
Учебное пособие 1536
.pdf3.2. ПРИБОРЫ, ОБОРУДОВАНИЕИИНСТРУМЕНТЫ
Макет вибрационного инерционного грохота. Штангенциркуль, линейка, секундомер, угломер.
3.3.ТЕОРЕТИЧЕСКИЕСВЕДЕНИЯ
3.3.1.Общие сведения
Изготовление дорожных и строительных материалов с гарантированными свойствами предъявляет строгие требования к фракционному составу используемых в качестве компонентов измельченных каменных материалов. Технологические операции, позволяющие добиваться заданного фракционного состава щебня, гравия, песка и других минеральных наполнителей, называются обогащением и классификацией.
Обогащение– этоудалениеизматериаланепригодныхпримесейивключений. Классификация – это сортировка материала на фракции (классы),
различающиеся крупностью входящих в них частиц.
В промышленности строительных материалов для обогащения и классификации используют просеивание и промывку. Просеивание позволяет сортировать каменные материалы по фракциям (классам), т.е. по размерам частиц. При промывке материал очищается от глинистых и пылеватых частиц, ухудшающих качество конечного продукта.
Грохочение – процесс разделения сыпучих материалов на классы крупности путем просеивания через одно или несколько сит или классификация материала на просеивающих поверхностях.
Зерна (куски) материала, размер которых больше размера отверстий сита, остаются при просеивании на сите, а зерна меньших размеров проваливаются через отверстия.
Материал, поступающий на грохочение, называется исходным, остающийся на сите – надрешетным продуктом (верхним классом), проваливающийся через отверстиясита– подрешетнымпродуктом(нижнимклассом).
Припоследовательномпросеиванииматериаланаn ситахполучаютn + 1 классов.
Показателем, оценивающим полноту разделения исходного материала на классы, служит эффективность грохочения.
Эффективность грохочения – выраженное в процентах или долях единицы отношение массы подрешетного продукта, прошедшего сквозь отверстия просеивающей поверхности, к массе нижнего класса в исходном материале. Эффективность грохочения современных виброгрохотов составляет 85…95 %.
Для механического разделения щебня, гравия, песка и других сыпучих материалов на классы по крупности применяют сортировочные машины – грохоты, рабочим органом которых является просеивающая поверхность.
21

Грохоты классифицируют по следующим признакам:
–потипупросеивающейповерхности– наколосниковые, сситамиирешетами;
–по характеру движения просеивающей поверхности – на неподвижные, качающиеся, вращающиеся и вибрационные;
–по форме просеивающей поверхности – на плоские и цилиндрические;
–по положению просеивающей поверхности в пространстве – на горизонтальные и наклонные.
Наибольшее распространение получили наклонные и горизонтальные вибрационные грохоты (виброгрохоты) с плоской просеивающей поверхностью в виде колосников, сит или решет (рис. 3.1).
Рис. 3.1. Просеивающие поверхности грохотов: а – колосники; б – решето; в – сито
Колосники представляют собой просеивающуюповерхностьизпараллельно установленныхпрофилированныхметаллическихбрусьев(рис. 3.1, а).
Сита представляют собой сетку с ячейками определенной формы и размера, изготовленную из плетеной проволоки, сваренных прутков или растянутых резиновых шнуров (рис. 3.1, в);
Решета – штампованный стальной или литой резиновый лист с отверстиями или колосники (рис. 3.1, б).
Просеивающей поверхности виброгрохотов сообщаются колебательные движения от вибратора. Частота и амплитуда колебаний у грохотов устанавливаются в зависимости от гранулометрического состава сортируемой смеси. Частицы материала интенсивно встряхиваясь колеблющейся поверхностью грохочения, перемещаются вдоль неё и, проходя сквозь ее отверстия, разделяются на классы. Размер отверстий просеивающей поверхности выбирают в зависимости от максимального граничного размера зерен отделяемого нижнего класса.
3.3.2. Вибрационные грохоты
Вибрационные грохоты (рис. 3.2) по способу возбуждения колебаний
разделяются на эксцентриковые (гирационные) и инерционные (дебалансные).
По траектории движения рабочего органа различают инерционные грохоты с круговыми (рис. 3.2, б) и направленными (рис. 3.2, в) колебаниями.
22

Эксцентриковые грохоты (рис. 3.2, а) сортируют материал за счет колебаний подвижной рамы 6 с ситами 7, закрепленной на эксцентрически смещенных шейках вала 4. На валу установлен шкив 5, получающий вращение от электродвигателя через клиноременную передачу. Вращение эксцентрикового вала вызывает колебание подвижной рамы с постоянной амплитудой. Эксцентриковый вал вращается в подшипниках 2 неподвижной (основной) рамы 1. Вибрационное воздействие на неподвижную раму уменьшается благодаря противовесам
3. При вращении эксцентрикового вала 4
Рис. 3.2. Схемы вибрационных грохотов:
а– эксцентриковый(гирационный); б– инерционныйскруговымиколебаниями;
в– инерционныйснаправленными колебаниями
подвижная рама 6 совершает круговые движения, направленные навстречу потоку материала, что способствует лучшему сортированию. Амплитуда колебаний равна эксцентриситету r шеек вала, т. е. 3 ... 5 мм при частоте колебаний 15 … 24 Гц. Амплитуда колебаний сит в эксцентриковых грохотах, в отличие от инерционных, не зависит от загрузки грохота и частоты вращения его вала.
Инерционные грохоты обеспечивают сортировку материала в результате вибрации, возникающей под действием сил инерции вращающихся неуравновешенных масс (дебалансов). Грохот с круговыми колебаниями (рис. 3.2, б) состоит из неподвижной 1 и подвижной (короб грохота) 3 рам, соединенных между собой пружинными амортизаторами 2.
23
На подвижной раме укреплены сита 8 и подшипники 7 дебалансного вала 6, который вместе с дебалансами 5 приводится во вращение клиноременной передачей 4 от электродвигателя, обеспечивая возбуждение круговых колебаний подвижной рамы. Под действием вынуждающей силы вибратора частицы сортируемого материала подбрасываются на сите и за счет наклона поверхности грохочения (α = 10 ... 25°) перемещаются вдоль неё. Частота колебаний сита составляет порядка 14 Гц, а амплитуда колебаний 4 ... 4,5 мм.
Более эффективное разделение исходного материала достигается на грохотах с вибраторами направленного действия (рис. 3.2, в). Подвижная 3 и неподвижная 1 рамы этого грохота соединены между собой амортизаторами в виде пластинчатых рессор 2, параллельно которым расположена линия центров дебалансных валов вибратора с направленными колебаниями 5. Вибратор с направленными колебаниями состоит из двух параллельно установленных дебалансных валов, вращающихся навстречу друг другу с одинаковой скоростью. В этом случае составляющие инерционные силы, действующие по линии соединяющей центры валов, взаимно уравновешиваются, а в перпендикулярном направлении складываются, обеспечивая действие постоянной по направлению, но переменной по амплитуде возмущающей силы. Привод одного из валов вибратора осуществляется с помощью клиноременной передачи от электродвигателя, а вращение другому валу передается цилиндрическими шестернями синхронизатора.
Виброгрохоты с направленными колебаниями имеют чаще всего по два сита, расположенных под углом 0…5° и колеблющихся с частотой около 12 Гц и амплитудой 8...12 мм.
Техническая производительность, м3/ч, вибрационных грохотов с круговыми колебаниями по исходному материалу определяется по эмпирической формуле:
ПТ Fqk1k2k3с, |
(3.1) |
где F – площадь поверхности грохочения, м2; q — удельная производительность 1 м2 поверхности грохочения, м3/ч; k1 – коэффициент, учитывающий процент содержания в исходном материале зерен нижнего класса; k2 – коэффициент, учитывающий процент содержания в нижнем классе зерен, размеры которых меньше 0,5 размера отверстия сита; k3 – коэффициент, учитывающий угол наклона грохота α ; с – коэффициент, учитывающий неравномерность загрузки грохотаи его конструкцию(длянаклонного виброгрохотас = 0,6).
3.4.ПОРЯДОКВЫПОЛНЕНИЯРАБОТЫ
1.Используя теоретическую часть (п. 3.3), плакаты, альбомы и действующую модель виброгрохота, изучить устройство, конструкцию и
24
принцип работы инерционного виброгрохота.
2. Определить размеры поверхности грохочения, размеры отверстий сит «в свету» и их угол наклона к горизонту α.
3. Определить частоту колебаний короба грохота по характеристике приводного электродвигателя с учетом передаточного числа клиноременной передачи, используя зависимости, приведенные в лабораторной работе № 1. Частотаколебанийкоробаравначастотевращениядебалансноговалавибратора.
4. Определить фактическую производительность грохота по объему разделенного материала за 5 мин работы машины.
5. Рассчитать теоретическое значение технической производительности грохота при размере отверстий сит l = 10; 16; 20; 25; 35 мм по ф-ле (3.1) и
данным таблиц П.2 и П.3. Построить график зависимости ПТ f l ,
приняв соответственно значения k1 = 0,66; 0,84; 0,92; 1,00; 1,08; k2 = 0,72; 0,91; 1,00; 1,09; 1,18.
3.5. ОФОРМЛЕНИЯ ОТЧЕТА ПО ЛАБОРАТОРНОЙ РАБОТЕ
1. Название работы.
2. Цель работы.
3. Краткое описание конструкции макета вибрационного грохота с необходимымисхемами, расчетнымиформуламиипояснениямикним.
4. Обработать и привести данные, полученные в результате измерений и расчета основных параметров вибрационного
грохота, а также график зависимости ПТ f l . 5. Выводы.
Контрольные вопросы
1.С помощью каких технологических операций обеспечивается заданный фракционный состав каменных материалов?
2.Что такое грохочение? Виды продуктов и оценка качества грохочения.
3.Что такое грохот? Классификация грохотов.
4.Виды просеивающих поверхностей.
5.Принцип работы и основные узлы эксцентриковых грохотов.
6.Принцип работы и основные узлы инерционных грохотов
с круговыми колебаниями.
7.Принцип работы и основные узлы инерционных грохотов с направленными колебаниями.
8.Приведите формулу для определения технической производительности инерционных грохотов с круговыми колебаниями.
Рекомендуемая литература: [2, 3, 5]
25
ЛАБОРАТОРНАЯ РАБОТА № 4
ИЗУЧЕНИЕ КОНСТРУКЦИИ И ОПРЕДЕЛЕНИЕ ОСНОВНЫХ ПАРАМЕТРОВ БЕТОНОСМЕСИТЕЛЯ ПРИНУДИТЕЛЬНОГО ДЕЙСТВИЯ
4.1. ЦЕЛЬ РАБОТЫ
Изучение области применения, принципа работы и устройства основных машин для приготовления бетонных смесей и экспериментального определения основных параметров бетоносмесителя принудительного действия.
4.2. ПРИБОРЫ, ОБОРУДОВАНИЕИИНСТРУМЕНТЫ
Макет бетоносмесителя принудительного действия. Штангенциркуль, линейка, секундомер.
4.3.ТЕОРЕТИЧЕСКИЕСВЕДЕНИЯ
4.3.1.Общие сведения
Бетон представляет собой искусственный строительный каменный материал, получаемый в результате затвердевания смеси, состоящей из вяжущего вещества (цемента), воды, крупного (щебня) и мелкого (песка) заполнителей. Приготовление бетонной смеси заключается в получении однородной смеси с равномерным распределением отдельных зерен и обволакиванием их вяжущим веществом путем механического перемешивания всех компонентов.
Процесс приготовления смеси состоит из ряда последовательно выполняемых операций: загрузки в смесительную машину отдозированных компонентов – вяжущих и заполнителей – перемешивания компонентов с добавлением необходимого количества воды и выгрузки из машины готовой бетонной смеси.
Смесительные машины классифицируются: по назначению – на бетоносмесители для приготовления бетонных смесей и растворосмесители для приготовления растворных смесей (строительных растворов); по способу перемешивания материалов – гравитационные (работающие по принципу свободного падения материалов при вращении барабана) и с принудительным перемешиванием (вращающимися лопастями); по характеру работы – периодического (цикличного) и непрерывного действия; по исполнению – стационарные и передвижные.
Главным параметром смесителей циклического действия принимают объем готового замеса, л. Необходимо иметь в виду, что объем готового
26

замеса меньше чем сумма объемов загруженных компонентов из-за уплотнения смеси при перемешивании, когда свободное пространство между кусками крупного заполнителя заполняется частицами мелкого заполнителя, вяжущего и водой. При этом плотность (удельная масса) смеси увеличивается по сравнению с плотностью исходных компонентов. Степень уменьшения объема смеси характеризируется коэффициентом выхода готовой смеси kвых, равным отношению объема готовой смеси к суммарному объему загруженных компонентов.
4.3.2. Циклические бетоносмесители принудительного действия
Циклические бетоносмесители принудительного действия могут быть с вертикально расположенными смешивающими валами и корпусом в виде чаши цилиндрической формы (рис. 4.1 а, б); с горизонтально расположенными (одним или двумя) смешивающими валами и с корытообразным корпусом (лотком) (рис. 4.1 в).
Рис. 4.1. Схемы циклических бетоносмесителей принудительного действия
Наибольшее применение получила первая группа бетоносмесителей, разновидностью которой являются роторные смесители (рис. 4.2).
Рис. 4.2. Принципиальная схема роторного циклического бетоносмесителя принудительного действия
27
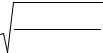
Вроторных смесителях (рис. 4.2) перемешивание материалов происходит вращающимся ротором 5 с лопастями в кольцевом смесительном пространстве чаши 2, в центре которой размещен стакан 6. Рычаги смесительных лопастей 3, 4 прикреплены к ротору с помощью амортизаторов на разном удалении от оси его вращения, а их рабочие поверхности расположены под различными углами к траектории движения лопастей. Такое расположение лопастей создает при их движении продольные и поперечные потоки смешиваемой массы, обеспечивая интенсивное и качественное перемешивание смеси любой консистенции. При движении лопасти прорабатывают весь объем смеси, а при выгрузке полностью очищают внутреннюю поверхность чаши. Пружинные амортизаторы предохраняют рычаги от поломки при попадании щебня между лопастями или скребками и днищем, или стенками (обечайками) чаши.
Загрузка отдозированнных компонентов производится сверху через специальное отверстие в крышке смесителя под действием силы тяжести. Приготовленная смесь выгружается через отверстие в днище чаши, закрываемое во время перемешивания секторным затвором.
Впланетарно-роторных смесителях (рис. 4.1, б) перемешивание компонентов смеси осуществляется также в неподвижной чаше ротором с лопастями, которые дополнительно вращаются вокруг подвижной собственной оси в сторону противоположную направлению вращения ротора.
Роторы со смесительными лопастями роторных и планетарно-роторных бетоносмесителей приводятся во вращение мотор-редуктором 1 (рис. 4.2), установленным вертикально.
Для обеспечения качественного перемешивания условная средняя скорость лопастей не должна превышать критическую скорость, при которой центробежные силы, действующие на частицы смеси, могут превышать силы трения, вследствие чего будет происходить сегрегация компонентов смеси.
Критическая угловая скорость определяется по формуле, рад/с:
g f 1 f , (4.1)
R
где f – коэффициент трения смеси о лопасть, f = 0,4 … 0,5; g – ускорение свободного падения, м/с; R – радиус наиболее удаленной от оси вращения
лопасти, м. |
|
|
|
|
|
|
|
|
|
|
|
|
|
Мощность необходимая для привода ротора бетоносмесителя, кВт: |
|
||||||||||||
N |
K р |
b |
r 2 |
r2 |
b |
r2 |
r2 |
b |
r 2 |
r2 |
, |
(4.2) |
|
2000 |
|||||||||||||
|
1 |
1n |
1в |
2 |
2n |
2в |
i |
in |
iв |
|
|
где К – коэффициент сопротивления движению лопасти (для тяжелых бетонных смесей в зависимости от водоцементного отношения К = 30 000 … 60 000 Па); ωр – угловая скорость вала ротора, рад/с; η – КПД привода,η ≈ 0,85; bi – проекция ширины лопасти на плоскость перпендикулярную
28
направлению вращения, м; rin, riв – радиусы соответственно наружной и внутренней кромок лопасти, м.
Производительность роторного бетоносмесителя периодического действия, м3/ч, определяется по формуле:
ПЭб |
3,6Vзkвыхkв , |
(4.3) |
|
tз tп tв |
|
где Vз – объем смесителя по загрузке, л; kвых – коэффициент выхода готовой смеси (для бетонных смесей kвых = 0,67 … 0,7, для растворов kвых = 0,85 … 0,95); kв – коэффициент использования машины по времени (kв = 0,85 … 0,95); tз – продолжительность загрузки смесителя, с (tз = 10 … 15 с);tп – продолжительность перемешивания смеси, с (tп = 45 … 60 с); tв – продолжительность выгрузки готового замеса, (tв = 45 … 60 с).
4.4.ПОРЯДОКВЫПОЛНЕНИЯРАБОТЫ
1.Используя теоретическую часть, плакаты, альбомы и действующую модель бетоносмесителя принудительного действия, изучить его устройство, конструкцию и принцип работы.
2.Определить размеры чаши – высоту, наружный диаметр и диаметр внутреннего стакана; размеры лопастей – bi, rin, riв.
3.Определитьугловуюскоростьроторапочислуегооборотовзаоднуминуту.
4.Определить объем смесителя по загрузке VЗ, приняв его равным 0,4…0,33 геометрического объема чаши.
5.Произвести загрузку сухих компонентов до полного закрытия лопастей и за 20 … 25 оборотов добиться равномерного распределения материала по объему смеси.
4.5.ОФОРМЛЕНИЯ ОТЧЕТА ПО ЛАБОРАТОРНОЙ РАБОТЕ
1.Название работы.
2.Цель работы.
3.Краткое описание действующей модели роторного бетоносмесителя с обозначением основных узлов и размеров рабочих органов, расчетные формулы и пояснения к ним.
4.Определить необходимую мощность привода
ипроизводительность роторного бетоносмесителя периодического действия. Сравнить действительную угловую скорость ротора с критической.
5.Выводы.
29
Контрольные вопросы
1.Что представляет собой бетон?
2.В чем заключается приготовление бетонной смеси?
3.Что представляет собой коэффициент выхода готовой смеси.
4.Классификацияциклическихбетоносмесителейпринудительногодействия.
5.Как производится загрузка компонентов и выгрузка готовой смеси в роторных бетоносмесителях?
6.Что значит критическая скорость лопастей. Как она определяется?
7.Назовите составляющие рабочего цикла роторного бетоносмесителя периодического действия.
Рекомендуемая литература: [1,2,5]
БИБЛИОГРАФИЧЕСКИЙ СПИСОК
1.Волков, Д.П. Строительные машины: учеб. пособие для вузов / Д.П. Волков,
Крикун В.Я. – М.: «АСВ», 2002. – 375с.: ил.
2.Доценко, А.И. Строительные машины: учеб. пособие./А.И. Доценко – М.:
Стройиздат, 2003.– 415.: ил.
3.Добронравов, С.С. Строительные машины и основы автоматизации: учебник для вузов./ С.С Добронравов. – М.: Высш. шк., 2001.– 574с., ил.
4.Щербинин, М.И. Метод. указ. к выполнению лабораторных работ № 14 … 22 по курсу «Дорожные машины, автомобили и тракторы»/ М.И. Щербинин, В.Н. Геращенко. – Воронеж : ВИСИ, 1989. – 37 с.
5.Строительные машины: справочник в 2 т. Т. 1: Машины для строительства промышленных, гражданских сооружений и дорог/ А.В. Раннев, Ю.Ф. Корелин, А.В. Жаворонков [и др]; под ред. Э.Н. Кузина. – М.: Машиностроение, 1991. – 496 с.
30