
LS-Sb89583
.pdf
(tкип = 90 °С), PCl3 (tкип = 75 °C). В качестве твердых источников используют пластины нитрида бора BN или пластины на основе компонента SiP2O7.
Схема установки для диффузионного легирования из жидкого источника показана на рис. 2.3. Установка представляет собой проточный кварцевый реактор 1, находящийся внутри термической печи 2. Пары диф-
фузанта подаются в реактор газом-носителем N2, пропущенным через барбо-
тер 3, заполненный жидким диффузантом BBr3 или PCl3 и помещенный внутрь термостабилизатора 4. В остальном схема аналогична установке термического окисления (см. рис.1.1).
Рис. 2.3. Схема установки диффузионного легирования из жидкого источника
В реакционную зону подаётся также сухой кислород. В горячей рабо-
чей зоне установки при температурах диффузии 900...1000 °С происходят следующие химические реакции:
∙ окисление паров диффузанта:
4BBr3 + 3O2 → 2B2O3 + 3Br2; ∙ окисление поверхности кремния:
Si + O2 → SiO2;
∙ образование боросиликатного стекла на поверхности кремния:
mSiO2 + nB2O3 → mSiO2·nB2O3.
На границе раздела стекла с кремнием идет реакция восстановления примеси из оксида бора:
11

2B2O3 + Si → 3SiO2 + 4B.
Из примесно-силикатного стекла легирующая примесь диффундирует в кремний. Слой стекла является не только источником примеси, но также предохраняет поверхность кремния от эррозии и служит геттером для загрязняющих быстродиффундирующих примесей.
В случае проведения диффузии из твердых источников их располагают между рабочими кремниевыми пластинами на той же кварцевой лодочке.
Расстояние между пластиной и источником должно быть не более 2√ τ (где
D − коэффициент диффузии примеси в газовой фазе, τ − время диффузии) и составляет, обычно, 3...5 мм. Диаметр планарного источника должен быть не меньше диаметра рабочих кремниевых пластин.
Планарный источник из нитрида бора требует предварительной активационной термообработки в сухом кислороде для образования на поверхности легируемых пластин оксидного слоя:
4BN + 7O2 → 2B2O3 + 4NO2.
Планарный фосфорный источник активации не требует, так как разла-
гается с выделением Р2O5. В присутствии сухого кислорода на поверхности легируемых пластин идут реакции окисления кремния:
Si + O2 → SiO2
и образования примесно-силикатного стекла:
mP2O5 + nSiO2 → mP2O5·nSiO2,
из которого и осуществляется диффузия примеси.
Диффузионное легирование в планарной технологии обычно проводят в две стадии. Первая стадия − диффузионная загонка из примесно-силикат- ного стекла соответствует диффузии из неограниченного (постоянного) источника:
C(x,τ) = Cповerfc[x/(2√ |
|
)], |
(2.1) |
τ |
где Спов − поверхностная концентрация легирующей примеси, которая на стадии загонки обычно поддерживается на уровне предельной растворимости Cs; x − глубина; D − коэффициент диффузии (D = D0exp(−E/kT), D0 −
предэкспоненциальный множитель, E − энергия активации, T – абсолютная температура, k – постоянная Больцмана (k = 8.62·10– 5 эВ/K)); τ − время диф-
фузии. Параметры основных легирующих примесей в кремнии приведены в табл. 2.1.
12
Вторая стадия − диффузионная разгонка проводится после удаления
источника примеси – примесно-силикатного стекла, как правило, при более высоких температурах и длительностях. На этой стадии распределение примеси соответствует случаю диффузии из ограниченного источника
|
|
С(x,τ) = Q/√ |
|
·exp[−x2/(4Dτ)] |
(2.2) |
||||||
|
|
π τ |
|||||||||
где Q − количество примеси в слое после первой стадии: |
|
|
|||||||||
|
|
|
|
|
|
|
|
|
|
||
|
|
|
Q = τ /π |
. |
|
(2.3) |
|||||
|
|
|
|
|
|
|
|
|
Таблица 2.1 |
|
|
|
|
Параметры легирующих примесей в кремнии |
|
|
|||||||
|
|
|
|
|
|
|
|
||||
|
|
Коэффициент |
|
Предельная растворимость |
|
|
|||||
|
Примесь |
диффузии |
|
при t = 1000...1200 °С |
|
|
|||||
|
|
|
|
|
|
|
|
|
|
|
|
|
D0, см2/с |
|
E, эВ |
|
|
Сs, см–3 |
|
|
|||
|
|
|
|
|
|
||||||
|
|
|
|
|
|
|
|
|
|||
|
B |
25 |
3,51 |
|
|
(4,0...5,5)·1020 |
|
|
|||
|
|
|
|
|
|
|
|
|
|||
|
Al |
4,8 |
3,36 |
|
|
(1,8...2,1) ·1019 |
|
|
|||
|
|
|
|
|
|
|
|
|
|||
|
P |
10,5 |
3,69 |
|
|
(1,0...1,5) ·1021 |
|
|
|||
|
|
|
|
|
|
|
|
|
|||
|
As |
68,6 |
4,23 |
|
|
(1,5...2,0) ·1021 |
|
|
|||
|
|
|
|
|
|
|
|
|
|||
|
Sb |
12,9 |
3,98 |
|
|
(4,0...6,0) ·1019 |
|
|
|||
|
|
|
|
|
|
|
|
|
|
|
|
Вторую стадию диффузии обычно совмещают с процессом термического окисления (см. лаб. раб. 1). Изменением режимов проведения первой и второй стадий диффузии можно получить заданные параметры диффузионных слоев.
2.2.Порядок выполнения работы
1.Получить инструктаж по технике безопасности от руководителя ра-
боты.
2.Ознакомиться с установкой диффузионного легирования, ее техническим описанием и характеристиками.
3.Получить от руководителя работы задание на режим диффузионного легирования пластин кремния (температура, время, тип источника, расходы газов).
4.Проверить температуру в рабочей зоне установки с помощью термо-
пары.
13
5.Установить начальные расходы газов в соответствии с заданными режимами (по указанию руководителя).
6.Подготовить для диффузии контрольные пластины кремния типа, противоположного диффузионному слою; с помощью пинцета поместить контрольные пластины в пазы кварцевой лодочки.
7.Вдвинуть лодочку с пластинами в рабочую зону установки с помощью автоматического загрузчика или вручную.
8.Проконтролировать заданные режимы проведения диффузионного процесса.
9.По окончании процесса диффузии выдвинуть лодочку с легированными пластинами из реактора и установить заглушку на кварцевую трубу.
10.Переложить пластины из кварцевой лодочки в специальную тару.
11.После удаления примесно-силикатного стекла (проводится в химическом шкафу с вытяжкой с помощью травителя на основе плавиковой кислоты) измерить сопротивление диффузионного слоя четырехзондовым методом в нескольких точках контрольной пластины.
12.Измерить толщину диффузионного слоя методом окрашивания косого шлифа.
13.Определить поверхностную концентрацию легирующей примеси по кривым Ирвина (см. рис. 2.1).
14.Рассчитать коэффициент диффузии легирующей примеси в соот-
ветствии с формулами (2.1) − (2.3).
15. Сравнить результаты расчета коэффициента диффузии легирующей примеси с данными из литературных источников (см. табл. 2.1) при соответствующей температуре.
2.3. Отчет о работе
Отчет о работе должен содержать:
1.Краткие сведения о методах диффузионного легирования кремния.
2.Схему установки диффузионного легирования, её описание и технические характеристики.
3.Краткое описание методики измерения параметров диффузионного
слоя.
14
4.Результаты индивидуальных измерений и расчетов параметров диффузионного слоя для заданного режима диффузионного легирования; оценку разброса сопротивления диффузионного слоя по контрольной пластине.
5.Результаты индивидуального расчета коэффициента диффузии легирующей примеси и сравнения его с данными из литературных источников.
6.Выводы по работе.
2.4.Контрольные вопросы
1.Каковы основные легирующие примеси в кремнии и методы проведения диффузионного легирования.
2.Опишите особенности диффузии легирующих примесей из жидких и из твердых источников.
3.Какова роль плёнки примесно-силикатного стекла, образующейся на первой стадии диффузии.
4.Укажите способы управления глубиной диффузии и поверхностной концентрацией легирующей примеси.
5.Укажите основные параметры диффузионных слоев и методы их контроля.
Список рекомендуемой литературы
Королёв М. А., Крупкина Т. Ю., Ревелева М. А. Технология, конструкции и мето-
ды моделирования кремниевых интегральных схем. М.: Бином, 2009. С. 91−116.
Технология СБИС / под ред. С. Зи. М.: Мир, 1986. T. 1. С. 227−291.
Лабораторная работа 3
ИОННАЯ ИМПЛАНТАЦИЯ
Цель работы: изучение технологии получения легированных слоев методом ионной имплантации и исследование параметров ионно-легированных слоев.
3.1.Общие сведения
Впланарной технологии кремниевых ИМС ионная имплантация применяется для создания легированных слоев и локальных областей n- и p-типов проводимости с заданным распределением примеси по глубине. Ионно-легированные слои используются для формирования активных (дио-
ды, транзисторы) и пассивных (резисторы, конденсаторы, подныры) элемен-
15
тов ИМС, их изоляции друг от друга, создания скрытых легированных слоев, подлегирования омических контактов и областей канала.
К установкам и процессу ионной имплантации предъявляются следующие требования:
∙ обеспечение заданной дозы имплантации с воспроизводимостью
4 %, не хуже;
∙малый разброс по энергии в пучке 0,1%, не более;
∙высокая разрешающая способность по массе 1 %, не хуже;
∙высокая степень вакуума в камере мишени 10– 5 Па, не хуже;
∙высокая производительность − около 100 пластин/ч;
∙максимальная степень автоматизации;
∙полная радиационная безопасность.
Современные установки ионной имплантации (Везувий-3М, -5М, -13, -15, -17, Днепр, Лада-30) удовлетворяют всем этим требованиям, что позволяет получать ионно-легированные слои с высокой однородностью параметров (слоевое сопротивление, глубина, поверхностная или максимальная концентрация) по площади пластины и высокой воспроизводимостью от процесса к процессу.
Сопротивление ионно-легированных слоев определяется четырехзон-
довым методом, глубина залегания p−n-перехода − методом окрашивания косого шлифа, поверхностная концентрация − по кривым Ирвина для гаус-
совского распределения (см. рис. 2.1).
Процесс ионного легирования по сравнению с диффузионным легированием имеет ряд преимуществ, основные из которых следующие:
1)возможность имплантации практически любой примеси, а также сложных комплексных ионов в любую твердотельную подложку;
2)возможность использования в качестве маски нетермостойких материалов, таких, как фоторезист, алюминий;
3)возможность имплантации примеси в подложку через тонкие субмикрометровые слои маскирующих и защитных покрытий на заданную глубину;
4)установки ионной имплантации производят сепарацию ионов по массам, обеспечивая высокую степень чистоты процесса введения примеси;
5)позволяют осуществлять точный контроль количества введенной примеси (дозы имплантации), что особенно важно.
16

Перечисленные достоинства обеспечили широкое применение ионной имплантации в технологии ИМС. Особенностью ионного метода легирования является необходимость проведения термического отжига для электрической активации имплантированной примеси, для восстановления нарушенной имплантацией кристаллической решетки и для отжига радиационных дефектов. Температура отжига зависит от дозы и энергии имплантации,
вида примесных ионов и лежит в диапазоне 900...1100 ºС.
Согласно теории Линхарда−Шарфа−Шиотта (ЛШШ) распределение имплантированной примеси по глубине подложки может быть приближенно описано распределением типа Гаусса
|
|
Q |
|
|
|
|
(x − R p ) |
2 |
|
|
|
|
|
|
|
|
|
|
|
|
|||
|
|
|
|
|
|
|
|
|
|
|
|
С(x) = |
|
|
|
|
exp − |
|
|
|
|
, |
|
|
|
|
|
|
2 |
|
|||||
|
|
2π |
2 |
|
|
|
2 R |
|
|
|
|
|
|
R p |
|
|
p |
|
|
|
где Q − доза имплантации, ион/см2; Rp − средний проецированный пробег ионов; Rp − среднеквадратичное отклонение пробегов, или страгглинг.
Значения пробегов и страгглингов основных легирующих примесей (B, P, As, Sb) в кремнии приведены в табл. 3.1.
|
|
|
|
|
|
|
|
|
|
|
Таблица 3.1 |
|
|
|
Параметры распределения ионов B, P, As, Sb в Si |
|
|
|
|||||||
|
|
|
|
|
|
|
|
|
|
|
|
|
|
|
B |
P |
|
|
As |
|
|
Sb |
|||
E, кэВ |
Rp, Å |
|
Rp, Å |
Rp, Å |
Rp, Å |
Rp, Å |
|
Rp, Å |
|
Rp, Å |
|
Rp, Å |
|
|
|
|
|
||||||||
40 |
1285 |
|
456 |
489 |
214 |
298 |
|
109 |
|
289 |
|
86 |
60 |
1880 |
|
573 |
731 |
300 |
402 |
|
145 |
|
370 |
|
110 |
80 |
2438 |
|
662 |
982 |
380 |
505 |
|
180 |
|
445 |
|
132 |
100 |
2964 |
|
733 |
1283 |
457 |
608 |
|
214 |
|
517 |
|
153 |
120 |
3463 |
|
792 |
1498 |
529 |
712 |
|
248 |
|
588 |
|
174 |
В результате проведения постимплантационных отжигов происходит диффузионное перераспределение имплантированной примеси и распределение примеси по глубине подложки примет вид
17
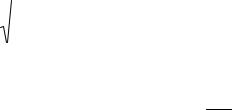
|
|
|
|
|
|
|
|
|
|
(x − R p )2 |
|
|
|
С(x) = |
|
|
Q |
|
|
exp − |
|
|
|
+ exp − |
|||
|
|
|
|
|
|
|
|
|
|
||||
|
|
|
|
2 |
|
|
|
|
|
2 |
|
|
|
|
|
R |
|
|
|
|
|
||||||
|
|
2π |
p |
+ 2Dτ |
|
2 |
R p + 2Dτ |
||||||
|
|
|
|
|
|
|
|
|
|
|
|
|
|
(x + R |
|
)2 |
|
|
||
|
p |
|
|
||||
|
|
|
|
, |
|||
2 |
R2 |
+ 2Dτ |
|
||||
|
|||||||
|
p |
|
|
|
|
|
|
|
|
|
|
|
|
где D − коэффициент диффузии; τ − время диффузии.
В случае неглубокой имплантации и достаточно длительного высоко-
температурного отжига, когда 2√ τ >> Rp, последнее выражение перехо-
дит в известное выражение для диффузии из ограниченного источника (см. (2.2)). В этом случае для определения поверхностной концентрации примеси в ионно-легированном слое можно воспользоваться соответствующими кривыми Ирвина (см. рис. 2.1). Выражение для сопротивления ионно-леги-
рованного слоя Rs имеет вид
Rs− 1 = ex∫jn(x)µ(x)dx, 0
где e − заряд электрона; xj − глубина залегания p−n-перехода; n(x) − ре-
зультирующая концентрация доноров или акцепторов; − подвижность носителей заряда. В общем случае необходимо учитывать зависимость по-
движности от концентрации носителей заряда μ(n) в виде
|
|
μ(n) = μ |
+ (μ |
− μ |
)/[1+(n/C |
)a]. |
||||
|
|
|
min |
max |
min |
r |
|
|
|
|
Параметры концентрационной зависимости подвижности приведены в |
||||||||||
табл. 3.2. |
|
|
|
|
|
|
|
|
|
|
|
|
|
|
|
|
|
|
|
Таблица 3.2 |
|
|
Параметры концентрационной зависимости подвижности |
|||||||||
|
|
|
носителей заряда в кремнии |
|
|
|
||||
|
|
|
|
|
|
|
|
|
|
|
|
Тип |
|
μmin, |
μmax, |
|
Cr, cм−3 |
|
a |
|
|
|
проводимости |
|
2 |
2 |
|
|
|
|
||
|
|
cм /(В·с) |
cм /(В·с) |
|
|
|
|
|
||
|
|
|
|
|
|
|
|
|
|
|
|
n-Si |
|
65 |
1330 |
|
8,5·1016 |
|
0,72 |
|
|
|
p-Si |
|
47,7 |
495 |
|
6,3·1016 |
|
0,76 |
|
Верхнюю оценку сопротивления ионнолегированого слоя Rsmax можно
получить, полагая μ(x) = μ(Cmax) = μmin, где Cmax − максимальная концентрация примеси в имплантированном слое:
18
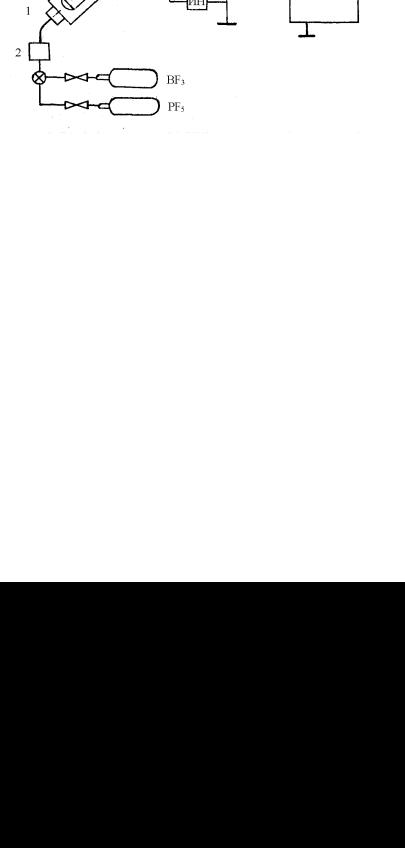
Сmax = |
|
Q |
|
. |
(3.1) |
|||
|
|
|
|
|||||
|
|
|
2π R p |
|
||||
В этом случае |
|
|
|
|
|
|
|
|
− 1 |
|
|
|
|
x j |
|
||
= eµmin |
∫ n(x)dx = eµminQ . |
(3.2) |
||||||
Rs max |
||||||||
|
|
|
|
|
0 |
|
Вобласти малых доз подвижность перестает зависеть от концентрации
иформула (3.4) станет точной.
3.2. Схема установки ионной имплантации
Схема установки ионной имплантации представлена на рис. 4.1. Ионы примеси для имплантации создаются в источнике ионов 1 из напускаемого газа, паров или твердого источника легирующей примеси формированием электрического разряда. Из источника вытягиваются ионы потенциалом до 40 кэВ с помощью системы экстракции 2 и формируются в узкий пучок с помощью системы электрофокусировки 4. В масс-сепараторе 5 происходит выделение из пучка ионов заданной массы M и заряда z (M/z). Отсепарированные ионы проходят выходную щель 6 и подвергаются линейному ускорению до заданной энергии (до 200 кэВ) в ускорительной трубке 7, питаемой источником напряжения ИН. В системе фокусирования и сканирования 8 производятся окончательная фокусировка и организация сканирования пучка ионов в вертикальном направлении. Далее ионы попадают в приемную камеру мишени 8, где на барабане 9 установлены полупроводниковые пласти-
Рис. 3.1. Схема установки ионной имплантации
19
ны. В установке поддерживается вакуум на уровне 1·10−3 Па в камере ис-
точника и на уровне 1·10−5 в приемной камере.
3.3.Порядок выполнения работы
1.Получить инструктаж по технике безопасности от руководителя ра-
боты.
2.Ознакомиться с установкой ионной имплантации, её техническим описанием и характеристиками.
3.Получить от руководителя задание на режим ионной имплантации контрольных пластин (тип примеси, энергия ионов, доза облучения, плотность тока пучка).
4.Подготовить контрольные пластины кремния для имплантации. Установить их с помощью пинцета в пазы барабана.
5.Закрыть камеру мишени.
6.Задать ускоряющее напряжение и плотность тока пучка.
7.Набрать необходимую дозу имплантации.
8.Осуществить выгрузку проимплантированных контрольных пла-
стин.
9.Провести активационный отжиг контрольных пластин при температуре 1050 ºС в течение 15 мин в атмосфере азота.
10.Измерить сопротивление имплантированного слоя на одной из контрольных пластин в нескольких точках. Оценить величину разброса слоевого сопротивления по пластине.
11.Рассчитать максимальную концентрацию примеси в соответствии с формулой (3.1), определить соответствующую ей подвижность носителей за-
ряда с помощью рис. 3.2 и рассчитать величину Rs max в соответствии с фор-
мулой (3.2).
12. Сравнить результаты расчета с экспериментальными значениями слоевого сопротивления и сделать вывод о степени точности расчетных формул.
3.4. Отчет о работе
Отчет о работе должен содержать:
1. Краткие сведения о методе ионного легирования полупроводников и его особенностях.
20