
4530
.pdf
21
лю. Приводим стандартное обозначение полученной величины твердости по
Бринеллю: .
Примечание 2. Приведенный пример 1 стандартного обозначения вели-
чины твердости стали по Бринеллю является самым кратким, и он рас-
пространяется только на металлы первой группы (приложение 1), имею-
щие твердость 140 и более единиц по Бринеллю, когда толщина испытуе-
мого образца или изделия позволяет применить шарик при
иот 10 до 15 с. Для всех остальных условий испытаний
стандартные обозначения величин твердости металлов по Бринеллю должны быть даны в расширенных вариантах.
Пример 2. Проведено измерение твердости по Бринеллю образца из про-
ката углеродистой конструкционной стали, которая применялась в примере 1,
однако образец имел толщину |
|
, что позволило применить стальной |
||
шарик |
, |
, |
, |
. Среднее число твер- |
дости, полученное в результате испытаний, составило 227 единиц по Бринеллю.
Приводим стандартные обозначения полученной величины твердости по
Бринеллю: .
Следует обратить снимание на результат изменения твердости стали. Он отличается от примера 1 на две единицы за счет возрастающей погрешности
измерения твердости |
по методу Бринелля с учетом применения |
шарика |
. Кроме того, в приведенном расширенном варианте стандартного |
||
обозначения твердости по Бринеллю указан диаметр шарика |
и задан- |
|
ное усилие на шарик |
. Однако в обозначении твердости продолжи- |
|
тельность выдержки |
не указана, так как она не отличается от интервала |
|
10…15 с, как в примере 1. |
|
|
Пример 3. Проведено измерение твердости по Бринеллю образцов прока- |
||
та углеродистой инструментальной стали У10. Образцы имели |
толщину |
|
. Они подвергались объемной закалке и получили твердость 648 |
||
единиц по Бринеллю. |
Толщина образцов позволила применить шарик |
22
, однако высокая твердость закаленной инструментальной стали (более
450 единиц) потребовала применить шарик из твердого сплава. Кроме того, для
проведения испытаний были выбраны , , от 10
до 15 с, что полностью соответствует требованиям ГОСТа. Приводим стан-
дартные обозначения полученной величины твердости по Бринеллю закаленной
стали У10: |
. |
|
|
Пример 4. Проведено измерение твердости по Бринеллю отливок из |
|||
бронзы с применением стального шарика |
при |
, |
|
и |
. Среднее число твердости, |
полученное в результате |
испытаний, составляет 60,1 единицы по Бринеллю. Приводим стандартное обо-
значение полученной величины твердости по Бринеллю: |
|
. |
|
Обратите внимание, что в приведенном развернутом стандартном обозна- |
|||
чении твердости по Бринеллю указаны: |
, |
, |
. |
Пример 5. В справочной литературе приводится твердость по Бринеллю алюминия технической чистоты – 20 единиц. Необходимо дать стандартные
обозначения твердости алюминия по Бринеллю.
Прежде всего, следует иметь ввиду, что в справочниках указана твердость по Бринеллю, которая имеет минимальную погрешность измерения. А это зна-
чит, что для измерения твердости применяли стальной шарик |
. За- |
тем, пользуясь приложением 1, принимаем для алюминия |
, так |
как алюминий относится к легким металлам и его величина твердости по Бри-
неллю менее 35 единиц. Следовательно, усилие на шарик составит по
формуле (2.9).
Пользуясь приложение 2 находим, что продолжительность выдержки ша-
рика по действием |
|
составит |
. |
Тогда стандартное обозначение твердости по Бринеллю алюминия |
|||
технической чистоты будет: |
|
. |
|
Следует обратить внимание, что в стандартном обозначении твердости |
|||
алюминия символу |
предшествует числовое значение твердости из трех зна- |
23
чащих цифр – , как того требует ГОСТ, хотя в отечественной литературе,
включая справочную, величина твердости, в данном случае, указана двузнач-
ным числом .
Пример 6. В справочной литературе приводится твердость по Бринеллю свинца технической чистоты – 4 единицы. Необходимо дать стандартное обо-
значение твердости свинца по Бринеллю.
Зная о том, что указная величина твердости свинца измерена и примене-
нием стального шарика |
, в приложении 1 находим |
, |
по формуле (1.9) определяем |
, из приложения 2 устанавливаем |
.
Тогда стандартное обозначение твердости по Бринеллю свинца будет:
.
5. ОСНОВНЫЕ УСЛОВИЯ ИЗМЕРЕНИЯ ТВЕРДОСТИ МЕТАЛЛОВ ПО
МЕТОДУ РОКВЕЛЛА
Данный метод измерения твердости металлов предложен американским металлургом С.П. Роквеллом в 1920 г. И за длительный период применения в
разных станах мира существенно видоизменен.
Настоящий стандарт устанавливает метод измерения твердости по Рок-
веллу (шкалы A, B, C, D, E, F, G, H, K) при температуре |
0С. При разно- |
|
гласиях в результатах измерение твердости проводят при температуре |
0С. |
Сущность метода заключается во внедрении в поверхность испытуе-
мого образца (или изделия) алмазного конусного (шкалы A, C, D) или стального сферического индентора (шкалы B, E, F, G, H, K) под действием
последовательно прилагаемых предварительного и основного уси-
лий и в определении глубины внедрения индентора после снятия основно-
го усилия ( ).
Толщина образца (или изделия) должна не менее чем в 10 раз превышать глубину внедрения индентора после снятия основного усилия ( ).
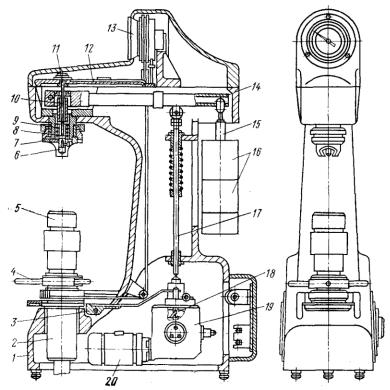
24
Образец должен быть подготовлен таким образом, чтобы не изменились его свойства в результате механической обработки на металлорежущих стан-
ках: от нагрева или от наклепа. Рабочие поверхности образца или испытуемого изделия должны быть плоскими, гладкими, не иметь окалины, ржавчины, тре-
щин, выбоин, раковин, загрязнения (включая пыль), смазки или каких-либо по-
крытий. Обработку рабочих поверхностей можно проводить чистовым точени-
ем или чистовым фрезерованием, шлифованием мелкозернистой шлифовальной шкуркой. Опорные поверхности образца или изделия должны быть очищены от посторонних веществ (окалины, ржавчины, загрязнений, смазки и др.).
Испытания металлов на твердость проводят на приборе Роквелла
(рис. 2.3), который должен обеспечивать применение условий, приведенных в табл. 2.1.
1 – литой чугунный корпус; 2 – механизм подъема рабочего столика; 3 – клавиша включения механизма нагружения; 4 – маховик; 5 – стол прибора;
6 – ограничитель индентора; 7 – наконечник; 8 – направляющая втулка; 9 – пружина предварительного нагружения; 10 – шпиндель; 11 – плавающая подвеска
шпинделя; 12 – рычаг; 13 – индикатор; 14 – рычаг; 15 –подвеска; 16 – грузы; 17 – шток; 18 – рабочий кулачок; 19 – одноступенчатый червячный редуктор;
20 – электродвигатель Рисунок 2.3 – Принципиальная схема прибора Роквелла
25
Прибор имеет при сенных индикатора: алмазный конус с углом при вер-
шине 1200 и радиусом сферической части 0,2 мм (шкалы твердости A, C, D);
стальные закаленные шарики двух |
диаметров |
– |
|
|
(шкалы |
||||||
твердости B, F, G) и |
|
|
(шкалы твердости E, H, K). |
|
|
||||||
Таблица |
2.1 – Условия и |
измерения |
|
твердости |
металлов по |
методу |
Роквелла |
||||
(ГОСТ 9013-59, ИСО 6508-86) |
|
|
|
|
|
|
|
|
|
||
|
|
|
|
Обо- |
|
|
|
|
|
|
Диапа- |
Шка- |
|
|
|
значе- |
|
Предва- |
Основное |
|
Общее |
|
зон |
|
Тип сменного ин- |
|
ние |
|
ритель- |
|
|
изме- |
|||
ла |
|
|
|
усилие |
|
усилие |
|
||||
|
дентора прибора |
|
едини- |
|
ное уси- |
|
|
рений |
|||
твер- |
|
|
|
|
|
|
|
||||
|
Роквелла |
|
цы |
|
лие |
|
|
|
|
единиц |
|
дости |
|
|
|
|
|
|
|
||||
|
|
|
твер- |
|
|
|
|
|
|
твер- |
|
|
|
|
|
|
|
|
|
|
|
||
|
|
|
|
дости |
|
|
|
|
|
|
дости |
A |
|
Алмазный конус |
|
HRA |
|
98 (10) |
490 (50) |
|
588 (60) |
|
20…88 |
B |
|
Стальной шарик |
|
HRB |
|
98 (10) |
883 (90) |
|
981 |
|
20…10 |
|
1,588 мм |
|
|
|
(100) |
|
0 |
||||
|
|
|
|
|
|
|
|
|
|||
C |
|
Алмазный конус |
|
HRC |
|
98 (10) |
1373 |
|
1471 |
|
20…70 |
|
|
|
(140) |
|
(150) |
|
|||||
|
|
|
|
|
|
|
|
|
|
||
D |
|
Алмазный конус |
|
HBD |
|
98 (10) |
883 (90) |
|
981 |
|
40…77 |
|
|
|
|
(100) |
|
||||||
|
|
|
|
|
|
|
|
|
|
|
|
E |
|
Стальной шарик |
|
HRE |
|
98 (10) |
883 (90) |
|
981 |
|
70…10 |
|
3,175 мм |
|
|
|
(100) |
|
0 |
||||
|
|
|
|
|
|
|
|
|
|||
F |
|
Стальной шарик |
|
HRF |
|
98 (10) |
490 (50) |
|
588 (60) |
|
60…10 |
|
1,588 мм |
|
|
|
|
0 |
|||||
|
|
|
|
|
|
|
|
|
|
||
G |
|
Стальной шарик |
|
HRG |
|
98 (10) |
1373 |
|
1471 |
|
30…94 |
|
1,588 мм |
|
|
(140) |
|
(150) |
|
||||
|
|
|
|
|
|
|
|
|
|||
H |
|
Стальной шарик |
|
HRH |
|
98 (10) |
588 (60) |
|
588 (60) |
|
80…10 |
|
3,175 мм |
|
|
|
|
||||||
|
|
|
|
|
|
|
|
|
|
|
|
K |
|
Стальной шарик |
|
HRK |
|
98 (10) |
1373 |
|
1471 |
|
40…10 |
|
3,175 мм |
|
|
(140) |
|
(150) |
|
0 |
|||
|
|
|
|
|
|
|
|
Алмазный конус применяют при измерениях твердости металлов в широ-
ком диапазоне – от 219 до 810 единиц по Бринеллю. Стальные шарики приме-
нят при твердости металлов до 240 единиц по Бринеллю.
Прибор Роквелла содержит следующие механизмы, смонтированные на литой чугунной станине:
1 Механизм привода, состоящий из электродвигателя и редуктора.
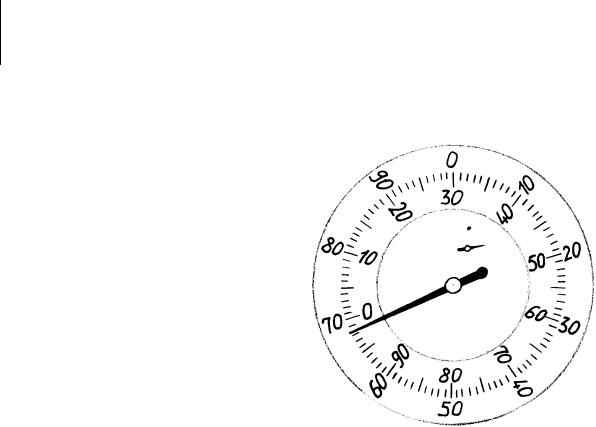
26
2 Механизм подъема рабочего столика.
3 Механизм нагружения индентора.
4 Индикатор часового типа для измерения глубины вдавливания инденто-
ра в металл и отсчета числа твердости по Роквеллу.
Примечание 4. Вместо индикатора часового типа прибор Роквелла может иметь электронное цифровое отсчетное устройство.
Последовательность операций при проведении испытаний металлов
на твердость на приборе Роквелла заключается в следующем (см. рис. 2.3).
Исходя из предполагаемой твер- |
|
||
дости материала испытуемого образца, |
|
||
необходимо по табл. 2.1 выбрать шкалу |
|
||
твердости индикатора (рис. 2.4), тип |
|
||
сменного индентора и основное усилие |
|
||
на индентор, после чего провести под- |
|
||
готовку прибора к работе. При этом, |
|
||
наравне с установкой на шпинделе при- |
|
||
бора выбранного сменного индентора, |
|
||
необходимо установить на подвеску |
|
||
механизма нагружения сменные гири, |
Рисунок 2.4 – Индикатор прибора |
||
Роквелла |
|||
|
|
||
обеспечивающие основное усилие |
на |
|
индентор, а также необходимо установить нуль черной шкалы циферблата ин-
дентора в верхнее положение симметрично окружности шкалы (см. ниже опи-
сание циферблата индентора).
Опорные поверхности рабочего столика или подставки должны быть очищены от посторонних веществ (пыли, окалины, смазки и др.), а перед про-
ведением испытаний их следует протирать ветошью из белой хлопчатобумаж-
ной ткани.
Образец должен быть установлен на столике или подставке устройства во избежание его смещения и прогиба во время измерения твердости. При этом
27
должна быть обеспечена перпендикулярность приложения предварительного и основного усилий к поверхности образца. При измерении твердости
прибор должен быть защищен от вибрации, толчков и ударов.
С помощью тумблера следует включить электродвигатель механизма привода прибора. Вращая маховик механизма подъема рабочего столика по ча-
совой стрелке, плавно поднимают столик с испытуемым образцом.
При измерении твердости должны соблюдаться следующие условия
ГОСТа:
1. Плавное приведение индентора в контакт с рабочей поверхностью об-
разца. |
|
2. Плавное приложение предварительного усилия |
к образцу при подъ- |
еме рабочего столика за счет сжатия тарированной пружины, установленной на шпинделе. С момента соприкосновения индентора с поверхностью образца бу-
дут вращаться обе стрелки индикатора.
Подъем столика продолжают до тех пор, пока маленькая стрелка не при-
мет вертикальное положение, указанные на циферблате красной точкой. Это означает, что индентор вдавился в образец под действием предварительного
усилия (10 кгс). Большая стрелка в этот момент должна остановиться
против нуля черной шкалы. Если положение большой стрелки не совпадает точно с цифрой 0, то поворачивают шкалу циферблата до совмещения 0 черной шкалы со стрелкой. Это положение шкалы является исходным при измерении твердости как алмазным конусом, так и стальными шариками.
3. Нажимая клавишу механизма нагружения, должно быть обеспечено
плавное приложение основного усилия в течение 2…8 с. При этом большая
стрелка индикатора, вращаясь против направления движения часовой стрелки,
отсчитает на выбранной шкале циферблата глубину вдавливания |
индентора |
|
под действием общего усилия |
. Каждому делению глубины вдав- |
|
ливания будет соответствовать 0,002 мм. |
|
|

|
|
28 |
4. Через 1…3 с после резкого замедления или остановки большой стрелки |
||
индикатора основное усилие |
автоматически плавно снимается, а предвари- |
|
тельное усилие |
остается. При этом большая стрелка будет вращаться в про- |
тивоположную сторону, т.е. по направлению часовой стрелки, уменьшая глу-
бину вдавливания до величины . После остановки большая стрелка пока-
жет на выбранной шкале твердости число делений, соответствующее величине твердости по Роквеллу. Этой твердости металла будет соответствовать изме-
ренная индикатором глубина внедрения индентора .
Примечание 5. Для металлов, при измерении твердости которых резкого замедления или остановки большой стрелки индикатора не наблюдается,
время выдержки под общим усилием должно составлять от 10 до 15 с.
Число твердости по Роквеллу определяется по шкале циферблата индика-
тора с округлением до целых единиц или до 0,5 единицы твердости, и оно
выражается числовым значением из трех значащих цифр.
Количество отпечатков на одном образце при измерении твердости по Роквеллу указывается в нормативно-технической документации. Для учебных целей следует рекомендовать три опыта. Расстояние между центрами двух со-
седних отпечатков должно быть не менее 2 мм. Расстояние от центра отпечатке до края образца должно быть не менее 1 мм.
После смены индентора, рабочего столика или подставки первые три из-
мерения не учитываются.
Чтобы понять сущность измерения твердости металлов по методу Рок-
велла, необходимо ознакомиться с устройством и принципом работы индикато-
ра часового типа (рис. 2.4), а также со схемами измерения твердости металлов алмазным конусом (рис. 2.5) и стальными шариками (рис. 2.6).
Окружность циферблата индикатора прибора Роквелла разбита на 100
равных делений, которые отмечены штрихами. Между штрихами точками от-
мечены половинки делений. По окружности циферблата нанесено две цифро-
вых разметки через 10 делений по направлению движения часовой стрелки:

29
Рисунок 2.5 – Схема измерения твердости металлов по методу Роквелла (индентор – алмазный конус, шкалы твердости – A, C, D)
Рисунок 2.6 – Схема измерения твердости металлов по методу Роквелла (инденторы – стальные шарики: 1,588 мм – шкалы твердости B, F, G; 3,175 мм –
шкалы твердости E, H, K)
– внешняя разметка нанесена черной краской, поэтому называется черной
шкалой. Начало шкалы (0 делений) и конец шкалы (100 делений) совпадают.
30
Она является кольцевой шкалой или замкнутой. Эта шкала предназначена для измерений твердости металлов алмазным конусом при трех разных общих уси-
лиях (см. табл. 2.1). Поэтому и числа твердости, полученные при этих изме-
рениях, обозначают по трем шкалам твердости: A, C, D;
– внутренняя цифровая разметка нанесена красной краской, поэтому на-
зывается красной шкалой. Эта шкала начинается на 30 делений раньше, чем черная цифровая разметка: 0 красной шкалы совпадает с цифрой 70 черной шкалы. Красная шкала имеет 130 делений и является разомкнутой. Конец этой шкалы (130 делений) совпадает с концом черной шкалы (100 делений). Красная шкала предназначена для измерений твердости металлов стальными шариками:
диаметром 1,588 мм (шкалы твердости B, F, G) и диаметром 3,175 мм (шкалы
твердости E, H, K).
На рис. 2.5 и 2.6 показано, что при внедрении в поверхность испытуемого образца алмазного конуса либо стального шарика под действием предваритель-
ного усилия |
(10 кгс) индентор погружается в металл на некоторую |
||
глубину , |
которую индикатор не измеряет, поэтому величина |
нам неиз- |
|
вестна. Значение глубины |
зависит от следующих условий испытаний: типа |
индентора, испытуемого металла и шероховатости его поверхности. Однако при любых условиях после предварительного нагружения инденторы испыты-
вают одну и ту же величину сопротивления металла, которая численно равна 98
Н (10 кгс).
Таким образом, предварительное нагружение инденторов при испытаниях металлов на твердость по методу Роквелла создает равные исходные условия
для дальнейшего нагружения образцов. Поэтому на рис. 2.5 и 2.6 на глубине от поверхности образца показана исходная линия измерения. От этой вообра-
жаемой линии большая стрелка индикатора отсчитывает глубину вдавливания
индентора под действием общего усилия . При этом большая
стрелка, вращаясь против часовой стрелки, отнимает от 100 делений (рис. 2.5)