
Расчет пропеллерной мешалки для суспензирования (90
..pdfФедеральное агентство по образованию
Государственное образовательное учреждение высшего профессионального образования
«Казанский государственный технологический университет»
РАСЧЕТ ПРОПЕЛЛЕРНОЙ МЕШАЛКИ ДЛЯ СУСПЕНЗИРОВАНИЯ
Методические указания к курсовому проектированию
Казань
КГТУ
2007
УДК 532:66.02
Маминов О. В., Ильяшенко Е. Б., Костромин В. П., Мухутдинов Э. А.
Расчет пропеллерной мешалки для суспензирования: метод. ука- зания. / сост. О. В. Маминов [и др.]. – Казань: Изд-во Казан. гос. тех-
нол. ун-та, 2007. – 41 с.
Приведены методические указания расчета пропеллерной мешал- ка для приготовления суспензии и механический расчет лопасти про- пеллера.
Предназначены для студентов всех специальностей, выполняю- щих курсовой проект по дисциплине «Процессы и аппараты химиче- ской технологии». Могут быть использованы студентами механиче- ских и технологических специальностей при работе над курсовыми и дипломными проектами. Представлено проведение расчета в про- грамме.
Подготовлены на кафедре процессов и аппаратов химической тех- нологии.
Печатаются по решению методической комиссии кафедры ПАХТ.
Под редакцией проф. О. В. Маминова Рецензенты: проф. КГЭУ Р. Г. Тахавутдинов
проф. КГТУ А. М. Кузнецов
СОДЕРЖАНИЕ |
|
Содержание..................................................................................................................... |
3 |
Введение.......................................................................................................................... |
4 |
Задание............................................................................................................................ |
6 |
1. Определение физических свойств суспензии......................................................... |
6 |
1.1. Определение коэффициента динамической вязкости суспензии ...................... |
7 |
1.2. Определение плотности суспензии....................................................................... |
7 |
2. Выбор сосуда для смесителя..................................................................................... |
8 |
2.1. Определение размеров сосуда............................................................................... |
8 |
2.2. Определение коэффициента заполнения.............................................................. |
8 |
3. Выбор типа и размеров мешалки (предварительный расчет) ............................. |
10 |
3.1. Выбор типа мешалки............................................................................................ |
10 |
3.2. Предварительный расчет трехлопастной пропеллерной мешалки.................. |
11 |
4. Оптимизация процесса перемешивания................................................................ |
13 |
4.1. Основные положения по оптимизации процесса перемешивания.................. |
13 |
4.2. Составление сводных расчетных данных для мешалок ................................... |
14 |
4.3. Определение продолжительности процесса перемешивания.......................... |
15 |
4.4. Дополнительные критерии, необходимые для оптимизации........................... |
17 |
4.5. Анализ данных таблицы 1.................................................................................... |
18 |
5. Расчет смесителя для dм = 250 мм.......................................................................... |
19 |
5.1. Основные размеры аппарата................................................................................ |
19 |
5.2. Определение глубины воронки при вращении жидкости в сосуде................. |
20 |
5.3. Определение мощности привода мешалки ........................................................ |
21 |
5.3.1. Мощность, затрачиваемая на преодоление трения в уплотнениях вала |
|
мешалки ................................................................................................................ |
21 |
5.3.2. Мощность привода мешалки............................................................................ |
22 |
6. Расчет лопасти пропеллера..................................................................................... |
22 |
6.1. Расчет размеров лопасти пропеллера ................................................................. |
22 |
6.2. Расчет лопасти на прочность............................................................................... |
26 |
7. Проведение расчета в программе........................................................................... |
28 |
Приложение.................................................................................................................. |
33 |
Библиографический список ........................................................................................ |
40 |
– 3 –
ВВЕДЕНИЕ
Перемешивание жидких сред – один из наиболее распространен- ных процессов химической технологии. Перемешивание может осу- ществляться различными способами, в данном случае рассматривается только механическое перемешивание. В этом случае происходит про- цесс многократного относительного перемещения макроскопических элементов объема жидкой фазы под действием импульса, передавае- мого среде механической мешалкой, а само движение жидкой среды является вынужденным.
Механическое перемешивание используется для решения следую- щих задач: интенсификации процессов тепло- и массопереноса в том числе и при наличии химических реакций; равномерного распределе- ния твердых частиц в объеме жидкости (при приготовлении суспен- зий); для равномерного распределения и дробления до заданной дис- персности жидкостей в жидкости (при приготовлении эмульсий) и т. д.
Процесс перемешивания характеризуется эффективностью, ин- тенсивностью и расходом энергии на его проведение.
Под эффективностью перемешивания понимают технологический эффект качества проводимого процесса. В зависимости от назначения перемешивания эту характеристику выражают различным способом. Например, при получении суспензий и эмульсий эффективность пере- мешивания можно характеризовать равномерностью распределения фаз в суспензии или эмульсии.
Интенсивность перемешивания связана со временем достижения заданного технологического результата и характеризуется количеством энергии N подводимой к единице объема V перемешиваемой среды в единицу времени (N / V) или единице массы перемешиваемой среды (N / Vρ). Интенсивностью перемешивания обусловлен характер движе- ния жидкости в аппаратуре. Повышение интенсивности перемешива- ния всегда связано с увеличением энергозатрат, а технологический эф- фект от увеличения интенсивности перемешивания ограничен строго определенным пределом. Поэтому интенсивность перемешивания сле- дует определять исходя из условий достижения необходимого техноло- гического эффекта при минимальных энергозатратах. Интенсификация процесса перемешивания позволяет повысить производительность ус-
– 4 –
тановленного аппарата или снизить объем проектируемого.
В работе рассматривается процесс приготовления суспензии в ап- парате с пропеллерной мешалкой и приведено обоснование выбора данного типа перемешивающего устройства.
Сложность расчета процесса суспензирования заключается в том, что имеющиеся в учебной литературе данные не дают возможности дать детальный расчет этого процесса. Использование же иной науч- но-технической литературы затруднено для студентов тем, что теоре- тических данных для расчета недостаточно, а выбор эмпирических за- висимостей для расчета из указанной литературы для студентов за- труднителен, так как следует использовать зависимости, отвечающие реальной физической картине протекания процесса суспензирования.
Приведен выбор оптимальных размеров стандартного аппарата для перемешивания и условий его работы.
Описан метод механического расчета профиля лопасти пропел- лерной мешалки и расчет лопасти мешалки на прочность, чего нет в учебной литературе по дисциплине «Процессы и аппараты химиче- ской технологии».
– 5 –
ЗАДАНИЕ
Рассчитать аппарат с механической мешалкой для приготовления однородной по концентрации суспензии катализатора в жидкости. Как суспензия, так и вещества, входящие в нее, не являются огне- и взры- воопасными и токсичными.
Материал для изготовления аппарата: углеродистая сталь 20К. Процесс приготовления суспензии протекает при постоянной темпера- туре t = 20° С. Вещества на перемешивания подаются при той же тем- пературе.
Физические свойства исходных веществ при температуре t = 20° С. Жидкость имеет:
–плотность ρ1 = 810 кг/м3;
–коэффициент динамической вязкости μ1 = 0,4·10-3 Па·с. Катализатор имеет:
–плотность ρ2 = 2200 кг/м3;
– размеры твердых частиц примерно одинаковы и равны δ = 0,3 10-3 м, имеющие форму многогранника с равными гранями.
Аппарат для перемешивания должен быть стандартным. Порядок загрузки исходных веществ:
1.В пустой аппарат загружается катализатор в объеме самих кри- сталлов 15 литров материала катализатора.
2.В аппарат заливается жидкость в объеме 210 литров.
После загрузки начинается процесс перемешивания.
Разгрузка аппарата: готовая суспензия перетекает в трубопровод че- рез штуцер, расположенный в днище аппарата, с помощью сжатого газа.
1. Определение физических свойств суспензии
По условиям задания приведены следующие данные: t = 20°C – температура;
ρ1 = 810 кг/м3 – плотность жидкости; μ1 = 0,4·10-3 Па·с – коэффициент динамической вязкости жидкости;
V1 = 210 л = 0,21 м3 – объем заливаемой в смеситель жидкости; ρ2 = 2200 кг/м3 – плотность материала катализатора; δ = 300 мкм = 0,3·10-3 м – средний размер частиц катализатора;
V2 = 0,015 м3 – объем, занимаемый массой катализатора.
– 6 –

1.1. Определение коэффициента динамической вязкости суспензии
Объемная доля соотношения фаз суспензии (объемная концен- трация)
j = |
V2 |
= |
0, 015 |
= 0, 0714 = 7,14 %; |
|
|
|
|
|||
|
V1 |
0, 210 |
|
|
|
вязкость суспензии μс при ϕ < 10 % определяется по формуле [9] |
|||||
|
|
μс = μ1 (1 + 2,5ϕ) |
(1) |
||
μ = 0,4·10-3(1 + 2,5·0,0714) = 0,471·10-3 |
Па·с |
||||
с |
|
|
|
|
1.2. Определение плотности суспензии
Плотность суспензии ρс определяется по формуле [5]
1 |
|
|
|
|
|
1 − |
|
|
|
|
|||
= |
|
x |
+ |
x |
, |
(2) |
|||||||
r |
c |
r |
2 |
|
r |
|
|||||||
|
|
|
|
|
1 |
|
|
|
где x – массовая доля катализатора.
Масса жидкости G1 = V1ρ1 = 0,21·810 = 170,1 кг.
Масса катализатора G2 = V2ρ2 = 0,015·2200 = 33 кг.
Масса суспензии Gc = G1 + G2 = 170,1 + 33 = 203,1 кг.
|
|
|
= |
G2 |
|
= |
|
33 |
= 0,162, |
кг/кг; |
|||||||
|
|
x |
|||||||||||||||
|
|
|
|
|
|||||||||||||
|
|
|
|
|
Gc |
|
203,1 |
|
|
|
|
|
|
||||
1 |
= |
0,162 |
+ |
0,838 |
= 1,1079 |
×10 |
−3 |
|
м3 |
||||||||
|
|
|
|
|
|
|
|
|
|
, |
|
; |
|||||
rс |
2200 |
|
810 |
|
|
|
|||||||||||
|
|
|
|
|
|
|
|
|
кг |
||||||||
|
|
|
|
|
rc |
= 902,7 кг/м3. |
|
|
|
|
|
– 7 –
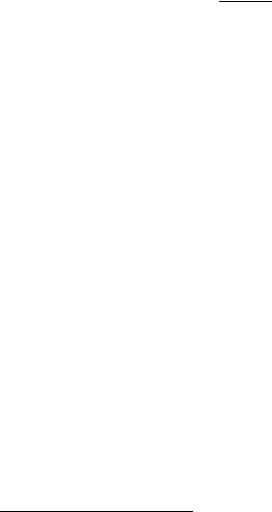
2. Выбор сосуда для смесителя
2.1. Определение размеров сосуда
Объем суспензии в сосуде Vc составляет
Vc = V1 + V2 = 0,210 + 0,015 = 0,225 м3.
Номинальный объем сосуда Vн, м3 (объем для выбора стандартно- го сосуда) определяется по формуле [3]
V = |
Vc |
, |
|
ϕ3 |
|||
н |
(3) |
||
|
где ϕ3 – коэффициент заполнения сосуда.
Для не пенящихся жидкостей ϕ3 = 0,7÷0,8 [3].
Vн = 0, 225 = 0, 280, м3. 0,8
По каталогу (табл. П1 ) принимаем ближайший по объему сосуд смесителя с Vн = 0,250 м3 с эллиптическим днищем. В дальнейшем для выбранного сосуда уточним значение коэффициента заполнения ϕ3.
Подберем основные размеры выбранного сосуда. Схема сосуда, с соответствующими обозначениями показана на рис. 1.
Эллиптическое днище имеет размеры (табл. П5): D = 700 мм – внутренний диаметр;
dв = 40 мм – диаметр вала мешалки;
hд = 175 мм – высота днища (внутренняя, по его оси); Vд =0,055 м3 – объем днища.
2.2. Определение коэффициента заполнения
Расчет ведется в соответствии с рис. 1. Поскольку объем днища Vд = 0,055 м3, то объем цилиндрической части сосуда, занятый суспен- зией, равен:
Vц1 = Vc - Vд = 0,225 – 0,055 = 0,170, м3
Индекс П означает, что данные приведены в приложении.
–8 –
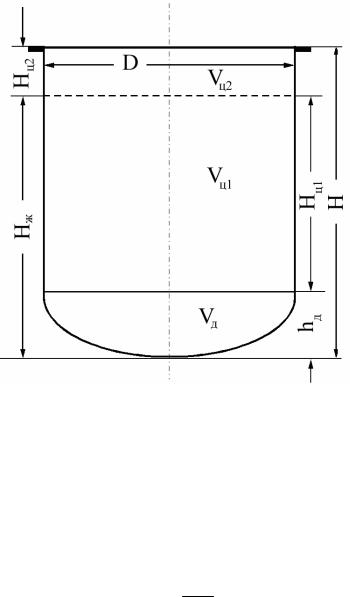
Рис. 1. Схема сосуда: D – внутренний диаметр сосуда, H – высота сосуда, Hж – высота слоя суспензии, hд – высота днища (внутренняя), Vд – объем днища, Vц1 – объем цилиндрической части сосуда, занятой
суспензией, Vц2 – свободный объем сосуда
В этом случае высота слоя суспензии, соответствующая объему Vц1, находится по формуле:
Hц1 = Vц1 ,
F
где F – площадь поперечного сечения сосуда.
F = 0,785·D2 = 0,785·0,72 = 0,385 м3;
таким образом,
Н |
|
= |
0,17 |
= 0, 443, м. |
ц1 |
|
|||
|
0,385 |
|
||
|
|
|
||
Высота слоя суспензии равна |
|
|||
H ж = hд + Hц1 = 0,175 + 0, 443 = 0, 618, м. |
||||
|
|
|
– |
9 – |
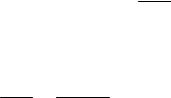
Предварительную высоту сосуда H рекомендуется определять по зависимости [8]:
Нж = k·H,
где k = 0,7÷0,75, откуда
H = Hж . k
Принимаем среднее значение k = 0,72. Тогда
H = H ж = 0,618 = 0,8583, м≈ 0,85, м. k 0, 72
Объем свободного от суспензии пространства будет равен
Vц2 = (H – H ж)·F = (0,850 – 0,618) ·0,385 = 0,089, м3.
Полный объем сосуда аппарата
Vа = Vд + Vц1 + Vц2 = 0,055 + 0,171 + 0,089 = 0,314, м3.
Действительный коэффициент заполнения
ϕ |
|
= |
0, 225 |
= 0, 716. |
3 |
|
|||
|
0, 314 |
|
||
|
|
|
Значение ϕ3 лежит в допустимых пределах ϕ3 = 0,7 ÷ 0,8 [3].
3. Выбор типа и размеров мешалки (предварительный расчет)
3.1. Выбор типа мешалки
ГОСТ 20680-75 предусматривает десять типов исполнения верти- кальных аппаратов с перемешивающими устройствами, отличающи- мися формой крышек и днищ и конструкциями мешалок. В табл. П1 приведены основные технические данные аппаратов с эллиптически- ми крышками и днищами. В табл. П2 представлены основные пара- метры и условия работы перемешивающих устройств.
Так как по условию задания необходимо получить суспензию твердого катализатора в жидкости, и катализатор подается в аппарат до его пуска, то необходимо производить его взвешивание в жидко- сти. По этой причине выбираем по табл. П2 аппарат с трехлопастной
– 10 –