
2943
.pdf
621.7
Т462
СИБИРСКИЙ ГОСУДАРСТВЕННЫЙ УНИВЕРСИТЕТ ПУТЕЙ СООБЩЕНИЯ
Л.Б. Тихомирова, К.А. Медведев
ОБРАБОТКА МЕТАЛЛОВ ДАВЛЕНИЕМ: РАЗРАБОТКА
ТЕХНОЛОГИЧЕСКОГО ПРОЦЕССА КОВКИ
Методические указания к выполнению лабораторной работы
Новосибирск
2015
1
УДК 621.735
Т462
Ти х о м и р о в а Л . Б . , М ед в ед е в К . А . Обработка металлов давлением: разработка технологического процесса ковки: Метод.
указ. к выполнению лабораторной работы. – Новосибирск: Изд-во СГУПСа, 2015. – 16 с.
Излагается последовательность разработки технологического процесса ковки, методика выбора и расчета режимов оборудования, проектирование чертежа поковки, заготовки.
Предназначены для выполнения лабораторной работы по дисциплине «Технология конструкционных материалов», «Основы технологии производства», «Материаловедение и технологии конструкционных материалов» для студентов дневной и заочной форм обучения по направлениям подготовки 23.03.03 «Эксплуатация транс- портно-технологических машин и комплексов», 27.03.01 «Стандартизация и метрология», 20.03.01 «Техносферная безопасность» и специальности 23.05.01 «Наземные транспортно-технологические средства».
Рассмотрены и рекомендованы к изданию на заседании кафедры «Технология траспортного машиностроения и эксплуатация машин».
О т в е т с т в е н н ы й р е д а к т о р
канд. техн. наук, доц. С.В. Щелоков
Р е ц е н з е н т
канд. техн. наук, доц. кафедры «Материаловедение в машиностроении» ФГБОУ ВПО «Новосибирский государственный технический университет»
А.В. Плохов
©Сибирский государственный университет путей сообщения, 2015
©Тихомирова Л.Б., Медведев К.А., 2015
2
Введение
Свободной ковкой называется обработка металлов давлением с помощью специального инструмента – бойков, один из которых (верхний) крепится к подвижному органу кузнечной машины (бабе молота или ползуну пресса), а второй (нижний) закрепляется на шаботе молота или столе пресса. Верхний боек совершает воз- ратно-поступательные движения, а нижний неподвижен.
Бойки – это закрепляемый инструмент. Кроме них используется вспомогательный инструмент (топоры, раскатки, прошивни, обжимки и т.д.).
Основными операциями свободной ковки являются: протяжка, осадка, высадка, раскатка, рубка, гибка, кручение [3, 4].
Кованные заготовки имеет смысл использовать для ответственных деталей, испытывающих большие знакопеременные и динамические нагрузки и имеющих сравнительно простую форму с плоскими или цилиндрическими поверхностями (сплошные или с одним цилиндрическим отверстием, бруски квадратные и прямоугольные, диски, валы, оси ступенчатые, кольца, втулки и цилиндры).
Ковка находит применение в машиностроении, в ремонтномеханических цехах при единичном и мелкосерийном производстве поковок. Иногда применяется и в серийном производстве, и даже массовом (например, вагонные оси). Масса поковок может быть от доли килограмма до 200 т.
Для получения поковок в качестве исходных заготовок применяются: для крупных поковок (от 300 кг и выше) – слитки; для мелких и средних поковок – сталь горячекатаная круглая, квадратная, болванка обжатая (блюм) и другие профили сортового проката. В зависимости от массы поковки ковка может производиться на ковочных молотах и гидравлических прессах (при массе более 1 т).
Подготовка слитков к ковке заключается в удалении с поверхности слитка обнаруженных дефектов.
3
При подготовке проката к ковке с поверхности удаляют имеющиеся закаты, плены, волосовины и другие внешние дефекты путем вырубки пневматическими зубилами или заточкой абразивными кругами. Далее пруток может подвергаться разделке на мерные заготовки, которую выполняют резкой на сортовых ножницах и прессах, кислородной резкой, резкой на пилах. Резка на сортовых ножницах и прессах является самым высокопроизводительным способом, так как не вызывает дополнительных потерь на прорезку, но имеет недостаток – искажение формы торцевой части заготовки.
При разработке технологического процесса свободной ковки необходимо:
–составить чертеж поковки;
–рассчитать массу поковки;
–определить массу и размеры заготовки;
–назначить температурный интервал ковки, режим нагрева заготовки и охлаждения поковки;
–определить виды, число и последовательность кузнечных операций, инструмента, приспособлений;
–выбрать необходимое оборудование.
Порядок выполнения работы
1.Сделать эскиз выданной детали.
2.Назначить припуски, допуски, напуски.
3.Выполнить эскиз поковки.
4.Найти объем и массу детали.
5.Найти объем и массу поковки.
6.Определить массу и объем заготовки.
7.Определить размеры заготовки. Выполнить эскиз заго-
товки.
8.Определить коэффициент использования металла и коэффициент выхода годного металла.
9.Указать температуру нагрева при ковке, продолжительность нагрева, время охлаждения поковки.
10.Назначить основные операции ковки.
11.Выбрать оборудование, инструмент и приспособления для операций ковки.
4
1. Разработка чертежа поковки
Чертеж поковки составляется на основании чертежа готовой детали с учетом припусков на механическую обработку, напусков на упрощение формы поковки и допусков на точность ковки.
1.1. Припуски, допуски, напуски
Припуск – слой металла на поверхности поковки, подлежащий удалению механической обработкой для получения готовой детали требуемых размеров и чистоты поверхности. Размеры детали увеличивают на величину припусков в местах, которые подлежат механической обработке (знак « »).
Допуск – допустимое отклонение размеров поковки, обусловленное невозможностью ее изготовления с абсолютно точными размерами. Допуск равен разности между наибольшим и наименьшим предельными размерами поковки. Допуск назначается на все размеры поковки.
Напуск – дополнительный объем металла, добавляемый к поковке сверх припуска для упрощения ее формы, что облегчает процесс ковки. Напуски удаляют последующей механической обработкой. Поковки должны быть простыми, очерченными плоскостями и цилиндрическими поверхностями. Следует избегать в поковках клиновидных и конических форм, а также пересечения цилиндрических поверхностей между собой и с призматическими поверхностями.
Численные значения величины припусков, допусков и напусков назначают по соответствующим таблицами стандартов. Для поковок большого веса (до 130 т), изготавливаемых свободной ковкой из слитков, на прессах используют ГОСТ 7062–90 [1].
Средние и мелкие поковки массой до 700 кг куют из сортового проката на паровоздушных и пневматических молотах, определяя припуски и допуски согласно ГОСТ 7829–70 [2].
Пример назначения припусков и допусков на поковки сплошного круглого сечения показан на рис. 1 и в табл. 1, 2.
5
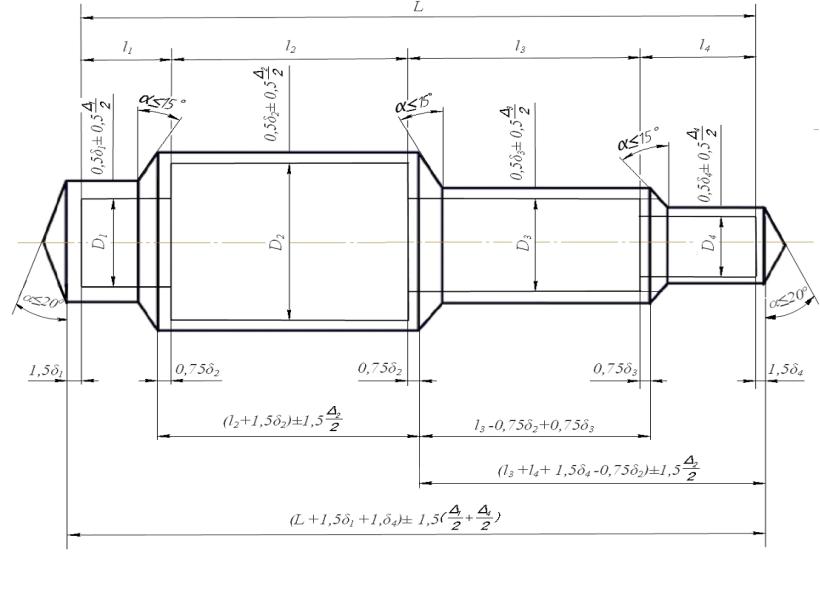
6
Рис. 1. Схема назначения основных припусков и допусков для вала, все поверхности которого механически обрабатываются
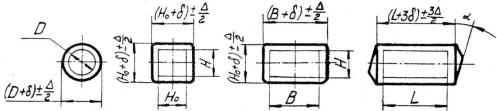
Припуски δ и допуски ±
2
Таблица 1
на поковки круглого сечения,
изготавливаемые свободной ковкой (ГОСТ 7829–70) на молотах, мм
Длина |
|
|
δ и ± |
|
при диаметре D |
|
|
|||
|
|
2 |
|
|
||||||
детали |
|
|
|
|
|
|
|
|
|
|
70–90 |
90–120 |
|
120–160 |
160–200 |
|
200–220 |
220–250 |
|||
|
|
|
||||||||
До 250 |
7 ± 2 |
8 ± 3 |
|
9 ± 3 |
11 ± 3 |
|
12 ± 4 |
15 ± 5 |
||
251–500 |
8 ± 2 |
9 ± 3 |
|
10 ± 3 |
11 ± 3 |
|
13 ± 4 |
15 ± 5 |
Припуски δ и допуски ±
2
Таблица 2
на поковки различных сечений,
изготавливаемые на прессах (ГОСТ 7062–90), мм
|
|
|
|
|
|
|
|
|
|
|
|
|
|
мм |
|
|
|
|
δ и ± |
|
при размерах D, H0, B |
|
|
|
|||
|
|
|
|
2 |
|
|
|
||||||
, |
|
|
|
|
|
|
|
|
|
|
|
|
|
Длина детали |
|
|
|
|
|
|
|
|
|
|
|
|
|
201–224 |
225–250 |
251–280 |
281–315 |
|
316–355 |
|
356–400 |
401–450 |
451–500 |
501–560 |
561–630 |
631–710 |
|
|
|
|
|
|
|
|
|
|
|
|
|
|
|
1000 |
16 ± 6 |
17 ± 6 |
18 ± 6 |
19 ± 7 |
|
20 ± 7 |
21 ± 7 |
22 ± 8 |
23 ± 8 |
24 ± 8 |
25 ± 9 |
26 ± 9 |
|
До |
|
|
|
|
|
|
|
|
|
|
|
|
|
|
|
|
|
|
|
|
|
|
|
|
|
|
|
–1250 |
17 ± 6 |
18 ± 6 |
19 ± 7 |
20 ± 7 |
|
21 ± 7 |
22 ± 8 |
23 ± 8 |
24 ± 8 |
25 ± 9 |
26 ± 9 |
27 ± 9 |
|
1001 |
|
|
|
|
|
|
|
|
|
|
|
|
|
|
|
|
|
|
|
|
|
|
|
|
|
|
|
–1600 |
18 ± 6 |
19 ± 7 |
20 ± 7 |
21 ± 7 |
|
22 ± 8 |
23 ± 8 |
24 ± 8 |
25 ± 9 |
26 ± 9 |
27 ± 9 |
28 ± 10 |
|
1251 |
|
|
|
|
|
|
|
|
|
|
|
|
|
|
|
|
|
|
|
|
|
|
|
|
|
|
|
–2000 |
19 ± 7 |
20 ± 7 |
21 ± 7 |
22 ± 8 |
|
23 ± 8 |
24 ± 8 |
25 ± 9 |
26 ± 9 |
27 ± 9 |
28 ± 10 |
29 ± 10 |
|
1601 |
|
|
|
|
|
|
|
|
|
|
|
|
|
|
|
|
|
|
|
|
|
|
|
|
|
|
|
7
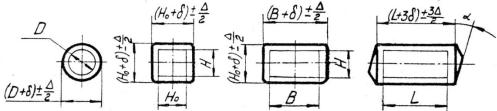
Окончание табл. 2
|
|
|
|
|
|
|
|
|
|
|
|
|
|
|
деталиДлина |
|
|
|
|
δ и ± |
|
при размерах D, H0, B |
|
|
|
||||
224–201 |
250–225 |
280–251 |
315–281 |
2 |
560–501 |
630–561 |
710–631 |
|||||||
|
355–316 |
400–356 |
450–401 |
500–451 |
||||||||||
|
|
|
|
|
|
|
|
|
|
|
|
|
||
|
|
|
|
|
|
|
|
|
|
|
|
|
||
–2500 |
20 ± 7 |
21 ± 7 |
22 ± 8 |
23 ± 8 |
|
24 ± 8 |
25 ± 9 |
26 ± 9 |
27 ± 9 |
28 ± 10 |
29 ± 10 |
30 ± 10 |
||
2001 |
|
|
|
|
|
|
|
|
|
|
|
|
|
|
|
|
|
|
|
|
|
|
|
|
|
|
|
||
–3150 |
21 ± 7 |
22 ± 8 |
23 ± 8 |
24 ± 8 |
|
25 ± 9 |
26 ± 9 |
27 ± 9 |
28 ± 10 |
29 ± 10 |
30 ± 10 |
31 ± 10 |
||
2501 |
|
|
|
|
|
|
|
|
|
|
|
|
|
|
|
|
|
|
|
|
|
|
|
|
|
|
|
|
|
4000 |
22 ± 8 |
23 ± 8 |
24 ± 8 |
25 ± 9 |
|
26 ± 9 |
27 ± 9 |
28 ± 10 |
29 ± 10 |
30 ± 10 |
31 ± 11 |
31 ± 11 |
||
3151– |
|
|||||||||||||
|
|
|
|
|
|
|
|
|
|
|
|
|
||
|
|
|
|
|
|
|
|
|
|
|
|
|
|
Если поковка имеет выступы и впадины, то назначаются дополнительные припуски на диаметры всех сечений, кроме наибольшего. Величина дополнительных припусков зависит от разницы основных (наибольшего сечения) и рассматриваемых (табл. 3). Припуски и допуски на поковки в форме дисков приведены в табл. 4.
Таблица 3
Дополнительные припуски на диаметры для поковок с уступами
Разность диаметров |
До 30 |
30–50 |
50–80 |
80–140 |
140–180 |
180–220 |
220–250 |
|
|
|
|
|
|
|
|
Дополнительный |
|
|
|
|
|
|
|
припуск на диаметр, |
2 |
3 |
4 |
5 |
7 |
8 |
9 |
мм |
|
|
|
|
|
|
|
8
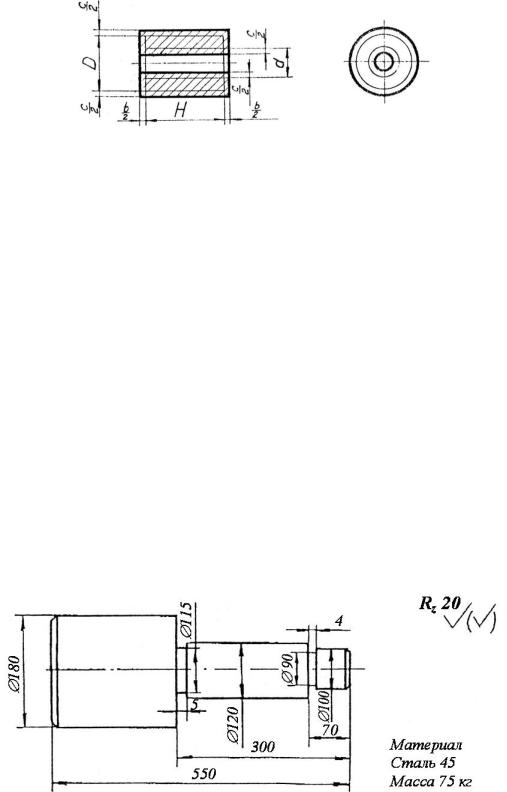
Таблица 4
Припуски и допуски на поковки типа дисков (при H ≤ D и d ≤ 0,5D), изготавливаемые на молотах (ГОСТ 7829–70), мм
|
|
|
|
|
|
|
|
|
Высота |
Диаметр |
|
|
Припуски b, c и допуски |
|
|
||
на высоту |
на диа- |
|
на диаметр d при разности D–d |
|||||
детали Н |
детали D |
|
||||||
H |
метр D |
до 50 |
|
51–130 |
131–250 |
251–400 |
||
|
|
|
||||||
|
60–250 |
8 ± 2 |
11 ± 3 |
14 ± 3 |
|
15 ± 3 |
– |
– |
До 50 |
251–360 |
9 ± 2 |
14 ± 5 |
17 ± 5 |
|
18 ± 5 |
19 ± 5 |
– |
361–500 |
10 ± 3 |
16 ± 7 |
19 ± 7 |
|
20 ± 7 |
21 ± 7 |
– |
|
|
|
|||||||
|
501–800 |
12 ± 5 |
19 ± 9 |
22 ± 9 |
|
23 ± 9 |
24 ± 9 |
27 ± 9 |
|
60–250 |
9 ± 2 |
12 ± 3 |
15 ± 3 |
|
16 ± 3 |
– |
– |
51–80 |
251–360 |
11 ± 3 |
16 ± 5 |
19 ± 5 |
|
20 ± 5 |
21 ± 5 |
– |
361–500 |
12 ± 4 |
18 ± 7 |
21 ± 7 |
|
22 ± 7 |
23 ± 7 |
– |
|
|
|
|||||||
|
501–600 |
14 ± 5 |
21 ± 9 |
24 ± 9 |
|
26 ± 9 |
26 ± 9 |
27 ± 8 |
|
61–250 |
11 ± 3 |
14 ± 4 |
17 ± 4 |
|
18 ± 4 |
– |
– |
81–120 |
251–600 |
13 ± 5 |
17 ± 5 |
20 ± 5 |
|
21 ± 5 |
22 ± 5 |
– |
|
361–800 |
14 ± 5 |
19 ± 7 |
22 ± 7 |
|
23 ± 7 |
24 ± 7 |
– |
1.2. Последовательность составления чертежа поковки
Тонкой сплошной линией выполняют эскиз готовой детали. На контур детали более толстой сплошной линией наносят эскиз поковки с учетом припусков, допусков, напусков. На нем проставляют все размеры.
Номинальные размеры детали проставляют в скобках под размерной линией, а номинальные размеры поковки с допусками – над ней. Типовое оформление эскиза детали и поковки вала показано на рис. 2, 3.
Рис. 2. Эскиз детали вала
9

Рис. 3. Эскиз поковки вала
2. Расчет объема и массы поковки
Объем поковки определяется как сумма объемов отдельных ее частей. Это должны быть простые геометрические фигуры. Расчет ведется по номинальным поковочным размерам. Умножение объема поковки на плотность металла дает массу поковки.
3. Определение массы и размеров заготовки из проката
Масса заготовки равна: |
|
mз = mп + mу + mобс + mвыд, |
(1) |
где mз – масса заготовки; mп – масса поковки; mу – масса отхода на угар (2 % от массы нагреваемого металла под ковку); mобс – масса отхода на обсечки (2,5 % от массы нагреваемого под ковку металла); mвыд – масса выдры (подсчитывается по ее размерам).
Объем металла при прошивке (выдра) составит:
V KH |
d |
2 |
(2) |
2 |
, |
||
|
|
|
где К – коэффициент, равный 0,2 при прошивке с кантовкой сплошными прошивнями и 0,7 при прошивке с подкладными кольцами; H – высота поковки; d – диаметр отверстия.
Определив массу заготовки для поковки и разделив ее на плотность материала, рассчитывают объем заготовки. Зная массу готовой детали, можно найти коэффициент использования металла Ки и коэффициент выхода годного металла Кв:
10