
Методическое пособие 527
.pdf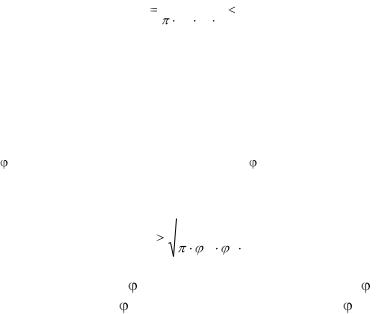
Уточнив геометрические параметры передачи, определяют и проверяют условие (65). Расчет на прочность мальтийского механизма проводят аналогично, рассматривая кривизну замков креста и кривошипа, и выбирая им соответствующие материалы.
5.2. Износостойкость механизма винт–гайка
Расчет сводится к определению фактического среднего контактного напряжения (давления) P между ветками винта и гайки и сравнению его с допускаемым [p]. Условие износостойкости в предложении равномерного распределения нагрузки по виткам резьбы равно:
P |
Fa |
|
|
[ p] , |
(69) |
|
|
|
|||
|
d 2 |
h1 |
z |
|
где d2 и h1 – средний диаметр и рабочая высота профиля резьбы; z – число витков; [p] – допускаемое контактное давление; Fa – осевая сила.
Допускаемые напряжения для пар материалов винт – гайка: закаленная сталь – бронза [p]=10-13 МПа, незакаленная сталь и бронза [p]=8-10 МПа. Для механизмов точных перемещений значение [p] принимает в 2-3 раза меньше, чем для механизмов общего назначения. Заменив в приведенной выше формуле z на h/p2, где р1 – шаг резьбы, h – высота витка и обозначив
H=h/d2 – коэффициент высоты гайки, h=h1/p – коэффициент рабочей высоты профиля резьбы, получим формулу для проектировочного расчета передачи:
d2 |
|
|
Fa |
|
|
. |
(70) |
|
|
|
|||||
|
|
H |
|
h [ p] |
|
Принимают h=0,5 для трапецеидальной и h=0,75 для упорной резьбы, H=1,2+1,25 для целевых гаек и H=2,5+3,5 для разъемных гаек. Длину винта выбирают конструктивно в зависимости от требуемого перемещения l. Наружный диаметр гайки D определяют из условия прочности ее тела на растяжение и кручение:
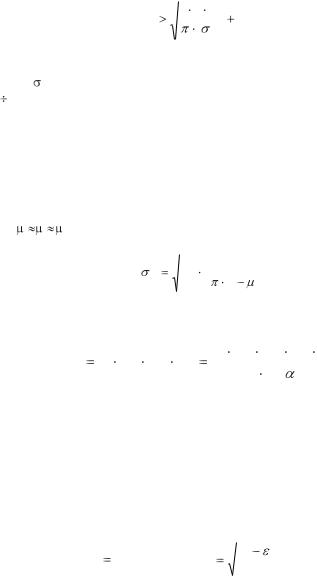
|
|
|
|
|
|
|
D |
4 k |
Fa |
d |
2 , |
(71) |
|
[ |
p ] |
2 |
|
|
||
|
|
|
|
|
где k=1.25 для трапецеидальных и k=1.2 для прямоугольных и метрических резьб; [ p] – допускаемое напряжение на растяжение для бронзы равное
3444 МПа.
5.3.Расчет на прочность цилиндрических и конических зубчатых передач
Определение контактной прочности рабочих поверхностей зубьев производят в полюсе зацеплений П (рис. 9). Контакт зубьев рассматривают
как контакт двух цилиндров с радиусами r1 |
и r2, а формулу (65) записывают в |
||||||||
виде 1 2 : |
|
|
|
|
|
|
|
|
|
|
|
|
|
|
|
|
|
|
|
|
|
q |
|
|
Eпр |
|
, |
(72) |
|
N |
r |
2 |
(1 |
|
2 ) |
|
|
||
|
|
пр |
|
|
|
|
|
|
|
где для прямозубых передач нормальная нагрузка:
|
F |
|
|
F K |
И |
K |
H |
K |
N |
Z 2 |
|
|
q |
|
K |
И KH K N |
t |
|
|
|
, |
(74) |
|||
l |
|
b2 |
cos |
w |
|
|
||||||
|
|
|
|
|
|
|
|
KИ, KH, KN – коэффициенты нагрузки учитывающие соответственно распределение нагрузки между зубьями (для прямозубых KИ = 1), неравномерность распределения нагрузки по ширине зубчатого венца и дополнительные динамические нагрузки; l – суммарная длина контактных линий, зависящая от коэффициентов торцевого перекрытия и ширины венца колес b2 (при однопарном зацеплении) и 2b2 (для двухпарного зацепления).
При расчете l определяют по формуле:
l |
b2 |
, |
где Z |
|
(4 ) |
|
. |
(75) |
|
Z 2 |
3 |
||||||||
|
|
|
|
|
|
|
Приведенный радиус кривизны:
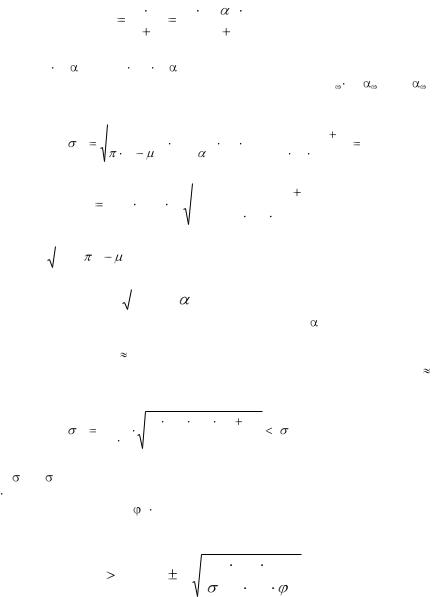
rпр |
r1 |
r2 |
|
d1 sin |
w |
U |
, |
(76) |
r1 |
r2 |
|
2(U |
1) |
|
|||
|
|
|
|
|
где r1=d1/2 sin и r2=d1 U/2 sin
– радиусы эвольвентных профилей зубьев. Подставив значения q и rпр в формулу (72) и заменив sin
cos = sin2 /2 получим:
|
|
Eпр |
|
2 |
|
Z 2 |
F K |
И |
K |
H |
K |
N |
(U 1) |
||
|
|
|
|
|
|
|
t |
|
|
|
|
||||
N |
(1 |
2 ) |
|
sin 2 |
w |
|
|
b |
|
d |
1 |
|
u |
||
|
|
|
|
|
|
|
|
2 |
|
|
|
|
|
|
|
|
Z M |
Z H |
Z |
|
Ft K |
И K H K N (U 1) |
|
, |
(77) |
||||||
|
|
|
|
|
|
|
|
|
|
|
||||||||
|
|
|
|
|
|
|
b2 |
d1 |
u |
|
||||||||
|
|
|
|
|
|
|
|
|
|
|
||||||||
где ZM= E |
пр |
/ |
(1 |
2 ) |
– |
коэффициент, |
учитывающий |
механические |
||||||||||
|
|
|
|
|
|
|
|
|
|
|
|
|
|
|
|
|
|
|
свойства материала сопряженных зубчатых колес, |
для стальных равный |
|||||||||||||||||
ZM=275 H1/2 |
|
|
|
|
|
|
|
|
|
|||||||||
мм, |
ZH= |
|
2 / sin 2 |
w |
– |
коэффициент, |
учитывающий форму |
|||||||||||
|
|
|
|
|
|
|
|
|
|
|
|
|
|
|
|
|
||
сопряженных поверхностей зубьев в полюсе П, |
при |
|
|
w=200, ZH=1,76; Z – |
коэффициент, учитывающий суммарную длину контактных линий, для прямозубых передач Z 0,9.
Учитывая, что Ft=2T2/d2, где d2=2awu/(u+1) и заменив d1=d2/u1, K 1 получим формулу проверочного расчета прямозубых передач:
|
310 |
|
|
T |
K |
K |
|
(U 1) |
3 |
|
(77) |
|
|
|
|
|
2 |
N |
H |
|
[ ], |
||
|
|
|
|
|
|
|
|
|
|||
N |
aw u |
|
|
|
b2 |
|
|
N |
|
||
|
|
|
|
|
|
|
|
||||
где N и [ N] – расчетное и допускаемые контактные напряжения, Н/мм2; Т – |
|||||||||||
Н мм; aw и b2 – мм. |
|
|
|
|
|
|
|
|
|
|
|
Учитывая, что b2= |
ba |
aw, |
получим формулу проектировочного расчета |
||||||||
прямозубых передач: |
|
|
|
|
|
|
|
|
|
aw |
48.5(U 1)3 |
T2 |
|
KN |
|
KH |
|
, |
(78) |
|
[ N |
] |
2 |
U |
2 |
|
|
||||
|
|
|
|
|
ba |
|
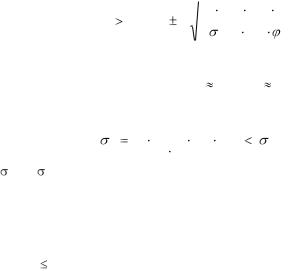
Рассчитанные значения aw (мм) выбирают из ряда: 20; 30; 40; 50; 62; 80; 100; 125; 140; 160; 180; 200; 324; 250; 280; 315; 355; 400 и т.д. (СТ СЭВ
229-75).
Поскольку для зубчатых колес используют не только сталь, но и другие материалы выражение для aw принимает следующий вид:
aw |
0.82(U 1)3 |
|
T2 |
K H |
K N Eпр |
|
, |
(79) |
||
|
|
]2 |
|
|||||||
|
|
|
[ |
N |
U |
2 |
|
|
|
|
|
|
|
|
|
|
ba |
|
где Eпр – приведенный модуль.
Обычно принимают значения KHV 1,25, KHP 1.
Далее, рассматривая зуб как консольную балку, определяют напряжение изгиба в опасном сечении по формуле /1,2/:
|
|
Y |
|
Ft |
|
|
K |
|
K |
|
[ |
|
], |
(80) |
|
f |
f |
|
|
|
f |
fV |
r |
||||||
|
|
b2 |
m |
|
|
|
|
|||||||
|
|
|
|
|
|
|
|
|
|
|
||||
где f и [ |
f] – расчетное |
и допускаемое напряжение |
изгиба, Н/мм; Ft – |
|||||||||||
окружная сила; m – модуль, мм; Yf |
– коэффициент формы зуба, безразмерная |
|||||||||||||
величина, |
зависящая от |
числа |
|
зубьев |
Z; |
Kf, |
KfV |
– коэффициенты, |
учитывающие неравномерность распределения нагрузки по ширине зубчатого венца и дополнительной динамической нагрузки в зацеплении.
При твердости материала хотя бы одного из колес меньше 350 НВ и скорости V 15 м/с, что практически наблюдается для большинства зубчатых передач РЭС, принимают KN=1,0; Kf=1,0; KfV=1,4. Значения для зубчатых колес без смещения равны /7/ (табл. 5).
|
|
|
|
|
|
|
Таблица 5 |
|
|
|
Значения Yf |
|
|
|
|
|
|
|
|
|
|
|
|
Z |
17 |
20 |
22 |
|
24 |
26 |
30 |
Yf |
4,27 |
4,07 |
3,98 |
|
3,92 |
3,88 |
3.8 |
Z |
35 |
40 |
50 |
|
80 |
100 |
>100 |
Yf |
3,75 |
3,7 |
3,65 |
|
3,6 |
3,6 |
3,6 |
Из–за меньшего числа зубьев зуб шестерни у основания более тонкий, чем у колеса, что отражено в большем значении Yf. Для обеспечения примерно равной прочности зубьев шестерки и колеса на изгиб, шестерню делают из более прочного материала, чем колесо. Зубья шестерни и колеса
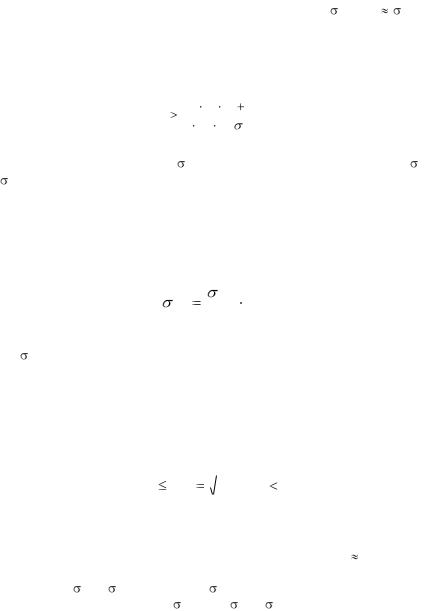
будут иметь примерно равную прочность при условии: [ f]1/ Yf [ f2]/ Yf2. Модуль зубьев m определяют расчетом на изгиб исходя из межосевого расстояния aw, полученного из условия контактной прочности. В этом случае, заменяя Ft=2T2/d2, где d2=2awu/(u+1), получим для модуля следующее выражение:
m |
8,8 |
T2 |
(u |
1) . |
(81) |
|
u |
aw |
b2 [ |
f ] |
|
|
|
|
|
В формулу (81) вместо [ f] подставляют меньшее из значений [ f1] и |
|
[ f2]. Полученное значение модуля округляют в большую сторону |
до |
стандартного. Формула (81) является основной для определения |
m |
прямозубых передач, рассчитываемых на контактную прочность. При этом |
обеспечивается примерно равная контактная и изгибная прочность зубьев.
Допускаемые контактные |
напряжения |
определяют |
по формуле |
||||
(Н/мм2): |
|
|
|
|
|
|
|
[ H ] |
|
HO |
|
KHl |
, |
(82) |
|
[SH ] |
|||||||
|
|
|
|
где HO – предел контактной выносливости рабочих поверхностей зубьев, соответствующий базе испытаний (числу циклов перемены напряжений); [SH]
– допускаемый коэффициент безопасности, равный [SH]=1,1 при однородной структуре материала (нормализация, улучшение, объемная закалка) и [SH]=1,2 при неоднородной структуре (поверхностная закалка, цементация, азотирование); KHl – коэффициент долговечности, учитывающий влияние срока службы и режима нагрузки:
|
|
|
|
|
|
|
1 K |
Hl |
6 N |
HO |
/ N 2,6 , |
||
|
|
|
|
|
где N=60nt – расчетное число циклов нагружения на весь срок службы, n – частота вращения колес (об/мин), t – срок службы (ч).
Обычно при длительной работе передачи выбирают KHl 1. При расчете цилиндрических прямозубых передач в качестве допускаемого контактного напряжения [ H1], [ H2] принимают [ H] того зубчатого колеса, для которого оно меньше, как правило, это [ H2], т.е. [ H]= [ H2]. Допускаемое напряжение изгиба [f], Н/мм2, определяют из соотношения:

[ f ] |
fo |
K fC K fl , |
(83) |
|
|||
|
S f |
|
где fo – предел выносливости зубьев при изгибе, соответствующий базе испытаний; [Sf] – допускаемый коэффициент безопасности, равный [Sf]=1,75 для колес, изготовленных из подковок и штамповок, [Sf]=2,3 из литых заготовок; KfC – коэффициент, учитывающий влияние приложения нагрузки, KfC=1 при одностороннем приложении нагрузки (передача не реверсная) и KfC=0,7 0,8 при двустороннем приложении нагрузки (передача реверсная);
Kfl – |
коэффициент |
долговечности; |
при |
твердости |
350 НВ |
|
|
|
|
|
|
|
|
1 Kfl= |
N fC / N <2,1; |
при твердости |
350 НВ |
его значение |
лежит в |
пределах 1 Kfl 1,63; при длительно работающей передаче выбирают Kfl=1. Пределы контактной и изгибной выносливости зубьев определяют из
табл. 6. |
|
|
|
|
|
|
|
|
|
Таблица 6 |
|
|
Значения |
HO и fo |
|
|
|
|
|
|
|
|
|
Термообработка |
Марка сталей |
|
HO, Н/мм2 |
fo, Н/мм2 |
|
Нормализация, |
35;45; 40X; 40XH; |
|
2HB + 70 |
1,8 HB |
|
Улучшение |
35XH |
|
|
|
|
|
|
|
|
|
|
Закалка ТВЧ по |
40X; 40XH; |
|
17HRCэ +200 |
650 |
|
Контуру зубьев |
35XМ; |
|
|
|
|
|
45XЦ |
|
|
|
|
|
|
|
|
|
|
Закалка ТВЧ |
|
|
|
550 |
|
сквозная (m<3мм). |
|
|
|
|
|
Цементизация и |
20X;20XH2M; |
|
23HRCэ |
300 |
|
закалка. |
18XГТ |
|
|
|
|
|
|
|
|
|
|
Расчет на прочность начинают с выбора материала, условий термообработки и способов изготовления колес, а затем находят [ H1],[ H2], [ f1] [ f2], задаваясь наименьшим [ H] и [ f]
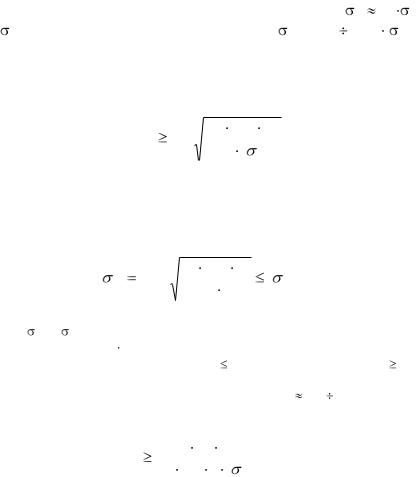
определяют aw и m. Далее, округляя эти значения до стандартных awc и mc рассчитывают и проверяют условия прочности (77) и (80) для стандартных awc и mc. Если условия прочности выполняются, то расчет закончен, если не выполняется, то изменяют материал и условия термообработки. Допускаемые контактные напряжения для колес, изготовленных
из латуней и бронз определяются выражениями [ |
H] 0,9 |
b, где |
b – предел прочности на растяжение и [ f]=(0,20 |
0,25) |
b. |
При проверочном расчете конических прямозубых передач сначала определяют внешний делительный диаметр колеса по формуле /7/:
|
T2 KH U |
|
|||
d12 1653 |
|
|
|
. |
(84) |
0.85 [ |
H |
]2 |
|||
|
|
|
|
|
Значения d12 регламентированы ГОСТ 12289-76. При известном d12 формула проверочного расчета прямозубых конических передач на контактную прочность имеет вид:
|
210 |
T2 |
KH |
U |
[ H |
] , |
(85) |
|
H |
d12 |
|
0.85 d12 |
|||||
|
|
|
|
где [ H] и H – допустимое и расчетное контактное напряжения, Н/мм2; T2 – крутящий момент Н мм, d12 – мм. Коэффициент динамической нагрузки при
твердости поверхности зубьев колеса |
350 НВ равен KHV=1,2 при 650 НВ, |
||||||
значение KHV=1,1. Коэффициент неравномерности распределения нагрузки |
|||||||
по ширине зубчатого венца KH составляет KH 1,01 1,02 /7/. Внешний |
|||||||
окружной модуль определяют расчетом на изгиб по формуле: |
|
||||||
m1 |
|
14 T2 |
Kr |
|
, |
(86) |
|
v f |
d12 b [ |
f ] |
|||||
|
|
|
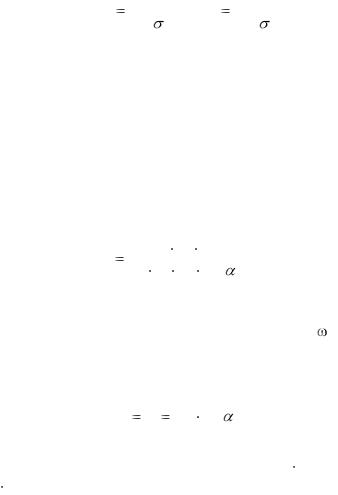
где vf – коэффициент вида конических колес, для прямозубых колес vf=0,85; Kr=1,0 для колес с прямыми зубьями; b – ширина зубчатого венца.
Полученное значение m можно округлить до стандартного. Затем определяется эквивалентное число зубьев шестерни и колеса:
z |
|
z1 |
; |
z |
|
z2 |
э1 |
cos 1 |
э2 |
cos 2 |
|||
|
|
|
|
|
и для них находится коэффициент формы зуба Yf1 и Yf2 (табл.
4).
5.4. Расчет на прочность червячных передач
Расчет на контактную прочность зубьев червячного колеса проводят по аналогии с расчетом зубчатых передач по формуле (72), в которой величина нормальной нагрузки q на единицу длинны контактных линий колеса и червяка равна:
q |
2 T2 |
K |
|
. |
(87) |
|
1,3 d1 |
d2 |
cos |
|
|||
|
w |
|
В осевом сечении витка червяка имеют профиль прямобочной рейки с радиусом кривизны r1= , поэтому приведенный радиус кривизны rпр червячной пары равен кривизны профиля червячного колеса в полюсе зацепления:
r |
r |
d 2 |
sin |
|
. |
(88) |
|
w |
|||||
пр |
2 |
2 |
|
|
|
|
|
|
|
|
|
|
Приведенный модуль упругости Епр=2Е1 Е2/ Е1+Е2, где Е1=2,1 105 Мпа – модуль упругости стального колеса и
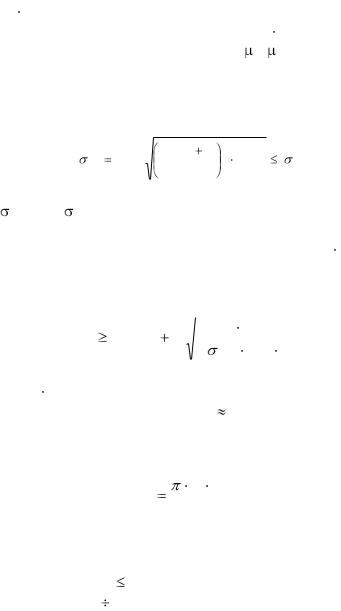
Е2=0,98 105 Мпа – модуль упругости бронзового колеса. В связи с этим приведенный модуль равен Епр=1,33 105 Мпа, принимая коэффициент Пуассона равным 12=0,3. Подставив выражения для q, rпр, Eпр в формулу (72) после преобразования получают формулу проверочного расчета на контактную прочность /7/;
|
170q |
(z2 / q |
1) |
|
3 |
|
|
|
|
|
|
] , |
(89) |
|||
H 2 |
|
|
|
|
|
|
|
T K |
H |
|
[ |
|
H 2 |
|||
|
|
|
|
|
|
|
|
|
||||||||
|
z2 |
aw |
|
|
|
2 |
|
|
|
|
|
|||||
|
|
|
|
|
|
|
|
|
|
|
|
|
||||
где H2 и [ H2] |
– расчетное |
и |
допускаемое |
контактные |
||||||||||||
напряжения в зубьях колес, Н/мм2; aw – межосевое расстояние, |
||||||||||||||||
мм; T2 – вращающий момент на червячном колесе, Н мм. Решив |
||||||||||||||||
это уравнение относительно aw |
|
получаем формулу |
||||||||||||||
проектировочного расчета червячных передач: |
|
|
|
|
||||||||||||
|
|
|
|
|
|
|
|
|
|
|
|
|
|
|
|
|
aw |
30,7(z2 |
q)3 |
|
|
T2 |
KH |
|
|
, |
|
(90) |
|||||
([ |
|
H 2 ] |
z2 ) |
2 |
q |
|
||||||||||
|
|
|
|
|
|
|
|
|
|
|
|
где KH=K KV, величина К – коэффициент концентрации нагрузки, близкой к единице К 1,0; КV – коэффициент динамической нагрузки, зависящий от окружной скорости червячного колеса V2. Окружную скорость V2 рассчитывают по формуле:
V |
n1 d2 |
, |
(91) |
|
|||
2 |
60U |
|
|
|
|
где n1 – частота вращения червяка; U – передаточное число; d2 – делительный диаметр колеса. Для окружной скорости червячного колеса V2 3 м/с принимают КV=1, а при V2>3 м/с принимают КV=1,1 1,3. Далее определяют прочность зубьев червячного колеса на изгиб:
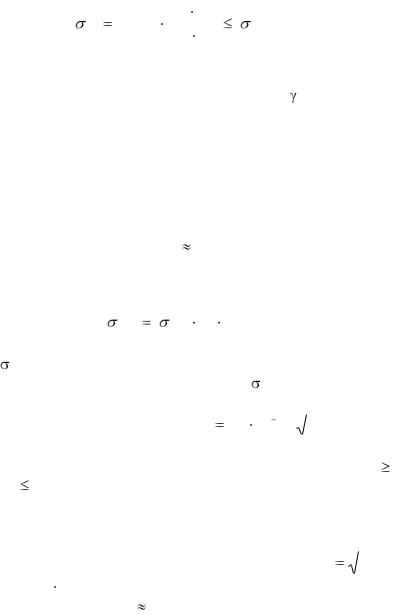
|
0,7Yf 2 |
Ft 2 |
K f |
[ |
f 2 ] , |
(92) |
f 2 |
b2 |
m |
||||
|
|
|
|
|
где коэффициент формы зуба Yf2 выбирают в зависимости от эквивалентного числа зубьев колеса zv2=z2/cos3 :
zv2 |
28 |
30 |
32 |
35 |
37 |
40 |
|
45 |
50 |
60 |
|
80 |
100 |
|
|
|
|
|
|
|
|
|
|
|
|
|
|
|
|
|
|
|
|
|
|
|
|
|
|
|
|
Yf2 |
1,8 |
1,76 |
1,71 |
1,64 |
1,61 |
1,56 |
|
1,48 |
1,45 |
1,4 |
|
1,34 |
1,3 |
|
|
|
|
|
|
|
|
|
|
|
|
|
|
|
|
|
|
|
|
|
|
|
|
|
|
|
|
|
Коэффициент нагрузки Кf |
1,0. |
|
|
|
|
|
|
|
||||
|
Допускаемые контактные напряжения для колес из |
||||||||||||
оловянных бронз (Бр010Ф1 и др.) определяют из условия: |
|
||||||||||||
|
|
|
[ |
H 2 ] |
[ H 0 ] |
Cv |
K Hl , |
|
|
(93) |
|
где [ H0] =0,9b – допускаемое контактное напряжение при числе циклов перемены напряжений NH=107; b – предел прочности бронзы при растяжении; Cv – коэффициент износа зубьев колеса
зависит от скорости скольжения V |
4,3 10 |
4 n 3 |
T |
|
(м/с): |
|
|
|||||||
|
|
|
|
s |
|
|
1 |
2 |
|
|
|
|
|
|
|
|
|
|
|
|
|
|
|
|
|
|
|
|
|
Vs, |
1 |
2 |
3 |
4 |
|
5 |
6 |
|
|
|
7 |
|
8 |
|
м/с… |
|
|
|
|
|
|
|
|
|
|
|
|
|
|
Cv |
1.33 |
1.21 |
1.11 |
1.02 |
|
0.95 |
0.88 |
|
|
0.82 |
|
0.80 |
|
|
|
|
|
|
|
|
|
|
|
|
|
|
|||
|
|
|
|
|||||||||||
KHl – коэффициент долговечности равный KHl |
8 107 / N2 , |
если N2>25 107, то KHl=0,67. Обычно при полном ресурсе службы t=20000 г. n1 100 об/мин, KHl=0,76. Допускаемые