
Учебное пособие 1422
.pdf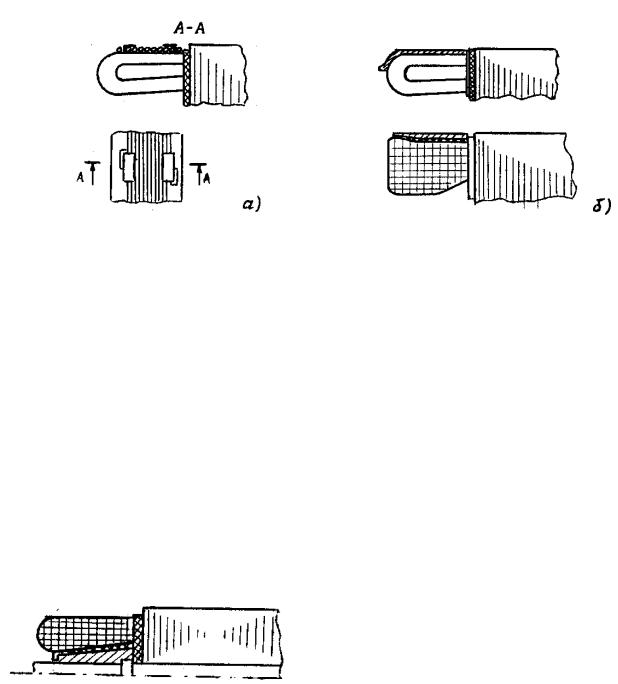
31
поверхность лобовых частей выравнивают путем увеличения длины вылета пластмассы коллектора со стороны петушков.
Для машин средней и больших мощностей ранее широко использовались проволочные бандажи со скобами из тонкой медной ленты (рис.2.13 а)).
Рис. 2.13
Всовременных конструкциях проволочные бандажи не применяются изза неудобства их пайки высокотемпературными припоями на уже готовых обмотках.
Всовременных машинах в качестве бандажей применяют сплошные каппы и кольца. Кольца и каппы изолируются от обмотки опрессовкой пластмассой или наклейкой с внутренней стороны изоляционных лент
(рис.2.13 б)).
Бандажные каппы обычно штампуются, кольца точатся или штампуются. Чтобы исключить соскальзывание каппы с лобовых частей, на каппе сделан небольшой конус. Высокие механические свойства стеклолент и стеклонитей позволяют использовать их в качестве бандажа для крупных машин. Такие бандажи упрощают технологию и повышают надежность машин.
Вмашинах средней и большой мощности для фиксации лобовых частей со стороны вала применяются поддержки, опрессованные пластмассой (рис.
2.14).
При опоре лобовых частей на поддержки, посадку бандажей можно осуществлять с достаточным натягом. Часто поддержки используют для
Рис. 2.14
размещения в них балансировочных грузов.
2.1.5. Обмотки явно выраженных полюсов машин переменного тока
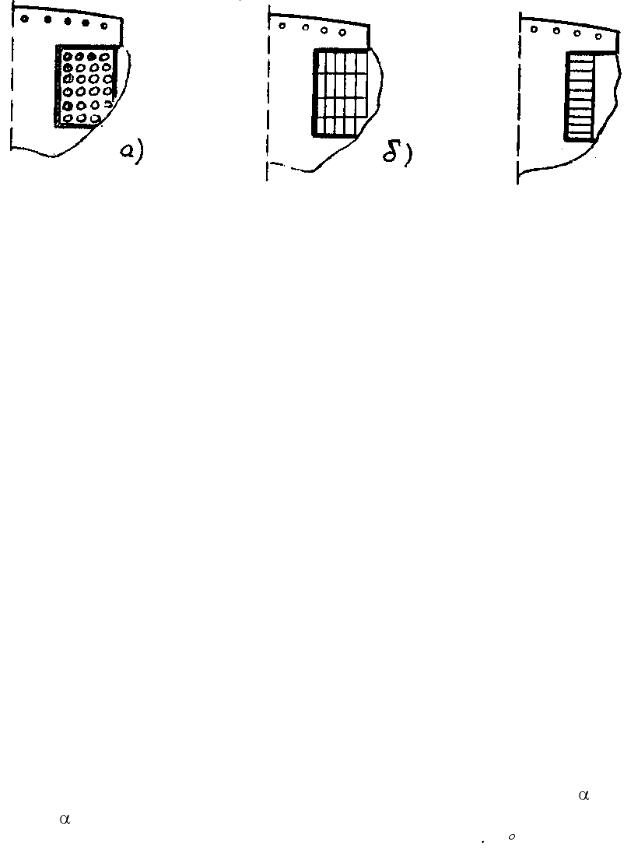
32
Обмотки полюсов на роторах могут выполняться как прямоугольными, так и круглыми проводами.
Рис. 2.15
Катушки, выполненные прямоугольным проводом, выполняются как с изгибом шинки на плоскую сторону (2.15 б)), так и на ребро (рис.2.15 в)). Наиболее важным преимуществом катушек на ребро является лучшие условия охлаждения. В качестве изоляции катушек от полюсов используется стекломиканиты, стеклослюдениты, пленочная изоляция. Наименьшее тепловое сопротивление обеспечивает пленочная изоляция из-за своей малой толщины. Ее использование более предпочтительно. Наиболее технологична изоляция напылением.
2.1.6. Температурная компенсация
Необходимость температурной компенсации возникает всякий раз, когда температурные коэффициенты линейных расширений сопрягаемых деталей или их рабочие температуры различны.
Существует несколько приемов для решения вопросов компенсации:
1). Применение материалов с одинаковыми коэффициентами линейного расширения. При этом часто приходится отказываться от выгодного в технологическом, конструктивном или весовом отношениях материала ради исключения необходимости температурной компенсации.
2). Снижение разности температур сопрягаемых деталей за счет интенсификации охлаждения.
3). Использование специальных конструктивных приемов для температурной компенсации.
Необходимость температурной компенсации видна из следующего примера. Рассмотрим узел, состоящий из двух деталей - ступицы 1 и кольца 2
(рис.2.16). Пусть для вала коэффициент линейного расширения будет |
, а для |
кольца 2. |
|
При нагревании этого образца до температуры t , зазор |
между |
сопрягаемыми деталями будет определяться следующим выражением: |
|
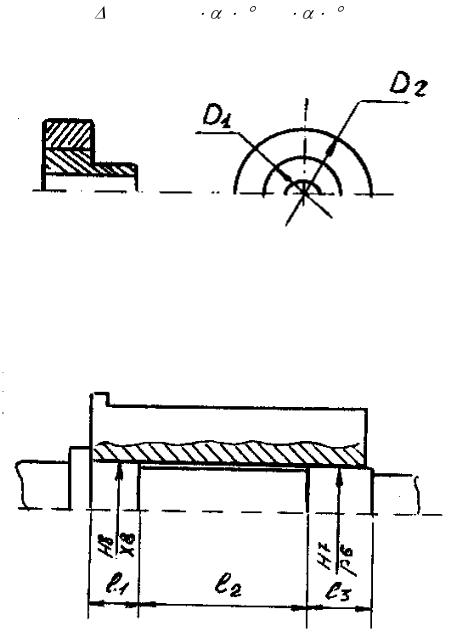
33
D = (D2-D1) 2 t - D1 1 t |
(2.4) |
Рис. 2.16
В некоторых случаях величина этого зазора может привести к нарушению соединения деталей и нарушению выполняемых функций узла в целом. С температурной компенсацией приходится сталкиваться и в случаях посадки на стальной вал длинных алюминиевых ступиц (рис.2.17).
Рис. 2.17
Если посадка ступицы на вал на всей ее длине одинакова, то из-за разницы в коэффициентах температурного расширения могут наблюдаться случаи "сползания" ступицы с вала в процесса работы. Чтобы избежать этого, посадку ступицы на вал делают ступенчатой: на участке l1 натяг берется наибольшим, на участке l2 посадка с зазором и на - с меньшим натягом. При такой ступенчатой посадке случаи "сползания" ступицы устраняются, так как она всегда надежно фиксирована в осевом направлении на участке l3.
При посадке пакетов стали в алюминиевые корпуса также возникает проблема температурной компенсации. Для машин с широким диапазоном рабочих температур нельзя осуществлять посадку пакета в алюминиевый корпус с таким первоначальным натягом, который исключал бы возможность
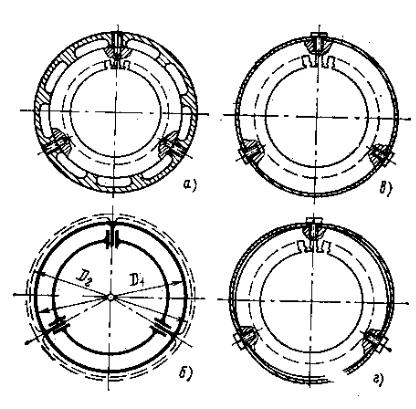
34
появления зазора при максимальном нагреве. Поэтому натяги при посадке выбирают средними (например Н8/Х8), а сохранение центричности пакета в корпусе обеспечивают специальными конструктивными решениями. Одним из возможных решений является установка пакета стали на цилиндрических направляющих штифтах (рис.2.18).
Рис. 2.18
Принцип центрирования пакета стали относительно корпуса поясняет схема, приведенная на рис. 2.18 а). Действительно, при изменении диаметра внешнего контура центричность внешнего и внутреннего контура сохраняется, т.к. внутренний контур скользит по трем направляющим, расположенным под углом 120 оС. Необходимым условием является плотная посадка цилиндрических концов штифтов в пакете и корпусе.
Другое возможное решение, применяемое для тонкостенных корпусов с равномерной жесткостью, проиллюстрировано на рис. 2.18 в). Пакет закреплен с помощью болтов, посаженных в него резьбовой частью. Тонкий корпус в этом случае имеет возможность свободно деформироваться на участках между болтами, сохраняя центричность (рис. 2.18 г)).
Для герметичных машин, в которых любое сквозное отверстие в корпусах крайне нежелательно, могут использоваться способы посадки, схематически показанные на рис. 2.19 а) - г).
Первый из этих способов (рис. 2.19 а)) применим для относительно коротких пакетов. Здесь фланец 1 приваривается к крайнему листу 2, образованному из нескольких скрепленных сваркой средних листов. Все листы
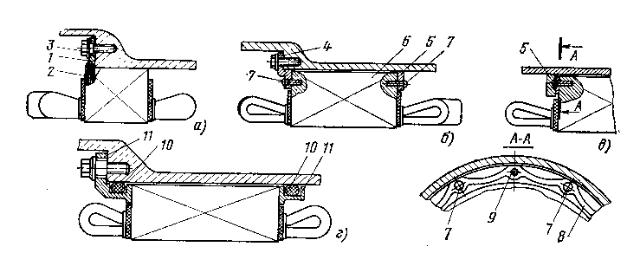
35
затем скрепляются в единый пакет, который стопорится относительно корпуса болтами 3.
Рис. 2.19
Длинные пакеты (рис. 2.19б)) могут закрепляться в алюминиевых корпусах на двух алюминиевых центрирующих дисках 4 и 5, скрепленных с пакетом 6 рядом винтовых заклепок 7 или винтов. Этот способ крепления допускает применение пакетов без механической обработки по их наружному диаметру.
При значительных температурных расширениях, когда упругости заклепочных соединений становится недостаточно, для компенсации возникающих деформаций между пакетом стали 6 и боковым алюминиевым кольцом 5 может устанавливаться пружинный элемент в виде фигурного стального кольца 8 (рис. 2.19 в)). Пружинное кольцо через отверстие (крепится винтами к пакету стали, а через отверстие 7 к кольцу 5. Жесткость пружинного кольца и диаметр заклепок выбираются из условия отсутствия остаточных деформаций.
На рис. 2.19 г) показан способ вывешивания пакета в корпусе с помощью круглых резиновых колец 10, которые располагаются в канавках фланцев 11. Фланцы могут крепиться к пакету или несколькими продольными сварными шнами по наружному диаметру, или винтовыми заклепками.
2.2. Коллекторы и контактные кольца
2.2.1. Общие требования к коллекторам и контактным кольцам
Коллектор - узел электрической машины, служащий для подвода тока от якорной обмотки к неподвижным щеткам. Условия работы коллектора определяются следующими отрицательными факторами:
1). Действие центробежных сил.
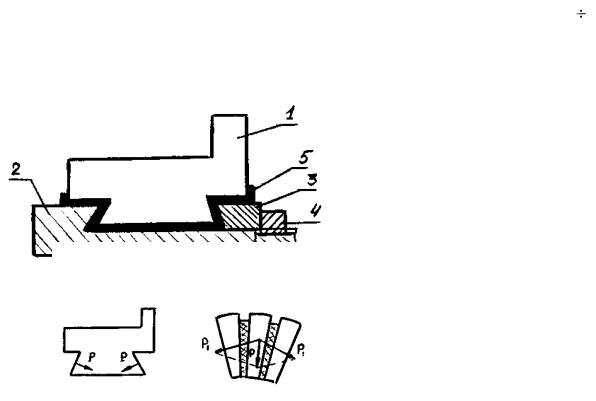
36
2). Значительные тепловые нагрузки, обусловленные как электрическими, так и механическими потерями.
3). Работа в среде, насыщенной щеточной пылью.
Основное требование, предъявляемое к коллекторам - обеспечение устойчивой, безискровой коммутации во всех режимах работы.
Для выполнения этого требования, конструкция коллектора должна обеспечить точную цилиндричность наружной поверхности, по которой скользят щетки. Повышенное биение этой поверхности (более 0,01 мм), а особенно выступание медных пластин, приводят к появлению искрения и ускоренному износу щеток. Существенное влияние на цилиндричность коллектора оказывает его нагревание. Так как материалы из которых изготавливается коллектор, имеют разные коэффициенты линейного расширения, то вопросы температурной компенсации принимают важное значение.
С учетом эксплуатационных и технологических требований основными задачами при разработке коллектора являются:
1). Обеспечение монолитности конструкции коллектора.
2). Обеспечение цилиндричности его наружной поверхности во всех условиях эксплуатации.
3). Обеспечение ремонтопригодности коллектора, т.е. производить проточку наружной поверхности при периодических ремонтах.
4). Возможность использования существующих технологий при изготовлении.
За последние годы разработано большое число различных конструкций коллекторов. Наибольшее распространение получили два следующих типа коллекторов: арочные коллекторы на стальных конусных втулках и коллекторы на пластмассе.
Первый тип используется для машин мощностью более (200 300) Вт, второй - для машин малых мощностей.
2.2.2. Конструкции коллекторов
Конструкция коллекторов на стальных конусных втулках показана на рис. 2.20.
Коллекторы на стальных втулках в зависимости от их длины могут иметь один или несколько ласточкиных хвостов. В качестве изоляции используется слюда или миканит. В верхней части пластин имеется выступ, в котором сделаны
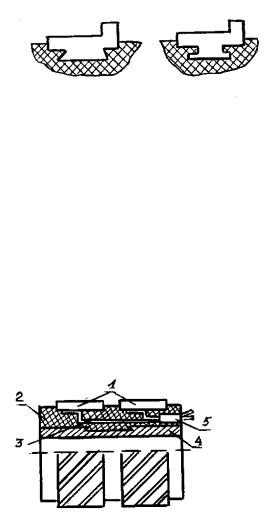
37
шлицы для укладки проводников обмотки якоря.
Конусные втулки передают давление (см. рис. 2.21) только на внутренние конические поверхности ласточкиного хвоста, стягивая
пластины по направлению к центру. Однако в связи с тем, что пластины в поперечном сечении имеют форму клина, при стягивании их к центру создается боковое давление - арочный распор, аналогичный распору в строительных арках. Арочный распор обеспечивает монолитность коллектора, что необходимо для сохранения строго цилиндрической формы его в течение всего срока службы.
Коллекторы на пластмассе применяются в электрических машинах малой мощности. В этих коллекторах пластмасса является как изолирующим, так и силовым элементом конструкции. Использование пластмассы упрощает изготовление коллектора и снижает его стоимость. Следует учитывать, что коэффициенты теплопроводности пластмасс на три порядка ниже, чем коэффициенты теплопроводности меди. Это приводит к тому, что при нагреве пластин могут возникать значительные температурные напряжения, вызванные разностью температур различных деталей. Существует несколько разновидностей коллекторов на пластмассе. На рис.2.22 приведены конструкции коллекторов с "ласточкиным хвостом" и "Т" образной формой пластины.
Достоинствами коллекторов на пластмассе являются:
1). Простота изготовления.
2). Высокая технологичность.
3). Меньший расход меди, следовательно и экономичность.
Одним из способов снижения тепловых нагрузок на коллектор всех типов является увеличение их наружного диаметра до максимального допустимого диаметром якоря машины, а также увеличения их длины сверх той, которая требуется для размещения щеток. Однако прибегать к этому следует в тех случаях, когда все другие способы интенсификации охлаждения исчерпаны.
2.2.3. Конструкции контактных колец
Контактные кольца на пластмассе используются в машинах переменного тока чаще всего для щеточных синхронных машин. Для машин с охлаждением путем продува с максимальной температурой +80 оС нашли применение контактные кольца, опрессованные пластмассой. Для нагревостойких машин могут применяться
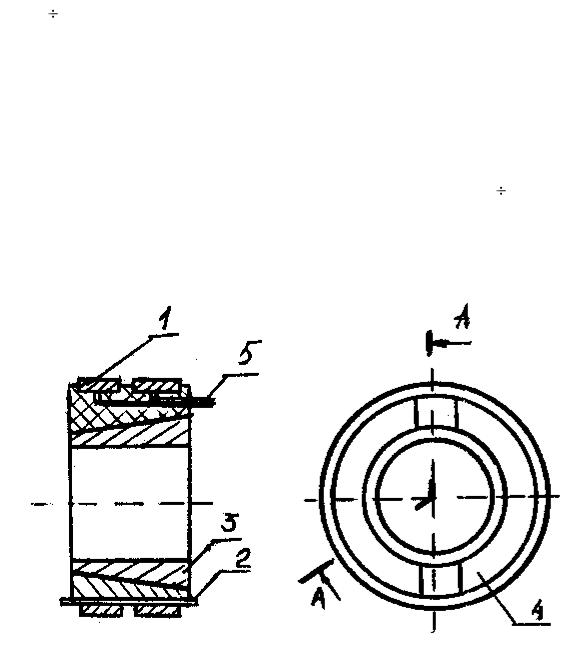
38
контактные кольца на стальных втулках со слюдяной изоляцией.
Рассмотрим конструкцию контактных колец, опрессованных пластмассой
(рис.2.23). Два одинаковых контактных кольца 1 с припаянными к ним |
||
Рис. 2.23 |
выводами 3 опрессованы пластмассой 2. На наружной |
|
поверхности колец обычно делают наклонные канавки под |
||
|
углом (30 60) оС для улучшения коммутации и охлаждения колец.
Наклонное положение канавок устраняет дрожание щеток при работе машины. Внутренняя стальная втулка 4 служит для компенсации сил, возникающих при напрессовке узла колец на вал ротора. Чтобы исключить замыкание выводных концов на соседние пластмассы и на внутреннюю втулку в процессе опрессовки, на них надеваются изоляционные втулки.
Материалом контактных колец является медь или хромистая бронза. Опрессовка осуществляется пластмассой АТ-4. Опрессованные пластмассой кольца удовлетворительно работают в диапазоне температур (-60 +80) оС.
Контактные кольца на стальной втулке могут работать при более высокой температуре, чем контактные кольца на пластмассе. Конструкция контактных колец на стальной втулке показана на рис. 2.24.
Рис.2.24
Контактные кольца 1 разделены изоляционной шайбой из нагревостойкой пластмассы и посажены на слюдяную прокладку 2. Между центральной конусной втулкой 3 и слюдяной прокладкой находятся два конусных полукольца 4, с помощью которых производится сборка и создается предварительный натяг контактных колец. Натяг легко регулируется в процессе монтажа усилием пресса при запрессовке конусов. Выводы сделаны в
39
виде шин 5, приваренных к контактным кольцам и надежно изолированных. Выводы шин проходят в зазор между двумя конусными полукольцами. Это пространство после сборки заполняют компаундом.
Материал конусных колец и втулки выбирается с температурным коэффициентом линейного расширения, равным температурному коэффициенту линейного расширения материала колец. Этим исключается ослабление посадки контактных колец в процессе работы.
2.3. Валы
2.3.1. Общие требования и классификация
Вал электрической машины является основным силовым элементом ротора, на котором располагаются все его узлы и детали. Правильно сконструированный вал должен отвечать следующим требованиям:
1). Жесткость вала должна быть такой, чтобы максимальные нагрузки, возможные при эксплуатации, не приводили к большим прогибам. Прогибы могут вызвать касание ротора о статор или возникновение больших сил одностороннего притяжения.
2). Критические частоты вращения вала должны быть выше рабочих частот вращения.
3). Напряжения в сечениях вала при всех режимах работы не должны превышать предельно допустимых для примененного материала.
4). Элемент стыковки с приводом или исполнительным механизмом должен обеспечивать "мягкое" сочленение, исключающее передачу на подшипники дополнительных нагрузок вызванных несоосностью машины и привода. Предъявляемые требования определяют виды проверок, которым подвергаются валы при механических расчетах: проверку прогибов, критической частоты вращения и допустимых напряжений в сечениях.
По конструктивной форме валы подразделяют на следующие типы: 1). Гладкие (двигатели малой мощности).
2). Ступенчатые (двигатели средней и большой мощности). 3). Полые валы.
4). Гибкие валы (генераторы с периодической нагрузкой).
Материалами для валов обычно являются легированные углеродистые и нержавеющие стали или титановые сплавы. Нержавеющие стали (с термообработкой) и титановые сплавы обладают высокой коррозийной стойкостью и диамагнитны. Поэтому при их использовании резко сокращаются магнитное рассеяние и паразитные подшипниковые токи. Необходимо помнить, что модули упругости нержавеющих сталей и титановых сплавов существенно ниже, чем модули упругости углеродистых сталей, вследствие чего жесткость таких валов будет ниже.
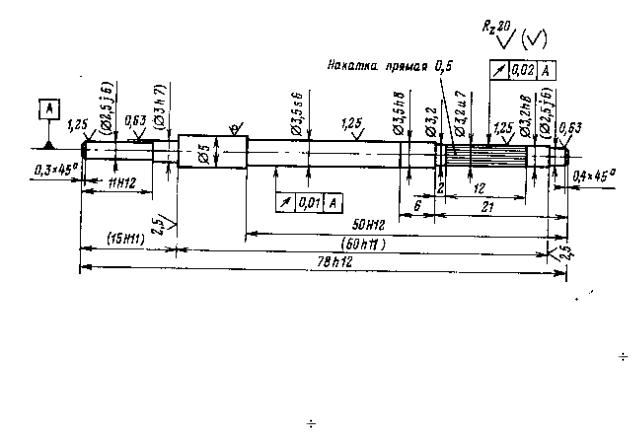
40
Вбольшинстве случаев вал, имеющий критическую частоту вращения выше диапазона рабочих частот автоматически удовлетворяет как условиям прочности, так и условиям малых прогибов. Поэтому при выборе конструкции вала и первоначальных расчетах ограничиваются только критической частотой вращения. Остальные виды расчетов производят как поверочные после полной разработки конструкции. Для обеспечения технологичности конструкции вала число ступеней на его наружней поверхности (а у полых валов и на внутренней) должно быть минимальным. Однако это не должно противоречить требованиям наименьшей массы при заданной жесткости. Часто в валах наибольший наружный диаметр, на который не производится посадка деталей, остается без обработки (равен диаметру заготовки).
Вцелях снижения наружного диаметра и массы, упорные буртики на валу (например для опоры колец подшипников) иногда образуют за счет прессовой посадки специальных колец. Это требует дополнительных деталей с жесткими требованиями по классу размеров и удлиняет технологический цикл изготовления.
Для двигателей постоянного и переменного тока применяются сплошные цилиндрические валы, конструкция которых показана на рис. 2.25.
Рис. 2.25
Диаметральные размеры (кроме Ø 5) обрабатываются по квалитетам 6 8, так как они являются посадочными для деталей ротора. Линейные размеры, которые определяют взаимное положение насаживаемых деталей, выполняются по квалитетам 11 12. Остальные линейные размеры выполняются "свободными", т.е. допуски на них оговариваются общей надписью на чертеже. Линейные размеры с допусками входят в схему допусков всей машины. Для линейных размеров не следует использовать квалитеты меньше 11, так как это затрудняет обработку и резко увеличивает стоимость работ.