
Учебное пособие 800175
.pdfследовательности операций. На схемах каждый элемент изделия обозначают прямоугольником, в котором указывается наименование составной части, её индекс и количество (рис. 2.1).
Деталь (сборочная единица), с которой начинают сборку изделия, присоединяя к ней другие детали и сборочные единицы, называют базовыми деталями (базовой сборочной единицей). Процесс сборки изображается на схеме горизонтальной линией в направлении от прямоугольника с изображением базовой составной части до прямоугольника, изображающее готовое изделие (или сборочную единицу). Выше горизонтальной линии показываются в порядке последовательности сборки прямоугольники, условия обозначающие деталь, а ниже – прямоугольники, условно изображающие сборочные единицы.
Технологическая схема сборки является основой для проектирования технологического процесса (ТП) сборки. При сборке сложного изделия иногда бывает целесообразно сначала разработать общую схему сборки изделия и после этого – схемы узловых сборок (т.е. сборочные соединения 1-го и 2-го и более высоких порядков). Каждая деталь машины или механизма при работе занимает в любой момент времени вполне определённые положения относительно других деталей. Это условие обеспечивается соответствующей кинематической схемой и конструкцией машины или механизма, что в конечном счёте выражается определённость базирования деталей.
Предусмотренное конструкцией положение любой детали в машине или механизме обеспечивается при сборке благодаря соответствующим её поверхностям, осям или точкам. Поверхность или выполняющее ту же функцию сочетание поверхностей, ось, точка, принадлежащая заготовке или изделию, и используемое для базирования называется базой.
9

Рис. 2.1.Технологическая схема сборки
10
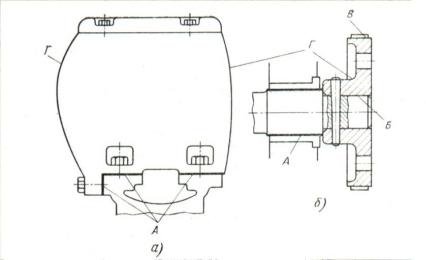
По назначению базы делятся на три вида: - конструкторские, технологические и измерительные.
На характер сборочных соединений влияет конструктор-
ские базы, которые бывают основными и вспомогательными.
Например, поверхность А корпуса коробки скоростей (рис. 2.2,а) и приводного вала (рис. 2.2, б) при соприкосновении с другими поверхностями (поверхность станины(см. рис. 2.1) и подшипник(см. рис.2.2)) обеспечивают определённость положения корпуса и вала. Такие поверхности называются основными базовыми поверхностями станины, на которые опираются корпус коробки скоростей основными базами и поверхности скольжения подшипника, называют вспомогательными поверхностями.
Рис. 2.2. Виды поверхностей деталей: А, Б - основные базы; Г – вспомогательные
11
Поверхность Б (рис. 2.2, б) шкива является базовой для этой детали, а сопрягающаяся с ней поверхность вала в данном случае выполняет роль вспомогательной базы. Следовательно, при сборке соединений основные базы одной детали опираются на вспомогательную базу другой. Основные и вспомогательные базовые поверхности образуют в совокупности сопряжения, а при достижении силового замыкания – соединения.
Деталь с базовыми поверхностями, выполняющая в сборочной единице роль соединительного звена, обеспечивающего при сборке соответствующее относительное положение других деталей, называют базовыми деталями.
Схемы базирования при узловой и общей сборке выбирают с учётом обеспечения заданной точности, удобств её выполнения сборщиками, упрощение приспособлений, оборудования и транспортных средств, надёжной собираемости деталей
ПОРЯДОК ВЫПОЛНЕНИЯ РАБОТЫ
1.Начертить эскиз сборочного изделия (чертеж выдает преподаватель) и составить спецификацию входящих деталей.
2.Провести анализ сборочного изделия на технологичность сборки с учетом основных требований, предъявляемых к конструкции изделия при её сборке.
3.Провести разбивку изделия на составные части и разработать технологическую схему сборки данной сборочной единицы.
4.Разработать схему базирования узловой и общей сборки изделия.
12
КОНТРОЛЬНЫЕ ВОПРОСЫ
1.Что является исходными данными процесса сборки?
2.Перечислить основные показали технологичности сборочного изделия и какая конструкция является технологичной?
3.Общие принципы разбивки изделия на составные части при разработке технологической схемы сборки?
4.Дать понятие технологической схемы сборки и привести элементарный пример изображения схемы?
БИБЛИОГРАФИЧЕСКИЙ СПИСОК
1. Новиков Н.П. Основы технологии сборки машин и механизмов / Н.П. Новиков. – М.: Машиностроение, 1980. – 592 с.
2. . Справочник технолога – машиностроителя: в 2 т. / под ред. А.Г. Косиловой и Р.А. Мещерякова. - М.: Машиностроение, 1985.
3.Сборка и монтаж изделий машиностроения: Справочник: в 2 т. / под ред. В.С. Корсакова, В.К. Замятина. -М.: Машиностроение, 1983. Т.1. 180 с.
4.Проектирование технологии сборки и испытаний из-
делий: учеб. пособие [Электронный ресурс]. - электрон. Текстовые, граф. данные (1,46 МБ) / В.А Сай, О.Н. Кириллов.- Воронеж: ФГБОУ ВО «Воронежский государственный технический университет», 2015.
13
Практическая работа № 3 РАЗРАБОТКА ТЕХПРОЦЕССА РАЗЪЕМНЫХ
СОЕДИНЕНИЙ
Цель работы: ознакомиться с методикой построения технологического процесса сборки резьбовых соединений и расчетом силовых параметров этих соединений.
СОДЕРЖАНИЕ РАБОТЫ
1.Ознакомление со способами выполнения резьбовых соединений.
2.Расчет геометрических параметров болтовых соедине-
ний.
ОБЩИЕ ПОЛОЖЕНИЯ
Соединения болтами и винтами
Разъёмные соединения допускают разборку без повреждения сопрягаемых и скрепляющих деталей. К ним относятся резьбовые, клиновые, штифтовые, шпоночные, шлицевые и профильные соединения, а также соединения посредствам упругих элементов (стопорных колец).
Резьбовые соединения очень распространены в машиностроении. Трудоёмкость резьбовых соединений относительно велика. Их сборку выполняют, применяя крепёжные детали (болты, винты, резьбовые шпильки). При болтовых соединениях не требуется нарезания резьбы в соединённых деталях, что важно, если материал детали не обеспечен необходимой прочности резьбы. Недостатки болтовых соединений: утяжеляет конструкцию, усложняет её внешние очертания, необходимость удержания болта от проворачивания при завинчивании гайки. Винтовые соединения просты по конструкции и удобны для сборки. При частой разборке винты не применяют,
14
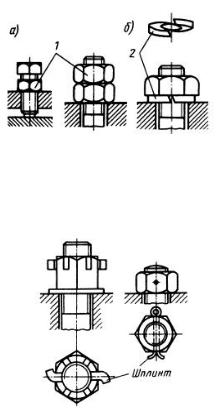
так как они могут повредить резьбу в детали. В этом случае их заменяют болтами или шпильками.
Важным элементом в процессе резьбового соединения является стопорение. Особенно в случае, когда резьбовые соединения воспринимают переменные и ударные нагрузки или подвержены действию вибрации.
Применяют три основных способа стопорения:
1. Повышают трение в резьбе путём постановки контргайки, переменных шайб, использование резьбовых пар с натягом в резьбе (рис.3.1).
Рис. 3.1
2. Жёстко соединяют гайку со стержнем болта (шпильки) с помощью шплинтов или соединяют группу винтов проволочной связкой (рис 3.2).
Рис. 3. 2
15
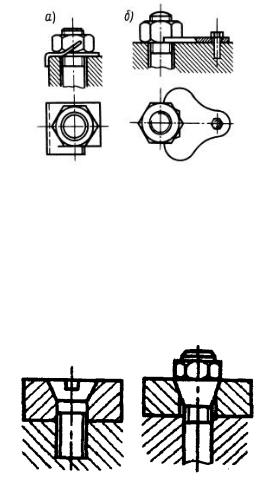
3. Гайку (головку винта) жёстко соединяют с деталью, применяя специальные шайбы, плёнки, накернивание или точечную сварку ( рис. 3.3).
Рис. 3. 3
Резьбовые соединения, расположенные внутри механизмов стопорят только вторым и третьим способом. Винты и гайки с коническими опорными поверхностями обладают хорошими стопорящими свойствами из-за больших моментов трения на этих поверхностях (рис. 3.4).
Рис. 3. 4
Расположение крепёжных деталей должно быть удобным для применения высокопроизводительных и механизирован-
16

ных сборочных инструментов, расстояние между осями крепёжных деталей не должно быть малым, так как это затруднит использование многошпиндельных винто- и гайкозавёртывающих устройств. Следует избегать расположение крепёжных деталей в труднодоступных и неудобных местах.
Последовательность выполнения сборочных резьбовых соединений состоит из нескольких последовательно выполняемых этапов:
1)сначала на сборочном стенде устанавливают и взаимно ориентируют сопрягаемые детали изделия;
2)затем, устанавливают крепёжные резьбовые детали, осуществляя их наживление, завинчивание и затяжку с заданным осевым моментом;
3)у ответственных соединений осуществляется: контроль затяжки и стопорение резьбовых деталей.
Сборка деталей винтами наиболее простая. В единичном
имелкосерийном производстве наживление винтов выполняется вручную, а завинчивание и затяжка – гаечными или торцовыми ключами и отвёртками. В крупносерийном производстве эти этапы сборки выполняются средствами механизации и автоматизации.
Более сложная сборка болтовых соединений. Она вклю-
чает:
– вставку болтов и придерживание их от проворачива-
ния;
- надевание шайб;
–нацеливание, навёртывание и затяжку гаек с использованием тех же средств производства, как и в предыдущем случае.
В болтовом ненапряженном соединении напряжение в болте возникает после приложения нагрузки (рис. 3.5, рис.3.6). Условие прочности болта определяется по формуле:
∙ [σ ]=P.
17
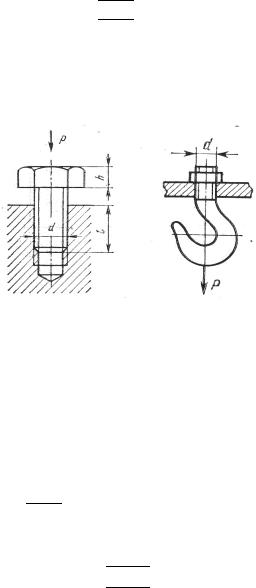
Откуда
=,
где Р - сила , действующая вдоль оси болта, Н; 1 – внутренний диаметр резьбы, мм; [σр] – допустимое напряжение при растяжении (сжатии), МПа.
Рис.3.5 Рис.3.6
Резьбовое соединение с поперечной нагрузкой выполняется в виде постановки точеного болта без зазора (плотно, с небольшим натягом, рис. 3.7). Болт в этом случае работает на срез и смятие.
На срез болт рассчитывается по формуле:
∙[ ср]≥Р,
откуда внутренний диаметр резьбы будет:
=,
ср
18