
Учебное пособие 800233
.pdfсиликатного компонента, для чего известь и компонент предварительно смешивали, затворяли водой и гидратировали. Компактирование смеси прессованием проводилось после завершения процесса гидратации извести в смеси.
Полученные сырьевые смеси при необходимости доувлажняли таким количеством воды, которое обеспечивало возможности формования и получения бездефектных образцов в виде цилиндров размером 30 × 30 мм. Прессование в случае модельных систем осуществлялось на гидравлическом прессе при удельном давлении 100 МПа.
С учетом результатов первого этапа исследований на втором этапе эксперименты проводили с использованием метода активного планирования. Применялось центральное (с центральной и «звездными» точками) композиционное (на двух уровнях с тремя факторами 23), исключающее случайные ошибки планирование. В качестве варьируемых факторов приняты массовая доля алюмосиликатного наполнителя по отношению к портландиту Н:П, влажность сырьевой смеси по показателю В/Т, прессовое давление Р.
Анализ участия природных и техногенных алюмосиликатов в формировании структуры композита проводили с использованием рентгенофазового (ДРОН-4), электронномикроскопического (растровый электронный микроскоп «JEOL – JSM-6380LV») методов анализа, метода инфракрасной спектроскопии (спектрометр «Vertex 70»).
Для композита оценивались средняя плотность, влажность материала в образцах после прессования, предел прочности при сжатии непосредственно после изготовления (через 1 ч), а также через 1, 3, 7, 28 сут после изготовления. Испытания вели в сухом и водонасыщенном состоянии, по которым вычисляли коэффициент размягчения материала.
Характеристики структуры и свойств исследуемых образцов оценивали по результатам испытаний малых выборок, количество образцов в которых составляло от 6 до 12. Доверительные интервалы оценок математического ожидания изучаемых показателей задавали с вероятностью 0,95. Относительная ошибка опытов в экспериментах не превышала 10 %.
Алюмосиликаты как структурообразующий компонент портландитоалюмосиликатных систем твердения
Возможность «структурного сочетания» алюмосиликатных компонентов с кристаллами портландита определяется их составом и неравновесностью энергетического состояния. Многообразие алюмосиликатных компонентов, представленных природными и техногенными их разновидностями (рис. 2), характеризуется различной реакционной способностью, как следствие различного энергетического их состояния, предопределяемого природными процессами образования компонентов или их технологической обработкой, например, термической активацией при обжиге, механо-химической активацией при помоле и т.п.
11
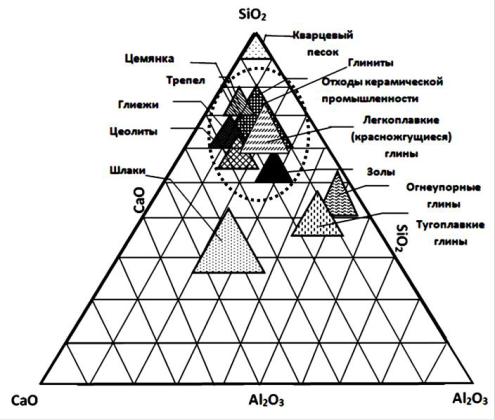
Рис. 2 – Положение компонентов на диаграмме Аl2О3- SiO2 - СаО
Расположение компонентов природного и техногенного происхождения их на тройной диаграмме СаО – SiO2 – Al2O3 позволяет выделить область, в которой они сосредоточены. Из выделенной области для исследований нами были выбраны два вида алюмосиликатных компонентов – цеолитовый туф (представитель природного типа), и отход производства керамики (представитель «техногенного» типа). Цеолитовый туф — наиболее интересный с позиции возможного структурообразования природный каркасный алюмосиликат, который обладает возможностью изменения химического состава кристаллов, а также формы и размеров внутрикристаллических пор, связанных с легкой перестройкой внутри каркаса и способностью замещения катионов в каналах на другие катионы. Бой керамического кирпича выбран как наиболее интересный представитель техногенного типа.
Осуществлено тестирование структурно-значимых физикомеханических и физико-химических характеристик этих двух видов алюмосиликатных компонентов, принятых для исследования. Дисперсным и элек- тронно-микроскопическим анализами показано, что тонкомолотые алюмосиликатные компоненты можно отнести к тонко- и микро-размерным (рис. 3).
По результатам рентгено-фазового анализа определено, что бой керамического кирпича включает кварц, шпинель, анортит, галуазит, а цеолит - клиноптиллолит, монтмориллонит, полевой шпат (рис. 4).
12
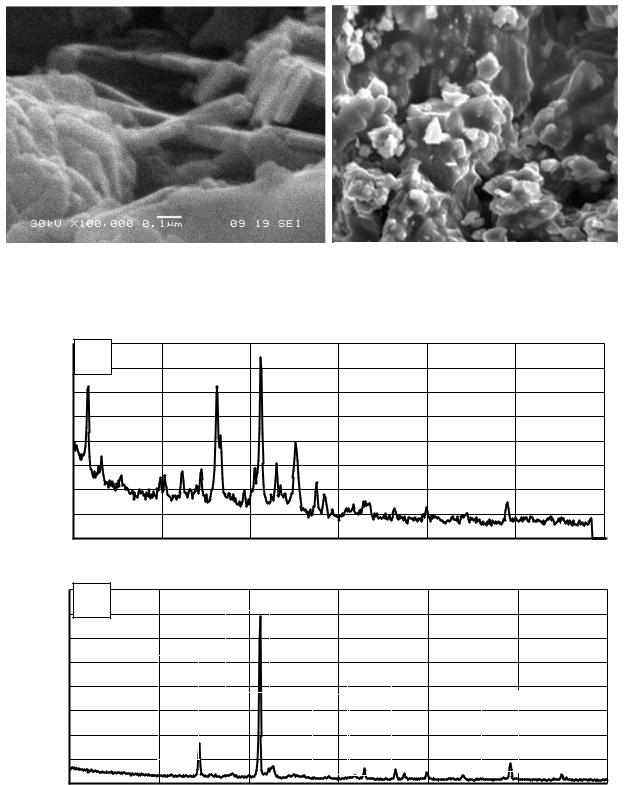
1 |
|
2 |
|
|
|
|
|
|
|
|
|
Рис. 3 - Электронномикроскопические фотографии образцов: |
||||
|
|
|
|
|
1 – молотого цеолитового туфа; |
|
|
|
|
|
|
2 – молотого боя керамического кирпича. |
|
||
|
1600 |
1 |
|
|
|
|
|
Интенсивность. отн.ед. |
1400 |
|
|
|
|
|
|
|
|
клиноптилолит |
кварц |
клиноптилолит |
|
||
1200 |
гейландит |
|
|
||||
1000 |
гейландит |
|
|||||
800 |
|
||||||
600 |
кварц |
||||||
400 |
|||||||
200 |
|||||||
|
0 |
|
|
|
|
|
|
|
10 |
20 |
30 |
40 |
|
50 |
60 |
70 |
|
|
|
|
Угол 2θ, град |
|
|
|
|
|
8000 |
2 |
|
|
|
|
|
|
. |
|
|
|
|
|
|
|
|
7000 |
|
|
|
|
|
|
|
|
.ед |
|
|
|
|
|
|
|
|
|
|
|
|
|
|
|
|
|
Интенсивность, отн |
6000 |
|
|
|
|
|
|
|
5000 |
|
кварц |
|
|
|
|
|
|
4000 |
тридимит |
|
|
|
|
|
||
3000 |
анортит |
шпинель |
|
анортит |
|
|||
2000 |
гематит |
|
||||||
1000 |
|
|||||||
|
|
|||||||
|
0 |
|
|
|
|
|
|
|
|
10 |
20 |
30 |
40 |
|
50 |
60 |
70 |
|
|
|
|
Угол 2θ, град |
|
|
|
Рис. 4 - Рентгенограммы образцов: 1-тонкомолотого цеолитового туфа;
2- тонкомолотого боя керамического кирпича
13

На спектрограммах цеолитового туфа и боя керамического кирпича (рис. 5) наиболее интенсивная полоса при 1052 см -1 соответствует асимметричным валентным колебаниям связи Si-O-Si; полосы при 800 -780 см -1 связаны с валентными колебаниями связи Al – O связи, 1620 см -1 – полоса деформационных колебаний молекул воды.
|
1,1 |
1 |
|
|
|
|
|
|
|
|
|
|
|
|
|
|
|
|
|
|
|
|
|
|
1 |
|
|
|
|
|
|
|
|
|
|
% |
0,9 |
|
|
|
|
|
|
|
|
|
|
0,8 |
|
|
|
|
|
|
|
|
|
|
|
Пропускание, |
|
|
|
|
|
|
|
|
|
|
|
0,7 |
|
|
|
|
|
|
|
|
|
|
|
0,6 |
|
|
|
|
|
|
|
|
|
|
|
0,5 |
Рис. 5 – Ренгенограмма образца молотого цеолитового туфа |
|
|||||||||
0,4 |
|
||||||||||
|
|
|
|
|
|
|
|
|
|
||
|
|
|
|
|
|
|
|
|
|
|
|
|
0,3 |
|
|
|
|
|
|
|
|
|
|
|
0,2 |
|
|
|
|
|
|
|
|
|
|
|
500 |
900 |
1300 |
1700 |
2100 |
2500 |
2900 |
3300 |
3700 |
4100 |
4500 |
|
|
|
|
|
Волновое число, см -1 |
|
|
|
|
|
1,1 |
2 |
|
|
|
|
|
|
|
|
|
|
|
|
|
|
|
|
|
|
|
|
|
|
1 |
|
|
|
|
|
|
|
|
|
|
, % |
0,9 |
|
|
|
|
|
|
|
|
|
|
0,8 |
|
|
|
|
|
|
|
|
|
|
|
Пропускание |
0,7 |
|
|
|
|
|
|
|
|
|
|
0,6 |
|
|
|
|
|
|
|
|
|
|
|
0,5 |
|
|
|
|
|
|
|
|
|
|
|
0,4 |
|
|
|
|
|
|
|
|
|
|
|
0,3 |
|
|
|
|
|
|
|
|
|
|
|
|
|
|
|
|
|
|
|
|
|
|
|
|
0,2 |
|
|
|
|
|
|
|
|
|
|
|
500 |
900 |
1300 |
1700 |
2100 |
2500 |
2900 |
3300 |
3700 |
4100 |
4500 |
|
|
|
|
|
Волновое число, см -1 |
|
|
|
|
Рис. 5 - ИК – спектрограммы образцов: 1 – молотого цеолитового туфа
2 - молотого боя керамического кирпича
Экспериментальные исследования на модельных системах
Целью проведения экспериментов на модельных системах являлось исследование возможности получения компактированного композиционного материала с выбранными компонентами алюмосиликатного состава природного и техногенного типа.
Установлено (табл. 3), что в А-варианте технологии при реализации I-го способа подготовки кристаллов портландита композит непосредственно после формования обладает относительно невысокой прочностью – 5 - 6 МПа как при использовании молотого боя керамического кирпича, так и цеолитового туфа. Однако к семи суткам прочность повышается до 10 и 11 МПа соответственно (табл. 3). Применение II –го способа подготовки портландита позволяет получить непосредственно после компактирования прочность 8 МПа, которая к
14

28 сут возрастает до 14,3 - 17,4 МПа.
Реализация Б – варианта технологии для указанных способов получения портландита обеспечивает формирование композита, обладающего прочностью непосредственно после компактирования 9-10 МПа, что в А-варианте технологии достигается только к семи суткам.
Таблица 3 Прочность портландито-алюмосиликатного композита в зависимости от способа получения кристаллов портландита при реализации варианта гидратации в присутствии наполнителя
Способ |
Вариант |
|
Предел прочности при сжатии, |
|||||
гидратации |
|
|
|
МПа |
|
|
||
технологи- |
|
|
|
|
|
|||
извести |
|
|
|
|
|
|
|
|
|
через |
|
в возрасте, сут |
|
||||
ческого |
|
|
|
|||||
при полу- |
|
один |
|
|
||||
сочетания |
Вид наполнителя |
|
|
|
|
|
||
|
|
|
|
|
||||
чении кри- |
час |
|
|
|
|
|
||
портландита |
|
|
|
|
|
|
||
сталлов |
|
после |
|
|
|
|
|
|
и |
|
1 |
|
3 |
7 |
28 |
||
портланди- |
|
формо- |
|
|||||
наполнителя |
|
|
|
|
|
|
||
та |
|
вания |
|
|
|
|
|
|
|
|
|
|
|
|
|
||
|
|
Тонкомолотый цеолит |
6,0 |
6,1 |
|
6,4 |
7,9 |
16,5 |
I |
|
|
|
|
|
|
|
|
|
Тонкомолотый бой |
5,6 |
5,4 |
|
6,6 |
10,0 |
15,8 |
|
|
|
керамического кирпича |
|
|||||
|
|
|
|
|
|
|
|
|
|
|
Тонкомолотый цеолит |
8,1 |
8,4 |
|
11,1 |
11,2 |
17,4 |
II |
|
Тонкомолотый бой |
8,0 |
8,5 |
|
8,8 |
8,8 |
14,3 |
|
|
керамического кирпича |
|
|||||
|
А |
|
|
|
|
|
|
|
|
Тонкомолотый цеолит |
5,4 |
5,5 |
|
7,6 |
10,3 |
12,2 |
|
|
|
|
||||||
III |
|
Тонкомолотый бой |
4,8 |
6,3 |
|
6,4 |
6,4 |
8,2 |
|
|
керамического кирпича |
|
|||||
|
|
|
|
|
|
|
|
|
|
|
Тонкомолотый цеолит |
3,0 |
4,1 |
|
4,1 |
7,93 |
12,2 |
IV |
|
Тонкомолотый бой |
5,6 |
5,6 |
|
5,6 |
9,9 |
11,3 |
|
|
керамического кирпича |
|
|||||
|
|
|
|
|
|
|
|
|
|
|
Тонкомолотый цеолит |
9,4 |
10,5 |
|
10,6 |
14,3 |
15,6 |
I |
|
|
|
|
|
|
|
|
|
Тонкомолотый бой |
8,8 |
9,3 |
|
9,4 |
11,4 |
12,2 |
|
|
|
керамического кирпича |
|
|||||
|
|
|
|
|
|
|
|
|
|
|
Тонкомолотый цеолит |
9,1 |
9,4 |
|
11,1 |
11,2 |
17,0 |
II |
|
Тонкомолотый бой |
10,2 |
10,5 |
|
10,8 |
12,8 |
15,6 |
|
|
керамического кирпича |
|
|||||
|
Б |
|
|
|
|
|
|
|
|
Тонкомолотый цеолит |
3,0 |
4,1 |
|
5,4 |
7,9 |
14,2 |
|
|
|
|
||||||
III |
|
Тонкомолотый бой |
5,6 |
5,4 |
|
5,6 |
10,0 |
12,6 |
|
|
керамического кирпича |
|
|||||
|
|
|
|
|
|
|
|
|
|
|
Тонкомолотый цеолит |
2,9 |
4,1 |
|
5,4 |
7,9 |
8,9 |
IV |
|
Тонкомолотый бой |
5,6 |
5,6 |
|
5,6 |
9,9 |
13,2 |
|
|
керамического кирпича |
|
|||||
|
|
|
|
|
|
|
|
Определено, что коэффициент размягчения прессованных портландитоалюмосиликатных композитов составляет 0,75 - 0,85. Это свидетельствует об относительно высокой водостойкости материала и доказывает, что прочность материала определяется возникшими связями физико-химического порядка, а не силами капиллярного стяжения.
По результатам модельных исследований для Б-варианта технологии, как наилучшего решения, предлагается применение II -го способа подготовки
15
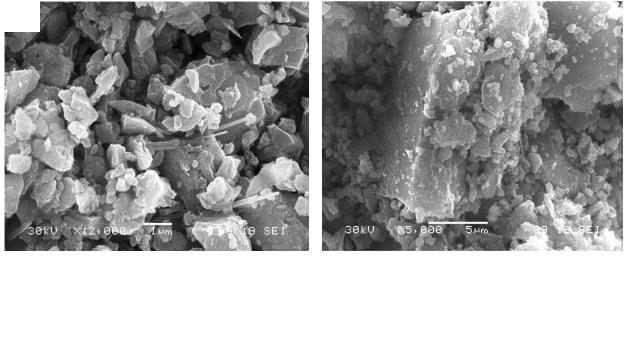
кристаллов портландита, когда гидратация ведется при температуре воды и компонентов 100 0 С. Такое решение способствует получению максимума прочности образца после компактирования.
В раздельном А - варианте, который в целом уступает Б – варианту, рекомендуется реализовывать I - ый способ подготовки кристаллов портландита, когда гидратация СаО осуществляется в нормальных температурных условияхпри (17 ± 2) 0С. Это обеспечивает минимум дополнительных (на разогрев компонентов) энергетических затрат в технологии.
Методом электронной микроскопии (рис. 6) определено, что структура композита складывается из плотно уложенных кристаллов размером до 0,3 – 0,6 мкм, образующих слитный конгломерат.
1 |
|
2 |
|
|
|
Рис. 6 – Электронно-микроскопические фотографииРис.. Электроннопортландито-микроскопиче-алюмосиликатногокая фо ография
(с наполнителем в виде тонкомолотого цеолита) портландито-алюмосиликатного композита
композита с наполнителем:
(с наполнителем в виде тонкомолотого боя керами-
1- молотый цеолитовый туф, ческого кирпича)
2- молотый бой керамического кирпича
Данные ИК-спектроскопии (рис. 7), а также рентгенографические данные (рис. 8) свидетельствуют о формировании в композите связей как между кристаллами портландита, так и между кристаллами портландита и алюмосиликатным компонентом. На спектрограммах наблюдаются полосы валентных колебаний СаО – (560 -600 см -1), [Si, Al] – O при 900-1100 см -1 , на рентгенограмме отмечены пики, соответствующие как Са(ОН)2 - d = 2,63; 1,916; 1,68 Å), так и линии, характерные для низкоосновных гидросиликатов Са
(d = 3,34; 3,07; 2,42; 1,876 Å) и гидроалюминатов Са.
Проведенные структурные исследования свидетельствуют о том, что при использовании активных алюмосиликатных компонентов реализуются механизмы отвердевания за счет формирования кристаллических сростков, то есть кристаллитной структуры портландитовой матричной субстанции при одновременном образовании композитной структуры и развитии механо- физико-химических связей портландита с алюмосиликатным компонентом по обозначенным ранее механизмам.
16
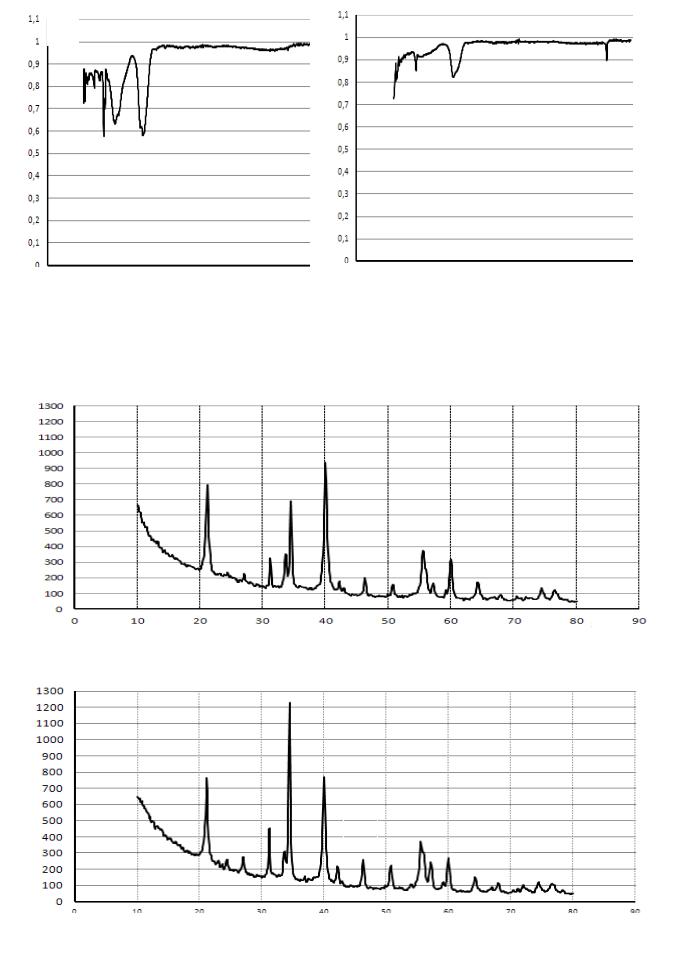
|
1 |
|
|
|
|
|
|
|
|
|
|
2 |
|
|
|
|
|
|
|
|
Пропускание, % |
|
|
|
|
|
|
|
Пропускание, % |
|
|
|
|
|
|
|
|
|
|
|
|
|
|
|
|
|
|
|
|
|
|
|
|
|
|
|
|
|
|
|
||
0 |
1000 |
2000 |
3000 |
|
4000 |
|
0 |
|
|
1000 |
|
2000 |
3000 |
4000 |
||||||
|
|
|
|
|
|
|
Волновое число, см-1 |
|
||||||||||||
|
|
|
Волновое число, см-1 |
|
|
|
|
|
|
|
|
|
|
|||||||
|
Рис. 7 – ИК-спектрограммы композиционного материала с наполнителем: |
|
||||||||||||||||||
|
|
|
|
|
1- тонкомолотый цеолитовый туф; |
|
|
|
|
|||||||||||
|
|
|
|
2- тонкомолотый бой керамического кирпича |
|
|
||||||||||||||
|
|
|
|
|
|
|
|
|
|
|
|
|
|
|
|
|
|
|
|
|
|
|
1 |
|
|
|
|
|
|
|
|
|
|
|
|
|
|
|
|
|
|
отн.ед |
|
|
|
|
4,87 |
|
|
|
2,63 |
|
|
|
|
|
|
|
|
|
|
|
|
|
|
|
|
|
|
|
|
|
|
|
|
|
|
|
|
|
|||
Интенсивность, |
|
|
|
|
3,34 |
3,27 3,07 |
3,049 |
2,42 |
|
|
1,916 |
1,876 |
1,787 |
1,684 |
|
|
|
|
||
|
|
|
|
|
|
|
|
|
|
|
|
|
|
|
|
|
|
|
Угол 2θ, град |
|
|
|
|
|
|
|
|
|
|
|
|
|
|
|
|
|
|
|
|
|
|
|
|
2 |
|
|
|
|
|
|
|
|
|
|
|
|
|
|
|
|
|
|
отн.ед |
|
|
|
|
|
|
3,049 |
2,63 |
|
|
|
|
|
|
|
|
|
|
|
|
|
|
|
|
|
|
|
|
|
|
|
|
|
|
|
|
|
|
|||
Интенсивность |
|
|
|
4,87 |
|
|
|
|
|
|
|
|
|
|
|
|
|
|
|
|
, |
|
|
|
|
|
|
|
|
|
|
|
|
|
|
|
|
|
|
||
Интенсивность |
|
|
|
3,307 |
3,27 |
3,07 |
2,42 |
2,25 |
2,11 |
1,916 |
1,898 |
1,787 |
1,684 |
1,59 |
|
|
||||
|
|
|
|
|
Рис. 8 - |
Рентгенограммы образцов: |
|
Угол 2θ, град |
|
|||||||||||
|
|
|
|
|
1-молотого цеолитового туфа; |
|
|
|
|
|
2- молотого боя керамического кирпича
17
Исследование и оптимизация рецептурно-технологических факторов получения портландито-алюмосиликатного композита
Второй этап исследований проводили методом активного планирования эксперимента для решения трех оптимизационных задач, связанных с критериями цели: 1) максимума прочности непосредственно после формования; 2) максимума количества наполнителя в композите при условии достижения задаваемой прочности; 3) минимума величины прессового давления с условием получения регламентированной прочности. В качестве варьируемых факторов приняты массовая доля алюмосиликатного наполнителя по отношению к портландиту Н:П, влажность сырьевой смеси по показателю В/Т, прессовое давление Р.
Эти факторы для использованных видов наполнителя, способов и вариантов получения кристаллов портландита и формовочной смеси кодированы соответственно как Х1, %; Х2, %; Х3, МПа (табл. 4).
|
|
|
Таблица 4 |
Входные факторы и пределы их изменения в эксперименте 23 |
|||
Наименование технологических |
Массовая доля |
Влажность |
Прессовое |
факторов |
наполнителя, % |
сырьевой смеси, |
давление, МПа |
|
|
% |
|
|
|
|
|
Кодированные обозначения |
X1 |
X2 |
X3 |
Основной уровень |
50 |
12 |
80 |
Верхний уровень |
80 |
16 |
120 |
Нижний уровень |
20 |
8 |
40 |
Верхняя «звездная»точка |
91 |
17,5 |
135 |
Нижняя «звездная точка» |
9 |
6,5 |
25 |
По результатам проведенных экспериментов и их математической обработки получены полиномиальные модели показателя предела прочности при сжатии (Rсж, МПа) и плотности (ρm , кг/м3 ) композита:
Rсж {I,(А), К} |
=6,68 –1,83Х1+ 2,4 Х3- 0,52Х12 -0,51Х22+0,37Х32- 0,15Х1· Х2 -1,69Х1· Х3; |
Rсж {II,(Б), К} |
= 9,53-1,13X1+1,99X3-0,92X12-0,35X22+1,55X32+0,73X1·X2-1,2X1·X3-0,65X2·X3; |
Rсж {I,(А), Ц) |
=7,09-1,59Х1+1,05Х2+2,92Х3+1,28Х32-0,88Х1·Х3+0,45Х2·Х3; |
Rсж {II,(Б), Ц} =9,51-2,72Х1+0,33Х2+4,08Х3-1,52Х22+1,22Х32-2,36Х1·Х3; |
|
ρm {I,(А), К} =1612+62,36Х1+ 25,14 Х2+81,01 Х3-29,56 Х32-21,25Х2 Х3; ;МПа |
|
ρm {I, (Б), К} |
=1712+63,16X1+24,53 Х2 +78,11X3-28,36Х32-20,45Х2 Х3; |
ρm {I, (А), Ц} |
=1693,3+56,6Х3+60,22Х12+35,01Х1·Х3-55,3Х2·Х3; |
ρm {II, (Б), Ц} |
=1678,6-33,23Х1+70,2Х3+37,05 Х12 +24,2Х22+27,5Х1·Х2; |
где обозначения {I, (А), К}, {II, (Б), К}, {I, (А), Ц}, {II, (Б), Ц}– соответству-
ют показателям Rсж и ρm пределу прочности при сжатии и средней плотности непосредственно после изготовления, при компактировании кристаллов портландита, полученных по I или II способу гидратации соответственно, по раздельной (А) или совмещенной (Б) технологии, (К) - с наполнителем– тонкомолотый бой керамического кирпича, (Ц) - с наполнителем– тонкомолотый цеолитовый туф.
18
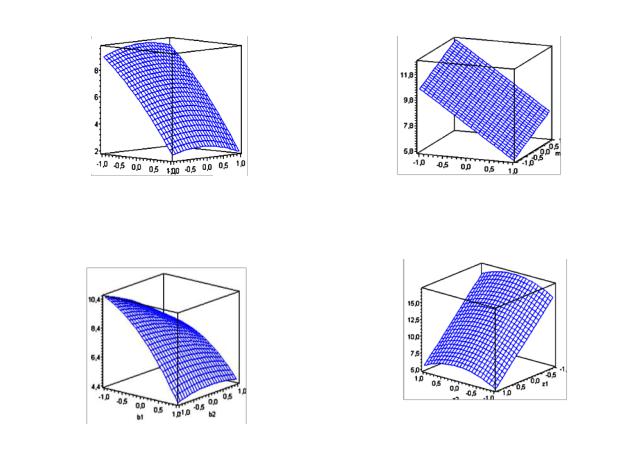
По уравнениям регрессии построены поверхности отклика (рис. 9), которые иллюстрируют границы значений параметров получения изделий с максимально возможной прочностью непосредственно после компактирования.
А - вариант технологии и I способ подготовки кристаллов портландита
Предел прочности при сжатии , МПа
X1 X2
тонкомолотый цеолит
Б - вариант технологии и IIой
при |
|
|
|
МПа |
|
|
|
прочности |
|
|
|
, |
|
|
|
сжатии |
|
|
|
Предел |
|
|
|
|
|
X2 |
|
|
X1 |
|
|
|
|
|
|
|
|
|
|
тонкомолотый бой керамического кирпича
способ подготовки кристаллов портландита
Предел прочности при сжатии , МПа
X1 |
|
X2 |
|
|
|
тонкомолотый цеолит
при |
|
|
|
МПа |
|
|
|
прочности |
|
|
|
, |
|
|
|
сжатии |
|
|
|
Предел |
|
|
|
|
|
X2 |
|
|
X1 |
|
|
|
|
|
|
|
|
|
|
|
|
|
|
тонкомолотый бой керамического кирпича
Рис. 9 - Поверхности отклика, отражающие зависимость предела прочности при сжатии от технологических параметров при фиксированном значении удельного давления прессования 120 МПа при реализации раздельной (А - вариант) и совмещенной (Б - вариант) технологии для указанных способов подготовки кристаллов портландита
Установлено, что с увеличением давления прессования (фактор X3) во всех случаях прочность растет при сравнительно одинаковой средней плотности (1700 – 1790 кг/м3 и 1800 - 1860 кг/м3). При максимальном давлении прочность непосредственно после формования составляет 8,7-10,5 МПа для композита с наполнителем – тонкомолотый бой керамического кирпича и 10,5-14,5 МПа для композита с наполнителем – тонкомолотый цеолитовый туф. Увеличение содержания наполнителя в композите выше 28-32 % снижает его прочностные показатели. Увеличение влажности смеси (фактора X2) свыше 15 % сопровождается снижением значения прочности непосредственно после формования.
Для поставленных вариантов оптимизационных задач по полиномиальным моделям определены рациональные значения рецептурнотехнологических факторов (табл. 5).
19
|
|
|
|
|
|
|
Таблица 5 |
|
|
|
Рациональные значения рецептурно-технологических факторов |
||||||
Крите- |
Вид алюмоси- |
Вариант |
Массовая |
Влаж- |
Прессо- |
Предел проч- |
||
рий |
ликатного |
техноло- |
доля |
ность |
вое дав- |
ности при сжа- |
||
цели |
компонента |
гии |
компо- |
формо- |
ление, |
тии непосред- |
||
|
|
|
|
нента, % |
вочной |
МПа |
ственно после |
|
|
|
|
|
|
смеси, % |
|
формования, |
|
|
|
|
|
|
|
|
МПа |
|
) = |
|
Цеолитовый |
А |
28-30 |
10-12 |
100-110 |
≥(11-13) |
|
max |
туф |
Б |
28-30 |
10-12 |
100-110 |
≥(13-15) |
||
0 |
||||||||
R(τ |
|
|
|
|
|
|
||
R |
Бой керамиче- |
А |
30-32 |
10-12 |
110-120 |
≥(8-10) |
||
|
|
|||||||
|
|
ского кирпича |
Б |
30-32 |
10-12 |
110-120 |
≥(9-11) |
|
= |
|
Цеолитовый |
А |
20-25 |
9-11 |
90 |
≥10 |
|
≥10) |
|
туф |
|
|
|
|
||
min |
Б |
20-25 |
9-11 |
90 |
||||
|
||||||||
|
|
|||||||
|
|
|
||||||
0 |
|
|
|
|
|
|
||
Р (Rτ |
Р |
Бой керамиче- |
А |
30-32 |
10-12 |
100-110 |
|
|
|
|
|
|
|
||||
|
ского кирпича |
Б |
30-32 |
10-12 |
100-110 |
|
||
|
|
|
|
|||||
|
|
|
|
|
|
|
|
|
|
|
Цеолитовый |
А |
42-45 |
12-14 |
≥120 |
≥9 к 3-м сут |
|
= |
|
|
|
|
|
|||
|
|
|
|
|
|
|||
|
|
|
|
|
|
|
||
≥10) |
|
туф |
Б |
40-45 |
10-12 |
≥120 |
9 - 10 к 3-м сут |
|
max |
|
|
|
|
|
|||
|
|
|
|
|
|
|||
|
|
38-42 |
9-11 |
≥120 |
8-10 |
|||
0 |
|
|
||||||
(Rτ Q |
|
А |
||||||
Бой керамиче- |
|
|
|
|
||||
|
|
|
|
|
||||
|
38-43 |
8-10 |
≥120 |
9-11 к 3-м сут |
||||
Q |
|
ского кирпича |
Б |
|||||
|
|
|
|
|
||||
|
|
|
|
|
|
|
||
|
|
|
|
|
|
|
|
При оптимальных рецептурно-технологических факторах получен материал, обладающий прочностью непосредственно после формования 10-14 МПа и упрочняющийся к 28 сут до 20 МПа, а к 500 сут - до 25 МПа. Рост прочности в материале объясняется образованием связей по обозначенным нами механизмам как в портландитовой матрице, так на границе матрицанаполнитель при реализации синтезного механизма формирования новообразований.
Практическая реализация результатов работы
Для двух вариантов технологии разработаны технологические схемы, а для совмещенного (Б - варианта), предлагаемого нами как наиболее перспективного, разработаны предложения к технологическому регламенту изготовления прессованного кирпича; в стендовых экспериментах изготовлена опытная партия прессованного кирпича размерами 250×120×88 мм.
На основе разработанных предложений к технологическому регламенту подготовлен вариант компоновки технологической линии по производству прессованного кирпича мощностью 5 млн. шт. в год. В качестве основного оборудования линии предлагается применение дезинтеграторов, гидраторов барабанного типа, прессов. Линия может входить в состав муниципальных центров строительного производства.
Предлагаемая технология на основе реализации механизмов контактноконденсационного твердения наряду с цементной (гидратационной), силикатной (гидротермально-синтезной) определяет еще один путь получения
20