
4873
.pdf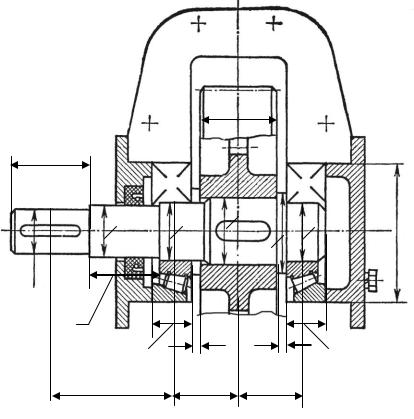
11
lст
l1
d упл |
d подш |
d пп |
d подш |
|
|||
|
|
d св |
|
d
l2
|
|
|
y |
y |
||
|
Tmax |
|
|
|
|
Tmax |
|
|
|
|
|
||
a |
|
b |
c |
D
Рисунок 4. Вал в сборе
Если полученное значение диаметра вала незначительно отличается от расчетного значения диаметра шестерни, то ее целесообразно изготовить заодно с валом. В противном случае диаметр посадочной поверхности вала (под зубчатое колесо) можно принять:
dпп dподш 2...5 мм
Диаметр свободного участка вала (упорного буртика):
dсв dпп 5 мм
Длину выходного конца вала определяют по соотношению:
l1 1,5...2 d
Полученное значение уточняют исходя из длин ступиц деталей, которые на них насаживают.
Расстояние от края ступицы до подшипника ориентировочно назначают:

12
l2 1,5 Тmax ,
где Тmax - ширина подшипника, мм.
На данном этапе проектирования типоразмеры подшипников намечаются ориентировочно для возможности компоновки вала; в дальнейшем при подборе подшипников по динамической грузоподъемности их параметры будут уточнены. Предварительно можно принять Тmax = 20…25 мм.
Величина зазора между деталями передачи:
y 3 L 3 ,
где L- расстояние между внешними деталями передачи, мм. Для цилиндрического и червячного редуктора:
L da 1 da 2 ,
где d a 1 и da 2 - соответственно диаметры вершин зубьев шестерни и
колеса (червяка и червячного колеса), мм. Для конического редуктора: L= 1,5 da 2 .
Для ременных и цепных передач, а также открытых зубчатых передач L можно принять исходя из компоновки привода.
Вычисленное значение зазора округляют в большую сторону до целого числа.
В случае необходимости, например для удобства посадки на вал подшипников качения, зубчатых колес, размеры валов могут быть назначены иными исходя из конструктивных или технологических соображений.
2.2 Проектный расчет
На данном этапе проектирования составляют расчетную схему вала, определяют реакции в опорах (подшипниках), а также строят эпюры изгибающих и крутящих моментов.
При действии на вал сил, расположенных в разных плоскостях, их раскладывают на две взаимно перпендикулярные плоскости, за одну из которых выбирают плоскость действия одной из сил. Если силы расположены в плоскостях под углом менее 300, то их можно совместить в одну плоскость.
При этом считают, что реакции опор и силы, действующие на вал, сосредоточены посередине детали. Следовательно, расстояния между линиями приложения нагрузок могут быть определены следующим образом (см. рисунок 4):
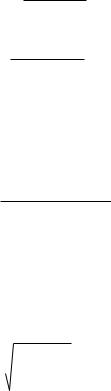
13
a 0,5l1 l2 0,5Tmax , b 0,5Tmax y 0,5lст ,
с 0,5lст y 0,5Tmax ,
где lст – длина ступицы насаживаемой на вал детали, мм.
Опоры вала принято обозначать заглавными буквенными знаками (А, В). На основании расчетной схемы вала для каждой опоры (подшипника) со-
ставляют условия равновесия в двух рассматриваемых плоскостях ( Fl 0).
При этом отбрасывают одну из связей (опор) и если момент от действующей силы способствует вращению вала относительно оставшейся опоры против часовой стрелки, то его считают положительным, в противном случае - отрицательным.
Из условий равновесия определяют реакции в опорах для каждой
плоскости (RA x, RВ x, RA y, RВ y).
Суммарную реакцию в каждой опоре и результирующий изгибающий момент в соответствующем сечении вала определяют по формулам:
R R2x R2y ;
M M 2x M 2y ,
где Rx, Ry, Mx, My – соответственно опорные реакции и изгибающие моменты во взаимно перпендикулярных плоскостях.
Эквивалентный момент вычисляют по формуле:
Mэкв M2 0,75 T2 ,
где Т - крутящий момент на валу, Нм.
По величине эквивалентного момента определяют диаметр вала при совместном действии изгиба и кручения:
d 3 |
0,1 , |
|
Mэкв |
где – допускаемое напряжение на изгиб, = 50…60 МПа. Полученное значение диаметра округляют до ближайшего большего
числа из стандартного ряда (см. стр. 10).

14
2.3 Расчет на выносливость
После предварительных расчетов производят уточненный (проверочный) расчет валов на усталостную прочность (выносливость) с целью определения общего коэффициента запаса прочности.
Приступая к расчету, предположительно намечают опасное сечение вала, которое подлежит проверке (наличие шпоночного паза, максимальный изгибающий момент). Для опасного сечения находят общий коэффициент запаса прочности:
S |
S |
S |
|
S , |
|
|
|
|
|
||
|
S2 |
S2 |
|||
|
|
|
|
|
|
где S – коэффициент запаса прочности по изгибу;
S - коэффициент запаса прочности по кручению;
S - допустимое значение общего коэффициента запаса прочности, S =2,5. Коэффициенты S , S , в свою очередь, соответственно определяются
следующим образом:
|
S |
|
|
1 |
|
; |
||||
|
a |
K |
|
|
m |
|
||||
|
|
|
|
|
|
|||||
|
|
|
|
|
|
|||||
|
|
|
|
|
|
|
|
|
||
|
S |
|
|
1 |
|
, |
||||
|
a |
K |
|
|
m |
|||||
|
|
|
|
|
|
|
||||
|
|
|
|
|
|
|
||||
|
|
|
|
|
|
|
|
|
|
|
где 1 , |
1 – пределы выносливости соответственно при изгибе и кру- |
чении, определяемые в зависимости от величины предела прочности материала вала в :
1 0,4...0,5 в
1 0,2...0,3 в ,
а , а - амплитуды переменных составляющих циклов напряжений:
а М ;
Wнетто

15
а |
|
|
Т |
, |
|
|
|
||||
2 |
WК.нетто |
||||
|
|
|
где М - изгибающий момент в опасном сечении, Нмм; Т - крутящий момент на валу, Нмм;
Wнетто, WК нетто – соответственно моменты сопротивления сечения вала изгибу и кручению (без учета шпоночного паза), вычисляемые по формулам:
|
|
d3 |
|
b t |
1 |
d t |
2 |
|
|
||||
Wнетто |
|
|
|
|
1 |
|
|
|
; |
||||
32 |
|
|
|
2 d |
|
|
|
||||||
|
|
|
|
|
|
|
|
|
|
|
|||
WК .нетто |
|
d3 |
|
b t |
1 |
d t |
1 |
2 |
|
, |
|||
|
|
|
|
|
|
|
|||||||
16 |
|
|
|
2 d |
|
|
|
|
|||||
|
|
|
|
|
|
|
|
|
|
|
|
где d- диаметр вала, определенный при проектном расчете, мм; в- ширина шпоночного паза, мм (таблицы 2-3);
t1- глубина шпоночного паза, мм (таблицы 2-3);
К , К - коэффициенты концентрации напряжений при изгибе и кручении
соответственно (таблица 4).
- коэффициент шероховатости поверхности (для сталей: 0,99);, - масштабные факторы изгиба и кручения, выбираемые в зависимо-
сти от диаметра вала в опасном сечении и его материала (таблица 5).
, - коэффициенты асимметрии циклов напряжений на изгиб и кручение соответственно (для валов из углеродистых сталей принимают = 0,1,
= 0,05; из легированных - =0,15, =0,1).
m , m - средние значения напряжений изгиба и кручения, МПа.
Принимают:
m |
Fa |
; |
d2 |
||
4 |
|
|
m а , |
|
|
где Fa - осевая сила, действующая на вал, Н. |
|
16
4 ПОДБОР ПОДШИПНИКОВ
Подшипники качения подбирают в зависимости от размера и направления, действующих на подшипник нагрузок, диаметра вала, характера нагрузок, желательного срока службы подшипника и его наименьшей стоимости.
В соответствии с установившейся практикой проектирования и эксплуатации машин тип подшипника выбирают по следующим рекомендациям.
Для опор валов цилиндрических прямозубых и косозубых колес редукто-
ров чаще всего применяют шариковые радиальные подшипники. Первоначально назначают легкой серии. При чрезмерно больших размерах шариковых подшипников в качестве опор валов цилиндрических колес применяют подшипники роликовые конические.
Конические и червячные колеса должны быть точно и жестко зафиксированы в осевом направлении. Шариковые радиальные подшипники характеризует малая осевая жесткость. Поэтому в силовых передачах для опор валов конических и червячных колес применяют конические роликовые подшипники. Первоначально выбирают легкую серию. При длительной непрерывной работе червячной передачи с целью снижения тепловыделения иногда применяют шариковые радиально-упорные подшипники.
При спокойном характере нагрузки, если на подшипник действует только радиальная сила, то выбирают радиальные шариковые подшипники. При совместном действии радиальной и осевой силы также допускается применение радиальных шариковых подшипников, если выполняется условие:
Fa |
≤ 0,22, |
||
R |
max |
||
|
где R max - наибольшее из значений суммарных реакций в опорах от действия радиальных сил (R A или R B), Н.
Вслучае если указанное условие не выполняется, производят выбор радиально-упорных подшипников качения.
Врасчетах радиально-упорных подшипников учитывают, что при нагружении их радиальными силами возникают дополнительные осевые уси-
лия, которые определяются:
для радиально-упорных шариковых подшипников - S e R
для радиально-упорных роликовых подшипников- S 0,83 e R ,
где е – коэффициент влияния осевой нагрузки, выбирается в зависимости от типа предварительно выбранного подшипника по величине статической грузоподъемности С0 (таблицы 6-9).
Под статической грузоподъемностью понимают такую статическую силу (радиальную для радиальных и радиально-упорных подшипников; осевую - для упорных и упорно-радиальных), которой соответствует общая ос-
17
таточная деформация тел качения и колец в наиболее нагруженной точке контакта, равная 10-4 диаметра тела качения.
Суммарные осевые нагрузки в подшипниках (Fa A, Fa В) для каждой из опор (А и В) определяют в зависимости от условий нагружения по формулам, приведенным в таблице 10.
Для каждой подшипниковой опоры определяют значения коэффициентов радиальной Х и осевой Y нагрузок, а также уточняют значение коэффициента влияния осевой нагрузки по отношению (таблица 11):
|
|
Fa А,В |
, |
|
|
V R А,В |
|||
|
|
|||
где V - коэффициент вращения кольца подшипника. При вращении |
||||
внутреннего кольца – V = 1. |
|
|
|
|
Эквивалентную динамическую нагрузку для каждой опоры определяют: |
||||
Р ХV R |
|
YFa Кб Кт , |
||
|
|
|
|
где Кб- коэффициент безопасности, Кб = 1,3…1,5; Кт - температурный коэффициент, Кт = 1.
Величины Y и Fa учитывают только для наиболее нагруженной опоры. Долговечность наиболее нагруженной опоры определяют по формуле:
|
|
|
|
106 |
C K |
L |
, |
|||
L |
|
a a |
|
|
|
|
|
|
||
|
|
n |
|
|||||||
|
h |
1 23 |
|
60 |
|
P |
h |
|
где а1 – коэффициент надежности: при вероятности безотказной работы равной 90% - а1 = 1;
а23 – коэффициент, характеризующий влияние на долговечность особых свойств металла деталей подшипника и условий его эксплуатации: для шариковых подшипников – а 23 = 0,7…0,8; для роликовых – а 23 = 0,5…0,7;
n – частота вращения вала на котором установлены подшипники, мин-1; С- динамическая грузоподъемность подшипника, Н (таблицы 6-9.); К- показатель степени: для шариковых подшипников - К=3,
для роликовых- 3,33;
Lh - допустимое значение долговечности подшипников, Lh =20000 ч.
Под динамической грузоподъемностью понимают постоянную силу
(радиальную для радиальных и радиально-упорных подшипников; осевую - для упорных и упорно-радиальных), которую может воспринять подшипник в течение 1 миллиона оборотов.
Если величина расчетной долговечности оказывается меньше допустимого значения, то, как правило, выбирают подшипники других более высоких серий. В случае если же полученное значение долговечности будет в несколько раз превышать допустимое значение, то целесообразно принять подшипник более легкой серии.
18
3 РАСЧЕТ ШПОНОК
3.1 Расчет призматических шпонок
Соединения деталей механических передач в большинстве случае осуществляют с помощью призматических шпонок.
Размеры шпонки выбирают в зависимости от диаметра вала (таблица 2). Длину шпонки l выбирают на 5…10 мм меньше длины ступицы из стандарт-
ного ряда: 6, 8 10, 12, 14, 16, 18, 20, 25, 32, 36, 40, 45, 50, 56, 63, 70, 80, 90.
Выбранную шпонку проверяют на смятие:
см |
4 Т |
< см |
, |
|
|
||||
d h lp |
||||
|
|
|
где Т - крутящий момент на валу, Нмм; d - диаметр вала, мм;
h - высота шпонки, мм (таблица 2);
lp- рабочая длина шпонки, мм; lp l b ,
b - ширина шпонки, мм (таблица 2);
см - допускаемое напряжение смятия, см = 110 МПа.
Если расчетное напряжение смятия будет значительно ниже допускаемого, можно взять шпонку на номер меньше и проверить ее. В случае если же оно превысит допускаемое, следует поставить две шпонки (под углом 1800).
3.2 Расчет сегментных шпонок
При небольших диаметрах сопряжений валов с деталями (до 38 мм) находят применение сегментные шпонки, характеризующиеся высокой технологичностью изготовления и удобством сборки. Вследствие снижения прочности вала за счет глубоких пазов сегментные шпонки применяют при передаче небольших крутящих моментов.
Сегментную шпонку проверяют на смятие, а соединение - на срез:
|
|
|
4 Т |
< ; |
|
2 Т |
, |
|
d h l |
d l b |
|||||
|
см |
|
см |
|
|
||
|
|
|
|
|
|
где Т - крутящий момент на валу, Нмм; d - диаметр вала, мм;
h - высота шпонки, мм (таблица 3); l –длина шпонки, мм;
b - ширина шпонки, мм (таблица 3).
- допускаемое напряжение на срез, = 90 МПа.
Если прочность соединения окажется недостаточной, следует поставить по длине ступицы насаживаемой на вал детали две или даже три шпонки.

|
|
|
19 |
|
|
|
|
4 ПРИМЕРЫ РАСЧЕТОВ |
|
|
|||
|
4.1 Пример проектного расчета вала |
|
|
|||
Выполним расчет тихоходного вала конического редуктора на основании |
||||||
следующих известных данных: окружная сила на колесе Ft= 1535 H; радиаль- |
||||||
ная сила Fr= 203 H; осевая сила Fa= 520 H; средний делительный диаметр |
||||||
зубчатого колеса dm=240 мм; расстояния между линиями приложения нагру- |
||||||
зок –а = 0,06 м, с = 0,155 м; крутящий момент на валу Т= 175 Нм. |
|
|||||
На вал действуют вилы в двух взаимно перпендикулярных плоскостях, |
||||||
поэтому расчетные схемы будем рассматривать в горизонтальной и в верти- |
||||||
кальной плоскости (рисунок 5). |
|
|
|
|
|
|
|
RΣ A |
|
|
RΣ B |
Y |
|
RA Y |
Fa |
|
|
|
X |
|
|
|
RB Y |
|
|||
|
|
|
|
|||
|
RA x |
Fr |
|
RB x |
|
|
|
|
|
|
|
|
|
|
Ft |
|
|
|
|
Z |
А |
С |
|
В |
|
|
|
а |
с |
|
|
|||
|
|
|
|
|
||
RAX |
|
Ft |
|
RBX |
|
|
|
|
|
|
|
|
|
|
|
|
|
Ми x, Нм |
|
|
|
Fa |
66, 6 |
|
|
|
|
RAY |
|
|
RBY |
|
|
|
|
|
|
|
|
||
|
|
Fr |
|
|
|
|
|
|
26, 2 |
|
|
|
|
|
|
|
|
Ми y, Нм |
|
|
|
36,3 |
|
|
|
|
|
|
175 |
|
|
Т, Нм |
|
|
|
|
|
|
|
|
|
Рисунок 5. Эпюры изгибающих и крутящих моментов на валу |
20
а) Определим реакции опор в горизонтальной плоскости (для данной расчетной схемы учитываем только окружную силу и одну реакцию опоры).
Условие равновесия относительно точки А:
МА Ft a RB X a c 0;
отсюда |
|
|
|
|
|
|
|
|
|
|
Ft a |
|
|
1535 0,06 |
|
|
|
|
|
RB X a c |
|
|
|
428 |
Н; |
||||
0,06 0,155 |
|||||||||
Условие равновесия относительно точки В: |
|
|
|
|
|||||
|
МВ Ft с RА X a c 0 ; |
|
|
||||||
отсюда |
|
|
|
|
|
|
|
|
|
|
Ft с |
|
1535 0,155 |
|
|
|
|
||
R |
А X a c |
|
|
|
1106,6 |
Н; |
|||
0,06 0,155 |
Проверка: RA X Ft RB X 1106,6 1535 428 0 .
б) Определим реакции опор в вертикальной плоскости (учитываем осевую и радиальную силу, а также реакцию опоры).
Условие равновесия относительно точки А:
МА Y Fa 0,5 dm Fr a RB Y a c 0;
отсюда
R |
|
|
|
Fr a |
Fa 0,5 dm |
|
|
203 0,06 520 0,5 0,24 |
234 |
Н; |
|||||
B Y |
|
|
a c |
|
|
0,06 0,155 |
|
||||||||
|
|
|
|
|
|
|
|
|
|
|
|||||
|
|
|
|
|
|
|
|
|
|
|
|
|
|||
Условие равновесия относительно точки В: |
|
|
|
|
|||||||||||
|
|
|
|
|
МВY Fr c Fa 0,5 dm RA Y a c 0; |
|
|||||||||
отсюда |
|
|
|
|
|
|
|
|
|
|
|
|
|
|
|
R |
|
|
|
Fr c |
Fa 0,5 dm |
|
|
|
203 0,155 520 0,5 0,24 |
437 |
Н; |
||||
A Y |
|
|
a c |
|
|
0,06 0,155 |
|
|
|||||||
|
|
|
|
|
|
|
|
|
|
|
|
||||
|
|
|
|
|
|
|
|
|
|
|
|
|