
Перспективные материалы и технологии порошковой металлургии
..pdfпостепенном разрушении тяжей возникает значительная величина прогиба при медленном снижении нагрузки.
Протяженность четвертой стадии напрямую связана с пластическими свойствами матрицы, а также зависит от толщины испытываемых образцов. Например, образцы ВПЯМ–Cu с П > 93 % и толщиной 2–4 мм довести до разрушения практически не удавалось, и они выдерживали изгиб до соприкосновения. Для образцов ВПЯМ с матрицей средней пластичности протяженность четвертой стадии несколько меньше.
На диаграмме изгиба образцов ВПЯМ с хрупкой матрицей отсутствует третья стадия. Процесс зарождения макротрещин наблюдается сразу после завершения второй стадии упругой деформации и заканчивается хрупким разрушением образца.
91
Глава 6. ПУТИ УПРАВЛЕНИЯ СТРУКТУРОЙ И СВОЙСТВАМИ ПОРОШКОВЫХ МАТЕРИАЛОВ
Повышенная склонность порошковых сталей к коррозии, окислению, эрозионному и контактному износу вызывает необходимость их защиты и упрочнения. Наряду с методами термической обработки (ТО) и химико-термической обработки (ХТО) в технологии порошковой металлургии используются методы пропитки, покраски их поверхности или эмалирование, электролитические покрытия. Существующие методы характеризуются недостаточной эффективностью упрочнения, высокой энергоемкостью, громоздкостью и сложностью оборудования, низкой степенью автоматизации и экологической безопасности, необоснованными затратами на дорогие и дефицитные легирующие материалы.
Как правило, наилучшие результаты по структуре и свойствам достигаются при совместной оптимизации режимов прессования, спекания и термообработки поликомпонентных сталей сложного химического состава. В то же время назначение и область применения порошковых материалов могут быть существенно расширены за счет разработки нетрадиционных методов модифицирования поверхности, основанных на использовании концентрированных потоков энергии, таких как плазма и излучение лазера.
Плазменное напыление оксинитрида кремния на пенистое основание из того же материала при низком давлении применяется для создания высокоэффективных обтекателей антенны радиолокаторов авиакосмической техники. В патентах для снижения в 2–4 раза теплопроводности деталей из карбида и нитрида кремния предлагается покрывать их поверхность теплозащитным слоем из стабилизированного оксида циркония, нанесенного плазменным напылением.
Перспективным направлением упрочняющей обработки порошковых материалов является лазерное модифицирование поверхности.
Среди исследований специфики лазерного термического модифицирования (ЛТМ) порошковых материалов необходимо выделить работы школы Н.Н. Рыкалина, в которых детально проанализирована роль пористости в механизмах взаимодействия излучения с веществом. Установлено, что при импульсной обработке наличие пористости обусловливает следующие особенности:
92
− снижение затрат на нагрев, плавление и испарение вещества (в том числе объемного на готовых центрах) из-за уменьшения коэффициентов отражения излучения и температуропроводности основы с ростом пористости;
−увеличение параметров зоны лазерного воздействия (ЗЛВ) за счет выделения свободной энергии пространства пор;
−возрастание доли удаленного вещества в ЗЛВ по механизму «выкалывания».
Наибольшее внимание исследователей уделяется изучению ЛТМ порошковых материалов на основе железа в целях повышения их поверхностных свойств (износо- и коррозионностойкости, жаростойкости
идр.). Установлено, что лазерное борирование быстрорежущих сталей марок РОМ 23-МП повышает их твердость в 1,8 раз, а износостойкость – в 2,5–4,5 раза по сравнению с объемной закалкой. Установлено, что микротвердость зоны закалки из жидкости может быть как выше, так и ниже исходной; структура зоны термического влияния (ЗТВ) обладает значительной наследственностью, твердость зоны термического влияния выше твердости зоны оплавления (ЗО); горячая твердость резцов при 700 °С на 200–300 НV выше стандартной. Аналогичные зависимости улучшения долговечности при плоском изгибе установлены для спеченных сталей типа дисталоя и бондалоя.
При детальном исследовании лазерного упрочнения порошковой стали ЖГр0,5ДЗК0,3 установлено благоприятное влияние ЛТМ на гомогенизацию стали и ее упрочнение. В ходе лазерного химикотермического модифицирования (ЛХТМ) хромом и карбидом бора в структуре формируются упрочняющие фазы боридов железа и карбидов хрома, что обеспечивает твердость стали порядка 1400–1500 HV. При этом наблюдается значительное трещинообразование. Комплексное легирование стали карбидом титана и хромом обеспечивает повышение износостойкости в 200 раз относительно исходной и в 7 раз относительно нитроцементированной.
Необходимо отметить, что наилучшие результаты по структуре и свойствам порошковых сталей достигнуты при ЛТМ и ЛХТМ непре-
рывным излучением СО2-лазера. В работах, в которых, по-видимому, впервые проведены исследования влияния лазерной обработки (импульсным и непрерывным излучением) на структуру и свойства порошковых углеродистых и легированных сталей, установлено, что в ходе ЛТМ непрерывным излучением поры концентрируются в приповерх-
93
ностной зоне, а импульсным – преимущественно на границе раздела ЗО и ЗТВ. Показано, что ЛТМ позволяет получать литые поверхностные слои высокой твердости, обеспечивающие повышение износостойкости сталей от 2–5 до 17–70 раз в сравнении со спеченным состоянием.
Лазерное химико-термическое модифицирование порошковых сталей
В целях установления закономерностей формирования структуры, прочностных и триботехнических характеристик исследовано ЛХТМ порошковой стали СП60-2 из твердого и жидкого легирующего материла.
Предварительная подготовка образцов (в виде прямоугольных призм размерами 6×6×40) проводилась по двум схемам:
1)нанесением насыщающего покрытия двух видов (раствор коллоидного графита в этиловом спирте на силикатной связке и каменноугольный лак толщиной 30 и 130 мкм для каждого вида) с последующей просушкой на воздухе;
2)предварительной пропиткой углеродсодержащими жидкостями двух видов (тетрахлорид углерода с выдержкой 24 ч, индустриальное масло И-45 с выдержкой 3, 4, 192 ч) при нормальных условиях.
Количество углерода в мартенсите после ЛХТМ исследовали на дифрактометре ДРОН-3 (СОα-излучение) по положению одной из линий мартенситного дублета (вторая линия дублета накладывается на линию α-Fе, получаемую при съемке попавших под рентгеновский пучок необработанных участков поверхности образца) и вычисляли с применением квадратичной формы для тетрагональной сингонии и известной методики определения межплоскостных расстояний в мартенсите Курдюмова. Количественное содержание остаточного аустенита исследовали методом рентгенофазового анализа (РФА), микротвердость – на приборе ПМТ-3 при нагрузке 0,5 Н, триботехнические характеристики в условиях смазки – на машине трения СМЦ-2 при нагрузке 400 МПа и скорости скольжения образца по контртелу из закаленной стали Х12М, равной 1 м/с. Для сравнения исследовали образцы из стали СП60-2, обработанные аналогично, но без примененияуказанныхспособовлазерной цементации.
В ходе лазерной обработки без использования легирующих углеродсодержащих материалов исходная однородная ферритоперлитная структура поверхности образцов трансформировалась в две последовательно расположенные зоны различной структуры и фазового состава: зону оплавления (ЗО) и зону термического влияния (ЗТВ). Зона закалки из рас-
94
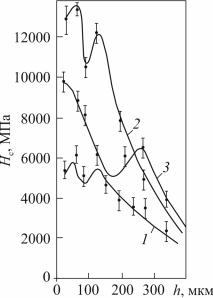
плава представляет собой мартенсит, содержащий до 0,6 % углерода, и остаточный аустенит. Пористость ЗО снизилась до 4–5 %. Структура ЗТВ представляет собой смесь мартенсита, троостита и феррита.
Необходимо |
отметить, что |
|
|
распределение микротвердости по |
|
||
глубине носит немонотонный ха- |
|
||
рактер (рис. 42, кривая 1). Уста- |
|
||
новлено, что распределение мик- |
|
||
ротвердости в этом случае имеет |
|
||
минимум на глубине 80–100 мкм, |
|
||
что, по-видимому, связано с обез- |
|
||
углероживанием ЗТВ на границе |
|
||
раздела с ЗО ввиду повышенной |
|
||
растворимости углерода в жидкой |
|
||
фазе. Судя по полученным дан- |
|
||
ным, упрочнение достигает 2,5– |
|
||
3 раз при общей глубине упроч- |
|
||
ненной зоны 300–350 мкм. |
|
||
Исследования |
обработанных |
|
|
сталей с покрытием из раствора |
Рис. 42. Микротвердость стали |
||
коллоидного графита |
показали, |
СП60-2 при лазерном легирова- |
|
что на поверхности |
образуется |
нии: 1 – ЛТМ; 2 – ЛХТМ с пред- |
|
беспористая белая плохо травя- |
варительной пропиткой в масле; |
||
щаяся (в 4%-ном растворе НNО3 |
3 – ЛХТМ с покрытием из лака |
||
в этиловом спирте) зона мартен- |
толщиной 130 мкм |
сита (рис. 43). Установлено, что количество углерода в мартенсите достигает 0,8 %. При этом РФА показал
наличие в поверхностном слое фаз у-Fе, FеС, Fе2С, FеО, Fе2О. Пересыщение мартенсита углеродом, а также наличие аустенита и карбидов свидетельствует о протекании процессов легирования в ЗО. Структура ЗТВ характеризуется наличием мартенсита закалки, троостомартенсита, троостита и феррита. Аналогичными особенностями отличается поверхность стали, обработанная излучением, с легирующим покрытием из каменноугольного лака. Однако в мартенсите ЗО, имеющей пористость 5–7 %, зафиксировано до 1,5 % углерода и некотороеувеличение глубины ЗТВ.
Отмеченные закономерности обусловливают 30–50%-ное возрастание микротвердости легированных сталей в сравнении с нелегированными (см. рис. 42). При этом сохраняется характерный минимум в распределении микротвердости по глубине. Необходимо отметить, что ука-
95
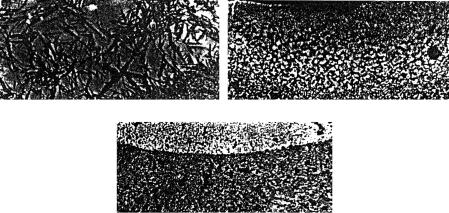
занный минимум лежит глубже по сечению материала в сравнении со случаем ЛТМ стали (см. рис. 42, кривые 1, 3). Эта особенность объясняется наличием источника диффузии углерода на поверхности стали (покрытие), что интенсифицирует процессы массопереноса в жидкой фазе. Установленное повышение микротвердости лазерно модифицированной поверхности порошковой стали вызвано, по-видимому, лучшим тепловым контактом и более высокой термостойкостью лака в сравнении с графитовым покрытием. Кроме того, ввиду жидкотекучести лака наблюдается инфильтрация материала покрытия в поверхностные слои порошковой стали, что активирует процесс насыщения углеродом как материала ЗО, так и припоровых областей ЗТВ.
а |
б |
в
Рис. 43. Структура поверхности стали СП60-2 при ЛХТМ: а – графитовое покрытие толщиной 30 мкм, ×500; б – предварительная пропитка в масле (τ = 24 ч), ×100; в – предвари-
тельная пропитка в масле (τ = 192 ч), ×63
Таким образом, наряду с известным механизмом термокапиллярной конвекции в расплаве и взаимодействием с продуктами эрозии (плазма углеродсодержащих продуктов) в порошковой стали наблюдается более интенсивная диффузия в твердой фазе за счет относительно глубокого проникновения материала покрытия в приповерхностные поры основы.
Наиболее полно установленный механизм реализуется в условиях предварительной пропитки порошковой стали жидкостью, содержащей легирующие элементы. Согласно полученным данным, структура ЗО в случае пропитки маслом характеризуется наличием мелкодисперсного мартенсита, содержащего до 1,5 % углерода, аустенита и мелкодисперс-
96
ных карбидов. ЗТВ состоит из мартенсита закалки и мелкодисперсных продуктов его распада.
Равномерное распределение легирующей жидкости в поровом пространстве внутреннего объема стали повышает контактную устойчивость соединения «легирующий элемент – матрица», что обусловливает значительное (в 2–2,5 раза) поверхностное упрочнение порошковой стали в ходе ЛХТМ. По-видимому, превалирующий характер диффузионного насыщения объясняется развитой поверхностью порового пространства, активно взаимодействующего с углеродсодержащей средой по всему объему зоны закалки из твердой фазы при соответствующем данному процессу структурообразования распределении температур. Установлено, что увеличение времени пропитки с 24 до 192 ч существенно не повышает степень упрочнения стали, однако при увеличении продолжительности пропитки возрастает пористость ЗО (см. рис. 43).
Необходимо указать, что пропитка тетрахлоруглеродом незначительно повлияла на превращения и свойства сталей. Установленный эффект свидетельствует о пренебрежимо малом насыщении модифицируемого объема стали углеродом в этих условиях, что связано с малой его концентрацией в жидкости и значительным испарением в ходе ЛХТМ. Данные по влиянию ЛХТМ на износостойкость порошковых материалов представлены в табл. 21. Установлено, что наилучшей износостойкостью обладает сталь при ЛХТМ с предварительной пропиткой в масле. Износостойкость стали, предварительно пропитанной в тетрахлоруглероде, не превышает износостойкости стали после ЛТМ без цементации. Полученные данные по износостойкости коррелируют со значениями микротвердости поверхностиматериалов (модуль коэффициента корреляции 0,928).
Таблица 2 1
Относительный износ (I, мкм/км)
и микротвердость поверхности стали СП60-2
|
|
|
|
|
|
|
ЛХТМ |
|
|
|
|
Исход- |
|
Обмазка, толщина покрытия, |
Пропитка, время |
||||||
I , |
|
|
|
мкм |
|
|
выдержки, ч |
|||
ное |
ЛТМ |
|
|
|
|
|
Тетра- |
Масло |
||
мкм/км |
|
|
|
|
|
|||||
состоя- |
|
Графит |
|
Лак |
хлорид |
|||||
|
ние |
|
|
угле- |
индустриальное |
|||||
|
|
|
|
|
|
|
||||
|
|
|
|
|
|
|
|
рода |
|
|
|
|
|
30 |
130 |
|
30 |
130 |
192 |
24 |
192 |
HV0,05 |
20 |
15 |
10 |
10 |
|
12 |
12 |
16 |
3 |
2 |
100–200 |
550–600 |
680–720 |
900–950 |
900–980 |
950–1050 |
550–580 |
1200–1250 |
1300–1350 |
97
Проведенные исследования и полученные результаты положены в основу разработанного способа поверхностного легирования спеченных проницаемых сталей, включающего в себя насыщение зоны оплавления легирующими элементами из жидкости в процессе лазерного облучения, отличающегося тем, что в целях повышения износостойкости перед лазерным облучением осуществляют пропитку стали жидкостью с легирующими элементами на органической основе.
Согласно предложенному способу проницаемый спеченный материал пропитывается легирующей жидкостью на органической основе на глубину зоны термического воздействия лазерного излучения и подвергается лазерной обработке. Наличие сообщающихся пор в исходном материале позволяет реализовать несколько благоприятных для процесса насыщения легирующими элементами эффектов. Легирующая среда однородно распределяется по внутреннему объему необходимой зоны (достаточна пропитка на глубину оплавляемого лазером слоя), что повышает контактную устойчивость соединения «легирующий элемент – материал матрицы». Массоперенос атомов легирующего элемента (углерода) осуществляется по механизму термокапиллярной конвекции по объему всей ванны расплава, что гораздо эффективнее гидролучевой имплантации термоионизированных компонентов легирующей жидкости в поверхность материала. При этом более низкая теплопроводность заполненных инфильтратом пор сдерживает распространение теплового фронта, локализуя его на необходимом участке, что позволяет использовать меньше энергии лазерного излучения.
Таким образом, данный способ отличается от известного тем, что насыщение стали легирующими элементами происходит не только с внешней поверхности контакта материала с жидкостью, но и из порового пространства, заполненного легирующей жидкостью.
Разработанный способ основывается на использовании неотъемлемого качества структуры порошковых материалов – пористости – для интенсификации ЛХТМ. В этом проявляется одно из положительных свойств структурной неоднородности материалов при их модифицировании.
Реализованный выше подход актуален при разработке процессов лазерного газофазного легирования порошковых материалов. В целях изучения процессов фазо- и структурообразования, выбора и обоснования схем и методов ЛХТМ из газовой фазы проведено исследование лазерного газофазного цементирования стали СП90 с различной по-
98
ристостью на лазерном комплексе ЛТ1-2М при плотностях потока энергии (1,6; 3,2)108 Вт/м2 и скорости транспортировки образцов 0,4·10–2 м/с. Легирующим газом служила углекислота (расход 5·10–2 л/с), подаваемая через насадок с дистанции 20 см до обрабатываемой поверхности.
В целях оптимизации насыщения образующегося в ходе ЛХТМ расплава продуктами эрозии (плазмы) и легирующим газом реализована возможность влияния на интенсивность плазмообразования вариации давления газа в области облучения. При этом использована важнейшая характеристика порошковых сталей (порог газопроницаемости), определяющая интенсивность газотранспортных реакций при химикотермической обработке, а также формирование структуры и свойств азотированных порошковых сталей. Известно, что порог газопроницаемости порошковых углеродистых и легированных сталей определяется средней пористостью материала, его химическим составом, структурой и наследственностью, может меняться в ходе химико-термической обработки ввиду протекания процессов диссоциации и восстановления и составляет 5–15 % доли открытых пор к общей пористости материала. На основании этого созданы специальные устройства, позволяющие осуществлять инфильтрацию газовой среды из активной области плазмообразования через внутриобъемное открытое поровое пространство порошковой стали при различном давлении.
Устройство – изостатический резервуар 3 (рис. 44) – является элементом установки для лазерной обработки, включающей в себя также источник лазерного излучения (лазер на рисунке не указан) и газовую магистраль 4. Обрабатываемый материал 7 устанавливают в паз 6 резервуара 3 и закрепляют. Газ через поры материала попадает на обрабатываемую поверхность, а выпускной клапан поддерживает давление постоянным, что обеспечивает однородность свойств обрабатываемой поверхности. Таким образом, в экспериментах по лазерному газофазному цементированию использована разработанная установка, отличающаяся тем, что для повышения качества обработки путем получения однородных свойств материала устройство подачи газа выполнено в виде изостатического газового резервуара с патрубком подвода газа и выпускаемым регулировочным клапаном. Устройство закрепления детали размещено на стенках резервуара со стороны источника лазерного излучения, при этом на внутренней поверхности боковых стенок выполнен паз для размещения в нем детали.
99
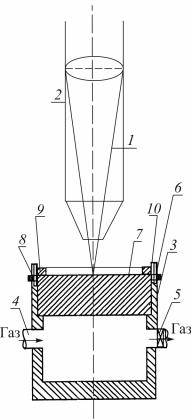
Рис. 44. Установка для лазерной обработки: 1 – лазерное излучение; 2 – фокусирующая система; 3 – изостатический резервуар; 4 – газовая магистраль; 5 – выпускной клапан; 6 – паз резервуара; 7 – обрабатываемый материал; 8 – прокладка; 9 – прижимной крепеж; 10 – винт крепежа
Следует отметить, что один из недостатков предложенной установки состоит в невозможности предотвращения разбрызгивания расплава при обработке в режиме оплавления под воздействием избыточного давления газа в резервуаре. В связи с этим предложена более совершенная конструкция камеры – устройство для лазерного химико-терми- ческого модифицирования спеченных проницаемых сталей, в котором для увеличения твердости и износостойкости изделие 5 (рис. 45) закрепляется фиксирующим механизмом 4 в посадочном вырезе 7 выходного окна 8 газостатической камеры 9, в которой вакуумным насосом 10 создается разрежение, величина которого может регулироваться вакуумным клапаном 11. Через сопло 2 с газоподводящим клапаном 3 коаксиально лазерному излучению подается на поверхность изделия газовая
100