
Промышленная экология. Утилизация крупнотоннажных отходов производс
.pdfБетоны на основе золошлаковых отходов изготавливают и на бесцементном вяжущем, полученном из этих же отходов.
Кирпич, керамика и другие обожженные материалы
В настоящее время накоплен значительный опыт использования отходов ТЭС для производства обожженного кирпича и других керамических изделий, особенно стеновой керамики.
Проблема утилизации золошлаковых отходов ТЭС для производства стеновой керамики решается по двум основным направлениям. Первое – применение в качестве эффективной добавки к основному сырью на действующих кирпичных заводах взамен традиционных материалов. Второе – использование в виде основного сырья для производства стеновой керамики на специализированных предприятиях, расположенных в непосредственной близости от ТЭС.
По результатам систематических исследований массовых топливосодержащих отходов разработаны и опубликованы «Технические условия на золу ТЭС, пригодную для производства керамического кирпича и камней», «Указания по испытанию золы и золошлаковой смеси ТЭС как добавок при производстве стеновых керамических изделий» и «Рекомендации по выбору и использованию золошлаковой смеси отвалов ТЭС в производстве стеновых керамических изделий». Указанными нормативными документами регламентированы требования к отходам ТЭС, применяемым в качестве добавки, методы их испытания и особенности промышленного производства стеновой керамики с вводом в глиняную массу золы.
Характерной особенностью кирпича на основе зол являются устойчивые и высокие показатели прочности при изгибе. Он выдерживает 50 циклов попеременного оттаивания и замораживания и по этому показателю относится к марке МР3-50.
На основе зол возможно получение и других, помимо кирпича, керамических изделий (фасадная плитка, плитка для полов), а также золоситаллов.
Из других направлений утилизации зол ТЭС для производства строительных материалов можно указать следующие.
61
Зола сухого отбора пригодна для применения в производстве асфальтовых бетонов, выполняя роль дефицитного минерального порошка, вместо которого часто используют цемент.
Перспективной является утилизация ЗШС для подсыпок при строительстве дорог, площадок под крупные объекты, насыпей под железнодорожное полотно, засыпок шахтных выработок. При этом целесообразно смешение золошлаков с природным грунтом с целью получения большей плотности и прочности.
Центробежное грохочение ЗШС и обогащение золы-уноса электросепарацией позволяют получить зольные щебень и песок, гранулирование – зольный гравий.
Возможно также применение золы и шлаков ТЭС в производстве кровельных рулонных материалов, для заполнения околотрубного пространства нефтяных скважин.
В последние годы выявляется новое направление в переработке зол – плавление в печах Ванюкова (ПЖВ) с получением материалов, по свойствам не уступающих гранулированным доменным шлакам.
4.4.3. Утилизация в металлургии
Золы могут представлять интерес как потенциальный источник техногенного сырья для металлургии, поскольку в их состав входят соединения железа и цветных металлов.
Известна технология комплексной переработки каменноугольных зол на глинозем и портландцемент [8].
В процессе производства глинозема сода регенерируется и возвращается в технологический цикл. Образующийся при данной технологии побочный продукт представляет собой материал, по химическому составу подобный белитовому шламу обычного глиноземного производства. Он содержит: 30,2 % SiО2; 3,0 % А12О3;
0,40 % Fe2О3; 57,1 % СаО; 0,85 % MgO; 0,25 % SО3; 2,5 % R2О.
Реализация технологии комплексной переработки зол на глинозем и портландцемент в значительной степени базируется на оборудовании цементного завода, следовательно, время и затраты
62
на освоение данной технологии на нем существенно сокращаются. При этом производительность печи обжига цементного клинкера возрастет на 20–25 %, расход топлива снизится на 15–18 %. Предварительные расчеты показывают, что рентабельность производства может составить 50 % при сроке окупаемости 2–3 года.
В Казахском политехническом институте (г. Алма-Ата) была изучена комплексная переработка зол экибастузских углей на глинозем и железный концентрат. Магнитная сепарация показала, что при напряженности магнитного поля порядка 119,5 кА/м при сухом и 83,5 кА/м при мокром методе из золы удается выделить до 10 % магнитной фракции в первом случае и 4–5 % во втором. Содержание Fe2О3 в основной немагнитной фракции снижается с 4 до 2,2– 3,2 %. В магнитной фракции доля железа достигает 41–43 %, или
60 % по Fe2О3.
Перспективным представляется направление в области использования золы, связанное с извлечением из нее железа, цветных, особенно редких металлов.
Известна технология производства окатышей из тонкоизмельченных железорудных концентратов и отходов, в которой наряду с известью в качестве одного из компонентов вяжущей композиции применяют 2,5–5 % зольной пыли (зольно-известковое вяжущее) – патент № 1574719 Великобритании.
4.4.4. Использование в качестве адсорбента и наполнителя
Большие возможности утилизации золы связаны с ее сорбционными свойствами. По составу она близка к природным неорганическим катионитам класса пермутита, особенно при гидрозолоудалении. Активным адсорбентом по отношению к органическим малодиссоциирующим соединениям типа нефтяных загрязнений выступают также несгоревшие частицы угля, присутствующие в золе.
Статическая емкость золы по катионам металлов составляет: 3–10 мг/г Сu, 2–5 мг/г Zn, 4–6 мг/г Рb. Поскольку она не слишком велика, золу целесообразно использовать только для очистки сла-
63
бозагрязненных сточных вод. Степень очистки зависит от количества вводимой золы. Опыты показывают, что при концентрации Сu, Zn, РЬ в исходном растворе на уровне 0,25–6,6 мг/л расходом золы, достаточным для снижения содержания металлов до следов, является 3 мг/л. Увеличение кислотности раствора подавляет сорбцию металлов.
Опытно-промышленные испытания золы ТЭЦ при очистке сточных вод Усть-Каменогорского свинцово-цинкового комбината (Казахстан) показали возможность ее использования в следующих случаях: применение золы взамен извести на существующих очистных сооружениях; смешение стоков с золопульпой в насосной станции с последующей транспортировкой смеси в золоотвал и ее нейтрализацией.
Контрольные вопросы
1.Дайте определение понятий «зола и топливные шлаки».
2.Классификация отходов ТЭС.
3.Каков состав ЗШМ по ГОСТу?
4.Каковы основные пути утилизации отходов ТЭС?
5.Какие строительные материалы получают из отходов ТЭС?
64
ГЛАВА 5. ОТХОДЫ ХИМИЧЕСКИХ ПРОИЗВОДСТВ
Предприятия химической промышленности относятся к числу производств со значительным выходом крупнотоннажных отходов. Разработка мероприятий по их утилизации способствует предотвращению загрязнения окружающей среды, а также улучшению эффективности химических производств за счет снижения затрат, преобразования технологических процессов, расширения ассортимента продукции.
5.1. Классификация отходов химических производств
Классификация отходов химических производств представлена на рис. 5.1.
Распределение веществ по классам опасности:
I класс опасности (чрезвычайно опасные) – наличие в отходах высокотоксичных веществ, таких как ртуть, сулема, хромовокислый калий, треххлористая сурьма, бенз(а)пирен, оксид мышьяка
идр.;
II класс опасности (высокоопасные) – наличие в отходах менее токсичных веществ, таких как хлористая медь, хлористый никель, трехокисная сурьма, азотнокислый свинец и др.;
III класс опасности (умеренно опасные) – сернокислая медь, щавелевокислая медь, хлористый никель, оксид свинца, четыреххлористый углерод и др.;
IV класс опасности (малоопасные) – сернокислый марганец, фосфаты, сернокислый цинк, хлористый цинк.
5.2.Количество, химический состав и свойства
Внародном хозяйстве страны образуется более 50 видов гипсосодержащих отходов. Значительная их доля образуется на неорганических и органических производствах химической промышленности.
65
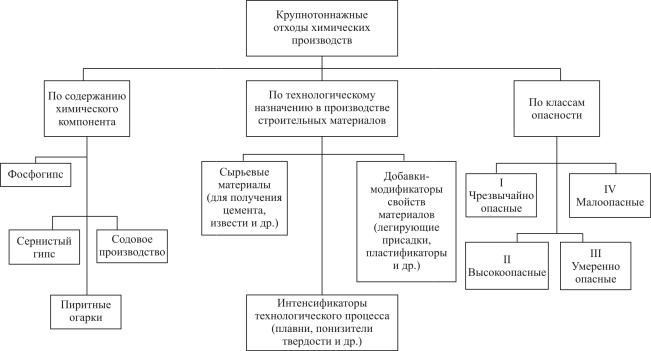
66
Рис. 5.1. Классификация отходов химических производств
Основная часть этих отходов представлена дигидратом сульфата кальция (CaSО4·2H2О), но их примеси в зависимости от генезиса материалов различаются по химическому и фазовому составам. К наиболее часто встречающимся гипсосодержащим отходам относятся следующие отходы.
Фосфогипс – отход сернокислотного производства фосфорных удобрений, экстракционной фосфорной кислоты. В зависимости от вида исходного сырья, используемого для получения экстракционной фосфорной кислоты и фосфорных удобрений, различают апатитовый и фосфоритовый фосфогипс.
Апатитовый фосфогипс образуется при переработке апатитовых концентратов на фосфорную кислоту и фосфорные удобрения. Фосфоритовый фосфогипс является побочным продуктом сернокислотного разложения фосфоритовых руд. Апатитовый фосфогипс преобладает, так как апатиты составляют основное (до 80 %) сырье, добываемое для производства фосфорной кислоты и фосфорных удобрений.
Фосфогипс – весьма крупнотоннажный отход химической промышленности, образующийся в количестве 4,5 т на 1 т Р2О5
впроизводстве экстракционной фосфорной кислоты. Ежегодные объемы его накопления в мире составляют 120–130 млн т. В отвалах России складировано до 300 млн т шлама фосфогипса. Занимаемая ими площадь достигает 1000 га. Используется всего 10–15 % отхода,
втом числе при производстве строительных материалов – 4 %. Шлам тонкодисперсен: содержит 40–55 % фракции менее 10 мкм (в возрасте до 8 мес.), имеет удельную поверхность 3400–4300 см2/г.
Фосфоритовый фосфогипс отличается большим (до 10 %) со-
держанием SiО2, отражающим особенности исходного сырья, меньшим количеством SО3 (37–39 %) и Н2О (16–18 %) при доле гидратированных сульфатных соединений кальция на уровне 83– 85 %. В состав последних в обоих типах фосфогипса в различных отношениях входят дигидрат и полугидрат сульфата кальция.
67
Следует отметить возможную радиоактивность фосфогипса, величина которой зависит от содержания радиоактивных элементов, прежде всего Ra-226, в исходном сырье.
Сернистый гипс – продукт химического жидкофазного способа улавливания SО2 из отходящих газов ряда предприятий, особенно ТЭС и ТЭЦ за рубежом. Начало внедрения метода относится к 70-м гг. ХХ в. Суть его заключается в улавливании SО2 известковым, иногда известняковым, молоком. При этом последовательно образуются сульфит и сульфат кальция. Последний переходит
вгипс. За рубежом он получил название REA-Gips.
В1996 г. общее количество REA-Gips в мире составляло около 15 млн т, в том числе в Германии около 5 млн т, США и Канаде – 3 млн т, столько же в Японии и на Тайване, в России – 60 тыс. т.
Другие виды гипсовых отходов можно отнести к попутным продуктам получения монокарбоновых и дикарбоновых органических кислот.
Внастоящее время в переработку довольно широко вовлечены наиболее крупнотоннажные гипссодержащие отходы – фосфогипс и сернистый гипс.
Пиритные огарки – побочные продукты обжига серного колчедана (пирита) при получении серной кислоты. На 1 т кислоты образуется около 2 т отходов в виде пиритных огарков. Ежегодное образование этих отходов в России оценивается в 5–6 млн т при общем объеме складирования 15–20 млн т и уровне использования порядка 80 %.
Рациональное использование пиритных огарков является составной частью общей задачи – комплексной переработки минерального сырья. Как правило, они содержат: 45–47 % Fe; 0,36– 0,44 % Cu; 0,38–0,94 % Zn; 0,03–0,06 % Рb; 0,5–4,6 % S; 0,04– 0,07 % As. Кроме этих основных компонентов, в них встречаются золото (1,6–1,8 г/т), серебро (8,4–20,8 г/т), редкие, в частности, рассеянные элементы [2].
Отходы содового производства образуются при производст-
ве кальцинированной соды (Na2CО3), ежегодный мировой выпуск
68
которой находится на уровне 40 млн т. Основной технологией ее получения служит метод Сольвэ, на долю которого приходится 80 % продукта. Исходным сырьем является хлористый натрий. Общемировой объем отходов содового производства превышает 300 млн м3/год. Количество образующихся твердых отходов (ТОС) на каждую тонну соды равно 200–250 кг, а дистиллерной жидкости
9–10 м3.
На территории России более 40 млн т ТОС находятся в шламонакопителях и ежегодно увеличиваются на 1 млн т. На основном предприятии по производству каустической соды «Сода» (г. Стерлитамак, Башкортостан) в шламонакопителях, занимающих 500 га земли, находится более 20 млн т отходов и около 17 млн м3 дистиллерной жидкости (ДЖ). По расчетным данным, шламонакопитель находится на грани исчерпания своей возможности.
Химический состав ТОС: 1,8 % SiО; 1,9 % Al2О3 +Fe2О3; 45,5 % CaО, в том числе 1,6 % CaОакт; 4,2 % MgО; 3,8 % SО32–; 9,4 % Cl–. Ему соответствует следующий минералогический состав:
61,5 % CaCО3; 2,6 % Ca(ОH)2; 9,6 % CaCl2; 6,0 % NaCl; 5,0 % CaSО4. Средняя влажность 44 %. ТОС представляет собой в высушенном состоянии светло-серый порошок, 80 % которого составляют частицы размером 0,1–0,6 мм. Состав дистиллерной жидкости (суспензии): общее содержание солей 120 г/л, не более 110 г/л Cl–, менее 0,8 г/л SО4, не более 40 г/л Ca2+, 25–30 г/л твердых веществ. Плотность ДЖ ~1,12 г/см3, рН 10–11.
Основные направления утилизации отходов химической промышленности рассматриваются ниже.
5.3.Нормы образования химических отходов
Всоответствии со сборником удельных показателей образования отходов производства и потребления нормы образования химических отходов ТЭС представлены в табл. 5.1.
69
|
|
Таблица 5.1 |
Нормы образования химических отходов |
||
|
|
|
Технологический процесс или |
Наименование |
Значениеудельных |
вид производства |
образующихся отходов |
показателей, т/т |
|
и попутных продуктов |
продукции |
Производство серной кислоты |
Шлам серный (пирит- |
0 590–0 900 |
контактным способом |
ные огарки) |
|
Производство серной кислоты |
Шлам серный (пирит- |
0 600–0 660 |
башенным способом |
ные огарки) |
|
Производство серной кислоты |
Шлам серный (пирит- |
0 102 |
на установке СК-28 |
ные огарки) |
|
Производство кальцинирован- |
Дистиллерная жид- |
8 139–10 500 |
ной соды (на предприятиях |
кость (сульфатный рас- |
0 124 |
содового производства) |
твор) |
|
|
Осадок после дистил- |
|
|
ляции или отстаивания |
|
|
раствора (шлам) |
|
Производство аммиачной се- |
Шлам (от фильтрации) |
0 010 |
литры |
|
|
Производство экстракционной |
Фосфогипс-дигидрат |
4 239 |
фосфорной кислоты на основе |
(сухой) |
|
апатита (дигидратной 100 % |
|
|
Р2О5) |
|
|
Производство экстракционной |
Фосфогипс-полугидрат |
3 590 |
фосфорной кислоты на основе |
(сухой) |
|
апатита (полугидратной |
|
|
100 % Р2О5) |
|
|
Производство экстракционной |
Фосфогипс-дигидрат |
5 428 |
фосфорной кислоты на основе |
(сухой) |
|
фосфорита Каратау (100 % |
|
|
Р2О5) |
|
|
Производство простого су- |
Раствор фторсодержа- |
0 070 |
перфосфата (18 7 % Р2О5) |
щий (10 % Н2SiF6) |
|
Производство двойного су- |
Раствор фторсодержа- |
0 235 |
перфосфата поточного |
щий (10 % Н2SiF6) |
|
(43 % Р2О5) |
|
|
Производство хлористого ка- |
Галитовые отходы |
4 000 |
лия (обогащенных калийных |
|
|
удобрений) |
|
|
70 |
|
|