
Методическое пособие 162
.pdfпо твердости. Твердомер может использоваться в производственных, лабораторных и полевых условиях в машиностроении, металлургии, энергетике и других отраслях промышленности.
Твердомер позволяет производить измерения твердости на любых крупногабаритных изделиях, в том числе в труднодоступных зонах, на плоских и выпуклых поверхностях с радиусом кривизны не менее 15 мм, под различными углами, и с параметром шероховатости не более Ra 2,5 по ГОСТ 2789-73. Диапазоны измерения твердости на основных шкалах:
- |
по шкале "С" Роквелла, HRC |
20... 70; |
- |
по шкале Бринелля, НВ |
90... 450; |
Принцип работы твердомера |
основан на измерении |
отношения скоростей индентора (ударного элемента) при падении и отскоке от поверхности контролируемого изделия. Отношение скоростей индентора перемещения при отскоке и падении характеризует твердость контролируемого материала.
Твердомер состоит из преобразователя, электронного блока и зарядного устройства.
Преобразователь, совмещенный с ударным механизмом, формирует напряжение, пропорциональное скорости перемещения индентора. Он представляет собой отдельно выполненное механическое устройство, связанное с электронным блоком при помощи кабеля. Его подвижная часть (индентор) при помощи предварительно взведенной пружины сбрасывается при нажатии спусковой кнопки на контролируемую поверхность. На конце индентора расположен твердосплавный шарик, непосредственно - контактирующий с контролируемой поверхностью. При этом индентор (внутри которого находится постоянный магнит) перемещается внутри катушки индуктивности и своим магнитным полем наводит в катушке электродвижущую силу. Напряжение с выхода катушки индуктивности подается на вход электронного блока.
Электронный блок производит усиление и преобразование аналогового сигнала преобразователя в цифровой код, математическую обработку полученной измерительной информации, хранение переменных и промежуточных
19
результатов измерений, управление режимами работы прибора и индикацию результатов непосредственно в единицах твердости. Входной сигнал от преобразователя поступает на вход усилителя. С выхода усилителя сигнал подается на вход пикового детектора. Аналоговый сигнал с выхода пикового детектора поступает на вход аналого-цифрового преобразователя, который после преобразования передает эту информацию в микро-ЭВМ для дальнейшей обработки. МикроЭВМ представляет собой однокристальную микромощную ЭВМ, имеющую внутреннее постоянное запоминающее устройство. Микро-ЭВМ через шины адреса данных и управления связана с системным супервизором, оперативным запоминающим устройством (ОЗУ), клавиатурой и цифровым индикатором. Системный супервизор осуществляет сброс микро-ЭВМ при включении и выключении питания, при выходе напряжения питания за допустимые пределы, а также при появлении сбоев в микро-ЭВМ. ОЗУ используется для хранения промежуточных данных. Клавиатура представляет собой пленочное герметично защищенное поле из 4 кнопок и предназначена для управления работой твердомера. Цифровой индикатор представляет собой четырехразрядный однострочный индикатор. Блок питания обеспечивает стабилизированное напряжение для всей электрической схемы.
Порядок выполнения работы при испытаниях на растяжение.
1.Снимите геометрические размеры с приготовленных для испытаний образцов.
2.Проведите термообработку части образцов в муфельной печи по схеме, приложенной преподавателем.
3.Установите испытываемый образец с помощью преподавателя (учебного мастера) в испытательной машине.
4.Проведите испытания и снимите показания приборов.
5.По приведенным выше формулам определите σв, δ и сделайте вывод о влиянии данного вида термообработки на свойства материала.
6.Полученные результаты представьте в виде таблицы.
20
Порядок выполнения работы при измерении микротвердости.
1. Закрепить предмет пластилином на столике так, чтобы исследуемая поверхность была параллельна рабочей поверхности столика.
2.Поместить на утолщенную часть штока груз.
3.Выбрать место на образце для отпечатка.
4.Плавно повернуть столик против часовой стрелки до упора, не допуская при этом толчков.
5.Медленным поворотом рукоятки против часовой стрелки опустить шток так, чтобы алмаз коснулся исследуемой поверхности. Рукоятку поворачивать на 180 в течение 10-15 с. После выдержки под нагрузкой (5с) повернуть рукоятку в исходное положение.
6.Измерить диагональ отпечатка. Передвигая предметный столик, подвести отпечаток к перекрестию (рис.2.1). Измерительный барабанокуляр-микрометра совмещен с «0». Затем, вращая измерительный барабан, добиться совмещения перекрестия окуляра с противоположными 2-мя сторонами отпечатка (рис.2.2). Произвести отчет по окуляр-микрометру. Число делений, умноженное на цену деления измерительного
барабана, дает истинную величину диагонали отпечатка Н=1854·Р/С2 (кг/мм2), где Р – нагрузка (г); С – диагональ, мкм, цена деления 0,000310 мм.
Порядок выполнения работы при измерении твердости.
Подготовить прибор к работе согласно технической инструкции.
Установить требуемую шкалу твердости, а также требуемые значения параметров в подрежимах "Угол" и "Статистика". При измерении твердости прибор автоматически учитывает поправочные коэффициенты в соответствии с выбранным углом наклона преобразователя.
Подготовить поверхность в месте измерения твердости. Поверхность не должна иметь окалины, защитных
21
покрытий, следов грубой обработки, окисной пленки, выбоин и смазки. Для измерения необходимо подготовить площадку размером 20x20 мм с шероховатостью поверхности не более Ra 2,5. При измерении твердости на выгнутых криволинейных поверхностях радиус кривизны должен быть не менее 15 мм. Если масса контролируемого изделия менее 3 кг или толщина стенки менее 10 мм, то необходимо с помощью смазки ЦИАТИМ - 221 по ГОСТ 9433-80 или смазки УТ (консталин) по ГОСТ 1957-73 притереть контролируемое изделие к металлической плите массой более 3 кг, имеющей плоскошлифованную поверхность. Контакт должен обеспечивать отсутствие воздушных пустот. Некачественное притирание дает существенное отклонение измеренной величины твердости от действительной. Если контролируемое изделие не удается притереть к массивной металлической плите, то проводить измерения не разрешается, ввиду возникновения недопустимых погрешностей.
"Взвести" преобразователь, плавно загрузив индентор с помощью толкателя до защелкивания ударного механизма.
Установить "взведенный" преобразователь на контролируемую поверхность, плотно прижать его и нажать на спусковую кнопку.
Снять показание твердости.
Для корректной индикации среднеарифметического значения результата измерения необходимо провести соответствующее количество измерений на данном изделии (т.е. не меньше 3 или 5).
Для получения необходимой точности измерений расстояния между точками снятия отсчетов (лунками) на поверхности контролируемого изделия должны быть не менее 3 мм.
Во избежание порчи прибора категорически запрещается работать вблизи источников мощного
22
электромагнитного излучения (электродуговая сварка, |
|
Лабораторная работа № 3 |
|||||
электродуговые |
спектроанализаторы, |
импульсные |
|
|
|
||
регуляторы и т.п.). |
|
|
|
МЕТОДЫ МАКРОСТРУКТУРНОГО АНАЛИЗА |
|||
|
|
|
|
|
|
МЕТАЛЛОВ И СПЛАВОВ |
|
|
Контрольные вопросы |
|
|
Цель работы: |
|
||
1. |
Что понимают под механическими испытаниями? |
1.Изучить методику и возможности макроструктурного |
|||||
2. |
В чем разница между статическими и |
анализа металлов и сплавов. |
|||||
динамическими испытаниями? |
|
|
2. Приобрести практические навыки в исследовании |
||||
3. |
Какие механические характеристики |
можно |
макроструктур металлов и сплавов. |
||||
определить при испытаниях на растяжение? |
|
|
|
Оборудование |
и материалы: Лупа, оптический |
||
4. |
Как определяется модуль упругости? В чем его |
стереомикроскоп MC-2 ZOOM, видеоокуляр DM130 или |
|||||
физический смысл? |
|
|
|
цифровая фотокамера, компьютер, монитор, изломы и |
|||
5. |
для каких материалов используют испытания на |
макрошлифы сплавов и сварных соединений. |
|||||
сжатие, изгиб, кручение? Почему? |
|
|
Задание: |
|
|||
6. |
Что означают характеристики материалов σ0,2, σв, δ, |
1. |
Изучите теоретическую часть работы. |
||||
ψ, Е? |
|
|
|
|
2. |
Ознакомьтесь со способами макроанализа металлов |
|
7. |
Что понимают под ударной вязкостью материала? |
|
и сплавов. |
|
|||
Как определяют ударную вязкость? |
|
|
3. |
Ознакомьтесь |
с видом изломов и макроструктурой |
||
8. |
В чем разница между понятиями |
«прочность» и |
|
металлов и сплавов. |
|||
«твердость»? Существует ли корреляция между ними? |
4. |
Сфотографируйте наблюдаемую структуру изломов |
|||||
9. |
Какие существуют способы измерения твердости? |
|
и макрошлифов. |
||||
|
|
|
|
|
5. |
Охарактеризуйте наблюдаемые структуры. |
|
|
|
|
|
|
Содержание отчета: |
||
|
|
|
|
|
1. |
Краткая характеристика макроанализа |
|
|
|
|
|
|
2. |
Основные характеристики изломов металлов и |
|
|
|
|
|
|
|
сплавов. |
|
|
|
|
|
|
3. |
Описание методики исследования макрошлифов и |
|
|
|
|
|
|
|
изломов |
|
|
|
|
|
|
4. |
Фотографии и описание изломов и макроструктур |
|
|
|
|
|
|
|
исследованных образцов. |
23 |
24 |
Характеристики макроанализа
Макроскопический анализ заключается в определении строения металлов невооруженным глазом или при небольших увеличениях (до 30 крат). В этом случае можно одновременно наблюдать большую поверхность заготовки, что часто позволяет судить о качестве металла и определять условия предшествующей обработки, влияющие на сплошность металла и особенности его строения, затвердевания, а также характер и качество обработки, применявшейся для придания детали окончательной формы и свойств (литье, обработка давлением, сварка, резание).
Макроанализ в отличие от микроанализа не позволяет определить всех особенностей строения металла. По данным макроанализа можно выбрать те участки изучаемой поверхности, которые надо подвергнуть дальнейшему микроскопическому исследованию.
Результаты макроскопического исследования можно зафиксировать, получив снимок макроструктуры исследуемого места детали или заготовки. Для этой цели применяют специальные установки, позволяющие проводить съемку плоских и рельефных объектов при увеличении от 0,5 до 20 крат.
Макростроение можно изучать не только непосредственно на поверхности металла (например, отливок, поковок), но и в изломе заготовки (детали), а также после предварительной подготовки исследуемой поверхности, заключающейся в ее шлифовании и травлении специальными реактивами. Шлифованный и протравленный образец называют макрошлифом; если макрошлиф протравлен в поперечном сечении детали, то его иногда называют темплетом. На шлифованной поверхности не должно быть загрязнений, следов масла и т.п.
25
Макроанализ излома металла
Излом может быть разным по форме, виду и способности к отражению света, следовательно, различаться в зависимости от состава металла, его строения, отдельных дефектов, условий обработки и напряженного состояния, при котором произошло разрушение образца (детали). Поэтому анализ излома позволяет установить многие особенности строения, а в ряде случаев и причин хрупкого или вязкого разрушения.
Наиболее часто наблюдаются характеристики излома сталей и других материалов. По форме различают излом:
1)ровный, блестящий – характерен для хрупкого состояния, когда разрушение произошло без видимой пластической деформации;
2)с выступами или чашечкой - для вязкого состояния.
Это описание излома может измениться в зависимости от условий разрушения. Так, излом, происходящий при кручении, наоборот, ровный и перпендикулярен оси образца у вязкого металла и сложной формы (по винтовой линии) у хрупкого.
Анализ строения излома более полно характеризует поведение металла при разрушении. По этому признаку различают излом:
1)зернистый, или кристаллический (блестящий с фасетками); он наблюдается при хрупком разрушении сталей пониженной вязкости (в том числе закаленных со значительным перегревом) и сталей, испытанных ниже порога хладноломкости;
2)матовый или волокнистый – зерна в этом случае не видны; такой излом наблюдается при вязком разрушении, которому предшествовала значительная пластическая деформация;
26
3) смешанный зернистый (или кристаллический) в одних участках и волокнистый в других. Он характерен для стали разрушенной в переходном температурном интервале между верхним и нижним порогами хладноломкости или прокалившейся не полностью; в этом случае в закаленной зоне излом матовый (фосфоровидный), а в середине – зернистый (или кристаллический). Смешанный излом наблюдается также в условиях усталостного разрушения.
Макроанализ шлифов
На макрошлифах при проведении макроанализа выявляют:
1) нарушение сплошности металла: подусадочную рыхлость, центральную пористость, свищи, подкорковые пузыри, межкристаллитные трещины; трещины, возникающие при обработке давлением и термической обработке; флокены, дефекты сварки (в виде непроваров, газовых пузырей);
3)дендритное строение, зону транскристаллизации, размеры и ориентацию зерен в литом металле;
4)химическую неоднородность литого металла (ликвации) и присутствие в нем грубых инородных включений;
5)волокнистую структуру деформированного
металла;
6)структурную или химическую неоднородность металла, созданную термической, термомеханической или химико – термической обработкой.
Для определения дефектов, нарушающих сплошность стали, применяют реактивы глубокого травления и реактивы поверхностного травления. Реактивы глубокого травления сильно воздействуют на поверхность. Агрессивное действие концентрированных кислот и их
27
смесей неодинаково на отдельных участках металла; оно интенсивнее с более развитой поверхностью, т.е. спорами, раковинами, трещинами и концентрацией напряжений, а также на участках, неоднородных по составу и структуре вследствие ликвидации. Поэтому после травления макрошлиф имеет избирательно протравленную поверхность, на которой видны трещины и пористость. Реактивы поверхностного травления хорошо выявляют сравнительно крупную пористость, например в сварных заготовках, а также определяют характер ликвидации и фигур течения металла, но они не могут заменить реактивов глубокого травления для определения флокенов, а также трещин, рыхлости и пор, не выходящих на поверхность. Преимущество реактивов поверхностного травления состоит в их меньшей агрессивности и простоте обращения с ними. Эти реактивы широко используют, особенно при макроанализе деталей из низко- и среднеуглеродистых сталей.
Контрольные вопросы
1.Что такое макрошлиф, как его готовят?
2.Что позволяет установить макроанализ поверхности излома?
3.Какие бывают виды излома в зависимости от поведения металла при разрушении?
4.Какой излом характерен для закаленных сталей?
5.Что можно выявить при исследовании макрошлифов?
6.С какой целью используют реактивы глубокого и поверхностного травления?
7.В чем преимущество реактивов поверхностного травления? Для каких материалов их используют?
28
Лабораторная работа № 4
МЕТАЛЛОГАФИЧЕСКИЕ ИССЛЕДОВАНИЯ МИКРОСТРУКТУРЫ МЕТАЛЛОВ И СПЛАВОВ
Цель работы:
1. Изучение методики микроскопического анализа структуры металлов и сплавов.
2.Изучение типичных структур некоторых металлов и сплавов (углеродистой, легированной сталей, цветных металлов, чугунов).
3.Оценка величины зерна стали.
Оборудование и материалы: Металлографический микроскоп ЛВ-34 или РВ-21-1, видеоокуляр DM130 или цифровая фотокамера, компьютер, монитор, набор микрошлифов сталей, цветных металлов и чугуна, фотографии микроструктур сталей.
Задание:
1.Изучить теоретическую часть работы.
2.Ознакомьтесь с устройством и работой металлографического микроскопа.
3.Определите общее увеличение микроскопа с заданными объективом и окуляром.
4.Исследуйте под микроскопом шлифы углеродистых и легированных сталей, цветных металлов, чугунов, сделайте фотографии наблюдаемых структур.
5.Определите характерные признаки фазы в наблюдаемых структурах.
6.Произведите оценку величины зерна.
Содержание отчета:
1.Назначение микроанализа.
2.Методика и результаты определения общего увеличения микроскопа.
29
3.Фотографии структур исследованных сплавов с их краткой характеристикой.
4.Определение величины зерна по фотографии
микроструктуры стали.
Микроскопический анализ заключается в исследовании структуры материалов при больших увеличениях с помощью микроскопа. Наблюдаемая структура называется микроструктурой. В зависимости от требуемого увеличения в микроскопах используют:
1.Белый свет и обычные оптические системы, меняющиеся комбинацией стеклянных линз и призм (оптическая микроскопия). Оптические микроскопы
обеспечивают увеличение до 2000 раз при разрешающей способности 0,2·10-3 мм.
2.Поток электронов, для создания оптических систем
вкоторых необходимо применять электромагнитные или электростатические линзы - электронная микроскопия. В
электронных микроскопах увеличение достигает 20000 раз, а разрешающая способность (8-10)·10-7 мм.
Микроанализ позволяет определить форму и размер кристаллических зерен, из которых состоит металл или сплав; изменение внутреннего строения сплава под
влиянием механической, термической или химикотермической обработки; микродефекты материала – микротрещины, неметаллические включения – сульфиды, оксиды и др.; характер обработки металла и т.д.
Изучение микроструктуры проводят на микрошлифах, которые получают вырезкой образцов из исследуемого материала и специальным образом подготавливают поверхность для микроанализа.
В зависимости от цели исследования и формы исследуемой детали выбирают место вырезки образцов сравнительно небольших размеров: диаметром 10 – 15 мм при высоте 10 – 20 мм. Затем, используя наждачный круг
30
или напильник, добиваются плоской поверхности, которую шлифуют вручную или на специальных станках применяя крупнозернистые, а затем мелкозернистые шкурки. После шлифования образец полируют для удаления мелких рисок, оставшихся после шлифования. Полирование ведут на полировальном станке, вращающийся диск которого обтянут материалом (фетр, бархат и т.п.). При полировании используют различные абразивные вещества (окись хрома, окись алюминия и т.д.), которые периодически наносят в виде водной суспензии на материал. Полированную поверхность подвергают травлению определенным химическим реактивом для выявления микроструктуры сплава. Для выявления структуры сталей и чугунов после различных видов термической и химико-термической обработки широко используется 2 – 4 % спиртовой раствор азотной кислоты.
Приготовленные микрошлифы исследуются с помощью металлографического микроскопа, который позволяет рассматривать непрозрачные тела в отраженном свете.
Микроскоп представляет собой оптическое устройство, состоящее из двух увеличивающих систем – объектива и окуляра.
Объектив, представляющий собой сложное сочетание линз, расположенных в одной оправе, дает действительное увеличение обратное изображение микроструктуры.
Окуляр представляет собой лупу с увеличением до 20 раз и предназначен для увеличения изображения, полученного объективом.
Общее увеличение, которое дают микроскопу совместно объектив и окулятор при визуальном наблюдении, равно
Nm=Nоб·Nок=L/Fоб·250/Fок,
31
где Fоб, Fок – фокусные расстояния объектива и окуляра;
250 – нормальное расстояние для зрения, мм; L – оптическая длина тубуса.
Определение величины зерна. Существует много методов определения величины зерна.
Наиболее доступные - методы визуальной оценки, площадей и случайных секущих. Величина действительного зерна, т.е. зерна, которое имеет сплав в условиях эксплуатации и которое образуется при данном виде обработки, определяется на микрошлифах путем травления или на фотографиях микрошлифов.
Размер зерна определяют следующими методами:
1)Визуальным – сравнением видимых под микроскопом зерен при увеличении в 100 раз с эталонными или стандартными шкалами;
2)Подсчетом числа зерен, приходящихся на единицу поверхности шлифа, с определением среднего диаметра и средней площади зерна;
3)Подсчетом числа пересечений границ зерен отрезками прямых с определением среднего условного диаметра (в случае равноосных зерен), числа зерен в 1 в случае неравноосных зерен.
Следует заметить, что в случае разнозернистой структуры средние размеры (диаметр, площадь зерен) не являются характеристиками структуры.
Подсчет числа зерен проводят на матовом стекле камеры металломикроскопа или на микрофотографиях, в которых поле зрения ограничено одной из плоских фигур – окружностью, квадратом или прямоугольником, площадь
которых отвечает 0,5 мм2 поверхности шлифа при увеличении в 100 раз. Общее число зерен на этой площади
32
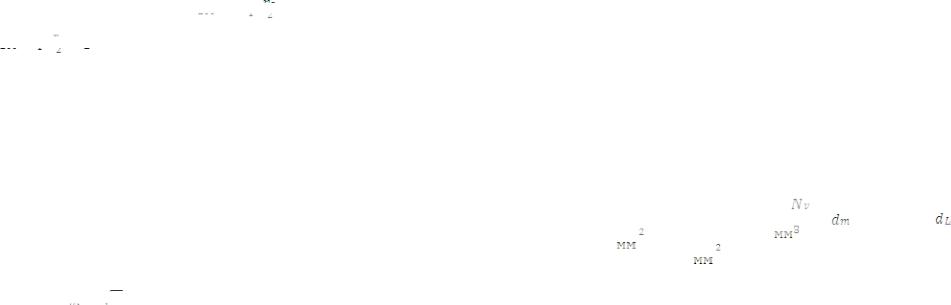
и при этом увеличении =
+
для круга или
=
+
для прямоугольника или квадрата, где n1 -
число зерен, попавших внутрь выбранной плоской фигуры, а n2 - число зерен, пересеченных ее границами. Число зерен, приходящихся на 1 мм2 площади шлифа, равно 2n100 . При увеличении, отличном от 100, число зерен, приходящихся на 1 мм2 поверхности шлифа, подсчитывают по формуле m=2(g/100)2ng, где ng - число зерен, находящихся внутри плоской фигуры, ограничивающей поле зрения на шлифе или фотографии при увеличении g. Подсчет общего числа зерен проводят не менее чем в трех характерных местах шлифа и по ним рассчитывают их среднее арифметическое значение. Среднюю площадь сечения зерна α и диаметр зерен вычисляют по формулам α=1/m и =1/
. Сравнение этих значений m, α и dm с указанными в табл.1 определяют номер зерна.
В табл.1 приведены результаты расчета параметров зерна: для их номеров (G) от 3-го до 14-го – средней площади сечения, среднего числа зерен на площади в 1 мм2 и в объеме 1 мм3,среднего и условного диаметра зерна.
Для определения среднего условного диаметра dL в случае равноосных зерен или числа зерен в 1 мм3 в случае неравноосных зерен применяют метод подсчета пересечений границ зерен отрезком прямой на матовом стекле микроскопа или микрофотографии. Проводится несколько отрезков произвольной длины так, чтобы каждый из них пересекал не менее 10 зерен, а увеличение микроскопа (или микрофотографии) должно быть таким, чтобы на исследуемой поверхности было не менее 50 зерен. При этом подсчитывают точки пересечения прямых линий с границами зерен ( или число пересеченных зерен). Средний условный диаметр зерна определяют по формуле
33
dL = L/N, где L- суммарная длина отрезков, выраженная в миллиметрах натуральной величины на шлифе, а N– суммарное число зерен, пересеченных отрезками длинной L. Чем больше число пересеченных зерен, тем больше номер зерна. Но при этом надо учитывать и принятые увеличения.
|
Расчет параметров оценки зерна |
Таблица 1 |
|||
|
|
||||
Номер |
Средняя |
Среднее |
Среднее |
Средний |
Средний |
зерна,G |
площадь |
число |
число |
диаметр |
условный |
|
сечения |
зерен m |
зерен |
зерна |
диаметр |
|
зерна α, |
на |
в 1 |
, мм |
зерна , |
|
|
площади |
|
мм |
|
|
|
1 |
|
|
|
|
|
|
|
|
|
|
|
|
|
|
|
-3 |
1 |
1 |
1 |
1,0 |
0,875 |
-2 |
0,5 |
2 |
2,8 |
0,707 |
0,650 |
-1 |
0,25 |
4 |
8 |
0,5 |
0,444 |
0 |
0,125 |
8 |
22,6 |
0,353 |
0,313 |
1 |
0,0625 |
16 |
64 |
0,250 |
0,222 |
2 |
0,0612 |
32 |
181 |
0,177 |
0,157 |
3 |
0,0156 |
64 |
512 |
0,125 |
0,111 |
4 |
0,00781 |
128 |
1448 |
0,088 |
0,0783 |
5 |
0,00390 |
256 |
4096 |
0,062 |
0,0553 |
6 |
0,00195 |
512 |
11585 |
0,044 |
0,0391 |
7 |
0,00098 |
1024 |
32768 |
0,031 |
0,0267 |
8 |
0,00049 |
2048 |
92682 |
0,022 |
0,0196 |
9 |
0,000244 |
4096 |
262144 |
0,015 |
0,0138 |
10 |
0,000122 |
8192 |
741485 |
0,011 |
0,0099 |
11 |
0,000061 |
16384 |
2097152 |
0,0079 |
0,0069 |
12 |
0,000031 |
32768 |
5931008 |
0,0056 |
0,0049 |
13 |
0,000015 |
65536 |
16777216 |
0,0039 |
0,0032 |
14 |
0,000008 |
131072 |
47449064 |
0,0027 |
0,0027 |
Число неравноосных зерен в 1 мм3 определяют таким же образом на шлифах, изготовленных вдоль и поперек главной оси симметрии, а отрезки прямых проводят
34
параллельно осям симметрии. Среднее число неравноосных зерен в 1 мм3 объема шлифа вычисляют по формуле, где 0,7 – коэффициент, учитывающий неравноосность зерен; - числа пересечений границ зерен в направлениях x, y и z на 1 мм длины отрезков.
В производственных условиях в большинстве случаев применяют метод визуальной оценки величины зерна в стали. Стандартные номера зерен от 1 до 10 определяются сравнением видимых зерен под микроскопом при 100кратном увеличении со шкалой стандартных размеров зерна (табл.2.2). Если размер зерна исследуемого образца выходит за пределы номеров зерен 1-10 шкалы, пользуются другими увеличениями. Номера зерен -3, -2, -1, 0 при 25-кратном увеличении соответствуют номерам 11, 12, 13, 14; при 400-кратном увеличении – номерам 7,8,9,10.
Таким образом, эталонная шкала стандартных размеров зерен состоит из 18 номеров. Зерна с номером до 4 считаются крупными, а свыше 6 – мелкими.
Число зерен должно быть не менее 50. Если их меньше, то используют меньшее увеличение.
Таблица 2 Пересчет номера зерна на стандартное увеличение (х100)
при использовании увеличений от 25 до 800
Увели- |
|
|
|
|
|
|
|
Номер зерна (баллы) |
|
|
|
|
|
|
|||||
чение |
- |
- |
- |
0 |
1 |
2 |
3 |
4 |
5 |
6 |
7 |
8 |
|
9 |
10 |
11 |
12 |
13 |
14 |
|
3 |
2 |
1 |
|
|
|
|
|
|
|
|
|
|
|
|
|
|
|
|
25 |
1 |
2 |
3 |
4 |
5 |
6 |
7 |
8 |
9 |
10 |
- |
- |
|
- |
- |
- |
- |
- |
- |
50 |
- |
- |
1 |
2 |
3 |
4 |
5 |
6 |
7 |
8 |
9 |
10 |
- |
- |
- |
- |
- |
- |
|
200 |
- |
- |
- |
- |
- |
- |
1 |
2 |
3 |
4 |
5 |
6 |
|
7 |
8 |
9 |
10 |
|
|
400 |
- |
- |
- |
- |
- |
- |
- |
- |
1 |
2 |
3 |
4 |
|
5 |
6 |
7 |
8 |
9 |
10 |
800 |
- |
- |
- |
- |
- |
- |
- |
- |
- |
- |
1 |
2 |
|
3 |
4 |
5 |
6 |
7 |
8 |
35
Контрольные вопросы
1.С какой целью проводится микроанализ сплавов?
2.Опишите методику подготовки микрошлифов.
3.На чем основаны оптическая и электронная микроскопия?
4.Сравните основные характеристики оптических и электронных микроскопов (увеличение, разрешающая способность).
5.Опишите устройство оптического микроскопа.
6.Как рассчитать общее увеличение микроскопа?
7.Какие методы используют для определения величины зерна? Опишите использованную в лабораторной работе методику.
СОДЕРЖАНИЕ
Лабораторная работа № 1. КРИСТАЛЛИЗАЦИЯ МЕТАЛЛОВ И СПЛАВОВ ………………………………… 1
Лабораторная работа № 2. МЕТОДЫ МЕХАНИЧЕСКИХ ИСПЫТАНИЙ МАТЕРИАЛОВ …………………………. 10
Лабораторная работ № 3. МЕТОДЫ МАКРОСТРУКТУРНОГО АНАЛИЗА МЕТАЛЛОВ И СПЛАВОВ ………………………………………………… 24
Лабораторная работа № 4. МЕТАЛЛОГРАФИЧЕСКИЕ ИССЛЕДОВАНИЯ МИКРОСТРУКТУРЫ МЕТАЛЛОВ И СПЛАВОВ……………………………………………….. 29
36
МЕТОДИЧЕСКИЕ УКАЗАНИЯ
к выполнению лабораторных работ
по дисциплине «Материаловедение» для студентов направления 15.03.01 «Машиностроение» (профиль «Оборудование и технология сварочного производства») очной и заочной форм обучения
Составитель Селиванов Владимир Федорович
В авторской редакции
Компьютерный набор В.Ф. Селиванова
Подписано к изданию 20.10.2016.
Уч.-изд. л. 2,2. «С»
ФГБОУ ВО «Воронежский государственный технический университет»
394026 Воронеж, Московский просп., 14
37