
Методическое пособие 416
.pdf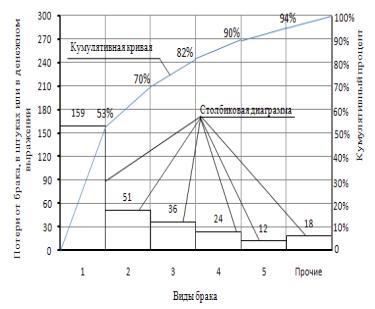
5.Строят одну горизонтальную и две вертикальные оси:
-горизонтальную ось делят на интервалы в соответствии с числом типов (групп) дефектов (ширина интервалов должна быть одинаковой, но ее размер значения не имеет);
-на левую вертикальную ось наносят шкалу с интервалами (делениями) от 0 до числа, соответствующего общей сумме потерь от брака;
-на правую вертикальную ось наносят шкалу с интервалами (делениями) от 0 до 100 %.
При построении вертикальных осей необходимо соблюсти масштаб таким образом, чтобы значение общей суммы потерь от брака (на левой оси) находилось строго на одном уровне со значением 100 % (на правой оси).
6.Строят столбиковую диаграмму, где каждому виду брака (дефекта) соответствует свой прямоугольник, высота которого соответствует величине потери от этого вида брака (столбец 4 таблицы).
7.Строят кумулятивную кривую по данным столбца 6 таблицы. Значения откладывают по правой оси.
8.На диаграмме указывают ее название, период получения данных, наименование видов брака, сумму потерь от каждого вида брака (над соответствующим столбцом), кумулятивный процент (над соответствующей точкой кривой Лоренца).
Пример построения диаграммы Парето приведен на
рис. 5.
Анализ диаграммы Парето проводят с помощью АВС-анализа. Цель анализа: выявить проблемы, подлежащие первоочередному решению, путем определения их приоритетности. Число групп при проведении АВС-анализа может быть любым, но наибольшее распространение получило деление рассматриваемой совокупности на три группы: А, В и С, чем и обусловлено название метода (ABC-Analysis).
Группа А – незначительное число видов дефектов, на долю которых приходятся наибольшие потери. Группа В – средняя по численности группа со средним уровнем суммарных потерь от брака. Группа С – большое число видов брака с незначительной величиной суммарных потерь.
19
Рис. 5. Диаграмма Парето
Экономический смысл АВС-анализа сводится к тому, что максимальный эффект достигается при решении проблем, относящихся к группе А. Графическая интерпретация АВС-анализа представлена на рис. 6.
20
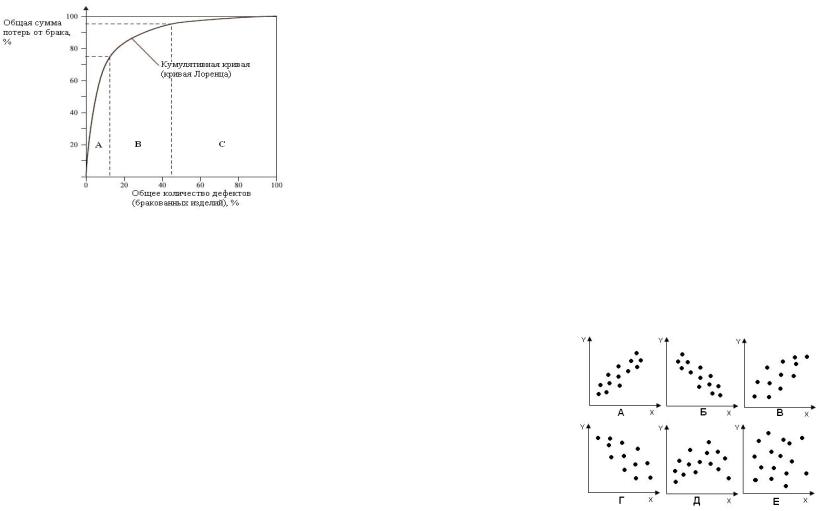
Рис. 6. Графическая интерпретация АВС-анализа
3.6. Диаграмма разброса (рассеивания)
Диаграмма разброса (рассеивания) – это инструмент,
позволяющий определить вид и тесноту связи между парами соответствующих переменных .
Эти две переменные х и у могут относиться:
а) к характеристике качества у и к влияющему на нее фактору х;
б) к двум различным характеристикам качества х и у; в) к двум факторам х и у, влияющим на одну характе-
ристику качества z.
Для выявления связи между ними и служит диаграмма разброса (рассеивания), которую также часто называют полем корреляции.
Этапы построения диаграммы разброса (рассеивания):
1. Соберите парные данные (х и у), между которыми хотите исследовать зависимость. Хорошо иметь, по меньшей мере, 30 пар данных.
21
2.Найдите максимальные и минимальные значения х
и у.
3.Постройте систему координат в таком масштабе, чтобы вертикальная и горизонтальная оси были одинаковой длины (т.е. расстояние от нуля до максимального значения х и у соответственно), тогда диаграмма будет нагляднее. Если одна переменная – фактор, а вторая – характеристика качества, то выберите для фактора горизонтальную ось Х, а для характеристики качества – вертикальную ось Y.
4.Нанесите данные на график.
5.Укажите на диаграмме все необходимые обозначения, например: название диаграммы; период времени сбора данных; число пар данных; названия и единицы измерения для каждой оси; дату составления диаграммы; имя (и прочие данные) человека, который составлял эту диаграмму.
Типичные виды диаграмм разброса (рассеивания) приведены на рис. 7.
Рис. 7. Типичные виды диаграмм разброса : А – сильная положительная корреляция; Б – сильная отрицательная корреляция; В – слабая положительная корреляция; Г – слабая отрицательная корреляция; Д – криволинейная корреляция; Е – отсут-
ствие корреляции
22

Для оценки степени корреляционной зависимости необходимо вычислить коэффициент корреляции по формуле:
r |
|
S(xy) |
|
, |
|
(6) |
|||
|
|
|
|
|
|
||||
|
|
S(xx) S(yy) |
|
||||||
где S(xy) – ковариация; |
|
|
|
|
|
|
|
|
|
S(xx), S(yy) – дисперсии x и y соответственно. |
|
||||||||
Ковариация определяется по формуле: |
|
||||||||
n |
|
|
|
|
|
|
|
|
|
S(xy) (xi |
|
) (yi |
|
|
, |
(7) |
|||
x |
y) |
i 1
где xi и yi – собранные статистические данные;
x и y – средние значения переменных х и у; п – число пар данных.
Дисперсия определяется по формуле (для переменных х и у формулы подобны):
|
|
|
|
n |
2 |
|
|
|
|
||||||
|
|
|
|
S(xx) (xi |
|
|
) |
. |
|
|
(8) |
||||
x |
|||||||||||||||
|
|
|
|
i 1 |
|
|
|
|
|
||||||
Получив коэффициент корреляции можно определить |
|||||||||||||||
тесноту связи между переменными: 0 < |
|
r |
|
|
≤ 0,2 – очень слабая |
||||||||||
|
|
||||||||||||||
корреляция; 0,2 < |
|
r |
|
≤ 0,5 – слабая корреляция; 0,5 < |
|
r |
|
≤ 0,7 – |
|||||||
|
|
|
|
средняя корреляция; 0,7 < r ≤ 0,9 – высокая корреляция; 0,9 <
r ≤ 1 – очень высокая корреляция (зависимость между пере-
менными можно выразить в виде линейной функции).
3.7. Контрольные карты
Все описанные выше статистические методы дают возможность зафиксировать и проанализировать состояние процесса в определенный момент времени. В отличии от них, контрольные карты позволяют отслеживать состояние процесса во времени (в динамике) и более того – воздействовать на процесс
23
до того, как он выйдет из под контроля. Впервые этот инструмент был предложен в 1924 году Уолтером Шухартом.
Контрольные карты – это инструмент, позволяющий отслеживать ход протекания процесса и воздействовать на него (с помощью соответствующего механизма обратной связи), предупреждая отклонения от предъявляемыхк процессутребований.
Существуют следующие виды контрольных карт:
1)средних арифметических значений (X-карта);
2)медиан (X-карта);
3)среднеквадратических отклонений (S-карта);
4)размахов (R-карта);
5)числа дефектных единиц продукции в подгруппе объе-
ма n (np-карта);
6)доли дефектных единиц продукции в подгруппе (р-
карта);
7)числа дефектов в подгруппе (с-карта);
8)числа дефектов, приходящихся на единицу продукции
вподгруппе (u-карта).
Для контроля процессов с высокими требованиями к качеству продукции, особенно в части, связанной с обеспечением безопасности потребителя (производство строительных материалов и конструкций, авиатехника, автомобилестроение и т.д.),
наиболее часто применяют X и R-карты (средних арифметических значений и размахов). Их удобно применять при измерении таких показателей, как длина, масса, диаметр, время, предел прочности на растяжение и т.д.
Этапы построения ( X и R)-карты:
1. Сбор данных. С определенной периодичностью (например, два раза в смену) выполняют измерение 20–25 последовательно изготавливаемых групп изделий (количество групп обозначим, как K), по 4–5 изделий в группе (количество измерений в группе обозначим, как n). Получаем массив данных xi.
24

2.Вычисление средних арифметических значений xk
для каждой k-й группы наблюдаемых значений:
|
|
1 |
n |
|
|
|
xk |
|
xi . |
(9) |
|||
|
||||||
|
|
n i 1 |
|
|
||
|
|
|
|
|
|
3. Вычисление общего среднего значения x по всем имеющимся группам данных:
|
|
1 |
K |
|
|||
|
|
|
|||||
x |
|
|
xk |
. |
(10) |
||
|
|||||||
|
|
K k 1 |
|
4. Вычисление размаха Rk в каждой группе путем вычитания из максимального значения по группе минимальное:
Rk xmax xmin . |
(11) |
5.Вычисление среднего арифметического значения раз-
махов R для всех групп данных:
|
|
|
|
|
|
|
|
1 |
K |
|
|
|
|
|
|
|
|
|||
|
|
|
|
|
|
|
|
Rk . |
|
|
|
(12) |
||||||||
|
|
|
|
|
|
R |
|
|
|
|||||||||||
|
|
|
|
|
|
|
|
|
|
|||||||||||
|
|
|
|
|
|
|
|
K k 1 |
|
|
|
|
|
|
|
|
||||
|
Пример подготовки данных для построения ( |
|
и R)-карты |
|||||||||||||||||
X |
||||||||||||||||||||
приведен в табл. 4. |
|
|
|
|
|
|
|
|
|
|
|
|
|
|
|
Таблица 4 |
||||
|
|
|
|
|
|
|
|
|
|
|
|
|
|
|
|
|
|
|
||
|
|
|
Данные для построения ( |
|
|
и R)-карты |
|
|
|
|
|
|||||||||
|
|
|
X |
|
|
|
|
|
||||||||||||
|
|
|
|
|
|
|
|
|
|
|
|
|
|
|
|
|
|
|
|
|
|
Номер |
|
|
|
|
|
|
5 |
|
|
|
|
|
|
|
|
|
|
|
|
|
х1 |
х2 |
х3 |
х4 |
х5 |
|
xi |
|
|
xk |
|
|
|
Rk |
|
|||||
|
группы |
|
|
|
|
|
|
|
||||||||||||
|
|
|
|
|
|
|
|
i 1 |
|
|
|
|
|
|
|
|
|
|||
|
|
|
|
|
|
|
|
|
|
|
|
|
|
|
|
|
|
|||
|
1 |
47 |
32 |
44 |
35 |
20 |
178 |
|
|
|
35,6 |
|
|
27 |
|
|||||
|
|
|
|
|
|
|
|
|
|
|
|
|
|
|
|
|
|
|
||
|
2 |
19 |
37 |
31 |
25 |
34 |
146 |
|
|
|
29,2 |
|
|
18 |
|
|||||
|
3 |
19 |
11 |
16 |
11 |
44 |
101 |
|
|
|
20,2 |
|
|
33 |
|
|||||
|
|
|
|
|
|
|
|
|
|
|
|
|
|
|
|
|
|
|
||
|
4 |
29 |
29 |
42 |
59 |
38 |
197 |
|
|
|
39,4 |
|
|
30 |
|
|||||
|
|
|
|
|
|
|
|
|
|
|
|
|
|
|
|
|
|
|
||
|
5 |
28 |
12 |
45 |
36 |
25 |
146 |
|
|
|
29,2 |
|
|
33 |
|
|||||
|
|
|
|
|
|
|
|
|
|
|
|
|
|
|
|
|
|
|
||
|
|
|
|
|
|
|
|
|
Итого |
|
153,6 |
|
|
141 |
|
|||||
|
|
|
|
|
Средние значения |
|
|
|
|
|
|
|
= 28,2 |
|
||||||
|
|
|
|
|
x |
= 30,72 |
|
|
R |
|
25
6. Вычисление контрольных линий (границ регулирования и центральной линии). Данный этап является самым важным при разработке контрольных карт. Контрольные линии рассчитываются
для X и R-карт отдельно.
X -карта: Центральная линия CL = x . Верхняя граница регу-
лирования UCL = x +A2 R. Нижняя граница регулирования LCL = x –
A2 R.
R-карта: Центральная линия CL = R . Верхняя граница регу-
лирования UCL = D4 R . Нижняя граница регулирования LCL =
D3 R . В зависимости от количества измерений (n) нижняя граница регулирования может отсутствовать. Константы А2, D4, D3 – коэффициенты, зависящие от количества измерений в группе (n), значения приведены в табл. 5.
7. Нанесение контрольных линий. На листе бумаги в клеточку
нанесите слева вертикальные оси со значениями X и R и горизонтальные оси с номерами групп. Начертите прерывистой линией верхнюю
(USL) и нижнюю (LSL) границы регулирования на X -карте и R-карте. Центральную линию (CL) на обе карты нанесите сплошной линией.
Укажите также на X -карте жирными сплошными линиями значения верхней USL и нижней LSL границ поля допуска (если эти значения имеются).
Коэффициенты для расчета контрольных границ |
Таблица 5 |
||||
|
|
||||
|
|
|
|
|
|
Кол-во измерений в гр. (n) |
А2 |
D3 |
|
D4 |
|
2 |
1,880 |
– |
|
3,267 |
|
3 |
1,023 |
– |
|
2,575 |
|
4 |
0,729 |
– |
|
2,282 |
|
5 |
0,577 |
– |
|
2,115 |
|
6 |
0,483 |
– |
|
2,004 |
|
7 |
0,419 |
0,076 |
|
1,924 |
|
8 |
0,373 |
0,136 |
|
1,864 |
|
9 |
0,337 |
0,184 |
|
1,816 |
|
10 |
0,308 |
0,223 |
|
1,777 |
|
26

8. Нанесение точек. Выберите и разметьте масштабы по осям
X и R, а по каждой горизонтальной оси нанесите номера групп (с интервалом 5 мм). Для удобства дальнейшего одновременного использо-
вания X -карты и R-карты рекомендуется нанести тонкие вертикальные линии для обозначения границ интервалов каждой группы, причем они
должны проходить непрерывно через всю ( X и R)-карту, так, как это показано на рис. 8.
9.Нанесение необходимой информации: объем групп (n = 5)
вверхнем левом углу X-карты; сведения, имеющие отношение к
изучаемому процессу (название процесса и продукции, период времени ведения контрольной карты, метод измерения, смена, сведения о рабочем и т.п.).
Рис. 8. Пример построения ( X и R)-карты
С помощью построенной контрольной карты можно определить контролируем ли протекающий процесс, при этом осуществляется либо простой контроль без вмешательства в ход процесса (когда он идет успешно), либо оказывается воздействие на процесс при отклонении условий протекания от нормальных. Контролируемое состояние процесса – это такое состояние, ко-
гда процесс стабилен и его среднее значение X и разброс R не
27
меняются (остаются близкими к x и R , не выходят за пределы верхней UCL и нижней LCL границ регулирования). Для анализа контрольной карты рекомендуем воспользоваться учебным пособием.
4. НОВЫЕ И НОВЕЙШИЕ ИНСТРУМЕНТЫ УПРАВЛЕНИЯ КАЧЕСТВОМ
4.1. Восемь новыхинструментов управления качеством
Эти новые инструменты управления качеством являются частью методологии решения проблем, рассматриваемой в тео-
рии TQM:
-мозговая атака (штурм) (brainstorming);
-диаграмма сродства (affinity diagram);
-диаграмма (график) связей (interrelationship diagram);
-древовидная диаграмма, дерево решений (tree diagram);
-матричная диаграмма, таблица качества (matrix diagram or quality table);
-стрелочная диаграмма (arrow diagram);
-поточная диаграмма процесса (flow chart) и диаграмма процесса осуществления программы (process decision program chart – PDPC);
-матрица приоритетов (анализ матричных данных) (matrix data analysis).
Наиболее успешно эти инструменты могут быть использованы в рамках групповой работы в командах, создаваемых в организациях для поиска и выработки решения проблем качества.
Матричная диаграмма (таблица качества) – инстру-
мент выявления важности различных связей, выражает соответствие определенных факторов (и явлений) различным причинам их проявления и средствам устранения их последствий, а также
28

показывает степень (силу) зависимости этих факторов от причин их возникновения и/или от мер по их устранению (рис. 9).
А |
|
|
В |
|
|
b1 |
b2 |
|
b3 |
b4 |
|
|
|
||||
a1 |
|
∆ |
|
|
|
a2 |
|
|
|
|
|
a3 |
|
|
|
|
|
a4 |
|
|
|
|
|
Рис. 9. Условный пример матричной диаграммы
Символ, стоящий на пересечении строки и столбца матричной диаграммы, указывает на наличие связи между компонентами и на тесноту этой связи. Степень (сила) взаимосвязи обозначается так (в скобках указан весовой коэффициент):
∆ – слабая связь (1); – средняя связь (3); – сильная связь (9).
A(a1, … a4) – основные причины проблемы, представленные в виде компонентов;
B(b1, … b4) – возможные средства для устранения последствий этих причин.
Если возникает необходимость в более подробном отображении силы связей, используют следующие символы и коэффициенты :
∆ – слабая связь (1);
– существенная связь (3); – средняя связь (9); – сильная связь (16);
– очень сильная связь (25).
Связь между факторами может быть как положительной, так и отрицательной, в этом случае рекомендуется использовать:
– сильная положительная связь (+9);
29
– средняя положительная связь (+3); ∆ – слабая положительная связь (+1); «пусто» – отсутствие связи (0);– слабая отрицательная связь (–1);
– средняя отрицательная связь (–3); – сильная отрицательная связь (–9).
Наибольшее распространение в практике получили матричные диаграммы (по своей компоновке) в виде L-карты, T- карты и X-карты (рис. 10).
|
|
|
|
|
|
|
c5 |
|
|
|
|
|
|
a) |
|
|
|
|
|
б) |
c4 |
|
|
|
|
|
|
|
|
|
|
|
c3 |
|
|
|
|
|
|||
|
|
|
|
|
|
|
c2 |
|
|
|
|
|
|
А |
|
|
B |
|
|
|
c1 |
|
|
|
|
|
|
|
|
|
|
|
b1 |
b2 |
b3 |
b4 |
b5 |
b6 |
|||
b2 |
b3 |
b4 |
b5 |
b6 |
b7 |
||||||||
b1 |
|
|
|
|
|
|
|||||||
a1 |
|
|
|
|
|
|
a1 |
|
|
|
|
|
|
a2 |
|
|
|
|
|
|
a2 |
|
|
|
|
|
|
a3 |
|
|
|
|
|
|
a3 |
|
|
|
|
|
|
a4 |
|
|
|
|
|
|
a4 |
|
|
|
|
|
|
a5 |
|
|
|
|
|
|
a5 |
|
|
|
|
|
|
A6 |
|
|
|
|
|
|
a6 |
|
|
|
|
|
|
|
|
|
|
|
c5 |
|
|
|
|
|
|
|
|
|
|
|
|
|
|
c4 |
|
|
|
|
|
|
|
|
|
|
|
|
|
|
c3 |
|
|
|
|
|
|
|
|
|
|
|
|
|
|
c2 |
|
|
|
|
|
|
|
|
в) |
|
|
|
|
|
c1 |
|
|
|
|
|
|
|
|
|
d5 |
d4 |
d3 |
d2 |
d1 |
|
b1 |
b2 |
b3 |
b4 |
|
b5 |
|
|
|
|
|
|
|
|
a1 |
|
|
|
|
|
|
|
|
|
|
|
|
|
|
a2 |
|
|
|
|
|
|
|
|
|
|
|
|
|
|
a3 |
|
|
|
|
|
|
|
|
|
|
|
|
|
|
a4 |
|
|
|
|
|
|
|
|
|
|
|
|
|
|
a5 |
|
|
|
|
|
|
|
|
Рис. 10. Примеры различных форм матричных диаграмм: а) – L-карта; б) – T-карта; в) – X-карта
30

Поточная диаграмма процесса представляет собой гра-
фическое представление этапов процесса, позволяет выявлять возможности улучшения за счет сбора сведений о фактическом протекании процесса. Анализ связи различных этапов процесса позволяет выявить источники возникновения неблагоприятных ситуаций. Может применяться к любым процессам, начиная с маркетинга и до обслуживания продукции у потребителя. На рис. 11 приведены используемые с этой целью символы и пояснение к ним. Используется в основном для описания уже существующего процесса, либо при разработке нового.
– начало или окончание про-
цесса;
– процесс (операция);
–решение (разветвление процесса);
–контроль качества или количества (инспек-
ция);
–регистрация данных о качестве в виде документа;
–данные, комментарии (не является процес-
сом);
– направление протекания процесса.
Рис. 11. Символы поточной диаграммы
На практике часто используется инструмент «Диаграмма процесса осуществления программы» (PDPC). Он представляет собой диаграмму похожую на рассмотренную выше поточную. Разница в том, что PDPC используется для отображения последовательности решений и действий, которые необходимы для получения желаемого результата (оценка сроков проведения работ по выполнению программы, корректировка сроков их выполнения). При построении PDPC наиболее часто используются следующие символы (рис. 12).
31
– начало или окончание процесса;
– типовой прцесс;
– решение;
– направл. протекания процесса;
– типовой документ.
Рис. 12. Основные символы PDPC
PDPC наиболее эффективен при разработке новой программы достижения требуемого результата, поскольку обеспечивает предварительное планирование и отслеживание действий на стадии анализа возможных проблем; а также за счет прогноза неблагоприятных исходов и разработки корректирующих действий в программе. Использование этого инструмента позволяет запустить механизм непрерывного планирования.
При необходимости можно использовать весь спектр символов, перейдя от PDPC к построению поточной диаграммы.
4.2. Новейшие инструменты управления качеством
Новейшие инструменты управления качеством – это: развертывание функции качества (Quality Function Deployment, QFD-методология, «Дом качества»); методология реперных точек (benchmarking); анализ форм и последствий отказов (Failure Mode and Effect Analysis, FMEA-методология); анализ деятель-
ности подразделения; система «Ноль дефектов» (Zero Defect, ZD-методология); система «Точно во время» (Just-in-Time, JIT- мето-дология); функционально-стоимостной анализ (ФСАметодология).
32

Развертывание функции качества (QFD) – это методо- |
Этапы построения первого «дома качества»: |
логия систематического и структурированного преобразования |
1. Определение ожиданий потребителей. Ожидания |
пожеланий потребителей в требования к качеству продукции |
устанавливаются путем анкетирования и приводятся в субтабли- |
(услуги, процесса). В основе методологии лежит принцип по- |
це 1 (рис. 14). Выявляется важность (ВО) ожиданий в виде весо- |
строения таблиц-матриц, так называемых «домов качества» (рис. |
вых коэффициентов по пятибалльной шкале. |
13). Первый «дом качества» (рис. 13) устанавливает связь между |
2. Определение сравнительной ценности продукции (ОП). |
пожеланиями потребителей и техническими условиями, содер- |
Выпускаемая продукция сравнивается с лучшим видом конкури- |
жащими требования к характеристикам продукции. В центре |
рующей продукции (насколько она совершенна при сравнении с |
внимания второго «дома качества» находится взаимосвязь меж- |
аналогом) по пятибалльной шкале. Данные заносятся в субтаб- |
ду характеристиками продукции и характеристиками частей этой |
лицу 2. |
продукции. Третий «дом качества» устанавливает связь между |
3. Установление целей проекта. Необходимо исправить |
требованиями к компонентам продукции и требованиями к ха- |
имеющийся уровень показателей удовлетворения ожиданий по |
рактеристикам процесса (в результате определяются критерии |
отношению к установленным показателям для конкурента. |
выполнения критических процессов). В четвертом «доме каче- |
|
ства» характеристики процесса преобразуются в характеристики |
|
оборудования и способы контроля технологических операций |
|
производства, обеспечивающих выпуск качественной продук- |
|
ции. |
|
Рис. 13. Структура «дома качества» |
Рис. 14. Шаги последовательного применения QFD |
33 |
34 |

Следует установить целевые значения (ЦЗ) для каждого ожидания потребителей по пятибалльной шкале. Если характеристика продукции проигрывает в оценке продукции конкурента, нужно установить в виде цели оценочное значение конкурента. В случае, если продукция оценена выше, чем продукция конкурента, достаточно отразить в целях полученное значение.
Относительные величины «степени улучшения» (СУ) качества вычисляем по формуле:
СУ ЦЗ ОП . |
(13) |
Весомость (ВЕС) каждого ожидания потребителя (характеристики продукции) по формуле:
ВЕС ВО СУ . |
(14) |
После расчета весомости ожиданий , значения необходимо просуммировать и в четвертом столбце рассчитать весомость, выраженную в процентах (ВЕС,%).
4.Описание технических характеристик продукции. Ис-
пользуя метод «мозгового штурма» выявляются и размещаются технические характеристики продукции, за счет изменения параметров которых могут быть выполнены различные ожидания потребителя.
5.Заполнение матрицы связей. Применение матрицы свя-
зей позволяет изучить силу влияния технических характеристик продукции на выполнение ожиданий потребителя. При заполнении элементов матрицы применяют символы и коэффициенты (сила взаимосвязи) (СВ), которые используются при составлении матричных диаграмм. В элементах матрицы, помимо символа, необходимо указать цифровые оценки значимости взаимосвязи (ЗВ) технических характеристик продукции, которые рассчитываются по формуле:
ЗВ СВ ВЕС , %. |
(15) |
35
«Сила взаимосвязи» в виде символов , , ∆ размещается в левой верхней части элементов матрицы связей и, как правило, определяется в результате применения мозговой атаки. В нижние – правые части элементов матрицы связей заносятся рассчитанные цифровые оценки ЗВ.
Рассчитывается суммарная оценка (сумма числовых значений показателей ЗВ по каждому столбцу). Полученные значения суммируются и получается итоговая величина, которая необходима для расчета второй строки, отражающей приоритетность каждой технической характеристики продукции. Приоритетность выражается в процентах от итоговой величины, сумма по строке должна быть равна 100 %.
6.Определение взаимодействия между техническими ха-
рактеристиками продукции. Сила взаимосвязи между техническими характеристика указывается в элементах «крыши» – треугольной корреляционной матрицы при помощи уже известных символов.
7.Инженерная оценка конкурентоспособности продукции – технический анализ. На этом этапе указываются единицы измерения технических характеристик или виды дефектов, второй строкой приводятся значения технических характеристик продукции. Третьей строкой – значения технических характеристик продукции конкурента.
8.Определение целевых значений технических характери-
стик продукции. Целевые значения определяются с учетом приоритетности технических характеристик . Целевые значения имеют непосредственное отношение к улучшению технических характеристик.
Аналогично строятся второй, третий и четвертый «дома качества», в которых определяются характеристики сырья, технологического процесса и оборудования. По результатам анализа разрабатываются рекомендации по улучшению качества продукции.
36
Анализ форм и последствий отказов (FMEA-методо-
логия) применяется для анализа продукции и процессов, и позволяет идентифицировать возможные отказы процессов для предотвращения их последствий. Суть методологии заключается в совокупности мероприятий, позволяющих выявить потенциальные дефекты и варианты отказов (которые могут возникнуть при применении продукции/функционировании процесса); определить основные причины их появления и возможные последствия; выработать действия по устранению причин или предотвращению возможных последствий.
Последовательность действий:
составляется список возможных последствий (S) каждого отказа;
каждое последствие оценивается по десятибалльной шкале (10 соответствует самым тяжелым последствиям);
оценивается вероятность возникновения последствия (O);
оценивается вероятность обнаружения отказа и его последствий (D);
для каждого последствия вычисляется приоритетное чис-
ло риска (ПЧР) – R (Risk Priority Number):
R S O D; |
(16) |
отбираются отказы, которые необходимо устранить;
вырабатываются технические решения, позволяющие предотвратить или сократить последствия отказов с высоким показателем риска;
рассчитывается новый показатель риска с учетом разработанных мероприятий.
Результаты оформляются в виде табл. 4.
37
|
|
|
|
|
|
|
|
|
|
|
|
|
|
|
|
|
Таблица 6 |
||
|
|
Протокол проведения FMEA-анализа |
|
|
|
||||||||||||||
Компо- |
|
|
|
|
|
|
|
|
Выявле- |
|
|
|
|
|
|
||||
Потенци- |
Влияние |
|
Причины |
ние де- |
|
|
ПЧР |
|
Реко- |
|
|||||||||
ненты |
альный |
|
|
|
|
|
|
|
|
фекта |
|
|
|
|
мен- |
|
|||
(опера- |
|
|
|
|
|
|
|
|
|
|
|
|
|
||||||
дефект |
Опи- |
|
|
Опи- |
|
Опи- |
|
|
|
|
|
дации |
|
||||||
ции) |
S |
|
O |
|
D |
|
R |
|
|
||||||||||
|
сание |
|
сание |
сание |
|
|
|
|
|
|
|||||||||
1 |
|
2 |
3 |
|
4 |
|
5 |
6 |
7 |
|
8 |
9 |
|
10 |
|
||||
|
|
|
|
|
|
|
|
|
|
|
|
|
|
|
|||||
|
|
|
|
|
Результаты анализа |
|
|
|
|
|
|
|
|||||||
|
|
Меры |
|
|
S |
|
|
O |
|
D |
|
|
R |
|
|
|
|||
|
|
11 |
|
|
12 |
|
|
13 |
|
14 |
|
|
15 |
|
|
|
5.ПРОГРАММА СЕМИНАРСКИХ ЗАНЯТИЙ
5.1.Основополагающие понятия в области качества
Сущность и роль качества. Эволюция и многоаспектность понятия «качество». Аспекты, характеризующие понятие «качество». Основные причины, определяющие необходимость повышения и обеспечения качества.
Понятия «качество трудовой жизни», «качество продукции (услуг)», «качество жизни», «качество деятельности организации».
Классификация и номенклатура показателей качества. Показатели качества продукции. Квалиметрия – наука об измерении качества, статусы квалиметрии. Роль квалиметрии в управлении качеством. Методы определения фактических численных значений показателей качества.
5.2. Стандарты на системы менеджмента качества. Концепция всеобщего управления качеством (TQM).
Процессный подход
Стандарты на системы менеджмента качества (СМК) версии 2000 и 2008 годов. Роль и развитие стандартов ISO серии 9000. Принципы менеджмента качества в соответствии со стан-
38