
1158
.pdf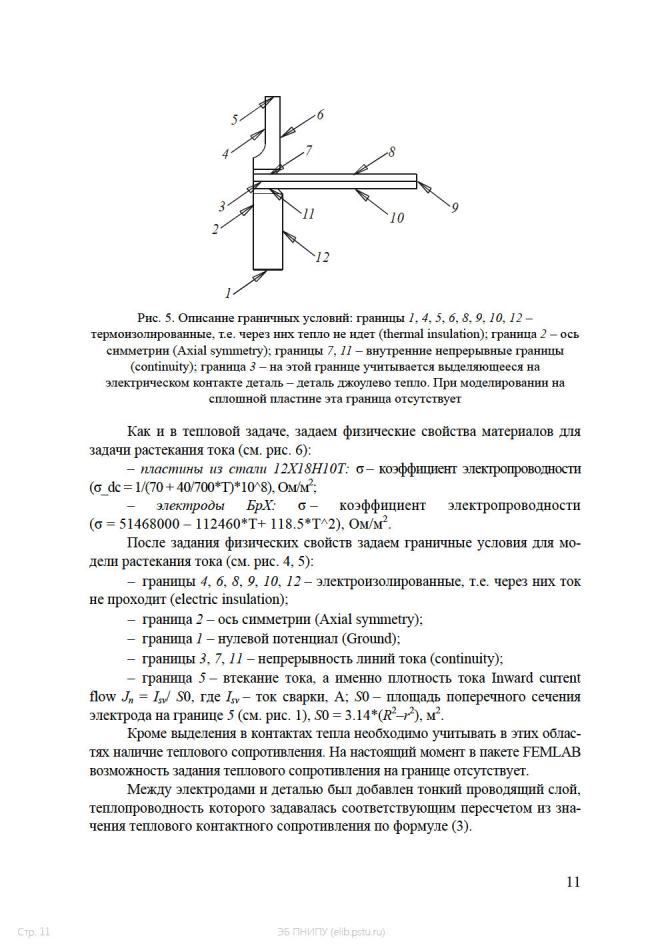
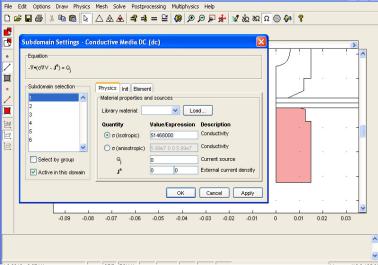
Рис. 6. Окно описания электрических свойств материала |
|
Конечная формула для записи в FEMLAB выглядит так: |
|
k =h_ed / Rt_ed , |
(3) |
где Rt_ed – тепловое электросопротивление электрод – деталь, Ом; h_ed – толщина тонкого проводящего слоя.
Помимо теплового сопротивления для точного построения математической модели необходим учет контактного электрического сопротивления [4, 5], для чего электропроводность проводящего слоя задаем из пересчета следую-
щих формул: R = ρSh и σ_ dc =1/ ρ. В итоге получаем следующее уравнение:
σ_dc = h / (SRed ) , |
(4) |
где ρ – удельное электросопротивление, Ом·м; σ_dc – электропроводность, Ом/м2; S – площадь поверхности проводящего слоя, м2.
Граничные условия слоя для тепловой задачи (рис. 7) выглядят следующим образом:
– границы 13 – неоднородный тепловой поток (heat flux discontinuity), где q0 = (Jz_dc^2 + Jr_dc^2) (3.14 0.005^2) R_ed / 2 .
12
Стр. 12 |
ЭБ ПНИПУ (elib.pstu.ru) |
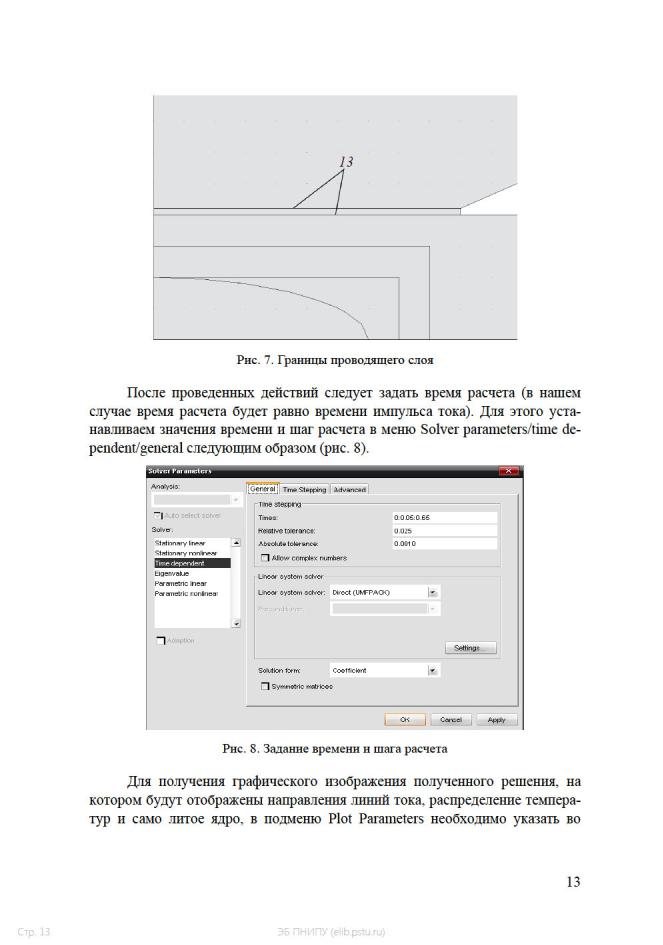
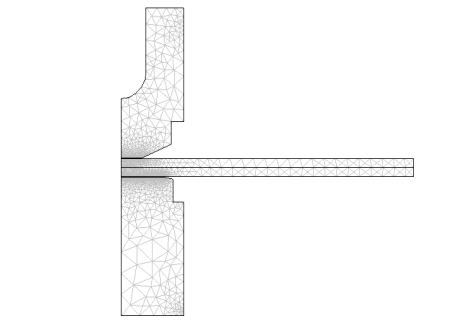
вкладках следующие параметры: Surface – Temperature, Streamline – Total current density, Contour – T*(1 – sign (T – Ts)) / 2 + T*(1 – sign (Tl – T)) / 2.
Завершающим этапом перед началом расчета является разбиение геометрии на сетку. Малые области автоматически разбиваются системой на более мелкую сетку (Mesh/Mesh Mode), при необходимости более точных расчетов в некоторых областях можно измельчать ее вручную (Mesh/Mesh Parameters). А именно – измельчаем в области плавления металла, т.е. в месте образования ядра (рис. 9).
Рис. 9. Нанесение сетки
Построенная по вышеприведенному алгоритму модель процесса контактной точечной сварки (КТС) дает графическое решение, на котором мы можем видеть литое ядро, распределение температур, направление линий тока (рис. 10). Данная модель позволяет получить размеры и форму литого ядра, близкие к экспериментальным в широком диапазоне режимов, исключая режимы, в которых ядро только начинает формироваться. Погрешность вычисления объема литого ядра составила не более 10 %.
Конечные результаты были внесены в таблицу, где указаны размеры ядер (диаметр dя и высота hя), полученных в результате физических экспериментов и в результате моделирования. Построен график зависимости размера диаметра литого ядра от величины пропускаемого тока (рис. 11).
14
Стр. 14 |
ЭБ ПНИПУ (elib.pstu.ru) |

Таким образом, построенная модель КТС с достаточной степенью точности воспроизводит реальный технологический процесс и может быть использована для анализа физических закономерностей и обоснованного выбора технологических режимов контактной сварки.
Список литературы
1.Ульрих Т.А. Математическое моделирование процесса контактной точечной сварки: дис. … канд. техн. наук; Перм. гос. техн. ун-т. – Пермь, 2000. – 124 с.
2.Ульрих Т.А., Колмогоров Г.Л., Ошивалов М.А. Анализ теплового
итермонапряженного состояния оснастки при контактной точечной сварке // Сварочное производство. – 2000. – № 3. – С. 19–23.
3.Ульрих Т.А., Колмогоров Г.Л., Ошивалов М.А. Термодеформационная модель контактной точечной сварки // Механика и технология материалов
иконструкций; Перм. гос. техн. ун-т. – Пермь, 1998. – С. 82–88.
4.Гуляев А.И. Технология и оборудование контактной сварки. – М.: Машиностроение, 1985. – 254 с.
5.Технология и оборудование контактной сварки / под ред. Б.Д. Орлова. – М.: Машиностроение, 1975. – 536 с.
Получено 10.06.2010
Стр. 16 |
ЭБ ПНИПУ (elib.pstu.ru) |
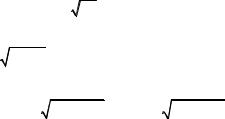
УДК 621.791.4
В.М. Язовских, В.В. Каратыш, В.Я. Беленький
Пермский государственный технический университет
ТЕПЛОВАЯ МОДЕЛЬ СВАРКИ В УГЛЕКИСЛОМ ГАЗЕ
Подробно описано построение математической модели сварки в среде углекислого газа, основанной на тепловой модели и статистической обработке экспериментальных данных, приведенных в работах Н.М. Новожилова и А.Г. Потапьевского. Приведенная математическая модель позволяет определять параметры зоны проплавления при сварке, рассчитывать термические циклы сварки, определять мгновенную скорость охлаждения в любой точке сварного соединения. Приведены некоторые листинги решений в пакете Mathcad.
Влияние отдельных параметров режима сварки на форму и размеры швов изучалось многими исследователями. Нами использовались экспериментальные данные, приведенные в работах Н.М. Новожилова и А.Г. Потапьевского [1–3]. Швы, выполненные в углекислом газе, имеют при прочих равных условиях большее отношение глубины проплавления к ширине шва по сравнению со швами, выполненными автоматической сваркой под слоем флюса. Для определения зоны проплавления при сварке в СО2 можно использовать комбинированную ММ, состоящую из нормально-распределенного точечного на поверхности и линейного по глубине источника [4].
|
k1qη t |
1 |
|
|
(x +V τ)2 + y2 |
|
||||
T (x, y, z,τ) = |
|
|
|
∫0 |
|
exp |
− |
|
|
× |
4cρ |
aπ |
3 |
τ+t0 |
4a(τ+t0 z ) |
||||||
|
|
|
|
|
|
∞ |
|
1 |
|
|
(z + 2nL) |
2 |
|
k2qη |
t |
1 |
|
|
(x +V τ) |
2 |
+ y |
2 |
|
|||||||
× ∑ |
|
|
exp − |
|
dτ+ |
|
|
exp |
− |
|
|
|
× (1) |
|||||||||||
|
τ+t0 z |
|
|
|
|
|
∫0 τ+t0 |
4a(τ+t0 ) |
|
|||||||||||||||
n=−∞ |
|
|
4a(τ+t0 z ) |
|
8λhπ |
|
|
|
|
|
||||||||||||||
∞ |
z + h + 2nL |
z − h + 2nL |
|
|
|
|
|
|
|
|
||||||||||||||
× ∑ |
erf |
|
|
|
|
−erf |
|
|
|
|
|
|
|
dτ, |
|
|
|
|
|
|
|
|
||
2 |
a(τ+t |
|
|
|
a(τ+t |
|
) |
|
|
|
|
|
|
|
|
|
||||||||
n=−∞ |
|
|
0z |
) |
2 |
0z |
|
|
|
|
|
|
|
|
|
|
||||||||
|
|
|
|
|
|
|
|
|
|
|
|
|
|
|
|
|
|
|
|
|
где t0 характеризует распределенность источника по диаметру пятна нагрева; t0z характеризует распределенность источника по глубине; h характеризует условную величину внедрения сварочной дуги в свариваемый металл; k1 и k2 – коэффициенты распределения мощности дуги между точечным и линейным источниками соответственно (k2 = 1 – k1).
Таким образом, меняя четыре указанные параметра, можно добиться максимального приближения расчетных значений глубины проплавления и ширины шва к экспериментальным.
17
Стр. 17 |
ЭБ ПНИПУ (elib.pstu.ru) |
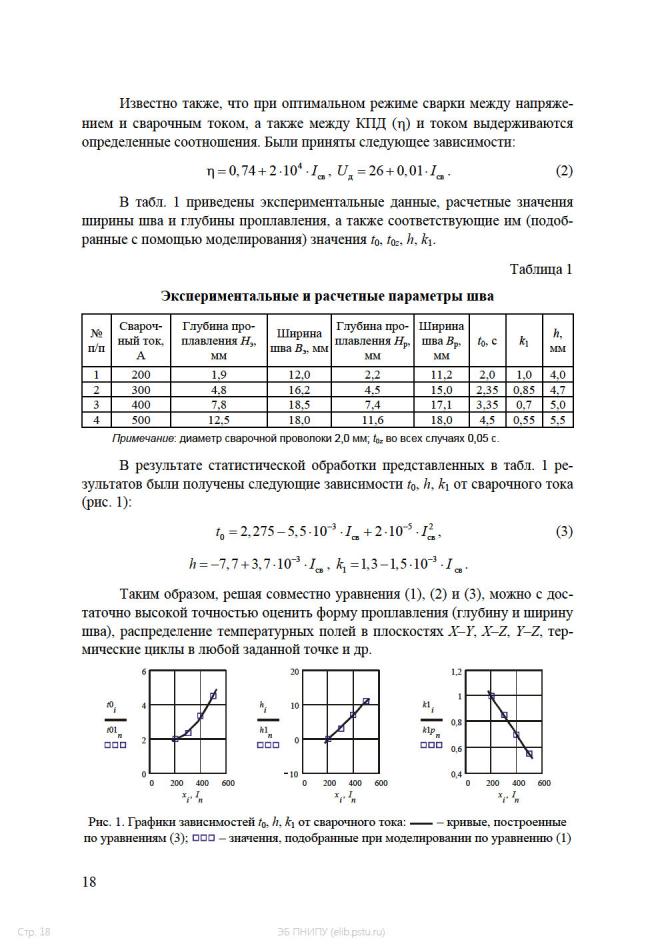
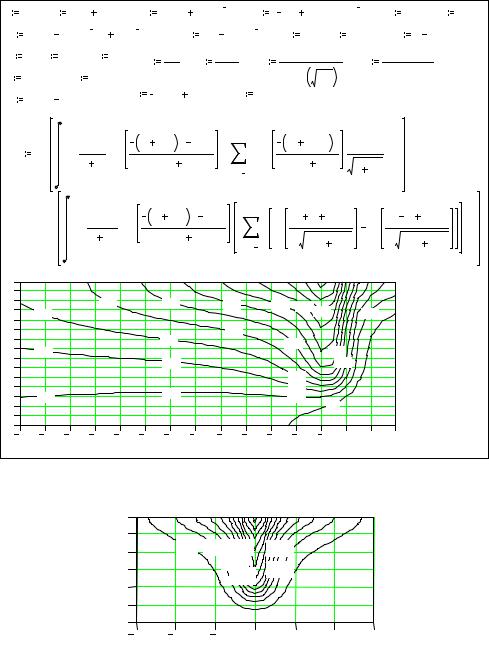
|
|
На рис. 2–3 приведен полный листинг решения уравнения (1) с исполь- |
||||||||||||||||||||||||||||||||||
зованием зависимостей (2) и (3) и показан характер распределения темпера- |
||||||||||||||||||||||||||||||||||||
тур в плоскости X–Z, Y–Z. |
|
|
|
|
|
|
|
|
|
|
|
|
|
|
|
|
|
|
|
|
|
|
|
|||||||||||||
I |
|
500 |
U |
24.7 |
|
0.013 |
. |
I |
η |
0.727 |
|
2.3 |
. |
10 |
4. |
I |
h |
( 7.7 |
|
. . |
10 |
3 |
t0z |
|
0.05 |
q |
. |
I |
||||||||
|
|
|
|
|
|
0.037 I) |
|
|
U |
|||||||||||||||||||||||||||
t0 |
|
2.275 |
|
5.5.10 3.I |
2.10 5.I2 |
|
k1 |
1.3 |
1.5.10 3.I |
|
t |
50 |
L |
|
0.015 |
k2 |
1 |
k1 |
|
|
||||||||||||||||
λ |
|
30 |
c |
|
703 |
ρ |
|
7620 |
|
a |
|
λ |
|
V |
|
18 |
|
F1 |
|
|
q.η.k1 |
|
|
|
F2 |
|
|
q.η.k2 |
|
|
|
|||||
k 0 .. 15 |
|
i 0 ..30 |
|
|
|
|
c.ρ |
|
|
3600 |
4.c.ρ. |
|
3 |
|
|
|
8.c.ρ.π .a.h |
|
|
|||||||||||||||||
|
|
xi |
|
0.025 |
|
0.001.i |
|
y |
0 |
π .a |
|
|
|
|
|
|
|
|
|
|
||||||||||||||||
z |
|
0.015 |
|
0.001.k |
|
|
|
|
|
|
|
|
|
|
|
|
|
|
|
|
|
|
|
|
|
|||||||||||
k |
|
|
|
|
|
|
|
|
|
|
|
|
|
|
|
|
|
|
|
|
|
|
|
|
|
|
|
|
|
|
|
|
|
|
|
|
|
|
|
|
|
t |
|
|
|
|
|
|
V.τ 2 |
|
(y)2 |
|
3 |
|
|
|
|
|
2 |
|
|
|
|
|
|
|
|
|
|
||||
|
|
F1. |
|
|
1 |
|
.exp |
|
x |
|
|
|
|
z |
2.n.L |
|
|
1 |
|
|
|
|
|
|
|
|||||||||||
T |
|
|
τ |
|
|
i |
|
|
t0) |
|
. |
|
|
exp |
|
k |
|
. |
|
|
dτ ... |
|
|
|
||||||||||||
i,k |
|
|
|
t0 |
|
|
|
|
4.a.(τ |
|
n = 3 |
|
4 |
.a.(τ |
t0z) |
|
τ |
t0z |
|
|
|
|
|
|||||||||||||
|
|
|
|
|
|
|
|
|
|
|
|
|
|
|
|
|
|
|
|
|
|
|
|
|
|
|
|
|
|
|||||||
|
|
|
|
|
0 |
|
|
|
|
|
|
|
|
|
|
|
|
|
|
|
|
|
|
|
|
|
|
|
|
|
|
|
|
|||
|
|
|
|
|
|
|
|
|
|
|
|
|
|
|
|
|
|
|
|
|
|
|
|
|
|
|
|
|
|
|
|
|
|
|
|
|
|
|
|
|
|
t |
|
|
|
|
|
|
|
|
|
|
2 (y)2 |
|
5 |
|
|
|
|
|
|
|
|
|
|
|
|
|
|
|
|
||
|
|
|
|
. |
|
|
1 . |
|
|
|
x |
|
V.τ |
. |
|
|
|
z |
h 2.n.L |
|
|
z |
|
h 2.n.L |
|
|
||||||||||
|
|
+ F2 |
|
|
|
|
|
i |
|
|
|
|
|
|
|
erf |
|
k |
|
|
|
|
|
|
k |
|
|
dτ |
||||||||
|
|
|
|
τ |
t0z exp |
|
4.a.(τ |
|
t0z) |
|
|
n = |
5 |
|
2. a.(τ |
t0z) |
|
erf |
2. a.(τ |
t0z) |
||||||||||||||||
|
|
|
|
|
0 |
|
|
|
|
|
|
|
|
|
|
|
|
|
|
|
|
|
|
|
|
|
|
|
|
|
|
|
|
|
||
|
|
|
|
|
|
|
|
|
|
|
|
|
|
|
|
|
|
|
|
|
|
|
|
|
|
|
|
|
|
|
|
|
|
|
|
|
15 |
|
|
|
|
|
|
|
|
|
|
|
|
|
|
|
|
|
|
|
|
|
|
|
|
|
|
|
|
|
|
|
|
|
|
|
|
14 |
|
|
|
|
|
|
|
|
|
|
|
|
|
|
|
|
|
|
|
|
|
|
|
|
|
|
|
|
|
|
|
|
|
|
|
|
13 |
|
|
|
|
|
|
2500 |
|
|
|
|
|
3000 |
|
|
|
3500 |
|
4000 |
4500 |
|
|
|
|
|
|
|
|
|
|
|
|||||
12 |
|
2000 |
|
|
|
|
|
|
|
|
|
|
|
|
|
|
|
|
|
|
|
|
|
5000 |
|
|
1000 |
|
|
|
|
|
|
|||
11 |
|
|
|
|
|
|
|
|
|
|
|
|
|
|
|
|
|
|
|
|
|
|
|
|
|
|
|
|
|
|
|
|
|
|
|
|
10 |
|
|
|
|
|
|
|
|
|
|
|
|
|
|
|
|
|
2500 |
|
|
|
|
|
|
|
|
|
|
|
|
|
|
|
|
||
9 |
|
|
|
|
|
|
|
|
|
|
|
|
2000 |
|
|
|
|
|
|
|
3000 |
|
|
|
|
|
|
|
|
|
|
|
|
|||
8 |
|
1500 |
|
|
|
|
|
|
|
|
|
|
|
|
|
|
|
|
|
|
|
|
|
3500 |
|
|
|
|
|
|
|
|
|
|
||
7 |
|
|
|
|
|
|
|
|
|
|
|
|
|
1500 |
|
|
|
|
|
|
|
|
|
|
|
2500 |
|
|
|
|
|
|
|
|
||
6 |
|
|
|
|
|
|
|
|
|
|
|
|
|
|
|
|
|
|
|
|
|
|
|
|
|
|
|
|
|
|
|
|
||||
|
|
|
|
|
|
|
|
|
|
|
|
|
|
|
|
|
|
|
|
|
|
2000 |
|
|
|
|
|
|
|
|
|
|
|
|
||
5 |
|
|
|
|
|
|
|
|
|
|
|
|
|
|
|
|
|
|
|
|
|
|
|
|
|
|
|
|
|
|
|
|
|
|
||
4 |
|
1000 |
|
|
|
|
|
|
|
|
|
|
1000 |
|
|
|
|
|
|
|
|
1500 |
|
|
|
|
|
|
|
|
|
|
|
|
||
3 |
|
|
|
|
|
|
|
|
|
|
|
|
|
|
|
|
|
|
|
1000 |
|
|
|
|
|
|
|
|
|
|
|
|
||||
|
|
|
|
|
|
|
|
|
|
|
|
|
|
|
|
|
|
|
|
500 |
|
|
|
|
|
|
|
|
|
|
||||||
2 |
|
|
|
|
|
|
|
|
|
|
|
|
|
|
|
|
|
|
|
|
|
|
|
|
|
|
|
|
|
|
|
|
|
|
||
1 |
|
|
|
|
|
|
|
|
|
|
|
|
|
|
|
|
|
|
|
|
|
|
|
|
|
|
|
|
|
|
|
|
|
|
|
|
0 |
25 |
23 |
|
21 |
19 |
17 |
|
15 |
|
13 |
|
11 |
|
9 |
|
7 |
|
5 |
|
3 |
1 |
1 |
|
|
3 |
|
5 |
|
|
|
|
|||||
|
|
|
|
|
|
|
|
|
|
|
|
|
|
|
|
|||||||||||||||||||||
T |
|
|
|
|
|
|
|
|
|
|
|
|
|
|
|
|
|
|
|
|
|
|
|
|
|
|
|
|
|
|
|
|
|
|
|
|
|
|
|
Рис. 2. Листинг решения по уравнению (1) и зависимостям (2) и (3); |
|
|
|||||||||||||||||||||||||||||||
|
|
график показывает распределение температур в плоскости X–Z при y = 0 |
|
|
15 |
|
|
|
|
|
|
12.5 |
500 |
10002500 |
|
2000 |
|
|
10 |
|
|
|
|||
|
1500 |
|
1500 |
|
|
|
7.5 |
|
|
|
|
||
|
2000 |
|
|
|
||
5 |
|
|
|
1000 |
|
|
|
|
|
500 |
|
|
|
2.5 |
|
|
|
|
|
|
|
|
|
|
|
|
|
0 |
10 |
5 |
0 |
5 |
10 |
15 |
15 |
T
Рис. 3. Распределение температур в плоскости Y–Z
19
Стр. 19 |
ЭБ ПНИПУ (elib.pstu.ru) |
Наибольший практический интерес представляет сварка в углекислом газе проволокой диаметром 1,2 мм. В табл. 2 представлены экспериментальные данные, взятые из работ А.Г. Потапьевского, а также подобранные значения t0, h, k1. Для подбора применялось уравнение (1).
|
|
|
|
|
|
|
|
|
|
|
|
Таблица 2 |
|
|
|
Экспериментальные и теоретические параметры шва |
|
||||||||||
|
|
|
|
|
|
|
|
|
|
|
|
|
|
|
|
Свароч- |
Глубина |
|
Ширина |
Глубина |
Ширина |
|
|
|
|
||
№ |
|
проплав- |
|
|
|
|
|
||||||
п/п |
|
ный ток, |
ления Hэ, |
|
шва Bэ, |
проплавле- |
шва Bр, мм |
|
t0, c |
k1 |
h, мм |
||
|
|
А |
мм |
|
мм |
ния Hр, мм |
|
|
|
|
|
||
|
|
|
|
|
|
|
|
|
|
|
|
|
|
|
|
|
|
|
|
|
|
|
|
|
|
|
|
1 |
|
120 |
2,1 |
|
7,0 |
2,3 |
|
6,8 |
|
0,3 |
1,0 |
0 |
|
2 |
|
145 |
2,8 |
|
7,6 |
2,8 |
|
7,5 |
|
0,6 |
0,8 |
1,0 |
|
3 |
|
170 |
3,5 |
|
8,1 |
3,6 |
|
8,1 |
|
0,85 |
0,6 |
2,0 |
|
4 |
|
200 |
4,6 |
|
9,0 |
4,6 |
|
9,0 |
|
0,92 |
0,4 |
3,0 |
|
5 |
|
230 |
5,8 |
|
10,2 |
5,8 |
|
9,9 |
|
0,99 |
0,35 |
4,5 |
|
|
Примечание: диаметр сварочной проволоки 1,2 мм; t0z во всех случаях 0,025 с. |
|
|||||||||||
|
|
В результате статистической обработки приведенных в табл. 2 данных |
|||||||||||
получены следующие зависимости t0, h, k1 от величины сварочного тока: |
|||||||||||||
|
|
|
t0 = −2,067 + 0,027 Iсв −5,944 10−5 Iсв2 |
, |
|
(4) |
|||||||
|
|
|
h = −4,827 10−3 + 4,004 10−5 Iсв , |
|
|
|
|||||||
|
|
|
k |
= 2,804 −0,02 I |
св |
+3,817 10−5 I 2 . |
|
|
|
||||
|
|
|
1 |
|
|
|
|
св |
|
|
|
После статистической обработки экспериментальных данных, взятых из работ А.Г. Потапьевского и Н.М. Новожилова по оптимальным параметрам режима сварки, получены зависимости напряжения на дуге Uд и значений КПД (η) от величины сварочного тока:
Uд =19,358 −0,014 Iсв +1,397 10−4 Iсв2 , |
(5) |
η= 0,7 + 2,3 10−4 Iсв .
На рис. 4 показаны кривые зависимости t0, h, k1 и Uд от сварочного тока, построенные по уравнениям (4) и (5).
20
Стр. 20 |
ЭБ ПНИПУ (elib.pstu.ru) |