
Методические указания к выполнению лабораторных работ по дисциплине «Материаловедение» для студентов направления 15.03.01 «Машиностроение». Селиванов В.Ф
.pdfФГБОУ ВО «Воронежский государственный технический университет»
Кафедра технологии сварочного производства и диагностики
МЕТОДИЧЕСКИЕ УКАЗАНИЯ
к выполнению лабораторных работ по дисциплине «Материаловедение» для студентов
направления 15.03.01 «Машиностроение» (профиль «Оборудование и технология сварочного производства») очной и заочной форм обучения
Воронеж 2016
2
Составитель д-р техн. наук В.Ф. Селиванов
УДК 691.791
Методические указания к выполнению лабораторных работ
по дисциплине «Материаловедение» |
для |
студентов |
направления 15.03.01 «Машиностроение» |
(профиль |
«Оборудование и технология сварочного производства») очной и заочной форм обучения / ФГБОУ ВО «Воронежский государственный технический университет; сост. В.Ф. Селиванов. Воронеж, 2016. 36 с.
В методических указаниях содержатся необходимые теоретические сведения, практические рекомендации, порядок выполнения лабораторных работ и контрольные вопросы, позволяющие студенту самостоятельно оценить свой уровень подготовленности.
Предназначены для студентов 2 курса. Методические указания подготовлены в электронном
виде в текстовом редакторе MS Word XP и содержатся в файле «Материаловедение_СП.pdf».
Табл. 2. Ил. 6.
Рецензент канд. техн. наук, доц. Л.В. Усачева
Ответственный за выпуск зав. кафедрой д-р техн. наук, проф. В.Ф. Селиванов
Издается по решению редакционно-издательского совета Воронежского государственного технического университета
©ФГБОУ ВО «Воронежский государственный технический университет», 2016
3
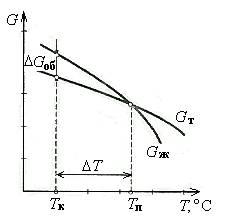
Лабораторная работа № 1
КРИСТАЛЛИЗАЦИЯ МЕТАЛЛОВ И СПЛАВОВ
Цель работы: изучить процесс кристаллизации металлов и сплавов.
Оборудование и материалы: оптический стереомикроскоп MC-2 ZOOM, видеоокуляр DCM130 или цифровая фотокамера, компьютер, монитор, водные растворы NaCl, NH4Cl, K2Cr2O7, Pb(NO3)2.
Задание:
1.Изучите теоретическую часть работы.
2.На примере кристаллизации солей из водных растворов проследить процесс образования и роста различных кристаллов.
3.С помощью видеоокуляра и компьютера зафиксировать различные стадии роста кристаллов для дальнейшего иллюстрирования отчета.
Содержание отчета:
1.Краткие теоретические сведения.
2.Результаты проведенных наблюдений: описание, фотографии и выводы.
Краткие теоретические сведения
Процесс образования твердой кристаллической фазы из жидкости называется первичной кристаллизацией.
Твердая кристаллическая фаза характеризуется определенным, закономерным расположением атомов в пространстве — пространственной кристаллической решеткой.
Перекристаллизация некоторых металлов и сплавов в твердом состоянии при нагреве и охлаждении называется
вторичной кристаллизацией.
Кристаллизация протекает в условиях, когда система переходит к термодинамически более устойчивому состоянию с меньшей энергией Гиббса (свободной энергией) G , т.е. когда энергия Гиббса кристалла меньше, чем энергия Гиббса жидкой фазы. Если превращение происходит с небольшим изменением объема, то
G E T S ,
где E - полная энергия (внутренняя энергия фазы); T - абсолютная температура; S - энтропия.
Рис. 1.1. Изменение энергии Гиббса в жидком (GЖ ) и
твердом (GТ ) состояниях в зависимости от температуры (ТK - температура, при которой происходит кристаллизация)
Изменение энергии Гиббса металла в жидком и твердом состоянии в зависимости от температуры показано на рис.1.1. При температуре выше температуры превращения (ТП ) более устойчив жидкий металл, имеющий меньший запас свободной энергии, а ниже ТП - устойчив твердый металл. При температуре ТП значения энергии Гиббса металла в жидком и твердом состояниях равны. Температура ТП соответствует равновесной температуре кристаллизации (или плавления) данного вещества, при которой обе фазы (жидкая и твердая) могут сосуществовать одновременно. Процесс кристаллизации при этой температуре еще не начинается, а начинается тогда, когда возникает разность энергий Гиббса ( G), образующаяся вследствие меньшей энергии Гиббса твердого металла по сравнению с жидким.
2
Следовательно, процесс кристаллизации может протекать только при переохлаждении металл ниже равновесной температуры ТП . Разность между температурами ТП и ТK , при которых может протекать процесс кристаллизации, носит название степени переохлаждения:
Т TП TК .
Переход сплава из жидкого состояния в твердое, как и при кристаллизации чистых металлов, протекает только при наличии некоторого переохлаждения, когда энергия Гиббса жидкой фазы оказывается ниже энергии Гиббса твердой фазы.
Процесс затвердевания протекает в результате образования центров кристаллизации (зародышей) и последующего их роста в виде дендритных или полногранных кристаллитов.
Любые твердые фазы, образующиеся в твердом сплаве, отличаются по составу от исходного жидкого раствора, поэтому для устойчивого зародыша необходимы не только гетерогенные флуктуации, но и флуктуации концентрации. Флуктуациями концентрации называют временно возникшие отклонения химического состава сплава в отдельных малых объемах жидкого раствора от среднего его состава.
Такие флуктуации возникают вследствие диффузионного превращения атомов вещества в результате тепловых движений в жидком растворе.
Русский ученый Д.К. Чернов, изучая структуру литой стали, указал, что процесс кристаллизации состоит из двух элементарных процессов. Первый процесс заключается в зарождении мелких частиц кристаллов, которые Чернов назвал зачатками, а теперь их называют зародышами, или центрами кристаллизации. Второй процесс состоит в росте кристаллов из этих центров.
Рассмотрение схем кристаллизации позволяет объяснить два момента:
1) по мере развития процесса кристаллизации в нем участвует все большее и большее число кристаллов. Поэтому процесс вначале ускоряется, пока в какой-то момент взаимное
3
столкновение растущих кристаллов не начинает заметно препятствовать их росту;
2) в процессе кристаллизации, пока кристалл окружен жидкостью, он часто имеет правильную форму, но при столкновении и срастании кристаллов их правильная форма нарушается, внешняя форма кристалла оказывается зависимой от условий соприкосновения растущих кристаллов.
Зародыш новой фазы может возникнуть только в тех микрообъемах исходной фазы, состав которых в результате флуктуации концентрации и расположения атомов соответствует составу и строению новой кристаллизующей фазы. Если при этом концентрационные флуктуации соответствуют микрообъемам, имеющим размер меньше критического, возникает устойчивый зародыш, способный к росту.
Самопроизвольное образование зародышей на основе фазовых и энергетических флуктуаций может проходить только в высокочистом жидком металле при больших степенях переохлаждения.
Чаще источником образования зародышей являются всевозможные твердые частицы, которые всегда присутствуют в расплаве. Если частицы примеси имеют одинаковую кристаллическую решетку с решеткой затвердевающего металла, и параметры сопрягающихся решеток примесей и кристаллизующегося вещества примерно одинаковы, то они играют роль готовых центров кристаллизации.
Структурное сходство между поверхностями сопряжения зародыша и частицы посторенней примеси приводит к уменьшению размера критического зародыша, работа его образования, и затвердевание жидкости начинается при меньшем переохлаждении, чем при самопроизвольном зарождении.
Чем больше примесей, тем больше центров кристаллизации, тем мельче получается зерно. Такое образование зародышей называется гетерогенным.
Модифицированиеиспользование специально вводимых в
жидкий металл примесей для получения мелкого зерна по
4
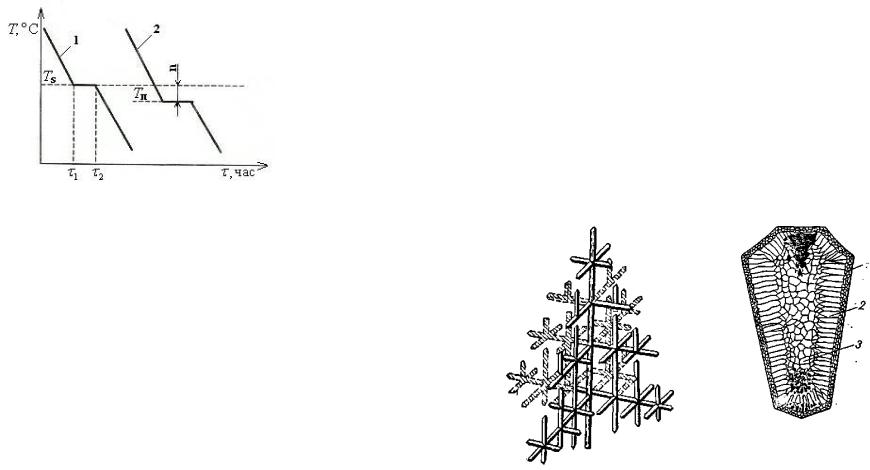
описанному выше механизму. Эти примеси, практически не изменяя химического состава сплава, вызывают при кристаллизации измельчение зерна и в итоге улучшение механических свойств.
Процесс перехода металла их жидкого состояния в кристаллическое можно изобразить кривыми в координатах «времятемпература» (рис.1.2).
Рис. 1.2. Схема кристаллизации металла (кривые охлаждения при кристаллизации)
Охлаждение металла в жидком состоянии сопровождается плавным понижением температуры и может быть названо простым охлаждением, так как при этом нет качественного изменения состояния.
При достижении теоретической температуры кристаллизации (TS ) на кривой появляется горизонтальная
площадка, так как отвод тепла компенсируется выделяющейся при кристаллизации скрытой теплотой кристаллизации. Теоретически процесс кристаллизации изображается кривой 1.
При TS |
начинается |
процесс |
кристаллизации, |
который |
|
продолжается определенное время от 1 |
до 2 . |
Кривая 2 |
|||
показывает |
реальный |
процесс |
кристаллизации. |
Жидкость |
непрерывно охлаждается до температуры переохлаждения ТП ,
5
лежащей ниже теоретической температуры кристаллизации. При охлаждении ниже TS создаются энергетические условия,
необходимые для протекания процесса кристаллизации.
Вреальных условиях при кристаллизации слитка могут получиться кристаллы самых разнообразных форм и размеров.
Это зависит от условий охлаждения слитка, а также от того,
скакой температурой металл попадает в изложницу и какова была температура перегрева сплава, от скорости отвода тепла и т.д. Чаще всего при кристаллизации металлов и солей образуется дендритная структура (дендритдревовидный кристалл). В реальных металлических слитках дендриты имеют правильную форму (рис. 1.3). Кристаллы неправильной формы называют зернами или кристаллитами. Процесс заканчивается тем, что заполняются все межосные пространства и кристалл принимает округлую форму, но вытянутую в направлении главного теплоотвода. Такие кристаллы называют столбчатыми.
Втех случаях, когда металла не хватает для заполнения всех межосных пустот, что встречается в усадочных раковинах, то дендритная форма кристалла сохраняется.
Рис. 1.3. Дендрит |
Рис. 1.4. Строение слитка металла |
6
Обычно слиток состоит из трех зон, каждая их которых характеризуется особым расположением зерен (рис. 1.4), образовавшихся при различных условиях охлаждения.
Первая зона (1) - наружная мелкозернистая корка, состоящая из дезориентированных мелких кристалловдендритов.
Вторая зона (2) - зона столбчатых кристаллов. Их форма определяется направлением отвода тепла.
Третья зона (3) - зона равноосных кристаллов. Центрами кристаллизации являются мельчайшие включения, не растворившиеся в жидком металле.
Наблюдение за процессом кристаллизации металлов и сплавов затруднено в связи с их непрозрачностью и высокими температурами кристаллизации. Поэтому изучение этих процессов осуществляется различными косвенными методами.
В настоящей работе изучают процессы первичной кристаллизации насыщенных растворов различных солей, вызванные испарением растворителя.
Изучение процесса кристаллизации осуществляется с помощью бинокулярной лупы или биологического микроскопа.
Водные растворы солей составляются насыщенными с тем расчетом, чтобы незначительное испарение воды привело растворы к состоянию перенасыщения.
При кристаллизации жидкого раствора любой соли, так же как и у стального слитка, можно наблюдать три различные зоны кристаллов, отличающиеся своей формой и величиной (рис. 4). Образование трех зон можно объяснить различными условиями кристаллизации.
Обычно кристаллизация капли начинается у краев, так как здесь быстрее всего испаряется растворитель, и раствор быстро перенасыщается. У краев капли возникает зона весьма мелких кристаллов (зона /), что указывает на зарождение большого числа центров кристаллизации.
Значительное пресыщение водного раствора соли можно уподобить значительному переохлаждению кристаллизующегося металла.
7
К мелкозернистой зоне примыкает зона более крупных столбчатых кристаллов (зона 2), Направление роста этих кристаллов обычно перпендикулярно краю капли.
Большой размер образующихся кристаллов указывает на уменьшение числа центров кристаллизации и увеличение скорости роста кристаллов. Направленный рост, обусловливающий столбчатую форму, вызван тем, что в связи с небольшим пересыщением жидкого раствора в более толстом слое капли не образуется центров кристаллизации, не связанных с ранее затвердевшей зоной у краев капли, а возникшие на границе мел козернистой зоны центры растут в сторону постепенно пересыщающихся краев, т. е. к центру капли.
Постепенное пресыщение слоев утолщающейся по направлению к центру капли создает условия кристаллизации, подобные направленному отводу тепла в формы или в изложницы для металла.
В центре капли возникает третья зона (зона 3), состоящая из очень крупных, различно ориентированных равновесных кристаллов. Большой размер кристаллов указывает на малое число образующихся центров кристаллизации в связи с медленным пресыщением этой части капли. Малая степень пересыщения, так же как « малая степень переохлаждения в центральной зоне слитка или отливки металла, создают условия для зарождения наибольшего числа различно ориентированных равновесных кристаллов.
Методика выполнения работы
Процесс образования кристаллов в настоящей работе изучается на примере кристаллизации солей из водных растворов ( NaCl , NH4Cl , K2Cr2O7 , Pb NO3 2 ) с помощью
микроскопа.
После нанесения капли раствора на предметное стекло начинается процесс испарения воды, приводящий к выпадению кристаллов. На примере кристаллизации NaCl можно проследить процесс образования и роста кристаллов правильной формы, а также влияние примесей на форму и число центров
8
кристаллизации. Кристаллизация раствора NH4Cl позволяет наблюдать процесс роста дендритных кристаллов. (Обратить внимание на динамику их роста.) Раствор K2Cr2O7 служит моделью, позволяющей проследить рост столбчатых кристаллов.
Порядок выполнения работы
1.Нанести с помощью пипетки каплю раствора на предметное стекло.
2.Поместив стекло с каплей под объектив микроскопа,
получить резкое изображение края капли (капли растворов K2Cr2O7 , Pb NO3 2 необходимо предварительно подогреть до выпаривания воды).
3.Наблюдать за ростом кристаллов, фиксируя с помощью видеоокуляра кристаллы на нескольких последовательных стадиях роста.
4.Выполнить вышеуказанные задания для каждого
раствора.
Контрольные вопросы
1.При каких условиях протекает кристаллизация?
2.Что называют степенью переохлаждения?
3.Что такое флуктуации концентрации?
4.Что такое центры кристаллизации?
5.Как строят кривые охлаждения? В каких координатах?
6.Что такое модифицирование?
7.Из каких зон состоит кристаллизующийся слиток?
8.Что такое скрытая теплота кристаллизации?
9.Что называют дендритом?
10.Что происходит с энергией Гиббса при кристаллизации?
9
Лабораторная работа № 2
МЕТОДЫ МЕХАНИЧЕСКИХ ИСПЫТАНИЙ МАТЕРИАЛОВ
Цель работы: Ознакомление со способами механических испытаний материалов, изучение методики одного из видов испытаний материалов. Изучение методов определения твердости материалов.
Оборудование и материалы: Разрывная машина Р-10,
муфельная электропечь ЭКПС-10, штангенциркуль, твердомер ТДМ-2, микротвердомер ПМТ3М1, паспорта и инструкции к оборудованию, набор образцов.
Задание:
1.Изучите теоретическую часть работы.
2.Ознакомьтесь с методикой проведения испытаний по одной из схем (растяжение, сжатие, изгиб, определение твердости или микротвердости материала).
3. Изучите принцип действия и порядок работы на разрывной машине, твердомере и микротвердомере.
4.Проведите испытания материала по указанной преподавателем методике и определите характеристики материала.
5.Оформите полученные результаты.
Содержание отчета:
1.Краткая характеристика методов испытаний.
2.Описание используемого оборудования и образцов.
3.Методика проведения испытаний.
4.Данные испытаний образцов и выводы.
Общая характеристика методов испытаний
Под механическими свойствами понимают характеристики, определяющие поведение материала под действием приложенных внешних механических сил. К механическим свойствам относятся: прочность (сопротивление деформации), сопротивление разрушению (пластичность, вязкость).
10
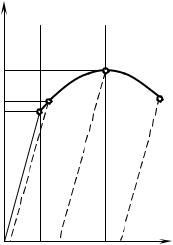
Испытания, проводимые для выявления механических свойств материалов, делят на две группы: статические и динамические.
Статическими называют испытания, при которых прилагаемая к образцу нагрузка возрастает медленно и плавно.
Кним относятся:
1)испытания на растяжение – применяются преимущественно для сравнительно пластичных материалов, разрушению которых предшествует пластическая деформация;
2)испытания на сжатие – наиболее пригодны для хрупких материалов, образцы которых разрушаются практически без пластической деформации;
3)испытания на кручение – применяют для пластичных,
атакже для малопластичных металлов;
4)испытания на изгиб – применяют для малопластичных материалов, главным образом для серых и белых чугунов, инструментальных сталей в состоянии высокой твердости, а также с целью определения влияния коррозии.
Наиболее распространенным видом таких испытаний являются испытания на растяжение. При этом виде испытаний удается определить сразу несколько механических характеристик материала.
Размеры и формы принимаемых образцов стандартизированы в ГОСТе, и он допускает широкий выбор разных видов образцов, однако обычно при испытаниях на растяжение используют образец цилиндрической формы с утолщениями по краям.
Как правило, машины для испытаний снабжены прибором, записывающим диаграмму растяжения (рис.2.1).
Кривая, приведенная на рисунке, характеризует деформацию металла под действием напряжений σ, величина которых является условной
σ = Р/F0,
где F0 – начальная площадь поперечного сечения.
До точки А деформация нарастает пропорционально напряжению. Модуль упругости материала определяется как
11
тангенс угла наклона ОА к оси абсцисс или Е = σ/δ, где δ – относительная деформация. Модуль упругости определяет жесткость материала, и его физический смысл сводится к тому, что он характеризует сопротивляемость материала упругой деформации. Модуль упругости практически не зависит от структуры материала и определяется силами межатомной связи. Другие механические свойства изменяются в зависимости от структуры (обработки) в широких пределах.
Следует отметить, что пропорциональность между напряжением и деформацией справедлива с определенным приближением. Точные измерения показывают отклонение от закона пропорциональности. Это явление называют неупругостью. Неупругость связана с движением точечных дефектов дислокаций и атомов в приграничных объемах и является причиной внутреннего трения.
σ,S |
|
|
|
|
|
|
I |
|
II |
III |
|
σв |
|
|
|
|
|
σ0,2 |
|
|
|
|
С |
σпц |
А |
|
|
|
|
|
|
|
|
||
|
0,2 |
5 |
7 |
40 50 |
δ, % |
Рис. 2.1. Диаграмма растяжения металлов: I – область упругой деформации; II - область пластической деформации; III - область развития трещин
12

Напряжение в точке А называют пределом пропорциональности σпц. Напряжения, не превышающие σпц, практически вызывают только упругие (в микроскопическом объеме) деформации, поэтому зачастую предел пропорциональности отождествляют с условным пределом упругости. Предел упругости определяется как напряжение, при котором остаточная деформация не превышает 0,05 % первоначальной длины образца:
σ 0.05 = P0,05/F0
Напряжение, вызывающее остаточную деформацию равную 0,2 %, называют условным пределом текучести:
σ0,2 = P0.2/F0
При испытании металлов с ОЦК-решёткой при достижении определённого напряжения σт на кривой растяжения образуется площадка. Напряжение, при котором образец деформируется без увеличения растягивающей нагрузки, называется физическим пределом текучести:
σт = Рт /F0.
Дальнейшее повышение нагрузки вызывает значительно большую пластическую деформацию во всем объеме металла. Напряжение, соответствующее наибольшей нагрузке Рmax, перед разрушением образца называют временным сопротивлением, или пределом прочности:
σв = Рmax/F0
Кроме того, при испытании на растяжение определяют характеристики пластичности. К ним относятся удлинение:
lk l0 100 l0
иотносительное сужение:
F0 Fk 100
F0
13
Где l0 и lk – длина образца, а F0 и Fk – площадь поперечного сечения образца до и после разрушения соответственно. Отношение изменения длины к начальной длине образца определяет условное удлинение. Истинное удлинение определяется как:
|
|
1 |
|
|
lk ln |
|
|
||
|
||||
|
|
|
||
|
|
1 |
Истинное сопротивление разрушению Sk определяется как отношение нагрузки в момент разрушения к минимальной площади поперечного сечения образца в месте разрушения:
Sk = Рk/Fk
Характеристики материалов σ0,2, σв, δ, , а также Е являются базовыми и включаются в ГОСТ на поставку конструкционных материалов, в паспорта приемочных испытаний, а также входят в расчеты прочности.
Для материалов с прочностью выше 2500 МПа, а также для чугуна, литых алюминиевых сплавов и прочих материалов, хрупких при растяжении используют другие более мягкие виды испытаний – сжатие, изгиб, кручение. При этом получают те же характеристики прочности, что и при растяжении – σ0,2сж, σвсж и т.д., но количественно отличающиеся (вследствие другого напряженного состояния в образце).
Для определения прочности зачастую пользуются простым и не разрушающим образец методом – измерением твердости.
Под динамическими понимают испытания, при которых скорость деформирования значительно выше, чем при статических испытаниях. К ним относят испытания на удар (определение надежности).
Эти испытания применяют для металлов с решеткой ОЦК, т.е. для сталей (главным образом пластичных конструкционных). Эти испытания излишни для сталей и сплавов с аустенитной структурой – их трудно перевести в хрупкое состояние. При испытаниях определяют ударную вязкость материала.
14
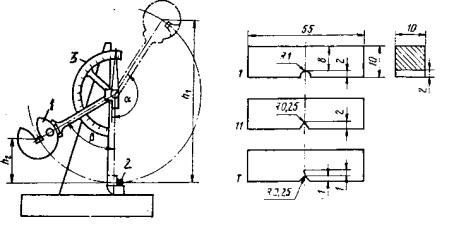
Разрушение образца, расположенного на двух опорах, осуществляют ударом маятника копра (рис. 2.2, а). Образец для испытаний (рис. 2.2, б) имеет посередине концентратор одного из трех видов: U с радиусом концентратора R = 1 мм, V с радиусом концентратора R = 0,25 мм и углом 45º и Т – с усталостной трещиной. В последнем случае надрез глубиной в 1 мм делается механически и затем создается усталостная трещина тоже глубиной в 1 мм.
Соответственно ударная вязкость обозначается КСU, КСV, КСТ. Под ударной вязкостью КС, Дж/м² понимают работу удара К, отнесенную к начальной площади поперечного сечения S0 образца в месте концентратора:
КС = К/S0
Работу удара К определяют по шкале маятникового копра. Ударная вязкость включает в себя работу зарождения трещины (аз) и работу распространения трещины (ар), т.е.
КС = аз + ар. При ударных испытаниях лучше определять
Рис. 2.2. Схема маятникового копра (а), образцы для испытания на удар (б):
1 маятник; 2 образец; 3 шкала
15
работу распространения трещины, поскольку она характеризует надежность материала или склонность к хрупкому разрушению.
Долговечность материала определяют испытанием на усталость, ползучесть, износ, коррозию и другими методами.
При знакопеременной нагрузке в материале могут образовываться трещины и затем происходить разрушения при напряжениях меньших, чем предел прочности.
Постепенное накопление повреждений в металле под действием циклических нагрузок, приводящих к образованию трещин и разрушению, называют усталостью, а свойство металлов сопротивляться усталости – выносливостью.
Твердость как характеристика свойств материала.
Определения твердости являются широко применяемыми в лабораторных и в заводских условиях способами испытаний для характеристики механических свойств металлов.
Твердость металлов измеряют при помощи воздействия на поверхность наконечника, изготовленного из малодеформирующегося материала (твердая закаленная сталь, алмаз, сапфир или твердый сплав) и имеющего форму шарика, конуса, пирамиды или иглы.
Существует несколько способов изменения твердости, различающихся по характеру воздействия наконечника. Твердость можно измерять вдавливанием наконечника (способ вдавливания), царапанием поверхности (способ царапания), ударом или же по отскоку наконечника-шарика. Твердость, определенная царапанием, характеризует сопротивление разрушению (в основном по срезу); твердость, определенная по отскоку, характеризует упругие свойства; твердость, определенная вдавливанием – сопротивление пластической деформации.
Преимущества измерения твердости:
1. Между твердостью пластичных металлов, определяемой способом вдавливания, и другими механическими свойствами (главным образом пределом прочности), существует количественная зависимость. Твердость, определенная вдавливанием, характеризует также предел выносливости
16
некоторых металлов, в частности меди, дюралюминия и стали в отожженном состоянии.
2.Измерение твердости по технике выполнения значительно проще, чем определение прочности, пластичности и вязкости. Испытания твердости не требуют изготовления специальных образцов и выполняются непосредственно на проверяемых деталях после зачистки на поверхности ровной горизонтальной площадки, а иногда даже и без такой подготовки.
3.Измерение твердости обычно не влечет за собой разрушения проверяемой детали, и после измерения ее можно использовать по своему назначению.
4.Твердость можно измерять на деталях небольшой толщины, а также в очень тонких слоях, не превышающих (для некоторых способов измерения твердости) десятых долей миллиметра, или в микрообъемах металла.
Для полной характеристики свойств металла необходимо наряду с измерением твердости проводить и другие механические испытания.
Следует различать два способа определения твердости вдавливанием: измерение твердости (макротвердости) и измерение микротвердости.
Измерение макротвердости характерно тем, что в испытуемый материал вдавливается тело, проникающее сна сравнительно большую глубину, зависящую прежде всего от величины прилагаемой нагрузки и свойств металла. Кроме того. Во многих испытаниях вдавливается тело значительных размеров, например стальной шарик диаметром до 10 мм, в результате чего в деформируемом объеме оказываются представленными все фазы и структурные составляющие сплава
вколичествах и с расположением, характерным для измеряемого материала. Измеренная твердость должна в этом случае характеризовать твердость всего испытываемого материала.
Измерение микротвердости имеет целью определить твердость отдельных зерен, фаз, структурных составляющих сплава (а не «усредненную» твердость, как при измерении макротвердости). В данном случае объем, деформируемый
17
вдавливанием должен быть меньше объема (площади) измеряемого зерна. Поэтому прилагаемая нагрузка выбирается небольшой. Кроме того, микротвердость измеряют для характеристики свойств очень малых по размерам деталей.
Значительное влияние на результаты испытаний твердости оказывает состояние поверхности измеряемого материала.
Если поверхность неровная – криволинейная или с выступами, то отдельные участки в различной степени участвуют в сопротивлении вдавливанию и деформации, что приводит к ошибкам в измерении. Чем меньше нагрузка для вдавливания, тем более тщательно должна быть подготовлена поверхность. Она должна представлять шлифованную горизонтальную площадку, а для измерения микротвердости – полированную (при изготовлении шлифа нельзя допускать наклепа в поверхностном слое).
Наибольшее применение получило измерение твердости вдавливанием. В результате вдавливания с определенной нагрузкой поверхностные слои металла, находящиеся под наконечником и вблизи него, пластически деформируются. После снятия нагрузки остается отпечаток. Особенность протекающей при этом деформации, заключается в том, что она протекает только в небольшом объеме, окруженном недеформированным материалом. Преобладание в этом случае касательных напряжений позволяет производить оценку пластической деформации и хрупких металлов (чугун), которые при обычных механических испытаниях (на растяжение, сжатие, кручение, изгиб) разрушаются без макроскопически заметной пластической деформации.
В последнее время все более широко применяются динамические малогабаритные переносные твердомеры. Типичным представителем такого оборудования является твердомер ТДМ-2.
Твердомер динамический малогабаритный типа ТДМ-2 предназначен для экспрессного неразрушающего измерения и контроля твердости конструкционных, углеродистых и нержавеющих сталей, а также сплавов из цветных металлов по шкалам Роквелла HRC и Бринелля НВ и разбраковки материалов
18