
- •ВВЕДЕНИЕ
- •ОРГАНИЗАЦИЯ ЛАБОРАТОРНЫХ ЗАНЯТИЙ
- •ПОРЯДОК ВЫПОЛНЕНИЯ ЛАБОРАТОРНЫХ РАБОТ
- •ТРЕБОВАНИЯ К ОТЧЕТУ
- •ТЕХНИКА БЕЗОПАСНОСТИ ПРИ РАБОТЕ СТУДЕНТОВ В ЛАБОРАТОРИИ
- •робото-технических комплексов
- •Цель работы: ознакомиться с составом и назначением средств автоматизации производственных процессов применительно к металлообрабатывающим робототехническим комплексам.
- •Цель работы: ознакомиться с приспособлениями, применяемыми при автоматизации металлообрабатывающих станков в зависимости от типа производства.
- •БИБЛИОГРАФИЧЕСКИЙ СПИСОК
ЛАБОРАТОРНАЯ РАБОТА №2 Автоматизация производственных процессов и построение циклограммы
робото-технических комплексов
Цель работы: ознакомиться с составом и назначением средств автоматизации производственных процессов применительно к металлообрабатывающим робототехническим комплексам.
Технические средства и программное обеспечение:
1.IBM-PC или совместимый компьютер;
2.Операционная система Microsoft Windows;
3.Пакет офисных программ Microsoft Office;
Средства для эскизирования:
1.Линейка инструментальная;
2.Штангенциркуль;
3.Карандаш.
Теоретические сведения:
Автоматизация производства — это процесс в развитии машинного производства, при котором функции управления и контроля, ранее выполнявшиеся человеком, передаются приборам и автоматическим устройствам.
Различают частичную, комплексную и полную автоматизацию производства.
Частичная автоматизация производства, точнее — автоматизация отдельных производственных операций, осуществляется в тех случаях, когда управление процессами вследствие их сложности или скоротечности практически недоступно человеку и когда простые автоматические устройства эффективно заменяют его.
Частично автоматизируется, как правило, действующее производственное оборудование. По мере совершенствования средств автоматизации и расширения сферы их применения было установлено, что частичная автоматизация наиболее эффективна тогда, когда производственное оборудование разрабатывается сразу как автоматизированное. К частичной автоматизации производства относится также автоматизация управленческих работ.
При комплексной автоматизации производства участок, цех, завод, электро-
станция функционируют как единый взаимосвязанный автоматизированный комплекс. Комплексная автоматизация производства охватывает все основные производственные функции предприятия, хозяйства, службы; она целесообразна лишь при высокоразвитом производстве на базе совершенной технологии и прогрессивных методов управления с применением надёжного производственного оборудования, действующего по заданной или самоорганизующейся программе, функции человека при этом ограничиваются общим контролем и управлением работой комплекса.
10
Полная автоматизация производства является высшей ступенью автоматизации, которая предусматривает передачу всех функций управления и контроля ком- плексно-автоматизированным производством автоматическим системам управления. Она проводится тогда, когда автоматизируемое производство рентабельно, устойчиво, его режимы практически неизменны, а возможные отклонения заранее могут быть учтены, а также в условиях недоступных или опасных для жизни и здоровья человека.
Наибольший эффект автоматизация дает в основном в массовом и крупносерийном производстве, однако и мелкосерийное и даже индивидуальное производство не исключают возможности использования автоматических систем.
При переходе к автоматизированному производству является анализ конструкции изделия, который состоит из следующих шагов:
1.определение степени пригодности деталей, входящих в изделие, к автоматической загрузке и выявление технологических возможностей автоматизированного изготовления изделия;
2.заключается в оценке подготовленности изделия к автоматизированному производству с учетом автоматического выполнения основных и вспомогательных операций технологического процесса.
Технические средства и устройства
Технические средства и устройства автоматизации производства делятся на основные, т.е. те, с помощью которых реализуется автоматизация производственного процесса и вспомогательные, с помощью которых информация, сформулированная на этапах анализа и модернизации технологического процесса (ЭВМ и периферийные устройства), передается устройствам автоматизации.
К основным техническим устройствам автоматизации производственных процессов можно отнести транспортные устройства. Транспортные устройства предназначены для выполнения таких операций, как загрузка полуфабрикатов, заготовок, инструмента, приспособлений и изделий для хранения на склад и их выгрузку по требованию; перемещение этих предметов со складов к рабочим местам (сборочным позициям, станкам) и обратно, а также межоперационные перемещения заготовок между станками.
Для перемещения грузов широко применяют ленточные транспортеры.
Для размещения заготовок, выдачи их на позицию захвата роботом в ориентированном положении предназначены подающие устройства.
Частью обобщенной операции подачи объекта в рабочую машину является загрузка, которая включает в себя комплекс элементарных операций по автоматическому подводу объектов в рабочую позицию. Базирование и закрепление их относится к другой части операции ввода.
Для загрузки непрерывных заготовок используют загрузочные устройства. К непрерывным заготовкам относят прутки, трубы, проволоку, ленту и другие аналогичные материалы, предназначенные для переработки в дискретные изделия.
11
Для загрузки прутковых и трубных токарных автоматов применяют в основном
цанговые и силовые устройства подачи; клещевые и шариковые устройства полу-
чили значительно меньшее распространение.
Для подачи ленты, проволоки, листового материала наибольшее применение находят роликовые устройства.
К средствам формирования и первичной обработки информации относятся клавишные устройства для нанесения данных на носители информации механическим, оптическим или магнитным способами; накопленная информация передаётся на последующую обработку или воспроизведение.
Исполнительные устройства состоят из пусковой аппаратуры, исполнительных гидравлических, пневматических или электрических механизмов (сервомоторов) и регулирующих органов, воздействующих непосредственно на автоматизируемый процесс. Важно, чтобы их работа не вызывала излишних потерь энергии и снижения кпд процесса.
Построение циклограммы РТК
В автоматизированном производстве металлообрабатывающие станки работают в составе робото-технических комплексов. Для обеспечения совместной работы ПР и металлорежущего оборудования необходимо согласовать работу систем управления роботом и станком. Станки должны быть оснащены автоматизированными устройствами с регулируемым усилием зажима для закрепления заготовки. Для обработки заготовок несимметричной формы в оборудовании следует предусмотреть возможность останова шпинделя в заданном положении.
Компоновка и параметры рабочей зоны металлорежущего оборудования, а
также конструкция приспособлений должны обеспечивать беспрепятственный доступ руки робота в зону резания для установки, заготовки и снятия детали. Конструкция станины, компоновка станка и точки крепления станочных приспособлений должны обеспечивать возможность загрузки и разгрузки станка с фронтальной или тыльной стороны (в зависимости от конкретной планировки РТК).
При создании РТК важным является решение проблемы автоматизации удаления стружки. Короткая и дробленая стружка должна удаляться из зоны резания активно (путем выдувания, отсоса или смывания) или пассивно (под действием силы тяжести).
Управление автоматизированными перемещениями пинолей, прижимов,
зажимных элементов приспособлений и другой оснастки подобного назначения должно иметь блокировку, допускающую перемещение этих элементов только при исходном положении инструмента и при отсутствии вращения заготовки, поддерживаемой этими элементами.
12

а) токарный |
б) фрезерный |
в) сверлильный |
г) долбежный д) строгальный е) зубонарезной
Рис. 2. Структура РТК
Автоматические устройства для контроля должны выполнять измерения в процессе обработки и управлять режимом работы основного технологического оборудования.
Циклограмму будем строить для простейших РТК, состоящих из тактового стола, промышленного робота и металлообрабатывающего станка, структура которых показана на рисунках №3 при помощи программы «циклограмма.xls».
Рис. 3. Программа «Циклограмма»
Исходными данными являются масса детали, время обработки заготовки, сек, время обработки на первом перестанове, сек и время обработки после перестанова. Меняя эти параметры остальные вычисляются автоматически, так же автоматически происходит перестроение диаграммы. Суммарное время обработки берется из работы №1 для выбранной ранее детали.
Выполнение работы:
Для выполнения работы необходимо сделать следующее:
1. Выбрать средства автоматизации технологического процесса изготовления детали-представителя, дать их краткую характеристику. Предоставить информацию в виде перечня в таблице;
13
2.Составить ориентировочную компоновку участка изготовления изделия в условиях автоматизированного производства в составе робототехнического комплекса.
3.Построить диаграмму Ганта для выбранного металлообрабатывающего оборудования.
14
ЛАБОРАТОРНАЯ РАБОТА №3 Автоматизированные транспортные устройства и механизмы
Цель работы: ознакомиться с типами устройств, предназначенных для выполнения таких операций, как загрузка полуфабрикатов, заготовок, инструмента, приспособлений и изделий для хранения на склад и их выгрузку по требованию; перемещение этих предметов со складов к рабочим местам (сборочным позициям, станкам)
и обратно, а также межоперационные перемещения заготовок между станками.
Технические средства и программное обеспечение:
1.IBM-PC или совместимый компьютер;
2.Операционная система Microsoft Windows;
3.Пакет офисных программ Microsoft Office;
Средства для эскизирования:
1.Линейка инструментальная;
2.Штангенциркуль;
3.Карандаш.
Теоретические сведения:
В современных условиях механического, механосборочного цеха машиностроительного завода необходимо решить комплексную задачу автоматизации транспортных операций (подачи заготовок к основному технологическому оборудованию) при загрузки:
1.материалов;
2.заготовок;
3.режущего инструмента;
4.приспособлений.
Кроме того, транспортные устройства используются при межоперационных перемещениях заготовок между станками.
Такое многообразие транспортных операций создало предпосылки к созданию комплексной транспортной системы, управляемой от единой ЭВМ.
В качестве транспортных средств применяют:
1.автоматизированные тележки;
2.штабелеры;
3.конвейеры;
4.кантователи;
5.поворотные столы;
6.роботы;
7.конвейеры для удаления стружки и т.д.
15

Рис. 4. Классификация транспортных систем
Рассмотрим структуру транспортной системы АЛ (рис. 4).
В связи с многообразием форм заготовок для установки заготовок все большее применение находят приспособления-спутники (ПС) (рис. 5) с устройством для автоматической их смены (рис. 6).
Приспособление-спутник (ПС) 11 (см. рис. 5) устанавливают на платформу 7(вместимостью 2 ПС), на которой смонтированы гидроцилиндры 10 и 13, штоки которых имеют Т-образные захваты 14 и 6.
Рис. 5. Приспособление- |
Рис. 6. Устройство |
спутник |
для автоматической смены ПС |
При установке на платформу (перемещение по стрелке Б) ПС своим фигурным вырезом 12 входит в зацепление с захватом 14 штока.
На платформе ПС базируется на роликах 9 и центрируется (по боковым сторонам) роликами 8 (исходное положение ПС в позиции ожидания).
Перемещение штока гидроцилиндра 10 обусловливает В результате захват 6 выйдет из зацепления с ПС и стол станка (с закрепленным на нем ПС) на быстром ходу переместится в зону обработки.
Заготовку закрепляют на ПС во время обработки предыдущей заготовки (когда ПС находится в позиции ожидания) или заранее вне станка.
После того, как заготовка будет обработана, стол станка автоматически (на быстром ходу) передвигается вправо к устройству для смены ПС и останавливается в положении, когда фигурный паз ПС окажется под захватом 6.
Гидроцилиндр поворотного стола расфиксирует ПС, после чего ПС войдет в зацепление с захватом 6. Затем масло поступает в штоковую полость гидроцилин-
16

дра 13, шток смещается в крайнее правое положение и перемещает ПС с заготовкой на платформу 7, где уже находится ПС с новой заготовкой.
Чтобы поменять ПС местами, платформа поворачивается на 180° (на стойке 15) зубчатым колесом 3, сопряженным с рейкой 4, приводимой в движение гидроцилиндрами 5 и 16.
Платформу 7 точно выверяют относительно поворотного стола станка с помощью регулировочных болтов 2 и 17, ввернутых в выступы базовой плиты 7, неподвижно закрепленной на фундаменте.
На рис. 7 показаны наиболее широко применяемые схемы загрузочных устройств.
Рис. 7. Схемы компоновок загрузочных устройств: а – поворотное, б – с раздельной платформой, в – с одной стороны стола.
В поворотном загрузочном устройстве (рис. 4, а) для смены столовспутников 3 стол 2 станка1 перемещается по одной или двум координатам в позицию смены заготовок, в которой он стыкуется с загрузчиком 4, после чего на свободную платформу загрузчика со станка перемещается спутник с обработанной деталью. Затем загрузчик 4 поворачивается на 180° и с другой его платформы на станок перемещается спутник с новой заготовкой.
Загрузочные устройства с раздельными платформами 4, расположенными с двух противоположных сторон от стола станка (рис. 4, б) обычно применяются в достаточно крупных ГПМ с шириной столов-спутников не менее 1000 мм.
Широко распространено загрузочное устройство с платформами 4 расположенными с одной стороны стола и установленными на подвижном или неподвижном основании (рис. 4, в). Загрузочные устройства оснащаются механизмами перемещения (гидроцилиндрами, винтовыми или цепными передачами) сто- лов-спутников.
На ГПМ для обработки деталей типа тел вращения в качестве загрузочного устройства используются промышленные роботы, которые одним захватом могут переносить заготовки различного диаметра.
Система автоматической смены столов-спутников ГПМ состоит из двух частей:
1.загрузочного устройства,
2.накопителя столов-спутников.
Транспортные устройства (ТУ) - бывают:
1.стационарные,
2.подвижные.
Стационарные − конвейеры, подъемники, которые установлены неподвижно на полу.
17

Подвижные − тележки (электрокары, самоходные тележки, работающие по автоматическому циклу, робокары и т.д.). По способу транспортирования ТУ делятся на непрерывного и прерывистого действия.
Непрерывные ТУ выполняются:
1.ленточными,
2.цепными и роликовыми,
3.вибрационные,
4.лотковые самотечные, которые применяют для легких заготовок. Прерывистые ТУ (шаговые) бывают 2-х типов:
1.с убирающимися упорами (собачками),
2.с поворачивающимися захватными устройствами.
ВГПС при большой серийности используют конвейерные ТУ, а при малой серийности - автоматические тележки (рис. 8): рельсовые - для деталей больших размеров и безрельсовые, управляемые от ЭВМ перемещающиеся по заданному маршруту (по магнито-электропроводу и т. д.).
Рис. 8. Транспортная тележка
Тележка состоит из основания 1 с ромбовидным размещением колес 6, 9, что повышает маневренность тележки и упрощает устройство разворота. С торцов основания смонтированы подвижные бамперы 5 для автоматического торможения и остановки в случае возникновения препятствия.
В основании расположены приводы на колеса 9, состоящие из редукторов 8, электродвигателей 7 с питанием от аккумуляторных батарей. На основании монтируется грузовая платформа 2 для транспортирования и загрузки-выгрузки столовспутников 3 с заготовками 4.
Расчет количества средств механизации
Количество элементов напольно-тележечного транспорта (электротележ-
ки, электроштабелеры, погрузчики и т.п.) определяют по формуле:
(5)
где Q – годовой грузооборот, т;
qэ – грузоподъемность электротележки, т;
Тэ – общее время пробега (оборот) электротележки, мин;
18
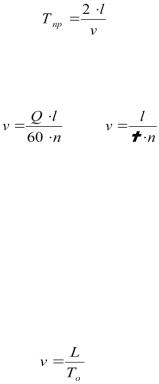
К1 – коэффициент неравномерности; К2 = 0,8 - коэффициент использования грузоподъемности;
Фдо – действительный годовой фонд времени работы оборудования при соответствующем числе смен, час;
m = 1 или 2 коэффициент, учитывающий одно или двухстороннюю систему перевозок;
Общее время пробега электро-тележки:
Тэ = Тпр Тп Тр Тз, (6) где Тпр – время пробега эл. тележки в оба конца, мин;
Тп – время погрузки, мин (принимаем равным 0,07 – 0,15 на 1 т, чел.-ч); Тр – время на разгрузку, мин (принимаем равным 0,07 на 1 т чел.-ч); Тз – время случайных задержек (примерно 10% на каждый рейс), мин; Время пробега эл. тележки в оба конца:
(7)
где l – среднее расстояние при маршрутных перевозках;
v – среднетехническая скорость электрокара (принимаем равным 3,6…5 км/ч). При расчете подвесных конвейеров используют скоростьили производительность:
или |
(8) |
где Q – производительность конвейера в шт/час;- такт работы в мин;τ
l – шаг подвесок в м;
n – количество изделий на одной подвеске, шт.
Для конвейеров, обслуживающих станочные линии, скорость принимается 1 – 6 м/мин (при массе изделий 30 – 50 кг скорость принимают не более 3 м/мин). При необходимости создания запаса на конвейере в расчет вводят коэффициент увеличения производительности (до 5). При обслуживании подвесным конвейером сушильных, моечных или лакокрасочных камер скорость его определяется:
(9)
где L – общая длина рабочего участка камеры; То – технологическое время обработки.
Расчет производительности конвейера
Конвейер (транспортер) - наиболее распространенная транспортирующая машина в кузнечно-штамповочных и литейных цехов на машиностроительных предприятиях. Конвейеры предназначены для перемещения холодных и горячих заготовок в горизонтальном и наклонном направлениях при угле подъема, не превышающем 2/3 угла естественного откоса в движении. Производительность конвейеров,
т/ч, рассчитывается по формуле |
|
П = 3600 ∙ ∙ ∙ ∙ , |
(10) |
19
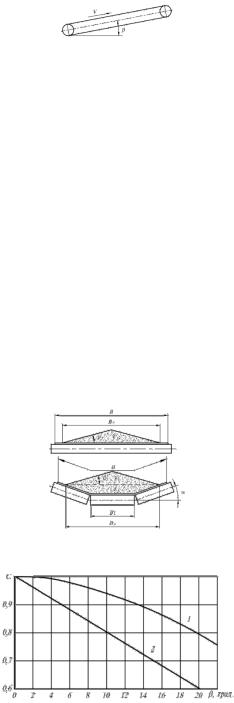
где F - площадь поперечного сечения потока материала на тележке, м2; V - скорость движения материала, м/с (табл. 3);
γ- плотность материала, т/м3 , (табл. 3);
С- коэффициент, учитывающий снижение производительности в зависимости от
угла наклона конвейера, угол наклона конвейера β (рис. 10) принимать по табл. 3. Значения коэффициента С определять по графику (рис. 11, кривая 1).
Рис. 9. Схема ленточного конвейера
Площадь сечения материала на ленте подсчитывается следующим образом. Многочисленные исследования и многолетний опыт эксплуатации ленточных конвейеров показали, что поперечное сечение материала на плоской ленте без бортов
представляет собой треугольник с углом при основании ρ3, равным половине угла
естественного откоса в движении ρ2, и длиной основания Вo меньшей ширины лен-
ты В (рис. 11 а). 0 = 0,85 ∙ ; 3 = 0,5 ∙ 2 = 0,35 ∙ 3, (11)
где ρ1 - угол естественного откоса в покое. Площадь сечения материала на желобчатой ленте (рис. 11, б) можно рассматривать как сумму площадей треугольника и трапеции.
Длину среднего ролика В1 определяют через ширину ленты В1 = 0,38В. Угол наклона боковых роликов a принимать из табл. 3.
Рис. 10. Схема к определению поперечного сечения материала на тележке конвейера
Рис. 12. График для определения значения коэффициента С для 1) ленточного конвейера; 2) винтового конвейера.
20

Таблица 3
Выполнение работы:
1.По выданному преподавателем варианту определить состав и количество грузоподъемных механизмов, достаточных для обеспечения грузопотока цеха в соответствии с производственной программой.
2.Количество тележек рассчитывается в специализированной программе при следующих исходных данных (рис. 13).
3.Расчет конвейера выполнить в программе «Расчет производительности конвейера (рис. 13 - 14).
Рис. 13. Ввод исходных |
Рис. 14. Оформление |
данных |
отчета |
Результаты расчетов (рис. 15), |
|
Рис. 15. Результат расчета
21

Рис. 16. Ввод исходных данных
Рис. 17. Результаты расчета
22