
Учебное пособие 782
.pdf
Для получения окончательного изображения выполнить рен-
деринг.
Воронежский государственный технический университет
УДК 681.3: 621.9.042
ТРЕХМЕРНОЙ ОПИСАНИЕ ШЕРОХОВАТОСТИ ОБРАБОТАННОЙ ПОВЕРХНОСТИ С ПОМОЩЬЮ OPENGL
Е.Д. Федорков, Ю.С. Скрипченко, И.Ю. Скрипченко
Качественный и комплексный анализ обработанной поверхности сложный процесс, который обусловлен прежде всего особенностью процесса обработки. Микрогеометрия обработанной поверхности отличается случайным характером. Поэтому анализ поверхностей необходимо проводить с использованием математического аппарата теории случайных функций и планирования многофакторного эксперимента. Такой подход позволяет "учесть" случайные и периодические составляющие профиля обработанной поверхности.
Для того, что бы отобразить шероховатость поверхности с применением графической библиотеки написана программа c ис-
пользованием OpenGL (GL/gl.h, GL/glu.h, GL/glaux.h) и функций (void myinit(void), void CALLBACK display(void), void CALLBACK myReshape(GLsizei w, GLsizei h)). В программе описываются основ-
ные данный точек (количество, координаты и номера вершин). Входными данными являются трехмерный массив ctlpoints. Можно задавать различное число узлов(knots) при этом массив увеличивать до любых размеров, данные массива – высоты.
Алгоритм программы приведен ниже: -Инициализация параметров OpenGL.
-Установление параметров материала поверхности и др. -Создание объекта NURBS.
-Заполнение объекта информацией. -Отображение поверхности.
-Вывод поверхности на экран и отображение поверхности.
Данный фрагмент программы показывает реализацию алгоритма построения поверхности, что позволяет достаточно быстро и легко описать шероховатую поверхность по ее высотам.
Воронежский государственный технический университет
УДК 621.9.025
ПРОГРАММНОЕ ОБЕСПЕЧЕНИЕ ПРИ ПРОЕКТИРОВАНИИ АВТОМАТИЗИРОВАННОЙ СКЛАДСКОЙ СИСТЕМЫ
Ю.С. Скрипченко, Н.Ю. Скрипченко
Складские системы предприятий играют важную роль в производственном процессе производства и поддерживают ритм работы предприятия. Трудности при проектировании складских систем возникают вследствие многовариантности технических решений и постоянной изменяемости складов в процессе работы.
Склад штучных грузов относится к сложным вероятностным системам по устройству и числу входящих элементов и параметров. Прибытие и отправление грузов со склада представляют собой случайный процесс по своей природе и могут быть достаточно точно описаны с помощью известных методов математической статистики и теории вероятностей.
Программа расчета основных параметров складского комплекса разработана для операционных систем Windows 9х. Программные модули осуществляют выделение памяти, загрузку экранных форм и окон диалога для ввода исходных данных, количества групп грузов и высоты зоны хранения, норм запаса хранения, годового запаса хранения, связи с базой данных, в которой хранится информация о параметрах тары, складского оборудования, осуществляет координацию по работе прикладных модулей, осуществляется запуск приложений.
Алгоритм программы расчета параметров складского комплекса представляет собой следующую последовательность:
-формирование данных в таблицах по таре и оборудованию складского комплекса;
-определения типа и количества транспортно складской тары. Входные данные параметры тары и типичного представителя группы грузов длина, ширина, высота.
В качестве результатов определяются следующие параметры тары (тип и размеры), стеллажа (число ячеек, высота яруса и зоны хранения и др.), крана-штабелера.
Воронежский государственный технический университет
УДК 681.3
ВНЕДРЕНИЕ ИНФОРМАЦИОННЫХ ТЕХНОЛОГИЙ В СИСТЕМУ УПРАВЛЕНИЯ ПРЕДПРИЯТИЕМ
Е.Д.Федорков,М.В.Зюзина
Внедрение Интегрированной Информационной Системы Управления Предприятием – задача, которая стоит перед руководителями многих российских компаний и не имеет простого и ясного решения. Сегодняшняя ситуация на рынке консалтинга характеризуется двумя особенностями: с одной стороны, достаточно много предложений по разработке и внедрению решений класса ERP (Enterprise Resource Planning), с другой – практически отсутствует положительный опыт их успешной реализации.
По опыту российских аналитиков, в большинстве случаев выявляются следующие основные проблемы при внедрении систем управления:
1.отсутствие постановки задачи менеджмента на предприятии;
2.необходимость в частичной или полной реорганизации структуры;
3.необходимость изменения технологии бизнеса в различных аспектах;
4.сопротивление сотрудников;
5.временное увеличение нагрузки во время внедрения систе-
мы;
6. отсутствие лидера и квалифицированной команды для ее внедрения.
Системный подход позволяет представить организацию как сложную открытую социальную систему - механизм, берущий элементы входа из внешнего по отношению к организации окружения и подвергающий их различным преобразованиям, в результате чего получаются элементы выхода.
Организации, представленные в виде систем, состоят из взаимозависимых составных частей: задачи, структуры и системы, культура, люди. Таким образом, внедрение информационной технологии, являясь частью элемента «структуры и системы», может рассматриваться только с учетом его взаимного влияния на другие составляющие системы.
В рамках системного подхода существуют различные методики проведения изменений, в зависимости от характеристик ситуации. Предварительная диагностика, с целью выявления признаков мягкой или жесткой, ограниченной или неограниченной ситуации изменения, может определить правильный выбор методики проведения изменений и, соответственно, успех всего мероприятия.
Организация – это система процессов, в которые вовлечены материальные, финансовые, кадровые, информационные и прочие виды ресурсов, и, соответственно, процессное описание компании – это первых шаг на этапе проектирования и внедрения информационной системы управления.
Анализ деятельности и последующее моделирование бизнес - процессов – необходимое условие для эффективного внедрения IT-решения.
Разработка и внедрения решения с применением информационных технологий – процесс итерационный и требует постоянной корректировки, поэтому компания должна быть обеспечена соответствующими ресурсами: персонал (знание и навыки), инструментарий (методики и программное обеспечение), информация (внешнее и внутреннее окружение, потребители, поставщики, конкуренты).
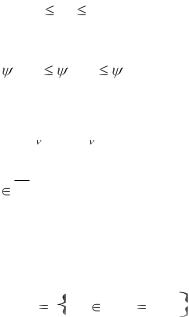
Литература:
1.Курс Открытого Университета (Великобритания) BZR751 “Управление развитием и изменением”, МИМ ЛИНК, 2000г
Воронежский государственный технический университет
УДК 681.3
АЛГОРИТМ ОПРЕДЕЛЕНИЯ И ВЫБОРА ОПТИМАЛЬНОГО ВАРИАНТА ПРОЕКТНОГО РЕШЕНИЯ
Н.Н. Свиридова, В.В. Свиридова
Пусть математическая модель объекта проектирования задана
изависит от n варьируемых параметров x1, x2, … , xn. Такими параметрами могут быть характеристики станков, стоимостные величины
ит.п. В процессе проектирования вводятся следующие ограничения: а) параметрические
x*j x j x*j* |
(1) |
б) функциональные
* |
(x) |
j (x) |
** |
j |
j |
в) критериальные
f (x) f ** (x)
(x) (2)
(3)
где ψ j (x) – некоторые функции от параметров; fv**(x) - худшее
значение критерия ƒv(x), которое проектировщик считает приемлемым, v 1,l.
В данном случае предполагается, что все критерии желательно минимизировать. Ограничения (2), (3) выделяют некоторую область G в пространстве параметров, где каждому i-му значению параметров и структуры проектируемого объекта соответствует своя точка
здесь N – количество точек варьируемых в области G.
xi xi |
|
|
|
|
|
; j 1, n;i 1, N , |
|||||
j |
|
|
|
|
|
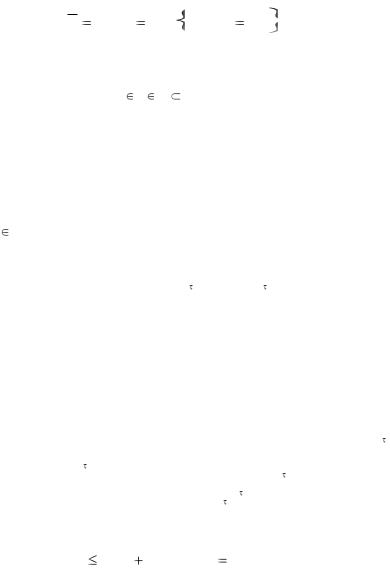
Качество проектируемого объекта в каждой точке оценивается с помощью вектора:
|
ˆ |
ˆ |
i |
|
opt fv (xˆ |
i |
|
|
|
|
) |
); v 1,3 (5) |
|||||||
F |
F (xˆ |
|
|
Задача оптимального проектирования состоит в том, чтобы выбрать такую точку xˆ i x D G, которая минимизирует (максимизирует) совокупность целевых функций {fv(xi)} при наиболее предпочтительном соотношении между их значениями в точке решения, то есть
opt – оператор, определяющий принципы оптимальности путем выбора управляющих стратегий в интерактивном режиме;
D – набор допустимых точек, которые удовлетворяют всем видам ограничений (1)-(3).
D – набор паретовских точек, для которых значения всех критериев не могут быть улучшены одновременно.
Наша задача является многокритериальной и на основе этого методом решения задачи выбран ЛП -поиск. ЛП -поиск заключается
вматематическом просмотре областей, где в качестве пробных точек
впространстве параметров используются точки равномерно-
распределенных последовательностей.Рассмотрим произвольную последовательность точек Р0, Р1, … , Рi принадлежащих Kn (n- мерный куб). Пусть множество членов Рi - двоичный участок этой последовательности. Назовем двумерными отрезками все отрезки которые могут быть получены при делении отрезка на 2m равных частей удовлетворяющих неравенству
Последовательность точек Р0, Р1 куба К называется ЛП - последовательностью, если любой ее двоичный участок, содержащий не менее чем 2 +1 точек представляет собой П -сетку (сетка состоящая из N=2 точек куба Kn называется П -сеткой), если каждому второму параметру Пn с объектом VnK=2 /N принадлежит 2 точек сетки.
K 2s i2 (K S )2s , (K 0,1).
Воронежский государственный
технический университет ВНИИС
УДК 681.3
АВТОМАТИЗИРОВАННАЯ ПОДСИСТЕМА РАСЧЕТА КОЛИЧЕСТВЕННОГО СОСТАВА ОБОРУДОВАНИЯ
ДЛЯ ГИБКОЙ ПРОИЗВОДСТВЕННОЙ СИСТЕМЫ
О.В. Собенина, В.В. Мирошниченко
Задача расчета количественного состава ставится как задача определения количества единиц оборудования в группах, отвечающих позициям обработки. При выборе количественного состава оборудования исходными данными являются параметры технологического процесса, общее количество позиций обработки и типаж технологического оборудования.
Для решения задачи используются уравнения баланса межгруппового обмена продукцией с учетом времени обработки на позициях участка, заданных потоков обрабатываемых изделий между различными группами оборудования, требуемой производительности участка, заданных рабочих площадей и обобщенных стоимостей, выделяемых на оборудование и его установку. Затем вводятся ограничения на допустимый разбаланс оборудования в группах. Эти условия соответствуют ограничениям на взаимно обусловленные простои оборудования при рассогласовании требований различных потоков обрабатываемых изделий, а также рассматривается дополнительный критерий – время, необходимое на переналадку оборудования при переходе от одной модификации к другим. На основании введенных ограничений строится математическая модель задачи, которая представляется собой задачу линейного программирования. Для решения поставленной задачи используется симплекс-метод.
На основании математического аппарата разработаны алгоритмы, которые реализованы в виде программного средства «Расчет количественного состава оборудования». Разработка программного средства осуществлялась в среде программирования Delphi 5.
Программное средство реализовано на языке высокого уровня и требует определенных машинных ресурсов. Необходимые системные требования:
- IBM PC совместимый компьютер с процессором
Pentium 100;
-объем оперативной памяти не менее 16 Мбайт;
-свободное место на жестком носителе (HDD) - 1 Мбайт для размещения программных модулей;
-SVGA – адаптер, поддерживающий область экрана 800 на 600 точек;
-объем видеопамяти не менее 1 Мбайта;
-манипулятор «мышь» для упрощения работы с интерфейсом программы.
Подсистема выполняет следующие функции:
-накопление информации, поступающей с экрана из матриц смежности технологического маршрута и количества продукции, других данных;
-обработка поступающей информации;
-вывод конечного результата на экран.
Разработанное программное средство работает под управлением 32-разрядных операционных систем Windows95/98/2000/NT. В роли специального программного обеспечения выступает разработанный программный модуль «RKOb», реализующий всю совокупность задач, поставленных перед подсистемой «Расчет количественного состава оборудования».
Созданное программное средство может служить элементом комплекса программ, автоматизирующих расчет и проектирование участков гибкого производства. Программное средство «Расчет количественного состава оборудования» зарегистрировано в государственном фонде алгоритмов и программ Российской Федерации.
Воронежский государственный технический университет
УДК 681.3
БАЗА ДАННЫХ ДЛЯ АВТОМАТИЗИРОВАННОГО ПОИСКА ПО РАЗЛИЧНЫМ КЛАССИФИКАЦОННЫМ ПРИЗНАКАМ МЕТАЛЛОРЕЖУЩЕГО ИНТСТРУМЕНТА
О.В. Собенина, О.Ю. Пьяных, Ю.С. Скрипченко
Стремительный рост технических возможностей современных компьютеров и специального программного обеспечения позволяет автоматизировать процессы проектно-конструкторской деятельности. Одним из таких процессов является поиск по различным классификационным признакам металлорежущего инструмента. Для автоматизации этого процесса предлагается использовать базы данных.
Создание базы данных по классификации резцов упростит процесс поиска и выбора необходимого инструмента для того или иного вида обработки, обеспечит быстрый доступ к данным в таблице. Для создания такой базы данных выбрана СУБД Microsoft Access. Это современное широко используемое приложение, предлагающее широкий диапазон средств для эффективного упрощения информации, основанное на логических отношениях данных и поддерживающее реляционную модель данных.
В данной работе рассмотрены основные этапы проектирования базы данных: изучение и описание рассматриваемой предметной области, выбор СУБД, проектирование концептуальной датологической модели.
Проектирование базы данных начинается с предварительной структуризации предметной области. Для этого выбраны следующие объекты, на основе которых строится база данных: подгруппа резцов, вид резца.
Объекты представляются таблицами. Полями таблицы подгруппы резцов являются: номер, название, описание подгруппы. Для таблицы вид резцов полями являются: номер, название, тип, конструктивные особенности резцов.
При помощи данной базы данных созданы запросы по определению кода, вида необходимого инструмента, а также его конструктивных особенностей.
Воронежский государственный технический университет
СОДЕРЖАНИЕ
Раздел 1. ВОССТАНОВЛЕНИЕ ДЕТАЛЕЙ МАШИН ___________ 3 В. М. Пачевский, Р. В. Струков ВЛИЯНИЕ МЕХАНИЧЕСКОЙ ОБРАБОТКИ НА
ВОССТАНОВЛЕННЫЙ ПОВЕРХНОСТНЫЙ СЛОЙ ___________ 3 В. М. Пачевский, Т. В. Петрова НОВЫЕ МЕТОДЫ ПОВЫШЕНИЯ ИЗНОСОСТОЙКОСТИ
ДЕТАЛЕЙ МАШИН ПОДБОРОМ ОПТИМАЛЬНЫХ РЕНОВАЦИОННЫХ ТЕХНОЛОГИЙ ________________________ 4
В. М. Пачевский, Р. П. Ююкин РОЛЬ ИСПЫТАТЕЛЬНОГО ОБОРУДОВАНИЯ В
РЕНОВАЦИОННЫХ ТЕХНОЛОГИЯХ _______________________ 5
А. В. Шевцов, Р. В. Струков, Т. В. Петрова, Р. П. Ююкин СПОСОБЫ ЭКСПЕРИМЕНТАЛЬНОГО ОПРЕДЕЛЕНИЯ ЭКСПЛУАТАЦИОННЫХ ХАРАКТЕРИСТИК ВОССТАНАВЛИВАЮЩИХ ПОКРЫТИЙ ДЕТАЛЕЙ МАШИН _______________________________________ 6
А. В. Шевцов ПРИМЕНЕНИЕ МЕТОДА КОНЕЧНЫХ ЭЛЕМЕНТОВ
К ОПРЕДЕЛЕНИЮ ПОЛЯ МАГНИТНОГО ИЗНОСА ПОВЕРХНОСТИ ТРЕНИЯ __________________________________ 7
А. В. Шевцов, В. А. Тройных ВЗАИМОСВЯЗЬ РЕНОВАЦИОННЫХ ТЕХНОЛОГИЧЕСКИХ ПРОЦЕССОВ И ЭКСПЛУАТАЦИОННОЙ
НАСЛЕДСТВЕННОСТИ ДЕТАЛЕЙ МАШИН _________________ 8 М. И. Чижов, Е. М. Чижова ПОКАЗАТЕЛИ ГАЛЬВАНОМЕХАНИЧЕСКОГО
ОСАЖДЕНИЯ ____________________________________________10
М. И. Чижов УСТАНОВКА ДЛЯ КОМБИНИРОВАННОГО
ВОССТАНОВЛЕНИЯ ДЕТАЛЕЙ ____________________________11
М. И. Чижов СНИЖЕНИЕ ТРУДОЕМКОСТИ И ЦИКЛА
ИЗГОТОВЛЕНИЯ ДЕТАЛЕЙ ГАЛЬВАНОМЕХАНИЧЕСКИМ ОСАЖДЕНИЕМ ______________12