
Изучение энергетических характеристик активной турбины на модельном однофазном и двухфазном рабочем теле (120
..pdf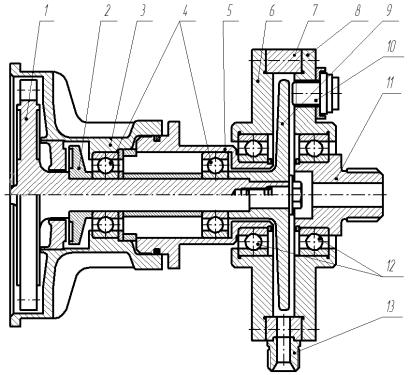
Рис. 1.3. Общий вид рабочего участка:
1 – ротор турбины; 2 – импеллерный гидрозатвор; 3, 5 – части корпуса турбины; 4 – подшипники турбины; 6, 7, 8 – части корпуса гидротормоза; 9 – диск гидротормоза; 10 – датчик оборотов; 11 – станина гидротормоза; 12 – подшипники корпуса гидротормоза; 13 – штуцер для подсоединения магистрали подачи рабочей жидкости в гидротормоз
Воздух подается к газоводу 46 из ГГ через дозирующий вентиль 4. Смешиваясь с продуктами горения в газоводе, воздух поступает на турбину 31. Выхлоп из турбины происходит в окружающую среду. Воспламенение компонентов в ГГ осуществляется авиационной искровой свечой 26. Спирт поступает в ГГ 25 из бака 10 через дозирующий вентиль 11, фильтр 14 и отсечный пневмоклапан 15, управляемый электропневмоклапаном (ЭПК) 16. Система подачи спирта – вытеснительная. Для быстрого прекращения горения в ГГ в случае возникновения нештатной ситуации из водяного бака 41 к ГГ подведена отдельная магистраль к отсечному клапану 20, управляемому ЭПК 19.
11
2.3. Описание рабочего участка
Питание гидротормоза водой происходит из бака 41 через вентили
39 и35.
Рабочий участок включает объект испытаний – турбину 31 – и механическое нагрузочное устройство турбины в виде гидравлического тормоза 36. Рабочее колесо турбины 31 и дисковый ротор гидротормоза установлены на одном валу и вращаются совместно. Гидротормоз позволяет изменять потребляемую мощность в широком диапазоне в зависимости от частоты вращения вала. Гидротормоз – это агрегат, где потребляемая мощность сознательно превращается в потери, так как тепловая энергия, в которую преобразуется механическая энергия торможения, полезно не используется. Принцип действия гидротормоза заключается в торможении вращающегося диска силами трения жидкости, находящейся в зазоре между диском и неподвижным корпусом. Глубина погружения (поверхность трения) диска определяется равновесием центробежных сил, стремящихся отбросить жидкость к периферии гидротормоза, и сил давления подачи, выдавливающими жидкость к центру. Изменяя уровень заполнения рабочей полости гидротормоза водой, тем самым меняя площадь контакта жидкости с диском и корпусом гидротормоза, можно в широком диапазоне регулировать нагрузку на турбину.
Для снятия характеристик одноступенчатой активной парциальной турбины с использованием дискового гидротормоза газ из ГГ через сопловый аппарат, состоящий из одного сопла с косым срезом (на рис. 1.3 не показан), поступает на рабочие лопатки турбины. Ротор турбины 1 опирается на шарикоподшипники 4, установленные в частях 3 и 5 разборного корпуса. Подшипники турбины 4 для надежной работы требуют смазки и охлаждения, в двигательных установках обеспечиваемые жидкими компонентами топлива.
В данной установке для охлаждения подшипников организован проток воды в корпусе, подаваемой из автономной магистрали. Для обеспечения стойкости подшипники и корпус турбины выполнены из нержавеющей стали. Газовую полость турбины и полость с опорами вала, заполненную водой, разделяет гидрозатвор 2, выполненный на основе импеллера (гидродинамического уплотнения). Принцип его работы основан на запирании жидкости, поступающей под давлением, в зазоре между корпусом и диском, создающими противодавление. Диск гидротормоза 9 посредством шпонки соединен с валом турбины. Корпус гидротормоза, образо-
12
ванный крышками 6, 8 и кольцом 7, установлен на шарикоподшипниках 12 и может свободно поворачиваться относительно корпуса турбины и станины 11. Это позволяет использовать корпус гидротормоза как датчик крутящего момента. Крутящий момент, развиваемый турбиной, передается через вал к диску гидротормоза, а от него через вязкую жидкость (воду), заполняющую внутреннюю полость, на корпус гидротормоза. Момент, воспринимаемый корпусом гидротормоза, отличается от крутящего момента турбины только на значение момента трения в подшипниках гидротормоза (который пренебрежимо мал). Для предотвращения вскипания жидкости (следовательно, резкого уменьшения трения и тормозящего момента, что может привести к неконтролируемому разгону турбины) в конструкции гидротормоза предусмотрено обновление жидкости в рабочей полости путем подачи воды через штуцер 13 и слива ее через специальное отверстие.
Крутящий момент, передаваемый жидкостью на корпус гидротормоза через плечо L = 0,02 ...0,15 м (выставляется при тарировке, чтобы не превысить усилие 50 Н), воспринимается датчиком усилия ВСА-5L и через электронное силоизмерительное устройство типа С1-5010А с визуальным контролем в виде аналогового сигнала передается на оцифровку в плату ввода данных. Режимы и управление работой стенда настраиваются с выносного пульта.
3. Методика проведения испытания
3.1. Основные измеряемые параметры
Характеристика газовой турбины определяется при постоянной скорости истечения газа из сопла с1, обеспечиваемой постоянными давлением и температурой газа на входе в турбину. Разные значения окружной скорости и на среднем диаметре лопаток турбины получают при изменении числа оборотов вала регулированием нагрузки на валу с помощью гидротормоза.
Температуру и давление на входе в турбину задают по указанию преподавателя. Частота вращения вала турбины во время эксперимента устанавливается трех-четырех уровней в диапазоне 600…1500 рад/с посредством изменения расхода воды через гидротормоз с помощью вентиля 35 (см. рис. 1.2).
Все измерения проводят после выхода турбины на заданный режим по команде «Замер» специальной измерительной системой сбора и расшифровки экспериментальных данных.
13
При этом измеряют следующие величины:
1)полное давление на входе в турбину p1 , МПа;
2)статическое давление на выходе из турбины р2 (принимается равным атмосферному давлению), МПа;
3)температуру на входе в турбину T0т, К;
4)перепад давления газа на шайбе рт, МПа;
5)частоту вращения ротора турбины ω, рад/с;
6)усилие на статоре гидротормоза Р, Н.
Результаты измерений вносят в таблицу.
3.2.Порядок проведения испытаний
1.После открытия вентилей 3 и 5 с помощью редуктора 7 проводится наддув бака горючего 10 до давления 1,6 МПа, которое контролируется с помощью манометра 9 (см. рис. 1.2).
2.С помощью редуктора 45 проводится наддув водяного бака 41 до давления 6 МПа, контролируемого манометром 40.
3.Давление привода отсечных клапанов 15 и 20 для подачи горючего на форсунку 24 обеспечивается с помощью редуктора 17 посредством электропневмоклапанов 16 и 19 и контролируется манометром 18. Редуктор 17 предварительно настроен на давление за ним, равное 4,5 МПа.
4.С целью охлаждения подшипников турбины и гидротормоза
спомощью вентиля 47 предварительно подается вода из водопровода.
5.Для ограничения частоты вращения турбины при выходе на режим полость гидротормоза 36 полностью заполняется водой посредством полного открытия вентиля 35.
6.Для запуска газогенератора (при «горячих» испытаниях) открывают вентили 22 и 23, при этом редуктор 21 предварительно настраивают на давление за ним, равное 0,5–0,8 МПа, а затем открывают отсечные клапаны 15, 20 и одновременно подают напряжение на электросвечу 26.
7.После запуска ГГ выход его на номинальный режим обеспечивается балластировкой продуктов сгорания воздухом с помощью подстройки вентиля 4 и редуктора 21. Номинальный режим
работы ГГ соответствует давлению перед турбиной p1 , равному 10 МПа, и температуре перед ней T0 т 500 К.
8.Изменение режимов работы турбины в дальнейшем обеспечивается за счет увеличения частоты ее вращения путем уменьшения расхода воды в гидротормоз с помощью регулируемого венти-
14
ля 35. Контроль частоты вращения осуществляется с помощью датчика оборотов 32, сигнал от которого поступает на электронный частотомер и отображается на его дисплее с размерностью – Гц.
ВНИМАНИЕ! Показания частотомера не должны превышать
400…450 Гц.
4. Методика регистрации результатов эксперимента на ЭВМ
4.1. Описание регистрирующих элементов системы измерения
Частота вращения ротора определяется индукционным датчиком оборотов 10 (рис. 1.2). Температура рабочего тела перед турбиной измеряется с помощью хромель-алюмелевой термопары.
Давление рабочего тела перед турбиной измеряется потенциометрическим датчиком давления типа ДТ или МД, а расход рабочего тела определяется по перепаду давления на дроссельной шайбе при помощи дифференциального датчика перепада давления типа МДДФ-УК.
Крутящий момент, развиваемый турбиной, измеряется с помощью тензометрического датчика усилий типа ВСА-5L и электронного устройства С1-5010А.
Указанные первичные датчики преобразуют измеряемые физические параметры в электрические сигналы, поступающие затем на регистрирующие приборы. Сигналы с первичных преобразователей направляются на пульт управления установкой и встроенную в ЭВМ плату ввода данных L-305 с визуализацией на экране дисплея в темпе эксперимента.
Для обработки результатов эксперимента и расчета энергетических характеристик используется автоматизированный программный комплекс TurboLab, разработанный на кафедре «Ракетные двигатели».
4.2. Описание программного комплекса TurboLab
Программа TurboLab предназначена для регистрации параметров в процессе проведения лабораторных работ по исследованию характеристик турбины и определению основных параметров. Программа работает в операционной среде Windows и позволяет записывать в оперативную память компьютера текущие измеряемые параметры, проводить расчет основных характеристик турби-
15
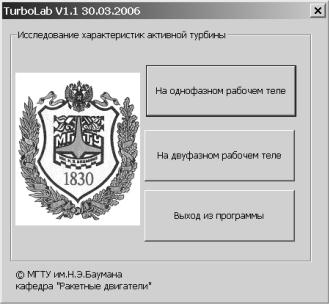
ны и по окончании испытания формировать файл отчета в формате HTML, позволяет также в автоматизированном режиме проводить градуировку датчиков.
В начале работы следует включить компьютер и запустить TurboLab. При этом происходит загрузка драйверов и тестирование платы устройства сопряжения модели L-305. При нормальном функционировании платы и драйверов появляется основное меню
(рис. 1.4).
Рис. 1.4. Меню выбора лабораторной работы
Программа позволяет проводить регистрацию и расчет характеристик активной турбины на однофазном и двухфазном рабочем теле. Выбор лабораторной работы осуществляется из меню (рис. 1.4) нажатием соответствующей экранной кнопки. После чего программа переходит в режим настройки параметров. В заголовке окна возникает вид лабораторной работы.
В программе предусмотрено несколько режимов работы:
1)настройка параметров;
2)отображение измеряемых величин;
3)калибровка датчиков;
4)замеры и создание отчета.
16
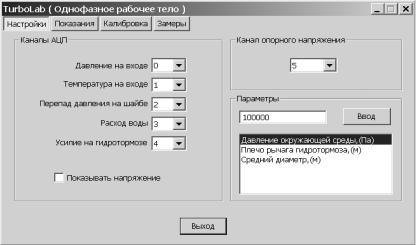
Переключение между режимами осуществляется нажатием соответствующих пунктов меню в верхней части окна программы.
Режим настройки параметров программы. После выбора ла-
бораторной работы переходят в режим настройки нажатием кнопки главного меню «Настройки» (рис. 1.5).
Рис. 1.5. Окно настройки параметров
«Каналы АЦП» – выбор канала АЦП для каждого регистрируемого параметра.
«Показывать напряжение» – показывать в режиме мониторинга считываемые значения в вольтах вместо единиц физических величин.
«Канал опорного напряжения» – выбор канала АЦП опорного напряжения, необходимого для более точной регистрации значений потенциометрических датчиков
«Параметры» – ввод параметров окружающей среды и геометрических параметров турбины.
Режим отображения измеряемых величин. Переход осуществ-
ляется нажатием кнопки главного меню «Показания», после чего открывается окно, показанное на рис. 1.6.
В режиме «Показания» на экране дисплея отображаются текущие значения напряжений или физических величин, а также графики изменения этих величин во времени.
17
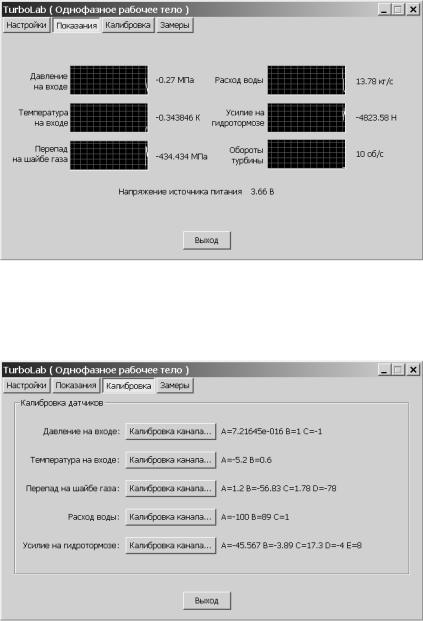
Рис. 1.6. Окно отображения параметров
Режим калибровки датчиков. Переход осуществляется нажатием кнопки главного меню «Калибровка», после чего открывается окно, показанное на рис. 1.7.
Рис. 1.7. Меню режима калибровки датчиков
18
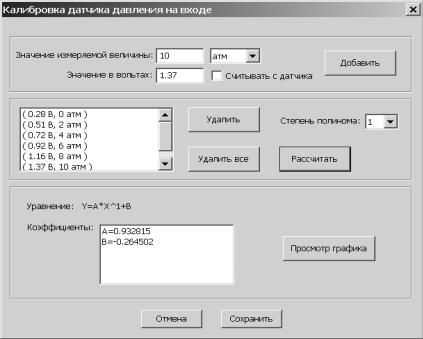
Вэтом режиме возможна выборочная калибровка следующих каналов: Давление на входе, Температура на входе, Перепад на шайбе газа, Расход воды и Усилие на гидротормозе. Данные по оборотам турбины считывают по цифровому каналу с частотомера, поэтому этот канал не калибруется.
Вправой части окна для каждого датчика показаны коэффициенты аппроксимирующего полинома. Диалоговое окно калибровки датчиков вызывается нажатием соответствующей экранной кнопки «Калибровка канала…». Вид окна калибровки на примере датчика давления показан на рис. 1.8
Рис. 1.8. Окно калибровки канала измерения
Для выхода из режима калибровки канала с сохранением результатов необходимо нажать экранную кнопку ОК. Для выхода из режима без сохранения результатов необходимо нажать экранную кнопку «Отмена».
Показанные в окне поля обеспечивают следующее.
19
«Значение измеряемой величины» – в это поле вводится значение измеряемой физической величины, единица измерения которой назначается из выпадающего списка справа.
«Значение в вольтах» – в это поле вводится значение в вольтах, соответствующее значению единицы физической величины.
«Считывать с датчика» – если это поле отмечено, то показания датчика в вольтах будут автоматически считываться с датчика, в противном случае его вводят вручную.
«Добавить» – добавляет содержимое полей «Значение измеряемой величины» и «Значение в вольтах» к списку.
«Удалить» – удаляет выбранные данные из списка. «Удалить все» – очистка списка.
«Степень полинома» – выбор степени аппроксимирующего полинома. Возможно задавать полином 1–4-й степени.
«Рассчитать» – расчет по методу наименьших квадратов значений коэффициентов аппроксимирующего полинома на основе сформированных данных.
«Уравнение» – после расчета коэффициентов в этой строке отображается вид аппроксимирующего полинома (символ ^ озна-
чает степень, т. е. А*Х^2+B*X^1+C = A·X2+B·X+C). «Коэффициенты» – после расчета коэффициентов в этом поле
отображаются коэффициенты аппроксимирующего полинома. «Просмотр графика» – показ окна с графиком, построенным по
рассчитанным коэффициентам и исходными данными. По оси абсцисс откладывается напряжение в вольтах, а по оси ординат – единица измеряемой физической величины. Маркерами показаны введенные при калибровке данные. Вид окна с графиком показан на рис. 1.9. Полученные аппроксимирующие зависимости используют в дальнейшем при представлении результатов регистрации параметров работы установки.
Режим замера и создания отчета. Переход осуществляется нажатием кнопки главного меню «Замеры», после чего открывается окно, показанное на рис. 1.10.
Функционирование на данном режиме осуществляется с помощью следующих команд. В поле «Исходные параметры» отображаются исходные параметры, считываемые с датчиков, в поле «Расчетные параметры» – некоторые из расчетных параметров. При нажатии кнопки «Ручной ввод» происходит вызов диалогового окна для ручного ввода исходных параметров.
20