
m34700
.pdf
|
91 |
|
|
Глава 5. МУФТЫ ПРИВОДОВ |
|
|
Краткое содержание |
|
* |
Расчетный вращающий момент |
5.1 |
* |
Нерасцепляемые муфты |
5.2 |
* |
Предохранительные муфты |
5.3 |
В приводах машин используются наиболее распространенные муфты двух классов: муфты нерасцепляемые, упругие и компенсирующие, муфты самодействующие, преимущественно предохранительные. Часто применяемые муфты стандартизованы.
5.1. Расчетный вращающий момент
При выборе муфт по каталогам или проектировании величина вращающего момента ТМ, нагружающего муфту в приводе, может приближенно определяться зависимостью
ТМ = kТН ,
где ТН – номинальный длительно действующий момент; k – коэффициент режима работы.
k = 1,1 … 1,4 – при спокойной работе и небольших разгоняемых при пуске массах (конвейеры, стенды испытательные и т. п.). k = 1,5 … 2,0 – при неравномерной работе с толчками и средних разгоняемых массах (мельницы, дробилки, поршневые
компрессоры).
k = 2,5 … 3,0 – при ударной нагрузке и больших разгоняемых массах.
Радиальная сила от муфты, нагружающая концы соединяемых валов из-за их несоосности, зависит от типа муфты и возможных смещений валов. Имеются рекомендации по ее вычислению. Ориентировочно в учебном проектировании радиальная сила принимается до 0,3 от окружной силы элемента передачи (зубчатого колеса, звездочки и т. п.). Направление действия силы выбирается из условия наиболее опасного влияния на прочность вала.
Справочные материалы для некоторых типов муфт приведены в приложении.
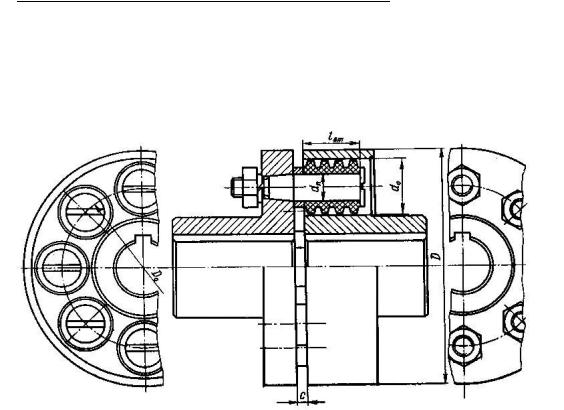
92
5.2. Нерасцепляемые муфты
Упругие и компенсирующие муфты служат для передачи крутящего момента с одного вала на другой. В процессе работы они должны в определенных пределах компенсировать ошибки изготовления, монтажа и возникающие деформации соединяемых валов. При монтаже проектируемого механизма с двигателем или исполнительным органом машины возможны осевые, радиальные, угловые или комбинированные смещения осей соединяемых муфтой валов. Так как компенсирующие муфты не могут полностью компенсировать все возможные ошибки монтажа, то возникающие перекосы и силы трения в деталях муфт вызывают дополнительные радиальные нагрузки и изгибающие моменты, нагружающие валы и их опоры сверх действующих от передач и т.п.
Рассмотрим некоторые конструкции нерасцепляемых муфт. Муфты упругие втулочно-пальцевые (МУВП) по ГОСТ
21424-93 часто находят применение в машиностроении для соединения быстроходных валов. Муфта (рис. 5.1) состоит из двух чугунных или стальных полумуфт, стальных пальцев и упругих резиновых втулок.
Рис. 5.1
Посадочные отверстия полумуфт выполняют цилиндрическими или коническими, сами полумуфты закрепляют на валах
93
шпонками, а в осевом направлении – винтами или с торца концевыми шайбами либо гайками. В пределах каждого габарита допускается соединение валов разных диаметров; при этом муфту выбирают по наибольшему диаметру вала. Характеристика муфт нелинейная – жесткость муфт является функцией угла закручивания, который не пропорционален крутящему моменту.
При угловых (более 1градуса) и радиальных (более 0,2...0,5 мм) смещениях валов происходит быстрый износ упругих втулок. Неточное расположение осей пальцев и отверстий вызывает радиальную нагрузку на валы порядка 0,1...0,3 окружной силы, действующей на пальцы муфты.
Муфты упругие со звездочкой. Муфты применяются на быстроходных валах с небольшим крутящим моментом и рекомендуются для соединения вала двигателя с валом механизма. Две полумуфты имеют на торцах кулачки, которые входят во впадины упругой звездочки. Материал звездочки – резина маслобензостойкая.
Муфты изготовляются двух типов: для малых диаметров валов (до 14 мм) звездочка имеет четыре луча, полумуфты стальные; для больших диаметров валов (до 45 мм) звездочка имеет шесть лучей. В пределах каждого габарита муфты в полумуфтах допускается любое сочетание диаметров посадочных отверстий. Муфты имеют малые габариты, нелинейную характеристику жесткости, обладают хорошими демпфирующими свойствами, компенсируют радиальные смещения валов до 0,2 мм и угловые до 1,5 градуса.
Муфты зубчатые по ГОСТ 50895-96. Муфты широко используют в промышленности для соединения быстроходных и тихоходных валов. Они обладают большой несущей способностью при небольших габаритах и массе, просты в монтаже, надежны в работе. Широко применяются в грузоподъемных машинах.
Твердость рабочей поверхности зубьев не ниже 40 HRC. Отверстия втулок могут быть расточены под цилиндрический или конический конец вала. На торцах втулок имеются резьбовые отверстия под съемник для удобства демонтажа. Зубчатые муфты обеспечивают значительную компенсацию смещения валов (радиальные, угловые или их комбинацию), при этом перекос оси каждой втулки относительно оси обоймы допускается до половины градуса. При
94
несоосности валов происходит скольжение профилей зубьев, вызывающее их износ. Неравномерность распределения нагрузки между зубьями и по их длине создает дополнительные нагрузки на валы в пределах 0,2...0,4 от окружной силы на делительном диаметре зубчатого венца втулки. Для уменьшения износа внутреннюю полость муфты заливают жидким маслом. Для устранения утечек масла предусматривают уплотнения между обоймами и втулками, а при наличии шпонок – шпоночного паза.
Для тихоходных валов находят применение цепные муфты.
5.3. Предохранительные муфты
Для многих исполнительных механизмов характерно возникновение перегрузок, сопровождающихся значительными динамическими нагрузками элементов машины, в том числе деталей привода. К перегрузкам приводят неправильно выбранные технологические режимы работы машины при несоответствии производительности рабочих агрегатов и мощности энергетической установки. Затупление и другие нарушения нормальной работоспособности рабочих органов, а также изменчивость состояния обрабатываемого материала затрудняют поддержание такого соответствия при эксплуатации машин.
Большинство механизмов сельхозтехники подвержены возможным аварийным перегрузкам в результате попадания в рабочие органы посторонних предметов.
Предохранительные муфты ограничивают нагрузки систем передач и исполнительных механизмов машин, защищают от перегрузки двигатель. Выбор величины вращающего момента срабатывания предохранительной муфты и ее конструктивных особенностей зависит от характера перегрузки – технологической или аварийной (стопорной).
Требования к конструкции предохранительной муфты для привода с большей важностью защиты ведущей (относительно предохранительной муфты) части привода (деталей передач) следующие:
1)повышенная точность срабатывания муфты;
2)увеличенный момент инерции ведущей части предохранительной муфты.
95
Чаще встречаются системы с опасностью повреждений при стопорной перегрузке исполнительных механизмов (деталей рабочих органов). Здесь основные требования к конструкции предохранительной муфты будут:
1)малый момент инерции ведомой части муфты;
2)повышенные упругие свойства ведомой части муфты.
Из-за инерционного характера перегрузки точность срабатывания муфты в этом случае имеет меньшее значение. Совмещение в одной конструкции указанных непротиворечивых требований возможно. Однако для удовлетворения двух из них - повышенной точности срабатывания и повышенных упругих свойств – требуются большие затраты.
Основные типы предохранительных муфт: с разрушающимся элементом, фрикционные, кулачковые, шариковые. Последние три типа муфт стандартизованы.
Строгая соосность ведущей и ведомой частей предохранительных муфт является обязательным условием их нормальной работы. Поэтому она должна располагаться на одном валу, а соединение с другим валом осуществляется за счет комбинации с соединительной муфтой (комбинированные муфты).
Муфты с разрушающимся элементом применяются при малой вероятности перегрузок. Конструкции разрушающихся элементов - штифтов, выполняемых из хрупких металлов (серый чугун, бронза, силумин, сталь и др.). В момент перегрузки штифт срезается и муфта разъединяет кинематическую цепь.
Для замены срезанных штифтов в круглых фланцах полумуфт делают отверстия большого диаметра (рис 5.2).
При повороте полумуфт относительно друг друга до совмещения срезанных штифтов с этими отверстиями штифты удаляются.
Уменьшить осевые размеры муфты можно за счет конструктивного решения.
Фрикционные предохранительные муфты отличаются от фрикционных сцепных отсутствием управления. Сила на поверхностях трения создается постоянно замкнутыми пружинами, обычно цилиндрическими, витыми или тарельчатыми. Наибольшее распространение получили многодисковые муфты (рис. 5.3).
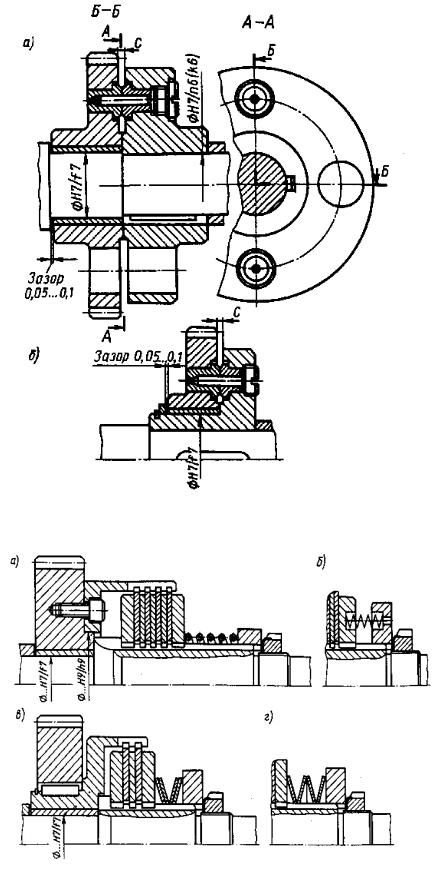
96
Рис. 5.2
Рис. 5.3
97
При срабатывании муфта передает момент, на который она отрегулирована. После снятия перегрузки проскальзывание прекращается, и нормальная работа привода возобновляется. Из-за интенсивного нагрева поверхностей трения при проскальзывании продолжительные перегрузки не допускаются.
Кулачковые и шариковые предохранительные муфты применяются в машиностроении при небольших скоростях и моментах. При проскальзывании полумуфт происходит динамическое нагружение деталей муфты и привода.
Комбинированные муфты чаще получают объединением соединительной, компенсирующей смещение осей валов, и предохранительной муфт. Число возможных вариантов конструктивных исполнений велико.
Действуют стандарты на основные типы предохранительных муфт:
фрикционные - ГОСТ 15622 - 77 для диаметров валов от 9 до 48 мм и крутящих моментов 6,3...400 Нм;
пружинно-кулачковые - ГОСТ 15620 - 77 для валов 8...48 мм и крутящих моментов 7...400 Нм;
пружинно-шариковые - ГОСТ 15621 - 77 для тех же валов и моментов.
В сельхозмашиностроении используются отраслевые стандарты с расширенным диапазоном диаметров валов и крутящих моментов.
|
98 |
|
|
Глава 6. СОЕДИНЕНИЕ ДЕТАЛЕЙ МАШИН |
|
|
Краткое содержание |
|
* Шпоночные, шлицевые и безшпоночные соединения |
6.1 |
|
* |
Резьбовые соединения |
6.2 |
* |
Сварные соединения |
6.3 |
* |
Анализ производственных ситуаций |
6.4 |
* Руководство пользователя системами автоматизиро- |
|
|
|
ванного проектирования соединений |
6.5 |
Фиксация взаимного положения деталей и сборочных единиц машин осуществляется формозапиранием, зацеплением и сцеплением (фрикционным, электромагнитным и др.). Для этого применяют различные конструктивные способы, используя отдельные части соединяемых деталей, дополнительные детали, - механические связи (например, шпонки, болты, штифты и др.), технологические процессы (сварка, склеивание и др.), формирующие молекулярно - механические связи между деталями.
Надежность работы конструкции часто определяется работоспособностью соединений.
6.1. Шпоночные, шлицевые и безшпоночные соединения
Для закрепления деталей на осях и валах используют шпоночные, шлицевые, прессовые, затяжные конусные и профильные соединения.
Соединения призматическими шпонками применяют в конструкциях наиболее широко, так как они просты в изготовлении и имеют сравнительно небольшую глубину врезания в вал. Основным является расчет на смятие (упругопластическое сжатие в зоне контакта). У стандартных шпонок сечение (ширина и высота) подобрано так, что напряжение среза шпонки менее опасно, чем напряжение смятия на поверхности контакта шпонкаступица или шпонка-вал.
Для упрощения можно допустить, что шпонка врезана в вал на половину своей высоты и напряжения распределяются равномерно по высоте и длине шпонки. Тогда напряжения смятия

99 |
|
|
см 4Т / hl p d |
см , |
(6.1) |
где Т – передаваемый вращающий момент; lp – расчетная длина шпонки;
h – высота шпонки; d – диаметр вала.
Значение допускаемых напряжений зависит от режима нагрузки (постоянная, пульсирующая, знакопеременная), прочности материала вала, втулки и шпонки, типа посадки на вал. Стандартные шпонки изготовляют из чистотянутых стальных прутков
– углеродистой или легированной стали с пределом прочности не ниже 500 МПа. Для неподвижных соединений [ см] = 80…200 МПа. Меньшие значения для чугунных и алюминиевых ступиц при резких изменениях нагрузки. В подвижных в осевом направлении соединениях допускаемые напряжения значительно снижают – в два и более раз.
В алгоритмах расчета учитываются стандартные размеры шпоночных соединений.
При невозможности обеспечить работоспособность шпоночного соединения применяют шлицевые (зубчатые) соединения.
Шлицевые соединения чаще используют с прямобочным профилем (стандарт для валов диаметром до 125 мм). Эвольвентные шлицы предпочтительны при больших диаметрах валов (стандарт до 500 мм), когда проявляются их технологические преимущества. Треугольный профиль не стандартизирован.
Уточненный расчет шлицевых соединений стандартизован с учетом основных критериев работоспособности и расчета:
1)сопротивление рабочих поверхностей смятию;
2)сопротивление изнашиванию от фреттинг – коррозии (ко- розионно-механическое изнашивание при малых относительных колебательных перемещениях контактирующих поверхностей).
Допускается выполнять упрощенные расчеты по обобщенному критерию, аналогичному шпоночным соединениям, с учетом неравномерности распределения нагрузки по шлицам и других факторов.
100
Ослабление валов и ступиц деталей пазами под шпонки и шлицами можно исключить применением прессовых соединений с обеспечением натяга посадки. Сборку любого прессового соединения можно выполнить следующими способами: прессованием, нагревом втулки (ступицы), охлаждением вала.
Алгоритм расчета предусматривает как условия прочности (неподвижности) соединения в окружном и осевом направлениях под действием передаваемого крутящего момента и/или осевой силы, так и условия прочности его деталей, когда натяг вызывает разрушение или чрезмерные деформации.
Ослабление валов и ступиц деталей можно исключить применением соединений посадкой на конус. Давление на конической поверхности (стандартная конусность 1/10) образуется затяжкой гаек или технологического осевого усилия (сверло с коническим хвостовиком). В отличие от прессового, соединение легко собирается и разбирается без применения прессов. Разборка соединения упрощается, если нанести удар по боковой поверхности детали (втулки).
Соединение затяжными конусами, создающими распорные радиальные силы (давления) и на цилиндрических поверхностях вала и ступицы, аналогично прессовому, но может быть применено, когда необходимы повторные сборки и разборки, а также при действии больших крутящих моментов.
На практике часто применяют комбинацию прессового или конусного соединения со шпоночным. Сложность расчета таких соединений заключается в определении нагрузки, которую передает каждое из соединений. Поэтому используют приближенный расчет, в котором допускают, что вся нагрузка передается только одним соединением (чаще шпонкой), но допускаемые напряжения выбирают повышенными.
Профильные соединения, имеющие фасонный профиль, отличный от круглого, обеспечивают фиксирование деталей и передачу вращающего момента соединением вал-ступица. По сравнению со шпоночными и шлицевыми соединениями существенно снижается концентрация напряжений. Наиболее технологичными являются призматические профильные соединения, имеющие плоские грани (от 1 до 8) и переходные участки, очерченные дугами окружностей.