
4530
.pdf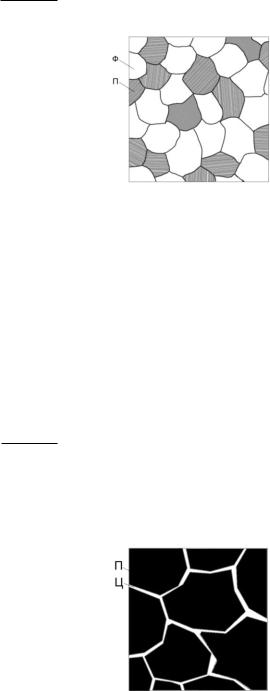
11
Пример выполнения индивидуального задания
1. В доэвтектоидной стали согласно варианту содержится 50 % перлита,
следовательно остальные 50 % – феррит. Так как при комнатной температуре в феррите содержится 0,006 % углерода, количеством углерода в феррите пре-
небрегаем. Перлит содержит 0,8 % углерода. 100 % П – 0,8 % С; 50 % П – x % С,
50 0,8
тогда x 0,4 % С – содержится в данной стали.
100
Рисунок 1.4 – Схема микроструктуры стали 40
2. В заэвтектоидной стали согласно варианту содержится 1 % цементита,
тогда остальное 99 % перлита. Цементит содержит 6,67 %, а перлит – 0,8 % уг-
лерода.
100 % П – 0,8 % С; 99 % П – x % С, тогда x |
99 0,8 |
0,792 % С. |
|
100 |
|
||
|
|
|
|
100 % Ц – 6,67 % С; 1 % Ц – y % С, |
|
|
|
1 6,67
тогда y 0,0667 % С.
100
z x y 0,792 0,0667 0,8587 0,9 % С – содержится в данной
стали.
Рисунок 1.5 – Схема микроструктуры стали У9
12
ЛАБОРАТОРНАЯ РАБОТА 2.
ОПРЕДЕЛЕНИЕ ТВЕРДОСТИ, ПЛАСТИЧНОСТИ,
УДАРНОЙ ВЯЗКОСТИ МЕТАЛЛОВ
1. ЦЕЛЬ РАБОТЫ
1.1. Изучить два основных метода определения твердости металлов в ма-
шиностроении – метод Бринелля (ГОСТ 9012-59, ИСО 6506-81, ИСО 410-82)
и метод Роквелла (ГОСТ 9013-59, ИСО 6508-86).
1.2. Получить навыки измерения твердости металлов по методам Бринел-
ля и Роквелла.
1.3. Изучить варианты стандартных обозначений чисел твердости метал-
лов по Бринеллю и Роквеллу для различных условий испытаний образцов или изделий, а также уметь воспроизводить эти обозначения на чертежах и в тек-
стовых документах (пояснительных записках) курсовых работ, курсовых и ди-
пломных проектов, в отчетах о производственных практиках, в производствен-
ной конструкторской и технологической документации.
2. ОБЩИЕ ПОЛОЖЕНИЯ ТВЕРДОСТИ МЕТАЛЛОВ
Твердость металла – это сопротивление, которое оказывает металл,
проникновению в него другого более твердого тела (индентора).
Измерение твердости является наиболее простым и быстрым видом меха-
нических испытаний металлов, при котором не происходит разрушение образ-
цов или изделий. Этот вид испытаний широко применяется в металлургии и машиностроении для контроля качества металлов на образцах, полуфабрикатах и готовых изделиях после различных видов их обработки.
Существующие методы измерения твердости делятся на несколько групп:
вдавливание одного тела в другое; царапание одного тела другим; отскакивание стандартного бойка при падении с определенной высоты на поверхность испы-
туемого материала; магнитные; электрические и другие. При измерении твер-
13
дости металлов самое большое распространение получили статические методы вдавливания, когда твердый индентор, имеющий определенную форму (шарик,
конус, призма) плавно вдавливается в испытуемый металл под действием за-
данного усилия. Величина этого усилия должна обеспечивать не только упру-
гую, но и пластическую деформацию металла в месте вдавливания индентора.
После снятия усилия измеряют глубину отпечатка или его поперечный размер
(диаметр, диагональ) и путем расчета определяют число твердости металла.
Методы вдавливания позволяют определить:
1.Макротвердость металлов – при усилиях на индентор больше 3 кгс.
2.Твердость металлов при малых нагрузках – при усилиях на инден-
тор от 0,2 до 3 кгс.
3. Микротвердость металла –при усилиях на индентор до 0,2 кгс.
3. ОСНОВНЫЕ УСЛОВИЯ ИЗМЕРЕНИЯ ТВЕРДОСТИ МЕТАЛЛОВ ПО МЕТОДУ БРИНЕЛЛЯ
Данный метод измерения твердости металлов предложен шведским ин-
женером Ю.А. Бринеллем в 1900 г. и значительно усовершенствован за более вековой период применения во многих странах мира: в металлургии, в различ-
ных отраслях машиностроения, в научных исследованиях.
В нашей стране и в странах СНГ, с учетом гармонизации ГОСТов с меж-
дународными стандартами ИСО, действующий ГОСТ 9012-59 (ИСО 6506-81 и
ИСО 410-82) устанавливает метод измерения твердости по Бринеллю металлов с твердостью не более 650 единиц. При этом минимальная величина твердости металла, которую можно измерить по методу Бринелля, соответствует твердо-
сти самого мягкого металла – свинца (при комнатной температуре его твер-
дость составляет четыре единицы по Бринеллю).
Сущность метода заключается во вдавливании шарика (стального закаленного или из твердого сплава) диаметром (мм) в образец металла или в изделие под действием усилия (Н или кгс), приложенного перпен-
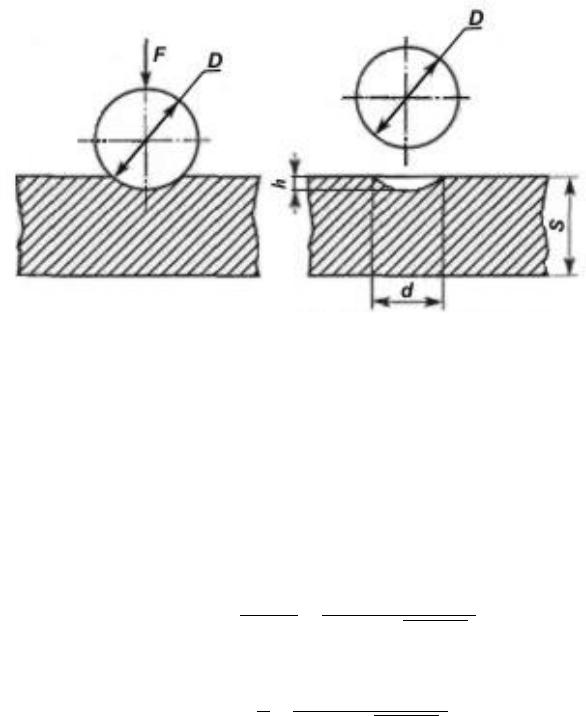
14
дикулярно поверхности испытуемого металла, в течение определенного
времени (с), и измерении диаметра сферического отпечатка (мм) на
F – приложенная сила, Н (кгс); D – диаметр шарика, мм; d – диаметр отпечатка, мм; h – глубина отпечатка, мм
Рисунок 2.1 – Схема измерения твердости металлов по Бринеллю
поверхности металла после снятия усилия (рис. 2.1). |
|
|
Твердость по Бринеллю обозначается символом |
при испытании |
|
стальным шариком или символом |
при испытании шариком из твердого |
сплава. Величина твердости численно равна отношению приложенного усилия к площади сферического отпечатка (мм2) и рассчитывается по формулам
(2.1) или (2.2):
когда усилие выражается в Н;
когда усилие выражается в кгс.
Из формул (2.1) и (2.2) следует, что площадь сферического отпечатка ,
представляющего собой шаровой сегмент, равна (2.3):
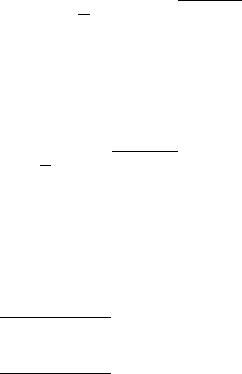
15
где – глубина отпечатка, мм.
Отсюда следует, что глубину отпечатка можно вычислить по формуле
(2.4):
Толщина испытуемого образца (мм) должна не менее чем в 8 раз пре-
вышать глубину отпечатка . Значение определяется по формулам (2.5) или
(2.6) при известных величинах твердости металла или :
Поверхность образца или испытуемого изделия должна быть плоской,
гладкой и свободной от окалины, ржавчины, трещин, раковин, загрязнений,
масла. Обработку поверхности можно проводить чистовым точением (торцева-
нием), чистовым фрезерованием, мелким напильником, шлифованием. При оп-
ределении твердости шариком мм поверхность образца должна быть от-
полирована.
Прибором для измерения твердости является пресс Бринеллю по ГОСТ
23677-79. Для испытаний применяют следующие инденторы: стальные шарики диаметром 10,0; 5,0; 2,5; 2,0; 1,0 мм, которые должны иметь после закалки и низкого отпуска твердость по Виккерсу не менее 850 единиц; шарики из твер-
дого сплава также диаметром 10,0; 5,0; 2,5; 2,0; 1,0 мм, которые должны иметь твердость по Виккерсу не менее 1500 единиц. Применение шариков диаметром
10,0 мм приводит к минимальной погрешности измерения твердости. Если применять шарики меньших диаметров, то полученные величины твердости будут меньше, чем для шариков диаметром 10,0 мм. Так, для сталей и чугунов с твердостью 140 и более единиц по Бринеллю уменьшение величины твердости

16
составляет: 1…2 единицы – для шариков диаметром 5,0 мм; 2…3 единицы – для шариков диаметром 2,5 мм и т.д. по сравнению с твердостью, полученной
при испытании металла шариком диаметром 10,0 мм. |
|
Измерения твердости проводят при температуре |
0С. При разно- |
гласиях в оценке качества металлопродукции измерения проводят при температуре 0С.
Образец должен быть установлен на плоский стол или подставку пресса
Бринелля устойчиво, без перекосов во избежание его смещения и прогиба во время испытания твердости. При твердости металлов до 450 единиц по Бри-
неллю для измерения применяют как стальные шарики, так и шарики из твер-
дого сплава; при твердости металлов более 450 единиц – шарики только из твердого сплава.
Усилие устанавливают в зависимости от коэффициента подобия испы-
таний и диаметра шарика . В приложении 1 помещена таблица, в которой приведены значения коэффициентов для пяти групп металлов. Коэффициент представляет собой отношение усилия к квадрату диаметра шарика и опре-
деляется по формулам (2.7) и (2.8):
Первая группа металлов содержит сталь, чугун, высокопрочные сплавы
(на основе никеля, кобальта и др.). В этой группе – две подгруппы металлов по твердости: первая подгруппа металлов с твердостью по Бринеллю до 140 еди-
ниц имеет коэффициент |
; вторая подгруппа металлов с твердо- |
|
стью по Бринеллю 140 и более единиц имеет коэффициент |
. |
|
Следует подчеркнуть, что значение выбранного коэффициента |
распространя- |
|
ется на все диаметры шариков при испытании данного металла. |
|
17
Пользуясь формулой (2.8), при выбранных значениях и легко опре-
делить по формуле (2.9):
Диаметр шарика и соответствующее усилие выбирают таким обра-
зом, чтобы диаметр отпечатка неходился в пределах от 0,24 до 0,6 .
Приведем пример. Углеродистая конструкционная сталь имеет твердость
по Бринеллю |
229 |
единиц. |
Из приложения |
1 |
выбираем значение |
||||
|
. |
|
|
|
|
|
|
|
|
Если |
толщина |
испытуемого |
образца |
позволяет |
применить шарик |
||||
, |
то |
по |
формуле |
(2.9) |
усилие |
на |
шарик |
должно быть |
|
|
|
|
. В этом случае после испытания получим среднее |
||||||
значение диаметра отпечатка |
|
. |
|
|
|
|
|||
Если |
толщина |
испытуемого |
образца |
позволяет |
применить шарик |
||||
, то по формуле (2.9) усилие на шарик должно быть в 4 раза меньше, |
|||||||||
т.е. |
|
или |
|
. В этом случае после испытания получим |
|||||
среднее значение диаметра отпечатка |
|
( |
будет немногим более 2 |
мм, что приведет к снижению величины твердости по Бринеллю примерно на
1…2 единицы по сравнению с испытанием этой же стали шариком |
). |
|
Принципиальная схема пресса Бринелля показана на рис. 2.2. Прибор со- |
||
держит следующие механизмы, смонтированные на литой чугунной станине: |
|
|
1 |
Механизм привода, состоящий из электродвигателя и двухступенчатого |
|
червячного редуктора. |
|
|
2 |
Механизм подъема стола. |
|
3 |
Механизм шарнирного четырехзвенника. |
|
4 |
Механизм нагружения шарика. |
|
5 |
Механизм переключения направления движения (реверсирования). |
|
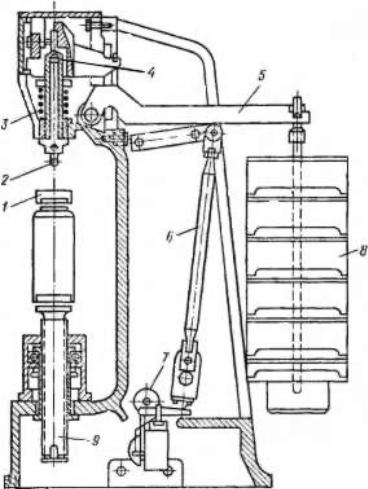
18
Последовательность операций при проведении испытаний металлов
на твердость на прессе Бринеллю заключается в следующем. На плоский стол или специальную подставку устанавливают подготовленный образец ме-
талла (см. рис. 2.2). Вращая маховик по часовой стрелке, поднимают стол с об-
|
разцом до упора в огра- |
|||
|
ничитель подъема. При |
|||
|
этом шарик, закреплен- |
|||
|
ный на шпинделе, войдет |
|||
|
в соприкосновение с ис- |
|||
|
пытуемым образцом и за |
|||
|
счет сжатия |
пружины |
||
|
будет вдавливаться в ме- |
|||
|
талл |
предварительным |
||
|
усилием 100 кгс. Нажи- |
|||
|
мая на пусковую кнопку, |
|||
|
включают механизм при- |
|||
|
вода пресса. При этом |
|||
|
приходит в движение ме- |
|||
|
ханизм |
шарнирного ры- |
||
|
чажного четырехзвенни- |
|||
1 – плоский стол; 2 – шарик; 3 – пружина; |
ка, который обеспечивает |
|||
4 – шпиндель; 5 – грузовой рычаг; 6 – механизм шар- |
||||
|
|
|
||
нирного рычажного четырехзвенника; |
работу механизма нагру- |
|||
7 – механизм привода пресса; 8 – гири; 9 – механизм |
||||
|
|
|
||
подъема стола |
жения. |
Грузовой рычаг с |
||
Рисунок 1.2 –Принципиальная схема |
|
|
|
|
пресса Бринелля |
подвешенными |
гирями |
плавно опускается, передавая усилие на шпиндель с шариком. После плавного
(статического) нагружения усилие достигает установленного значения. В этот момент загорается сигнальная лампа прибора, и она должна гореть в течение определенного времени , соответствующего продолжительности выдержки образца под усилием . По истечении времени сигнальная лампа гаснет, и
19
происходит разгрузка шарика. При этом грузовой рычаг поднимается в исход-
ное положение.
После цикла нагружения шарика, его выдержки под действием усилия
и разгрузки происходит автоматическое отключение электродвигателя. Враще-
нием маховика против часовой стрелки опускают стол с образцом. На его по-
верхности будет получен сферический отпечаток. Расстояние между центром отпечатка и краем образца должно быть не менее 2,5 диаметра отпечатка ;
расстояние между централи двух отпечатков должно быть не менее ; для ме-
таллов с твердость по Бринеллю до 35 единиц эти расстояния должны быть со-
ответственно и .
При разногласиях в результатах измерения твердости на образцах с кри-
волинейной поверхностью длина и ширина изготовленной плоской площадки
должна быть не менее .
На одном образце металла должно быть проведено не менее двух опытов.
Для учебных целей следует рекомендовать три опыта. Диаметр каждого отпе-
чатка измеряют в двух взаимно перпендикулярных направлениях с помощью
микроскопа МПБ-2, который имеет 24-кратное увеличение ( 24). Длина изме-
рительной шкалы микроскопа – 6,5 мм, цена деления шкалы – 0,05 мм.
После измерений для каждого отпечатка получают два значения его диа-
метра – и . За диаметр отпечатка принимается среднее арифметическое
значение результатов измерений. При этом разность измерений диаметров од-
ного отпечатка не должна превышать 2 % меньшего из них.
По среднему значению диаметра отпечатка определяют величину твердо-
сти по Бринеллю для каждого отпечатка по формулам (2.1) и (2.2) или по таб-
лицам. Затем определяют среднее арифметическое значение |
, кото- |
рое характеризует твердость по Бринеллю испытанного металла. |
|

20
4. ОБОЗНАЧЕНИЕ ТВЕРДОСТИ МЕТАЛЛОВ ПО БРИНЕЛЛЮ После гармонизации ГОСТ 9012-59 с международными стандартами ИСО
6506-81 и ИСО 410-82 обозначения твердости металлов по Бринеллю существенно изменились, поэтому следует иметь ввиду, что прежние обозначения отменены и являются недействительными. Действующие обозначения твердости металлов учитывают условия испытаний и позволяют воспроизводить указанные условия при повторных измерениях.
Твердость по Бринеллю обозначают символом |
при испытаниях |
|
металлов стальным шариком и символом |
при испытаниях шариком |
из твердого сплава. Символу предшествует числовое значение твердости из трех значащих цифр, а после символа указывают диаметр шарика, зна-
чение приложенного усилия (в ), продолжительность выдержки, если она отличается от интервала 10…15 с.
Примечание 1. Значащимися цифрами называют все верные цифры числа, кроме нулей, стоящих впереди числа. Например, запись 20,4 означает, что верны все три цифры, включая десятые доли; истинное число может быть 20,43 или 20,39, но не 20,453 и не 20,342 с учетом правил округления чисел до трех значащих цифр.
Приведем примеры стандартных обозначений величин твердости ме-
таллов по Бринеллю, полученных при различных условиях испытаний образцов или изделий.
Пример 1. В соответствии с протоколом №1 проведено измерение твердости по Бринеллю образца из проката углеродистой конструкционной стали.
Условия испытания: толщина плоского испытуемого образца |
; диа- |
||
метр стального шарика |
; коэффициент |
подобия |
испытаний |
; заданное усилие на шарик |
; продолжительность вы- |
||
держки шарика под действием заданного усилия |
. Среднее число твер- |
дости, полученное в результате испытаний, составляет 229 единиц по Бринел-