
Разработка технологии гетерогенной реакции в системе газ-жидкость (90
..pdfМИНИСТЕРСТВО ОБРАЗОВАНИЯ И НАУКИ РОССИЙСКОЙ ФЕДЕРАЦИИ
Государственное образовательное учреждение высшего профессионального образования
«КАЗАНСКИЙ ГОСУДАРСТВЕННЫЙ ТЕХНОЛОГИЧЕСКИЙ УНИВЕРСИТЕТ»
РАЗРАБОТКА ТЕХНОЛОГИИ ГЕТЕРОГЕННОЙ РЕАКЦИИ В СИСТЕМЕ ГАЗ-ЖИДКОСТЬ
Учебное пособие к лабораторному практикуму по общей химической технологии
Казань
КГТУ
2011
УДК 66
Разработка технологии гетерогенной реакции в системе газ-жидкость:
учебное пособие к лабораторному практикуму по общей химической технологии / И.М.Кузнецова, Э.В.Чиркунов, Х.Э.Харлампиди – 2-е изд. перераб. и доп. Казань: Каз. госуд. технол. ун-т , 2011, 49 с.
Пособие предназначено для обучения студентов методу разработки технологии гетерогенной реакции, постановке технологического эксперимента с составлением статистической модели технологического процесса, а также формирования представления об инновационной деятельности инженера при модернизации существующих промышленных систем.
Подготовлено на кафедре Общей химической технологии.
Печатается по решению научно-методической комиссии по проблемам качества в образовании и методологии инженерной деятельности.
Рецензенты: О.В.Угрюмов, докт. техн. наук, зам. генерального директора ОАО «НИИНефтепромхим»; В.П.Тутубалина, докт. техн. наук, проф. каф. ТЭС КГТУ
2
ВВЕДЕНИЕ
При создании учебного пособия авторы преследовали следующие цели:
∙обучение студентов методу разработки технологии гетерогенной реакции на основе ее технологической классификации;
∙ознакомление студентов с понятием технологического эксперимента и практикой его постановки;
∙формирование представления об инженерной деятельности в области модернизации существующей промышленной системы на основе результатов системного анализа.
Вкачестве объекта исследования был выбран процесс жидкофазного окисления парафина кислородом воздуха (система ГАЗ-ЖИДКОСТЬ) до синтетических жирных кислот
(СЖК).
Вкниге отсутствует строгое разграничение теоретической и экспериментальной частей. Ее структура построена на чередовании теоретической и прикладной сторон исследования. Это чередование осуществляется в последовательности реализации вышеупомянутых целей.
Теоретическая часть в целом предназначена для закрепления лекционного материала
ииспользования его прикладной стороны при решении рассматриваемой проблемы. Экспериментальная часть предназначена для преобразования полученных знаний в
умения.
Теоретические закономерности, необходимые для реализации поставленной задачи проектирования технологии гетерогенной реакции, отделены от экспериментальной части рамкой.
Экспериментальная часть работы в свою очередь складывается из логического проектирования технологии перед выполнением физических экспериментов для получения количественных оценок эффективности принятых на основе теоретического проектирования решений.
Заключительная часть работы посвящена реализации третьей цели.
Используемые для обоснования инновационных инженерных решений по проблеме модернизации промышленного производства СЖК данные получают из результатов критического системного анализа. Применяются следующие его принципы: для установления структуры выполняется декомпозиция системы «сверху вниз», то есть на подсистемы и далее на операторы; выявление взаимосвязей между ними и оценки эффективности выполняемых функций.
Критический анализ функционирования производственной системы с позиций современных достижений науки и техники позволяет выявить недостатки устаревших технологий, оборудования и принятых способов выделения целевых продуктов, в подсистемах экологизации и пр.
Напоминаем, что технология является наукой экономической, поэтому при оценке качества выполняемых новой предлагаемой системой или ее элементами функций следует использовать комплексный критерий «затраты-эффективность-реализуемость».
Если затраты превышают полученный эффект, а реализация принятого решения невозможна в технически приемлемых условиях, следует рассмотреть альтернативные варианты решения проблемы.
Экспериментальные данные для разработки статистической модели, а также исследование статических характеристик химико-технологического процесса окисления парафина получают на лабораторной установке.
3
Методики расчетов необходимых данных для составления математической модели, снятия материального баланса, скоростей реакции и сопровождающего ее процесса массопередачи приведены в приложениях либо непосредственно в тексте.
Методология и методики работы по реализации 1-ой цели изложены в разделе II, 2 – ой цели – в разделе III.
Проблемы модернизации промышленного производства СЖК (3-я цель) изложены в комментарии для преподавателей.
4
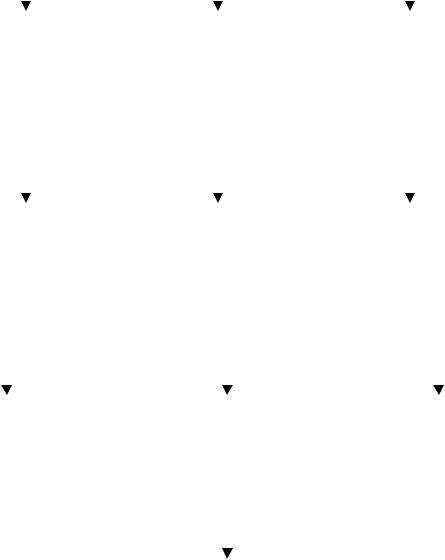
Cхема поэтапной разработки технологии реакции [1]
|
|
|
ИСХОДНАЯ ИНФОРМАЦИЯ |
|
|
|
|
|
О ПРОЦЕССЕ |
|
|
|
|
|
|
|
|
ЭТАП I |
|
Источники информации: патенты, |
|
||
|
периодика (журналы), монографии, |
|
|||
|
|
|
|
||
|
|
|
производственные отчеты, |
|
|
|
|
|
производственный опыт операторов |
|
|
|
|
|
|
|
|
|
|
|
|
|
|
|
|
Сырье |
|
|
|
|
|
Механизм и |
|
|
|
|
Фазовое состояние |
|
|
|
||||||||||
|
|
и |
|
|
|
|
|
химизм |
|
|
|
|
системы на стадии |
|
|
|
||||||||||
|
продукты |
|
|
|
|
|
реакции |
|
|
|
|
|
|
|
химического |
|
|
|
||||||||
|
|
|
|
|
|
|
|
|
|
|
|
|
|
|
|
|
|
|
превращения |
|
|
|
||||
|
|
|
|
|
|
|
|
|
|
|
|
|
|
|
|
|
|
|
|
|
|
|
|
|
|
|
|
|
|
|
|
|
|
|
|
|
|
|
|
|
|
|
|
|
|
|
|
|
|
|
|
||
|
|
|
|
|
|
|
|
CТРАТЕГИЯ ПРОЕКТИРОВАНИЯ |
|
|
|
|
|
|
|
|
|
|
|
|
|
|||||
|
ЭТАП II |
|
|
|
|
ТЕХНОЛОГИИ РЕАКЦИИ |
|
|
|
|
|
|
|
|
|
|
|
|
|
|||||||
|
|
|
|
|
|
|
|
|
|
|
|
|
|
|
|
|
|
|
|
|
|
|
||||
|
|
|
|
|
|
|
|
|
Технологическая классификация |
|
|
|
|
|
|
|
|
|
|
|
|
|
||||
|
|
|
|
|
|
|
|
|
|
реакции |
|
|
|
|
|
|
|
|
|
|
|
|
|
|||
|
|
|
|
|
|
|
|
|
|
|
|
|
|
|
|
|
|
|
|
|
|
|
|
|
||
|
|
|
|
|
|
|
|
|
|
|
|
|
|
|
|
|
|
|
|
|
|
|
|
|||
|
Выбор |
|
|
|
|
|
Выбор факторов |
|
|
|
|
|
|
Выбор типа |
|
|
||||||||||
|
критериев |
|
|
|
|
интенсификации реакции и |
|
|
|
|
математической |
|
|
|||||||||||||
|
оптимизации, |
|
|
|
|
|
сопровождающих ее |
|
|
|
модели процесса |
|
|
|||||||||||||
|
|
y |
|
|
|
|
физических процессов хi. |
|
|
|
|
|
|
|
|
Yi=F(xi). |
|
|
||||||||
|
|
|
|
|
|
|
|
|
|
|
Планирование |
|
|
|||||||||||||
|
|
|
|
|
|
|
|
|
|
Ввод ограничений |
|
|
|
|
|
|
|
|
||||||||
|
|
|
|
|
|
|
|
|
|
|
|
|
|
|
эксперимента |
|
|
|||||||||
|
|
|
|
|
|
|
|
|
|
|
|
|
|
|
|
|
|
|
|
|
||||||
|
|
|
|
|
|
|
|
|
|
|
|
|
|
|
|
|
|
|
|
|
|
|
|
|||
|
|
|
|
|
|
|
|
|
|
|
|
|
|
|
|
|
|
|
|
|||||||
|
ЭТАП III |
|
|
ТЕХНОЛОГИЧЕСКИЙ ЭКСПЕРИМЕНТ |
|
|
|
|
|
|
|
|
|
|
|
|||||||||||
|
|
|
|
|
|
|
|
|
|
|
|
|
|
|
|
|
|
|
|
|
|
|
||||
|
|
|
|
|
|
|
|
|
|
|
|
|
|
|
|
|
|
|
|
|
|
|
|
|
|
|
|
|
|
|
|
|
|
|
|
|
|
|
|
|
|
|
|||||||||||
|
|
|
|
|
|
|
|
|
|
|
|
|
|
|
|
|
|
|
|
|
|
|
|
|
|
|
Проектирование |
|
|
|
|
|
Реализация плана эксперимента |
|
|
|
|
|
Выбор методов |
||||||||||||||
|
реактора и |
|
|
|
|
|
Расчет коэффициентов модели |
|
|
|
|
|
|
контроля и |
||||||||||||
лабораторной |
|
|
|
|
|
|
Оптимизация модели |
|
|
|
|
|
|
управления |
||||||||||||
|
установки. |
|
|
|
|
Снятие материального баланса процесса |
|
|
|
|
|
|
процессом |
|
||||||||||||
|
Монтаж |
|
|
|
|
Расчет технологических показателей |
|
|
|
|
|
|
Параметры |
|||||||||||||
|
установки |
|
|
|
|
|
Разработка принципиальной |
|
|
|
|
|
технологического |
|||||||||||||
|
|
|
|
|
|
|
|
|
технологической схемы |
|
|
|
|
|
|
режима |
||||||||||
|
ЭТАП IV |
|
|
|
|
|
|
|
|
|
|
|||||||||||||||
|
|
|
|
|
|
|
|
|
|
|
|
|
|
|
|
|
|
|||||||||
|
|
|
|
|
|
|
|
|
|
|
|
|
|
|
|
|
|
|||||||||
|
|
|
|
|
|
|
|
|
|
|
|
|
|
|
|
|
||||||||||
|
|
|
|
|
СИСТЕМНЫЙ АНАЛИЗ ХТС |
|
|
|
|
|
|
|
|
|
|
|
||||||||||
|
|
|
|
|
|
|
|
|
ОФОРМЛЕНИЕ ОТЧЕТА |
|
|
|
|
|
|
|
|
|
|
|
||||||
|
|
|
|
|
|
|
|
|
|
|
|
|
|
|
|
|
|
|
|
|
|
|
|
|
|
|
5

I.ОБЩИЕ СВЕДЕНИЯ
1.1.Исходная информация
1.1.1.Характеристика сырья и продуктов
Реакция окисления углеводородов положена в основу производства различных классов кислородсодержащих соединений, таких как кислоты, спирты, альдегиды, кетоны и пр.
К числу наиболее крупнотоннажных продуктов окисления парафиновых углеводородов относятся высшие жирные кислоты.
|
|
ЦЕЛЕВЫЕ ПРОДУКТЫ |
РЕАКЦИИ ОКИСЛЕНИЯ |
→ |
ВЫСШИЕ ЖИРНЫЕ |
ПАРАФИНА: |
|
КИСЛОТЫ (СЖК)* |
Высшие жирные кислоты составляют основную группу сырья для промышленности тонкого и тяжелого органического синтеза. Поскольку в результате реакции образуется смесь кислот различной молекулярной массы, то в качестве товарной продукции заводы СЖК поставляют не отдельные кислоты, а их фракции (рис.1.1).
С Ы Р Ы Е Ж И Р Н Ы Е К И С Л О Т Ы
фракция С5- |
фракция С7-С9 |
фракция С10-С16 |
фракция С17-С20 |
C9 |
|
|
|
Синтетичес- |
пластификаторы, |
мыловарение |
мыловарение |
кие масла для |
ПАВ, |
(заменитель |
(хозяйственное |
авиационных |
деэмульгаторы, |
кокосового масла в |
мыло), лаки, |
двигателей |
флотореагенты |
производстве |
краски, смазочные |
|
|
туалетного мыла) |
материалы) |
Рис.1.1. Товарные фракции СЖК и основные направления их использования
СЫРЬЕ. В промышленной практике наиболее распространены два способа получения СЖК на основе разных видов сырья:
-жидкофазное каталитическое окисление твердого (tпл.=40-60оС, tкип.=350-450оС) и жидкого (tпл.=7-13оС, tкип.=240-270оС) нефтяных парафинов, получаемых в процессе депарафинизации масляных и дизельных фракций нефти. В качестве окислителя применяется воздух;
-гидрокарбоксилирование α-олефинов:
\ |
/ |
\ |
/ |
C |
= C |
+ СO + H 2O → − C − С |
− COOH |
/ |
\ |
/ |
\ |
Последний способ отличается высокой экологичностью, но приводит к получению большого числа малопригодных для синтеза ПАВ изомерных кислот.
1.1.2. Функциональная схема промышленной установки производства СЖК показана на рис.1.2.
* СЖК - синтетические жирные кислоты.
6
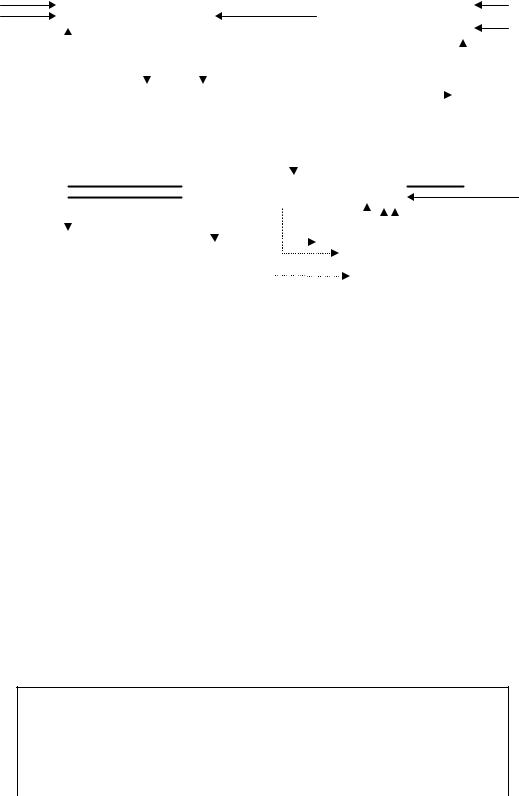
I |
|
|
|
|
|
|
|
XVI |
|
|
|
|
|
|
|
|
|
|
|
|
|
|
|
III |
|
|
|
ПОДСИСТЕМА |
|
|
|
ПОДСИСТЕМА |
|
|
|||||||||||||||||
|
|
|
|
|
|
|
|
|
|
|
|
||||||||||||||
II |
|
|
ПОДГОТОВКИ СЫРЬЯ |
|
|
|
|
ПРИГОТОВЛЕНИЯ |
|
|
|
|
|
|
|||||||||||
|
|
|
|
|
|
|
|
|
|
КАТАЛИЗАТОРА |
|
|
|
|
IV |
||||||||||
|
|
|
|
V |
VI |
|
|
|
|
|
|
||||||||||||||
|
|
|
|
|
|
|
|
|
|
|
|||||||||||||||
|
|
|
|
|
|
|
|
|
|
|
|
|
|
|
|
|
|
|
|
||||||
|
XV |
|
|
|
|
|
|
|
|
|
|
|
XIV |
|
XVII |
||||||||||
|
|
|
|
|
|
|
|
|
|
|
|
|
|||||||||||||
|
|
|
|
|
|
|
|
|
|
|
|
|
|
|
|
|
|||||||||
|
|
|
|
|
|
|
|
|
|
|
|
|
|
|
|
||||||||||
|
|
|
|
|
|
ПОДСИСТЕМА |
|||||||||||||||||||
|
|
|
|
|
|
|
|
|
|
|
|
|
|
||||||||||||
|
|
|
|
|
|
|
|
|
|
|
|
|
|
||||||||||||
|
|
|
|
|
|
ХИМИЧЕСКОГО ПРЕВРАЩЕНИЯ |
|
|
|
|
|
|
|
|
|||||||||||
|
|
|
|
|
|
|
|
|
|
|
|
|
|
|
|
|
|
|
|
|
|
|
|
|
|
|
|
|
|
|
|
|
|
|
VII |
|
|
|
|
|
|
||||||||||
|
|
|
|
|
|
|
|
|
|
|
|
|
|
|
|
|
|
|
|
|
XII |
||||
|
|
|
|
|
|
|
|
|
|
|
|
|
|
|
|
|
|
|
|
|
|
|
|
||
|
|
|
|
|
|
|
ПОДСИСТЕМА РАЗДЕЛЕНИЯ |
|
|
|
|
|
|
|
|||||||||||
|
|
|
|
|
|
|
|
|
|
|
|
||||||||||||||
|
|
|
XI |
|
|
РЕАКЦИОННОЙ СМЕСИ |
|
|
|
|
|
|
|
|
|||||||||||
|
|
|
|
|
|
|
|
|
|
|
|
|
|
||||||||||||
|
|
|
|
|
|
|
|
X |
XIII |
|
|
|
|
|
|
|
IX |
||||||||
|
|
|
|
|
|
|
|
|
|
||||||||||||||||
|
|
|
|
|
|
|
|
|
|
|
|
|
|
|
|
|
|
|
|
|
|
|
|
|
|
|
|
|
|
|
|
|
|
|
|
|
|
|
|
|
|
|
|
|
|
|
|
|
|
VIII |
|
|
|
|
|
|
|
|
|
|
|
|
|
|
|
|
|
|
|
|
|
|
|
|
|
||
|
|
|
|
|
|
|
|
|
|
|
|
|
|
|
|
|
|
|
|
|
|
|
ХVIII |
||
|
|
|
|
|
|
|
|
|
|
|
|
|
|
|
|
|
|
|
|
|
|
|
Рис.1.2. Функциональная схема производства СЖК.
I - парафин; II - воздух; III - водный раствор MnSO4 или MnO2; IV,VIII - водный раствор NaOH; V - смесь свежего и возвратного парафинов с катализаторным комплексом; VI - воздух очищенный; VII - оксидат; IX - серная кислота; X - водный раствор Na2SO4; XI - промывная вода; XII - вода на промывку; XIII - фракции кислот; XIV - абгаз реактора окисления; XV - возвратный парафин, XVI - катализатор, XVII-кислоты для приготовления катализатора; XVIII – водный раствор Na2CO3.
Полученный в процессе окисленный парафин (техническое название "оксидат") является сложной смесью непревращенного парафина (конверсия ~60%) и кислородсодержащих соединений кислого и нейтрального характера (рис.1.3). Условия процесса: 125оС, удельный расход воздуха 80 м3/т.час, концентрация катализатора 0,07% масс. Mn, считая на парафин.
Для выделения целевого продукта из этой смеси используют реакции нейтрализации
кислот: |
|
2RCOOH + Na2CO3 → 2RCOONa + H2O + CO2 |
(1.1) |
и омыления эфиров: |
|
RCOOR1 + NaOH → RCOONa + R1OH . |
(1.2) |
Из омыленной массы отгоняют неомыляемые (возвратный парафин). Образовавшиеся мыла (натриевые соли высших кислот) разлагают серной кислотой. Смесь сырых кислот промывают водой и разгоняют на фракции.
Термическая обработка осуществляется при 350оС и давлении 13 МПа. В результате жестких условий процесса теряется до 25% от потенциала кислот.
О К И С Л Е Н Н Ы Й П А Р А Ф И Н
Ж И Р Н Ы Е К И С Л О Т Ы |
Н Е О М Ы Л Я Е М Ы Е |
|
(32-35%) |
(60%) (возвратный парафин) |
|
Свободные |
Связанные |
Непревращенный парафин |
жирные кислоты |
жирные кислоты |
RH, спирты ROH, кетоны |
RCOOH |
RCOOR1 и пр. |
RCOR1 и пр. |
Рис.1.3. Состав окисленного парафина
7
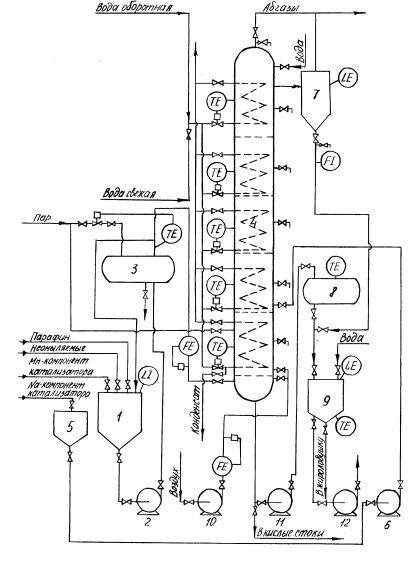
Рис.1.4. Технологическая схема непрерывной установки окисления парафина
1 - емкость для приготовления сырьевой смеси; 2,6,11,12 - насосы; 3 - теплообменник для подогрева сырьевой смеси; 4 - реактор окисления; 5 - емкость для натриевого компонента катализатора; 7 - сепаратор;
8,9 - емкости для оксидата; 10 – компрессор.
Реакторы промышленной установки работают в периодическом режиме.
Окисление смеси свежего и возвратного парафинов с катализатором на основе MnO2 проводят в аппаратах колонного типа, снабженных барботером для распределения воздуха и змеевиком для нагрева и охлаждения реакционной смеси.
После реконструкции промышленный реактор окисления (рис.1.4, поз.4) представляет собой прямоточный колонный аппарат, разделенный на секции непровальными ситчатыми тарелками с целью уменьшения эффекта продольного перемешивания и организации понижающегося температурного режима. Для съема реакционного тепла в каждой секции установлены змеевиковые теплообменники.
8
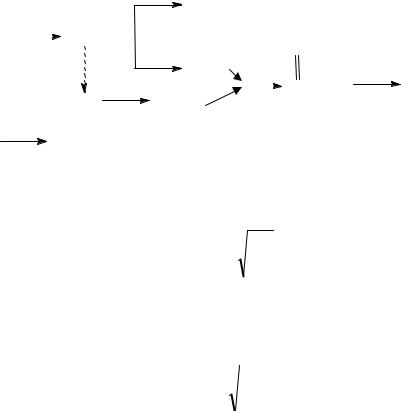
II.ПОДСИСТЕМА ХИМИЧЕСКОГО ПРЕВРАЩЕНИЯ
2.1.Механизм реакции и химическая схема синтеза
Химико-технологический процесс окисления углеводородов (RH) в жидкой фазе протекает по механизму цепных вырожденно-разветвленных реакций, который может быть записан в следующем виде:
RH+O2→R×+HO2×-221 кДж/моль |
зарождение цепей |
2RH+O2→2R×+H2O2-259 кДж/моль |
|
R×+O2→RO2×+80 кДж/моль |
продолжение цепей |
RO2×+RH→ROOH+R×+50 кДж/моль |
|
ROOH→RO×+OH×-146 кДж/моль |
вырожденное |
ROOH+RH→RO×+H2O+R×-71 кДж/моль |
разветвление цепей |
2ROOH→RO×+H2O+RO2×-29 кДж/моль |
|
R×+R×→R-R+334 кДж/моль |
обрыв цепей |
R×+RO2×→ROOR+240 кДж/моль |
|
RO2×+R1O2× →ROH+RCОRI+O2+174 кДж/моль |
|
(1.3)
Целевые продукты – кислоты (RCOOH) - образуются в результате протекания многочисленных реакций, промежуточными продуктами которых являются гидропероксиды ROOH, спирты ROH, кетоны RCOR1 и альдегиды RICHO.
Химизм реакции окисления можно представить в виде последовательности нескольких стадий:
|
|
|
|
RCOOH |
|
|
|
|
|
|||
RH |
+O2 |
ROOH |
|
|
|
|
|
|
|
|
|
|
|
|
|
|
|
|
|
|
O |
||||
|
|
|
|
|
|
|
|
|
|
|
||
|
|
|
|
RCOR1 |
+O2 |
|
|
|||||
|
|
ROH +O2 RCOR1 |
|
|
RC-CH-R1 |
|||||||
|
|
|
|
|
|
|
||||||
|
|
|
|
|
|
|
|
OOH |
||||
|
|
|
|
|
|
|
|
|||||
|
RCOOH+R1CHO+680 |
|
кДж/моль |
|
||||||||
|
|
|
|
|||||||||
|
|
|
|
|
|
|
|
|
|
|
(1.4) |
|
Кинетику окисления при больших концентрациях О2 в газе можно описать |
||||||||||||
уравнением |
|
|
|
|
|
|
|
|
||||
|
|
|
|
W o = k |
2 |
[R H ] |
|
W i |
, |
(1.5) |
||
|
|
|
|
|
||||||||
2 |
|
|
|
k 6 |
||||||||
|
|
|
|
|
|
|
|
|
|
|
где Wi - общая скорость зарождения цепей; k2, k6 - константы скорости продолжения и
квадратичного обрыва цепи на радикалах |
|
RO∙ |
соответственно; [RH] - концентрация |
||||||
|
|
|
2 |
|
|
|
|
|
|
углеводорода. |
|
|
|
|
|
|
|
|
|
При низких концентрациях О2 кинетика окисления описывается как |
|
||||||||
W o = k |
1 |
[O |
2 |
] |
|
W i |
|
, |
(1.6) |
|
|||||||||
2 |
|
|
|
k 4 |
|||||
|
|
|
|
|
|
|
9
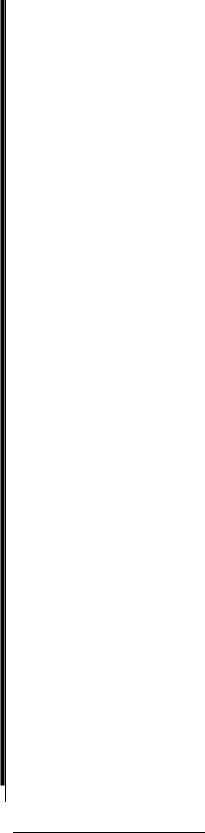
где k1, k4 - константы скорости зарождения и квадратичного обрыва цепи на радикалах R∙ ; [O2] - концентрация кислорода в углеводороде.
2.2. Понятие технологии. Факторы. Критерии эффективности процесса
Разработка технологии химико-технологического процесса заключается в поиске
оптимальных условий его проведения.
Оптимальные условия затем реализуются в конструкции реактора и превращаются в параметры его работы.
Условия проведения процесса можно представить совокупностью физических воздействий (факторов) Xi на химически реагирующую систему. Взаимодействия факторов приводят к изменениям в состояниях системы, выражающихся в изменении интенсивности протекающих в ней процессов.
В зависимости от выбранных методов1 и силы воздействий можно ожидать появления большого числа соответствующих состояний системы. Среди них могут оказаться лучшие и худшие варианты. Поэтому задача исследователя будет заключаться в поиске такой совокупности факторов, которая обеспечит состояние системы, отличающееся от прочих лучшими значениями критериев, то есть показателей, выбранных для оценки эффективности этих факторов в достижении поставленной цели.
К числу основных технологических факторов относят:
∙состав исходной смеси реагентов (растворителей, абсорбентов, катализаторов и пр.) – концентрация, С;
∙параметры состояния: температура Т и давление Р;
∙параметры потока реагентов: объемная скорость Vо, интенсивность перемешивания n;
∙параметры потока катализатора: условная объемная скорость УОС, условное время контакта τк, кратность циркуляции Кц, величина загрузки G;
∙свойства катализатора: активность А, селективность S, пористость ε, размер гранул d, радиус пор rп, поверхность f и пр.;
∙параметры силовых полей (магнитного, электрического, акустического): напряженность Н и потенциал ϕ, частотные характеристики ν и пр.
В качестве технологических критериев (критериев оптимизации) Yi совершенства технологии обычно используют скорость процесса (реакции, -rA),
селективность (S) и конверсию (αA).
Часто условия, обеспечивающие высокую скорость реакции, не соответствуют критерию высокой селективности. Поэтому в процессе поиска выбирают в качестве цели либо режим высокой скорости, либо высокой селективности.
2.3. Технологическая классификация реакций
Многоцелевой и многофакторный характер химико-технологического процесса осложняет задачу разработки технологии.
Существенную помощь в решении этой проблемы оказывает технологическая классификация реакции [1].
Химические реакции классифицируют по следующим категориям: химизму и механизму процесса; фазовому состоянию реагентов и катализаторов; величине и знаку теплового эффекта; порядку реакции; молекулярности; способу активации системы.
Напоминаем, что по признаку химизма реакция может быть отнесена к классу простых и сложных, обратимых и необратимых. Это позволяет выбрать технологические критерии оптимизации (показатели эффективности воздействия факторов).
1 Термоактивация, катализ, фотохимическая активация, плазмохимическая активация, механохимическая активация и др.
10