
Учебное пособие 1859
.pdf
Предложенная Чернышовым Е.М. методология системного тестирования и диагностики техногенных продуктов позволяют обозначить комплекс целенаправленных действий, в составе которых производится тестирование характеристик техногенного продукта и осуществляется его диагностика с точки зрения наиболее эффективного использования в строительном производстве. Такие действия были применены при комплексном исследовании конвертерных шлаков (рис. 2).
Тестирование
Достоверная информация о характеристиках и свойствах, определяющих потенциальную структурообразующую роль
|
Области применения |
|
Внедрение результатов исследований, |
|
|
конвертерных шлаков |
|
в том числе разработка предложений |
|
|
в стройиндустрии |
|
по техническому регламенту |
|
|
|
|
|
|
|
|
|
|
|
|
|
|
|
|
|
Диагностика |
|
|
|
|
|
|
|
|
Рис. 2. Методика системного тестирования и диагностики конвертерных шлаков
В результате тестирования выявлены следующие особенности конвертерных шлаков, определяющие их структурообразующую роль в строительных композитах:
сложное строение с конгломератным типом структуры, при этом выделяется силикатная и металлическая ферромагнитная составляющая, количественное соотношение которых зависит от типа сырья, использующегося в основном (ме-
11

таллургическом) производстве, технологии производства стали и переработки шлаков (использования различных систем отделения металлической части), времени хранения материала и др.
химический состав конвертерных шлаков варьируется в следующих преде-
лах: FeO – 8,0...21,1; SiO2 – 12,7...17,0; СаО – 40,0...54,2; МgО – 1,9...12,6; Аl2О3
– 1,7...8,3; МnО – 0,5...2,6; SO2 – 0,03...0,19; Р2O5 – 0,06...0,94. Модуль основно-
сти составляет 2,5...3,9, модуль активности – 0,06...0,54. При этом необходимо отметить высокое содержание СаО, приводящее к неустойчивости структуры шлаков текущего выхода; минералогический состав силикатной части определялся комплексом методов (рис. 3).
|
|
б |
а |
|
|
|
|
|
|
|
|
|
|
|
в
Рис. 3. Исследования конвертерных шлаков а– петрографические (увеличение ×600), б – метод сканирующей зондовой микроскопии увеличение ×3000), 1 – двухкальциевый силикат β- модификации (β-C2S); 2 – двухкальциевый силикат γ-модификации (γ-C2S); 3 – алюмоферритная фаза: браунмиллерит (C4AF), двухкальциевый феррит (C2F) и железистый геленит (C2FS); 4 – поры; в – рентгенограмма.
В результате установлено, что минеральный состав представлен следующими фазами: двухкальциевый силикат – белит двух модификаций: β-C2S (лар-
12

нит) и γ-C2S (35-45%); алюмоферритная фаза (20-28%): браунмиллерит (C4AF), двухкальциевый феррит (C2F) и железистый геленит (C2FS); магнетит (FeO·Fe2O3) и гематит (Fe2O3) с примесями RO-фазы (20-30%),α-модификации кварца (α-SiO2), окерманит (2CaO·MgO·2SiO2), кальциймагниевый феррит
(2CaO·MgO·Fe2O3).
Структура и свойства шлаков формируются на уровне расплава и определяются условиями кристаллизации, а также способами переработки в твердом состоянии. Активность шлакового порошка может быть обусловлена наличием щелочных и кислотных оксидов, содержанием ларнита, четырехкальциевого алюмоферрита, аморфного кварца, гематита и магнетита.
|
физико-механические свойства зависят от размеров частиц шлаков и спо- |
|
собов переработки и хранения: |
|
|
• |
истинная плотность, г/см3: |
3,47 – 3,56 |
• |
средняя плотность, кг/м3: |
3141 - 3404 |
• |
насыпная плотность (фр. 0…5 мм), кг/м3: |
1750 - 1843 |
• |
пористость, %: |
4,5 - 10,2 |
• |
пустотность (фр. 0…5 мм), %: |
48,1 - 52,4 |
• |
водопоглощение, %: |
1,3 - 2,6 |
• |
дробимость, %: |
13,4 - 18,2 |
• |
радиоактивность, Бк/кг: |
34,74 |
• |
содержание металлических включений, |
|
обладающих ферромагнитными свойствами, %: |
1-14. |
На основе этих исследований составили «дерево» материалов и изделий из конвертерных шлаков (рис. 4).
Конвертерные шлаки
Рис. 4. Основные направления использования конвертерных шлаков в стройиндустрии
13
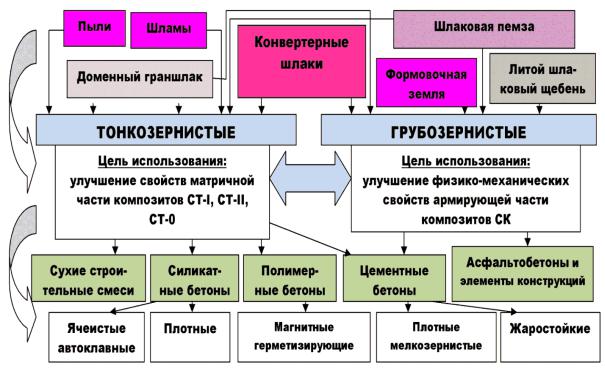
Экспериментально была определена огнеупорность отходов, которая составила: для доменных шлаков – 1400 °С; для конвертерных шлаков - 500°С; для боя шамотных огнеупоров – 1600-1700°С (в зависимости от минералогического состава и примесей); для гидрата глинозема - 1850°С; для пыли силикомарганца - 1110°С и для микрокремнезема - 900°С. Эти результаты позволили сделать вывод о целесообразности применения гидрата глинозема, доменных шлаков и шамота для жаростойких бетонов с температурой службы до 1800°С. Учитывая строительно-технологический потенциал отходов металлургии, а также технические решения по эффективному превращению их во вторичное минеральное сырье, можно предложить реализацию следующих направлений исследований (рис. 5).
Пыли |
|
Шламы |
|
|
|
|
Шлаковая пемза |
|
||
|
|
|
|
Конвертерные |
|
|
|
|
|
|
|
|
|
|
шлаки |
|
|
|
|
|
|
|
|
|
|
|
|
|
|
|
|
|
|
|
|
|
|
|
Формовоч- |
|
Литой шлако- |
||
|
|
|
|
|
|
ная земля |
|
вый щебень |
||
|
|
|
|
|
|
|
|
|
||
|
|
|
|
|
|
|
|
|
|
|
|
|
|
|
|
|
|
|
|
|
|
Рис. 5. Вовлечение всех неиспользуемых отходов в производство эффективных строительных материалов
Анализ работ по кристаллохимии, термодинамике, идеи Журавлева В.Ф. о проявлении вяжущих свойств соединениями щелочноземельных металлов с различными оксидами, исследования школ Боженова П.И., Бутта Ю.М., Волженского А.В. дали возможность доказать, что техногенные отходы металлургии могут применяться для синтеза цементирующих веществ и формирования систем твердения.
Под системами твердения (СТ) понимали результат получения камневидного состояния как следствие структурообразования в смесях, подвергаемых технологическому воздействию. При этом СТ характеризуются:
способностью к образованию безводных или частично обезвоженных соединений, которые могут взаимодействовать с водой;
способностью к коллоидному диспергированию и созданию пересыщенных систем с последующим образованием при этом твердеющих с течением времени пластических паст;
14

прочностью и стойкостью вновь созданных структур, последовательность и предпочтительность которых определяются наибольшей термодинамической вероятностью их возникновения.
При этом использовались следующие научные положения:
в структурообразовании систем твердения может использоваться: гидратационный принцип, гидротермальный синтез, контактно-конденсационный механизм. Твердение сопровождается протеканием комплекса процессов, в том числе химических, физико-химических и физических, а также гидратообразованием;
системы, в которых оксиды четных рядов второй группы периодической системы элементов с радиусом катионов г > 0,103 нм при взаимодействии с кислотными оксидами обладают вяжущими свойствами (Журавлев В.Ф.);
вяжущие свойства оксидов определяются зарядами ионов, степенью поляризации и активности, (Мощанский Н.А.), значениями их электроотрицательности (Федоров Н.Ф.);
неустойчивая координация ионов кальция (2-4) при взаимодействии вяжущего с водой переходит в более устойчивую (повышается до 6);
искажения в структуре силикатов - дыры, каналы, полости играют важную роль в проявлении вяжущих свойств;
проявление вяжущих свойств путем формирования межзерновых (межкристаллитных) контактов в вяжущих системах может быть связано с проявлением координационных и водородных связей (Сычев М.М. и Л.Б. Сватовская).
С целью формирования СТ на основе отходов систематизированы основные факторы, определяющие свойства таких материалов и составлена система факторов управления и регулирования строительно-технических свойств СТ.
Исследования систем твердения на основе неиспользуемых отходов металлургии
С целью экспериментального подтверждения проявления вяжущих свойств отходами в условиях реализации гидратационного механизма структурообразования, определены прочностные свойства систем «отход
– вода», сначала используя пластический способ формования образцов (рис. 6). Несмотря на то, что система «шлаковая пемза – вода» проявила достаточно высокую гидравлическую активность, а шламы и пыли изначально имеют тонкодисперное состояние, позволяющее использовать их без предварительного измельчения, дальнейшие исследования были ориентированы на создания СТ на основе конвертерных шлаков (проч-
15

ностная активность при этом способе формования не превысила 2,9 МПа. Это обусловлено тем, что конвертерные шлаки имеют высокий строительнотехнологический потенциал и являются самыми крупнотоннажными и не используются в стройиндустрии.
|
Для повышения прочности систем |
|||||
|
твердения на основе конвертерных |
|||||
|
шлаков использовали основной за- |
|||||
|
кон водоцементного |
|
отношения |
|||
|
(рис. 7), согласно которому высо- |
|||||
|
кая пористость цементного камня, |
|||||
|
получаемая при высоких значениях |
|||||
|
водовяжущего отношения, несмот- |
|||||
|
ря на высокую степень гидратации, |
|||||
|
является |
причиной |
пониженных |
|||
|
значений прочности. Учитывая не- |
|||||
|
значительное |
содержание аморф- |
||||
|
ной фазы в составе конвертерных |
|||||
|
шлаков, а, следовательно, и их |
|||||
Рис. 7. Зависимость активности СТ на основе |
сравнительно невысокую гидрата- |
|||||
ционную способность, |
увеличение |
|||||
конвертерных шлаков от количества воды за- |
||||||
творения при полусухом формовании, где 1 – |
активности |
шлакового |
вяжущего |
|||
формование на малом приборе СоюзДорНИИ |
добивались |
за счет |
|
повышения |
||
с уплотнением ударом, 2 – формование об- |
степени |
сближения |
дисперсных |
|||
разцов с пригрузом. |
||||||
частиц |
в процессе |
прессования |
||||
|
(было решено формировать СТ с низкими водошлаковыми отношениями от
0,12, до 0,16.
Максимальная прочность достигла 9 МПа, возможно, за счет того что средний эквивалентный диаметр межзерновых пор уменьшился настолько, что стала возможной капиллярная конденсация влаги. Это стимулировало гидратационные процессы, которые усилили адсорбционно-конденсационные явления в результате формирования новых твердых фаз. В соответствии с имеющимися техническими возможностями формования изделий со значениями влажности, являющихся оптимальными для СТ на основе конвертерных шлаков, приемлемыми являются методы прессования, вибропрессования, виброуплотнения, вибропроката, вибровакуумирования, центрифугирования с определенными частными оптимумами по критерию влажности.
Таким образом установлено, что для СТ на основе конвертерных шлаков характерен смешанный механизм твердения (гидратационный и контактноконденсационный), при котором конечная прочность материала зависит не только от интенсивности и полноты гидратации составляющих его минералов, но и во многом от степени сближения частиц при формовании. Цементация вяжущего контактного твердения осуществляется мгновенно, сопровождается появлением достаточно прочных водостойких связей между его частицами, возникающих в результате действия поверхностных сил притяжения.
16

Фазовый состав новообразований при гидратационных процессах в системе «конвертерные шлаки – вода» подтвержден результатами выполненного рентгенофазового анализа (рис. 8).
Рис. 8. Рентгенограмма систем твердения на основе конвертерного шлака в 28-суточном возрасте твердения при В/Ш=0,12
Процессы структурообразования СТ определяются гидратацией двухкальциевого силиката (ларнита). Это приводит к преобладанию высокоосновных гидросиликатов кальция в составе новообразований, тем более что со временем степень гидратации белитовой составляющей увеличивается. Наличие в составе конвертерных шлаков оксида кремния α-модификации (α- кристобалита) способствует их переходу в низкоосновные гидросиликаты типа CSH(B), тоберморит и ксонотлит. Образование низкоосновных гидросиликатов кальция в структуре гидратированных конвертерных шлаков объясняется также взаимодействием Ca(OH)2 как продукта гидратации β-C2S с кварцем. При этом общее количество гидрогранатов увеличивается, что приводит к росту прочности исследуемого материала в поздние сроки твердения.
Установлено, что для достижения удельной поверхности 300 м2/кг (по ПСХ), для шлака требуется на 180 минут больше, чем для цементного клинкера, но на 60 мин меньше, чем для кварца. Достижение показателей удельной поверхности 400 и 500 м2/кг увеличивает время помола соответственно на 4 и 6 часов. Поэтому удельная площадь поверхности равная 300 м2/кг признана оптимальной (рис. 9).
17

а
в
1
3
2
б
Рис. 9. Гранулометрический состав конвертерных шлаков: а - общий вид фракций, 1- фр. 0- 10, 2- Sуд=300 м2/кг, 3 - Sуд=400 м2/кг; б - изображение поверхности частицы шлака (увеличение х 3000); в - распределение по размерам частиц Sуд=400 м2/кг
Для выявления оптимальных условий синтеза СТ твердение осуществлялось в воздушной и в водной среде (рис. 10). Установлено, что максимальная прочность образцов, твердевших на воздухе, составила 10,2 МПа, в водной среде – 11,2 МПа.
Измельчение шлака до удельной поверхности 300…400 м2/кг дало наиболее значимый прирост прочности. Дальнейшее увеличение тонкости помола способствовало незначительному росту прочностной активности конвертерного шлака, и было
Рис. 10. Влияние тонкости помола конвер- признано нецелесообразным. терных шлаков на активность СТ: 1 - полусухое формование с уплотнением ударом, твердение в водной среде; 2 - формование образцов с пригрузом, твердение в водной среде; 3 - полусухое формование с уплотнением; 4 – формование образцов с пригрузом, твердение в воздушно-сухих условиях; ударом, тверде-
ние в воздушно-сухих условиях.
18

Важным моментом для выбора направлений использования конвертерных шлаков является значительный прирост прочности с течением времени. В результате прочность СТ двухлетнего возраста составила в среднем 12,4 МПа. Это подтверждает тот факт, что отвердевание систем определяет гидролиз и гидратация минералов, отличающихся медленным набором прочности.
Таким образом, на этапе исследования самостоятельной активности конвертерных шлаков получили СТ, прочностная активность которых в 28-дневный срок при удельной поверхности 300 м2/кг составляет 9 МПа, в двухлетний срок – 12,4 МПа. Резервом увеличения показателя активности является более тонкое измельчение (до 450 м2/кг), что приводит к увеличению прочности до 11,2 МПа (рис.12).
Известно, что с повышением температуры скорость многих химических реакций возрастает. Благодаря этому при повышенных температурах образование гидросиликатов, гидроалюминатов и гидроферритов кальция в коллоидном состоянии происходит значительно быстрее и интенсивнее, чем при обычных температурах. Поэтому системы твердения в первую очередь подвергались термоактивации.
Согласно результатам исследований за счет тепловлажностной обработки при температуре 60 - 80°С прочность системы была увеличена до 10,2 МПа. Автоклавирование также является эффективным (прочность до 13 МПА), но при этом способе необходимо регулировать влажность смеси (рис.13).
Максимальное значение прочности было достигнуто при введении на стадии совместного помола шлака с комплексной минерально-химической добавкой «БИО-НМ» (12 МПа). Это обусловлено, по-видимому, наличием в ее
19

составе аморфного кремнезема, который связываясь в процессе гидратации с Ca(OH)2, образовывал устойчивые новообразования в виде гидросиликатов кальция, способствовал уплотнению структуры вяжущей системы.
Среди щелочных активаторов наибольшее значение имели цементные вяжущие вещества и воздушная известь (рис. 14 и 15).
Полученные СТ имели прочность при сжатии до 24,9 МПа (при В/Т=0,12) и 24,0 МПа (при В/Т=0,30). С точки зрения максимального раскрытия потенциала конвертерных шлаков, рациональный расход активатора следует считать 20-40 %.
Положительное влияние сульфатной активации на гидравлические свойства шлаков было отмечено при расходе гипса в количестве 10%. Максимальное значение прочности в 12,9 МПа возможно связано с тем, что суль- фат-ион служит катализатором фазового перехода.
Учитывая влияние всех факторов на прочность систем твердения, было решено разработать оптимальные составы композиционных вяжущих на основе конвертерных шлаков. В качестве активатора твердения конвертерных шлаков использовался портландцемент марки ЦЕМ I 42,5Н производства Липецкого цементного завода. В качестве кислотного модифицирующего компонента использовался микрокремнезем, который является аспирационной пылью ферросплавного производства и представляет собой ультрадисперсный материал. Химический состав отходов представлен в основном диокси-
дом кремния аморфной модификации (от 85%), средний размер частиц составляет 0,1-0,2 микрон.
20