
Учебное пособие 800594
.pdfУДК 621.315.592
А.О. Власов, С.А. Акулинин*
МЕГАЗВУКОВАЯ ОЧИСТКА ПЛАСТИН В ПРОИЗВОДСТВЕ МИКРОЭЛЕКТРОНИКИ
В работе описывается метод мегазвуковой очистки пластин в процессе фотолитографии.
В последние десятилетия мы являемся свидетелями бурного развития производства полупроводниковых изделий. Основными направлениями развития являются микроэлектроника, фотоника, лазерная техника, солнечная энергетика. Общими тенденциями, характерными для всех направлений современного полупроводникового производства являются повышение степени интеграции элементов на кристалле, увеличение диаметра пластин с соответствующим уменьшением топологических норм.
При производстве микроэлектронных изделий полупроводниковые пластины проходят технологический маршрут, включающий операции окисления, диффузии, имлантации и многих других. При этом каждой последующей операции предшествует процесс фотолитографии. Фотолитографические процессы являются наиболее сложными и ответственными процессами в современной технологии изготовления изделий микроэлектроники являются. Именно характеристики и возможности оборудования для литографии в конечном итоге определяет возможность изготовления того или иного полупроводникового прибора или интегральных схем.
Задача литографии – послойный перенос на полупроводниковую подложку рисунка (топологии) интегральной схемы, сформированного в комплекте фотошаблонов. Технология литография – это процесс формирования в активночувствительном слое, нанесенном на поверхность подложек, рельефного рисунка, повторяющего топологию полупроводниковых приборов или ИМС.
После проведения различных процессов (удаления фоторезиста, травления технологических слоев и др.) подложки обрабатываются для очистки поверхности от различных загрязнений и подго-
190

товки к последующим операциям – ионного легирования, нанесения эпитаксиальных слоев и высокотемпературным диффузионным процессам.
Для уменьшения брака и получения более четкого рисунка после фотолитографии нужно обеспечить проведение процесса обработки пластины в чистой окружающей среде. Для решения этой задачи используют кластерные линии. Кластерная линия фотолитографии состоит из набора модулей, объединённых единой транспортной системой – центральным роботом. Каждый модуль реализует определённую технологическую операцию. Состав кластерной линии, и её возможности определяются набором модулей.[1]
На рис. 1 представлена структура кластерной линии фотолитографии.
Рис. 1. Расположение составных частей кластерной линии:
1 - модульный комплекс фотолитографии, 2 - бокс технологический, 3 - блок криостатов, 4 - модуль реагентов для проявления, 5 - модуль реагентов для нанесения, 6 - модуль сбора отработанных реагентов, 7 - шкаф силовой
Модули размещаются на общей несущей раме замкнутой конфигурации в контролируемой воздушной среде. Перемещение пластин от модуля к модулю обеспечивает единое транспортное
191

устройств в виде специализированного робота. Робот размещен на линейном транспорте.
Подобную структуру имеет кластерная линия фотолитографии производства НИИПМ (г. Воронеж). В данной кластерной линии каждый модуль оборудован фильтровентиляционным модулем, обеспечивающим ламинарный поток очищенного воздуха в рабочую зону. Каждый модуль с помощью трубопроводов соединен с вытяжной системой вентиляции.
Одной из отличительных особенностей предлагаемой кластерной линий является наличие модуля мегазвуковой очистки.
Название «мегазвуковой» используется для отличия высокочастотного метода очистки (0,8 – 2 МГц) от более известного низкочастотного ультразвукового метода (20 – 80 кГц). Система мегазвуковой очистки позволяет удалять частицы размером порядка 0,3 мкм, как это следует из рис. 2.
Рис. 2. Сравнение рабочих частот и размеров удаляемых загрязнений для ультразвуковой и мегазвуковой технологий
Основой мегазвуковой системы очистки является пьезоэлектрический преобразователь, генерирующий в рабочей ванне волны в диапазоне частот 0,8 – 2,0 МГц , мощностью порядка 5 – 10 Вт/см². В зависимости от характера загрязнений время обработки варьируется от 10 до 30 минут. Как известно, ультразвуковая обработка проводится на частотах 25 – 270 кГц (типичный диапазон 20 – 80 кГц) и для нее характерен спонтанный кавитационный процесс. В мегазвуковом процессе очистка достигается за счет управляемой кавитации и воздействия микропотоков очищающего раствора. Управляемая кавитация характеризуется наличием стабильных и сравнительно долгоживущих пузырьков, которые могут существовать в течение
192
нескольких циклов акустических воздействий и не повреждают поверхности. С физической точки зрения это связано с тем, что на более высоких частотах радиус кавитации и энергия схлопывания значительно меньше. При этом создаются оптимальные условия для проникновения моющей жидкости в область контакта поверхности и загрязнения, ослабляются силы адгезии и частица переходит в объем раствора. Как показали исследования, критичным является толщина граничного слоя раствора, экранирующего загрязнения от быстрого потока очищающей жидкости. Уменьшение толщины может быть достигнуто понижением кинематической вязкости очищающего раствора и увеличением частоты и мощности звуковых колебаний. При мегазвуковой очистке толщина этого слоя уменьшена с 2,5 мкм, характерной для ультразвуковой очистке, до 0,5 мкм, что увеличивает скорость обновления моющего раствора. Управление процессом мегазвуковой очистки производится с помощью изменения подводимой мощности, причем лучшее управление достигается при подаче импульсной мощности. Применение более высоких частот обработки устраняет такие разрушительные эффекты, как кавитационная эрозия и другие повреждения поверхности, и позволяет безопасно очищать чувствительные объекты [2].
Увеличение диаметра полупроводниковых пластин и повышение требований к качеству проведения всех технологических операций при переходе к субмикронным проектным нормам обусловили переход к обработке одной пластины. Применение оборудования для мегазвуковой отмывки дает возможность реализовать такой подход. Процесс хорошо настраивается под конкретное изделие и обеспечивает высокую производительность обработки, составляющую менее 1 мин. на пластину.
Литература
1.Быков В.А. Кластерное технологическое оборудование для создания элементной базы наноэлектроники [Текст] / В.А.Быков // Наноиндустрия. – 2010. - № 6. – С. 6 – 8.
2.Bushanina A.A. Megasoniccleaning [Текст] / A.A. Bushanina, F. Dai // Semiconductorinternational. - 1997. - V. 20. - № 8. – Р. 75 – 83.
ОАО «Научно-исследовательский институт полупроводникового машиностроения», г. Воронеж
*Воронежский государственный технический университет
193
УДК 538.975
В.А. Кулешов, А.В. Толкачев
ВЛИЯНИЕ ИЗОТЕРМИЧЕСКОГО ОТЖИГА НА ЭЛЕКТРОФИЗИЧЕСКИЕ СВОЙСТВА МЕТАЛЛООКСИДНЫХ ПЛЕНОК SnO2, ИЗГОТОВЛЕННЫХ СПРЕЙ–ПИРОЛИЗОМ
Исследование электрофизических параметров проводилось на образцах оксида олова SnO2, изготовленных по технологии спрей-пиролиза. Элементный состав полученных пленок контролировался рентгенофазовым анализом, оптические свойства снимались на спектрофотометре, электрофизические параметры измерялись методом Ван-дер-Пау.
Металлооксидные пленки SnO2 являются полупроводником n-типа с шириной запрещенной зоны Eg = 3,6 эВ. Удачное сочетание оптических и электрофизических свойств позволяет широко применять данный материал на практике. В зависимости от области применения плёнки нужны с различными характеристиками. Например, для светодиодов, фотоэлектрических устройств, электродов главным фактором является то, чтобы пленки были низкоомными, а для солнечных элементов важным является высокий коэффициент пропускания [1]. Из-за особых физико-химических свойств диоксида олова очень распространено его применение в микроэлектронике. Возможно его применение в качестве проводящих покрытий при изготовлении фотопреобразователей и оптоэлектрических приборов. SnO2 имеет высокие абсорбционные свойства и реакционную способность благодаря наличию в зоне проводимости свободных электронов. Поэтому нанокристаллические пленки SnO2 чувствительны к токсичным газам.
194
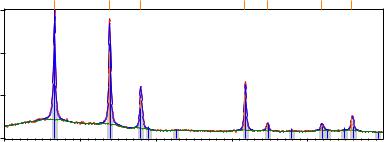
Целью работы является синтез методом спрей-пиролиза пленок оксида олова и определение изменений свойств SnO2 от изотермического отжига.
Пленки диоксида олова были получены методом пиролиза [2]. Данный метод обусловлен термическим испарением раствора на поверхности подложки с дальнейшим осаждении пленки нужного вещества. Раствор был составлен из [SnCl2 2H2O] и дистиллированной воды в объеме 200 мл и распылен при помощи аэрографа OPHIR AC004A. Количество соли в растворе соответствовало концентрации 0,25 M. Для того чтобы избежать гидролиза соли хлорида олова в воде, добавлялась соляная кислота HCl в количестве 1 мл.
Толщина пленок измерялась при помощи микроинтерферометра МИИ - 4. Полученные пленки имели толщину 0,8 мкм.
Структура полученных образцов исследовалась методом рентгеновской дифракции на дифрактометре ARL X'TRA (Швейцария) в Центре коллективного пользования научным оборудованием ВГУ. Сканирование проводилось методом: 2Theta Scan, при нормальном начальном угле 10 град., угол остановки 80 град. Число точек 1401, при размере шага 0,05 град. На рис. 1 показан результат рентгеновского анализа для образца оксида олова до отжига. Очевидно, что на дифрактограмме SnO2 присутствуют рефлексы от плоскостей (1,1,0), (1,0,1), (2,0,0), (2,1,1), расположение пиков 2Θ (26.51), (33.80), (37.89), (54.65).
Counts |
|
|
|
|
|
|
|
|
|
|
|
3000 |
|
0 |
1 |
|
|
|
|
|
|
|
|
|
1 |
0 |
|
|
|
|
|
|
|
|
|
|
|
|
|
|
|
|
|
|
|
||
|
SnO2_400 |
|
|
|
|
|
|
|
|
|
|
2000 |
|
Sn O2; 1 |
Sn O2; 1 |
0 |
|
1 1 |
|
|
|
|
|
|
|
|
|
0 |
|
2 |
|
|
|
|
|
|
|
|
|
2 |
|
Sn O2; |
Sn O2; 2 2 0 |
|
0 |
|
|
|
|
|
|
1 |
|
Sn O2; 0 0 2 |
1 |
Sn O2; 1 1 2 Sn O2; 3 0 1 |
|
||
|
|
|
|
1 |
|
1 |
|
||||
|
|
|
|
|
2 |
|
|||||
|
|
|
|
O2; |
Sn O2; 210 |
3 |
Sn O2; 3 11 |
||||
1000 |
|
|
|
1 |
2 |
||||||
|
|
|
Sn |
O2; |
|||||||
|
|
|
|
||||||||
|
|
|
|
O2; |
|||||||
|
|
|
|
O2;Sn |
Sn |
||||||
|
|
|
|
Sn |
|||||||
020 |
30 |
|
40 |
|
50 |
|
|
60 |
|
|
|
|
Рис. 1. Рентгеновская дифрактограмма образца до отжига |
|
195

Изотермический отжиг образца проводился при температуре 500 в течение 1 ч. На рис. 2 приведена дифрактограмма отожженного образца SnO2. Видно, что на дифрактограмме SnO2 после отжига усилилась интенсивность пиков, и присутствуют новые рефлексы,
которые соответствуют 2Θ (24,3), (31.72), (42,39).
Counts |
|
|
|
|
|
|
|
|
|
|
|
|
10 |
01 |
|
|
|
|
|
|
|
3000 |
SnO2_500_1h |
|
|
|
|
|
|
|
|
|
|
1 |
1 |
|
|
|
|
|
|
|
|
|
Sn O2; |
Sn O2; |
|
|
|
|
|
|
|
|
|
|
|
1 |
|
|
|
|
|
||
2000 |
|
|
0 0 |
|
2 1 |
|
|
|
|
|
|
|
|
2 |
|
Sn O2; |
Sn O2; 2 2 0 |
|
0 |
|
|
|
|
|
1 |
Sn O2; 2 1 0 |
Sn O2; 0 0 2 |
1 |
Sn O2; 1 1 2 Sn O2; 3 0 1 |
|
||
|
|
|
1 |
1 |
|
|||||
|
|
|
2 |
|
||||||
|
|
|
O2; |
3 |
Sn O2; 311 |
|||||
|
|
|
1 |
2 |
||||||
1000 |
|
|
Sn |
O2; |
||||||
|
|
|
O2; |
|||||||
|
|
|
O2;Sn |
Sn |
||||||
|
|
|
Sn |
|||||||
020 |
30 |
40 |
|
50 |
|
|
60 |
|
|
|
Рис. 2. Рентгеновская дифрактограмма отожженного образца оксида |
||||||||||
|
|
олова полученного спрей-пиролизом |
|
|
|
|
Оптические свойства исследовались для вычисления ширины запрещенной зоны, при помощи двухлучевого спектрофотометра СПЕКС ССП - 715М, работа которого основана на избирательном поглощении потока оптического излучения, при прохождении его через жидкие или твердые материалы [3]. На рис. 3 показаны спектры пропускания.
Определенная ширина запрещенной зоны для SnO2 составила 3,3 эВ, что совпадает с литературными данными [4] (рис. 4).
196

Рис. 3. Спектры пропускания SnO2
Рис. 4. Зависимость (αhν)2 от энергии света для пленки SnO2
В данной работе были синтезированы пленки оксида олова по технологии спрей-пиролиза. После нанесения пленки имели удовлетворительные электрофизические параметры, что делает их при-
197
годными для практического использования сразу после нанесения и позволяет сократить количество технологических операций, что удешевляет стоимость производства. Для всех пленок были определены: прозрачность в видимом диапазоне, ширина запрещенной зоны, тип проводимости, поверхностное сопротивление, подвижность носителей заряда. Измеренные поверхностные сопротивления пле-
нок, составили 141 Ом/ и 1500 Ом/ после отжига [5]. Увеличение сопротивления связанно с эрозией металлооксидной пленки в результате термической обработки при высокой температуре. Подвижность носителей заряда SnO2 составила 6,78 см2/В∙с, а концентрация свободных носителей 6,53∙1019 см-3.
Были определены спектры пропускания пленок SnO2. Они показали, что в видимой и инфракрасной части спектра прозрачность составляет более 80 %. Из порогового поглощения рассчитаны данные ширины запрещенной зоны 3,3 эВ.
Литература
1.Perez-Tomas A. Metal oxides in photovoltaics: all-oxide, ferroic, and perovskite solar cells [Текст]/ A. Perez-Tomas, A. Mingorance, D. Tanenbaum, M. Lira-Cantu // The Future of Semiconductor Oxides in Next-Generation Solar Cells. - 2018. - V. 1. - P. 267 - 356.
2.Eslamian M. Modelling of nanoparticle formationduring spray pyrolysis [Текст] / M. Eslamian // Nanotechnology. - 2006. - V. 17. - P. - 1674 - 1685.
3.Белоусов С.А. Электрофизические свойства металлоок-
сидных пленок SnO2, изготовленных по золь-гель технологии [Текст] / С.А. Белоусов, А.А. Носов, Т.Г. Меньшикова, С.И. Рембеза // Вестник воронежского государственного технического университета. - 2016. – T. 12. - № 2. - C. 22 - 26.
4.Batzill M. The surface and materials science of tin oxide [Текст] / M. Batzill, U. Diebold // Progress in Surface Science. - 2005. - V. 79. - P. 147 – 154.
5.Никольский А.Б. Физические методы исследования неорганических веществ [Текст]: учеб. пособие / А.Б. Никольский. - М.: Академия, 2006. - 443 с.
Воронежский государственный университет
198
УДК 621.315.592
Д.С. Минаков, С.А. Акулинин*
КЛАСТЕРНОЕ ОБОРУДОВАНИЕ ФОТОЛИТОГРАФИИ
ВПРОИЗВОДСТВЕ МИКРОЭЛЕКТРОНИКИ
Вработе рассматривается оборудование для производства интегральных микросхем, отвечающее современным требованиям технологии фотолитографии.
Современный этап развития микроэлектроники характеризуется переходом к субмикронным размерам элементов, увеличением размеров пластин до 300 миллиметров, необходимостью использовать многоуровневую систему металлизации. Все это приводит к повышению требований к качеству всех технологических процессов
– окислению, диффузии, имплантации, металлизации. Особенно актуальным является совершенствование технологии и оборудования для проведения фотолитографических процессов. Именно фотолитография обеспечивает формирование топологии интегральных схем и полупроводниковых приборов и в конечном итоге определяет достигнутый уровень масштабирования (scaling). Согласно эмпирического закона Мура плотность элементов в СБИС возрастает в два раза каждые 18 месяцев.
Совершенствование процессов фотолитографии обеспечивается продуманностью конструктивных особенностей оборудования, культурой фотолитографического производства и, в большой степени, качеством используемых комплектующих изделий и материа-
лов [1].
Для обеспечения требований технологии проекционной фотолитографии в производстве ИС технологического уровня 0,35 – 0,18 мкм, необходим переход на новые принципы организации фотолитографической обработки слоёв фоторезиста с использованием модульно-кластерных линий фотолитографии. При этом появляется возможность организовать производство по технологическим микроциклам, включающим последовательные операции. Обработ-
199