
Учебное пособие 800195
.pdfкость и пластичность, улучшается свариваемость, повышается сопротивление стали разрушению в конструкции. В низколегированных сталях лучшее сочетание свойств достигается при содержании алюминия в металле от 0,02 до 0,05%. Максимальное снижение загрязненности, практическое отсутствие строчечных включений и остроугольных оксисульфидов, являющихся концентраторами напряжений, достигается при совместном введении в сталь алюминия {0,02—0,05%), кальция
(около 0,003%) и церия (0,01—0,03%) [19]. Такая обработка стали в ковше позволяет снизить индекс загрязненности неметаллическими включениями в 3—7 раз, при этом оставшиеся включения прижимают глобулярную форму. Вместе с тем эта обработка стали способствует снижению содержания в металле газов — кислорода и азота. В результате пластичность и вязкость стали достигают возможного максимума, заметно улучшается свариваемость.
Условия выплавки (кипящая, полуспокойная, спокойная) были важными технологическими параметрами процесса производства стали до применения метода непрерывной разливки. В процессе кристаллизации и охлаждения стали в изложницах в зависимости от их типа неметаллические включения и газы б значительной части могли быть удалены, в частности, при обрезке прибыльной части слитка. Принимались также меры по наиболее равномерному распределению включений по слитку
— кипящая закупоренная и полуспокойная стали.
2.1.2. Непрерывная разливка стали
Примерно в 70-х годах в металлургической промышленности нашей страны и за рубежом широкое распространение получил метод разливки стали в специальных установках непрерывной разливки. В этих установках жидкий и частично закристаллизовавшийся металл непрерывно перемещается относительно места заливки в специальных кристаллизаторах, образуя слиток неограниченной длины, который на выходе из установки разрезается на слябы размерами, кратными разме-
30
рам будущего листа или другого проката. Процесс кристаллизации металла при непрерывной разливке протекает на всей длине разливочной машины. В момент заливки сталь кристаллизуется по поверхности, затем при перемещении слитка в кристаллизаторах на протяжении нескольких десятков метров (вплоть до его выхода из установки непрерывной разливки) кристаллизуется все сечение слитка.
Метод непрерывной разливки стали был разработан в нашей стране. Он быстро получил мировое признание, так как обеспечивал наиболее полный выход годного металла, резкое повышение производительности и улучшение условий труда в металлургической промышленности при практически полном устранении тяжелых ручных операций. Заметно снизилась себестоимость стали. Однако метод непрерывной разливки металла вызвал ряд трудностей при производстве качественной стали для труб мощных газопроводов.
При непрерывной разливке отсутствует возможность дополнительной очистки стали от вредных примесей, как это имеет место при разливке металла в изложницах, когда неметаллические включения и газы в значительной степени всплывают и сосредоточиваются в прибыльной части, которая затем обрезается. При непрерывной разливке все вредные примеси, имеющиеся в стали, остаются в прокате. Поэтому для получения высококачественной стали, необходимой для производства труб, потребовалось обеспечивать как можно более полную очистку чугуна и стали в процессе их выплавки и разливки. Для этого применяют продувку жидкого металла аргоном, вакуумирование, обработку стали в ковше синтетическими шлаками, а также модификацию жидкой стали в ковше кальцием, алюминием и редкоземельными металлами.
При методе непрерывной разливки оставшиеся в стали примеси сосредоточиваются по центру слитка, в результате чего образуется расслоение в центральной по толщине зоне листа или ярко выраженная ликвационная полоса. Поэтому для получения качественной листовой или рулонной стали из сляба, полученного методом непрерывной разливки, необходимо
31
в процессе кристаллизации непрерывного слитка применять метод магнитного перемешивания его центральной, еще жидкой зоны.
Магнитное перемешивание обеспечивает равномерное распределение оставшихся примесей по сечению металла и позволяет устранить или значительно уменьшить ликвационные скопления в центральной по толщине зоне листа, а также слоистость металла. Скопления ликвационных включений в металле могут вызывать зарождение трещин в швах при сварке. Слоистость не наблюдается в листовой стали, прокатанной из обычного слитка, полученного в изложницах, и в термически обработанной стали непрерывной разливки.
2.1.3. Влияние слоистости стали на сопротивляемость разрушению металла труб
С изменением методов разливки и прокатки сталей для труб современных магистральных трубопроводов изменился и вид вязкого излома при разрушении. Увеличились шероховатость поверхности и размеры волокнистости в изломе. Характерной особенностью стало образование слоистости, ориентированной параллельно поверхности излома. Слоистость образуется как в среднем по толщине стенки трубы сечении, так и в приповерхностных зонах. В изломах труб наблюдаются: слоистые вырывы длиной 10—15 мм, глубиной до 5 мм с максимальным раскрытием до 1,5 мм. Слоистость в изломе выявляется также при ударных испытаниях полнотолщинных образцов DWTT и стандартных по Шарпи.
Испытания образцов различного типа из сталей контролируемой прокатки показали, что изломы полнотолщинных образцов наиболее близко соответствуют изломам в трубах по характеру слоистости и количеству расслоений на единицу поверхности излома. Склонность стали к образованию слоистости в изломе определяют по результатам испытаний образцов DWTT согласно формуле
32
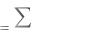
C |
li |
, |
|
||
|
S |
где С — индекс слоистости (1/мм); li — длина каждого расслоения более 1 мм; S— площадь излома образца, мм2.
Вопрос о взаимосвязи образующейся в изломе труб слоистости и сопротивляемости вязким разрушениям трактовался исследователями неоднозначно.
Чтобы установить, является ли образование слоистости дефектом стали или, наоборот, фактором, повышающим сопротивление разрушению, ряд фирм по производству труб провел специальные натурные испытания отрезков газопроводов. Исследовали стали контролируемой прокатки, склонные к образованию слоистого излома, и термообработанные (закалка с отпуском) высокопрочные вязкие стали, разрушающиеся без образования слоистости. Испытания отрезков газопроводов проводили по методике, изложенной в гл. 1.
По результатам испытаний (рис. 6) видно, что сопротивляемость вязким разрушениям, характеризуемая средней скоростью распространения трещины, в трубах из исследуемых сталей примерно одинакова при одинаковой вязкости металла. При среднем значении ударной вязкости KCV2/3 0,55— 0,6 МДж/м2 в трубах 1 испытываемого отрезка среднее значение скорости v составляет 260—275 м/с. При KCV2/3 = 0,85 МДж/м2 в трубе 3 из стали контролируемой прокатки и в трубе 2 из термообработанной стали v=180 м/с.
33
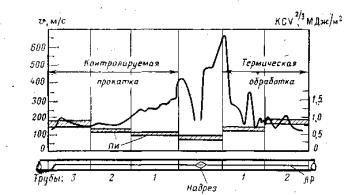
Рис. 6. Изменение скорости распространения разрушения при испытании отрезка газопровода 1420x17 мм длиной 200 м из стали Х-70 контролируемой прокатки и стали Х-80 термообработанной; давление разрушения рр = 8 МПа; ПИ — пределы изменения КСУ; ЛР — линия разрыва
Слоистость проявляется только в процессе динамического разрушения труб или образцов и не связана с нарушением цельности сечения при производстве листовой стали. В этом случае, как показали приведенные выше исследования, образование слоистости при разрушении не оказывает отрицательного влияния на сопротивление металла труб разрушению в магистральных газопроводах. Так как слоистость изломов металла труб все же связана с определенным несовершенством структуры, металлургические мероприятия, направленные на снижение склонности сталей контролируемой прокатки к слоистости, обеспечат дальнейшее повышение качества стали и стабильности свойств.
2.1.4. Контролируемая прокатка стали
Процесс контролируемой прокатки разработан для получения в листовой стали, микролегированной карбонитридами, наиболее высокого комплекса свойств путем придания ей особой структуры. С этой целью прокатка осуществляется по спе-
34
циально разработанной программе, основанной на оптимальной комбинации температуры металла и величины обжатия стали с условиями выделения карбонитридов, обеспечивающей получение заданной структуры.
Для эффективного осуществления контролируемой прокатки химический состав стали должен быть выбран в соответствии с количеством основных легирующих элементов— углерода, марганца, кремния и микролегирующих добавок—- ванадия, ниобия или других аналогичных по действию элементов. Сталь должна быть достаточно полно очищена от вредных примесей, в первую очередь от серы, обработана РЗМ с тем, чтобы исключить образование вытянутых строчечных и остроугольчатых включений.
Прокатка стали должна производиться на мощных станах, позволяющих обеспечить нужную степень обжатия в достаточно широком диапазоне температур металла.
В целом при контролируемой прокатке, программируя выделение карбонитридной фазы в процессе горячего деформирования, получают сталь с наиболее высокими показателями по прочности, вязкости и хладостойкости при минимальном легировании. Для дальнейшего повышения свойств стали сразу же после окончания цикла контролируемой прокатки (после чистовой клети) в интервале температур от 800—700 до 500—400 °С осуществляется ускоренное регулируемое охлаждение в специальных установках. Эта операция позволяет завершить структурные превращения в нужном направлении, дополнительно повысить прочностные свойства стали практически без снижения характеристик вязкости и хладостойкости.
Сочетание высокой степени очистки стали от вредных примесей, ее микролегирование карбидообразующими элементами с процессами непрерывной разливки и контролируемой прокатки позволили в 70-х годах получить особо качественную сталь для производства труб при минимальном расходе дорогих и дефицитных легирующих элементов. Все это сделало возможным быстрый прогресс в строительстве мощных газопроводов, эксплуатирующихся в сложных климатических
35
условиях.
2.2. Углеродистые стали
Для производства труб применяется сталь углеродистая обыкновенного качества, поставляемая по ГОСТ 380—71 группы «В», т. е. с гарантией механических свойств и химического состава, марок ВСт. 2, ВСт. 3 и редко ВСт. 4. Бесшовные трубы чаще изготавливают из качественных конструкционных углеродистых сталей марок 10—20, которые поставляются по ГОСТ 1050—74. В зависимости от степени раскисления все углеродистые стали могут поставляться кипящими, полуспокойными и спокойными.
Химический состав сталей и их механические свойства определяются государственными стандартами в зависимости от марки и степени раскисления. В табл. 1 и 2 приведены механические свойства и химический состав спокойных сталей в листах толщиной до 25 мм.
Содержание азота в углеродистых сталях не должно быть более 0,008%. Кроме оговоренных в табл. 1 свойств, ГОСТ 1050—74 для сталей марок 10 и 20 регламентирует твердость и некоторые элементы структуры. ГОСТ 380—71 предусматривает также производство углеродистой стали, упрочненной марганцем. В этом случае в маркировку стали вводится буква Г и сталь маркируется>ВСт. ЗГ. Применительно к условиям работы металла в напорных трубопроводах разница между углеродистыми сталями, поставляемыми по ГОСТ 380—71 и 1050— 74, незначительна.
36

Таблица 1 Свойства углеродистых спокойных сталей
Марка |
|
σВ, МПа |
|
σ0,2, |
|
5, |
|
Ψ, |
|
KCU+20, |
KCU-20, |
||||
|
|
|
|
|
МПа |
|
% |
|
% |
|
МДж/м2 |
МДж/м2 |
|||
ВСт. 2 |
|
340-420 |
|
220 |
|
32 |
|
|
|
- |
|
|
|||
Сталь |
|
Не менее |
|
210 |
|
31 |
|
55 |
|
- |
|
|
|
||
10 |
|
340 |
|
250 |
|
26 |
|
|
|
- |
|
|
|||
ВСт. 3 |
|
380-490 |
|
|
|
|
|
|
|
|
- |
|
|
|
|
|
|
|
|
|
|
|
|
|
|
|
|
При толщине 5-9 мм |
|||
|
|
|
|
|
|
|
|
|
|
|
|
0,8 |
|
|
|
|
|
|
|
|
250 |
|
21 |
|
55 |
|
0,4 |
|
|
|
|
Сталь |
|
Не менее |
|
270 |
|
24 |
|
|
|
При толщине 10-30 |
|||||
20 |
|
420 |
|
|
|
|
|
|
|
|
|
мм |
|
|
|
ВСт. |
420-540 |
|
|
|
|
|
|
|
|
0,7 |
|
|
|||
4 |
|
|
|
|
|
|
|
|
|
|
|
0,3 |
|
|
|
|
|
|
|
|
|
|
|
|
|
|
|
- |
|
|
|
|
|
|
|
|
|
|
|
|
|
|
|
- |
|
|
|
|
|
|
|
|
|
|
|
|
|
|
|
При толщине 5-9 мм |
|||
|
|
|
|
|
|
|
|
|
|
|
|
0,7 |
|
|
|
|
|
|
|
|
|
|
|
|
|
|
|
- |
|
|
|
|
|
|
|
|
|
|
|
|
|
|
|
При толщине 10-25 |
|||
|
|
|
|
|
|
|
|
|
|
|
|
|
мм |
|
|
|
|
|
|
|
|
|
|
|
|
|
|
0,6 |
|
|
|
|
|
|
|
|
|
|
|
|
|
|
|
- |
|
|
|
|
|
|
|
|
|
|
|
|
|
|
|
|
Таблица 2 |
||
Химический состав углеродистых спокойных сталей (%) |
|
||||||||||||||
Марки |
|
Углерод |
|
Марга- |
Кремний |
Фосфор |
Сера |
||||||||
|
|
|
|
|
|
нец |
|
|
|
|
|
|
|
|
|
ВСт. 2 |
|
0,09— |
|
0,25— |
|
0,12— |
|
Не более |
0,05 |
|
|||||
Сталь 10 |
|
0,15 |
|
|
0,50 |
|
|
0,30 |
|
|
0,040 |
0,04 |
|
||
ВСт. 3 |
|
0,07— |
|
0,25— |
|
0,17— |
|
0,035 |
0,05 |
|
|||||
Сталь 20 |
|
0,14 |
|
|
0,65 |
|
|
0,37 |
|
|
0,040 |
0,04 |
|
||
ВСт. 4 |
|
0,14— |
|
0,40— |
|
0,12— |
|
0,035 |
0,05 |
|
|||||
|
|
|
|
|
|
|
|
37 |
|
|
|
|
|
|
|
Спокойные углеродистые стали более качественны, имеют однородный химический состав, но более дорогостоящи. Качество поверхности спокойной листовой стали, может быть хуже, чем у кипящих марок. Структура кипящих сталей наименее Однородна из-за сегрегации углерода, серы и фосфора. При исследовании отдельных разрушений сварных конструкций, выполненных из кипящих сталей, в зоне разрушения обнаруживалось удвоенное содержание углерода и серы против сертификатных данных. Фактическое количество серы доходило до 0,1 %. По литературным данным, в зависимости от размера слитка массой 1—8 т в зоне сегрегации содержание элементов может превышать сертификатные данные по углероду в 1,6— 3,5 раза, по сере — в 3—10 раз. В спокойных сталях сегрегация незначительна. Неоднородность химического состава у кипящих и полуспокойных углеродистых сталей вызывает известную разницу свойств в различных частях листа. Так, против сертификатных данных разница свойств у кипящей стали может доходить по временному сопротивлению разрыву до 70 МПа, а у спокойных — до 25 МПа, по пределу текучести — соответственно до 50 и 30 МПа.
Значения ударной вязкости спокойной и полуспокойной листовой стали ВСт. 3 при толщинах до 10 мм и
.положительных температурах достаточно близкие, однако при температуре ниже 0 °С вязкость полуспокойных сталей снижается быстрее и при —20 °С может составлять менее 0,2 МДж/м2. У кипящей углеродистой стали с понижением температуры ударная вязкость падает еще быстрее, и удовлетворительные значения на уровне 0,3—0,4 МДж/м2 она имеет только при положительной температуре. Ударная вязкость и хладостойкость углеродистых сталей заметно снижаются с увеличением толщины листа.
Опыта применения труб из кипящих углеродистых сталей для газонефтепроводов практически нет. Имеется ограниченный опыт строительства городских газопроводов на давление менее 1,2 МПа диаметром 530 мм из труб, изготовленных из кипящей стали. ВНИИСТом был проведен ряд исследований
38
сварных труб 219x6 мм из кипящей стали марки 10 кп и труб 168x6 мм из полуспокойной стали 10 пс, а также из листовой углеродистой стали ВСт. ЗГ, ВСт. Зсп, ВСт. Зпс и ВСт. 3 кп толщиной 8—10 мм.
Исследования на большой партии труб (более 100 и около 1200 образцов) диаметром 219 и 168 мм при толщине стенки 6 мм позволили установить, что фактические значения расчетных характеристик стали труб (временного сопротивления и предела текучести) превышали требования государственного стандарта особенно по величине предела текучести (при норме не менее 250 МПа фактические значения составляли более 300 МПа). Прочностные и пластические свойства сталей 10 кп и 10 пс практически равноценны: σВ ≥420 МПа, σ0,2≥250 МПа. Вязкость стали труб оценивали на поперечных образцах 5х10x55 мм с надрезом Менаже. Результаты испытаний по данным более 600 образцов приведены в табл. 3
Вязкость кипящей стали толщиной 6 мм стабильна и достаточно удовлетворительна по величине только при 0 °С и выше. Хладостойкость стали удовлетворительна только при 10 °С и выше (В≥50%). Вязкость полуспокойной стали удовлетворительна при температуре до —10 °С, а хладостойкость— при температуре до —5 °С.
Таблица 3 Ударная вязкость и волокно в изломе (образцы Менаже) угле-
родистых сталей
Мар |
KCU+20, |
В, % |
KCU0, |
В, % |
KCU-20, |
В, % |
ка |
МДж/м2 |
|
МДж/м2 |
|
МДж/м2 |
|
10кп |
Более |
75—100 |
Более 0,5 |
25 |
0,2—0,4 |
10 |
10пс |
0,7 |
90—100 |
0,0—1,0 |
40—75 |
0,3—0,6 |
15—50 |
|
0,8-1,2 |
|
|
|
|
|
Исследования сопротивления зарождению трещин в основном металле и сварных соединениях труб диаметром 168 и 219 мм с толщиной стенки 6 мм из кипящей и полуспокойной сталей марки 10 были проведены на коротких патрубках шириной 100 мм. Патрубки испытывались на сплющивание при Т
39