
Учебное пособие 782
.pdfВЗАИМОСВЯЗЬ РЕНОВАЦИОННЫХ ТЕХНОЛОГИЧЕСКИХ ПРОЦЕССОВ И ЭКСПЛУАТАЦИОННОЙ НАСЛЕДСТВЕННОСТИ ДЕТАЛЕЙ МАШИН
А. В. Шевцов, В. А. Тройных
Как известно, основным критерием целесообразности применения той или иной технологии восстановления изношенной детали, из числа технически применимых, является величина материальных затрат, необходимых для осуществления данного процесса. Восстановление работоспособности детали целесообразно осуществлять с использованием той технологии, которая требует наименьшее количество материальных ресурсов.
Анализируя структуру расходов, возникающих при восстановлении работоспособности деталей, можно сделать вывод, что они образуются суммированием: переменных затрат, являющихся функцией износа и связанных с нанесением слоя материала, восстанавливающего износ поверхностей; постоянных затрат, возникающих при проведении разборочно-сборочных работ, подготовке деталей к восстановлению, последующей механической обработке поверхностей с покрытиями и временном выводе машины из эксплуатации. С одной стороны, очевидно, что переменные затраты на восстановление изношенной детали любым методом зависят от величины ее износа и имеют минимальное значение при минимальном износе детали. Соответствующий период эксплуатации детали до восстановления износа также будет минимальным. Но, с другой стороны, высокая частота проведения разборочно-сборочных работ в итоге может вызвать недопустимо большие ремонтные расходы по прошествии некоторого количества циклов восстановления данной детали. Поэтому, при выборе конкретного технологического процесса восстановления работоспособности детали наряду с себестоимостью восстановления необходимо учитывать величину периода ее эксплуатации, допускаемого данным методом наращивания изношенной поверхности. При этом очевидно, что должно соблюдаться условие минимума суммарных затрат на восстановление детали при максимально возможном периоде ее эксплуатации до восстановления. В связи с этим, представляется целесообразным ввести параметр, равный отношению суммарных затрат на восстановление к периоду непрерывной
эксплуатации детали (машины) до восстановления. Данный параметр, описывающий взаимосвязь между технологическим процессом восстановления изношенной детали (машины) и ее эксплуатационной наследственностью, предлагается назвать плотностью реновационной себестоимости (ПРС).
Очевидно, что, если для данной детали, группы деталей или машины ПРС будет минимально возможной, то на восстановление работоспособности указанных изделий за некоторый, достаточно длительный период эксплуатации будет израсходовано минимально возможное количество средств. Таким образом, имея несколько вариантов технологического процесса восстановления изношенной детали (группы деталей), соответствующих различным величинам ее износа, для практической реализации необходимо выбирать тот, который имеет минимальную ПРС. При этом восстановление работоспособности детали (группы деталей) будет наиболее выгодным экономически.
Воронежский государственный технический университет
УДК 621.357
ПОКАЗАТЕЛИ ГАЛЬВАНОМЕХАНИЧЕСКОГО ОСАЖДЕНИЯ
М.И. Чижов, Е.М. Чижова
СОВМЕЩЕНИЕ ПРОЦЕССА ГАЛЬВАНИЧЕСКОГО ОСАЖДЕНИЯ С МЕХАНИЧЕСКОЙ ОБРАБОТКОЙ ПОЛУЧАЕМЫХ ПОКРЫТИЙ В ПРОЦЕССЕ ЭЛЕКТРОЛИЗА ДАЕТ ВОЗМОЖНОСТЬ УВЕЛИЧИТЬ РАБОЧИЕ ПЛОТНОСТИ ТОКА, ПОВЫШАЯ ТЕМ САМЫМ ПРОИЗВОДИТЕЛЬНОСТЬ ПРОЦЕССА ОСАЖДЕНИЯ.
ПРИ ХРОМИРОВАНИИ В 2-30 РАЗ ПО СРАВНЕНИЮ С ТРАДИЦИОННЫМ ОСАЖДЕНИЕМ, ЖЕЛЕЗНЕНИИ (ОСТАЛИВАНИИ) – 2-50 РАЗ, НИКЕЛИРОВАНИИ – 5-40 РАЗ И Т.Д. ПРИ ЭТОМ ВЫХОД ПО ТОКУ (К.П.Д. ИСПОЛЬЗОВАНИЯ ЭЛЕКТРОЭНЕРГИИ) ПОВЫШАЕТСЯ ПРИ ИСПОЛЬЗОВАНИИ РАЗЛИЧНЫХ МЕТАЛЛОВ ДЛЯ
ОСАЖДЕНИЯ, ИНОГДА ДО 100%. В ОБЫЧНЫХ УСЛОВИЯХ ВЫХОД ПО ТОКУ, НАПРИМЕР ХРОМА, СОСТАВЛЯЕТ 8- 12%.
Микротвердость получаемых покрытий повышается в 1,1-2 раза и более для различных осадков:
хром 9800 МПа без мех. воздействия; 11530 с одновременным мех. воздействием;.
никелевые покрытия 3000 МПа и 6200 МПа соответственно; медные покрытия – микротвердость увеличивается в 2,2 – 2,5
раза.
Износостойкость для основных покрытий повышается, в зависимости от пары, в 1,4 - 50 раз.
Усталостные характеристики деталей с покрытиями также повышаются. Например, усталостная прочность хромированных деталей в малоцикловой области повышается в 1,2 – 1,5 раз, по сравнению с полученными традиционными технологиями.
Шероховатость получаемых покрытий для всех осадков достигает 0,02 мкм и менее при начальной шероховатости 2,5-3,2 мкм.
Это позволяет существенно снизить трудоемкость изготовления деталей.
Применение метода целесообразно 1.При изготовлении новых деталей
2. При ремонте и восстановлении изношенных.
Воронежский государственный технический университет
УДК 621.357
УСТАНОВКА ДЛЯ КОМБИНИРОВАННОГО ВОССТАНОВЛЕНИЯ ДЕТАЛЕЙ
М.И. Чижов
Восстановление сильноизношенных деталей гидравлического оборудования, когда износ штоков и цилиндров достигает нескольких миллиметров на сторону на сегодняшний день является актуальной задачей многих машиностроительных предприятий. При этом, восстанавливая изношенные поверхности деталей, основной слой покрытия рекомендуется наращивать из электролита железнения или
осталивания, затем хромировать на необходимую по техническим условиям толщину. Для реализации предлагаемой технологии с использованием гальванического осаждения с одновременной механической обработкой возможно использование установки с двумя ваннами: ванной осталивания и ванной хромирования.
В этом случае, в соответствии с технологическим процессом, вначале предварительно подготовленные для восстановления детали (очищенные, при необходимости, механически обработанные до необходимой точности и шероховатости поверхности) осталиваются на толщину, задаваемую технологией восстановления. Время обработки может контролироваться либо реле времени, Либо прибором активного контроля толщины покрытия. После завершения первой стадии восстановления осуществляется промывка головки установки с деталью в промежуточной ванне промывки поворотом стойки установки. Далее осуществляется хромирование на толщину, установленную требованиями для изготовления новых деталей, соответственно, в ванне хромирования. Последняя стадия – окончательная промывка восстановленной детали в соответствующей ванне промывки. Компоновка установки представляет собой центральную колонну с четырьмя ваннами, расположенными по окружности вокруг центральной колонны с головкой.
Это позволяет получать значительную экономию материалов и средств за счет непроизводительных затрат. При этом нет необходимости применять механическую обработку восстанавливаемых деталей, так как точность их после гальваномеханического осаждения соответствует 7-9 квалитету..
Воронежский государственный технический университет
УДК 621.357
СНИЖЕНИЕ ТРУДОЕМКОСТИ И ЦИКЛА ИЗГОТОВЛЕНИЯ ДЕТАЛЕЙ ГАЛЬВАНОМЕХАНИЧЕСКИМ ОСАЖДЕНИЕМ
М.И. Чижов
Остаточные напряжения, их величина и знак оказывают большое влияние на эксплуатационные характеристики и надежность работы хромированных деталей. Для большинства тяжелонагруженных деталей машин величина и знак остаточных напряжений являются практически прямыми эксплуатационными показателями. Для устранения вредного влияния хромирования традиционные процессы получения деталей включают в себя многократный низкотемпературный отпуск, значительно удлиняющий цикл их изготовления. Поэтому целью настоящих исследований было изучение влияния низкотемпературного отпуска на характер распределения остаточных напряжений, полученных гальваномеханическим хромировани-
ем.
В результате исследований выявлено, что наличие в основе сжимающих остаточных напряжений перед гальваномеханическим хромированием увеличивает результирующие остаточные напряжения в получаемых покрытиях;
Вместе с тем, низкотемпературный отпуск как перед гальваномеханическим хромированием, так и после него снижает уровень остаточных напряжений в полученных осадках;
Кроме того, получены закономерности изменения остаточных напряжений, возникающих в покрытиях от наличия, либо отсутствия термической обработки получаемых покрытий, что позволяет спроектировать оптимальный технологический процесс, обеспечивающий получение необходимых эксплуатационных и физикомеханических свойств деталей с покрытиями, в частности, отказаться от одного низкотемпературного отпуска, вследствие отсутствия механической обработки получаемых покрытий.
Воронежский государственный технический университет
РАЗДЕЛ 2. ОБОРУДОВАНИЕ МАШИНОСТРОИТЕЛЬНОГО
ПРОИЗВОДСТВА
УДК 621
АВТОМАТИЗИРОВАННЫЙ РАСЧЕТ КООРДИНАТ ШЕСТЕРЕН В МНОГОШПИНДЕЛЬНЫХ ГОЛОВКАХ
А.А. Кривоносов, В.И. Корнеев
ПРИ ПОСТРОЕНИИ МНОГОШПИНДЕЛЬНЫХ ГОЛОВОК ОТВЕТСТВЕННЫМ И ТРУДОЕМКИМ ЯВЛЯЕТСЯ ОПРЕДЕЛЕНИЕ КООРДИНАТ ЦЕНТРА ВЕДУЩЕГО КОЛЕСА, СЦЕПЛЯЮЩЕГОСЯ С ТРЕМЯ ВЕДОМЫМИ, КОТОРЫЕ ПРИВОДЯТ ВО ВРАЩЕНИЕ ШПИНДЕЛИ ГОЛОВОК.
В связи с этим целесообразно составить программу для ЭВМ, позволяющую решить эту задачу для одного из вариантов взаимного расположения ведомых и ведущего колеса.
Для решения данной задачи разработана программа в среде DELPHI 5.0, которая состоит из одного исполняемого файла Calculate.exe. Для использования программы необходим IBMсовместимый компьютер. Программа функционирует под операционной системой WINDOWS версии 95 и выше. Для выполнения программы требуется 3 Мб оперативной памяти и 1,2 Мб места на жестком диске.
После запуска программы появляется окно, в левом верхнем углу которого помещена схема взаимного расположения ведущего и ведомых колес. В правой верхней части окна имеются поля для ввода исходных данных – четыре для ввода координат, и одно для ввода передаточного отношения многошпиндельной головки. Далее необходимо нажать кнопку «Вычислить». После этого программа производит расчет и помещает результат в поля, расположенные в нижней части окна программы. Данная программа вычисляет координаты ведущего колеса, а также число зубьев ведомых и ведущего колеса. В расчете используется значение модуля, по умолчанию равного 2 мм. При значении модуля, отличном от 2 мм, необходимо нажать
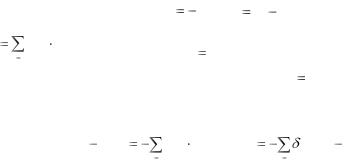
кнопку «Модуль», после чего появляется окошко с полем, в котором можно редактировать значение модуля. Затем необходимо нажать кнопку «Применить» в окошке для ввода значения модуля, и снова нажать кнопку «Вычислить» в главном окне программы. В полях для вывода количества зубьев появятся пересчитанные значения.
Формулы, в соответствии с которыми производится расчет, можно посмотреть, нажав кнопку «Формулы».
Воронежский государственный технический университет
УДК 621.981.216.002
ЗАВИСИМОСТЬ ДИНАМИЧЕСКОГО ПРОГИБА БАЛКИ С ДВУМЯ НАСАЖЕННЫМИ МАССИВНЫМИ ДИСКАМИ ОТ РАБОЧИХ ПАРАМЕТРОВ
Т.А. Сорокина, А.П. Бырдин, А.А. Сидоренко
В работе рассматривается модель расчета прогиба стальной балки, круглого и прямоугольного сечения, с двумя насажанными на нее дисками. Для построения математической модели свободных колебаний балки используется “обратный” метод составления дифференциальных уравнений. Рассматривается безмассовый упругий “скелет “ системы с отделенными грузами, находящийся под дейст-
вием внешних сил P1 |
, P2 и сил инерции (- m1 x1 ) и (- m2 x2 ), |
где x1 |
и x2 - прогибы балки |
в соответствующих точках, а m1 и m2 - |
массы |
дисков. Внешние силы, вызывающие прогибы, уравновешиваются
упругими силами. Поэтому |
F |
F |
* |
F |
P |
m |
x |
|
|
||||||
i |
i |
( |
|
i |
i |
i |
i - внешние силы, |
||||||||
2 |
|
|
|
|
|
|
|
|
|
|
|
|
|
|
|
F * |
C |
|
x |
|
|
|
i |
1, 2 |
|
|
|
|
F * |
|
|
i |
|
i,k |
|
k |
упругие силы, |
). Упругие силы |
выра- |
||||||||
k |
1 |
|
|
- |
|
|
|
i |
|||||||
жаются через коэффициенты жесткости |
|
Ci,k , |
Ci,k |
Ck ,i . |
|
|
|||||||||
|
|
|
|
|
2 |
|
|
|
|
|
|
2 |
|
|
|
Имеем: |
Pi |
mi xi |
Ci,k |
xk |
или |
xi |
|
i,k (Pk |
mk |
xk ) |
|||||
|
k |
1 |
|
|
k 1 |
|
|
, |
|||||||
|
|
|
|
|
|
|
|
|
|
|
|
|
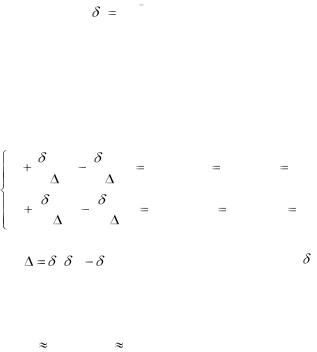
( i =1,2), где |
|
|
|
|
C |
|
1 |
|
|
|
|
|
|||
|
|
|
|
|
|
. |
|
|
|
|
|
|
Математическая модель задачи определяется системой двух уравнений
x |
22 |
|
x |
|
|
12 |
x |
|
|
0, |
x (0) |
x0 , x (0) |
x1 , |
|
||||||||||||||||
|
|
|
|
|
|
|
2 |
|
|
|||||||||||||||||||||
1 |
|
m1 |
1 |
m1 |
|
|
|
|
1 |
|
|
1 |
1 |
|
|
1 |
|
|
|
|
|
|||||||||
|
|
|
|
|
|
|
|
|
|
|
|
|
|
|
|
|
|
|
|
|
|
|
|
|
||||||
x |
12 |
|
x |
|
|
11 |
|
x |
|
0, |
x |
|
(0) |
x0 |
, x |
|
(0) |
|
|
x1 , |
|
|||||||||
|
|
|
|
|
|
|
|
2 |
2 |
2 |
|
|||||||||||||||||||
2 |
|
|
m2 |
1 |
|
m2 |
|
|
|
|
|
|
2 |
|
|
2 |
|
|
|
|
|
|||||||||
|
|
|
|
|
|
|
|
|
|
|
|
|
|
|
|
|
|
|
|
|
|
|
|
|
|
|
||||
|
|
|
|
|
|
|
|
2 |
|
|
|
|
|
|
|
|
|
|
|
|
|
|
|
|
|
|
|
|
|
|
|
|
|
|
|
|
|
|
|
|
|
|
|
|
|
|
|
|
|
|
|
|
|
|
|
|
|
|
|
|
|
где |
11 |
22 |
|
|
12 |
- |
|
определитель матрицы |
|
|
|
|
|
|
|
|
; |
|
||||||||||||
|
|
|
|
|
|
|
|
|||||||||||||||||||||||
|
x1 (0), x2 (0) |
|
|
, x1 (0), x2 (0) - начальное смещение и скорость |
||||||||||||||||||||||||||
начального смещения соответствующих дисков; |
|
|
|
|
|
|
|
|
|
|
||||||||||||||||||||
Для построения дискретной модели задачи вводим сеточные |
||||||||||||||||||||||||||||||
функции |
X x1 (nh) |
, |
Y x2 |
(nh) |
и аппроксимируем производные их |
|||||||||||||||||||||||||
|
|
|
|
|
|
|
|
|
|
|
||||||||||||||||||||
конечно-разностными отношениями, где h - шаг сетки. |
При |
различных значениях n получаем дискретную трехдиагональную систему уравнений для сеточных функций.
Дискретные модельные уравнения решались методом прогонки. Расчеты были получены при различных значениях параметров балки и массы дисков. Результаты расчетов приведены в таблицах и построены в виде графиков.
Рассмотрено также обобщение модели на случай линейного вязко-упругого материала стержня.
Предложенная модель расчета реализована в виде вычислительной программы на алгоритмическом языке Паскаль, позволяющая в режиме диалога с компьютером получать решение поставленной задачи.
Воронежский государственный технический университет
УДК 621.7.044
ИНЖЕНЕРНЫЙ РАСЧЕТ ПАРАМЕТРОВ
ГИДРАВЛИЧЕСКОГО УДАРА
И. А. Чечета, А. Р. Притчин, В.И. Биркин
В технологии импульсного пластического деформирования металлов и сплавов занимает особое место гидродинамическая штамповка, ориентированная на использование энергии гидравлического удара. Гидравлический удар при этом образуется в результате преобразования кинетической энергии бойка, наносящего удар по жидкости, чаще всего это вода, которая заполняет полость технологического блока.
Совершенствованию гидродинамической штамповки способствуют работы, связанные как с анализом напряженно-деформиро- ванного состояния обрабатываемого материала, так и механизма нагружения заготовки, и технологической оснастки, предопределяющей удар бойка по ограниченному объему жидкости.
Так как процесс гидродинамической штамповки многофакторный, то с целью получать приемлемые для инженерной практики расчетные уравнения формируют ряд упрощающих анализ предположений, среди которых основные: уравнение состояния жидкости линеаризовано; не учитываются силы, вызванные скоростным напором; пренебрегают силами трения жидкости о стенки камеры; не учитывают утечку жидкости сквозь зазоры в технологическом блоке.
На основании получаемых уравнений и экспериментальных работ выявлено, что амплитуда давления в жидкости при прочих равных условиях зависит только от скорости подлѐта бойка к жидкости, а длительность импульса давления зависит только от соотношения массы жидкости и массы бойка. При этом установлено, что, если это соотношение меньше 0.5, то форма импульса очень близка к синусоидальной, и в этом случае допустимо при расчетах не учитывать
волновые явления, сопровождающие процесс гидравлического удара.
В свою очередь, расчеты показывают, что уравнения, получаемые без учета волновых явлений, обеспечивают вычисление основ-
ных параметров гидродинамической штамповки с приемлемой для инженерной практики точностью.
Воронежский государственный технический университет
УДК 621.7.004
ТЕХНОЛОГИЧЕСКИЙ БЛОК ДЛЯ ГИДРОИМПУЛЬСНОЙ ШТАМПОВКИ
И.А.Чечета, А. В. Панин, В.И. Биркин
Вобщем случае установка для гидроимпульсной штамповки, реализующей эффект гидравлического удара, состоит из двух блоков:
а) энергопривод, обеспечивающий бойку требуемую скорость подлета к поверхности жидкости, покрывающей заготовку;
б) технологический блок, в котором на матрице расположена обрабатываемая заготовка, покрытая определенным слоем жидкости.
Конструкция применяемой матрицы всегда ориентирована на конкретную операцию формообразования деталей из трубчатых цилиндрических и конических заготовок, штамповку – вытяжку деталей из плоских заготовок, калибровку, пробивку отверстий и другие операции листовой штамповки.
Вкачестве жидкости, передающей давление от бойка к заготовке, применяют в основном воду. Однако, в ряде случаев технологичнее применять податливые среды типа гидропластов, что облегчает укладку заготовок и удаление готовых изделий, а также исключает коррозию металлической поверхности технологического блока, постоянно контактирующего с передаточной средой. В тоже время замечено, что применение гидропластов зачастую сопряжено с рез-