
Каталитический крекинг-2
.pdf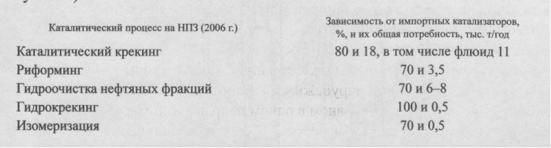
СПБГУАП группа 4736 https://new.guap.ru/i03/contacts
Установки каталитического крекинга. Первой установкой с движущимся шариковым аморфным катализатором была установка типа 43-1, ее развитием был тип 43-102, позже были построены установки ККФ типов 1Б, 1А, 1А/1М, 43103, 43-103М, 43-104, катализаторный блок комбинированной установки ГК-3 сначала на микросферическом аморфном катализаторе, потом установки были модернизированы для микросферического кристаллического катализатора. Комбинированная установка Г-43-107 содержит блок гидроочистки сырья, блок ККФ и блок ректификации.
В последнее время техническая и коммерческая активность по созданию на НПЗ мира новых установок каталитического крекинга в псевдоожижен-ном слое микросферического катализатора приобрела рекордно высокий уровень за все время применения ККФ. В мире установками ККФ оснащены более 330 НПЗ, при этом общая мощность установок ККФ равна примерно 1000 млн т сырья в год. В нефтепереработке Западной Европы каталитический крекинг занимает около 16 %, Японии - 17, США - 36, а России - 6 %. В 1980-1990 гг. процесс ККФ был существенно усовершенствован фирмами «UOP», «Kellogg», «Shell», «ABB Lummus», «Stone Webster» и другими с целью увеличения селективности при превращении (конверсии) сырья в бензиновые фракции на основе контролируемого каталитического крекинга (каталитические реакции - основные, а термические минимальны). При этом высокие рабочие показатели процесса достигаются за счет совершенствования лифт-реактора и узла ввода сырья для работы на катализаторе с более высокой плотностью, использования так называемой Х-образной технологической схемы фирмы «UOP», когда в стояк подается более холодный отработанный катализатор, который еще не потерял активности, что обеспечивает увеличение кратности циркуляции катализатора к сырью и вызывает большую степень превращения сырья. Одной из последних разработок фирмы «UOP» для увеличения выхода бензина является процесс миллисекундного каталитического крекинга «MSCC» (рис. 2.17), в котором первоначальный контакт сырья с катализатором осуществляется в течение очень короткого времени и без применения лифт-реактора.
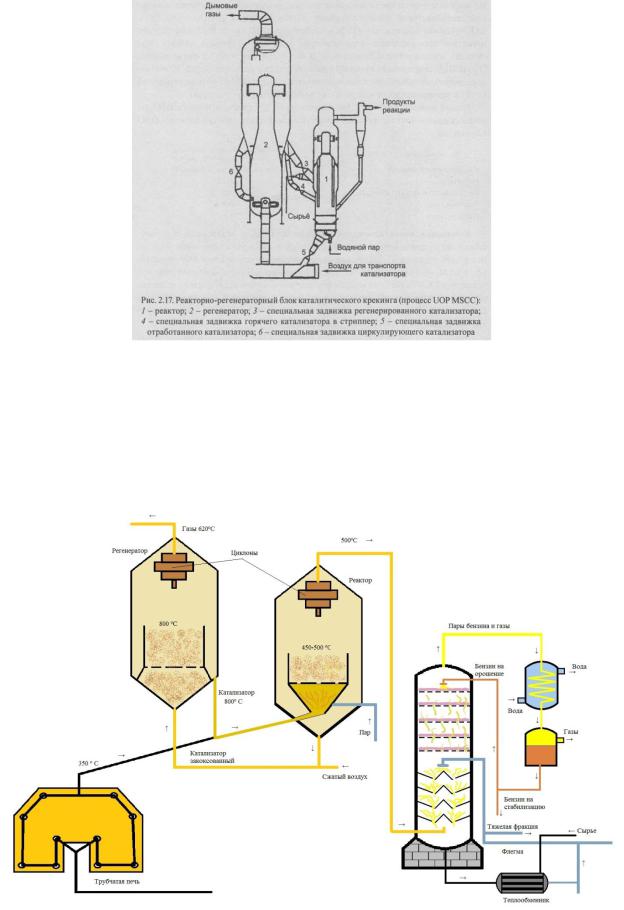
СПБГУАП группа 4736 https://new.guap.ru/i03/contacts
Для облагораживания компонента бензина ККФ и доведения его до нормативов на экологически чистый бензин применяются дополнительные технологические меры, которые стали возможными также благодаря достижениям последних лет. Кстати, в ОАО «Мозырский НПЗ» успешно работает недавно построенная установка каталитического крекинга модели «MSCC».
СПБГУАП группа 4736 https://new.guap.ru/i03/contacts
Каталитический риформинг
Наука - Технология добычи газа и нефти
Каталитический риформинг представляет собой один из значительных процессов развития нефтепереработки после Второй мировой войны, получивших широкое применение. Этот процесс впервые внедрен в промышленность в 1940 г. Он позволяет превратить низкооктановое сырье - прямогонные бензины (naphtha) в высокооктановый компонент - риформат. Непрекращающаяся в мире экологическая борьба за чистоту окружающей среды вытеснила применение антидетонаторов на основе свинца, что повысило роль каталитического риформинга в производстве неэтилированных бензинов с высоким октановым числом. С другой стороны, каталитический риформинг позволяет получать нефтехимическое сырье - ароматические углеводороды, бензол (наиболее ценный продукт), толуол и ксилолы (БТК), а также производить водородсодержащий газ. На начало 2001 г. ориентировочные мощности установок каталитического риформинга составляют в мире 480 млн т/год; из них в Северной Америке-180, в Западной Европе93, в России и СНГ-49 млн т/год.
В настоящее время существует целое семейство похожих вариантов (промышленных версий) этого процесса. Каталитический риформинг основан на применении необычных, многофункциональных алюмоплатиновых катализаторов, имеющих добавки дорогих металлов: платины, рения, иридия, германия и др. Зарубежные фирмы - продавцы промышленных процессов (установок) держат в секрете состав и технологию получения катализаторов. В зависимости от системы, типа, назначения и применения катализатора технологический режим каталитического риформинга, а также выход продуктов и их качество изменяются в широких пределах. Процесс протекает в присутствии водородсодержащего газа при высоких температурах и сравнительно невысоких давлениях. В результате процесса образуется избыточное количество водорода, который в 10-15 раз дешевле водорода, получаемого иными способами на специальных установках. Именно этот значительный ресурс получаемого водорода чистотой до 90 % на НПЗ дал возможность широко внедрить в нефтепереработке совершенные и столь необходимые другие гидрогениза-ционные каталитические процессы, протекающие в присутствии водорода, для гидроочистки бензиновых, керосиновых и дизельных фракций и даже для обессеривания мазутов, нефтяных масел, парафинов, вакуумных газойлей; для гидрообессеривания (деметаллизации) нефтяных остатков; для гидрокрекинга с получением топлив, сжиженных газов, изопарафинов и др.
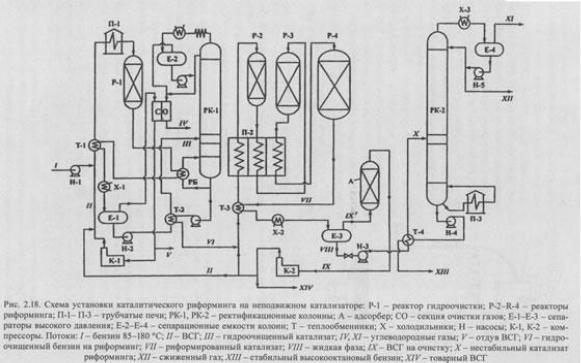
СПБГУАП группа 4736 https://new.guap.ru/i03/contacts
Различают три основных способа осуществления процесса каталитического риформинга:
1)непрерывная реакция в 3-4 реакторах в течение межрегенерационного периода службы катализатора и периодическая регенерация потерявшего активность катализатора одновременно во всех реакторах', вся установка переводится с режима реакции на режим регенерации одновременно во всех реакторах, в каждом реакторе используется неподвижный слой таблетированного или сферического катализатора (процессы «Platforming», «Catforming»,
«Houdriforming»);
2)непрерывная работа установки, непрерывная реакция в 2-3 реакторах, периодическая регенерация катализатора поочередно в каждом реакторе, который заменяется четвертым резервным (плавающим) реактором (процессы
«Powerforming», «Ultraforming»);
3)непрерывная реакция в четырех реакторах, расположенных один над другим или рядом друг с другом, непрерывный отвод для регенерации части катализатора в отдельном изолированном регенераторе с применением схемы циркулирующего (движущегося) катализатора между реакторами и регенератором (фирма «UOP», Французский нефтяной институт - IFP).
Принцип процесса риформинга (рис. 2.18).
СПБГУАП группа 4736 https://new.guap.ru/i03/contacts
Сырье (прямогонные бензины С6 -180 °С с ОЧм = 40-60) при температуре 480-520 °С и давлении от 1,2-1,4 до 3-4 МПа в присутствии водорода на поверхности высокоактивных катализаторов превращается в высокооктановые ароматические и изопарафиновые углеводороды. При этом образуются водород как продукт (1,3- 2,5 мае. % на сырье) и газообразные легкие парафиновые углеводороды, а также чрезвычайно нежелательный кокс, который снижает активность катализаторов. Используются чаще всего 3-4 реактора с неподвижным слоем катализатора, между которыми предусматривается межступенчатый подогрев промежуточных продуктов реакции в многокамерной трубчатой печи. Падение температуры из-за эндотермичности основных реакций равно 60-70 °С в первом реакторе, 30-40 °С во втором реакторе и 5-10 °С в третьем реакторе. Распределение общего объема катализатора по реакторам может быть разным 1-2-6, 1-1-2-7, 1-2-4.
Выход риформата до 75-88 мае. % на сырье, октановое число риформата ОЧи = 93-102, при этом при большом достигаемом выходе риформата снижается его октановое число. Для риформинга применяют дорогие алюмоплатиновые катализаторы, в которых кислотную функцию выполняет носитель - оксид алюминия А1203, а на его поверхность наносятся кристаллы платины Pt (0,3-0,8 %) размером от 1-5 до 10-12 нм. Платина занимает около 1 % поверхности оксида алюминия.
Активность, селективность и стабильность катализатора повышаются металлическими промоторами, в качестве которых давно используют дорогие металлы: рений Re (0,3-0,4 %), иридий 1г, германий Ge и др., а также промоторами галогенами: фтором (до 0,3 %) или хлором (от 0,4-0,5 до 2,0 %). Совершенство характеристик новых катализаторов, например R-56 фирмы «UOP», таких как срок их службы между регенерациями, количество регенераций, стойкость к ядам - примесям серы, азота и других в сырье, направлено на получение максимальных значений выхода риформата и его октанового числа. Но чем большее октановое число получает риформат, тем больше кокса образуется на поверхности катализатора и тем быстрее он стареет. Катализаторы выполняются в виде таблеток (экструдатов) диаметром 1,6-2,6 мм и высотой (длиной) 4-6 мм или в виде сферических гранул диаметром 1,6 или 2,1 мм с насыпной плотностью 600-820 кг/м3 и удельной поверхностью 180-300 м2/г.
Окислительная регенерация алюмоплатинового катализатора заключается в выжигании коксовых отложений с поверхности катализатора кислородом инертной смеси при температуре 300-500 °С.
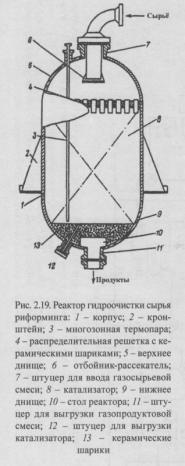
СПБГУАП группа 4736 https://new.guap.ru/i03/contacts
Катализаторы риформинга очень чувствительны к присутствию в сырье примесей свинца, мышьяка, металлов, воды, сернистых, кислород- и азотсодержащих соединений. Поэтому сырье риформинга подвергают глубокой гидроочистке от нежелательных примесей обычно в отдельном первом реакторе гидроочистки
(рис. 2.19).
Катализатор риформинга перерабатывает без регенерации 70-210 м3 сырья на 1 кг катализатора. Но любая регенерация не спасает катализатор от потери его первоначальной активности и от старения. Со временем катализатор заменяют свежей партией, а старый катализатор отправляют на специальные заводы по извлечению платины и других дорогих металлов, однако при эксплуатации около 1% платины теряется.
Чтобы показать многообразие промышленного каталитического риформинга и историю его развития, дадим названия некоторых зарубежных процессов (установок):
«Platforming» фирмы «UOP» (1949 г.) в слое неподвижного катализатора,
СПБГУАП группа 4736 https://new.guap.ru/i03/contacts
давление 2-4 МПа, три реактора, катализатор с платиной, марок R4-R7, R9-R12, RM, цикл работы катализатора 6-12 мес;
«Catforming» фирмы «Atlantic Richfield» (1952 г.), давление 3,5-4 МПа, схема похожа на схему платформинга, специальный катализатор;
«Houdriforming» фирмы «Houdry Process and Chemicals» (1953 г.), давление 2-4
МПа, периодическая регенерация катализатора с платиной марки Н3 и с платиной и рением марки HR-71; «Ultraforming» фирмы «Standard Oil» (1955 г.), давление
1,4-2,1 МПа, катализатор содержит до 0,6 мае. % платины, три реактора всегда в режиме реакции, а четвертый реактор в режиме регенерации;
-процесс «Sinclair-Becker-Kellogg» (1955 г.), давление 2,0-3,5 МПа, платиновый катализатор марок RD-150 и RD-150c, два первых реактора в режиме реакции, два последних реактора в режиме регенерации;
-«Powerforming» фирм «Esso» и «Engelhard» (1956 г.), давление 2-3 МПа, похож на схему процесса «Ultraforming», один из четырех реакторов в режиме регенерации;
-«Rheniforming» фирмы «Chevron Research» (1960-е годы), давление 1,4— 1,8
МПа, катализатор содержит платину и рений, три реактора;
-«Magnaforming» фирмы «Engelhard» (1960-е годы), катализатор с платиной марок RD-150 и RD-150c или платино-рениевый марок Е-500 и Е-501, достигается оптимальный режим увеличения температуры в четырех реакторах;
-процесс «UOP» (с 1971 г.) с движущимся слоем катализатора от вышерасположенного реактора к нижерасположенным реакторам и потом в регенератор, непрерывная регенерация катализатора, подаваемого в верхний реактор (их всего 4) пневмотранспортом, поддерживается более высокая активность катализатора с платиной, рением или германием марок R-16, R-20, R-22, R-20/30, давление 0,9-
1,3 МПа;
-«Selectoforming» фирмы «Mobil Oil» комбинирует риформинг с селективным гидрокрекингом полученного риформата;
-процессы «Isoreforming» и «Isomaxreforming» комбинируют предварительный гидрокрекинг сырья с риформингом',
СПБГУАП группа 4736 https://new.guap.ru/i03/contacts
-«Rexforming» комбинирует риформинг с экстракцией (выделением) ароматических углеводородов из риформата и их частичный возврат в секцию риформинга;
-«Isoplus» комбинирует риформинг с термическим крекингом полученного риформата.
Внедрение каталитического риформинга в СССР началось в 1955 г. с опытной установки на Краснодарском НПЗ и в 1959 г. с опытно-промышленной установки на Уфимском НПЗ. В 1962 г. на Новокуйбышевском НПЗ, а затем на Московском НПЗ были введены в эксплуатацию первые отечественные укрупненные установки риформинга типа 35-5 для получения риформата с ОЧм = 75. До 1965 г. строились установки типа 35-5 и 35-11/300 с использованием отечественного алюмоплатинового катализатора марки АП-56. До 1970 г. широко внедрялись типовые установки типа 35-11/300 и 35-11/600 на катализаторах марок АП-56 и АП-64 с получением риформата с ОЧм = 78-80. До конца 1980-х годов строятся укрупненные установки Л-35-11/1000 как отдельно стоящие, так и для типовой комбинированной установки ЛК-бу на катализаторе марки АП-64 с получением риформата с ОЧи = 95. К концу 1980-х годов также проектировались как отдельно стоящие установки ЛЧ-35-11/1000, так и комбинированные установки ЛК-9М на давление 1,5-1,8 МПа с применением пла-тино-рениевого катализатора серии КР (марки КР-102, КР-102с биметаллические; КР-104, KP-106, КР-108, КР-110, РБ-1, РБ-11, РБ-22 полиметаллические). В обозначениях установок последняя цифра после знака дроби - мощность установки по сырью, тыс. т/год.
Применение высокоэффективных катализаторов Hia модернизируемых установках позволяет увеличить ОЧи базового компонента - бензина до 100, что, например, достигнуто на установке Л-35-11/1000 Ново-Уфимского НПЗ на катализаторах RG-428 и CR-201 французской фирмы «Procatalyse».
Приведем некоторые технологические параметры процесса:
-блок предварительной гидроочистки сырья: температура 340-420 °С, давление 2,7-4,0 МПа, расход водородсодержащего газа 120-400 нм3/м3 сырья, алюмокобальтмолибденовый катализатор, цикл реакции 12 мес., срок службы катализатора 24-36 мес.;
-блок риформинга гидроочищенного сырья: температура 480-530 °С, давление в последнем реакторе 1,5-2,8 МПа, расход водородсодержащего газа 1200-1800
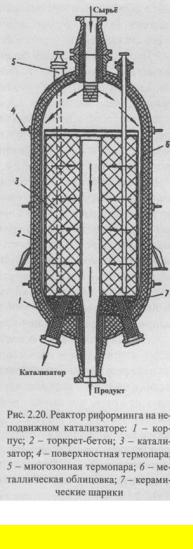
СПБГУАП группа 4736 https://new.guap.ru/i03/contacts
нм3/м3 сырья, катализатор КР (редко АП-64), цикл реакции 6-12 мес., срок службы катализатора 48-60 мес., перепад давления в реакторном блоке 1,0-1,8 МПа, распределение общего объема катализатора по реакторам 1-2-4 или 1-3-7, содержание водорода в циркулирующем газе 65-90 об. %;
тьего реактора (рис. 2.20) последовательно охлаждаются в теплообменниках, потом в АВО и ВХ и в сепараторе высокого давления разделяются при давлении 2,4-2,8 МПа на водородсодержащий газ и нестабильный риформат. Водородсодержащий газ, сжатый в компрессоре, подается циркулирующим потоком вновь на смешение с сырьем установки перед реактором гидроочистки, а также на смешение со стабильным гидрогенизатом перед первым реактором риформинга. Нестабильный риформат поступает в сепаратор низкого давления (1,6-1,8 МПа), где от него отделяется углеводородный газ, а нестабильный риформат направляется в ректификационную колонну давлением 1,3 МПа и температурой в низу колонны 200-240 °С. С верха колонны углеводородный газ выводится на ГФУ. Работа этой колонны аналогична работе колонны стабилизации нестабильного ги-дрогенизата. Стабильный риформат - нижний продукт ректификационной колонны охлаждается и покидает установку.
СПБГУАП группа 4736 https://new.guap.ru/i03/contacts
Регенерация неподвижного слоя катализатора. Окислительная регенерация катализатора проводится с целью выжигания кокса с поверхности катализатора кислородом воздуха [46]. Некоторые катализаторы регенерируют непосредственно в реакторе, при этом подача в реактор сырья заменяется на время подачей кислородсодержащего газа. Образование кокса при риформинге невелико, но при межрегенерационном цикле 11-12 мес. и более содержание кокса может достигать 3-5 мае. % на катализатор. При подготовке блока реакторов к регенерации освобождают связанные аппараты и трубопроводы от жидких и газообразных углеводородов. Для этого применяют разнообразные методы: горячую десорбцию водородсодержащим газом катализатора при температуре 400 °С, дренирование жидких углеводородов, вакуумирование системы, продувки системы азотом. Окисление кокса проводят при температуре 300-500 °С смесью инертного газа с воздухом с содержанием кислорода в смеси до 0,5 об. % (иногда 1,5-2,0 об. %), паров воды до 0,2 г/м3, С02 и СО до 1,0 и 0,5 об. % соответственно. От времени выжигания кокса (от 1 до 6 сут.) зависит содержание кислорода в смеси и ее давление. Применяют раздельную регенерацию по реакторам. Во всех случаях недопустимо возгорание катализатора, приводящее к его спеканию и потере его активности.
После окислительной регенерации катализатора проводится его восстановительная регенерация галогенированием для восстанавления кислотных свойств катализатора и улучшения дисперсности платины. Для этого используют разные соединения хлора (тетрахлоруглерод, дихлорэтан и др.). Все операции регенерации катализатора риформинга чрезвычайно деликатны, дороги и опасны и требуют высокого профессионализма персонала. Стоимость катализатора риформинга может быть соизмерима со стоимостью технологического оборудования установки. Поэтому чрезмерная регенерация катализатора сокращает полезный срок службы установки, недостаточная регенерация снижает межрегенерационный цикл, грубая регенерация разрушает катализатор и приводит к преждевременному его старению. Окислительная регенерация катализатора сразу во всех реакторах может занимать 5-10 сут. в год при длительности простоев до 20-40 сут. Катализаторы только с платиной имеют срок службы 1,5-2 года, а усовершенствованные полиметаллические катализаторы могут иметь срок службы до 5-6 лет. Но последние требуют глубокой гидроочистки сырья до содержания серы не более 0,00005-0,0001 мае. %, азота не более 0,0001-0,0002 мае. %, воды не более 0,001 мае. %, свинца, сурьмы и меди не более нескольких миллиграммов на тонну сырья.
Реакторный блок с движущимся слоем катализатора (рис. 2.21).