если средний размер кусков породы, добываемой в карьере, равен 1 м, а размер кусков, поступающих на помол в мель ницу, не должен превышать 40 мм, то общая степень дробления породы должна составить 10бщ = 1000/40 = 25.
Степень измельчения зависит от физических свойств породы, исходных размеров ее кусков и конструкции дробильных машин. Общая степень измельчения на всех стадиях дробления равна про изведению степеней, достигнутых на каждой стадии:
^Общ
Например, при двухстадийном дроблении на дробильных маши нах, степень измельчения каждой из которых составляет соответ
ственно |
= 6 |
и t2 = 5, |
|
|
«общ = 6-5 = 30. |
|
§ 26. |
Классификация дробильного оборудования |
Основными способами измельчения горных пород, осу ществляемыми рабочими органами оборудования, являются раз давливание (рис. 17, а), разрушение ударом (рис. 17, б), истирание
^1 ^
Шш
а)
.. Й Я
Рис. 17. Схемы способов дробле ния
Рис. 18. Схемы дробилок и мельниц
(рис. 17, в), раскалывание (рис. 17, г). При разработке дробильного оборудования часто используют различные комбинации этих спо собов (например, раздавливание с ударом, удар с истиранием), сопровождаемые действием изгибающих, срезающих и разрыва ющих сил. Твердые материалы наиболее эффективно измельчаются ударом или раздавливанием, пластичные — раздавливанием в со четании с истиранием, хрупкие материалы — раскалыванием.
На основании рассмотренных способов измельчения разработаны различные типы дробилок (рис. 18).
Вщековых дробилках (рис. 18, -а) дробление происходит в ре зультате раздавливания при периодическом сжатии между неподвиж ной 1 и подвижной 2 щеками.
Вконусных дробилках (рис. 18, б) дробление материала про исходит в результате раздавливания и истирания между двумя конусами, расположенными один внутри другого. Внешний конус 3 неподвижен, а внутренний (дробящий) 4, посаженный на вертикаль ный вал 5, движется по окружности эксцентрично к внешнему ко нусу. В конусных дробилках процесс измельчения происходит не прерывно. В связи со сложностью эксплуатации и ремонтного об служивания данные дробилки в цементной промышленности при меняют ограниченно. В отдельных случаях их используют на второй стадии дробления.
Ввалковых дробилках (рис. 18, в) дробление происходит сжатием материала между валками 6 и 7, вращающимися навстречу друг Другу.
Дробление |
в роторных |
(ударно-отражательных) дробилках |
(рис. 18, г) |
осуществляется |
в результате раскалывания кусков |
твердых пород ударами бил, жестко закрепленных на быстровращающемся роторе 8, а также удара породы об отражающие плиты 9.
62
Т а б л и ц а 16. Область использования дробилок для измельчения
сырьевых материалов
_ |
„ |
|
I |
Дробилки, используемые на |
различны х |
|
материал |
I |
|
стадиях дробления |
|
||
Сырьевой |
I____________________________ _____________________ |
|||||
|
|
|
1 |
I |
И |
111 |
|
|
|
|
|
|
|
Особо твердый известняк |
|
Щековая |
Щековая, |
Молотковая |
||
Твердый |
известняк, мергели |
|
|
роторная |
__ |
|
|
|
То же |
||||
средней твердости |
|
Молотковая |
Молотковая |
_ |
||
Твердый известняк-ракушеч- |
|
|||||
ник, трепел, опока |
|
самоочищаю |
|
|
||
Твердые трепел, |
туф |
|
щаяся |
|
|
|
|
То же |
|
|
|||
В молотковых дробилках (рис. 18, д) |
дробление материала про |
исходит в результате раскалывания ударами молотков 10, шар нирно закрепленных на быстровращающемся роторе 11, и отчасти истиранием о колосниковую решетку.
В мельницах «Гидрофол» мокрого самоизмельчения (рис. 18, ё) дробление и размучивание пластичных пород в присутствии воды
происходит за |
счет ударов о выступы 12 и 13 |
плит, закрепленных |
с внутренней |
стороны быстровращающегося |
барабана, а также |
соударения кусков породы. |
|
Выбор технологической схемы дробления и соответствующего дробильного оборудования определяется физическими свойствами породы, способом производства цемента и мощностью карьера.
Организация процесса дробления пластичных материалов за висит от способа производства цемента и существенно отличается от процесса дробления твердых материалов. При производстве це мента сухим способом мягкие породы (мел, мергель, глина и др.) доставляют с карьера на территорию завода без предварительного измельчения, здесь их дробят с одновременной сушкой. При про изводстве цемента мокрым способом мягкие породы предварительно измельчают в мельницах «Гидрофол», расположенных, как правило, в карьерах мощных заводов, и полученную пульпу влажностью до 60 % гидротранспортом доставляют на территорию завода для домола в сырьевых мельницах.
Организация процесса дробления сырьевых материалов твердых пород не зависит от способа производства цемента и в зависимости от физических свойств породы и исходной крупности кусков осу ществляется в несколько стадий с выбором соответствующего дро бильного оборудования (табл. 16).
§ 27. Щековые дробилки
При крупном и среднем дроблении твердых сырьевых пород с коэффициентом крепости / < 30 щековые дробилки являются основным агрегатом.
о |
2 |
Рис. 19. Кинематические схе |
|
|
мы щековых дробилок |
Основными параметра ми, характеризующими щековую дробилку, явля ются размеры приемного отверстия и выходной щели. Например, дробил ка ШДП-12Х15 имеет ши рину приемного отверстия
1200 мм, длину его 1500 мм и ширину выходной щели 155 мм. От ши рины приемного отверстия зависит максимальный размер исходного куска, что определяет выбор выемочно-погрузочного оборудования, обслуживающего дробилку. Размер загружаемого куска не должен превышать 0,85 ширины отверстия. От длины приемного отверстия зависит количество загружаемых кусков, а следовательно, и произ водительность дробилки. Ширина выходной щели характеризует максимальный размер дробленой породы, т. е. степень измельчения.
По принципу действия щековые дробилки разделяют на дробилки
спростым и сложным движением щеки.
Удробилок с простым движением щеки (рис. 19, а) подвижная щека 1 качается около точки О, то приближаясь к неподвижной щеке, то удаляясь от нее. Куски материала раздавливаются между ще ками. Такие дробилки предназначеныдля крупного дробления породы.
Удробилок со сложным движением щеки (рис. 19, б) подвижная щека 1, посаженная на вращающийся эксцентрик 2, не только ка чается, но и совершает сложное движение, приближающееся в сред ней части к эллипсу. Благодаря такому движению подвижной плиты куски материала не только раздавливаются, но и истираются, в ре зультате чего происходит эффективное дробление кусков средней крупности.
Дробилки с простым движением подвижной щеки (рис. 20, а) имеют сборную станину, состоящую из литых стальных боковых и торцовых стенок, соединенных стяжными болтами, и представляют собой жесткую конструкцию коробчатой формы. К стенке 1 болтами прикреплена ребристая неподвижная щека (плита) 13. Подвижная щека 3 с дробящей плитой 12 надета на ось 4, смонтированную на подшипниковых узлах. Боковые стенки дробилки облицованы бро невыми плитами 2.
Приводной вал 5 смонтирован на подшипниках качения. На экс центриковую часть этого вала надеты подшипники качения, охва тываемые головкой шатуна 6. На выступающие за подшипники концы вала насажены маховики 15, 16, один из которых {15) является и шкивом. Для плавного включения дробилки или прекращения работы подвижной щеки эксцентриковый вал соединен со шкивом многодисковой фрикционной муфтой 14.
Шлицы ведущих дисков 21 муфты (рис. 20, б) соединены с втул кой 20, скрепленной болтами с маховиком, а ведомые диски l'J
64
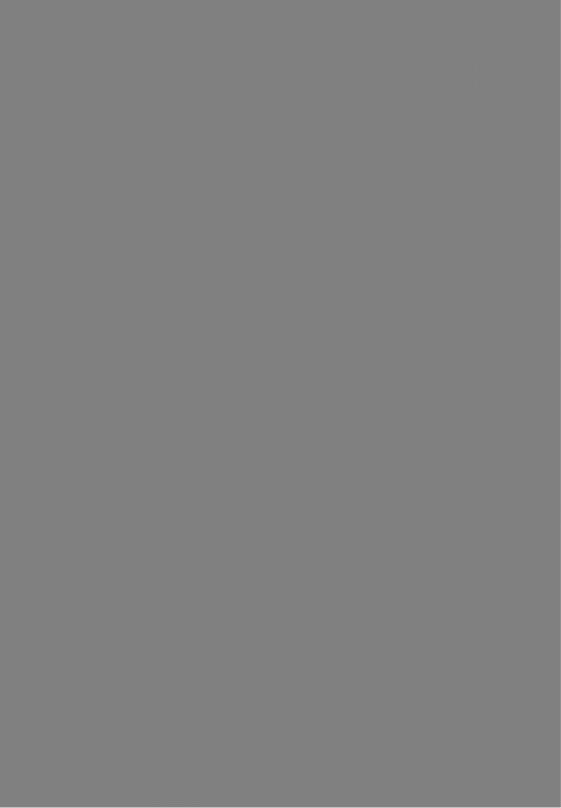
оттягивается тягой 8 с пружиной 7 Дробилки оборудуют центра
лизованной автоматической смазочной системой.
Привод дробилки смонтирован на одной раме и состоит из глав ного и вспомогательного электродвигателей. Главный электродви гатель посредством ведущего шкива и клиноременной передачи вращает главный эксцентриковый вал дробилки в рабочем режиме. Для разгона дробилки служит вспомогательный электродвигатель небольшой мощности (по сравнению с мощностью главного), снабжен ный редуктором и обгонной муфтой. Муфта позволяет пускать дро билку с малой частотой вращения и автоматически отключать Вспо могательный электродвигатель при включении главного.
При вращении главного эксцентрикового вала дробилки шатун совершает возвратно-поступательное движение в вертикальной Пло скости, попеременно поднимает и опускает примыкающие к Нему торцы распорных плит. При этом изменяется угол развала пдит^ в результате чего подвижная щека приближается к неподвижной (при движении шатуна вверх) или с помощью пружины запорного устройства удаляется от нее (при движении шатуна вниз). При сбди_ жении дробящих щек происходит раздавливание материала в кам$ре дробления, при расхождении щек — дробленый продукт выпадет через выходную щель, а не дробленый опускается в зону дробленця
В щековых дробилках материал дробится только в течение одной половины оборота эксцентрикового вала. Для выравнивания работы щековой дробилки служат маховики, которые накапливают энергню во время отхода щеки и отдают ее в период дробления.
Дробилки со сложным движением подвижной щеки (рис. 2п по конструкции узлов аналогичны дробилкам с простым движением подвижной щеки, кроме механизма приведения в движение щекц Станина 1 дробилки коробчатого типа с ребрами жесткости $ с внутренней стороны рабочей зоны для предохранения от изна„
шивания облицована гладкими боковыми износостойкими плитами 2 D
неподвижная щека — рифленой дробящей плитой 9. На подвижной щеке с помощью болтов с потайной головкой и клинового распора 11 закреплена рифленая дробящая плита 10. Подвижная щека 5 за креплена на эксцентриковом приводном валу 4 с помощью сфериче ского подшипника 6. Вал вращается на двух сферических под шипниках, установленных на станине в коренных разъемных кор пусах 3. На концах приводного вала закреплены шкив 2 и маховик 7. Нижняя часть подвижной^ щеки упирается в распорную плиту 21. Второй конец распорной плиты упирается в регулировочный клин 18, перемещению вверх которого препятствует площадка 20.
Угол наклона распорной плиты, а следовательно, и ширину выходной щели дробилки, регулируют вращением резьбовой втулки 13 с насаженной на нее звездочкой 12. При этом с помощью болта 17 перемещают упорный клин 19. Пружина 14 на тяге 16
сгайками 15 осуществляет постоянное прижатие подвижной щеки
краспорной плите.
Щековые дробилки классифицируют по характеру движения подвижной щеки, а также по размерам приемного отверстия. Напри мер, марка ЩДС-Н-1,6x2,5 означает — щековая дробилка со слож ным движением подвижной щеки с размерами приемного отверстия 160x250 мм, а ЩДП 15x21 — щековая дробилка с простым движе нием подвижной щеки с размерами приемного отверстия 1500X Х2100 мм.
Техническая характеристика отечественных щековых дробилок приведена в табл. 17.
Исходными данными для выбора щековых дробилок являются крупность загружаемых кусков породы £>тах, необходимая макси мальная крупность дробленой породы dmax, прочность породы и производительность дробилок Я.
Ширину В приемного отверстия (в мм) выбирают из условия свободного приема кусков максимальной крупности с соблюдением
условия |
(29) |
В ^ Апах/0,85. |
Например, для кусков загружаемой породы размером до 1 м ширина загрузочного отверстия должна быть не менее 1000/0,85 =
= 1176 мм.
Длину L приемного отверстия и выходной щели принимают: для дробилок с простым движением щеки L = (1,25-М ,4) В; для дробилок со сложным движением щеки L ■— (1,5-^3,5) В.
Максимальный размер (в мм) выходящих из выходной щели кусков породы dmах зависит от ее ширины b, а также от возможности
расположения куска длинной стороной вдоль щели: |
|
dnm* < 1.256. |
(30) |
Например, для получения дробленого куска максимальным раз мером 200 мм ширина выходной щели b = 200/1,25 = 160 мм.
Для определения высоты рабочей камеры дробилки определяют рациональный угол а между неподвижной и подвижной дробящими
Т а б л и ц а 17 Техническая характеристика щековых дробилок
Со сложным движением |
С простым |
|
движением |
||
|
Показатель
ЩДС-1-4 X 9
ю
сГ X
CD
6 tc
a
ЩДС-П-бХ 9 |
ЩДС-П-9Х 12 |
ЩДС-П-12Х 15 |
ЩДП-9Х 12 |
ЩДП-12Х 15 |
ЩДП-15Х 21 |
Размеры приемного |
от |
|
|
|
|
|
|
|
|
|||
верстия, мм: |
|
|
400 |
160 |
600 |
900 |
1200 |
900 |
1200 |
1500 |
||
длина |
|
|
|
|||||||||
ширина |
размер |
ку |
900 |
250 |
900 |
1200 |
1500 |
1200 |
1500 |
2100 |
||
Наибольший |
340 |
130 |
500 |
750 |
1000 |
750' |
1000 |
1300 |
||||
ска |
исходного |
мате |
|
|
|
|
|
|
|
|
||
риала, мм |
|
|
|
|
|
|
|
|
|
|
|
|
Ширина выходной щели |
|
|
|
|
|
|
|
|
||||
в фазе раскрытия, |
мм: |
60 |
30 |
100 |
130 |
155 |
130 |
155 |
180 |
|||
номинальная |
|
|
||||||||||
диапазон |
регулиро |
+304- |
±15 |
±25 |
±35 |
±40 |
±35 |
±40 |
±50 |
|||
|
вания, |
не менее |
—20 |
3 |
60 |
180 |
310 |
180 |
310 |
550 |
||
Производительность |
при |
( 30 |
||||||||||
номинальной ширине |
|
|
|
|
|
|
|
|
||||
выходной щели, |
м3/ч, |
|
|
|
|
|
|
|
|
|||
не менее |
двигателя |
55~ |
7,5 |
75 |
НО |
160 |
110 |
160 |
250 |
|||
Мощность |
||||||||||||
основного привода, |
|
|
|
|
|
|
|
|
||||
кВт, |
не более |
|
мм, |
|
|
|
|
|
|
|
|
|
Размеры дробилок, |
|
|
|
|
|
|
|
|
||||
не более: |
|
|
|
2500 |
950 |
3000 |
|
|
5300 |
6400 |
7500 |
|
длина |
|
|
|
— |
— |
|||||||
ширина |
|
|
|
2400 |
1100 |
2500 |
— |
— |
6000 |
6800 |
7000 |
|
высота |
|
т, |
не |
2200 |
1100 |
1800 |
— |
— |
4000 |
5000 |
6000 |
|
Масса |
дробилок, |
13 |
1,5 |
21 |
|
|
75 |
145 |
260 |
|||
более |
|
|
|
|
|
|
|
|
|
|
|
плитами (рис. 22, а). Этот угол называют углом захвата. При малом значении а увеличивается высота дробилки, при большом значе нии — куски породы могут не разрушаться при нажатии, а вытал киваться вверх.
Рассмотрим силы, действующие на кусок породы при его сжатии между плитами (см. рис. 22, а) Для упрощения расчета кусок дро бимого материала представлен шаром. Усилие Р дробления прини маем направленным перпендикулярно к плоскости щек, а весом куска дробимого материала пренебрегаем, поскольку он во много раз меньше усилий, действующих на него.
Усилие дробления вызывает силу трения Pf> где коэффициент трения скольжения твердой породы по металлу / = 0,3. Вертикаль ная составляющая силы трения Pf cos (а/2) направлена в сторону, противоположную действию сил, выталкивающих кусок из дро-
68
Рис. 22. Схема для определения параметров щековой дробилки:
а — рационального угла а захвата; б — частоты вращения эксцентрикового вала; в — произ водительности
билки. Усилие Р дробления раскладывается на вертикальную Р sin (а/2) и горизонтальную Р cos (а/2) составляющие. Исходя из условия равновесия куска породы в дробилке под действием силы Р нажатия и вызываемых ею в точках касания сил трения Р/, получим
2Psin (а/2) |
= 2Pf cos (а/2). Разделив |
обе части этого |
равенства на |
||
2Р cos (а/2), |
получим / |
= tg (а/2). Из курса механики |
известно, что |
||
/ = tg ф. |
Подставляя |
значение /, |
получим tg (а/2) |
= tg ф или |
|
(а/2) = ф, |
откуда а = 2ф. |
|
|
Следовательно, для обеспечения условий дробления угол за хвата а должен быть равен двойному углу трения или быть меньше его. При / = 0,3 ф = 16° 40' и предельное значение а = 33° 20'. При конструировании щековых дробилок принимают а = 15-f-20°.
Высоту Н рабочей камеры (в мм) при заданных размерах ширины приемного отверстия 5 , выходной щели Ъ и угла захвата а можно
определить по |
следующей формуле: |
|
||
|
|
|
В — Ъ |
(31) |
|
|
|
tg а |
|
|
|
|
|
|
Например, |
при В = |
1000 м, |
b = 140 мм, а = 20°, высота рабо |
|
чей камеры |
|
1000 - |
но = 2362 мм. |
|
|
|
|
||
|
|
0,364 |
|
|
При этом |
степень измельчения |
|
||
|
Ртах |
_ 0,855 |
_ 0,85-1000-0,8 |
|
|
^тах |
Ь/0,8 |
140 |
|
Частоту хода подвижной щеки, т. е. частоту вращения эксцен трикового вала дробилки, определяют из условия обеспечения времени прохождения пути h падающим раздробленным материалом
(рис. 22, б).
Учитывая, что ход щеки по сравнению с высотой рабочей камеры дробилки невелик, принимают угол а при качании щеки неизмен ным. Высота h слоя раздробленного и выпадающего из дробилки ма териала (в м) зависит от расстояния SKотхода нижней части подвиж
ной |
щеки и выражается |
зависимостью |
||||
|
|
|
h = |
SJtg а. |
(32) |
|
На основании закона свободного падения путь, пройденный |
||||||
телом |
|
|
|
|
|
|
где |
— время, необходимое для выпадания раздробленного материала из дробилки, |
|||||
с; g — ускорение |
свободного падения, |
g = 9,81 м/с2. |
||||
Подставляя |
это выражение |
в формулу (32), определим время |
||||
(в с) |
|
|
|
_ |
|
____ |
|
|
/ __ l f 2h _ l / |
2SH |
|||
|
|
^ |
У |
g |
У |
g t g « ‘ |
Для беспрепятственного выпадания раздробленного материала необходимо, чтобы время соответствовало времени t2 отхода щеки из левого положения в правое. Поскольку щека отходит за полоборота эксцентрикового вала, то
, |
_ |
J _ |
60 |
_ |
30 |
- |
““ |
2 |
п |
~ |
п 9 |
где п — частота вращения эксцентрикового вала, об/мин.
Учитывая, что /х = /2, получаем
2SH |
30 |
откуда п |
___ 30_ |
|
g tga |
п 9 |
V |
2SH |
|
|
|
|
- |
|
|
|
|
V |
g tga |
При g = 9,81 м/с2 и a = 20° частота вращения эксцентрикового вала (в об/мин)
40,1
(33)
Так как трение кусков материала между собой и о плиты щек тормозит свободное выпадение кусков через выходную щель, обычно принимают частоту вращения вала на 10 % меньше расчетной.
Ход сжатия плиты в нижней точке (в мм) при конструировании дробилок со сложным движением щеки принимают
S„ = |
7 +0.1&, |
(34) |
а дробилок с простым движением щеки |
|
|
SH= |
8 + 0,266. |
(35) |