
Металлургия черных и цветных металлов
..pdfможет |
окисляться |
мышьяк |
в |
газовой |
|
|
|
|
|
|
|||||
фазе: |
|
|
|
|
|
|
|
|
|
|
|
|
|
|
|
4As + 302 - 2AS20 3; |
4AS+ 502 = 2As20 8. |
|
|
|
|
|
|
||||||||
Уже с 60-х годов многоподовые печи |
|
|
|
|
|
|
|||||||||
успешно |
заменяются печами |
КС, рабо |
|
|
|
|
|
|
|||||||
тающими на основе кипящего или псев |
|
|
|
|
|
|
|||||||||
доожиженного слоя. Успех связан с вы |
|
|
|
|
|
|
|||||||||
сокой |
производительностью: |
одна |
печь |
|
|
|
|
|
|
||||||
КС с площадью пода 10—14 м2 заменя |
|
|
|
|
|
|
|||||||||
ет три десятка подовых печей. Печи КС |
|
|
|
|
|
|
|||||||||
позволяют лучше |
|
управлять |
процессом, |
|
|
|
|
|
|
||||||
получать газ с высоким содержанием |
|
|
|
|
|
|
|||||||||
S02, полнее утилизировать серу на про |
|
|
|
|
|
|
|||||||||
изводство серной |
кислоты и тепло |
отхо |
Рис. |
1.13. |
Схема |
обжига |
|||||||||
дящих |
газов, |
полнее механизировать и |
|||||||||||||
тельной печи, |
работающей |
||||||||||||||
автоматизировать |
процесс. На |
рис. |
1.13 |
по принципу кипящего |
слоя: |
||||||||||
представлена |
принципиальная |
схема че |
/ — питатель |
шихты: |
2 — |
||||||||||
главные |
горелки; |
3 — го |
|||||||||||||
тырехподовой |
печи |
КС. Тонкоизмельчен- |
релки |
для |
начального |
разо |
|||||||||
грева; |
4 — течка |
разгрузки |
|||||||||||||
ные |
материалы |
(3—0 мм) |
загружают |
обожженного |
|
продукта; |
|||||||||
на горизонтальный |
под, снабженный со |
5—7 — подогревательные ка |
|||||||||||||
меры; |
8 — обжиговая |
каме |
|||||||||||||
плами, через которые поступает горячий |
ра; 9 — охладительная |
ка |
|||||||||||||
мера; |
10 — воздушное |
ду |
|||||||||||||
восстановительный |
газ при |
магнетизи |
тье |
|
|
|
|
|
|||||||
рующем |
обжиге. Обжигаемый |
материал |
|
|
|
|
|
|
перемещается с верхних зон в нижние.
Скорость гааа должна обеспечить подвижность зерен обжи гаемого материала и газа, подобную подвижности спокойной вязкой жидкости. При превышении такой скорости слой из псевдоожиженного состояния перейдет в состояние пневмотранс порта, и частицы обжигаемого материала будут выноситься газом. Работающая печь КС загружается непрерывно через питатель. Степень загруженности печи постоянная. После пред варительного разогрева печи и слоя до 700—800 °С включается дутье, постепенно увеличиваются расход воздуха и давление. Температура частичного обжига достигает 800—900 °С в зави симости от свойств шихты и технологии. Характерен следующий состав материалов на частичный обжиг сульфидных медных шихт, концентратов Алавердского комбината (А) и Средне-
уральского медеплавильного завода |
(Б), %: |
|
|
|||
|
Си |
Fe |
S |
Zn |
SiO-, |
CaO |
A |
15— 18 |
24—26 28—31 |
0,5—0,9 |
15— 16 |
1,1— 1,6 |
|
Б |
10— 12 |
21—25 28—32 |
3,0—3,5 |
15—22 |
2,7—5,0 |
Подобные материалы для производства меди, медные суль фидные руды и их концентраты подвергают частичному обжигу, чтобы: 1) удалить излишнюю для процесса серу; 2) полнее ути лизировать серу концентрата для производства серной кислоты
и возможно меньше загрязнять серой атмосферу; |
3) окислить |
в нужной степени сульфид железа (чтобы при |
последующей |
плавке огарка на штейн и переделе последнего на медь меньше железа перешло в штейн, последний был бы более богат медью и это повысило бы экономическую эффективность всего пере дела на медь). Степень десульфурации для этих двух примеров 50—55 %. Газы содержали 12—14 % SO2, и извлечение серы в H2SO4 составляло 50—70 %. Таким образом, газы также являются одним из продуктов обжига. Газы, движущиеся с вы сокой скоростью, выносят из печи 30—40 % шихты, а если фло тационный концентрат очень тонкий, то и больше. По существу выносится продукт, поэтому пыль улавливают несколькими циклонами и электрогазоочисткбй на 90—95 %, и она идет возвратом на обжиг или непосредственно в производство, при мешиваясь к огарку, или более эффективно подвергается окускованию. В оставшейся части зерна шихты размягчаются, покрываются пленками эвтектического состава, слипаются друг с другом, образуя огарок. Аналогично при обжиге нике левого файнштейна происходит слипание и срастание его зе рен, чему способствует образование оксида никеля.
Образовавшийся огарок обжига в печах КС всегда значи тельно мельче, чем огарок, полученный в многоподовых печах. Это, а также получение продукта обжига в основном в виде пыли — отрицательные особенности печей КС. В связи с этим в технологии производства цветных металлов часто применяют окомкование продукта обжига на тарельчатых грануляторах, на них же производят окомкование шихты, подвергающейся об жигу, обжигая уже не пыль мелких фракций, а окатыши. Выгружают огарок обычно непрерывно, и эффективнее его транспортировать в последующий агрегат в горячем виде ваго нетками, а более совершенно — пневматически по трубам. Окислительный обжиг сульфидных материалов проходит за счет сильно экзотермических реакций окисления сульфидов же леза кислородом воздуха, поэтому после зажигания развива ются достаточно высокие температуры (600—900 °С). В приве денном примере обжига медно-сульфидного концентрата (табл. 1.3) развивалась температура 850—880 °С. Обжиг мате риалов не нуждался в притоке тепла извне, горелки отключа лись, и обжиг протекал без затраты горючего. Обжиг проходил за счет теплоты горения сульфидов и серы, так называемый пиритный обжиг.
В печах КС обычно тепло утилизируется на нагрев воды. Для обжига сульфидных материалов в печах КС эффективно применение кислорода. Обогащение воздуха кислородом уско ряет процесс и, что примечательно, дает огарок более крупный, чем при обжиге на необогащенном дутье. Если при обжиге раз виваются невысокие температуры (500—600 °С) при большом
Т а б л и ц а 1.3. Состав продуктов частичного обжига концентратов Среднеуральского медеплавильного завода, %'
|
|
Продукт |
|
|
Си |
S |
Fe |
Zn |
slo2 |
CaO |
Огарок |
из |
кипящей ванны |
5,9 |
5,4 |
12,4 |
3,8 |
31,3 |
9,9 |
||
Огарок, |
выгруженный |
из |
печи |
6,6 |
5,2 |
12,8 |
2,8 |
34,0 |
— |
|
Пыль: |
|
I ступени |
|
|
18,8 |
16,8 |
29,8 |
5,8 |
18,7 |
2,2 |
циклонов |
|
|
||||||||
циклонов |
II ступени |
|
|
14,6 |
11,3 |
20,2 |
9,3 |
14,9 |
3,0 |
|
электрофильтров |
на |
плавку |
14,2 |
12,6 |
20,8 |
8,6 |
9,8 |
3,2 |
||
Смесь огарка с пылью |
14,4 |
14,6 |
26,8 |
5,0 |
19,1 |
3,7 |
избытке воздуха, будут образовываться сульфаты, такой обжиг называют сульфатизирующим:
2SOj -(- 0 2 = 2S03; Fe20 3 -f- 3S03 = Fe2 (SO^-, CuO + S03 = CuS04.
В настоящее время обжиг в печах КС является основным этапом в процессе получения меди, еще более широко в печах КС проводят окислительный обжиг никелевых сульфидных кон центратов и полупродуктов в производстве никеля. Обжиг нике левого концентрата обычно ведут до получения оксида никеля, так как в последующих восстановительных процессах получе ния никеля серу будет трудно удалить, а даже небольшие при меси ее отрицательно сказываются на процессе электролитиче ского рафинирования/никеля. В результате обжига в печах КС получают порошок, содержащий 69—75 % Ni, 3,5—4,0 % Си, 1,0—1,3 % Со, <0,4 % S.
§ 5. Окускованне рудных материалов спеканием
Общая схема процесса и физико-химические основы спекания
Окускованне мелких руд и концентратов осуществляется пре имущественно спеканием с одновременным просасыванием воз духа сквозь слой шихты, что называется агломерацией. Цель агломерации не только окускованне, но и улучшение металлур гических свойств рудного материала: упрочнение кусков, повы шение пористости, удаление серы, создание новых качеств и составляющих материалов, благоприятных в последующем про цессе. Рудные материалы составляют основную массу в объеме расходуемого сырья и формировании себестоимости чернового металла. Поэтому повышение качества и производительности агрегатов для получения конечного металла невозможно без
|
|
|
|
|
агломерации |
рудных материалов. |
||||||||
|
|
|
|
|
Для черной |
|
металлургии |
этот |
||||||
|
|
|
|
|
вопрос |
особенно |
актуален, так |
|||||||
|
|
|
|
|
как производство чугуна в со |
|||||||||
|
|
|
|
|
временных доменных |
печах или |
||||||||
|
|
|
|
|
прямое |
подучение |
железа невоз |
|||||||
|
|
|
|
|
можны |
на |
основе неокускованно- |
|||||||
|
|
|
|
|
го |
м&териэда. |
Положение |
усу |
||||||
|
|
|
|
|
губляется м тем, что многие ру |
|||||||||
|
|
|
|
|
ды состоят из значительной до |
|||||||||
Рис. 1.14. |
Схема |
разреза агломера |
ли |
мелких фракций и при добы |
||||||||||
че |
кусковатых |
железных и мар |
||||||||||||
ционного слоя в процессе спекания: |
||||||||||||||
а — распределение температуры |
в слое: |
ганцевых |
руд |
|
образуется |
много |
||||||||
б — средний. |
рабочий температурный |
мелочи; |
так, |
руды |
эксплуатиру |
|||||||||
уровень; |
ЗГ — зона горения; |
t — тем |
||||||||||||
пература |
в зоне горения, °С |
|
емого |
Яковлевского |
месторож |
|||||||||
мелкими |
фракциями; |
|
дения КМА на 85 % составлены |
|||||||||||
Криворожский |
бассейн |
выдает |
более |
|||||||||||
65 % руды |
крупностью < 10 |
мм. Все |
более расширяющееся |
обобщение дает концентрат в виде тонкоизмельченного мате риала (шлих или эфель). Применение агломерата в доменной плавке уменьшает расход материалов и интенсифицирует про цесс. В связи с этим доля агломерата в шихте из года в год увеличивается, в среднем в стране достигла 80 %, на многих заводах— 100 %.
Для агломерации измельченные до < 8 мм рудные мате риалы тщательно перемешивают с коксиком крупности 3—0 мм, увлажняют до оптимальной влажности 8—15 % и подготовлен ную шихту загружают на колосники спекательной машины слоем высотой 200—450 мм. Топливо в шихте поджигается сверху. Эксгаустер создает разрежение, максимальная величина которого в зоне спекания 9,8—12,2 кПа. Предварительное пере мешивание увлажненной шихты распределяет влагу по поверх ности зерен материалов, на них создаются водяные пленки, раз деляющие зерна друг от друга. С другой стороны, капиллярные силы стягивают зерна в малые комочки, увеличивающиеся при комковании. Увеличение и уплотнение комков способствует равномерному просасыванию воздуха. Благодаря этим усло виям при воздействии горелки сверху, в узко ограниченной об ласти (20—25 мм) образуется зона горения.
На рис. 1.14 схематично представлен разрез слоя шихты в процессе спекания. Характерный для агломерации узкий слой горения создается тем, что скорость горения так высока и кис лород так быстро расходуется, что за зоной горения его уже недостаточно для развития горения. Кроме того, под нижней кромкой зоны горения топливо нагревается до температуры воспламенения как раз к моменту появления достаточных коли честв кислорода на этом горизонте. Этими обстоятельствами и
вызвано передвижение зоны горения сверху вниз, узко ограни ченной по высоте. За зоной горения остается все увеличиваю щийся слой спеченного материала, т. е. готового агломерата. Через слой готового горячего агломерата под действием разре жения продолжает просасываться воздух, который охлаждает горячий агломерат. Зону, остающуюся за понижающейся зоной горения, называют зоной охлаждения. При охлаждении агломе рат интенсивно отдает воздуху большое количество тепла, кото рое вносится в зону горения, возвращаясь в процесс. Продукты сгорания несут много тепла, которое усваивается слоем шихты, лежащей под зоной горения, которую называют зоной подо грева. Горение топлива и усвоение его тепла в процессе агло мерации происходят в исключительно благоприятных условиях: 1) топливо горит в слое материалов, которые поглощают вы деляющееся при этом тепло; 2) тепло спеченного материала (агломерата) в значительной доле возвращается в процесс; на
гретый за его счет воздух поступает в зону горения, повышая |
|
температуру горения и продуктов сгорания; 3) высоко нагре |
|
тые продукты сгорания отдают большую часть своего |
тепла |
в зоне подогрева, и нагретая до температуры воспламенения |
|
700 °С шихта поступает в зону горения, повышая температуру |
|
очага горения. Благодаря относительно малым теплопотерям, |
|
высокой утилизации тепла в быстро перемещающейся |
зоне |
горения |
развиваются |
высокие температуры |
(1300—1500 °С), |
||
хотя расход углерода |
очень |
мал, всего 5—6 % |
или в |
среднем |
|
6—7 % |
твердого топлива. |
Топливом служат |
коксик |
~ 5 мм, |
антрацитовый штыб, угольная пыль. Продукты сгорания, остав ляя в процессе большую часть своего тепла, уходят при 600— 700 °С. Если бы зона горения доходила до колосников, они бы скоро сгорели. Для предохранения их, а также чтобы шихта не проваливалась через колосники, на них укладывают постель из возврата готового агломерата фракцией 10—25 мм.
Температура в зоне горения меняется в зависимости от пере мещения зоны сверху вниз. Это изменение показано линией а на средней позиции (см. рис. 1.14). Пунктирной линией б пред ставлен уровень оптимальной, обычно 1250—1350 °С, и, следо вательно, желательной температуры в зоне горения.
В начале процесса до достижения зоной горения трети или четверти высоты слоя о,т его поверхности тепла для агломера ции не хватает. Это определяется еще недостаточным подогре вом шихты, высокой теплоотдачей в атмосферу, отсутствием или недостаточным подогревом просасываемого воздуха. Все эти недостатки по мере продвижения зоны горения уменьша ются, и наступает момент (линии а и б пересекаются), когда температура в зоне горения достигает оптимальной. После этого теплопотери уменьшаются; воздух для горения просасывается сквозь толстый и все увеличивающийся слой горячего агломе-
рата, все более нагревается и больше вносит физического тепла в зону горения. Зона горения в своем продвижении встречает шихту, все более нагретую просасываемыми сквозь нее горя чими газами, отдающими ей тепло. Все эти обстоятельства опре деляют все большее превышение'действительной температуры в зоне горения над оптимальной; создаются условия перегрева.
Недостаток тепла в верхних слоях спекаемого пирога при водит к образованию малого количества силикатного расплава связки, в результате чего получается непрочный агломерат. В районе пересечения линий а и б образуется мелкозернистый, легковосстановимый, прочный агломерат. В нижних горизонтах из-за избытка тепла наблюдается перегрев, что вызывает переоплавление, агломерат получает монолитную структуру с малой, пористостью и имеет пониженную восстановимость. Таким об разом, в зоне горения необходимо поддерживать равномерную температуру различными технологическими приемами.
Основы конструкции и работа ленточной агломерационной машины
Лента агломерационной машины составляется из отдель ных тележек — паллет. На рис. 1.15 представлены две проекции спекательной тележки современной агломашины. Между дви жущимися паллетами и вакуум-камерами имеется уплотнение. Торцы боковых бортов сделаны так, что при смыкании под дей ствием толкающего привода они соединяются в замок, обеспе чивая герметизацию общих боковых стенок ленты. Современную конструкцию агломашины рассмотрим по упрощенной схеме (рис. 1.16). Шихта собирается из бункеров и выдается дозато рами на сборный шихтовый конвейер. Предварительно увлаж ненная шихта смешивается во вращающемся барабане и пере носится конвейером в следующий вращающийся барабан, где увлажняется до оптимального уровня и проводится комкование.
В головной части машины зубчатое колесо механизма при вода поднимает с нижних направляющих одну за другой, пал леты, толкая их вперед по верхним направляющим. На пустые паллеты сформированной ленты из бункера возврата питатель укладывает постель. На нее из шихтового бункера питатель насыпает, слой шихты. Загруженная паллета оказывается над вакуум-камерами под разрежением и тотчас оказывается под действием зажигательного горна. Сводовые горелки, работающие на природном или смеси коксового и доменного газа, создают температуру —1300 °С, обеспечивая быстрый нагрев верхнего слоя шихты до температуры воспламенения. Через 10—15 мин зона горения достигает постели, а тележка с готовым агломера том— разгрузочного конца аглоленты. Паллета опрокидывается, выбрасывая готовый агломерат, и пустая под действием своей
46
4130 |
|
|
1500 |
|
|
; |
с 498 г |
т 498 |
2 |
^ |
|
1 |
ф - . - р н д г Н -» r r . : T J |
||||
\ |
О |
С |
н— |
— . t - |
|
|
|
|
H |
f i Т П |
F r jj |
|
|
|
|
чтг |
|
|
2 2 5 \( |
|
Ю50 |
■ те w |
|
|
|
|
j |
Рис. 1.15. |
Спекательная тележка-паллета агломашины АКМ 7-312 м2: |
1 — рама; |
2 — колосники; 3 — ходовой ролик; 4 — грузовой ролик; 5 — съемные борта; 6 — уплотнительная пластина |
/
Рис. 1.16? Упрощенная схема современной аглофабрнкн:
/ —загрузочная |
тележка; |
2 — верхняя |
решетка |
шихтовых |
бункеров; 3 — шихтовые |
бун |
||||||||||||||||
керы; |
4 — весовые |
дозаторы; 5 — сборный конвейер |
шихты; |
6 — барабан-смеситель |
ших |
|||||||||||||||||
ты; 7 — конвейер; |
8 — барабан-окомкователь |
шихты; |
9 — бункер |
шихты |
над аглолен |
|||||||||||||||||
той; |
10 — зажигательный |
горн; |
|
11 — спекатсльнмс |
тележки-паллеты; |
12 — вакуум-ка |
||||||||||||||||
меры; |
13 — сборный |
газоотвод; |
/-/— пылеуловители; |
|
15 — эксгаустер; |
16 — главный |
|
ре |
||||||||||||||
гулировочный |
шибер; |
/7 —дымовая |
труба; |
18, |
/9 — конвейеры |
уборки |
|
просыпи |
и |
|||||||||||||
пыли; |
20 — дробилка |
горячего |
агломерата; |
21 — грохот горячего |
аломерата; |
22 — охла |
||||||||||||||||
дитель агломерата;. 23 — конвейер |
охлажденного |
агломерата; |
24 — грохот |
холодного |
аг |
|||||||||||||||||
ломерата; |
25 — конвейер |
готового |
агломерата; |
26 — конвейер |
постели; |
27 — конвейер |
хо |
|||||||||||||||
лодного |
возврата; |
28 — сборный |
конвейер |
возврата.; |
29 — питатель |
ленты |
постелью; |
30 — питатель ленты шихтой
массы скатывается к головной части машины. Две ведущие звёздочки привода захватывают первую в ряду паллету за гру зовые ролики (подъемные) или за специальные выступы рамы, поднимают наверх и ставят на ходовые рельсы рабочей ветви машины. Постановка последующих паллет звездочкой стыкует их, при этом задние торцы бортов первой паллеты смыкаются с передними торцами последующей, звездочка оказывает нажим на всю ленту паллет. Выпавший из паллеты готовый горячий (700—800 °С)/ агломерат дробится в валковой дробилке,, про ходит грохочение, выделенный возврат <5 мм конвейером в горячем состоянии собирается в бункере возврата. Годный агломерат > 5 мм охлаждается в охладителе продувкой или прососом воздуха.
В СССР было распространено охлаждение агломерата в хво стовой части аглоленты. Получившийся агломерат на паллетах входит в зону охлаждения, где через его слой просасывается сверху холодный воздух. Получают распространение линейные ленточные охладители, представляющие собой цепной пластин чатый конвейер, смонтированный на наклонном каркасе. Агло мерат на конвейере продувается снизу воздухом под давлением
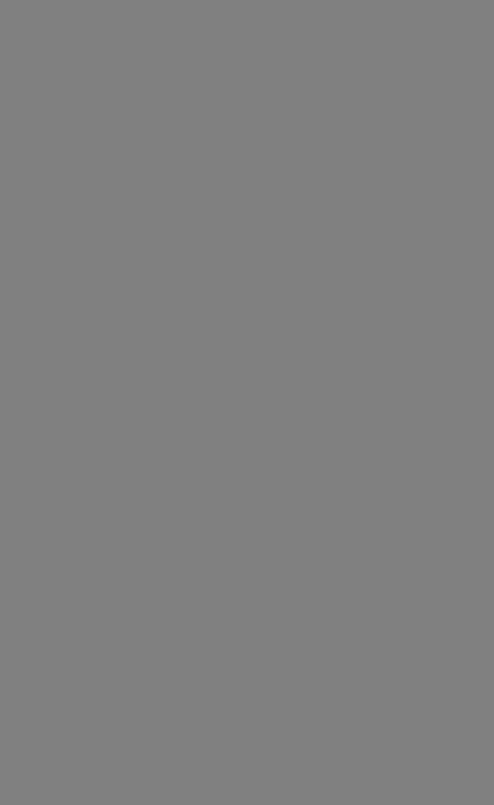
более высокую газопроницаемость, при основности 1,3—1,5 про изводительность ленты увеличивается на 10—12 %. Укрупнение концентрата после комкования может улучшить газопроницае мость на 25—30 % и в результате повысить производительность ленты на 7— 10 %.
В зоне сушки и нагрева из материалов шихты испаряются влага и связанная вода. Пары воды уносятся горячим газовым потоком в холодную зону, где в полосе высотой 30—40 мм на холодной шихте конденсируется влага при точке росы 51— 53 °С. Возникает местное переувлажнение, резко ухудшающее газопроницаемость. Для борьбы с переувлажнением сырые ма териалы подогревают до температуры 60—70 °С горячим воз духом, газовыми горелками в бункере; .паром или сжиганием газа во вращающемся барабане; горячим воздухом или сжи ганием газ-а над шихтой до ее зажигания на ленте. Эффек тивна добавка в шихту горячего возврата при 400'—600 °С. Кроме температуры, возврат повышает газопроницаемость шихты, ускоряет формирование агломерата.
В верхних слоях аглослоя в зоне горения имеет место не достаток тепла, тогда как в нижних горизонтах избыток тепла, а вследствие этого перегрев и излишнее появление жидкой фазы с ухудшением газопроницаемости. В борьбе с этими яв лениями эффективна двуслойная агломерация. Технология ее состоит в приготовлении двух шихт. В первую дается коксика меньше на 20—30 %, эта шихта укладывается в нижнюю поло вину слоя. Затем загружается верхний слой шихты с обычным количеством коксика. Кроме того, за счет этого экономится на 10—15% расход коксика и улучшается качество агломерата. Перегрев и переоплавление уменьшаются при спекании шихты на офлюсованный агломерат. Это связано с разложением изве стняка при 800 °С и офлюсованием шихты, происходящими с поглощением тепла, в результате эндотермических реакций температура в зоне горения оказывается ниже на 250—200 °С.
Повышает газопроницаемость шихты спекание под давлением. В этом случае вакуум увеличивается до 15—20 кПа, а к верхней поверхности спекае мого слоя от воздуходувки подают сжатый воздух под давлением 50—500 кПа. Повышение перепада давления увеличивает количество просасываемого воз духа, ускоряет горение в 4—5 раз. Эта технология очень перспективна, она позволяет увеличить спекаемый слой до 1 м. Обогрев шихты сверху ленты го релками, сжатым горячим воздухом повышает температуру в зоне горения, интенсифицирует горение, уменьшает переувлажнение и расход твердого топ лива. Эффективно применение в зажигательном горне воздуха, обогащенного кислородом. Обогащение воздуха при горении повышает температуру факела, увеличивает количество кислорода в продуктах сгорания до 18—23 %, тем создает условия ускорения зажигания и интенсификации горения. Разрабаты вается перспективный способ спекания высоконагретых шихт. В газовых го релках сжигают доменный газ, создавая температуру в факеле 1100—1200 °С. Чтобы не зажглось топливо шихты, в продуктах сгорания обеспечивается не более 2—3 % 0 2. Чтобы не расходовался углерод на реакцию С +С 02=2С0, нагрев шихты должен быть менее 800 °С. В пределах зоны сушки — подогрева