
Учебное пособие 1790
.pdf
41
Из рис.9.2 видно, что для сечений камеры от головки до узла крепления k = R2; для сечений камеры от узла крепления и до среза сопла k = R2 – p/pг; где p
– тяга камеры.
yсп=R |
P |
Pг R2 |
Pг R2-P |
Рис. 9.2. |
Погонное осевое (для произвольного сечения меридиальное) н окружное усилия вычисляются для нейтральной поверхности (рис.9.2). За нейтральную поверхность оболочки КС принимается поверхность спая вершин ребер (гофров) с рубашкой камеры. Погонная меридиальная (осевая) сила находится из условия:
N x |
X |
|
2 y |
cos |
|
|
сп |
|
где:
- угол наклона касательной к образующей оболочки к оси камеры; yсп - ордината точек вершин спая ребер.
Окружная погонная сила определяется из уравнения Лапласа:
N x |
N |
pг |
|
R1 |
R2 |
||
|
|||
где: |
|
|
R1 - первый главный радиус оболочки и координата yсп, берутся с чертежа; R2 = yсп / cos - второй главный радиус.
При оценке местной прочности оболочек КС, помимо напряжений, возникающих от внутреннего давления рг, учитывает также напряжения от действия на оболочки реакций связей рс, а для внутренней оболочки - и термические напряжения.
Сила реакций связи приводит к возникновению изгибающих моментов, действующих на оболочки камеры (рис.9.1). В результате их действия в оболочках камеры имеют место изгибные окружные напряжения 1 n и 2 n. Определим их.
Усилие рс, которое действует со стороны связей на оболочки, представляется в виде распределенной силы и находится из уравнения равновесия элемента наружной оболочки:
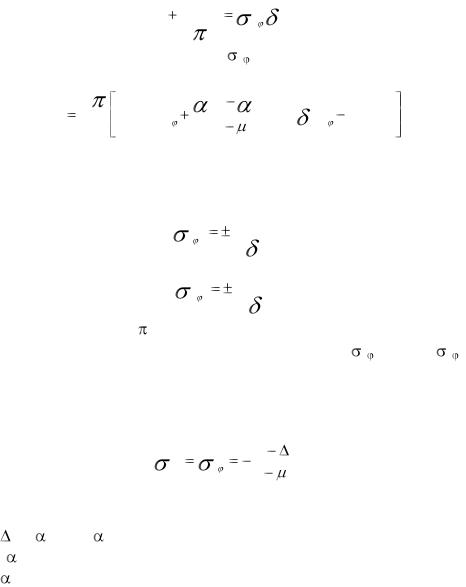
|
|
|
|
|
|
42 |
|
|
|
|
|
|
pж |
npc |
|
1 |
|
|
|||
|
|
|
|
|
2 2 R |
|
||||
|
|
2 R |
|
|||||||
Подставив сюда выражение для |
2 из (9.4) и решив полученное уравнение |
|||||||||
относительно рс найдем: |
|
|
|
|
|
|
|
|
||
pc |
2 |
pг R l2 |
|
1t1 |
2 t2 |
E2 2 l1 pж R |
(9.5) |
|||
|
|
|||||||||
n |
1 |
|
||||||||
|
|
|
|
|
|
|
||||
|
|
|
|
|
|
|
|
|
|
Наибольшие изгибные моменты и напряжения соответствует сечению приложения усилия рс. Изгибающий момент в этих сечениях равен Ми=pcl/12, а максимальные напряжения изгиба:
max |
|
pc l |
, |
||
1 и |
2 |
12 |
|
||
|
(9.6) |
||||
|
|
pc l |
|||
max |
|
|
|||
2 и |
2 |
22 |
|
В формулах (9.6) l=2 R/n - шаг между осевыми линиями связей. Если рс>0, то в точке приложения силы рс имеет место сжатие ( 1 n<0 или 2 n<0), а с противоположной поверхности оболочки - растяжение.
Дополнительные температурные напряжения, возникающие во внутренней оболочке в результате перепада температуры, могут быть определены из равенства:
|
|
E |
(9.7) |
|
1xt |
1 t |
|
||
1 |
||||
|
||||
|
|
|
где:
Е1 - модуль упругости в рассматриваемое слое;
= ( 1t1)сл - 1t1 – перепад температурной деформации;
( 1t1)сл – температурная деформация данного слоя внутренней оболочки; 1t1 - средняя температурная деформация внутренней оболочки.
Очевидно, что на "горячей" и охлаждаемой поверхностях внутренней оболочки температурные напряжения максимальны, причем на первой имеет место сжатие, а на второй - растяжение.
Суммарные напряжения в оболочках камеры в окружной и осевом направлениях находятся как сумма отдельных составлявши напряжений в тех не направлениях.
9.2. Определение напряжений в оболочках камеры сгорания на режиме гидроопрессовки.
Гидроопрессовка является основным видом испытаний КС на прочность или несущую способность. При этом внутренние объем КС и межрубашечное пространство заполняется водой. Предварительно все штуцеры и критическое сечение закрываются заглушками. Затем насосом в КС создается необходимое дав-
ление воды рж=роп.
При проведении гидроопрессовки производится измерение статических деформаций оболочек КС с помощью тензометрирования, а также определяется разрушающее давление. Измеренные статические деформации пересчитывают затем на напряжения. Определение разрушающего давления необходимо для

43
выяснения запаса прочности камеры, Для этого при гидроопрессовке постепенно повышают давление воды и фиксируют то значение давления, при котором происходит разрушение оболочек.
Гидроопрессовка камеры происходит в холодном состоянии или при температуре окружающей среды. Поэтому, чтобы приблизить условия испытаний к рабочим условиям (по напряжениям в материале), давление опрессовки принимается выше рабочего давления в камере рг с учетом падения механических свойств материала при повышении температуры. В первом приближении давление опрессовки равно:
pоп pг т.оп т. раб
где:
- пределы текучести материала оболочки при температуре опрессовки (обычно 20°С) и рабочей температуре соответственно.
Напряжения в оболочках камеры и связях определяются в соответствии с ранее изложенной методикой, Формулы для расчета и x на режиме гидроопрессовки упрощаются, так как отсутствует нагрев оболочек и температурные деформации, и имеют вид:
|
1 |
pоп R l1 |
, |
|
|
|
|
||||||
|
|
|
|
|
|
|
|
1 |
|
|
|
|
|
|
|
|
pоп R |
l2 |
|
|
|
|
|
||||
|
2 |
|
|
|
|
|
|
||||||
|
|
|
|
|
|
|
|
1 |
|
|
|
|
|
|
N x.оп |
l1x |
pоп |
R |
l1 |
lcx , |
(9.4’) |
||||||
1x |
|
|
|
||||||||||
|
|
|
1 |
|
|
|
|
|
|
1 |
|
|
|
|
N x.оп |
l2 x |
pоп |
R |
l2 |
lcx , |
|
||||||
2 x |
|
|
|
||||||||||
|
|
|
2 |
|
|
|
|
|
|
2 |
|
|
|
|
|
|
cx |
|
|
|
|
|
|
|
|
|
|
Осевое погонное усилие опрессовки равно: |
|
|
|
||||||||||
|
|
|
R2 pоп pоп R |
|
|
|
|||||||
N x.оп |
|
2 R |
|
|
|
|
2 |
|
|
|
|||
|
|
|
|
|
|
|
|
|
|
|
9.3. Расчѐт напряжений в оболочках камеры при работе материала в упруго-пластической области.
Приведенные выше формулы (9.4) и (9.4’) для расчета напряжений записаны для упругой области деформаций, то есть полагается, что напряжения в материале оболочек менее предела упругости у, коэффициент Пуассона = 0,З и в качестве модуля материала используется модуль упругости Е. Эти формулы можно применить и для расчѐта в упруго-пластической области, если использовать метод переменных параметров упругости и учесть зависимость механических свойств материала от температуры.
Для большинства металлов, работающих в упругой области, имеет место линейная зависимость между и .

44
E
где:
E=tg - модуль упругости материала (рис.9.3).
По аналогии для того же материала, работающего в пластической области, можно записать:
E
где:
E’ = tg - модуль пластичности или секущий модуль.
Принципиальная разница этих зависимостей состоит в том, что модуль упругости Е есть константа не зависящая от величины деформации, а модуль пластичности Е' зависит от величины деформации н заранее не известен. Поэтому расчет в этих случаях ведется путем последовательных приближений.
Предполагая в первом приближении работу в упругой области, по формулам (9.4) или (9.4’) находят составляющие напряжений в оболочках 1 (1), 2 (1), 1x(1), 2x(1) (индекс в скобках означает номер приближения). Затем по методу упругих
параметров определяет обобщенные эквивалентные напряжения i: для внутренней оболочки:
|
|
|
|
2 |
|
|
|
|
2 |
(9.8) |
|
|
|
1i(1) |
1 |
(1) |
1 |
(1) |
1x(1) |
1x(1) |
|
|
|
|
|
|||||||
и наружной: |
|
|
|
|
|
|
|
|
|
|
|
|
|
|
2 |
|
|
|
|
2 |
|
|
|
|
2i(1) |
2 |
(1) |
2 |
(1) |
2 x(1) |
2 x(1) |
|
и соответствующие им обобщенные интенсивности деформаций: |
|
|||||||||
|
|
|
1i(1) |
1i(1) , |
|
2i(1) |
2i(1) |
|
|
|
|
|
|
E1 |
|
E2 |
|
|
|||
|
|
|
|
|
|
|
|
|
||
|
|
i(1) |
|
|
|
|
|
|
|
|
|
|
|
|
`i(1) |
|
|
|
|
|
|
|
|
|
|
|
|
i(1) |
|
|
|
|
|
|
|
|
|
|
Рис. 9.3 |
|
|
||
Если |
1i(1)< |
1у и |
2i(1)< |
2у, |
то материал работает в упругой области и расчет |
|||||
закончен. В практике в качестве условия упругости принимается: |
|

45
|
1T |
, |
|
2T |
(9.9) |
1i(1) |
|
2i(1) |
E2 |
||
E1 |
|
||||
|
|
|
|
где:
у и т – пределы упругости и текучести материала. Если одно из условий (9.9) не выполняется, то необходимо провести второе приближение расчета с новым значением модуля материала и коэффициента Пуассона. В пластической области = 0,5, а в качестве модуля материала принимается значение секущего модуля Е’ (рис.9.3):
E 1(2) |
1i(1) |
, E 2(2) |
2i(1) |
|
|
||
|
1i(1) |
2i(1) |
который определяется с помощью диаграммы деформирования материала при рабочей температуре.
Расчет продолжают до тех пор, пока не будет обеспечена заданная точность.
9.4. Запас прочности оболочек камеры по несущей способности.
В связи с кратковременностью работы КС допускается еѐ работа в условиях пластичности. Поэтому работоспособность камеры удобно оценивать не по величинам напряжений, а по величинам деформаций. Опасные деформации возникают в оболочках, если давление в камере достигнет некоторого предельного или разрушающего давления. Естественно, что для работоспособной камеры должно выполняться общее условие прочности:
pг R |
|
(9.10) |
|
в |
|
|
|
где:
в - предел прочности материала.
Предельное (разрушающее) давление наиболее достоверно определяется экспериментально при гидроопрессовке. Однако, значение рпред может быть определено и расчетным путем по графику р=f( R).
Величина R - полная деформация оболочки в окружном направлении, учитывающая помимо упругих и температурные деформации, рассчитывается по формуле:
R 1 R |
2 R |
R |
R 1t1 |
|
1 1x |
||||
|
|
|
E1 |
(9.11) |
R |
|
|
|
|
2 x R |
2 t2 |
|
||
E2 |
|
|||
2 |
|
Расчет рпред осуществляется следующим образом. Задастся несколькими значениями давления в камере pг. Для них рассчитывают и x в обеих оболочках и соответствующие полные деформации R. Затем строится график зависимости р=f( R) (рис.9.4).
На этом графике отмечаем точку С, в которой прямая проведенная из начала координат касательно к кривой р=f( R). Эта точка определяет начало больших деформаций оболочек, опасных как с точки зрения геометрических размеров, так и прочности. Давление, соответствующее точке С, называют предельным.

|
46 |
||
За запас прочности по несущей способности оболочек принимают отношение |
|||
предельного или разрушающего давления pпред к рабочему давлению рраб: |
|||
n |
pпред |
(9.12) |
|
pраб |
|||
|
|
||
Обычно величину n принимают в пределах n = 1,5 - 2,0. |
|||
P |
|
|
|
Pпред |
|
C |
|
Pраб |
|
|
|
|
|
R |
|
|
Рис. 9.4 |
||
|
|
2в |
|
|
1в |
|
|
2т |
|
|
|
|
1в |
2в |
Рис. 9.5
Разрушающее давление для цилиндрической оболочки приближенно может быть оценено и более простым способом. Известна формула для pраз двухслойной цилиндрической оболочки бесконечной длины:
p |
|
0 |
1 |
1в |
|
1в |
|
1в |
|
|
|
|
|
|
|
1в 1 в |
2T 1 |
|
1 2в |
(9.13) |
|||
раз |
R0 |
1 |
|
|
2в |
|
|||||
|
|
1в |
|
2в |
|
2в |
|
которая справедлива для случая разрушения по внутренней оболочке, то есть если - 1в< 2в. В этой формуле R=R0(1+ ) и = 0(1+ ); R0 и 0 - начальные (недефор-

47
мированные) размеры. Деформации 1в и 2в соответствуют пределам прочности 1в и 2в материалов внутренней и наружной оболочек соответственно (рис.9.5).
Для цилиндрической оболочки конечной длины разрушающее давление выше, и формула имеет вид:
|
|
2 |
|
|
|
pразр |
pразр 1 4 |
R0 |
1в 1 |
1в |
(9.14) |
|
|
L |
|
|
|
где:
L - длина оболочки.
Формула (9.14) справедлива для разрушения по внутренней оболочке ( 1в< 2в). Если разрушение происходит по наружной оболочке ( 1в> 2в), то в формулах (9.13) и (9.14) индексы при параметрах «1» и «2» следует взаимно поменять местами.
9.5. Расчѐт оболочек камеры на динамическую прочность.
Расчѐт на динамическую прочность выполняется для неустойчивых режимов работы двигателя, сопровождающихся вибрациями, повышенными деформациями (прогибами) деталей и изменением параметров процессов (в первую очередь давление рабочего тела) по какому-либо периодическому закону. В этом случае наиболее опасными являются резонансные режимы, на которых имеет место равенство частот собственных колебаний детали (оболочки) и вынуждающей силы (давление).
Поэтому расчѐт оболочек камеры на динамическую прочность включает определение частоты собственных колебаний оболочек. Для цилиндрических оболочек характерно два вида колебаний: осесимметричные и изгибные. При первом виде колебаний камера в поперечном сечении сохраняет круглую форму, при втором виде колебаний камера в поперечном сечении приобретает в общем случае многолепестковую форму. Колебания оболочек по обоим видам различают по числу полуволн (по форме колебаний), укладывающихся по длине камеры для осесимметричных колебаний или по длине окружности для изгибных колебаний.
Собственная частота осесимметричных колебаний двухслойной цилиндрической оболочки с часто расположенными связями с учѐтом массы жидкости в зазоре и жѐстко закреплѐнной по концам рассчитывается по формуле:
|
|
|
f |
2 |
|
|
|
|
|
Eh |
пр |
|
|
|
1 |
k 4 |
|
|
|
|||
|
|
|
|
|
|
|
|
|
|
|
|
|
|
|
|
|
(9.15) |
|||||
|
ос |
mпр |
R |
2 |
1 |
|
|
2 |
|
|
|
|
||||||||||
|
|
|
|
|
|
|
|
|
|
|
|
|
|
|
|
|
|
|||||
где: |
|
|
|
|
|
|
|
|
|
|
|
|
|
|
|
|
|
|
|
|
|
|
|
|
|
|
|
|
|
|
2 |
|
|
|
|
|
|
|
|
|
|
|
|
|
|
k |
1 |
|
|
пр |
; |
|
|
|
|
|
|
Rn |
; |
mпр |
|
|
|
|||||
|
|
|
|
|
|
|
|
|
|
|
|
|
|
|
|
|
|
пр |
||||
12 |
|
R |
|
|
|
|
|
|
|
L |
|
|
g |
|||||||||
|
|
|
|
|
|
|
|
|
|
|
|
|
|
|
||||||||
|
|
|
|
|
|
|
|
|
|
|
|
|
|
|
|
|
||||||
|
hпр |
h1 h2 ; |
|
Eh пр |
|
E1 h1 E2 h2 ; |
|
|||||||||||||||
|
mпр |
1 |
|
|
1 h1 |
|
|
2 h2 |
|
c hc |
ж hж |
|
||||||||||
|
|
|
|
|
|
|
|
|
||||||||||||||
|
|
g |
|
|
|
|
|
|||||||||||||||
|
|
|
|
|
|
|
|
|
|
|
|
|
|
|
|
|
|
|
|
|

48
Вформуле (9.15) использованы обозначения: R – средний радиус оболочки;
L – длина оболочки;
h1, h2, hс, hж – толщины внутренней и наружной оболочек, связей и высота канала жидкости;
E1 и E2 – модули упругости материалов оболочек;
1, 2, с, ж - удельный вес материалов оболочек, связей и жидкости; - коэффициент Пуассона;
n – номер формы колебаний.
Собственная частота изгибных колебаний двухслойной оболочки с частыми связями определяется по формуле:
f |
2 |
|
E1 h1 |
E2 h2 |
|
|
|
|
|
|
|
|
|
|
|
|
|
|
|||||
|
|
|
|
|
|
|
|
|
|
|
|
|
|
|
|
|
|
|
|
|
|||
|
|
|
|
|
|
|
|
|
|
|
|
|
|
|
|
|
|
|
|
|
|||
изг |
mR |
2 |
|
|
|
|
|
|
|
|
|
|
|
|
|
|
|
|
|||||
|
|
|
|
|
|
|
|
|
|
|
|
|
|
|
|
|
|
|
|
|
|
||
|
|
|
4 k1 |
2 |
q2 4 |
1 |
|
2 |
|
q2 2 |
q2 1 |
2 |
2 2 q2 2 |
(9.16) |
|||||||||
|
|
|
|
|
|
|
|
|
|
|
q |
2 |
|
|
2 |
q |
2 |
2 |
|
|
|
|
|
|
|
|
|
|
|
|
|
|
|
|
|
|
|
|
|
|
|
|
|
|
|||
где: |
|
|
|
|
|
|
|
|
|
|
|
|
|
|
|
|
|
|
|
|
|
|
|
|
|
|
|
|
|
|
|
|
h1 |
|
E1 J1 |
E2 J 2 |
|
; |
|
|
|
||||||
|
|
|
|
|
|
|
|
|
|
E1 h1 |
E2 h2 R |
2 |
|
|
|
||||||||
|
|
|
|
|
|
|
|
|
|
|
|
|
|
|
|
||||||||
|
|
|
|
|
|
|
|
P1y |
P2 y |
|
|
|
|
|
P |
P |
|
|
|||||
|
|
|
|
|
|
|
|
|
; |
|
|
|
|
1x |
2 x |
|
|
||||||
|
|
|
|
|
|
1 E1 h1 |
E2 h2 |
|
2 |
|
E1 h1 E2 h2 |
|
|
Здесь использованы обозначения: q – номер формы колебаний;
J1 и J2 – моменты инерции – внутренней и наружной оболочек при единичной длине относительно оси, проходящей через центр тяжести расчѐтного сечения параллельно оси камеры;
P1у, P2у, P1x, P2x – окружные и осевые силы внутренней и наружной оболочек в рассматриваемом сечении;
остальные обозначения см. в пояснениях к формуле (9.15).
В случае малоповторяющихся пульсаций давления производится оценка малоцикловой усталости материала внутренней оболочки. При этом определяется наименьшее количество циклов нагружения N до образования трещин в материале внутренней оболочки:
|
0,125 ln |
|
1 |
|
|
|
|
|
|
||
|
|
|
|
|
|
|
|
||||
N |
|
|
1 |
|
|
|
|
|
|
|
|
|
|
|
|
|
|
|
|
|
|
|
|
|
|
|
|
|
(9.17) |
||||||
|
|
|
|
|
|
||||||
|
T max 273 |
1 |
0,125 |
T max 273 |
|||||||
|
|
|
|
|
|
|
|
||||
|
|
ln |
1 |
|
|
|
|||||
|
|
|
|
|
|
|
|
|
|
|
|
|
|
|
|
|
1 |
|
|
|
|
В формуле (9.17) использованы обозначения:
Tmax – максимальная температура внутренней оболочки;
-коэффициент линейного расширения материала оболочки при рабочей температуре;
-поперечное сужение материала.
49
10. Приложения
Приложение 1.
Соотношения между размерностями в различных системах измерения:
1.Давление (жидкости, газа), механические напряжения:
1атм = 1 кГ/см2 = 735,6 мм Hg = 9,807*104 Н/м2.
1Па (паскаль) = 1 Н/м2; 1 Мпа (мегапаскаль) = 106 Па.
2.Температура:
ТК = 273,2 + t 0C.
3.Работа, энергия мощность:
1 кГм = 9,807 Дж
1 кВт час = 3,6 106 Дж
1 л.с час = 2,648 106 Дж
1 кВт час = 860 ккал
1 ккал = 426,09 кГм = 1,163 10-3 кВт час = 0,2043 Вт с
4.Коэффициент вязкости:
1 кг сек / м2 = 98,1 г-масса / (см сек) (дина см / сек2 – пуаз)
1 пуаз = 100 сантипуаз = 0,0102 кг сек / м2 1 сантипуаз = 1,02 10-4 кг сек / м2 = 1,10-3 кг / (сек м) = 3,6 кг / (час м)
5.Коэффициент кинематической вязкости:
1м2 / сек = 3600 м2 / час = 10 000 см2 / сек
1см2 / сек = 0,36 м2 / час = 10-1 м2 / сек = 100 сст(сантистокс) =
=140УВ (градусов условной вязкости).

50
Приложение 2.
Некоторые справочные данные для расчѐта ПГС.
1. Зависимости газовой постоянной (R), характеристической скорости ( ), температуры продуктов сгорания (Т) и показателя изоэнтропы (n) от массового соотношения компонентов топлива (k).
1.1 Топливо – азотный тетраксид + диметилгидразин несимметричный (АТ+НДМГ).
p, МПа |
k |
R, Дж/кг К |
, м/с |
Т, К |
n |
|
|
1,536 |
438,0 |
1681 |
2775 |
1,232 |
|
|
2,151 |
376,8 |
1754 |
3340 |
1,178 |
|
10 |
2,612 |
350,4 |
1731 |
3469 |
1,168 |
|
2,919 |
338,74 |
1705 |
3471 |
1,167 |
||
|
||||||
|
3,073 |
333,8 |
1690 |
3459 |
1,166 |
|
|
12,290 |
282,0 |
1126 |
1943 |
1,240 |
|
|
1,536 |
437,6 |
1682 |
2785 |
1,236 |
|
|
2,151 |
374,7 |
1750 |
3399 |
1,184 |
|
25 |
2,612 |
347,5 |
1744 |
3564 |
1,169 |
|
2,919 |
335,57 |
1719 |
3572 |
1,168 |
||
|
||||||
|
3,073 |
333,8 |
1690 |
3459 |
1,166 |
|
|
12,290 |
282,0 |
1126 |
1943 |
1,240 |
|
|
1,536 |
437,4 |
1682 |
2790 |
1,239 |
|
|
2,151 |
373,5 |
1753 |
3436 |
1,189 |
|
50 |
2,612 |
345,3 |
1752 |
3633 |
1,171 |
|
2,919 |
333,3 |
1729 |
3647 |
1,168 |
||
|
||||||
|
3,073 |
328,5 |
1714 |
3643 |
1,168 |
|
|
12,29 |
281,9 |
1126 |
1944 |
1,291 |