
Авдеев Е.Ф., Смирнова В.О. Конспект лекций по курсу Механика жидкости и газа eng
.pdfpoint above above ̇set to remind that the components of the tensor tives of speeds, according to the rule:
|
|
( |
|
|
|
) |
|
|
|
||||
4.2. Dynamic Equations in Voltages |
|
|
|
|
̇expressed through deriva-
(4.10)
|
Taking into account the presented classification of forces, we write down the theorem of |
||||||||||
quantities of motion (4.1) for an arbitrary liquid volume τ in the form: |
|
||||||||||
|
|
|
|
|
|
|
|
∫ ̅ |
∫ ̅ |
∫ ̅ |
(4.11) |
|
|
|
|
|
|
|
|
||||
|
where the left side, due to the independence of time and volume, |
can be rewritten |
|||||||||
as∫ |
|
as |
|
( |
) |
, according to the law of conservation of mass. |
|
||||
|
|
|
|||||||||
|
After substituting into (4.1) the expression for the voltage (4.8) and passing from 3 inte- |
grals over the surface to integrals over the volume, all terms will consist of integrals over the volume. If we write all integrals over the volume into one, it will be equal to zero. As is known, the integral can be equal to zero due to the domain of integration or in the case of equality to zero of the integrand. In this case, we must accept the latter, since the volume of soap is taken arbitrary. As a result, we get:
̅ |
̅ |
|
|
̅̅̅̅ |
|
̅̅̅̅ |
̅̅̅̅ |
(4.12) |
|
|
|
|
|
|
|
|
|
||
|
|
|
|
|
|
|
|
Differential equation (4.12), expressing the law of conservation of momentum is called the equation of dynamics in voltages. It has a simple and literal physical meaning: full acceleration consists of acceleration due to mass forces and acceleration due to surface forces. In the projections on the coordinate axes, these will be three equations with nine. Scalar stresses, in which
only six are independent, since |
. |
|
|
|
|
4.3. Concept of pressure |
|
|
|
|
|
In the stress tensor with components |
|
and , stresses with the same indices physically |
|||
mean the normal components of the stresses, with different - the tangential stresses. |
|
||||
Equating in (4.9) linear invariants of tensors, we get: |
̅ |
||||
Whence for incompressible fluid ( |
̅ |
): |
|
|
|
|
|
|
|
. |
(4.13) |
|
|
|
|
This arithmetic average of three mutually orthogonal stresses, taken with a reverse sign, is taken to be the concept of pressure in a real (viscous) fluid; the hypothesis makes sense, since it is not from any considerations that the equality of orthogonal stresses in a viscous fluid cannot be proved.
In the case of a fluid model for which friction stresses are assumed to be zero, only diagonal orthogonal stresses remain in the stress tensor. It is easy to prove their equality. For the pressure take their total value:
(4.14) Exactly the same will be the concept of pressure at rest, but already real fluid. From here follow two known properties of pressure: it is normal to the wall and does not depend on direc-
tion.
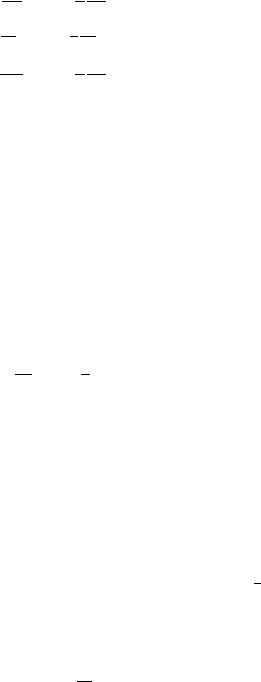
4.4. Equations of motion of a viscous fluid (Navier-Stokes)
Substituting the stresses from (4.9), in the case of constant density, into the dynamics equations in the stresses (4.12), we obtain the equations of motion of the Navier-Stokes viscous fluid:
(4.15)
where – kinematic viscosity, – Laplace operator. This kind of equation was obtained in 1822 by Navier and independently by Stokes in 1842. Their common analytical solution still does not exist, there are only solutions for simple special cases.
4.5. Equations of motion of an ideal fluid L. Euler
The need to introduce a model of an ideal fluid is generally caused by the reduction of the number of unknowns to the number of equations.
With known mass numbers, the number of unknown parameters will be 11: three components of velocity, density, 6 unknown stresses and temperature. And there will be 6 equations, including the equations of continuity of motion, energy and state. For an ideal fluid model, the 6 voltages are replaced by one concept of pressure. The number of unknowns is equal to the number of equations.
Dynamics equations in voltages for an ideal liquid or gas model have the form:
̅ |
̅ |
(4.16) |
|
This is a vector record of the classical equations of L. Euler. Equations (4.16) allow for a particular analytical solution.
4.6. Integral D. Bernoulli and the area of his reality
The solution of equation (4.16) we find under the conditions:
-stationary current;
-mass forces have the potential that is ̅
- Barotropy takes place ( |
( )) |
|
|
|
( |
) |
|
||
And there is a pressure function |
∫ |
|
, from where |
For the above conditions of equation (4.16) we rewrite as:
( |
|
) |
̅ ̅ |
(4.16’) |
|
When writing (4.16 ’) to take equal to zero, we get the decision:
(4.17)
To avoid confusion, further, with the D. Bernoulli equation for a viscous fluid flow of finite cross section, we call the solution (4.17) the Bernoulli integral. From the energy point of view, the Bernoulli integral expresses the law of conservation of the mechanical energy of a unit mass.
However condition ̅ ̅ |
̅ |
|
̅ will impose significant restrictions on the |
|
|||
scope (4.17): |
|
|
|
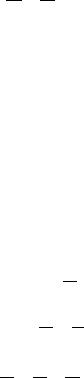
а) in case of irrotational movement ̅ |
Bernoulli integral can be applied to any points, |
||
that is, the sum |
|
will be the same; |
|
|
б) in the case when ̅ and ̅ parallel, the movement occurs along the vortex line;
в) the right side (4.16 ’) can be zeroed by scalar multiplication by a vector ̅.
Then in the left part of the work ̅ or ̅ , which is derived from b in direction ̅ or ̅.
In the first case, the sum is saved only for points on the same streamline, and in the second case only for points along the vortex line.
Knowledge of the correct application of the Bernoulli integral is of paramount importance, otherwise you can make false conclusions for the dependence of speed and pressure.
For a liquid at rest, we obtain the basic equation of hydrogasostatics, setting the velocity
to zero: |
|
. |
(4.18) |
The forces of gravity can be neglected in the case of a low density of the medium and a small vertical length of the flow, and at a high density - only with a small difference of two points.
4.7. Special cases of the Bernoulli integral
In the simplest case, at constant density and the action of only gravity, the Bernoulli integral has the form:
(4.19)
where z is the vertical coordinate of the point. It does not matter where to start the counting of this coordinate, since in the equation written for two points there will be a difference of coordinates.
In case of neglect of mass forces, the Bernoulli integral will be even simpler.:
|
|
|
(4.20) |
|
|
|
|
If we determine the integration constant at the stagnation point ( |
), we ob- |
tain the expression for the experimental determination of the speed through the difference of pressure braking and static pressure:
√ |
( ) |
(4.21) |
|
4.7.1. Isothermal process in gas
(4.22)
Substituting the density in the integrand for the pressure function by (4.22) we find:
(4.23)
Bernoulli integral will have the form:
. |
(4.23) |
Often used to calculate gas pipelines.
4.7.2. Adiabatic process in gas
( |
|
) ⁄ |
(4.24) |
|
Adiabatic processes are closest to real processes, since even at low velocities for gas, heat exchange with the environment does not have time to occur.

The pressure function in this case will be equal to:
[( |
|
) |
] |
(4.25) |
|
Neglecting the mass forces, after determining the constant integration at the stagnation point, we obtain a formula for experimentally determining the velocity:
√ |
|
|
|
|
|
|
|
|
|
|
|
|
|
[ |
( |
|
) ]. |
(4.26) |
|||
|
|
|
Known as the formula of Saint-Venant and Wenzel.
4.8. Ratios for resting fluid
Assuming in the considered special cases of the Bernoulli integral a velocity equal to zero, we obtain relations for a liquid or gas at rest.
At constant density and the action of gravity only, we obtain (called in hydraulics) the basic equation of hydrostatics:
(4.27)
For two points (4.27) with the same density, we find the Pascal law, which says: the change in pressure at any point is transmitted to other points without change. It can be proved in the case of two immiscible liquids, when there is a different density at the points, by introducing the third point at the interface of the liquids.
In the case of isothermal gas, we will have:
|
|
|
|
|
|
|
|
|
. |
(4.28) |
|
|
|
|
|
|
|
|
|
||
The dependence (4.28) is used in barometric leveling in the atmosphere, which consists in |
||||||||||
determining the increase of one point above another |
( |
): |
|
|||||||
|
|
|
[ |
|
|
( |
)] |
(4.29) |
||
|
|
|
|
|||||||
where |
– pressure and density at the point with coordinate |
. With a big differ- |
||||||||
ence |
he atmosphere is divided into layers, the temperature in which they take a con- |
|||||||||
stant. |
|
|
|
|
|
|
|
|
|
|
4.9. D. Bernoulli equation for a flow of a finite cross section of a viscous fluid
4.9.1. Smoothly changing current and its main properties
A smoothly changing current is a current, with slightly curved current lines or with a large radius of curvature. Directing the X-axis along the flow, we can approximately consider the full speed equal to its projection on the X-axis, and the transverse projections of the velocity to be taken equal to zero. Substituting these conditions into the Navier-Stokes equations (4.15), we obtain that in the plane of the living section (x; y) the equations will coincide with the equations of statics, which means that the basic hydrostatic equation holds in this plane:
(4.30)
This result will be the main property of smoothly changing currents. It is of fundamental importance in the derivation of the Bernoulli equation for the whole flow.
We also clarify that a strictly live section of a flow is a section, at each point of which the streamlines are directed along the normal. Therefore, the curved current lines will correspond to a curved living section, but for smoothly varying movements it is taken as flat..
4.9.2. Generalization of the Bernoulli integral to the flow of a finite section
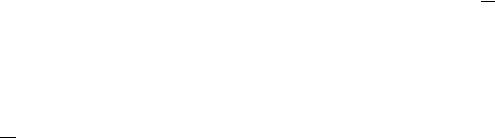
Let us proceed from the understanding that each term of the Bernoulli integral (4.19) rep-
resents energy per unit weight: |
|
– energy potentials due to mass forces and pressure, |
||||
|
||||||
– kinetic energy. |
|
|
|
|
|
|
Therefore, the expression: ∫ ( |
|
|
|
|
) |
|
|
|
It will be the energy of the weight flow rate through the living sections σ. After dividing it by the weight flow rate recorded through the average speed, we obtain energy per unit of weight already for the whole flow. Denote by He. Based on the basic property of a smoothly changing
flow, the term( ) can be expressed from under the integral, and ∫ делением на
get 1.
Another integral replacing in the form:
∫
where α is a coefficient that shows how much kenetic energy of a stream, recorded through true velocities, differs from kinetic energy recorded through average velocities.
Then the energy per unit of weight of the flow will be:
|
|
|
|
|
|
|
(4.31) |
|
|
|
|
|
|
|
|
For an ideal fluid model for a single section, it would be |
, for another |
. However, |
|||||
in a real thread |
, as part of the energy will go to overcome resistance: |
|
(4.32) Equation (4.32) will be an abbreviated notation of the Bernule equation for the flow of real fluid. After substitution, the expression for He1 and He2 according to (4.31), we obtain the
Bernoulli equation in expanded form:
|
|
|
|
|
|
|
|
|
|
(4.33) |
|
|
|
|
|
|
|
|
|
|
|
It should be noted that the coordinates are now |
|
and |
refer to cross section points |
|||||||
where pressure |
. Usually take |
and |
coinciding with the center of gravity of the |
sections. In hydraulics it is strictly proved that in round pipes for laminar flows α = 2, and for turbulent ones α = (1.01 ÷ 1.1), due to the difference in the laws of velocity distribution (parabolic and logarithmic).
5. Hydraulic resistance |
|
The power of the pumps on the shaft is determined by a simple formula: |
|
[ ] |
(5.1) |
where Q is the volumetric flow rate, and ∆p is the pressure loss (Pa) from the pump to the point of medium delivery. It is fundamentally important to understand that pressure losses are determined from the Bernoulli equation written for two flow sections:
|
( |
) |
|
(5.2) |
|
|
|||
It is clear from (5.2) that if the first term is negative, the same will happen with the se- |
||||
cond term, if |
. Last added meaning loss of pressure to overcome resistance. Thus, |
without determining the pressure loss to overcome the resistances, it is impossible to find the total ∆p.
Due to the different nature of resistances, they are divided into two types: local resistances ∆pm and resistances due to friction (in length) ∆pl. Both types of resistance are easily determined through average speed.
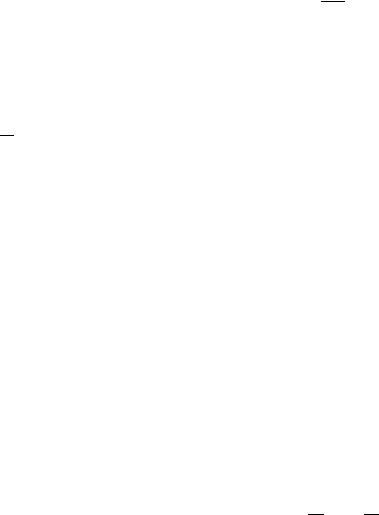
5.1. local hydraulic resistance
Local resistances arise due to local transmission, which causes is-curvature of the direction of movement (expansion, contraction, turns, gate valves, etc.), since changing the direction of movement requires energy, which in this case can only be borrowed from the flow. In very rare cases, it is possible theoretically to find an expression for these pressure losses.
One of these cases is the sudden expansion in channels, called in hydraulics the Borda theorem:
|
|
( |
) |
|
|
|
(5.3) |
|||
|
|
|
|
|
|
|
|
|
||
|
|
|
|
|
|
|
|
|
||
whence the general formula for calculating local resistance will follow. |
||||||||||
If in (5.3) out of the bracket or |
, get (provided |
|
|
) |
||||||
( |
|
) |
|
|
( |
|
|
) |
|
(5.4) |
|
|
|
|
|
|
where the expression in parentheses characterizes the geometry of sudden expansion (σ2 and σ1 are the areas of wide and narrow section), – average speeds in wide and narrow sections.
Based on (5.4), the generally accepted formula for the dependence of fission losses on local resistance will be:
(5.5) where – coefficient of local resistance, in most cases determined experimentally. Judg-
ing by (5.4), for the same resistance value |
will be different depending on the dynamic pres- |
|||||||
sure |
|
|
pressure loss recorded. |
|
( |
|
) |
( |
|
|
|
||||||
|
In |
particular, for sudden expansion |
can be taken |
|
||||
|
|
) . If the reference books do not indicate through which dynamic pressure it is necessary to
express the pressure loss, record through dynamic pressure behind the local resistance, counting in the direction of flow.
In the design calculations it is extremely important to know the following circumstance. If, according to the reference data by summation, the losses for all local resistances are found, then the actual losses may be less, which will lead to an increase in the design value of the flow rate. The fact is that the total pressure loss can be equal to the real, only with a certain distance of local resistances from each other. This effect was discovered relatively recently and was called the effect of the mutual influence of local resistance. In particular, in experiments with two washers conducted by the authors of these lectures at the Department of Thermal Physics of the Institute of Thermal Physics, NRNU MEPhI, the total coefficient of local resistance increases two and a half times the distance between the washers compared to their dense location. The effect can be turned in favor when it is necessary to create the required channel resistance in the experimental simulation of the processes in full-scale plants.
5.2. Channel friction resistance
The loss of pressure to overcome friction (in length) depends primarily on the mode during the flow - laminar or turbulent, since the friction stress for laminar flows is usually determined by the Newton formula:
(5.6)
where and – dynamic and kinematic viscosities, and in turbulent flows to добавляется напряжение , due to the mixing of macro volumes. Moreover, in some cases, if we present τт by analogy with (5.6):

̅ |
(5.7) |
|
, that is, molecular viscosity can be neglected. The latter circumstance must be used very carefully, analyzing the physics of the process.
5.2.1. Laminar flow
The loss of pressure on friction in the channels began to be used in the technique after the French physician Poiseuille received the formula for the volume flow of blood Q in large human covessels.
|
|
|
(5.8) |
|
|
||
where |
– pressure loss along the length of the vessel , – vessel radius. |
Here we omit an interesting analysis of this formula, indicating which parameter the drug should interact with for an urgent increase in the flow of blood into the organs and which one during conservative treatment.
If in (5.8) to replace the flow through the average speed, it is easy to get:
|
|
|
|
|
|
|
|
(5.9) |
|
|
|
|
|||||
where |
|
, – diameter. |
||||||
|
After introducing the concept of the coefficient of friction resistance λ, as a dimensionless quantity that shows how much dynamic pressure is lost due to friction on the length of the pipe, equal to its diameter:
(5.10)
and comparisons (5.9), (5.10), we find the expression for λ in a round pipe.
(5.11)
In the classical literature, on the basis of solving the Navier-Stokes equation, an expression has been obtained for the channels of elliptic, triangular, rectangular, and square sections, which can be written in general form:
(5.12)
where the constant depends on the cross-sectional shape of the channel. In the General case, the pressure loss on friction is written through λ:
(5.13)
and called in the classic Darcy-Weisbach formula.
The physical law of resistance follows from formulas (5.13) and (5.12): during laminar flow in channels, the pressure loss due to friction depends on the average velocity in the first degree (linearly).
In the record of formula (5.13), a new dimension d_g is introduced, which is characteristic of the transverse size of channels of non-circular cross section. The dependence for its calculation follows from the analogy for a round pipe, after introducing the concept of hydraulic radius R_g, as the ratio of the cross-sectional area of a channel to its wetted perimeter:
(5.14)
If you count |
for a round pipe of radius a, we get: |
|
|
|
whence follows the gen- |
|
|
eral formula for calculating the hydraulic diameter:
(5.15)
In order to avoid mistakes, we emphasize that only the perimeter that wets solid walls should be taken over the wetted perimeter. In particular, for cells of fuel rods with spacing of fuel rods with grids, its length will be equal to half the circumference of the fuel rod, and when

spacing the fuel rods with wire winding, the wire circumference must be added to half the circumference of the fuel rods.
5.2.2. Turbulent flow
Due to the absence, for fundamental reasons, of a rational theory of turbulent flows, the form of recording friction losses during a turbulent flow in channels (5.13), obtained from the theory of laminar flows, is adopted. It remains to solve the problem of finding the dependence for λ.
If we follow the analogy with laminar flows, it all began with the velocity distribution, since the Poiseuille formula was derived from the parabolic velocity distribution in circular tubes of radius a
( )
first of all, it is necessary to establish the distribution of velocities in a turbulent flow, at least in round pipes. This will be of immediate practical importance, since the equipment of a nuclear power plant (and thermal power stations), including the reactor core, has a turbulent coolant (or working fluid).
We start with obtaining the velocity distribution in round pipes.
Prandtl, considering the transfer of the amount of motion in macroscopic volumes, obtained a formula for the friction stress in turbulent flows:
|
|
( |
̅ |
) |
(5.16) |
|
|
|
|||
|
where l is the path of mixing (the path that an elementary volume passes when its velocity |
||||
changes by the magnitude of the pulsation velocity), u |
is the averaged velocity. |
||||
|
Making two assumptions: |
|
|||
1) |
, |
( – distance from the wall, – empirical coefficient); |
|||
2) |
|
(wall stress). |
|
In fact, according to experiments, the mixing path increases from zero (on the wall) to l⁄a≈16 on the pipe axis. The friction stress, regardless of the mode in the flow, decreases from the wall by linear dependencies. By making these assumptions, Prandtl sought to obtain the logarithmic distribution of speeds established by personal experiments. The logarithmic law really
follows from (5.16): |
|
|
|
|||||||
|
|
|
|
|
|
|
( ) |
(5.17) |
||
|
|
|
||||||||
where |
√ |
|
– dynamic speed. |
|
|
|
||||
|
|
|
|
|||||||
|
|
|
|
|||||||
Integration |
constant cannot be determined from the condition on the wall ( |
) |
|
|
||||||
|
|
. This cannot be done by physical understanding, since the flow is laminar near the wall in
the region of low velocities. Laminar sublayer thickness |
. That is, the role of the boundary for |
|||||
the turbulent flow will be |
, где |
: |
|
|
||
|
|
|
|
|
( ) |
(5.18) |
|
|
|
|
The constant C is eliminated by subtracting from (5.7) and (5.18).
|
|
|
|
|
|
|
|
|
|
|
|
|
|
|
|
( |
|
|
) |
|
|
||
|
|
|
|
|
|
|
|
|
|
|
|
|
|
|
|
||||||||
The last expression, when you enter a parameter |
|
and using Newton's formula |
|||||||||||||||||||||
|
|||||||||||||||||||||||
for friction stress |
|
|
|
|
|
|
|
|
, rewritten as: |
|
|
|
( ) |
|
|||||||||
|
|
|
|
|
|
|
|
||||||||||||||||
|
|
|
|
|
|
|
|
|
( |
|
) |
|
|
(5.19) |
|||||||||
|
|
|
|
|
|
|
|
|
|
The final form (5.19) obtained on the basis of experimental data Nikuradze:
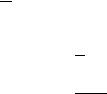
( |
|
) |
(5.20) |
|
from which, it is clear that:
( )
With experimental values |
. |
|
|
|||
However, formula (5.20) is valid for a hydraulically smooth wall of the pipe, where the |
||||||
bump of roughness |
. If |
, the same Nikuradze obtained a different dependence: |
||||
|
|
|
|
|
|
(5.21) |
|
|
|
|
Write formulas (5.20) and (5.21) for the pipe axis using the mean velocity deficit value.:
|
|
(experimental value, theoretical is – 3,75), get the expression for ( |
): |
|||||||||||
|
|
|||||||||||||
|
|
|
|
|
|
( |
|
|
|
) |
|
|
(5.22) |
|
|
|
|
|
|
|
|
|
|
|
|
||||
|
|
|
√ |
|
|
|||||||||
|
|
|
|
|
|
|
|
|
|
|
|
|||
at |
: |
|
|
|
|
|
|
|
|
|
|
|
|
|
|
|
|
|
|
|
|
|
|
|
|
|
|
. |
(5.23) |
|
|
|
|
|
|
|
|
|
|
|
|
|
||
|
|
|
|
√ |
( ( |
|
) |
) |
||||||
|
|
|
|
|
|
|
||||||||
|
|
|
|
|
|
|
|
|
Dependence (5.22) can only be represented graphically. This is the so-called Nikuradze schedule, which is given in all manuals on technical hydraulic engineering (hydraulics). And then an approximation of the graphical dependence for different ranges of Reynolds numbers in the region of turbulent flows was found:
|
|
|
|
|
, |
|
(5.24) |
|
|
|
|
|
|
||||
|
|
|
|
|
|
|
(5.25) |
|
|
|
|
|
|
|
|
||
Remembering these formulas is not the main thing, the main thing is the understanding |
||||||||
that for smooth hydraulic channels ( |
) depends only on the number of Re, for hydrau- |
|||||||
lically rough channels ( |
) does not depend on Reynolds number. The latter also confirms |
|||||||
the experimental graph Nikuradze. |
|
|
|
|
|
|
|
|
If you encounter a dependency in the directory |
( |
|
), then its use is possible when |
|||||
|
||||||||
. |
|
|
|
|
|
|
|
|
In the formula (5.23) |
– sand roughness, and it is always necessary to move from tech- |
|||||||
nical roughness k to sandy roughness |
, using reference data. |
|
|
One should not think that the pressure losses due to friction always depend on the average velocity in the square (5.13). If we substitute the corresponding expression for λ in (5.13), we obtain that for laminar flows the friction losses depend on the average velocity in the first degree, that is, linearly. In turbulent flow in hydraulically smooth channels to the power of 1, 75. A quadratic dependence appears only in the case of hydraulically rough channels.
Experimentally, physical laws of resistance are established very simply: by plotting
. The slope tangent will show the degree for average speed. Therefore, the indicator determines the flow regime and the choice of formula for λ.
The above is the essence of the Prandtl empirical theory for turbulent flow in pipes, which is used in the world practice of engineering calculations.
The determination of the friction drag coefficients in the channels of fuel assembly cells is also tied to the formulas obtained above, adjusted for the geometry of the fuel elements. The method of obtaining these dependencies belongs to the scientists of the SSC RF-FEI: academician V.I. Subbotin and Dr. of Sc. P.A. Ushakov.]
6. The thermal formula of the Bernoulli integral. The law of conservation and transformation. One-dimensional gas flow.
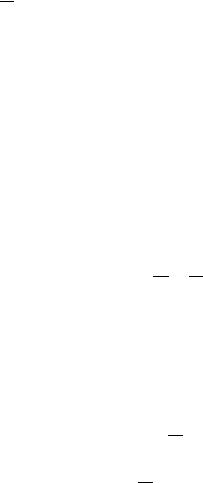
We apply the ideal gas model, neglecting friction. The gas flow parameters found in this assumption are quite acceptable for engineering estimates, due to the low dynamic viscosity of the gas.
The general problem, special cases of which have to be solved, is the ability to determine the thermodynamic parameters in arbitrary sections of the channel, according to known parameters in one of the sections and known areas of sections.
However, to close the system of equations, it is necessary to give a mathematical representation of the law of conservation and transformation of energy.
6.1 differential equation for the law of conservation and transformation of energy
The total time derivative of the total energy of a volume is equal to the sum of the powers due to the mass and surface forces, adding up with the amount of heat supplied (allocated) to the volume from the outside per unit time.
Mathematical dependence:
∫ ( |
|
) |
∫ ̅ ̅ |
∫ ̅ ̅ |
∫ |
(6.1) |
|
where u is the internal energy; q is the energy supplied from the outside to a unit of mass in a unit of time.
Acting mathematically, similarly with the law of conservation of momentum, we obtain the differential form of the record (6.1):
|
|
|
( |
|
|
|
) |
̅ ̅ |
|
|
( ̅) |
(6.2) |
||
|
|
|
|
|||||||||||
Where the factor P in the operation of divergence means the stress tensor during the tran- |
||||||||||||||
sition∫ ̅ ̅ ∫ |
( ̅) |
|
|
|
|
|
|
|
|
|
|
|||
Assuming adiabatic motion (q = 0) of a perfect gas ( |
|
|
) equation (6.2) has the form: |
|||||||||||
|
||||||||||||||
|
|
|
( |
|
|
) |
̅ ̅ |
̅ |
|
|
(6.3) |
|||
|
|
|
|
|
which, when considered together with a vector record, the equation of motion gives:
. |
(6.4) |
6.2. The thermal formula of the Bernoulli integral. Isentropic formulas
With the stationary motion barotropy, when the current lines and trajectories coincide, from (6.4) we obtain the relation between the enthalpy and the pressure function:
(6.5)
which gives grounds for writing the thermal formula of the Bernoulli integral.
(6.6)
In the approach of mass forces:
(6.7)
6.3. The concept of the speed of sound and the number M. Isentropic formulas
6.3.1 Setting a common task.
The general task, in relation to which other tasks will be its special cases (Fig. 6.1):
In one of the section of the channel A1 with arbitrary areas of sections A (x) along it, all thermodynamic parameters are known - density, pressure, temperature and speed of sound.