
m33170
.pdfдля изделий пластического формования и полусухого прессования: по длине – ± 5; по ширине – ± 4; по толщине (для кирпича) – ± 3; по толщине (для камня) – ± 4.
Таблица 10. Дефекты внешнего вида
Вид дефекта |
Значение |
1. Отбитости углов глубиной от 10 до 15 мм, шт |
2 |
2. Отбитости притупленности ребер глубиной не более 10 мм и |
|
длиной от 10 до 15 мм, шт |
2 |
3. Трещины протяженностью до 30 мм по постели полнотелого |
|
кирпича и пустотелых изделий не более чем до первого ряда |
|
пустот (глубиной на всю толщину кирпича или на ½ толщины |
|
тычковой или ложковой грани камней): |
|
ложковых гранях |
1 |
тычковых гранях |
1 |
Марку камня по прочности устанавливают по пределу прочности при сжатии, а кирпича – по пределу прочности при изгибе и сжатии.
Водопоглощение не должно быть для полнотелого кирпича менее 8%, для пустотелых изделий – менее 6%.
За марку по морозостойкости принимают число циклов попеременного замораживания и оттаивания, при которых в изделиях отсутствуют признаки видимых повреждений (шелушение, расслоение, растрескивание, выкрашивание и т.д.), а также изменения дефектов внешнего вида, указанных в таблице 10. Кирпич считают морозостойким, если средняя по пяти образцам потеря прочности и наименьшее значение показателя отдельного образца, установленные в таблице 11 для данной марки, не более 5%, а средняя потеря массы по пяти образцам – не более 3%.
Облицовочные материалы и изделия подразделяют на кирпич лицевой (сплошной и пустотелый), камни лицевые, ковровую керамику, малогабаритные плитки, фасадные детали. Фасадные изделия должны иметь водопоглощение от 6 до 14% и морозостойкость не ниже МРЗ 25.
61
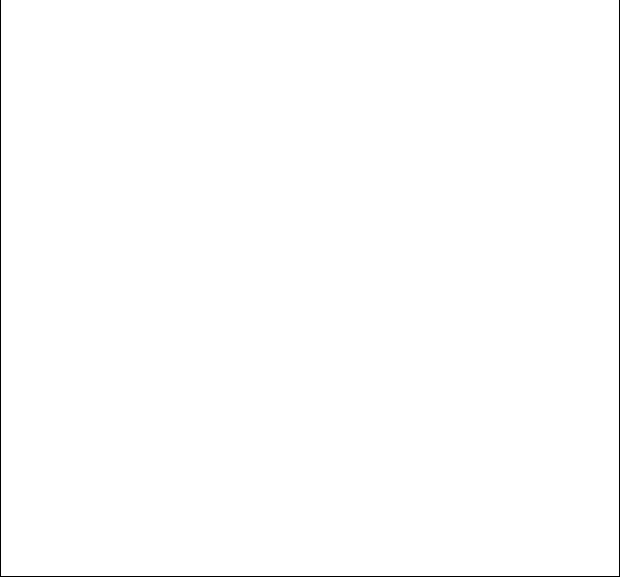
Таблица 11. Марки керамических камней и кирпича
|
|
Предел прочности, МПа, не менее |
|
||||
|
при сжатии |
|
при изгибе |
|
|||
Марка |
|
|
полнотелого кирпи- |
кирпича полусухого |
|||
всех видов изделий |
ча пластического |
прессования и пус- |
|||||
кирпича |
|||||||
|
|
формования |
|||||
|
|
тотелого кирпича |
|||||
и кам- |
|
|
|||||
|
|
|
|
||||
ней |
сред- |
наимень- |
сред- |
наимень- |
сред- |
наимень- |
|
|
ний для |
ший из |
ний для |
ший из |
ний для |
ший из |
|
|
пяти |
пяти зна- |
пяти |
пяти зна- |
пяти |
пяти зна- |
|
|
образ- |
чений |
образ- |
чений |
образ- |
чений |
|
|
цов |
|
цов |
|
цов |
|
|
300 |
30,0 |
25,0 |
4,4 |
2,2 |
3,4 |
1,7 |
|
250 |
25,0 |
20,0 |
3,9 |
2,0 |
2,9 |
1,5 |
|
200 |
20,0 |
15,0 |
3,4 |
1,7 |
2,5 |
1,3 |
|
175 |
17,5 |
13,5 |
3,1 |
1,5 |
2,3 |
1,1 |
|
150 |
15,0 |
12,5 |
2,8 |
1,4 |
2,1 |
1,0 |
|
125 |
12,5 |
10,0 |
2,5 |
1,2 |
1,9 |
0,9 |
|
100 |
10,0 |
7,5 |
2,2 |
1,1 |
1,6 |
0,7 |
|
75 |
7,5 |
5,0 |
1,8 |
0,9 |
1,4 |
0,7 |
|
Для кирпича и камней с горизонтальным расположением пустот |
|||||||
100 |
10,0 |
7,5 |
- |
- |
- |
- |
|
75 |
7,5 |
5,0 |
- |
- |
- |
- |
|
50 |
5,0 |
3,5 |
- |
- |
- |
- |
|
35 |
3,5 |
2,5 |
- |
- |
- |
- |
|
25 |
2,5 |
1,5 |
- |
- |
- |
- |
Примечание. Предел прочности при изгибе определяют по фактической площади изделия без вычета площади пустот
Кирпич облицовочный и камни лицевые керамические от-
личаются от обыкновенных большей плотностью, точностью формы и размеров, а также однородностью цвета и оттенка в одной партии. Эти материалы изготовляют из высококачественных легкоплавких глин. Лицевые кирпич и камни укладывают в стену здания в перевязку с обыкновенными, и они несут одинаковую с ними нагрузку. По внешнему осмотру для кирпича и камней не допускаются дефекты, размеры и число которых превышают указанные в таблице 12.
62
Таблица 12. Дефекты лицевой поверхности кирпича и камней
Показатель |
Величина |
Отклонения от размеров, мм, не более: - по длине |
± 4 |
- по ширине |
±3 |
- по толщине |
±3, - 2 |
Неперпендикулярность граней и ребер кирпича и камней, отне- |
|
сенная к длине 120 мм, не более |
2 |
Непрямолинейность лицевых поверхностей и ребер, мм, не бо- |
|
лее: - по тычку |
3 |
- по ложку |
2 |
Отбитость или притупленность углов и ребер длиной от 5 до 15 |
1 |
мм, шт., не более |
|
По пределу прочности при сжатии кирпич разделяют на марки 75, 100, 125, 150, 175, 200, 250 и 300.
Ковровая керамика представляет собой мелкоразмерные керамические плитки различного цвета, глазурованные и неглазурованные. Заводы выпускают мозаичные плитки с наклейкой их лицевой стороной на плотную бумагу, в результате чего образуется ковер. Размеры плиток полусухого прессования – 48х48, 22х22, 48х22 мм при толщине 3–4 мм. Ковровая керамика является одним из наиболее индустриальных керамических материалов и широко используется для облицовки наружных панелей и блоков при изготовлении их на заводах, стен вестибюлей, лестничных клеток, а также санузлов и кухонь вместо штучных облицовочных плиток.
Керамические изделия для внутренней облицовки зданий
подразделяют на две группы: для облицовки стен (рис. 13) и для покрытия полов.
Для облицовки стен применяют майоликовые и фаянсовые плитки. Майоликовые плитки изготовляют из легкоплавких глин с добавлением 20% углекислого кальция. Пористый черепок этих плиток с лицевой стороны покрывают глазурью. После этого майоликовые плитки дважды обжигают после сушки сырца и после нанесения глазури. Слой глазури обеспечивает плиткам полную водонепроницаемость и высокие декоративные качества.
63
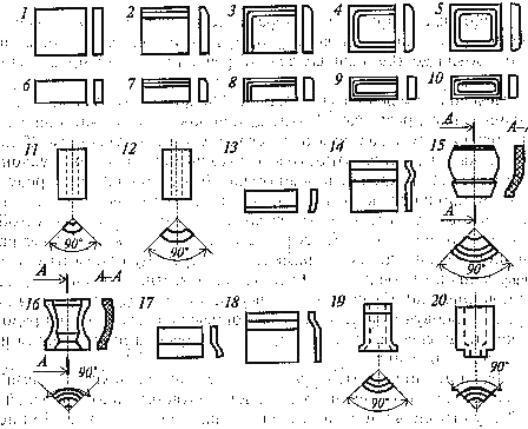
Рис. 13. Типы керамических плиток для внутренней отдел-
ки:
1-5 – квадратные; 6-10 – прямоугольные; 11, 12 – фасонные угловые; 13-16 – фасонные карнизные; 17-20 – фасонные плинтусные
Фаянсовые плитки изготовляют из тугоплавких глин с добавкой кварцевого песка. Для понижения температуры плавления вводят плавни: полевой шпат, мел, известняк. Плитки имеют слабоокрашенный или белый черепок. Лицевую сторону также покрывают глазурью. Технологическая схема глазурованных фаянсовых плиток показана на рис. 14.
Плитки должны иметь правильную форму, без искривлений и трещин. Допускаемые отклонения по размерам не должны превышать ± 1,5 мм, отклонение стороны прямого угла – не более 0,5 мм. Водопоглощение плиток не должно превышать 16%. Ассортимент плиток разнообразен – 50 типоразмеров: рядовые квадратные 200х200; 150х150; 100х100 мм и прямоугольные
200х150; 150х100; 150х75; 205х187 мм, карнизные, плинтусные и т.д. Толщина фаянсовых плиток – не более 6 мм, глиняных и плинтусных – не более 10 мм. По характеру поверхности они мо-
64

гут быть гладкими, рифлеными или иметь многоцветный рисунок.
Рис. 14. Принципиальная технологическая схема производства фаянсовых глазурованных плиток:
1 – бункер сырьевых материалов; 2 – вагонетка; 3 – шаровая мельница; 4 – удаление примесей электромагнитом; 5 – бассейн для массы с мешалкой; 6 – насос; 7 – распылительное сушило; 8 – транспортер; 9 – просев порошка; 10 – расходный бункер; 11 – прессование плиток; 12 – сушило; 13 – глазурование; 14 – печь для обжига; 15 – сортировка и упаковка
Плитки для полов изготовляют из каолиновых глин с добавкой отощающих веществ, плавней, окрашивающих веществ; формуют их прессованием полусухой массы и обжигают до спекания. Водопоглощение плиток не должно быть больше 3,5…4%, а истирание (для неглазурованных плиток) – 0,18 г/см2.
По внешнему виду лицевая поверхность плиток полов может быть: гладкой или рифленой; глазурованной и неглазурованной; одноцветной и многоцветной (узорчатой, порфировидной, мраморовидной и декорированной); неглазурованная поверхность плиток может быть полированной; с прямыми или закругленными кромками боковых граней. Форма плиток может быть квадратная, прямоугольная, многоугольная и фигурная (рис. 15).
65
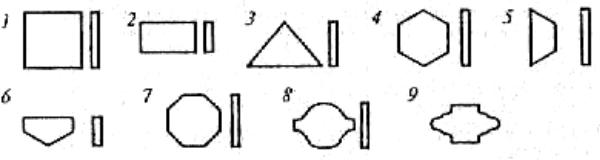
Рис. 15. Типы керамических плиток для полов:
1 – квадратная; 2 – прямоугольная; 3 – треугольная; 4 - шестигранная; 5 – четырехгранная; 6 – пятигранная; 7 – восьмигранная; 8, 9 – фигурные
Основные размеры плиток приведены в таблице 13. Применяют в помещениях с влажным режимом и повышенной интенсивностью движения – бани, ванные комнаты, кухни, коридоры, станции метрополитена, промышленные здания.
Таблица 13. Основные размеры плиток для полов
Координационные раз- |
Номинальные размеры, мм |
||
меры, мм |
|
|
|
длина |
ширина |
длина и ширина |
толщина |
Квадратные плиты |
Устанавливает предпри- |
не менее 7,5 |
|
500 |
500 |
ятие-изготовитель, чтобы |
|
400 |
400 |
ширина шва составляла |
|
|
|
от 2 до 5 мм |
|
330 |
330 |
|
|
300 |
300 |
|
|
250 |
250 |
|
|
200 |
200 |
|
|
150 |
150 |
|
|
Прямоугольные плиты |
|
|
|
500 |
300 |
|
|
400 |
300 |
|
|
300 |
200 |
|
|
250 |
200 |
|
|
200 |
150 |
|
|
Примечание. Координационный размер соответствует суммарной величине номинального размера плитки и ширины шва.
66
Полы из керамических плиток практически водонепроницаемы, характеризуются малым истиранием, не дают пыли, легко моются, долговечны, обладают стойкостью к действию кислот и щелочей. Недостатком таких полов являются высокая хрупкость, большая теплопроводность и высокая трудоемкость их возведения.
Плиты керамические фасадные предназначены для облицов-
ки фасадов зданий. В зависимости от конструкции, способов изготовления и методов крепления плиты разделяют на закладные и прислонные. Закладные плиты устанавливают во время кладки стен, а прислонные крепят на растворе после возведения и осадки здания. Выпускают плиты размером от 50х50 мм до 300х150 с допусками ± 5 мм по длине и ± 3 мм по ширине. Морозостойкость - не менее МРЗ 25, водопоглощение должно быть не более 12%.
Огнеупорные материалы изготовляют в виде кирпича, блоков, плит и фасонных элементов из различных сырьевых компонентов по технологии, близкой к керамической (формование или прессование, сушка, обжиг). По степени огнеупорности их разделяют на огнеупорные (1580–1770 °С), высокоогнеупорные (1770– 2000 °С) и высшей огнеупорности (выше 2000 °С), а в зависимости от химико-минералогического состава - на кремнеземистые, алюмосиликатные, магнезиальные, хромистые, углеродистые. Наибольшее распространение получили кремнеземистые и алюмосиликатные огнеупорные изделия.
Кремнеземистые (динасовые) изделия получают из кварце-
вых пород (кварц, кварцит, кварцевый песок) с добавкой глины обжигом. Огнеупорность изделий до 1730°С, они имеют достаточную прочность (15–35 МПа). Применяют динасовые изделия для кладки сводов и стен мартеновских и стекловаренных печей. Кварцевое стекло получают плавлением кварца. Оно обладает хорошей термостойкостью и весьма высокой плотностью.
Алюмосиликатные огнеупоры в зависимости от содержания SiO2 и Аl 2О3 в обожженном продукте разделяют на три вида:
полукислые, шамотные и высокоглиноземистые.
П о л у к и с л ы е о г н е у п о р ы изготовляют обжигом кварцевых пород на глиняной или каолиновой связке. Огнеупорность изделий на каолиновой связке не ниже 1710°С, на глиняной
67
– не ниже 1580°С. Их применяют для футеровки коксовых линий, вагранок и т.д.
Ш а м о т н ы е о г н е у п о р ы получают из огне-
упорных глин и каолинов, отощенных шамотом из этой же глины. Огнеупорность шамотных материалов – до 1730°С, а прочность при сжатии - 10–12,5 МПа. Они отличаются термической стойкостью. Применяют их для кладки доменных печей, облицовки топок паровых котлов, дымоходов и т.д.
В ы с о к о г л и н о з е м и с т ы е о г н е у п о р ы изготов-
ляют из высокоглиноземистого глинистого сырья с содержанием глинозема более 45% (бокситы, диаспор, корунд) обжигом до спекания или методом литья из расплавов. Эти изделия имеют огнеупорность до 2000°С и высокую теплоустойчивость. Применяют для кладки стекловаренных печей.
Гравий керамзитовый (пористый гранулированный материал ячеистого строения с закрытыми мелкими порами) получают путем обжига, сопровождающегося вспучиванием легкоплавкой глиняной массы.
По размеру зерен гравий подразделяют на три фракции: 5(3)–10; 10–20; 20–40 мм. Основной характеристикой керамзитового гравия является средняя насыпная плотность, по которой его подразделяют на 12 марок (от 150 до 800 кг/м3). Содержание в гравии расколотых зерен не должно превышать 15% по массе, морозостойкость должна быть не менее F15, причем потеря массы не должна превышать 8%, водопоглощение по массе должно быть не более 15–25% в зависимости от марки гравия.
Сырьем для производства гравия служат легкоплавкие глины, содержащие 6–12% окислов железа, 2–3% щелочных окислов и до 3% органических примесей, трепелы, глинистые сланцы, а также золы тепловых станций, способные вспучиваться при термической обработке.
Технологический процесс производства керамзитового гравия можно разделить на четыре этапа: подготовка глиняной массы, формование гранул, тепловая обработка, охлаждение готового гравия.
Глиняную массу можно подготовить сухим или пластическим способом. Более распространен пластический способ. Им перерабатывают рыхлые глины, которые после обработки на
68
зубчатых вальцах и в глиномешалке поступают на дырчатые вальцы, где формуют гранулы. Керамзитовый гравий обжигают во вращающихся печах барабанного типа при температуре до 1300 °С в течение 30–60 мин, затем охлаждают в барабанных охладителях.
Черепица глиняная изготавливается шести типов: пазовая штампованная и ленточная, плоская и волнистая ленточная, S- образная ленточная и коньковая.
По форме и размерам черепица должна соответствовать требованиям стандарта, не иметь короблений и трещин, искривление поверхности ребер допускается не более 3 мм, иметь морозостойкость не менее F25, глубина пазов черепицы должна быть не менее 5 мм, высота шпонов для подвески должна быть не менее 20 мм, на тыльной стороне черепицы должно иметься ушко с отверстием для привязки ее к обрешетке.
Основным сырьем для производства черепицы является легкоплавкая пластичная глина, которую тщательно обрабатывают для разрушения природной структуры, удаления твердых включений и повышения пластичности. Целесообразно вводить в
глиняную массу 10-15% шамота, что уменьшает усадку и коробление изделий. Схема производства ленточной черепицы показана на рис. 16.
Керамические канализационные трубы изготовляют диамет-
ром от 150 до 600 мм с градацией 50 мм (табл.14), они имеют плотный спекшийся черепок и покрыты изнутри и снаружи глазурью. Морозостойкость – не менее F15.
Сырьем для производства служат огнеупорные и тугоплавкие глины с добавкой тонкомолотого шамота. Канализационные трубы формуют с раструбом на трубных прессах, высушивают, покрывают глазурью и обжигают при температуре 1250–1300 °С. Глазурь создает внутри труб гладкую водонепроницаемую поверхность, увеличивает их химическую стойкость и уменьшает гидравлическое сопротивление при прохождении сточных жидкостей.
69
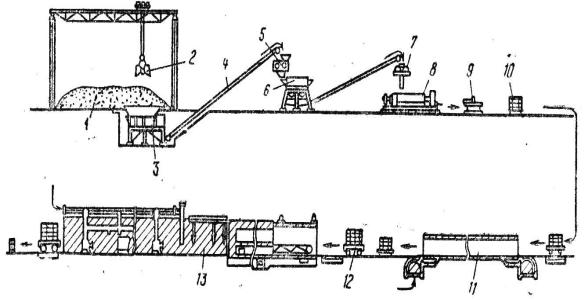
Рис. 16. Технологическая схема производства ленточной черепицы:
1 – хранилище глины; 2 – грейферный кран; 3 – ящичный подаватель; 4 – конвейер; 5 – камневыделительные вальцы; 6 – бегуны мокрого помола; 7 – вальцы тонкого помола; 8 – вакуумный пресс; 9 – автомат разрезки; 10 - вагонетки;11 – туннельная сушилка; 12 – вагонетка; 13 – туннельная печь
Таблица 14. Размеры керамических канализационных труб, мм
|
Ствол трубы |
|
Раструб трубы |
Номи- |
||||
внутренний |
номиналь- |
номи- |
внутренний |
номи- |
нальная |
|||
диаметр |
ная длина |
нальная |
диаметр |
нальная |
толщина |
|||
номи |
предел |
(± 20) |
длина |
номи- |
предел |
глубина |
стенки |
|
наль- |
откло- |
|
нарезки, |
наль- |
откло- |
(± 5) |
ствола и |
|
ный |
нений |
|
(± 5) |
ный |
нений |
|
раструба |
|
|
|
|
|
|
|
|
(± 4) |
|
150 |
± 7 |
1000, 1100, |
|
224 |
± 7 |
|
19 |
|
200 |
|
282 |
|
20 |
||||
|
1200, 1300, |
60 |
|
60 |
||||
250 |
± 9 |
340 |
± 9 |
22 |
||||
1400, 1500 |
|
|
||||||
300 |
± 10 |
|
398 |
± 10 |
|
27 |
||
|
|
|
||||||
350 |
|
|
|
456 |
|
|
28 |
|
400 |
± 11 |
1000, 1100, |
70 |
510 |
± 11 |
70 |
30 |
|
450 |
1200, 1300, |
568 |
34 |
|||||
500 |
|
1400, 1500 |
|
622 |
|
|
36 |
|
550 |
|
|
|
678 |
|
|
39 |
|
600 |
± 12 |
|
|
734 |
± 12 |
|
41 |
70