
4121
.pdf
11
Рис. 2.2. Схема испытаний
Порядок выполнения работы
1.Ознакомиться с методическими указаниями, установкой и приспособлениями для испытаний.
2.Измерить образцы и определить плотность материала.
3.Подготовить образцы для испытания.
4.Провести испытания.
5.Вычислить удельное сопротивление выдергиванию шурупов и занести результаты в табл. 2.1.
6.Построить график зависимости удельного сопротивления выдергиванию шурупов от плотности материала.
7.Проанализировать полученные результаты и сделать выводы.
8.Написать отчет.
12
Таблица 2.1
Результаты испытаний
№ |
Материал образца |
Размеры образца , мм |
Масса |
Плот- |
L, |
Рmax, |
gш, |
||
обр. |
и направление за- |
длина |
шири- |
тол- |
образца, |
ность, |
мм |
Н |
Н/мм |
|
|
|
|
|
|
кг/м3 |
|||
|
винчивания |
|
на |
щина |
г |
|
|
|
|
1 |
2 |
3 |
4 |
5 |
6 |
7 |
8 |
9 |
10 |
1 |
Дуб |
|
|
|
|
|
|
|
|
|
Радиальное |
|
|
|
|
|
|
|
|
|
Тангенциальное |
|
|
|
|
|
|
|
|
|
Торец |
|
|
|
|
|
|
|
|
2 |
Береза |
|
|
|
|
|
|
|
|
|
Радиальное |
|
|
|
|
|
|
|
|
|
Тангенциальное |
|
|
|
|
|
|
|
|
|
Торец |
|
|
|
|
|
|
|
|
3 |
Сосна |
|
|
|
|
|
|
|
|
|
Радиальное |
|
|
|
|
|
|
|
|
|
Тангенциальное |
|
|
|
|
|
|
|
|
|
Торец |
|
|
|
|
|
|
|
|
4 |
ДСтП |
|
|
|
|
|
|
|
|
|
Пласть |
|
|
|
|
|
|
|
|
|
Кромка |
|
|
|
|
|
|
|
|
5 |
МДФ |
|
|
|
|
|
|
|
|
|
Пласть |
|
|
|
|
|
|
|
|
|
Кромка |
|
|
|
|
|
|
|
|
Содержание отчета
1.Общая характеристика способа соединения деталей на шурупах.
2.Методика испытаний.
3.Результаты испытаний.
4.Графики зависимости удельного сопротивления выдергивания шурупов от плотности материала.

13
Лабораторная работа № 3
КОНТРОЛЬ ШЕРОХОВАТОСТИ ПОВЕРХНОСТИ
Цель работы: изучить влияние характера обработки поверхностей деталей из древесины и древесных материалов на шероховатость поверхности.
Общие сведения: Для оценки шероховатости поверхности древесины и древесных материалов применяют параметры: Rm max, Rm, Rz, Rи Sz.
Параметр Rm max представляет собой среднее арифметическое из наибольших по высоте неровностей Hmax, найденных выборочно на контролируемой поверхности
|
1 |
n |
|
Rm max |
|
Hmax i , |
(3.1) |
|
|||
|
n i 1 |
|
где Hmax I – расстояние от высшей до низшей точки i-той неровности, мкм; n – число измерений.
Параметр Rm представляет собой наибольшую высоту неровностей
профиля, вычисляемую по формуле |
|
Rm= Yp max+ Yv max, |
(3.2) |
где Yp max – расстояние от средней линии до высшей точки профиля в пределах базовой длины (рис. 3.1);
Yv max – расстояние от средней линии до низшей точки профиля в пределах базовой длины.
Параметр Rz представляет собой среднеарифметическое значение неровностей профиля, определяемое из пяти наибольших неровностей, расположенных в пределах базовой длины ℓ (рис. 3.1),
|
1 |
5 |
5 |
|
|
Rz |
|
hmax i |
hmini , |
(3.3) |
|
|
|
||||
5 |
|
||||
|
i 1 |
i |
1 |
|
где hmax I ; hmin I – расстояние от пяти наивысших и пяти наинизших точек профиля до линии отсчета, проведенной параллельно средней линии и не пересекающей профиль.
Параметр Rпредставляет собой среднее арифметическое отклонений профиля от его средней линии в пределах базовой длины ℓ и может быть определен путем измерения и последующего суммирования ряда ординат yi в пределах базовой длины (рис. 3.1)
|
1 |
n |
|
|||
R |
|
yi |
, |
(3.4) |
||
|
|
|||||
n i 1 |
||||||
|
|
|
|
где n – число ординат yi.
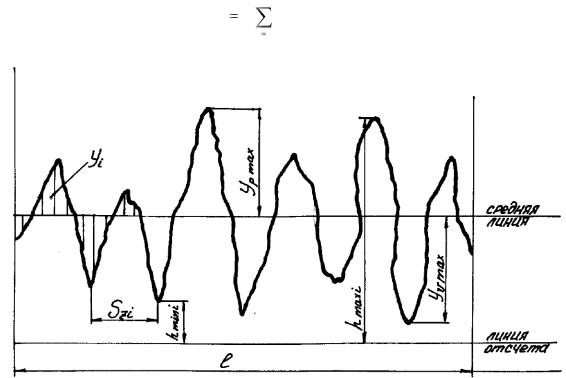
14
Параметр Sz характеризует шаг неровностей, определяемый по впадинам профиля (рис. 3.1),
|
1 |
|
n |
|
|
Sz |
|
|
Szi . |
(3.5) |
|
n i |
|||||
|
1 |
|
Рис. 3.1. Схематическое изображение профиля поверхности Согласно ГОСТ 7016-82 базовая длина выбирается в зависимости от
качества обработки поверхностей из следующих значений: 0,8; 2,5; 8 и 25 мм. Для контроля шероховатости поверхности древесины и древесных материалов принимаются индикаторные глубиномеры, допускающие выборочное измерение отдельных неровностей, оптические приборы МИС-11 и
ТСП-4, профилографы и профилометры.
Контроль шероховатости в производственных условиях может осуществляться путем визуального сравнения с эталонами.
Материалы, оборудование, приборы
1.Образцы из сосновой древесины, обработанные пилением, фрезерованием и шлифованием; образцы из ДСтП и МДФ, обработанные шлифованием. Шлифовальная шкурка различной зернистости.
2.Индикаторный глубиномер, микроскоп МИС-11, профилограф-
профилометр.
Порядок выполнения работы
1.Ознакомиться с методическими указаниями.
2.Ознакомиться с принципом действия измерительных приборов.
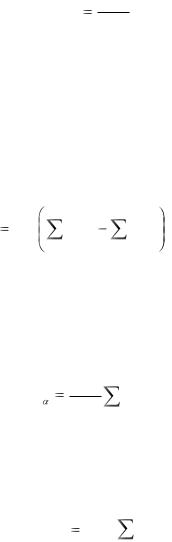
15
3.Подготовить образцы для измерений.
4.Провести измерения грубых неровностей с помощью индикаторного глубиномера.
5.Снять профилограммы поверхностей с помощью профилографапрофилометра и зафиксировать значения параметров Rm, Rz, Rи Sz.
6.Отметить на одной из профилограмм участок с базовой длиной, вычисляемой по формуле
ℓ=LхVh,
где L – базовая длина по ГОСТ 7016-82,
Vh – горизонтальные увеличения профилографа.
7.Для определения параметра Rm провести параллельно общему направлению перемещения ленты линии наибольших выступов и впадин и измерить расстояние между ними. Параметр Rm в микрометрах вычислить по формуле
1000 ,
Rm Vv X
где X – расстояние между линиями выступов и впадин, измеренное линейкой, мм;
Vv – вертикальное увеличение профилографа.
8.Для определения параметра Rz линейкой измерить пять максимальных hmax и пять минимальных hmin отклонений профиля от базовой линии в пределах выбранного участка. Параметр Rz вычислить по формуле
|
|
1 |
5 |
|
5 |
|
R |
|
|
h |
h |
103 , мкм. |
|
z |
|
|
||||
|
|
|||||
|
5Vv |
|
max i |
min i |
|
|
|
|
|
|
|
|
9.Для определения параметра Rвыбранный участок разделить на 10 равных частей, провести вертикальные линии из точек на средней линии до
пересечения с линией профиля и измерить значения yi в мм. Параметр R определить по формуле
R1000 10 yi ,мкм.
10Vv
10.Для определения параметра Sz на выбранном участке профилограммы измерить линейкой шаги неровностей по впадинам Szi в мм.
Параметр Sz вычислить по формуле
|
1 |
n |
|
Sz |
Szi , |
||
|
|||
MVh |
|||
|
1 |
где М – число шагов неровностей.

16
11.Результаты измерений и расчетов занести в табл. 3.1; 3.2; 3.3. 12.Проанализировать результаты и сделать выводы. 13.Написать отчет.
|
|
|
|
|
Таблица 3.1 |
|
Результаты измерений по определению параметра R m max индикаторным |
||||||
глубиномером |
|
|
|
|
|
|
|
|
|
|
|
|
|
Наименование |
Марка инди- |
Цена деле- |
Номер изме- |
Показание |
|
Значение |
образца |
катора |
ния |
рения |
индикатора |
|
параметра |
|
|
|
|
Hmax I, мкм |
|
R m max, мкм |
|
|
|
|
|
|
|
|
|
|
|
|
|
|
|
|
|
|
|
|
|
Таблица 3.2 Результаты измерений по определению параметра шероховатости прибором
МИС 11
Наименование |
Номер |
Показания окулярного |
Разность |
Значение |
Значение |
|
образца |
измерения |
микрометра |
показаний |
параметра |
параметра |
|
|
|
|
|
S |
Hmax i |
R m max |
|
|
Начальное |
Конечное |
|||
|
|
S1i |
S2i |
|
мкм |
мкм |
|
|
|
|
|
|
|
|
|
|
|
|
|
|
|
|
|
|
|
|
|
|
|
|
|
|
|
|
|
|
|
|
|
|
|
Таблица 3.3 Результаты измерений по определению параметров шероховатости с
помощью профилографа-профилометра
Наимено- |
Номер |
Увеличение |
Результаты измерений |
|
Значение параметра, |
|||||||||
вание |
измере- |
профило- |
|
|
|
|
|
|
|
мкм |
|
|
||
образца |
ния |
графа |
|
|
|
|
|
|
|
|
|
|
|
|
|
|
|
|
|
|
|
|
|
|
|
|
|
|
|
|
|
Vh |
Vv |
X |
hmax i |
hmin i |
yi |
|
Sz i |
Rm |
Rz |
|
R |
Sz |
|
|
|
|
|
|
|
|
|
|
|
|
|
|
|
|
|
|
|
|
|
|
|
|
|
|
|
|
|
|
|
|
|
|
|
|
|
|
|
|
|
|
|
|
|
|
|
|
|
|
|
|
|
|
|
|
|
|
|
|
|
|
|
|
|
|
|
|
|
|
|
|
|
|
|
17
Содержание отчета
1.Характеристика параметров шероховатости.
2.Способы контроля шероховатости.
3.Принципы работы приборов для контроля шероховатости.
4.Результаты определения параметров шероховатости.
5.Анализ результатов и выводы.
Лабораторная работа № 4
ОПРЕДЕЛЕНИЕ ТОЧНОСТИ ОБРАБОТКИ ДЕТАЛЕЙ
Цель работы: Практическое ознакомление студентов с методом статистического контроля точности обработки деталей на деревообрабатывающих станках.
Работа проводится группами студентов по 3 человека в каждой. Каждая группа с помощью точного измерительного прибора (микрометра или штангенциркуля) определяет размеры деталей, указанные в задании.
Точность обработки – это степень соответствия обработанной детали ее номинальному размеру и заданной форме. То или иное отклонение от заданного размера или формы является характеристикой погрешностей обработки. Погрешности, которые обычно имеют место при обработке деталей, могут быть систематическими или случайными. Систематические погрешности делятся на два вида:
1.Погрешности, остающиеся постоянными в процессе обработки партии деталей.
2.Погрешности, закономерно изменяющиеся в процессе обработки.
Кпервым относят погрешности обработки, являющиеся следствием геометрических погрешностей станка, инструмента или приспособления.
Ко вторым относятся погрешности, вызванные постепенным износом режущего инструмента в процессе работы, нагревом станка и режущего инструмента.
Случайные погрешности характеризуются рассеиванием размеров деталей в партии. К числу случайных погрешностей могут быть отнесены погрешности, вызываемые неоднородностью материала, неодинаковой величиной припусков, колебанием режимов обработки.

18
При определении результирующей погрешности точности обработки используется статистический метод, основанный на законе больших чисел. Все случайные погрешности подчиняются определенной закономерности. Проблема определения случайных событий разрешена Гауссом, который вывел закон нормального распределения событий.
Этот закон отвечает формуле
|
1 |
|
|
x 2 |
|
|
||
Y |
|
2 2 , |
(4.1) |
|||||
|
|
|
||||||
2 |
||||||||
|
|
|
|
|
|
где – среднеквадратичное отклонение от среднего значения (центр группи-
рования размеров); |
|
|
Y – частота появления погрешности; |
|
|
ℓ – основание натурального логарифма; |
|
|
X – погрешность размера, отсчитываемая от центра группирования. |
|
|
Среднее значение, или центр группирования размеров, |
|
|
Мср |
XZ , |
(4.2) |
|
n |
|
где X – среднее значение интервала;
Z – число замеров заготовок, находящихся в данном интервале; n – количество всех размеров.
Величина М совпадает с центром группирования, около которого, в основном, располагаются значения размеров партии.
Но это среднее арифметическое дает представление о средней точности обработки, но не выражает пределов их колебания.
Поэтому определяется среднеквадратичное отклонение
X |
M |
2 Z |
. |
(4.3) |
n |
1 |
|
||
|
|
|
Знаки ± показывают, что отклонение может быть как в ту, так и в другую сторону от центра группирования М.
При сравнении двух средних арифметических, выраженных в равных единицах, не достаточно знать среднее квадратичное отклонение. Вводится еще понятие коэффициента изменчивости
V |
100 |
, % . |
(4.4) |
|
|||
|
M ср |
|
Полученный результат среднего арифметического М не может точно характеризовать величину данного свойства, так как если мы получим несколько очень больших или очень малых результатов измерения, то они по-

19
влияют на величину М. Вводится еще понятие средней ошибки среднего арифметического, которая позволяет по частному значению арифметического судить об общей его величине
m |
|
|
|
. |
(4.5) |
|
|
|
|||
|
|||||
|
|
n |
|
Среднюю ошибку можно выразить в процентах от среднего арифметического
P |
100m |
, % . |
(4.6) |
|
|||
|
Mср |
|
Это показатель точности. Он характеризует надежность результатов опыта. Показатель точности должен быть меньше 5 %.
Порядок выполнения работы
1.Произвести 50 – 100 замеров, указанных в задании размеров деталей. Полученные результаты записать в табл. 4.1.
|
|
|
|
Таблица 4.1 |
|
Результаты замеров |
|
||
|
|
|
|
|
№ п/п |
Размер детали |
№ п/п |
|
Размер детали |
|
|
|
|
|
1 |
|
6 |
|
|
|
|
|
|
|
2 |
|
7 |
|
|
|
|
|
|
|
3 |
|
8 |
|
|
|
|
|
|
|
4 |
|
9 |
|
|
|
|
|
|
|
5 |
|
и т. д. |
|
|
|
|
|
|
|
2.Из полученных результатов выделить наибольший и наименьший размеры Xmax и Xmin. Разбить все полученные размеры на классы. Число классов должно быть более 6. Определить величину классового промежутка
К |
X max X min |
, |
|
||
|
N |
где N – число классов.
3. Произвести группирование размеров по табл. 4.2.
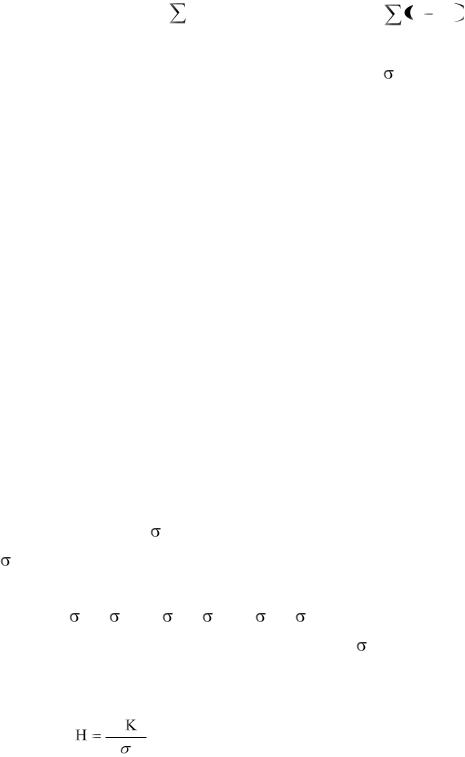
20
|
|
|
|
|
|
|
|
Таблица 4.2 |
|
|
Результаты обработки материалов |
|
|||||
|
|
|
|
|
|
|
|
|
№ клас- |
Граница |
Средний |
Число |
XZ |
X-M |
(X-M)2 |
|
(X-M)2Z |
са |
класса |
размер |
замеров |
|
|
|
|
|
|
|
|
|
|
|
|
|
|
1 |
|
|
|
|
|
|
|
|
|
|
|
|
|
|
|
|
|
2 |
|
|
|
|
|
|
|
|
|
|
|
|
|
|
|
|
|
3 |
|
|
|
|
|
|
|
|
|
|
|
|
|
|
|
|
|
и т.д. |
|
|
|
|
|
|
|
|
|
|
|
|
|
|
|
|
|
|
|
|
n |
XZ |
|
|
|
X M 2 Z |
|
|
|
|
|
|
|
|
|
4. Пользуясь приведенными выше формулами, определить М, |
, и Р. |
5.Построить фактическую кривую распределения. Для этого на оси абсцисс откладывается средний размер каждого класса (Х). На перпендикулярах, восстановленных из точек, соответствующих средним размерам каждого класса, отмечается точками высота, соответствующая частоте повторения размеров данного класса. Нанесенные таким образом точки последовательно соединить отрезками прямых, в результате чего получится ломаная линия. Эта линия называется экспериментальной кривой распределения.
6.Построить кривую нормального распределения, которая характеризуется двумя параметрами: средним размером партии М, определяющим центр группирования размеров, и средним квадратичным отклонением, определяющим величину поля рассеивания. В пределах М ±36 лежат практически 100 % всех размеров. Кривая нормального распределения строится на том же графике, что и экспериментальная кривая.
На оси абсцисс отмечается значение среднего размера М. Вправо и влево от точки М откладывается значение Х.
Х=М±d ,
где d – доля .
Для построения кривой достаточно вычислить значения абсцисс и координат для ±0,5 , ±1 , ±1,5 , ±2 , ±2,5 , ±3 .
Значение Х отмечается на графике как в долях , так и в мм. Наибольшая высота кривой будет в точке М. Она определяется по формуле
0,4 n ,