
Учебное пособие 800195
.pdf= 20÷-20°С. При оценке сопротивления сварного соединения зарождению трещин швы труб располагали в растянутой зоне, а при испытании основного металла — в сжатой зоне. При оценке сопротивления зарождению трещин основного металла труб на части патрубков наносили надрез глубиной 1 — 1,5 мм при радиусе дна надреза 0,5 мм. Проведенные исследования показали следующее:
в основном металле стали 10 при испытании более 150 патрубков без надреза из кипящих и полуспокойных плавок ни в одном случае зарождения трещин не наблюдалось;
при испытании 90 патрубков с надрезом по основному металлу зарождение трещин наблюдалось у кипящих сталей при деформации в зоне надреза 4,5—5, у полуспокойных сталей— 3—10%, т. е. стали кипящих и полуспокойных плавок при толщине 6 мм и диаметре труб 168 и 219 мм имели относительно удовлетворительное сопротивление зарождению трещин;
в сварном соединении труб при испытании более 100 патрубков наблюдалось раскрытие швов, сваренных токами высокой частоты, у трех патрубков из кипящей стали 10 и у четырех патрубков из полуспокойных сталей, что свидетельствует о недостаточно стабильном качестве заводского продольного шва труб;
у всех исследованных вариантов труб не установлено влияние температуры испытания в диапазоне от 20 до —20 °С на зарождение трещин.
Результаты исследований показывают целесообразность применения указанного типа сталей для городских газовых сетей с давлением до 1,2 МПа и нефтегазопроводов при положительной температуре эксплуатации. Поскольку применение кипящих и полуспокойных сталей позволяет увеличить выход годного проката на 8—12 % и снизить себестоимость производства 1 т труб, были проведены более широкие исследования листовых (толщиной 8—10 мм) сталей углеродистых марок, в том числе упрочненной марганцем ВСт. ЗГ и обычной ВСт. 3 — спокойной, полуспокойной и кипящей.
40
|
|
|
|
Таблица 4 |
|
Свойства углеродистых сталей (круглые образцы) |
|
||||
Марка |
σ0,2, МПа |
σВ, МПа |
σ5, % |
Ψ, % |
|
|
|
|
|
|
|
ВСт.ЗГ |
300 |
500 |
29 |
65 |
|
ВСт.Зсп |
250 |
420 |
30 |
60 |
|
ВСТ.Зпс |
250 |
450 |
30 |
60 |
|
ВСт.Зкп |
240 |
420 |
30 |
60 |
|
По ГОСТ 380—71 |
250 |
380—490 |
26 |
— |
|
|
|
|
|
|
|
Таблица 5 Ударная вязкость и волокно в изломе углеродистой стали (об-
разцы Менаже)
Марка |
KCU+20, |
|
KCU0, |
KCU-20, |
|
МДж/м2 В, |
|
МДж/м2 В, |
МДж/м2 В, |
|
% |
|
% |
% |
|
|
Не менее |
|
|
ВСт.3Г |
0,8 |
|
0,6 |
0,50 |
ВСт.3сп |
80-90 |
|
50-70 |
20-30 |
ВСт.3пс |
0,7 |
|
0,6 |
0,15-0,60 |
ВСт.3кп |
95-100 |
|
80-95 |
45-55 |
по ГОСТ |
0,6 |
|
0.4 |
0,30 |
380-71 |
60-70 |
|
30-40 |
5-10 |
ВСт.3сп |
0,6 |
|
0.4 |
0,25 |
|
70-80 |
|
30-45 |
5-10 |
|
0,7 |
|
- |
Более 0,3 |
|
- |
|
- |
- |
Химический состав сталей удовлетворял требованиям ГОСТ 380—71, а содержание углерода в плавках соответство-
41
вало верхнему пределу марочного состава — 0,19—0,23%. Свойства указанных сталей в горячекатаном состоянии на круглых образцах диаметром 6 мм приведены в табл. 4
Хладостойкость и вязкость стали определяли на поперечных к оси проката образцах Менаже (табл. 5).
Полученные данные показывают, что горячекатаная листовая сталь ВСт. ЗГ толщиной 8—10 мм (упрочненная марганцем) и ВСт. Зсп по вязкости и хладостойкости практически равноценны. Временное сопротивление стали ВСт.ЗГ (500 МПа) заметно выше сопротивления стали ВСт.Зсп (420 МПа), однако в ГОСТ 380—71 гарантируемые свойства обеих углеродистых марок стали практически равноценны, что не позволяет использовать повышенную прочность ВСт.ЗГ.
Зависимость ударной вязкости углеродистых сталей от температуры при толщинах 6—10 мм показана на рис. 7. Как видим, все исследованные марки углеродистой стали имеют, как правило, стабильную вязкость при температурах 20 °С и выше. В интервале температур от 20 до 0 °С вязкость заметно снижается, и тем больше, чем толще листовая сталь. Углеродистые стали толщиной 8—10 мм при температуре от 0 до — 10 °С не во всех случаях обеспечивают стабильное сопротивление вязкому разрушению применительно к условиям газопроводов. При использовании сварных труб диаметром менее 530 (мм из углеродистой стали необходимо учитывать, что они изготавливаются в основном из широкополосной стали толщиной 5, 6 и 8 мм (редко выше), свойства которой (прочность, хладостойкость и вязкость) повышаются по мере уменьшения толщины стенки.
В настоящее время, когда в металлургической промышленности все шире применяются методы непрерывной разливки и заметно снизилось количество вредных примесей в стали, экономические показатели и свойства сталей улучшаются, условия применения качественно выполненной углеродистой стали непрерывной разливки можно расширить. Опыт применения улучшенной углеродистой стали ВСт.З при строительстве резервуаров для хранения нефти и нефтепродуктов пока-
42
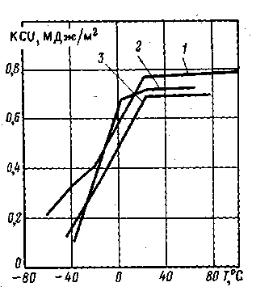
зывает, что углеродистые стали могут обеспечивать гарантированную вязкость до температуры —40 °С и хладостойкость до —10 °С.
Рис. 7. Зависимость ударной вязкости KCU листовой углеродистой стали (образцы Менаже) от температуры испытания и толщины листа:1 —сталь 10пс, h=6,8 мм; 2- Ст.Зсп, h=8— 10 мм; 3 — ВСт.Зпс и ВСт.Зкп, h = 8—10 мм
43
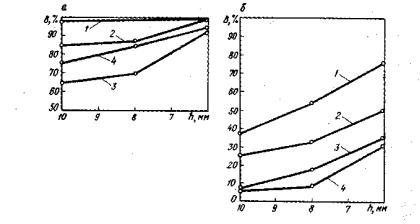
Рис. 8. Зависимость волокнистой составляющей в изломе от толщины образцов из углеродистых сталей при тем-
пературе испытания 20 °С (а) и —20 °С (б): 1 - ВСт.Зсп; 2 — ВСт.ЗГ; 3 — ВСт.Зпс; 4 — ВСт.Зкп
2.3. Низколегированные феррито-перлитные стали
При изготовлении труб для магистральных газонефтепроводов применяется несколько марок низколегированных сталей, поставляемых в горячекатаном или в нормализованном состоянии. Для труб диаметром 530—820 им используется горячекатаная сталь 17ГС, а также стали 09Г2, 10Г2С в различных модификациях, для труб диаметром 1020—1220 мм — простые нормализованные стали 17Г1С-У и в опытном порядке стали 15Г2АФЮ, упрочненные нитридами алюминия, и 13Г2АФ, упрочненные нитридами ванадия и др.
44
2.3.1 Влияние химических элементов на свойства феррито-перлитных сталей
Как уже указывалось, основными элементами, применяемыми при производстве стали для труб, являются углерод, марганец и кремний, а также раскисляющие и микролегирующие элементы — ванадий, ниобий, титан, алюминий и редкоземельные металлы. Кроме названных элементов, в состав стали неизбежно входят вредные примеси — сера и фосфор, а также газы — кислород, азот и водород. Рассмотрим влияние различных элементов на свойства стали. За последнее время хотя и появились новые марки стали для труб, но подход к созданию и производству нормализованных низколегированных сталей не изменился, а принципиально новые типы сталей, получаемые контролируемой прокаткой, будут рассмотрены ниже.
Прежде чем рассматривать влияние химических элементов на свойства стали, уточнить понятие «хладостойкость». Многие специалисты под хладостойкостью понимают обеспечение определенной величины ударной вязкости на образцах Менаже (KCU) или Шарпи (KCV) при заданной температуре. Для стали труб магистральных газопроводов такое понятие недостаточно, так как металл труб должен предупреждать образование протяженных вязких разрушений, а также хрупких разрушений лавинного типа. Поэтому хладостойкостью стали в газопроводах следует считать способность металла при заданной температуре обеспечивать вязкий характер излома труб в условиях высокоскоростного распространения разрушения. Хладостойкость стали труб обычно оценивают количеством вязкой составляющей в изломе полнотолщинных крупноразмерных образцов типа ДWТТ, а при толщине стенки труб менее 10 мм — на стандартных ударных образцах. Сопротивление стали протяженному вязкому разрушению определяют по работе, поглощенной образцом ДWТТ при разрушении, или по величине ударной вязкости на образцах с острым надрезом, испытанных при минимальной температуре эксплуатации га-
45
зопроводов.
Углерод повышает прочность стали, но снижает ее вязкость и ухудшает свариваемость. Поэтому количество углерода в низколегированных сталях для труб строго регламентируется— не более 0,20—0,22 %. Однако во многих марках стали для труб в зависимости от содержания марганца и кремния количество углерода принимают значительно меньшим. Влияние углерода на вязкость стали зависит от состояния металла, особенно от вида термической обработки. Неблагоприятное влияние углерода на вязкость усиливается после отжига, а нормализация и термическое улучшение повышают вязкость. Отрицательное влияние углерода также может быть уменьшено путем повышения однородности металла раскислением и модификацией в ковше, т. е. уменьшением развития ликвационных процессов при кристаллизации стали, обеспечением максимально дисперсного строения.
Марганец повышает прочность стали и в определенных пределах улучшает вязкость. Марганец способствует измельчению зерна и повышает дисперсность карбидов. Положительное влияние марганца может быть усилено введением в
сталь карбидообразующих элементов, обычно титана или ниобия, которые в определенной концентрации повышают ее прочностные характеристики и вязкость.
Влияние марганца необходимо рассматривать совместно с углеродом. В сталях для труб содержание марганца практически во всех марках ограничено 2%. При введении в сталь марганца более 2 % наблюдается заметное снижение вязкости. Положительное влияние марганца особенно хорошо проявляется при пониженном содержании углерода, поэтому такие марки стали, как 10Г2С и особенно 09Г2, применяются для производства труб в северном исполнении. Наиболее высокую вязкость имеют стали при отношении количества марганца к углероду более 7.
Кремний в количестве до 0,2—0,3 % применяется как раскислитель стали в процессе плавки. Кремний связывает кислород и способствует повышению прочности и вязкости ста-
46
ли. Опыт применения кремения для упрочнения низколегированных сталей труб неоднозначен. Считают, что содержание кремния более 0,5—0,6 % снижает вязкость и ухудшает свариваемость стали. В то же время имеется многолетний опыт производства и применения стали МК (в новой маркировке 09Г2СД) с содержанием кремния до 0,8 % в газонефтепроводах диаметром 530—620 мм. Большое применение находят стали 17ГС с содержанием кремния до 0,6%. Следовательно, при рациональном сочетании углерода, марганца и кремния можно получать качественные стали повышенной прочности и вязкости. Известны также марки стали для труб с содержанием кремния до 1 %. Однако в газонефтепроводах они не применяются. Дальнейшее повышение вязкости стали, легированной кремнием, может быть достигнуто путем совершенствования процессов выплавки, раскисления и модификации, более полной очистки стали от вредных примесей и усовершенствованием методов прокатки.
Алюминий является сильным раскислителем и одновременно оказывает эффективное модифицирующее действие на сталь. Последнее связано с выделением нитридов в процессе охлаждения стали. Алюминий в отличие от таких модификаторов, как титан, ниобий, ванадий, не образует карбидов. Нитриды алюминия препятствуют росту аустенитного зерна и приводят к образованию мелкозернистой вторичной структуры. Связывая свободный азот, алюминий снижает склонность стали к старению. Раскисление алюминием снижает температуру перехода в хрупкое состояние, повышает прочность и улучшает свариваемость стали. Оно особенно эффективно, когда выполняется вместе с кремнием. Важным преимуществом раскисления алюминием является то, что при этом практически не повышается стоимость стали.
Количество вводимого алюминия должно быть строго ограничено. Остаточное количество его в стали не должно превышать 0,05%. При большем количестве алюминия наблюдается увеличение неметаллических строчечных включений. В отдельных исследованиях, выполненных применительно к ста-
47
ли типа 17ГС, указывается, что оптимальное количество остаточного алюминия в стали находится в пределах 0,01—0,38%. Фактически все исследователи считают весьма желательным применение алюминия для раскисления и модифицирования низколегированной стали, однако нормы его количественного содержания по данным разных работ несколько расходятся.
Титан обычно используют в сочетании с алюминием в ограниченных количествах (примерно 0,02—0,03%), что позволяет несколько повысить прочность низколегированной нормализованной стали, измельчить структуру металла, улучшить свариваемость. Однако при использовании титана могут возникать технологические трудности в процессе производства стали, может снижаться ее пластичность. Поэтому металлургическая промышленность не всегда применяет титан. Отечественная промышленность имеет определенный опыт использования титана для модификации низколегированных сталей, в частности, титан предпочитают ванадию по экономическим соображениям. Применение титана имеет то преимущество, что его сульфиды при обычных температурах горячей прокатки менее деформируются, чем сульфиды марганца. Их вытяжка едва заметна, что препятствует образованию строчечных вытянутых включений. Титан как модификатор хорошо усваивается сталью,
стабильно ограничивает рост зерна. Опыты по применению титана в количествах примерно 0,15 % для упрочнения стали показали, что в листах толщиной до 7 мм временное сопротивление разрыву и предел текучести увеличиваются соответственно на 60 и 90 МПа, однако при этом снижается вязкость и повышается чувствительность к перегреву. В результате исследований было сделано заключение о неэффективности использования титана как упрочнителя в нормализованных сталях.
Ванадий широко используется для улучшения углеродистых сталей, измельчения зерна и повышения прочности низколегированных сталей, улучшения их свариваемости. Количество применяемого ванадия строго ограничено (менее 0,1
48
%). При содержании ванадия 0,1—0,15 % дальнейшего измельчения зерна не наблюдается, ударная вязкость при низких температурах уменьшается. Экспериментальные исследования [13] показали, что нормализованная сталь 17ГС при содержании 0,04—0,1% ванадия, 0,011—0,022% титана и обычном содержании углерода, марганца и кремния в трубах диаметром 1020 мм обеспечивает прирост временного сопротивления на 20—30 МПа, ударной вязкости КСU-40 на 0,1—0,3 МДж/м2. При этом качество заводских сварных швов труб не ухудшается. В низколегированных сталях для труб ванадий вводится в количестве до 0,1 %.
Ниобий — слабый раскислитель стали и сильный карбидообразующий элемент. При наличии в стали азота образует нитриды или карбонитриды. Ниобий является эффективным модификатором стали, он не вызывает ее загрязнения оксидами, улучшает технологичность стали при ее производстве, способствует улучшению свариваемости. Исследования стали, содержавшей 0,2 % углерода, 1,2 % марганца, 0,08 % кремния со ступенчато изменяющимся количеством ниобия от 0 до 0,1 %, показали, что при повышении содержания ниобия, количество выделившихся карбонитридов увеличивается, а их размер не изменяется, в результате чего получается необычайно тонкая вторичная структура (размер зерна в среднем в 3 раза меньше, чем у стали без ниобия). Предел текучести увеличивается на 80 МПа. Наиболее благоприятно действие ниобия проявляется в малых количествах (примерно 0,02— 0,03%), особенно в сочетании с алюминием (около 0,02%). В этом случае повышается предел текучести и временное сопротивление разрыву (примерно на 40 МПа), снижается склонность к старению, вязкость стали практически не меняется. Степень упрочнения стали ниобием увеличивается с понижением количества углерода. Так, у стали 10Г2 предел текучести повышается примерно на 30%, у стали 15Г2 — на 17%, а у стали 30Г2 —на 10%. Однако пластичность и вязкость стали несколько понижаются, а критическая температура хрупкости незначительно повышается.
49