
Учебное пособие 800508
.pdf
52
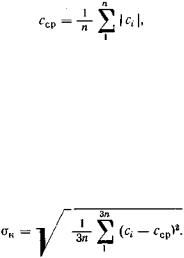
На рис. 3.23 представлены экспериментальные данные о жесткости, измеренной в различных точках рабочего пространства 25 токарных станков серийного производства.
Еще больший разброс имеют значения жесткости несущей системы многооперационных станков с несколькими координатными перемещениями (рис. 3.24). В связи с этим податливость несущей системы целесообразно характеризовать средним значением (мкм/Н)
где п — общее число значений податливостей в разных точках рабочего пространства; — податливость всей несущей системы в каждой точке.
Разброс жесткости характеризует среднеквадратичное отклонение податливостей по всем точкам рабочего пространства:
Иногда в практических целях полезно также использовать пре дельные значения податливостей — и
, их разность
==
—
и коэффициент вариации
=
Т е п л о в ы е д е ф о р м а ц и и несущей системы станка существенно влияют на точность обработки, на способность стайка сохранять первоначальную настройку и тем самым на технологическую надежность. Абсолютная величина линейных температурных деформаций в интенсивно работающих станках достигает нескольких сотых, а иногда и десятых миллиметра. Наконец, температурные деформации носят стохастический характер по причине нестационарности режима работы станка (рис. 3.29), что затрудняет их анализ и расчет на стадии проектирования.
Основными источниками тепла в станках являются двигатели, подвижные соединения, работающие при высоких скоростях, и сам процесс резания. Имеются программы расчета температурных полей и тепловых деформаций несущей системы станка как при стационарном, так и при нестационарном режимах на основе использования методов конечных элементов. Результаты расчета обычно удовлетворительно согласуются с экспериментальными данными (рис. 3.30) даже для сложных несущих систем.
3.3. НАПРАВЛЯЮЩИЕ
Направляющие станков формируют прямолинейные, а иногда и круговые движения в станках, влияя тем самым на точность обработки. Кроме того, они входят в несущую систему, общая жесткость которой существенно зависит от жесткости направляющих. В станках автоматических систем преимущественное распространение получили направляющие качения и направляющие скольжения, а также гидростатические и аэростатические направляющие.
Используются, кроме того, комбинированные направляющие из указанных выше основных типов.
В основе проектирования направляющих лежат следующие основные проектные критерии: 1) ограничение геометрических погрешностей при изготовлении в соответствии с необходимой точностью прямолинейного движения узлов станка; 2) ограничение упругих перемещений требованиями, предъявляемыми к общей жесткости несущей системы; 3) ограничение износа рабочих граней направляющих по требованиям сохранения прямолинейности в
53
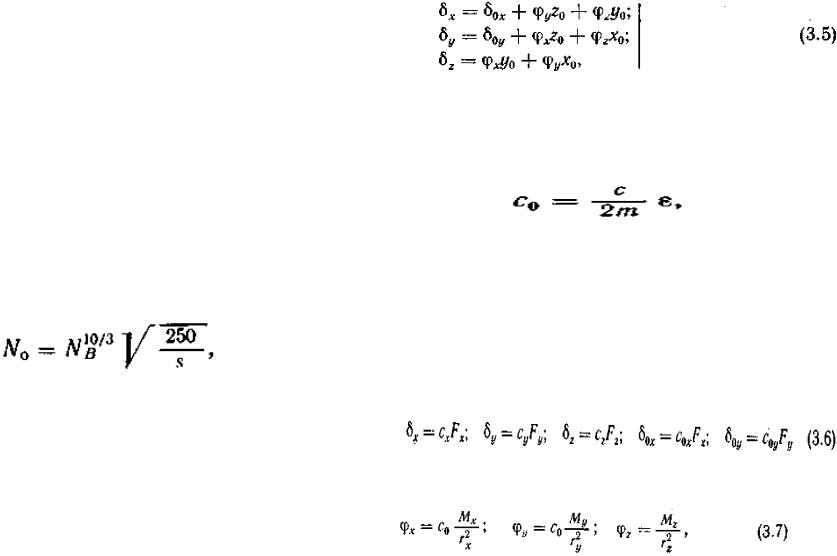
соответствии с технологической надежностью; 4)'минимальное и, по возможности, инвариантное к скорости и продолжительности неподвижного контакта трение; 5) высокие демпфирующие свойства для обеспечения динамических характеристик несущей системы станка.
Н а п р а в л я ю щ и е к а ч е н и я получили широкое распространение в многооперационных станках в связи с относительно небольшим и мало изменяющимся от скорости движения трением, сравнительно высокой долговечностью. Точность траектории движения и жесткость опор качения несколько ниже, чем у направляющих скольжения.
Условный коэффициент трения для роликовых комплектных опор с циркуляцией тел качения (рис. 3.31) обычно лежит в пределах = 0,001
0,003, а сопротивление движению при нормальной нагрузке N
и диаметре роликов d определяется средним значением |
|
Т = (10 + 0,01N) H. |
(3.4) |
Долговечность роликовых опор ограничена износом рабочих поверхностей опор, реже — поверхностей роликов. По результатам экспериментальных исследований при заданном общем пути пробега s необходимо ограничивать нагрузку на роликовую опору значением
где — базовая нагрузка при условном пути пробега 250 км, которая зависит от типа и размеров опоры (например, для опоры Р88102
50 кН). Жесткость роликовых опор в области малых нагрузок имеет сугубо нелинейный участок (рис. 3.32), и лишь при действии нормальной силы на опору N > 5000 Н приближается к линейной. Для стандартных роликовых опор серии Р-88 значения жесткости и условной «начальной» деформации
приведены в табл. 3.4, где даны также размеры опор и допустимая базовая нагрузка
по условиям долговечности. Расчет жесткости направляющих качения с приведением ее к произвольной точке рабочего пространства удобно вести на основе схемы, изображенной на рис. 3.33, по методике ЭНИМС. Оси
координат проводят через середину направляющих, и координатные упругие перемещения в произвольной точке получают в виде
где ,
— координатные перемещения в начале координат;
,
,
— углы поворота относительно осей координат. Жесткость направляющих по каждому координатному направлению оценивают приведенной податливостью. При этом вводят понятие номинальной податливости, которая имеет место при центральном приложении силы:
где с — податливость одной роликовой опоры; т — число опор по длине рабочей грани; — коэффициент, учитывающий совместную работу пары роликовых опор на противоположных гранях направляющих и зависящий от величины предварительного натяга: при использовании тарельчатых пружин
= 0,95, клиньев
= = 0,5, а при отсутствии натяга
= 1. Число роликовых опор выбирают обычно исходя из расстояния между ними в пределах 800—1250 мм.
Приведенные податливости получают из выражений (3.5) при подстановке туда значений координатных перемещений:
и углов поворота относительно координатных осей
54
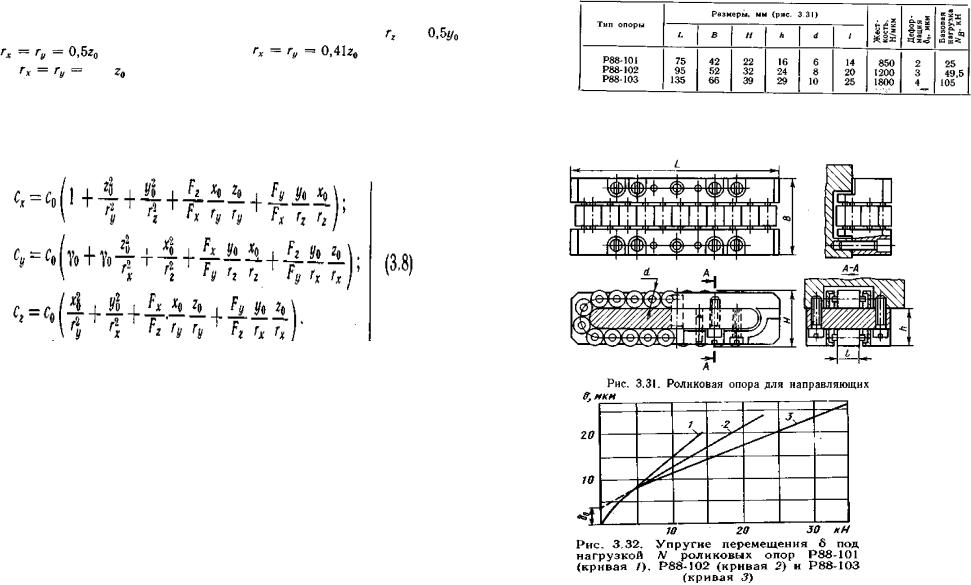
где ,
, .
— опрокидывающие моменты от составляющих сил резания, умноженных на соответствующие плечи
,
,
;
,
,
— радиусы инерции, зависящие от числа роликовых опор и их расстояния от
середины направляющих. |
|
|
|
|
|
При |
симметричной форме |
сечения |
направляющей |
= |
, |
а |
при m = 2, |
или |
при |
m |
= 3, |
или 0,37 при m = 4. |
|
|
|
|
В результате подстановок выражений (3.6) и |
(3.7) в |
формулу |
(3.5) и последующих несложных преобразований |
можно |
получить |
следующие выражения для приведенных податливостей |
при одно |
временном действии сил :
к любой точке рабочего пространства. Коэффициент учитывает полную податливость боковых граней обычно
=2) На стадии эскизного проектирования значение номинальной контактной податливости, учитыва
влияние погрешностей сборки можно принимать = (0,001
0,002)/2т.
Во всех ответственных случаях направляющие качения необходимо выполнять с предварительным натягом, для чего обычно используют регулировочные устройства типа тарельчатых пружин, регулировочных винтов, клиньев. Иногда натяг осуществляют точной пригонкой рабочих поверхностей направляющих при сборке, что обеспечивает высокую
Т а б л и ц а 3.4
Параметры роликовых опор
55
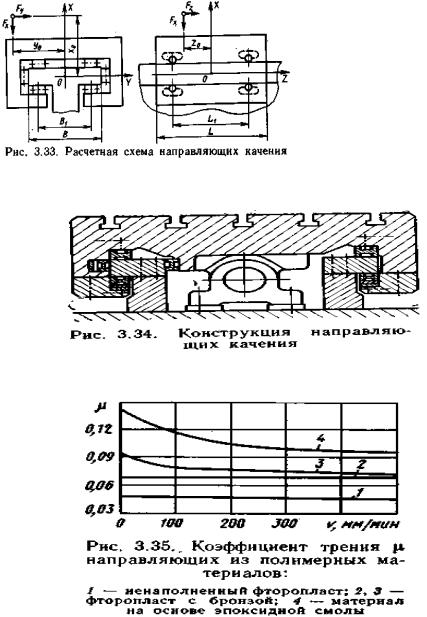
жесткость, но связано с существенным увеличением трудоемкости. На рис. 3.34 в качестве примера дано конструктивное оформление направляющих качения для стола многооперационного станка.
Н а п р а в л я ю щ и е с к о л ь ж е н и я уступают направляющим качения в потерях на трение и наличии зазоров, но обладают высокой жесткостью и хорошими демпфирующими свойствами. В современных станках применяют главным образом прямоугольную или, реже, цилиндрическую форму направляющих. Основное совершенствование направляющих скольжения идет по пути изыскания материалов, имеющих лучшие характеристики трения. Широкое распространение получили полимерные материалы двух видов: фторопласты (политетрафторэтилен) без наполнителей и с наполнителями в виде бронзы, дисульфита, молибдена, графита и т. п. и композиционные быстротвердеющие материалы на основе эпоксидных смол.
Ненаполненные и наполненные фторопласты в паре с чугуном или закаленной сталью имеют низкий (0,04—0,06) коэффициент трения, практически не зависящий от скорости скольжения, что обеспечивает равномерное движение в широком диапазоне малых скоростей. Введение наполнителей повышает механические свойства фторопласта, уменьшает хладотекучесть и повышает износостойкость, несколько увеличивая коэффициент трения. Материалы на основе фторопласта изготовляют чаще всего в виде ленты, которую приклеивают к тщательно обработанной рабочей грани направляющей.
Композиционные материалы на основе эпоксидной смолы позволяют резко упростить технологию изготовления. Короткие направляющие на подвижном узле (стол, каретка, ползун) получаются методом слепка и не требуют никакой последующей механической обработки. Подвижной узел предварительно выставляют с зазором 1,5—2 мм относительно окончательно обработанной поверхности станины, покрытой тонким разделительным составом.
56
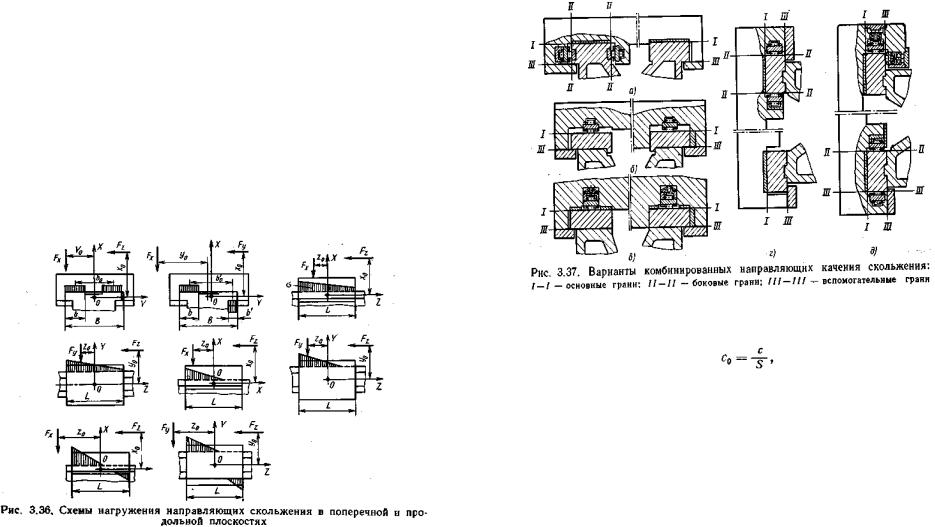
Зазор заполняется смесью на основе эпоксидной смолы, которая твердеет без усадки в течение суток. Материалы этой группы обладают хорошими противозадирными свойствами, но коэффициент трения их значительно выше, чем у материалов на базе фторопласта (рис. 3.35).
Расчет жесткости направляющих скольжения удобно вести на основе расчетных схем на рис. 3.36 с приведением податливости к
заданной точке рабочего пространства с координатами ,
,
Номинальная податливость плоских граней направляющих при центральном действии нормальной силы
где с — коэффициент контактной податливости; S — площадь рабочих граней, воспринимающих нагрузку.
На стадии эскизного проектирования можно принимать средние
значения . Для направляющих скольжения принимают обычно распределение давлений по ширине граней равномерным, а по длине направляющей — распределенным по линейному закону. При этих допущениях возможны различные случаи нагружения (см. рис. 3.36), когда работают только основные грани и когда грани работают совместно с планками. Для случаев, при которых рабочие грани воспринимают нагрузку по всей длине, определение приведенных податливостей возможно по формулам (3.8), принимая радиусы инерции
,
57
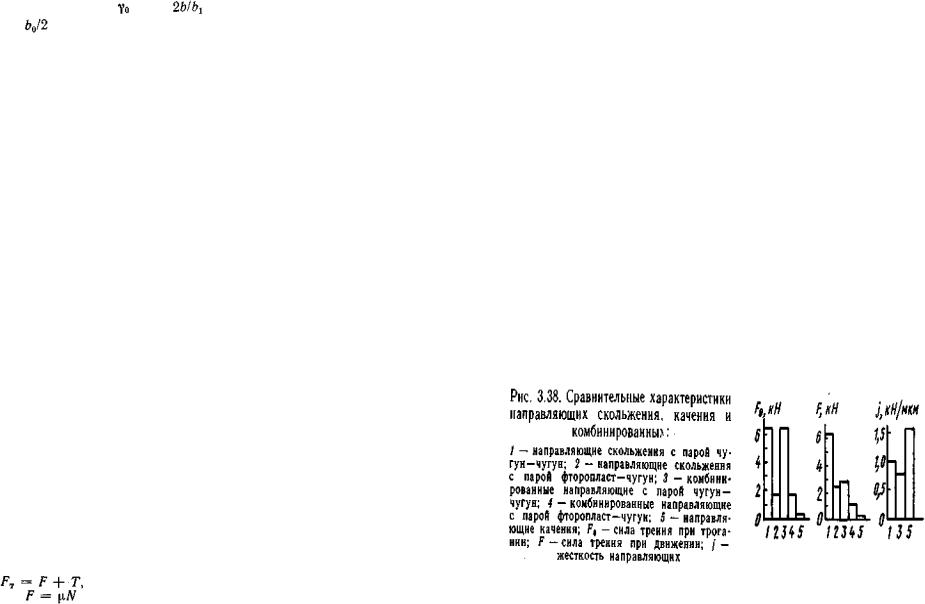
а коэффициент |
= |
.В тех случаях, |
когда |
рабочие |
Жесткость комбинированных направляющих близка к жесткости |
||
грани |
направляющих нагружены не по всей длине или в работу |
направляющих качения (рис. 3.38), а в некоторых случаях выше в 1,5— |
|||||
вступают |
планки, |
вводятся |
дополнительные |
коэффициенты. |
3 раза. |
||
К о м б и н и р о в а н н ы е |
н а п р а в л я ю щ и е |
|
качения и |
На рис. 3.39 даны примеры конструктивного оформления ком- |
|||
скольжения находят в станках с ЧПУ и в многооперационных |
бинированных направляющих качения-скольжения, когда основная |
||||||
станках все большее распространение в связи с тем, что их |
нагрузка от массы стола фрезерного станка с ЧПУ воспринимается |
||||||
применение снижает трение, |
устраняет зазоры |
и |
обеспечивает |
роликовыми опорами с предварительным натягом посредством |
|||
сравнительно высокую жесткость. В зависимости от назначения |
регулировочных устройств с клиньями. Горизонтальные силы |
||||||
направляющих возможны различные сочетания рабочих |
граней |
воспринимаются боковыми гранями скольжения. При чистовых |
|||||
скольжения и качения. Роликовые опоры можно |
устанавливать |
режимах работы зазоры в направляющих скольжения выбираются |
|||||
на основных, боковых или вспомогательных гранях, а остальные |
пружинными устройствами. В качестве антифрикционного материала |
||||||
рабочие |
грани направляющих выполняются |
со |
скольжением |
использован фторопласт марки ФЧК.15М5 в паре с закаленной сталью. |
|||
(рис. 3.37). Направляющие, в которых основные грани со |
|
||||||
скольжением, а боковые — с роликовыми опорами (рис. 3.37, а, г ) , |
|
||||||
устраняют вредное влияние зазоров на положение подвижно узла. |
|
||||||
При консольном расположении узла |
|
|
|
|
|||
(рис.3.37,г,д его масса воспринимается направляющими качения, |
|
||||||
что обеспечивает низкий коэффициент трения и соответственно |
|
||||||
небольшую тяговую силу в приводе подач. |
|
|
|
|
|||
Варианты с горизонтальными основными направляющими качения и с |
|
||||||
боковыми гранями скольжения (рис. 3.37, б) сохраняют вредное |
|
||||||
влияние зазоров, но обеспечивают малое трение под нагрузкой от массы |
|
||||||
подвижного узла. Горизонтальные направляющие с частичной |
|
||||||
разгрузкой направляющих скольжения подпружиненными роликовыми |
|
||||||
опорами (рис. 3.37, в) улучшают характеристики трения и повышают |
|
||||||
долговечность направляющих скольжения. Вертикальные направляющие |
|
||||||
с подпружиненными роликами на вспомогательных гранях (рис. 3.37, д) |
|
||||||
обеспечивают устранение зазоров и переориентацию при изменении |
|
||||||
нагрузки. |
|
|
|
|
|
|
|
Сопротивление движению при комбинированных направляющих |
|
||||||
определяется суммарной силой |
|
|
|
|
|
||
где |
|
— сила трения на гранях скольжения при |
|
||||
коэффи- |
|
|
|
|
|
|
|
циенте трения μ и нормальной силе N; Т — сила сопротивления при качении, определяемая по формуле (3.4).
58
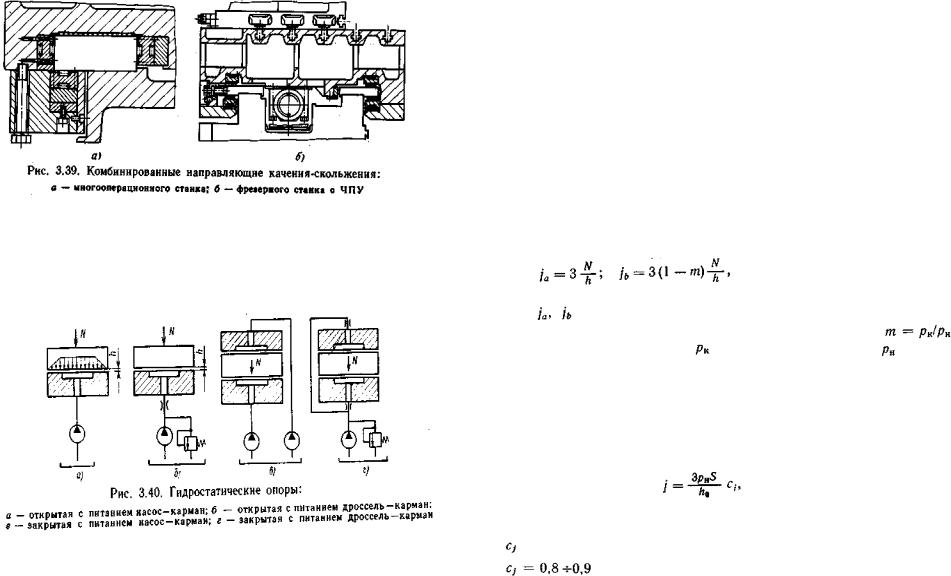
Г и д р о с т а т и ч е с к ие н а п р а в л я ю щ и е обеспечивают малое сопротивление движению, обладают высоким демпфированием, практически не изнашиваются, обеспечивают высокую точность траектории движения, но нуждаются в довольно сложной и дорогой системе питания и поэтому используются преимущественно в тяжелых станках и в станках с повышенными требованиями к точности обработки. К недостаткам гидростатических направляющих следует отнести и сложность фиксации подвижного узла в заданной конечной позиции.
Направляющие с использованием незамкнутых, открытых гидростатических опор (рис. 3.40, а, б) применяют только в тех случаях, когда нормальная сила N достаточно велика и приблизительно постоянна (например, от массы подвижного узла). При сильном изменении нагрузки соответственно меняется жесткость опоры и положение узла на направляющих, так как жесткость открытых опор прямо пропорциональна N:
где |
— жесткости опор, соответствующих рис. |
3.40, а и |
рис. 3.40, б; h — расчетная величина зазора; |
— |
|
характеристика дросселя; — давление в кармане; |
—давление |
|
насоса. |
|
|
Закрытые гидростатические опоры способны обеспечить высокую жесткость того же порядка, что и жесткость направляющих качения, но требуют тщательного изготовления и пригонки рабочих поверхностей основных и вспомогательных граней направляющих. Жесткость закрытых гидростатических опор может быть
представлена в виде
где S — расчетная площадь опоры; —начальный зазор при отсутствии нагрузки;
— безразмерная характеристика; при малых внешних нагрузках
59
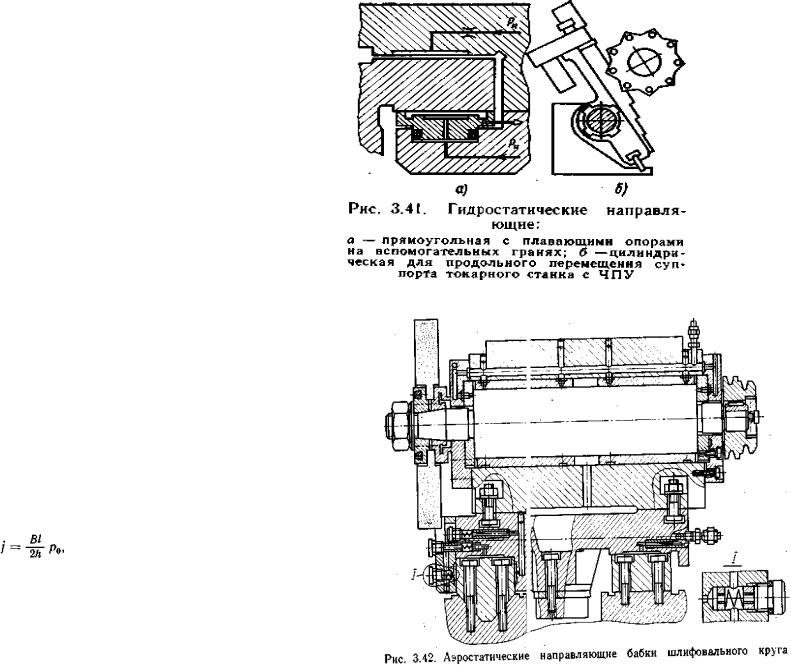
Для преодоления технологических трудностей пригонки основных и вспомогательных граней в станках получили распространение плавающие опоры (рис. 3.41, а), способные компенсировать непараллельность рабочих граней направляющей. Плавающую опору устанавливают в планке подвижного узла с возможностью свободного перемещения в вертикальном направлении и небольшого поворота относительно горизонтальных осей, что обеспечивает компенсацию и угловых погрешностей.
В гидростатических направляющих преимущественное распространение получила прямоугольная исходная форма, но встречаются станки с цилиндрическими направляющими (рис. 3.41, б), которые отличаются технологичностью и формой, удобной для создания надежных уплотнений.
А э р о с т а т и ч е с к и е н а п р а в л я ю щ и е весьма перспективны для точного позиционирования, поскольку обеспечивают весьма низкое трение при передвижении, а при фиксации узла после выхода в заданную позицию и сброса давления воздуха за время менее 0,1 с создают при высоком уже трении надежное соединение. К недостаткам аэростатических направляющих следует отнести малую нагрузочную способность, невысокое по сравнению с гидростатическими направляющими демпфирование и склонность к отказам из-за причин случайного характера (засорение магистралей и рабочего зазора, отказы системы питания и т. п.). Нагрузочная способность аэростатических направляющих может быть повышена при автономной системе питания от отдельного компрессора, а динамические характеристики обеспечиваются за счет минимизации объема воздуха в рабочем зазоре.
Жесткость аэростатических направляющих можно на стадии эскизного проектирования определять, пользуясь приближенной формулой
где В — ширина рабочей грани; /— длина кармана (микрока навки); h
— воздушный зазор; — давление питания
На
60
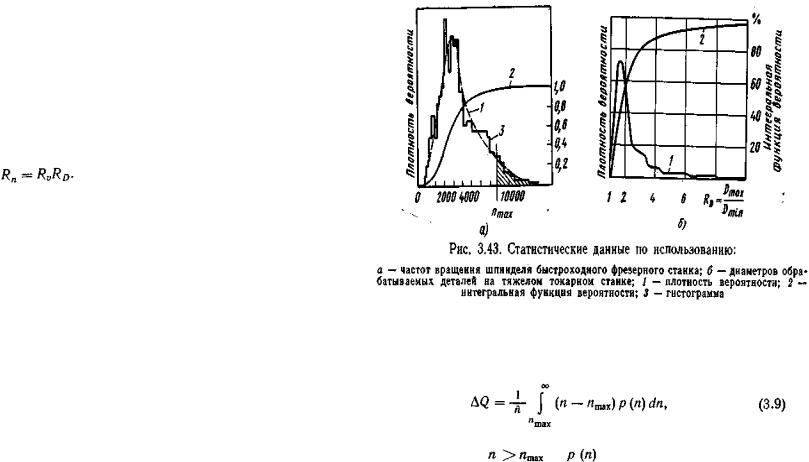
рис. 3.42 дан пример конструктивного оформления аэростатических направляющих для поперечного перемещения бабки шлифовального круга при модернизации круглошлифовального станка. Шпиндель станка также вращается в аэростатических опорах.
3.4. ГЛАВНЫЙ ПРИВОД И ШПИНДЕЛЬНЫЕ УЗЛЫ
Важнейшими исходными данными при проектировании главного привода станков с ЧПУ являются диапазон регулирования частоты вращения шпинделя и полезная мощность во всем рабочем диапазоне.
Д и а п а з о н р е г у л и р о в а н и я ч а с т о т ы в р а щ е н и я ш п и н д е л я зависит от диапазона
, необходимых для обработки скоростей резания и диапазона
размеров деталей (токарные станки) или размеров инструмента (фрезерование, сверление и т. п.):
Диапазон устанавливают по результатам анализа того множества деталей и того набора технологических операций, который необходимо реализовать на станке. При этом скорости резания должны обеспечивать оптимальные условия обработки. Если предварительные сведения о семействе обрабатываемых деталей недостаточны, то можно использовать статистические данные, полученные в реальных условиях производства, близких к проектным (рис. 3.43).
Реализация всего требуемого диапазона с охватом 100 % деталей обработкой при оптимальных скоростях резания ведет к удорожанию главного привода, а иногда и технически невыполнима. Оптимизация диапазона
основана на том, что при оправданном его сокращении соответствующая экономия стоимости главного привода перекрывает повышение затрат при изготовлении деталей с некоторой потерей производительности, которая может быть подсчитана исходя из следующих соображений. Если принять, что технологическая производительность пропорциональна скорости резания и соответственно для данной детали — частоте вращения
шпинделя, то потерю производительности для тех деталей, которые оказались в зоне частот выше принятого, можно оценить как
где — среднее арифметическое частот вращения в отброшенном
верхнем интервале ; |
— текущая ордината |
кривой |
распределения частот (рис. 3.43, а). |
|
|
Выражение |
(3.9) |
можно |
после некоторых преобразований и интегрирования |
привести |
|
к виду |
|
|
61