
Строительные машины и механизмы. метод. указания к выполнению лабораторных работ. Жулай В.А
.pdf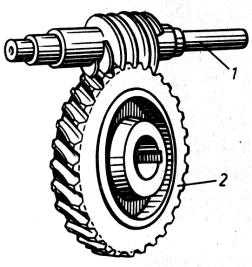
Основные параметры зубчатых передач
В качестве основного параметра зубчатых колес принят модуль. Модуль – расчетная величина, равная отношению окружного шага зубьев по делительной окружности к числу π.
Передаточное отношение зубчатой передачи, состоящей из двух зубчатых колес, определяется выражением:
i |
|
n1 |
1 |
|
z2 |
, |
(1.13) |
|
|
||||||
1,2 |
|
n2 |
2 |
|
z1 |
|
|
|
|
|
|
|
где n1, ω1, z1 и n2, ω2, z2 – частота вращения, угловая скорость и число зубьев ведущего и ведомого зубчатых колес.
Знак минус принимается для внешнего зацепления (рис. 1.5, а, б и в), знак плюс – для внутреннего зацепления (рис. 1.5, д).
1.3.6. Червячные передачи
Червячная передача – передача зацеплением со скрещивающимися осями валов (рис. 1.6). Передача движения происходит от червяка 1 (однозаходного или многозаходного винта) к зубчатому колесу специальной формы 2 и осуществляется по принципу винтовой пары.
Рис. 1.6. Червячная передача
Достоинства червячных передач: компактность и небольшая масса при большом передаточном числе, плавность и бесшумность в работе, возможность самоторможения.
Основной недостаток – низкий КПД.
Самоторможение – возможность передачи движения только от червяка к колесу; можно использовать механизм без тормозных устройств, препятствующих обратному движению колеса.
11
Впередаче возникает значительное взаимное скольжение витков червяка по зубьям колеса, что вызывает повышенный износ и значительное выделение теплоты.
Для уменьшения трения венцы червячных колес изготовляют из антифрикционных материалов (бронзы, реже чугуна). Наибольшее распространение получили червячные передачи с цилиндрическим червяком.
Встроительных машинах червячные передачи применяются как, самотормозящиеся в механизмах ручных грузоподъемных устройств, а также
вприводах различных систем управления.
Основной кинематический параметр червячной передачи
Передаточное число червячной передачи:
u |
n1 |
|
1 |
|
z2 |
, |
(1.14) |
||
n |
z |
||||||||
|
|
|
2 |
|
|
|
|||
2 |
|
|
1 |
|
|
где n1, ω1 и n2, ω2 – частота вращения и угловая скорость червяка и червячного колеса; z1 – число заходов червяка (z1 = 1; 2; 4); z2 – число зубьев червячного колеса.
Число заходов червяка равно числу зубьев червячного колеса, входящих или выходящих из зацепления за один оборот червяка.
1.4.ПОРЯДОКВЫПОЛНЕНИЯРАБОТЫ
1.Изучить теоретическую часть, обращая особое внимание на устройство, принцип работы и назначение каждой передачи.
2.Определить тип каждой передачи и установить расчетные формулы для определения их передаточного отношения (числа).
3.В соответствии с расчетными формулами пронумеровать каждую передачу. Определить для передач зацеплением число зубьев ведущего и ведомого элементов, а для передач трением – диаметры ведущего и
ведомого шкивов. Для всех передач повернуть ведущий элемент на n1 = 5 оборотов и определить (с точность до 1/4 оборота) число оборотов n2, на которое провернулся ведомый элемент.
4.Вычислить передаточное отношение (число) каждой передачи двумя способами – по числу оборотов и числу зубьев (или диаметру шкивов). Сравнить полученные результаты.
5.Пользуясь обозначениями ГОСТ 2.770–68 «Обозначения условные графические в схемах. Элементы кинематики» (прил. П.1) вычертить кинематические схемы каждой передачи.
6.Оформить отчет о работе.
12
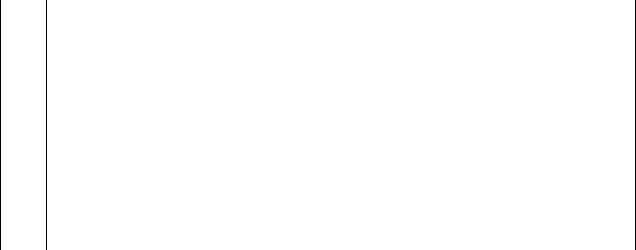
1.5ОФОРМЛЕНИЯ ОТЧЕТА ПО ЛАБОРАТОРНОЙ РАБОТЕ
1.Название работы.
2.Цель работы.
3.Краткое описание механических передач с необходимыми расчетными формулами и пояснениями к ним.
4.Обработать и привести данные, полученные в результате измерений
ирасчета кинематических параметров механических передач, и поместить в сводную табл. 1.1.
5.Выводы.
Таблица 1.1 Результаты определения кинематических параметров
механических передач
№ |
Результаты |
Расчетная формула |
Кинематическая схема |
|
п.п |
измерений |
и результаты |
передачи |
|
измерений |
||||
|
|
|
||
1 |
|
Наименование передачи |
|
n1 = ?; n2 = ? |
u |
n1 |
? ? |
|
|||
n2 |
|||||||
|
|
? |
|
||||
z1 = ? ;, z2 = ? |
|
z2 |
|
? |
|
||
u z ? ? |
|
||||||
|
|
||||||
|
1 |
|
|
|
|||
2 |
|
|
|
|
|
|
|
|
|
|
|||||
|
Контрольные вопросы |
1.Видымеханическихпередачипричиныихприменениявстроительныхмашинах.
2.Классификация механических передач.
3.Основные кинематические и энергетические соотношения
впередаточных механизмах.
4.Основные преимущества и недостатки каждой механической передачи.
5.Основные параметры каждой механической передачи и формулы
для их расчета.
6. Область применения каждой механической передачи в строительных машинах.
Рекомендуемая литература: [1, 2, 3]
13
ЛАБОРАТОРНАЯ РАБОТА № 2 ИЗУЧЕНИЕ КОНСТРУКЦИИ, ПРИНЦИПА РАБОТЫ
И ОПРЕДЕЛЕНИЕ ОСНОВНЫХ ПАРАМЕТРОВ ЩЕКОВОЙ ДРОБИЛКИ
2.1. ЦЕЛЬ РАБОТЫ
Изучение назначения, принципа работы и устройства основных машин и оборудования для переработки каменных материалов, а также расчета и экспериментального определения основных параметров щековой дробилки.
2.2. ПРИБОРЫ, ОБОРУДОВАНИЕИИНСТРУМЕНТЫ
Макет щековой дробилки со сложным движением подвижной щеки. Штангенциркуль, линейка, секундомер.
2.3.ТЕОРЕТИЧЕСКИЕСВЕДЕНИЯ
2.3.1.Общие сведения
Ккаменным (нерудным строительным) материалам относятся щебень, гравий, песок. Щебень получается в результате дробления различных горных пород. В соответствии с ГОСТ 8267–93 он разделяется на фракции с частицами размеров 5...10, 10...20, 20...40, 40...70 мм. Гравий – сыпучий материал с окатанными зернами размером 3 (5) ... 70 (150) мм. Окатанные камни крупностью более 150 мм называются валунами. Песок – сыпучий природный материал или материал, полученный при дроблении горных пород с зернами крупностью 0,14...5 мм.
Каменные материалы измельчают механическими способами: разда-
вливанием, раскалыванием, изгибом, истиранием, ударом; гидравлическими и термическими способами – гидравлическим ударом при электрическом разряде в воде, высокочастотной вибрацией, ультразвуковым и другими физическими способами, которые пока не получили широкого промышленного применения из-за высокой энергоемкости.
Дробильно-размольное оборудование
Для измельчения нерудных материалов применяют разнообразное дробильно-размольное оборудование (рис. 2.1).
14
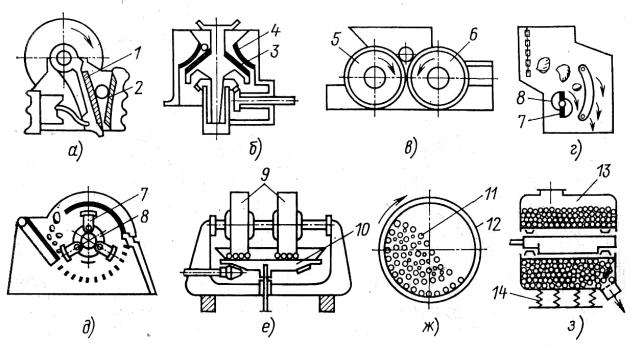
Рис. 2.1. Схемы дробильно-размольного оборудования:
а, б, в, г, д соответственно щековая, конусная, валковая, молотковая и роторная дробилки; с – бегуны; ж – шаровая мельница; з – вибромельница
В щековых дробилках (рис. 2.1, а) камень размельчается раздавливанием, а в некоторых частично и истиранием в пространстве между подвижной 1 и неподвижной 2 щеками. В конусных дробилках (рис. 2.1, 6) камень раздавливается, истирается, а в некоторых случаях раскалывается и изгибается между неподвижным и подвижным дробящими конусами. Подвижный конус 3, обкатываясь без принудительного вращения по внутренней дробящей поверхности неподвижного конуса 4, измельчает камень. В валковых дробилках (рис. 2.1, в) камень раздавливается и частично истирается в пространстве между вращающимися один навстречу другому валками 5 и 6. В роторных и молотковых ударных дробилках (рис. 2.1, г, д) камень измельчается силой ударов, наносимых молотками 7 роторов 8.
Бегуны (рис. 2.1, е) раздавливают материал, попадающий в пространство между катками 9 бегунов и рабочей поверхностью чаши 10. В шаровых (рис. 2.1, ж) и стержневых мельницах материал дробится истиранием, раздавливанием и частично ударами мелющих тел 11 (металлических шаров или стержней), загружаемых вместе с измельчаемым материалом внутрь вращающегося барабана 12. Вибромельницы тонкого помола (рис. 2.1, з) измельчают материал, попадающий в промежутки между соударяющимися шарами. Шары ударяются один о другой в результате вибрации барабана 13, установленного на пружинах 14.
Измельчениекаменныхматериаловобычнопроизводитсявнесколькостадий.
15
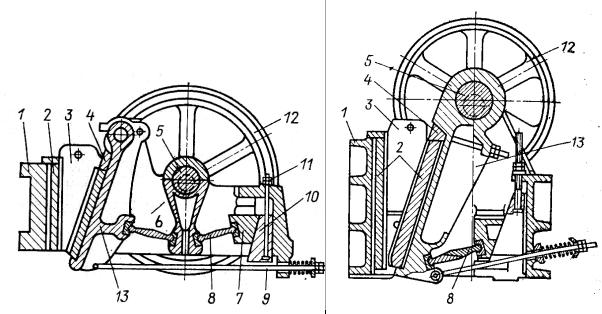
2.3.2. Щековые дробилки Щековые дробилки служат для измельчения горных пород средней и
большой твердости и из-за различных размеров приемного отверстия (от 160 х 250 до 2100 х 2500 мм), применяются как на первой, так и на последующих стадиях дробления. Производительность их при дроблении пород средней твердости достигает 300 м3/ч.
Различают щековые дробилки с простым (рис. 2.2, а) и сложным (рис. 2.2, б) движением щеки.
б)
а)
Рис. 2.2. Щековые дробилки:
а – с простым движением щеки; б – со сложным движением щеки
На сварной или литой станине 1 в роликовых подшипниках установлен
эксцентриковый вал 5, на который свободно надеты шатун 6 или подвижная щека 13. На станине и подвижной щеке укреплены ребристые дробящие плиты 2, изготавливаемые из марганцовистой стали или отбеленного чугуна. Внутренние боковые поверхности станины защищены от изнашивания футеровкой 3, неподвижно присоединенные к станине, как и неподвижная дробящая плита. Дробящая плита подвижной щеки закреплена на щеке накладками 4 при помощи болтов. На концах эксцентрикового вала устано-
влены маховики 12, предназначенные для накопления энергии во время холостого хода и для передачи ее при дроблении. Один из маховиков часто используется в качестве приводного шкива для клиноременной передачи от
16
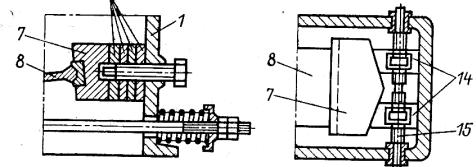
электродвигателя. Для поддержания подвижной щеки в рабочем положении и передачи усилий на дробление служат распорные плиты 8, являющиеся также предохранительным устройством. При перегрузке дробилки они в первую очередь выходят из строя, оставляя неповрежденными более ответственные детали. Распорные плиты часто выполняют с ослабленным сечением, а иногда из частей, соединяемых на заклепках.
Крупность дробления регулируют изменением зазора между дробящи-
ми плитами (рис. 2.3).
а) |
б) |
Рис. 2.3. Механизмы регулирования размеров разгрузочной щели:
а–регулировочное устройство с прокладками;
б– клиновое регулировочное устройство
Для этого заменяют прокладки 16 между задней стенкой станины 1 и опорной подушкой 7, производят смену распорных плит или используют регулировочные устройства. Клинья 14 (рис. 2.3, б) при вращении регулировочного винта 15, имеющего правую и левую резьбы, передвигаются один навстречу другому и смещают опорную подушку 7, а вместе с ней распорную плиту 8 и подвижную щеку в сторону уменьшения зазора. Для увеличения ширины разгрузочного отверстия регулировочный винт вращают в противоположную сторону.
Для ускорения отхода подвижной щеки и для удержания распорных плит от выпадения служит тяга 9 с пружиной.
Угол между дробящими плитами, исключающий возможность выталкивания камня через загрузочное отверстие, называется углом захвата. Он не должен превышать двойного значения угла трения между дробимым материалом и дробящими плитами. Обычно угол захвата составляет 15…25°.
Отношение средней крупности загружаемых камней к средней крупности камней, полученныхврезультатедробления, называетсястепеньюизмельчения.
Степень измельчения щековых камнедробилок не превышает 5…6. Максимальная крупность загружаемых в дробилку камней составляет
80…90 % ширины загрузочного отверстия.
17
Техническая производительность, м3/ч, щековых дробилок: |
|
ПТ 60 nV , |
(2.1) |
где μ – коэффициент, учитывающий наличие пустот между дробимыми камнями (μ = 0,3…0,7); n – частота вращения эксцентрикового вала, мин–1; V – объем призмы материала, выпадающего из дробилки за один отход подвижной щеки, м3.
Объем призмы материала, м3, равен:
V |
10 6 |
2e s hL |
, |
(2.2) |
|
2 |
|||
|
|
|
|
где е – минимальный зазор между дробящими плитами; см, s – ход подвижной щеки в нижней части, см; L – длина разгрузочного отверстия, см; h – высота призмы материала, выпадающего из дробилки за один отход подвижной щеки, см.
Высота призмы материала, выпадающего за один отход подвижной щеки:
h |
s |
, |
(2.3) |
|
tg |
||||
|
|
|
где α – угол захвата (угол между дробящими плитами), град.
Мощность привода щековой дробилки, кВт, определяется по формуле:
N |
BL |
, |
(2.4) |
|
60 |
||||
|
|
|
где B и L – ширина и длина зева дробилки, см.
2.4.ПОРЯДОКВЫПОЛНЕНИЯРАБОТЫ
1.Изучить теоретическую часть, обращая особое внимание на устройство, принципработыиназначениещековыхдробилокиихосновныхузлов.
2.В соответствии со схемой (рис. 2.4) определить размеры, см, камеры дробления макета щековой дробилки со сложным движением подвижной щеки.
18
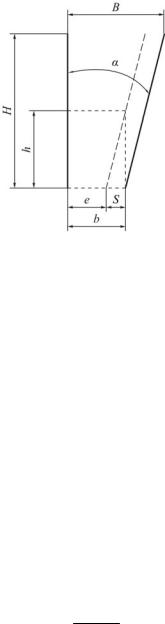
Рис. 2.4. Схема камеры дробления щековой дробилки:
В – ширина загрузочного отверстия (зева) дробилки; H – высота камеры дробления; b – ширина разгрузочного отверстия дробилки (определяется при максимальном удалении подвижной щеки от неподвижной в течение одного оборота эксцентрикового вала); е – размер разгрузочного отверстия при минимальном удалении подвижной щеки от неподвижной; α – угол захвата
Размеры разгрузочного отверстия b и е определяются при прокручивании эксцентрикового вала вручную за маховик и фиксации моментов максимального сближения и удаления щек.
3. Определить величину хода подвижной щеки в нижней части по формуле, см:
4. Вычислить значение тангенса угла захвата по формуле:
tg Bh e .
5. Определить высоту, объем призмы материала, выпадающего из дробилки за один отход подвижной щеки и техническую производительность щековой дробилки по формулам (2.1) … (2.3).
6. Рассчитать техническую производительность при ширине разгрузочного отверстия е = 1,0; 1,5; 2,0; 2,5; 3,0 см. Построить график
зависимости ПТ f e .
7.Определить частоту вращения эксцентрикового вала по характеристике приводного электродвигателя с учетом передаточного числа клиноременной передачи, используя зависимости, приведенные в лабораторной работе № 1.
8.Вычислить требуемую мощность привода щековой дробилки по формуле (2.4).
19
2.5.ОФОРМЛЕНИЯ ОТЧЕТА ПО ЛАБОРАТОРНОЙ РАБОТЕ
1.Название работы.
2.Цель работы.
3.Краткое описание конструкции макета щековой дробилки с необходимыми схемами, расчетными формулами и пояснениями к ним.
4.Обработать и привести данные, полученные в результате
измерений и расчета основных параметров дробилки, а также график зависимости ПТ f e .
5.Выводы.
Контрольные вопросы
1.Виды нерудных строительных материалов.
2.Способы измельчения каменных материалов.
3.Принцип работы щековых, конусных и валковых дробилок.
4.Принцип работы дробилок ударного действия.
5.Принципы работы мельниц.
6.Область применения и классификация щековых дробилок.
7.Назначение и конструкция основных элементов щековых дробилок.
8.Регулирование крупности готового продукта щековых дробилок.
9.Чем ограничивается величина угла захвата?
10.Основные параметры камеры дробления щековой дробилки.
11.Приведите зависимости, необходимые для определения технической производительности щековой дробилки.
Рекомендуемая литература: [2, 3, 5]
ЛАБОРАТОРНАЯ РАБОТА № 3
ИЗУЧЕНИЕ КОНСТРУКЦИИ, ПРИНЦИПА РАБОТЫ И ОПРЕДЕЛЕНИЕ ОСНОВНЫХ ПАРАМЕТРОВ ВИБРАЦИОНННОГО ГРОХОТА
3.1. ЦЕЛЬ РАБОТЫ
Изучение назначения, принципа работы и устройства основных машин и оборудования для сортировки каменных материалов, а также расчета и экспериментальногоопределенияосновныхпараметроввибрационногогрохота.
20