
Справочник по пайке
..pdfРис. 6. Виды покрытий и способы их нанесения
Наиболее широко применяют лужение изделий натиранием и погружением. В неко торых случаях рекомендуется метод реактив ного лужения. Горячее покрытие погружени ем изделий в жидкий припой можно произво дить через слой расплавленного флюса или окунанием в жидкий флюс, а затем в ванну с расплавленным припоем (рис. 7). Излишки незастывшего припоя удаляют вибрацией, обдувкой сжатым воздухом, центрифугирова нием, механической вращающейся щеткой (1400 об/мин), имеющей поступательное дви жение (скорость 2 3 м/с), или погружением в ванну с флюсом.
Для получения качественного лужения необходимо обеспечивать удаление окислов с поверхности лудильной ванны, для этого на поверхности ванны создают защитный слой
Рис. 7. Лужение погружением:
1 - тигель; 2 - расплавленный припой; 3 - детали, подвергающиеся лужению
Рис. 8. Схема лужения трубок радиатора:
/ - волна припоя; 2 - трубка радиатора; 3 - насос; 4 - ванна с припоем; 5 - сжатый воздух
флюса или графитового порошка, которые надо периодически возобновлять. Схема лужения трубок радиатора показана на рис. 8. Чтобы припой в процессе лужения не попадал внутрь трубок, последние перед подачей под прием ные ролики заглушают.
Для лужения относительно небольших деталей, не имеющих внутренних полостей, пользуются лужением через слой флюса в спе циальных ваннах (рис. 9). Скорость погруже ния должна быть такой, чтобы деталь, проходя флюс-гпС12, могла нагреваться до температу ры, при которой не происходит разбрызгива ния олова. Температура в ванне должна быть постоянной, так как ее повышение приводит к увеличению угара припоя и снижению качест ва лужения, а понижение затрудняет условия лужения и увеличивает расход припоя за счет наплывов на луженой поверхности.
Толщина покрытия влияет на паяемость луженых изделий. Покрытие толщиной менее 2,5 мкм будет иметь удовлетворительную пая емость, если пайка производится немедленно после обработки поверхности. Считается, что примерно такая же толщина покрытия доста точна для пайки при небольшом сроке хране ния. При продолжительном хранении толщину покрытия берут до 30 мкм.
Гальванические покрытия наносят в ста ционарных ваннах, в конвейерных установках или во вращающихся барабанах. Этот метод применим для всех сталей, медных сплавов, никелевых сплавов, для цинковых отливок под давлением и алюминия. Для покрытий приме няют не только чистые металлы, но и их спла вы: Sn-Cu, Sn-Zn, Sn-Cd, Sn-Ni и др. Лужение с помощью ультразвука можно производить паяльником или погружением в ванну с припо ем (рис. 10).
Рис. 9. Конструкция ванны для лужения через слой флюса
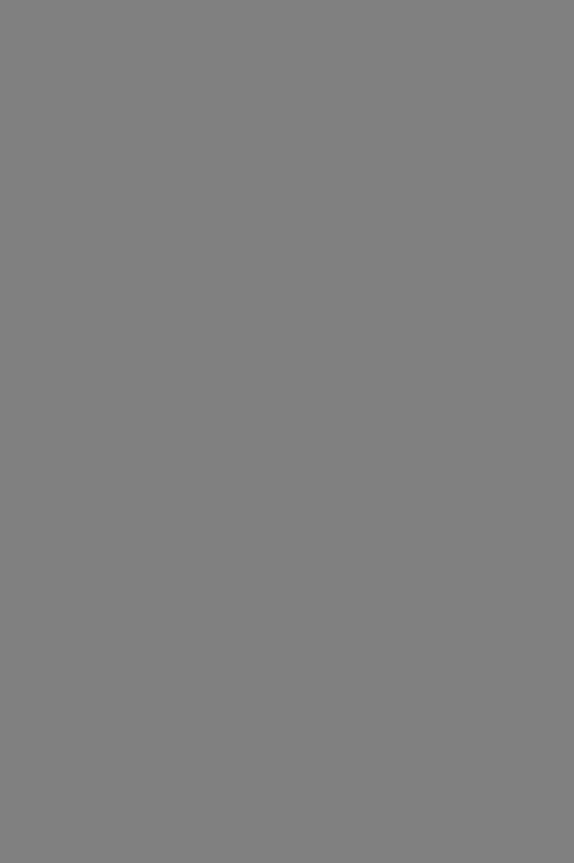
улучшения смачивания в дальнейшем поверх ность можно никелировать.
Нанесение покрытия может быть произ ведено совместной прокаткой паяемого метал ла и металла-покрытия (плакировка). Толщина покрытия при этом значительна - около 0,1 мм. Способность плакированной детали к пайке определяется ТКЛР плакирующего материала. Пайка получается качественной при соотноше нии ТКЛР паяемого и плакирующего материа лов больше 60 %.
Высокое качество покрытий обеспечива ется нанесением металлов в вакууме в резуль тате их испарения (термовакуумный способ). Этот метод дает возможность получать равно мерные покрытия малых толщин (2 ... 100 мкм) в условиях, обеспечивающих отсутствие окисле ния паяемого металла и металла покрытия.
Получение наиболее надежных покрытий обеспечивается при нанесении их в тлеющем разряде в ионизированном состоянии. При этом возможно равномерное покрытие всей поверхности детали. Обработка покрываемой поверхности быстрыми частицами нейтрально го газа в той же камере непосредственно перед нанесением покрытий обеспечивает удаление окислов с покрываемой поверхности. Покры тие наносится в электрическом поле при разно сти потенциалов до 10 кВ, что способствует надежному сцеплению покрытия с паяемым материалом. Эта особенность метода позволяет получать надежные покрытия практически на любом материале (спеченном материале, ситалле, магниевых сплавах и т.п.).
Контроль качества покрытий. Требо вания, предъявляемые к качеству покрытий, определяются назначением последних. Разли чают следующие виды контроля: визуальный контроль изделий после покрытия (цвет, блеск, шероховатость поверхности); определение по ристости и толщины слоя покрытий; испыта ние на коррозионную стойкость; определение механических и физических свойств покрытий (пластичности, стойкости к высоким темпера турам и др.).
Оценку качества покрытий производят по внешнему виду (осмотр невооруженным гла зом) на основании сравнения с эталонами и по результатам лабораторных методов испытания на основании требований к покрытиям, уста новленным техническими условиями.
Сцепляемость покрытия с паяемым ме таллом испытывается для листового материала загибом на угол 90° или 180° до поломки об
разца; для проволоки - навивкой образца во круг стержня того же или большего диаметра в зависимости от диаметра и назначения прово локи. Во всех случаях испытаний на сцепляе мость не должно быть трещин и отслаивания покрытия.
Коррозионную стойкость покрытий опре деляют методом ускоренных испытаний в ис кусственно создаваемых коррозионных средах и по данным поведения покрытий в естествен ных условиях их эксплуатации. Средой для искусственных испытаний может быть туман раствора поваренной соли, созданный в специ альной камере или атмосфере агрессивного газа, соответствующего условиям эксплуата ции изделия, и др.
Предотвращение растекания припоя.
В практике пайки часто требуется ограничить растекание припоя по поверхности паяемого металла.
Для ограничения растекания применяют следующие меры.
• 1. Нанесение покрытий на поверхность паяемого материала. Для этого используют со ставы (масс, ч.): 1) глиноземная пудра - 1, окис лы металлов (Si, Ti, Ge, Zr, Sn, Ce, Hf, Pb, Th) - 1, разбавитель (растворитель или связка) - 10; 2) паста из мела, глины, графита или известко
вый раствор; 3) порошок А120 3 - 15 |
20; аце |
||||
тон - |
90 |
100; отходы органического стекла - |
|||
0,9 |
1,1; 4) бихромат калия - 5 |
50; 5) сер |
|||
нокислый магний - |
1 |
30 (температура 40 |
|||
80 °С); 6) MgO - |
3,0 |
5,5; углекислый маг |
|||
ний - |
0,25 |
0,5; дистиллированная вода - |
|||
остальное; |
7) раствор |
хромовой |
кислоты; |
8) хромирование поверхности; 9) кремнийор-
ганическая жидкость - 80 |
99; порошок алю |
|
миния - 1 |
20 и пропеллент - смесь фреонов |
в соотношении с кремнийорганической жидко
стью и порошком алюминия 1 |
3 и 2 |
3 соот |
ветственно; 10) нитроцеллюлоза - 2,5 |
3,5; |
|
амилацетат и диэтилоксалат - |
остальное (при |
меняются при пайке в инертной атмосфере, в вакууме и газопламенным способом); 11) рас
твор полиметилфенилсилоксановой |
смолы в |
|
толуоле - 35 |
60; уротропин - 0,4 |
0,6, смесь |
фреонов - остальное; 12) композиционные огнеупорные покрытия порошков на основе А120 3, Si02, Zr02, MgO и других высокотемпе ратурных окислов, карбидов, нитридов с при менением газопламенного, плазменного, стержневого и детонационных способов нане сения покрытий; 13) оксидирование поверхно сти и т.д.
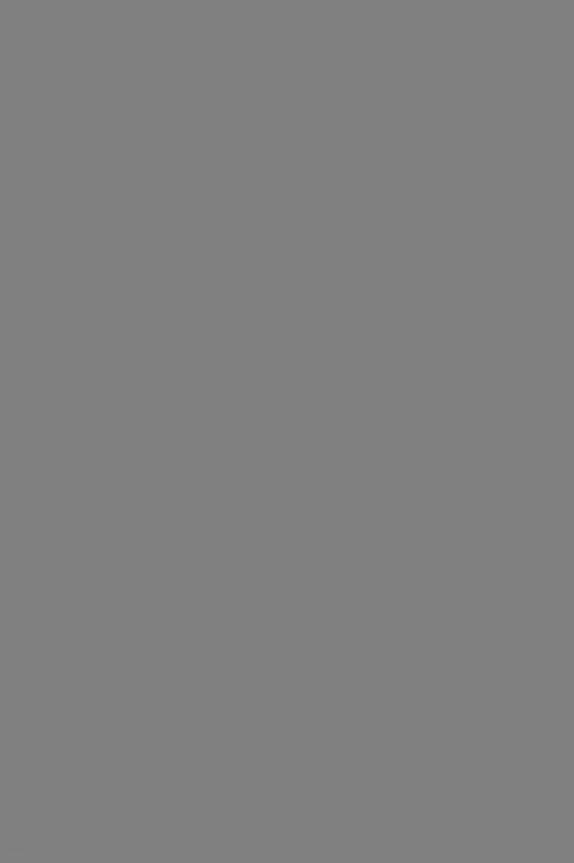
Применение приспособлений позволяет повысить производительность труда, обеспе чить заданную геометрию паяемой детали, локализовать нагрев ее поверхности и т.п. Это особенно выгодно при массовом производстве, так как отпадают операции по зачистке и до полнительной механической обработке деталей после пайки.
Правила конструирования приспособле ний и требования, предъявляемые к ним, сле дующие:
-масса и площадь контакта приспособ ления с изделием должны быть минимальными;
-конструкция приспособления не должна препятствовать быстрому и равномер ному нагреву изделия и вызывать его деформа цию (за исключением экранов и холодильни ков); должна обеспечивать свободную цирку ляцию газов в полости паяемого узла или их быструю откачку при пайке в вакууме;
-удобное расположение припоя и на блюдение за его расплавлением;
-изменения размеров деталей приспо собления и изделия при нагреве и охлаждении должны согласовываться. Это достигается или подбором материалов с соответствующими ТКЛР, применением легкодеформируемых де талей приспособления, или же обеспечением свободного перемещения изделия внутри при способления;
-шероховатость поверхности у разъем
ных соединений приспособления не |
ниже |
Ra 0,63, у точных баз - не ниже Ra 0,32 |
0,16; |
-все переходные кромки, ограничи вающие точные базы или поверхности разъем ных соединений, должны иметь плавные скругления максимально допустимого радиуса;
-сопряжения деталей приспособления
спаяемыми узлами и между собой должны иметь посадки с гарантированными зазорами (ходовые, широкоходовые);
-необходимо обеспечить несмачиваемосгь материала приспособления жидким припоем;
-материалы деталей приспособления должны хорошо обрабатываться и обладать термостойкостью и необходимой механиче ской прочностью при температуре пайки;
-при конструировании приспособле ний для индукционной пайки необходимо, чтобы в поле индукционной катушки попадало только паяемое соединение, исключая все дру гие материалы. Для такой пайки применяют приспособления, выполненные из фарфора, слюды, керамики или асбеста.
Эти требования ограничивают выбор пригодных материалов сравнительно немноги ми сплавами, металлами и керамиками. Для элементов оснастки используют следующие материалы: стали марок 12Х18Н10Т, 36Х18Н25С2, сталь 45, 20X13, нихром, молиб ден, никель, тантал, ковар, керамику различ ных марок, асбест, графиты.
ТКЛР в широком диапазоне температур некоторых материалов даны на рис. 12.
Сталь 12Х18Н10Т при нагреве в атмо сфере, содержащей незначительное количест во кислорода (не более 0,005 %) или паров воды (точка росы выше - 30 °С), покрывается плотной и стойкой пленкой окислов, которая плохо смачивается жидкими припоями. Эта сталь имеет ТКЛР, близкий к меди, что позво ляет делать из нее точные приспособления. Перспективна для изготовления приспособле ний сталь 20Х23Н13, у которой при темпера туре выше 500 °С ТКЛР больше, чем у меди. Сталь 45 может быть использована для различ ных деталей приспособлений. В тех случаях, когда приспособление должно быть предохра нено от припаивания, его поверхность хроми руют с последующим окислением,
а107,°С
Рис. 12. ТКЛР для наиболее употребительных металлов и сплавов электровакуумного производства
Нихром при нагреве покрывается стойкой пленкой окиси хрома. Его используют в основ ном в виде ленты и проволоки. Молибден при меняют главным образом благодаря низкому ТКЛР и достаточной прочности при высоких температурах. Для предохранения от припаивания молибден иногда хромируют, при этом его сцепление с покрытием непрочное, поэто му оно быстро отслаивается.
Керамика может выдерживать любую ат мосферу печи без окисления и раскрошивания, не смачивается припоями, не склонна к спека нию. Недостатками керамических материалов являются их склонность к растрескиванию при термоударах и трудность механической об работки.
Асбест является очень непрочным мате риалом, сильно загрязняет камеру печи, поэто му как материал для изготовления приспособ лений не пригоден.
Приспособления из графитовых и уголь ных пластин не подвергаются короблению; эти материалы легко обрабатываются. Однако при пайке стальных деталей возможно их наугле роживание, в результате чего резко падает температура плавления стали и отдельные уча стки деталей оплавляются. Процесс науглеро живания идет особенно интенсивно при пайке в вакууме. Науглероживание исключается, если на поверхность графита или угля поло жить тонкую асбестовую прокладку.
В качестве изолирующего материала ис пользуют силицированный графит объемного силицирования, обладающий термостойкостью до 2500 °С. В сыром виде (до силицирования) графиту можно придать любую форму. Так, из графита ПГ-50 обычно изготовляют мелкие детали приспособлений; для крупных деталей может быть применен графит ПРОГ-2400.
Детали приспособлений, изготовленные из графита, подвергают силицированию в вы сокотемпературных печах сопротивления или в
индукционных печах при 1700 |
2100 °С в |
атмосфере чистого азота с максимально допус тимой примесью кислорода 0,3 0,5 %. Прак тика показала, что применение силицированного графита вполне оправдано. Благодаря высо кой термостойкости, а также отсутствию газо образования при нагревании до 1100 °С сили цированный графит можно считать наиболее подходящим материалом для приспособлений.
Детали из фарфора при температуре на грева до 1100 °С выдерживают всего лишь дветри пайки, затем их поверхность остекляется, нарушая геометрию и размеры.
О
Рис. 13. Приспособление для пайки в виде штыря
Конструкция приспособлений для пайки определяется формой паяемых деталей. При пайке мелких деталей при мелкосерийном про изводстве можно рекомендовать приспособле ние в виде штыря (рис. 13).
Одним из элементов приспособлений для пайки являются подставки. На рис. 14 изобра жена многоместная подставка для печей, имеющих большую высоту рабочей зоны. Для предотвращения коробления полок подставки снабжены опорными дисками. Подставка для пайки неустойчивых изделий показана на рис. 15. В увеличенном масштабе показаны возможные виды сопряжения изделий и стойки подставки. На рис. 15, а показан случай, когда остаются замкнутыми объемы А и />, что может приводить к окислению деталей. На рис. 15, б и в показан случай, когда эти объемы легко проду ваются через отверстия или шлиц.
А-А
Рис. 14. Универсальная подставка для колпаковой водородной печи:
Б - отверстия для циркуляции газов; В - отверстия-
гнезда для установки ножек приспособлений
Рис. 15. Подставка для пайки неустойчивых изделий:
/- изделие; 2 - стойка; 3 - д иск; 4 - штырь для установки
вгнезда подставки; .П\ и П2- места пайки
Рис. 16. Многоместная подставка для пайки простых узлов:
1 - изделие: 2 - опорная стойка; 3 - фланец; 4 - ручка для удобства установки и вынимания подставки; П\ и П2 - места пайки
Многоместная подставка для пайки про стых узлов изображена на рис. 16. Такая под ставка позволяет расположить на ней детали в процессе сборки, транспортировать в универ сальной таре, быстро устанавливать изделия в печь и извлекать из нее.
При пайке в соляных ваннах применяют приспособления, позволяющие производить од
новременную пайку нескольких деталей (рис. 17).
?
Рис. 17. Приспособление для пайки в соляных ваннах одновременно нескольких деталей
Графитовая оправка для припаивания сильфона из бериллиевой бронзы к арматуре (рис. 18) позволяет нагревать арматуру до тем пературы пайки, в то время как сильфон, кроме непосредственно примыкающего к арматуре гофра, нагревается до гораздо меньшей темпе ратуры.
Закрепляющие или сжимающие приспо собления (или грузы) широко используют для взаимной фиксации деталей при сборке и в процессе пайки. Примеры применения про стейших приспособлений, сжимающих детали по торцам, показаны на рис. 19.
Рис. 18. Оправка для пайки деталей ТВЧ:
/ - графитовая оправка; 2 - сильфон; 3 - припой
Рис. 19. Приспособление для точного центрирования диаметров паяемых деталей:
7 и 2 - детали; 3 - центрирующий груз; 4 - стержень; 5 - втулка, обеспечивающая положение деталей
вболее равномерной температурной зоне;
А- буртик для удобства поднятия узла; Б - буртик
для уменьшения теплового контакта с грузом;
В- отверстия для циркуляции газов
9 - 8294
О
Рис. 20. Центрирующая оправка:
1 - оправка; 2 - полюсный наконечник;
3- керамическая втулка
Рис. 21. Оправка с винтовым поджимом
Часто оправка должна обеспечивать не только сжатие паяемых деталей, но и большую точность их взаимного расположения. В каче стве примера на рис. 20 показана оправка для впаивания керамической втулки в полюсный наконечник на определенной высоте. Оправка для пайки двух цилиндрических полых дета лей, достаточно жестких в направлении давле ния сжатия, показана на рис. 21. В этом случае сжатие деталей создается обычной резьбой. Материал таких оправок должен иметь ТКЛР, равный или близкий к ТКЛР материала паяе мых деталей.
Иногда необходимое при пайке сжатие паяемых деталей обеспечивается за счет разно сти в ТКЛР материалов оправки и паяемого узла. Так, если паяют детали из коррозионностойкой стали, то центральный стержень оп равки может быть изготовлен из молибдена. Когда детали паяют по торцовым поверхно стям, то для этих целей обычно используют грузы или пневматические приспособления.
Рис. 22. Скрепляющее приспособление
склиновым зажимом:
1- груз; 2 - скользящий клиновой груз; 3 - неподвижная опора со скосами
Рис. 23. Применение молибденовых пружин для поджатая деталей
На рис. 22 показано более сложное при способление, в котором легкий фланец волно вода прижимается обычным грузом, а закреп ление деталей по торцам в горизонтальном направлении осуществляется за счет скольже ния подвижного груза по скосу относительно неподвижной опоры.
Для создания необходимого сжатия паяе мых деталей могут быть использованы молиб деновые пружины. Примером такого рода оп равки является приспособление для припаивания узла вывода энергии к анодному блоку (рис. 23). Давление сжатия подбирают так, чтобы не деформировать паяемые узлы. Ос тальные детали обычно выполняют из высоко хромистых сталей, чаще всего марок 12Х18Н9Т, 20X13.
При пайке деталей из материалов с раз личными ТКЛР применяют специальные вкла дыши, ограничивающие коробление. На рис. 24 показан пример использования вкладыша при пайке прямоугольного медного волновода со стальным фланцем.
Рис. 24. Вкладыш, препятствующий короблению стенок медного волновода при пайке
со стальными фланцами:
/ - стальные фланцы; 2 - медный волновод; 3 - вкладыш; 4 - форма волновода после пайки
при отсутствии вкладыша; Я - место пайки
Рис. 25. Фиксатор, препятствующий возникновению деформации в стакане из никель-кобальтового сплава при пайке:
1 - фиксатор; 2 - стакан; 3 и 5 - нихромовая
проволока, препятствующая растеканию припоя; 4 - стальное кольцо; б - никелевое кольцо;
7 - фланец; П\ и Пг - места пайки
Кроме того, деформации паяемых дета лей могут возникать вследствие снятия их соб ственных напряжений (особенно в тонкостен ных деталях), а также в результате неравно мерного нагрева отдельных деталей паяемого узла. В таких случаях наряду с принятием мер, препятствующих неравномерному нагреву (применение экранов и т.п.), используют фик саторы, которые позволяют сохранять форму деталей. На рис. 25 приведен пример примене ния фиксатора, препятствующего возникнове нию деформаций стакана из никель-кобальто вого сплава вследствие снятия собственных напряжений.
Пайка тонких деталей представляет большую трудность ввиду того, что они быстро остывают, а сосредоточенный их нагрев при водит к прожогам. Чтобы устранить указанные трудности, рекомендуется применять пустоте лые оправки 1 и металлический компенсатор 3 (рис. 26).
Рис. 26. Приспособление для пайки тонкостенных деталей:
/- пустотелая оправка; 2 - деталь; 3 - металлический компенсатор
При пайке нагревают изнутри оправку У до расплавления ранее нанесенного на деталь 2 флюса, после чего второй горелкой при непре рывном передвижении пламени производят пайку. Если на оправку под шов подкладывают асбестовую прокладку, то в этом случае пайку производят одной горелкой.
Иногда создание температурного перепа да решается с помощью водоохлаждаемых радиаторов. На рис. 27 показан радиатор, пре дохраняющий сильфон и стеклянную трубку от перегрева при пайке его с корпусом прибора. Материал радиаторов и нагревательных опра вок должен обладать высокой теплопроводно стью, поэтому радиаторы чаще всего делают из меди, а оправки - из графита.
Рис. 27. Оправка с водоохлаждаемыми радиаторами:
/ - узел, подлежащий пайке; 2 — сильфон; 3 - стеклянная трубка; 4 - электроды для пайки
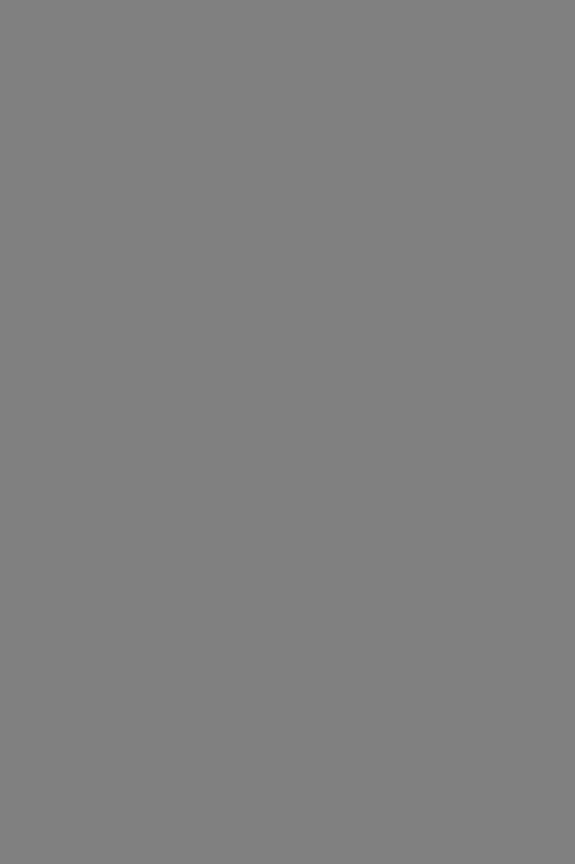