
Методы обеспечения точности автоматизированного машиностроительного производства. методические указания к выполнению практических работ. Симонова Ю.Э., Краснова М.Н
.pdfМИНИСТЕРСТВО НАУКИ И ВЫСШЕГО ОБРАЗОВАНИЯ РОССИЙСКОЙ ФЕДЕРАЦИИ
Федеральное государственное бюджетное образовательное учреждение высшего образования
«Воронежский государственный технический университет»
Кафедра автоматизированного оборудования машиностроительного производства
МЕТОДЫ ОБЕСПЕЧЕНИЯ ТОЧНОСТИ АВТОМАТИЗИРОВАННОГО МАШИНОСТРОИТЕЛЬНОГО ПРОИЗВОДСТВА
МЕТОДИЧЕСКИЕ УКАЗАНИЯ
к выполнению практических работ для студентов направления 15.04.01 «Машиностроение»
(программа магистерской подготовки «Обеспечение качественно-точностных характеристик при изготовлении изделий в автоматизированном машиностроительном производстве»)
всех форм обучения
Воронеж 2021
1
УДК 621.002:658.51(07) ББК 34.5я7
Составители:
ст. преп. Ю. Э. Симонова, канд. техн. наук М. Н. Краснова
Методы обеспечения точности автоматизированного машиностроительного производства: методические указания к выполнению практических работ для студентов направления 15.04.01 «Машиностроение» (программа магистерской подготовки «Обеспечение качественно-точностных характеристик при изготовлении изделий в автоматизированном машиностроительном производстве») всех форм обучения / ФГБОУ ВО «Воронежский государственный технический университет»; сост.: Ю. Э. Симонова, М. Н. Краснова. – Воронеж: Изд-во ВГТУ, 2021. - 39 с.
В методических указаниях изложены требования и общие вопросы по выполнению практических работ, приведены теоретические сведения, полезные не только для выполнения практических работ, но и при подготовке к сдаче зачетов и экзаменов. Выполнение практических работ дает возможность ознакомления при выборе параметров шероховатости поверхностного слоя при обработке лезвийным инструментом, способах расчета погрешностей, оценке изменения точностных характеристик технологических систем во времени.
Предназначены для студентов всех форм обучения.
Методические указания подготовлены в электронном виде и содержатся в файле МОТАМППР.pdf.
Табл. 38. Библиогр.: 5 назв.
УДК621.002:658.51(07) ББК34.5я7
Рецензент - С.Ю. Жачкин, д-р. техн. наук, проф., проф. кафедры автоматизированного оборудования машиностроительного производства
Издается по решению редакционно-издательского совета Воронежского государственного технического университета
2
Практическая работа № 1 РАСЧЕТНОЕ ОПРЕДЕЛЕНИЕ ПАРАМЕТРОВ ШЕРОХОВАТОСТИ
ПРИ ОБРАБОТКЕ ПОВЕРХНОСТИ ЛЕЗВИЙНЫМ ИНСТРУМЕНТОМ
Цель работы: ознакомление с методикой теоретического определения параметровшероховатостиприлезвийнойобработке материалов.
Эксплуатационные свойства деталей машин характеризуются состоянием их поверхностного слоя, в частности, шероховатостью. Одним из недостатков при конструкторско-технологической подготовке производства является недостаточная научная обоснованность назначения и технологического обеспечения параметров шероховатости. Решение данной задачи возможно на основе зависимостей между характеристиками шероховатостиитехнологическимиусловиямиобработки.
Отдельные элементы режима резания по-разному влияют на характеристики поверхностногослоя.
Машинное время обработки, вычисленное по формуле
степени зависит от скорости резания v и подачи S при неизменных значениях длины l, диаметраd обрабатываемойповерхностиичислапроходовi.
Привыборесочетаний элементоврежимарезаниясцельюобеспечениязаданного качества поверхностного слоя это условие нарушается, поскольку на формирование поверхностного слоя, так же, как и на характеристики точности обработки, оказывают одновременное воздействие температура и сила резания. С точки зрения обеспечения благоприятных эксплуатационных свойств обрабатываемых материалов желательна обработка при оптимальной скорости резания vо, обеспечивающая при принятых значениях S и t температуру в зоне резания, при которой наблюдается минимальный износ режущего инструмента.
Как известно, в соответствии с ГОСТ 2789—73 «Шероховатость поверхности. Параметры и характеристики» установлено шесть параметров шероховатости. Термины и определения шероховатости поверхности по ГОСТ 25142—82 приведены ниже.
Среднее арифметическое отклонение профиля Ra — среднее арифметическое абсолютных значений отклонений профиля в пределах базовой длины определитсяпоформуле
|
|
1 |
n |
|
|
Ra |
|
| yi | |
(1) |
||
|
|||||
|
|
n i 1 |
|
где n — число выбранных точек профиля в пределах базовой длины l; yi — отклонение профиля — расстояние между точкой профиля и базовой (средней) линией. Числовые значения Ra приведены в табл.1.
3
Таблица 1
Значения Ra, мкм
100 |
80 |
63 |
50 |
40 |
32 |
25 |
20 |
16,0 |
12,5 |
10,0 |
8,0 |
6,3 |
5,0 |
4,0 |
3,2 |
2,5 |
2,0 |
1,60 |
1,25 |
1,00 |
0,80 |
0,63 |
0,50 |
0,40 |
0,32 |
0,25 |
0,20 |
0,160 |
0,125 |
0,100 |
0,080 |
0,063 |
0,050 |
0,040 |
0,032 |
0,025 |
0,020 |
0,016 |
0,012 |
0,010 |
0,008 |
|
|
|
|
|
|
|
|
Примечание.Выделенызначенияпредпочтительногоприменения.
Высота неровностей профиля по десяти точкам Rz — сумма средних абсолютных значений высот пяти наибольших выступов профиля и глубин пяти наибольших впадин профиля в пределах базовой длины, определяется по формуле
|
1 |
|
5 |
5 |
|
|
|
Rz |
|
|
|
ypi |
yvi |
|
(2) |
|
|||||||
|
5 |
i 1 |
i 1 |
|
|
гдеypi —высотаi-гонаибольшеговыступапрофиля,определяемая расстоянием от средней линии профиля m до высшей точки выступа профиля; yvi — глубина i-й наибольшей впадины профиля, определяемая расстоянием от средней линии профиля донизшейточки впадиныпрофиля.
Наибольшая высота неровностей профиля Rmax — расстояние между
линией выступов профиля и линией впадин профиля в |
пределах базовой длины. |
|||||||||||
ЧисловыезначенияRzиRmaxприведены втабл.2. |
|
|
|
|
|
|||||||
|
|
|
Значения Rz и Rmax, мкм |
|
|
|
Таблица 2 |
|||||
|
|
|
|
|
|
|
||||||
|
|
|
|
|
|
|
|
|
|
1600 |
1250 |
|
|
1000 |
800 |
630 |
500 |
400 |
320 |
250 |
200 |
|
160 |
125 |
|
|
100 |
80 |
63 |
50 |
40 |
32 |
25,0 |
20,0 |
|
16,0 |
12,5 |
|
|
10,0 |
8,0 |
6,3 |
5,0 |
4,00 |
3,2 |
2,5 |
2,0 |
|
1,60 |
1,25 |
|
|
1,00 |
0,80 |
0,63 |
0,50 |
0,40 |
0,32 |
0,25 |
0,20 |
|
0,160 |
0,125 |
|
|
0,100 |
0,080 |
0,63 |
0,050 |
0,040 |
0,032 |
0,025 |
|
|
|
|
|
Примечание.Выделенызначенияпредпочтительногоприменения.
Средний шаг неровностей профиля Sm — среднее значение шага неровностей профиля в пределах базовой длины, определяетсяпоформуле
|
|
1 |
n |
|
|
Sm |
|
Smi |
(3) |
||
n |
|||||
|
|
i 1 |
|
где n — число шагов неровностей профиля; Smi — i-й шаг неровностей профиля—отрезоксреднейлиниипрофиля,содержащий неровностьпрофиля.
4
Средний шаг местных выступов профиля S — среднее значение шагов местных выступов профиля, находящихся в пределах базовой длины определяется по формуле
|
1 |
n |
|
|
S |
Si |
(4) |
||
|
||||
|
n i 1 |
|
где n — число шагов местных выступов; Si — i-й шаг местных выступов профиля — отрезок средней линии между проекциями на нее наивысших точек соседних местных выступов профиля (см. рис. 1); числовые значения параметров Sm иS всоответствии сГОСТ2769–73приведенывтабл.3.
Таблица 3
Значения Sm и S, мкм
|
|
|
|
|
|
|
|
|
12,5 |
10,0 |
8,00 |
6,3 |
5,0 |
4,0 |
3,2 |
2,5 |
2,0 |
1,60 |
1,25 |
1,00 |
0,80 |
0,63 |
0,50 |
0,40 |
0,32 |
0,25 |
0,20 |
0,16 |
0,125 |
0,100 |
0,080 |
0,063 |
0,050 |
0,040 |
0,032 |
0,025 |
0,020 |
0,016 |
0,0125 |
0,010 |
0,008 |
0,006 |
0,005 |
0,004 |
0,003 |
0,002 |
|
|
|
Относительная опорная длина профиля tp |
— отношение опорнойдлины |
||||||
профилякбазовойдлине: |
|
|
|
|
|
||
p |
1 |
n |
|
||||
tp |
|
|
|
|
bi |
(5) |
|
l |
l |
||||||
|
|
i 1 |
|
где ηp — опорная длина профиля равна сумме длин отрезков bi, отсекаемых на заданном уровне p в материале профиля линией, эквидистантой средней линии в пределах базовой длины; p — уровень сечения профиля — расстояние между линией выступов профиля и линией, пересекающей профиль эквидистантно линии выступов профиля,выраженный в процентах от Rmax.
Высота микронеровностей на обработанной поверхности определяется по формулам А.И.Исаева, а также по известной теоретической формуле В.Л. Чебышева:
Rz |
|
S2 |
(6) |
|
8r |
||||
|
|
|
где r—радиуспривершинерезцавплане,мм.
Известные теоретические зависимости для определения высоты неровностей учитывают только геометрические параметры зоны резания. Однако если считать подачу,входящуюв этиформулы,функциейтолщинысреза,томожноучитыватьфизико-
5
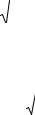
механические свойства обрабатываемого и инструментального материалов и режимы резания. Следовательно, в известные теоретические формулы для определения высоты неровностей, полученные из геометрических соображений, следует подставлять не S, а некоторое значение Sф, полученное в виде функции от толщины среза. Таким образом, параметры шероховатости могут быть определены по следующим уточненным теоретическим зависимостям:
|
|
|
|
|
|
|
|
|
|
|
|
sin sin |
|
|
|
|
|
|
|
|
(7) |
||||||||||||||||||
|
|
|
|
|
|
|
|
|
|
Rz |
|
|
|
|
|
|
|
1 |
(Sф r) tg |
|
|
tg |
1 |
|
|
||||||||||||||
|
|
|
|
|
|
|
|
|
|
|
|
|
|
|
|
|
|
|
|
|
|
2 |
|
|
|||||||||||||||
|
|
|
|
|
|
|
|
|
|
|
|
sin( 1) |
|
|
|
|
|
|
|
2 |
|
||||||||||||||||||
если φ1 ≤ arcsin |
S |
; φ≤ arcsin |
S |
|
|
|
|
|
|
|
|
|
|
|
|
|
|
|
|
|
|||||||||||||||||||
|
|
|
|
2r |
|
|
|
|
|
|
|
|
|
|
|
|
|
|
|
|
|||||||||||||||||||
|
|
|
|
2r |
|
|
|
|
|
|
|
|
|
|
|
|
|
|
|
|
|
|
|
|
|
|
|
|
|||||||||||
Rz r(1 cos 1) Sф sin 1 cos 1 sin 1 |
|
|
|
|
|
|
|
(8) |
|||||||||||||||||||||||||||||||
|
Sф sin 1(2r STM sin 1) |
||||||||||||||||||||||||||||||||||||||
если φ≥arcsin |
S |
|
; φ1≤arcsin |
S |
|
|
|
|
|
|
|
|
|
|
|
|
|
|
|
|
|
|
|
|
|
||||||||||||||
|
|
2r |
|
|
|
|
|
|
|
|
|
|
|
|
|
|
|
|
|
|
|
|
|
||||||||||||||||
|
|
2r |
|
|
|
|
|
|
|
|
|
|
|
|
|
|
|
|
|
|
|
|
|
|
|
|
|
|
|
|
|||||||||
|
Rz r(1 cos 1) Sф sin cos sin |
|
|
|
(9) |
||||||||||||||||||||||||||||||||||
Sф sin (2r STM sin ) |
|||||||||||||||||||||||||||||||||||||||
если φ≤ arcsin |
S |
; φ1 ≥ arcsin |
S |
|
|
|
|
|
|
|
|
|
|
|
|
|
|
|
|
|
|||||||||||||||||||
|
|
2r |
|
|
|
|
|
|
|
|
|
|
|
|
|
|
|
|
|||||||||||||||||||||
|
|
|
2r |
|
|
|
|
|
|
|
|
|
|
|
|
|
|
|
|
|
|
|
|
|
|
|
|
|
|
|
|||||||||
|
|
|
|
|
|
|
|
|
|
|
|
|
|
|
S |
2 |
|
|
|
|
|
|
|
|
|
|
|
|
|
|
|
|
|
|
(10) |
||||
|
|
|
|
|
|
|
|
|
|
|
|
Rz |
|
|
|
|
ф |
|
|
|
|
|
|
|
|
|
|
|
|
|
|
|
|
||||||
|
|
|
|
|
|
|
|
|
|
|
|
|
8r |
|
|
|
|
|
|
|
|
|
|
|
|
|
|
|
|||||||||||
|
|
|
|
|
|
|
|
|
|
|
|
|
|
|
|
|
|
|
|
|
|
|
|
|
|
|
|
|
|
|
|
||||||||
если φ≥arcsin |
S |
|
; φ1 ≥ arcsin |
|
S |
|
|
|
|
|
|
|
|
|
|
|
|
|
|
|
|
|
|||||||||||||||||
|
2r |
|
|
|
|
|
|
|
|
|
|
|
|
|
|
|
|
||||||||||||||||||||||
|
|
2r |
|
|
|
|
|
|
|
|
|
|
|
|
|
|
|
|
|
|
|
|
|
|
|
|
|
||||||||||||
Значение Sф определяется по формуле |
|
|
|
|
|
|
|
|
|
|
|
|
|
|
|||||||||||||||||||||||||
Sф |
|
|
|
|
|
|
|
|
|
1 |
|
|
|
|
a10,125b10,7c 10,1a0,43 |
|
|
|
|
|
|||||||||||||||||||
|
|
|
|
|
|
|
|
|
|
|
|
|
|
|
|
|
|
|
|
|
|
|
|
|
|
|
|
|
|||||||||||
|
1 |
|
|
|
|
|
|
|
|
|
|
|
v sin |
0,165 |
|
|
|
|
|
|
|
|
|
||||||||||||||||
|
|
|
|
|
|
|
|
|
|
|
|
|
|
|
|
|
|
|
|
||||||||||||||||||||
|
t p 1 |
|
|
|
|
tg(B ) |
|
|
|
|
|
|
|
|
|
|
|
|
|
|
|
|
|
|
|
|
|
||||||||||||
|
B |
|
|
|
|
|
|
|
|
|
|
|
|
|
|
|
|
|
|
|
|
|
|||||||||||||||||
|
|
|
|
|
|
|
|
|
|
|
|
|
|
|
|
|
|
|
|
|
|
|
|
|
|
|
|||||||||||||
2,85sin0,115 |
v0,57a10,345 b0,3 |
|
0,6625 p a0,57 10,075 0,5 p 1b |
(11) |
|||||||||||||||||||||||||||||||||||
|
|
|
|
|
b (1 sin) x |
|
|
|
|
|
|
|
|
|
|
|
a |
B1 b2 (1 sin) x |
|
|
|
|
|
|
|
|
|
|
|
||||||||||
arccos(1 a |
B |
2 |
|
) |
|
|
|
|
|
|
2 |
|
|
|
|
|
|
|
|
|
|
|
cos |
|
|||||||||||||||
|
|
|
|
|
|
|
|
|
|
|
|
|
|
|
|
|
|||||||||||||||||||||||
|
2 |
|
|
|
|
|
|
|
sin (cos Bsin ) |
|
1 |
|
|
|
|||||||||||||||||||||||||
|
|
|
|
|
|
|
|
|
|
|
|
|
|
|
|
||||||||||||||||||||||||
|
|
|
|
|
|
|
|
|
|
|
|
|
|
|
|
|
|
|
|
|
|
|
|
|
|
|
|
|
|
|
|
|
|
||||||
|
|
|
|
|
|
|
|
|
|
|
|
|
|
|
|
|
|
|
|
|
|
|
|
|
6 |
|
|
|
|
|
|
|
|
|
|
|
|
|
|
гдеφ иφ1 —соответственноглавныйивспомогательныйуглырезцавплане;r— радиус при вершине резца в плане; τp — сопротивление обрабатываемого материала пластическому сдвигу;B=tgβ1 — величина, характеризующая степень пластических деформаций металла снимаемого припуска и поверхностного слоя обрабатываемой детали; β1 — угол наклона условной плоскости сдвига; α и γ — соответственно задний и передний углы резца; a1 и b1 - соответственнотолщинаиширинасреза; cρ— удельная объемная теплоемкость обрабатываемого материала; θ — температура в зоне резания; ρ1 — радиус округления режущей кромки резца; a — температуропроводность обрабатываемого материала; v и t — соответственно скорость и глубина резания; λ и λр — коэффициенты теплопроводности обрабатываемого и инструментального материалов; b — суммарная длина рабочей части режущих кромок; β и ε — соответственно угол заострения и угол при вершинерезцавплане;a2,b2,x —величины,определяемые в зависимости от B; δ
— фаска износа по задней поверхности резца; |
|
|
|
|
|
|
|||||||
|
Физико-механические |
характеристики |
обрабатываемых |
материалов, |
|||||||||
необходимыедлярасчетов,приведенывтабл.4. |
|
|
|
|
|
|
|||||||
|
|
|
|
|
|
|
|
|
|
|
|
Таблица 4 |
|
|
Физико-механические характеристики обрабатываемых материалов |
||||||||||||
|
Обрабатываемый материал |
|
σ |
в |
,MПa |
σ |
,MПa |
τ ,MПa |
θ |
пл |
,0C |
|
|
|
|
|
|
|
т |
|
p |
|
|
|
|
||
|
ВТ9 |
|
1200 |
850 |
350 |
1700 |
|
|
|||||
|
ХН73МБТЮ |
|
1200 |
800 |
800 |
1450 |
|
|
|||||
|
Л62 |
|
360 |
110 |
228 |
905 |
|
|
|
||||
|
ЛС59-1 |
|
370 |
140 |
147 |
900 |
|
|
|
||||
|
АК7ч |
|
200 |
110 |
90 |
700 |
|
|
|
||||
|
Д16Т |
|
530 |
390 |
130 |
780 |
|
|
|
||||
|
МА2-1 |
|
270 |
160 |
73 |
630 |
|
|
|
||||
|
МЛ5 |
|
220 |
80 |
100 |
750 |
|
|
|
Формулы (7)—(11) устанавливают зависимость высоты неровностей обработанной поверхности от параметров, характеризующих процесс резания. Для конкретного сочетания обрабатываемого и инструментального материалов с общепринятой геометрией инструмента установлены упрощенные зависимости, учитывающие основные параметры процесса резания. Так, при чистовом точении, когда резание происходит только радиусной частью резца, высота неровностей может бытьопределенапоформуле
Rz |
|
сS |
X1 |
|
,мкм |
(12) |
|
|
|||||
Y |
Z |
|
||||
|
|
r 1 1 |
1 |
|
|
где S, мм/об; r, мм; ρ1, мкм; с, X1, Y1, Z1 - константы, зависящиеот сочетания обрабатываемого и инструментального материалов, а также от геометрии инструмента. При обработке резцом из ВК8значения констант могут быть взяты из табл. 5.
7

Другиепараметрышероховатостидляусловийлезвийнойобработки могут быть выраженычерезRzпоизвестнымзависимостям (табл.6).
Таблица 5
Значения коэффициентов в формуле (12)
Обрабатываемый материал |
c |
X1 |
Y1 |
Z1 |
ВТ9 |
4865 |
1,71 |
1,1 |
0,96 |
ХН73МБТЮ |
1016 |
1,42 |
1,0 |
0,85 |
Л62 |
608 |
1,58 |
1,04 |
0,95 |
ЛС59-1 |
123 |
1,64 |
0,94 |
0,93 |
АК7ч |
242 |
1,37 |
0,95 |
0,79 |
Д16Т |
82 |
1,23 |
1,07 |
1,07 |
МА2-1 |
125 |
2,04 |
1,54 |
1,44 |
МЛ5 |
146 |
1,66 |
1,25 |
1,05 |
Оптимальная скорость резания, при которой справедливо уравнение (12), может
бытьопределенапоследующейформуле: |
|
|
|
|
|
|
|
|
|
|
|
|
|
|
|
|
|
|
|
|
|
|
V |
сv |
|
, |
|
|
|
|
|
|
|
(13) |
|||
|
|
|
|
Sxv |
|
|
|
|
|
|
||||||||
|
|
|
|
0 |
|
|
|
|
|
|
|
|
|
|
|
|||
гдеS—подача,мм/об. |
|
|
|
|
|
|
|
|
|
|
|
|
|
|
|
|
|
|
Взаимосвязь параметров шероховатости |
Таблица 6 |
|||||||||||||||||
|
|
|
||||||||||||||||
Параметр шероховатости |
Выражениечерез другие параметры |
|
|
|
||||||||||||||
Rmax |
R |
max |
6R |
|
|
|
|
|
|
|
|
|
|
|||||
|
|
|
|
a |
|
|
|
|
|
|
|
|
|
|
||||
Ra |
Ra |
0,21Rz1,02 |
|
|
|
|
|
|
||||||||||
Sm |
Sm 2 |
|
|
|
|
|
|
приS 2rsin 1 |
|
|
|
|||||||
Rz(2r Rz) |
|
|
|
|||||||||||||||
|
|
|
|
|
|
|
|
|
|
|
|
|
|
r(1 cos 1) 0,5Rz |
|
|
||
|
S |
m |
2rsin arctg |
|
Rzctg |
|||||||||||||
|
|
|
||||||||||||||||
|
|
|
|
|
|
|
|
1 |
|
|
|
|
rsin 1 |
|
1 |
|||
|
|
|
|
|
|
|
|
|
|
|
|
|
|
|
|
|
|
|
|
при 2rsin 1 |
|
|
|
|
1 cos( ) |
|
|
|
|||||||||
|
S r |
|
|
1 |
|
|
|
|||||||||||
|
|
|
sin 1 |
|
|
|||||||||||||
|
|
|
|
|
|
|
|
|
|
|
|
|
|
|
|
|
|
|
|
S |
m |
|
2r(1 cos 1) |
0,5Rz(ctg 3ctg ) |
|
|
|||||||||||
|
|
|
|
|
||||||||||||||
|
|
|
|
|
sin 1 |
|
|
|
1 |
|
|
|||||||
|
|
|
|
|
|
|
|
|
|
|
|
|||||||
|
|
|
|
|
|
|
|
|
|
|
|
|
|
|
|
|
||
|
|
|
|
|
|
|
1 cos( ) |
|
|
|
|
|||||||
|
при S r |
|
|
|
|
|
|
1 |
|
|
|
|
||||||
|
|
|
sin 1 |
|
|
|
|
|
||||||||||
|
|
|
|
|
|
|
|
|
|
|
|
|
|
Значения cV и xV при обработке резцом из ВК8, глубине резания t = 1 мм и заданныхгеометрическихпараметрахинструментаприведенывтабл.7.
8
|
|
|
Таблица 7 |
|
Значения коэффициентов в формуле (13) |
||
Обрабатываемый |
СV |
ХV |
Геометрические параметры резца |
материал |
|
|
|
|
|
|
|
ВТ9 |
0,37 |
0,48 |
α=10о; γ=0о; φ=45о; φ =15о; r=1 мм |
|
|
|
1 |
ХН73МБТЮ |
0,35 |
0,38 |
α =12о; γ =12о; φ =45о; φ =45о; r=1 мм |
|
|
|
1 |
Л62 |
1,65 |
0,45 |
α =10о; γ =0о; φ =45о; φ =15о; r=1 мм |
|
|
|
1 |
ЛС59-1 |
0,58 |
0,67 |
α =10о; γ =0о; φ =45о; φ =15о; r=1 мм |
|
|
|
1 |
АК7ч |
4,00 |
0,40 |
α =10о; γ =0о; φ =45о; φ =15о; r=1 мм |
|
|
|
1 |
Д16Т |
3,29 |
0,31 |
α =10о; γ =0о; φ =45о; φ =20о; r=1 мм |
|
|
|
1 |
МА2-1 |
3,30 |
0,38 |
α =10о; γ =0о; φ =45о; φ =15о; r=1 мм |
|
|
|
1 |
МЛ5 |
3,10 |
0,42 |
α =10о; γ =0о; φ =45о; φ =15о; r=1 мм |
|
|
|
1 |
Содержание самостоятельной работы
1.Для заданного преподавателем варианта (табл. 8) определить значения параметров шероховатости Rz, Ra, Rmax, Sm при токарной обработке резцом из ВК8 двух деталей из разных материалов. В расчетах принять ρ = 30 мкм и r = 1 мм. Параметрышероховатости должны быть рассчитаны для каждого значения подачи.
2.Определить оптимальную скорость резания vо, при которой будет обеспечено
получение данных значений параметров шероховатости.
3.Построитьграфикзависимостиоптимальнойскоростирезанияvо отподачиS.
4.Построить график зависимости параметров шероховатости Rz, Ra, Rmax,Sm отподачиS.
5.Сделать выводы о влиянии режима резания и свойств обрабатываемых материаловнапараметры шероховатостипримеханической обработке.
Таблица 8
Варианты заданий для самостоятельной работы
Номер |
Обрабатываемый материал |
Значениеподач,мм/об |
варианта |
|
|
1 |
ВТ9 |
0,1;0,15;0,2;0,25 |
|
МА2-1 |
0,1;0,2;0,3;0,4;0,5 |
2 |
Л62 |
0,15;0,2;0,3;0,4 |
|
Д16Т |
0,1;0,2;0,3;0,4;0,5 |
3 |
ЛС59-1 |
0,1;0,2;0,3;0,4 |
|
МА2-1 |
0,1;0,2;0,3;0,4;0,5 |
4 |
ЛС59-1 |
0,1;0,2;0,3;0,4;0,5 |
|
МА2-1 |
0,1;0,2;0,3;0,4;0,5 |
5 |
ХН73МБТЮ (ЭИ698) |
0,1;0,15;0,2;0,25 |
|
Л62 |
0,1;0,2;0,3;0,4 |
6 |
ВТ9 ХН73МБТЮ |
0,15;0,2;0,3;0,4 |
|
(ЭИ698) |
0,1;0,15;0,2;0,25 |
|
|
9 |
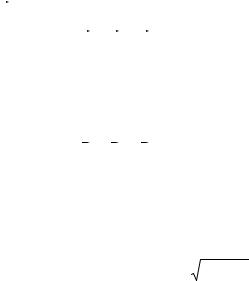
Окончание табл. 8
7 |
ВТ9 |
0,1; |
0,2; |
0,3; |
0,4;0,5 |
|
МЛ5 |
0,1; |
0,2; |
0,3; |
0,4;0,5 |
8 |
ХН73МБТЮ (ЭИ698) |
0,1; |
0,2; |
0,3; |
0,4; |
|
МА2-1 |
0,1; |
0,2; |
0,3; |
0,4; |
9 |
Л62 |
0,1; |
0,2; |
0,3; |
0,4; |
|
ЛС59-1 |
0,1; |
0,2; |
0,3; |
0,4;0,5 |
10 |
АК7ч |
0,1; |
0,2; |
0,3; |
0,4; |
|
Д16Т |
0,1; |
0,2; |
0,3; |
0,4;0,5 |
11 |
ЛС59-1 |
0,1; |
0,2; |
0,3; |
0,4; |
|
АК7ч |
0,1; |
0,2; |
0,3; |
0,4;0,5 |
12 |
ВТ9 |
0,1; |
0,2; |
0,3; |
0,4; |
|
АК7ч |
0,1; |
0,2; |
0,3; |
0,4;0,5 |
Практическая работа № 2 ТОЧНОСТЬ ОБРАБОТКИ
Цель работы: получение представления о причинах возникновения погрешностей обработки и способах их расчета.
Под точностью обработки понимают степень соответствия изготовленной детали требованиям чертежа и технических условий.
Погрешность установки является одной из величин, составляющих общую погрешность обработки. Эта погрешность в общем случае определяется векторной суммойпогрешностейбазированияεб изакрепленияεз:
εу =εб +εз. |
(1) |
При обработке плоских поверхностей векторы погрешностей базирования и закрепления направлены в одну сторону, поэтому погрешность установки определяется по следующей формуле:
εу =εб +εз. |
(2) |
При обработке тел вращения векторы погрешностей направлены под разными углами и погрешность установки можно принять по наиболее вероятному значению, равному
у |
|
б2 з2 , |
(3) |
Дляоценкивеличинвозникающихдеформацийиспользуютпонятиежесткости. Жесткость j — способность системы противостоять действию силы. Наибольшую деформацию при обработке деталей точением вызывает радиальная составляющая силы резания Ру, поэтому
10