
1363
.pdf2 |
1 |
Рис. 158. С хема автом атической упаковочной |
установки «Ф луксом атик» (Д ан и я) |
щему их на уровень штуцеров 11 и ориентирующему мешки клапа нами к штуцеру.
Насадочный механизм состоит из механического захвата и сопла для подачи сжатого воздуха. Поток сжатого воздуха раскрывает клапан мешка в то время, когда захват прижимает стенки клапана к соплу. Затем захват поднимает клапан до уровня штуцера упа ковочной машины. Штуцер при вращении проходит мимо мешка и, попадая наконечником в отверстие клапана, увлекает мешок за собой, отделяя его от пачки. Когда вес заполняемого мешка достиг нет заданного значения, автоматически срабатывает отсекающий шибер и подача цемента из штуцера прекращается. К моменту окон чания загрузки цемента рамка с мешком подходит к разгрузочной позиции, где с помощью ряда устройств мешок снимается со штуцера и подается на разгрузочный конвейер. Производительность уста новки 3000 мешков в 1 ч.
В упаковочных отделениях ряда цементных заводов СССР уста новлены линии по упаковке бумажных мешков в прочную термо усадочную пленку. Такая упаковка цемента намного ускоряет по грузочно-выгрузочные процессы, упрощает хранение цемента и сни жает его потери.
Автоматизированная линия фирмы «Меллере» (ФРГ) для упа ковки бумажных мешков с цементом (рис. 159) работает следующим образом. От упаковочных машин мешки подаются на роликовый конвейер 9, транспортирующий их на ленточный конвейер 8 вырав нивания мешков, который состоит из двух транспортеров — верх него и нижнего. Далее мешки подаются в штабелеукладчик 7. Шта-
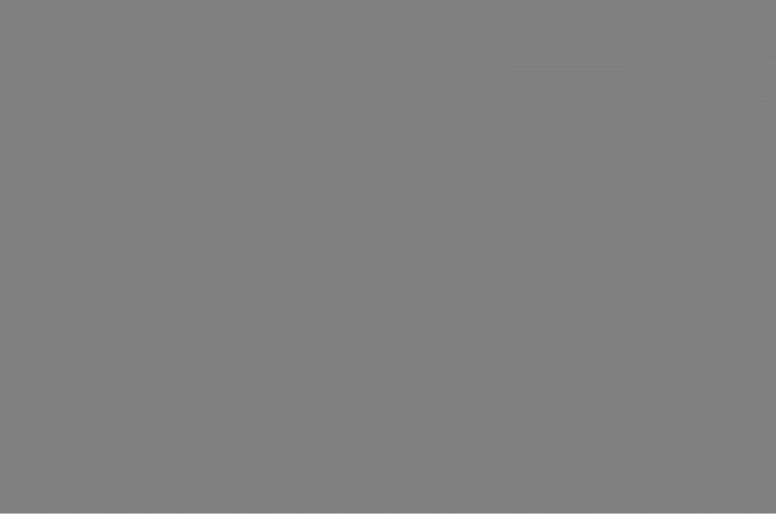
белеукладчик ориентирует (поворачивает) мешки так, чтобы полу* чить такой пакет, какой заложен в программном устройстве (обычно семь слоев по пять мешков и один слой по четыре мешка «вперевязку» общей массой 1950 кг). Повороты мешков осуществляются выдвиганием тех или иных упоров навстречу движущимся по кон вейеру мешкам. Кроме того, штабелеукладчик снабжен двумя вра щающимися вилками. Одна забирает мешки с подающего конвейера и поднимает на грузовой балкон, другая снимает их с балкона и подает на выгрузочный конвейер.
Выгрузочный конвейер транспортирует мешки к машине 6 для покрытия пакета пленочным рукавом, представляющей собой раму, на которой смонтировано устройство подачи пленки, намотанной на бобину. Пленка толщиной 0,15—0,25 мм поставляется в виде рукава с боковыми складками. В верхней части машины установлены сварочное устройство, состоящее из двух нагревающихся пластин, расширяющий механизм и отрезное устройство. Сверху на пакет надевается рукав, благодаря вертикальному перемещению расши ряющего механизма. После чего пластины сварочного устройства сваривают рукав сверху, а отрезное устройство его отрезает.
Пакет с надетым сверху рукавом контейнером направляется в формующее устройство 4, где выполняются сверху ниши для вилок погрузчиков. После этого пакет возвращается на кантователь 5, который переворачивает его так, чтобы надетый рукав оказался внизу, и цикл надевания рукава, сварки и отрезки повторяется снова.
Пакет с надетыми снизу и сверху рукавами подается в электро термическую печь 3 с автоматическими дверями, где под действием температуры 180—250 °С пленка усаживается и плотно облегает пакет. Готовый пакет подается в охлаждающее устройство 2, где пленка под действием мощных струй воздуха, создаваемых венти лятором, охлаждается и транспортируется дальше на выгрузочный конвейер /, с которого снимается вилочным погрузчиком.
Производительность установки 50 пакетов в час или 1950 меш ков в 1 ч (в одном пакете 39 мешков).
Р А З Д Е Л VI
ОБОРУДОВАНИЕ ДЛЯ ПРОИЗВОДСТВА ИЗВЕСТИ И ГИПСА
Г л а в а 25
ОБОРУДОВАНИЕ ДЛЯ ПРОИЗВОДСТВА ИЗВЕСТИ
§ 111. Технологические схемы производства извести
В промышленности строительных материалов известь используют в основном как вяжущее вещество в производстве авто клавных материалов (кирпича, камней, бетонов). Ее производят путем обжига (декарбонизации) карбонатных магниевых пород при температурах 1000—1200 °С.
В зависимости от вида и свойств карбонатной породы применяют различные технологические схемы и оборудование для производства извести. Принципиально они не отличаются от производства це мента, и их выбор также зависит от физико-механических свойств исходных сырьевых материалов. При прочих карбонатных породах
скоэффициентом крепости f = 8-4-10, характеризующим устойчи вое состояние кусков при обжиге, применяют технологические схемы
сиспользованием обжигового агрегата с шахтной печью. Низкопроч ные, растрескивающиеся и рассыпающиеся, мелкоразмерные куски
известняка (до 30 мм), а также меловые породы влажностью до 20 % перерабатывают на известь также по сухому способу с исполь зованием вращающейся печи. Производство извести из меловых по род влажностью более 20 % осуществляют по технологической схеме с вращающимися печами мокрого способа.
На рис. 160 приведена схема компоновки оборудования при производстве извести в шахтных печах. Сырьевую породу после предварительного рыхления в карьере с помощью экскаватора гру зят в технологический транспорт и доставляют на территорию завода для хранения на складе 1 сырья. Со склада куски породы подают на измельчение в дробильный агрегат 2 с щековой дробилкой, после чего их подвергают сортированию на грохоте 3. Кондиционный материал кусками размером 40—150 мм транспортируют на склад 6, рядом с которым размещают склад 5 технологического топлива (угля). Со складов 5 и 6 сырье и топливо через приемный бункер 7 загружают в подъемник 9 и подают в загрузочное устройство 8 шахтной печи 10. При этом соотношение минимального и максималь ного размеров загружаемых кусков материала не должно превышать
1 2 (например, 40—80, |
60—120, 75—150 и др.). |
После обжига в шахтной |
печи известь транспортером 11 подают |
на хранение в силосный склад 13. Сырье, топливо и готовую про дукцию транспортируют по автомобильной дороге 14 и железнодорож ным подъездным путям 4 и 12. Для отгрузки потребителю молотой
304
Рис. 160. Схема компоновки производ ства извести с использованием шахт ных пересыпных печей
извести на заводе предусма тривают помольное отделение с установкой трубных мельниц.
Технологическая схема про изводства извести по мокрому способу практически не отли чается от технологической Схе мы производства цемента ана логичного способа. При этом заимствуют как технологиче ское цементное оборудование, так и компоновочные решения технологических переделов це ментного производства. В ка честве сырья для производства извести этим способом исполь зуют меловые породы с карь ерной влажностью более 20 %.
§ 112. Классификация технологического оборудования
По функциональному назначению технологическое обо рудование для производства извести распределяют на следующие основные группы.
1. Оборудование для добычи и транспортирования сырьевых материалов от карьера до территории завода.
2. Оборудование для подготовки (кондиционирования) сырьевых материалов.
3.Оборудование для подачи сырья в обжиговый агрегат.
4.Обжиговый агрегат.
5.Оборудование для выгрузки готовой продукции.
6.Оборудование для сжигания топлива и обеспыливания отходя щих из печи газов и аспирационного воздуха.
Оборудование для добычи, измельчения и подготовки сырьевой шихты при производстве извести аналогично оборудованию, исполь зуемого при производстве цемента. При его выборе учитывают фи зико-механические свойства исходного сырья, мощность предприя тия, его удаленность от карьера и др. Как правило, предприятия по производству извести отличаются от цементных заводов сравни тельно незначительной мощностью, и все его технологические пере делы располагаются на одной площадке. Кроме того, значительную долю печного парка для обжига извести составляют шахтные печи различной конструкции, в то время как на цементных заводах они остались в единичных экземплярах.
§ 113. Классификация и эффективность печных агрегатов
В зависимости от вида используемого технологического топлива различают шахтные пересыпные (работающие на угле), газовые, полугазовые и работающие на жидком топливе печи. Пред приятиями промышленности строительных материалов на технологи ческих линиях с шахтными пересыпными печами выпускаются около 30 % общего количества извести, столько же на линиях с шахтными газовыми печами; с использованием вращающихся печей выпускают около четверти производимой извести. Остальной выпуск приходится на шахтные полугазовые, мазутные и выводящиеся из эксплуатации
всилу технического несовершенства кольцевые и напольные печи.
Впроизводстве извести в последние годы реализуется тенденция по вышения мощности обжиговых агрегатных печей всех типов.
Каждый обжиговый агрегат имеет свои достоинства и недостатки. К преимуществам печей шахтного типа, в первую очередь, следует отнести низкий расход топлива при обжиге извести, обусловленный конструкцией, обеспечивающей оптимальные условия теплообмена,
атакже низкие затраты при их строительстве. Технологическим не достатком этих печей является возможность обжига только прочных неразрушающихся карбонатных пород. Преимущество вращающихся печей — значительно более широкая возможность использования сырьевых материалов различных видов, т. е. их технологическая универсальность. К их основному недостатку относятся достаточно высокий расход топлива на обжиг, значительные затраты на их строительство.
Так, при обжиге по сухому способу 1 т извести в шахтных пе чах расходует 130—180 кг условного топлива и 10—30 кВт электро энергии, а во вращающихся печах этим же способом — соответст
венно 250—300 кг и 40—50 кВт. Поэтому выбор технологической схе мы и основного технологического оборудования для производства извести осуществляют прежде всего с учетом свойств сырья.
§ 114. Основные требования к размещению оборудования
Размещение технологического оборудования должно обе спечивать удобство его обслуживания и ремонта с соблюдением дей ствующих норм и правил по технике безопасности и промышленной санитарии и одновременным учетом максимально возможной ком пактности производства. Расстояние между осями печей при группо вом их расположении должно составлять: 9 м для шахтных печей производительностью до 100 т/сут и 12 м — более 100 т/сут; 12 м для вращающихся печей с диаметром корпуса до 4 м и 15 м — с диамет ром более 4 м.
Вращающиеся и шахтные печи, циклоны и электрофильтры рас полагают на открытых площадках с местными укрытиями приводов, тягодутьевых машин, лебедок и грузоподъемных механизмов. Зоны обслуживания устройств для подачи и сжигания топлива в печи,
306
Материал |
Плотность, |
Угол естественно |
т/м3 |
го откоса при |
|
|
|
хранении, ° |
Известняковая мелочь |
1,2—1,4 |
45—50 |
Известь: |
|
40—45 |
комовая |
1 - U |
|
мелкодробленая |
0,8—1 |
40—45 |
молотая |
0,5—0,9 |
35—40 |
Кокс |
0,4—0,6 |
40 |
Уголь и антрацит |
0,7—1 |
45 |
Двуводиый гипс |
1,2—1,4 |
45 |
дозирования и питания материалами, загрузочных устройств разме щают в неотапливаемых помещениях легкого типа.
Для производства ремонтных работ, связанных с монтажом или демонтажом установленного оборудования или его частей, преду сматривают проемы в перекрытиях или в стенах, а также установку грузоподъемных механизмов. Нагрузки на ремонтно-монтажные площадки определяют с учетом наиболее тяжелых узлов, запасных частей и деталей оборудования при проведении ремонтных и монтаж ных работ.
Технологическое оборудование компонуют, исходя из предельных возможностей транспортирования материалов с помощью спускных лотков, ленточных конвейеров, а также их хранения в емкостях и истечения через течки и учитывая плотность материалов и угол есте ственного откоса (табл. 60).
Г л а в а 26
ТЕХНОЛОГИЧЕСКИЕ ЛИНИИ ПРОИЗВОДСТВА ИЗВЕСТИ НА ОСНОВЕ ШАХТНЫХ ПЕЧЕЙ
§ 115. Оборудование для подготовки сырьевых материалов
Основой технологического передела подготовки сырья является дробильное отделение, аналогичное дробильному отделе нию цементного производства. Особенностью дробильного отделения при производстве извести является наличие в дробильной установке многоярусных грохотов, разделяющих перед загрузкой в шахтную печь сырьевой материал на фракции до кусков заданных размеров. Питатель, щековую дробилку, транспортер и грохот дробильной уста новки выбирают с учетом прочностных характеристик перерабаты ваемого сырья и суммарной производительности шахтных печей.
Сырьевой материал после измельчения в щековой дробилке сорти руют на инерционных грохотах вибрационного действия (рис. 161). Грохот состоит из короба 1 в сборе, вибратора 2, электропривода 5,
307
Рис. 161. Инерционный грохот вибрационного действия
просеивающих поверхностей 4 и пружинных опор 3. Короб грохота является каркасом, на котором закреплены все основные узлы и детали, и состоит из двух бортовых стенок, жестко соединенных ме жду собой поперечными связями-балками. Просеивающие поверх ности выполнены в виде колосниковых решеток или сит, прикреплен ных с помощью хомутов к поперечным связям-балкам. Вибратор состоит из вала на подшипниковых узлах, закрепленных на нем де балансов (эксцентричных грузов) и шкива клиноременной передачи.
При вращении вала вибратора его дебалансы развивают центро бежную силу инерции, возбуждающую плоские круговые колебания короба. Материал при этом транспортируется по наклонной просеи вающейся поверхности колосников и сортируется. Куски материала
Т а б л и ц а |
61. Техническая характеристика вибрационных |
|
|
||
двухъярусных грохотов |
|
|
|
|
|
|
Показатель |
СМД-21 |
СМД-24 |
СМД-51 |
СМД-53 |
Размеры полезной площади сита, м: |
|
|
|
\ , |
|
|
|
|
|
||
длина |
|
1,5 |
1,75 |
1,75 |
1 |
ширина |
|
3,75 |
4,5 |
4,5 |
2,5 |
Размеры щели (ячейки), мм: |
|
. |
|
|
|
верхнего |
яруса: |
135 |
26 |
40 |
26 |
длина |
|
||||
ширина |
|
135 |
26 |
40 |
26 |
нижнего яруса: |
75 |
5 |
|
5 |
|
длина |
|
12 |
|||
ширина |
|
75 |
20 |
12 |
20 |
Амплитуда колебаний короба, мм |
4 |
4 |
3,7 |
9,5 |
|
Частота вращения вала вибратора, |
875 |
800 |
800 |
740 |
|
nfi/uuu |
|
|
|
|
|
U U / m i l п |
|
|
|
|
|
Угол наклона |
сит, ° |
До 30 |
До 30 |
10—30 |
|
Мощность электродвигателя, кВт |
17 |
13 |
10 |
5Д |
|
Производительность, м3/ч |
250 |
200 |
450 |
40 |
|
Размеры, м: |
|
|
|
|
|
длина |
|
4,9 |
5,28 |
5,1 |
3,2 |
ширина |
|
2,9 |
2,91 |
2,7 |
1,95 |
высота |
|
1,4 |
1,2 |
1,3 |
1,5 |
Масса, кг |
|
6G15 |
3800 |
3600 |
1650 |
со второй колосниковой решетки транспортируют на склад готового сырья, куски с первой решетки направляют на домол, а просыпь после второй нижней решетки удаляют для дальнейшего использо вания в побочном производстве (в качестве заполнителя, сырья в цементном производстве) или для обжига на известь во вращаю щейся печи.
Техническая характеристика серийно выпускаемых двухъярус ных грохотов, используемых при производстве извести, а также дру гих строительных материалов, приведена в табл. 61.
Изменения фракционного состава сортируемого материала до стигают путем изменения размера щели между колосниками просеи вающих сит, а производительность грохота регулируют углом их наклона к горизонту.
§ 116. Оборудование для загрузки материалов в печь
Фракционированное сырье из бункеров хранения с по мощью дозаторов загружают в ковш устройства подачи сырья в печь. Аналогично в печь поступает и твердое топливо.
Автоматический весовой дозатор (рис. 162) состоит из двух при емных бункеров 7 (для известняка и твердого топлива), двух те чек 6 и 13, двух лотковых питателей 5 и 14, весовой системы рычагов /, 2 и 4. Дозирующий бункер 11 с помощью тросов 10 ПОЦ-
Вид А
Рис. 163. Кинематическая схема авто матической работы загрузочного уст ройства
вешен к раме весовой изме рительной системы, которая, в свою очередь, подвешена на тросах 8 к бункерам 7
Дозатор работает следующим образом. Известняк из левого бункера 7 лотковым питателем 5 подается в дозирующий бун кер. По мере заполнения бун кера материалом измерительная весовая система 9 приближается к равновесию и, достигнув уста новленного значения, выклю чает электродвигатель лотко вого питателя 5.
Загрузку печи сырьем и топ ливом осуществляют последова тельно. Одновременно с отклю чением питателя 5 сырья вклю чается привод питателя 14, который из правого бункера 7 подает твердое топливо в бун кер 11. Когда общая масса сырья и топлива в дозирующем бункере достигнет заданного значения, измерительная си стема выключает питатель 14.
При возвращении в нижнее положение ковш 15 скипового подъ емника нажимает на рычаг 1, который через рычаги 2 и 4 открывает
затвор 12 дозирующего бункера, и материал |
по течке |
3 ссыпается |
в ковш. При движении ковша вверх система |
рычагов |
1, 2 и 4 под |
действием контргруза прочно закрывает затвор дозирующего бун кера. Командный аппарат включает лотковый питатель 5, и цикл до зирования шихты повторяется. К моменту возвращения ковша в ниж нее положение дозирующий бункер 11 вновь заполнен шихтой.
Загружаемое сырье в печь, работающую на жидком или газооб разном топливе, дозируется с помощью питателей. В данном случае предусматривают только один бункер для сырья. Конструкция пита теля принципиально не отличается от рассмотренной конструкции дозатора. Сырье питателем дозируется по установленному времени его работы.
Шахтная печь сырьем загружается с помощью специального'устройства, состоящего из скипового подъемника с электрической ле бедкой, поворотной чаши и двухклапанного затвора. Электрическая лебедка 1 (рис. 163) посредством троса и системы блоков транспорти