
3652
.pdf
Министерство образования и науки Российской Федерации Федеральное государственное бюджетное образовательное учреждение высшего образования
«Воронежский государственный лесотехнический университет имени Г.Ф. Морозова»
ИНФРАСТРУКТУРА ЛЕСОПРОМЫШЛЕНННОГО ПРОИЗВОДСТВА
Методические указания к практическим занятиям
для студентов по направлению
35.03.02 - «Технология лесозаготовительных и деревоперерабатывающих производств»
Воронеж 2016
1
УДК 630.36 Бухтояров, Л.Д. Инфраструктура лесопромышленного производства [Электронный ресурс]:
Методические указания к практическим занятиям для студентов по направлению подготовки 35.03.02 - «Технология лесозаготовительных и деревоперерабатывающих производств» / Л.Д. Бухтояров, А.С. Черных, В.В. Абрамов: ВГЛТУ. – Воронеж, 2016 – 38 с.
Печатается по решению учебно-методического совета ФГБОУ ВО «ВГЛТУ» (протокол № 6 от 03.06.2016 г.)
Рецензент: заведующий кафедрой электротехники и автоматики Воронежский ГАУ д-р техн. наук, проф. Д.Н. Афоничев
2
|
ОГЛАВЛЕНИЕ |
|
Введение |
|
4 |
Практическое занятие № 1 Инфраструктура ремонтного хозяйства |
5 |
|
Практическое занятие № 2. Энергетическое хозяйство предприятия |
11 |
|
Практическое занятие № 3. |
Инструментальное хозяйство предприятия |
18 |
Практическое занятие № 4. |
Транспортное хозяйство предприятия |
25 |
Практическое занятие № 5. Складское хозяйство предприятия |
33 |
|
Библиографический список |
37 |
3
Введение
Настоящие методические указания предназначены для студентов обучающихся по направлению 35.03.02 - «Технология лесозаготовительных и деревоперерабатывающих производств» и содержит рекомендации по выполнению практических работ, предусмотренных рабочей программой дисциплины «Инфраструктура лесопромышленного производства».
В результате выполнения работ каждый студент углубляет знания о инфраструктуре ремонтного, энергетического, инструментального, складского и транспортного хозяйств лесозаготовительного предприятия и методах расчета их работы.
Данные методические указания способствуют овладению студентами навыками по использованию экономических знаний при оценке эффективности результатов деятельности предприятия, способностью понимать научные основы технологических процессов в области лесозаготовительных и деревоперерабатывающих производств
4
ПРАКТИЧЕСКОЕ ЗАНЯТИЕ № 1 ИНФРАСТРУКТУРА РЕМОНТНОГО ХОЗЯЙСТВА
(4 часа)
ЦЕЛЬ РАБОТЫ: изучение структуры ремонтного хозяйства лесозаготовительного предприятия, овладение расчетом календарно-плановых нормативов по системе планово-предупредительных ремонтов технологического оборудования.
1. Основные положения и методические указания.
Современные предприятия машиностроения оснащены дорогостоящим и разнообразным оборудованием, установками, роботизированными комплексами, транспортными средствами и другими видами основных фондов. В процессе работы они теряют свои рабочие качества, главным образом из-за износа и разрушения отдельных деталей, поэтому снижают точность, мощность, производительность и другие параметры.
Для компенсации износа и поддержания оборудования в нормальном, работоспособном состоянии требуется систематическое техническое обслуживание его и выполнение ремонтных работ, а также проведениемероприятий по технической диагностике.
Техническим обслуживанием принято называть комплекс операций по поддержанию работоспособности или исправности оборудования при его использовании по назначению, ожидании, хранении и транспортировании.
Ремонтом называется комплекс операций по восстановлению исправности, работоспособности или ресурса оборудования или его составных частей.
Износ оборудования в процессе его эксплуатации и нерациональная организация технического обслуживания и ремонта приводят к увеличению простоя в ремонте, к ухудшению качества обработки и повышению брака, а также к увеличению затрат на ремонт.
О значении улучшения организации содержания и ремонта оборудования можно судить по следующим показателям. Годовые затраты на ремонт и техническое обслуживание оборудования на предприятиях составляют 10-25% его первоначальной стоимости. А их удельный вес в себестоимости продукции достигает 6-8%.
Численность ремонтных рабочих колеблется в пределах 20-30% от общей численности вспомогательных рабочих.
В соответствии с изложенным выше следует отметить, что основными задачами организации планирования ремонтной службы предприятия является:
1)сохранение оборудования в рабочем, технически исправном состоянии, обеспечивающем его высокую производительность и бесперебойную работу;
2)сокращение времени и затрат на обслуживание и все виды ремонтов.
5
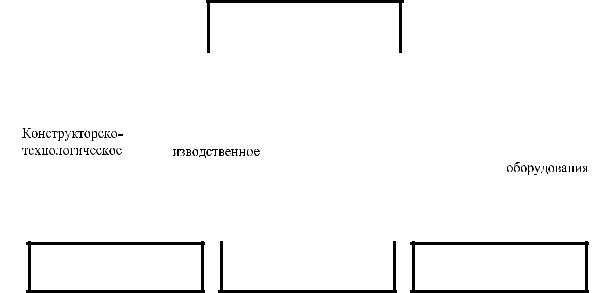
Решение таких задач требует организации правильной эксплуатации, текущего обслуживания, своевременного выполнения необходимого ремонта, а также модернизации оборудования.
Для выполнения всех видов работ по организации рационального обслуживания и ремонта оборудования и других видов основных фондов на предприятиях создаются ремонтные службы. Их структура зависит от ряда факторов – типа и объема производства, его технических характеристик, развития кооперирования при выполнении ремонтных работ, системы централизации и др.
В состав ремонтной службы крупного и среднего предприятия входят отдел главного механика (ОГМ), ремонтно-механический цех (РМЦ), цеховые ремонтные службы, общезаводской склад запасных деталей и узлов (см. рис. 11.1).
Главный механик
(ОГМ)
|
|
|
|
|
|
|
|
|
|
|
|
|
|
|
|
|
|
|
|
|
|
|
|
|
|
|
|
|
|
|
|
|
|
|
|
Планово-про- |
|
|
Бюро планово- |
|
Группа |
||||||
|
|
|
|
|
|
|
|
|
предупредите- |
|
кранового |
||||
|
бюро |
|
бюро |
|
|
льного ремонта |
|
|
|
|
|||||
|
|
|
|
|
|
|
|
|
|
|
|
|
|
|
|
|
|
|
|
|
|
|
|
|
|
|
|
|
|
|
|
|
|
|
|
|
|
|
|
|
|
|
|
|
|
|
|
|
|
|
|
|
|
|
|
|
|
|
|
|
|
|
|
|
|
|
|
|
|
|
|
|
|
|
|
|
|
|
|
Цеховые ремонтные |
Ремонтномехани- |
Склад запасных |
службы |
ческий цех |
частей |
Рис. 1. Структура ремонтной службы предприятия
Возглавляет ОГМ главный механик, подчиненный непосредственно главному инженеру завода.
Всоставе ОГМ, как правило, создаются следующие функциональные подразделения: бюро планово-предупредительного ремонта (ППР), конструкторскотехнологическое бюро, планово-производственное бюро и группа кранового оборудования.
Всостав бюро ППР входят группы: инспекторская, учета оборудования, запасных частей и ремонтно-смазочного хозяйства.
Инспекторская группа планирует, контролирует и учитывает выполнение всех видов ремонтных работ; инспектирует правильность эксплуатации и разрабатывает инструкции по уходу за оборудованием.
Группа учета оборудования ведет паспортизацию и учет всех видов оборудования, следит за его перемещением, контролирует состояние хранения и качества консервации не установленного оборудования, проводит
6
ежегодную инвентаризацию.
Группа запасных частей устанавливает номенклатуру, сроки службы, нормы расхода и лимиты на запасные детали и покупные материалы, планирует изготовление запасных частей и руководит складскими запасами деталей.
Группа ремонтно-смазочного хозяйства контролирует выполнение графика смазки оборудования; устанавливает лимиты на обтирочносмазочные материалы и на сбор отработанного масла и его регенерацию.
Планово-производственное бюро планирует и контролирует работу ремонтно-механического цеха и цеховых ремонтных службы, осуществляет материальную подготовку ремонтных работ, составляет отчеты по выполнению планов ремонтных работ по заводу, производит анализ техникоэкономических показателей ремонтной службы завода, выявляет непроизводительные затраты, разрабатывает мероприятия по их устранению.
Конструкторско-технологическое бюро осуществляет всю техническую подготовку системы ППР и всех видов ремонтных работ, включая модернизацию; обеспечивает комплектование альбомов чертежей и их хранение по всем видам оборудования.
Группа кранового оборудования следит за эксплуатацией и состоянием всех подъемно-транспортных механизмов, планирует и контролирует выполнение всех видов ремонтов.
Ремонтно-механический цех является основной материальной базой ремонтной службы предприятия. Комплектуется разнообразным универсальным оборудованием и высококвалифицированными рабочими. Выполняет все наиболее сложные работы по ремонту оборудования, изготовлению и восстановлению сменных деталей. Выполняет работы по модернизации оборудования.
Цеховые ремонтные службы создаются в крупных основных цехах завода только при использовании децентрализованной и смешенной системы организации ремонтных работ. Службы находятся в ведении механиков цехов.
Общезаводской склад запасных деталей и узлов осуществляет хранение и учет всех материальных ценностей необходимых для проведения всех видов ремонтов оборудования и подъемно-транспортных средств.
Штаты ИТР и служащих ремонтной службы предприятия устанавливаются в зависимости от числа ремонтных единиц оборудования в целом по заводу.
2 Расчет трудоемкости ремонтных работы и численности ремонтных рабочих
Эффективность применения системы ППР находится в прямой зависимости от совершенства нормативной базы, соответствия нормативов условиям эксплуатации оборудования. От точности нормативов в большой степени зависят размеры расходов предприятия на техническое
7

обслуживание, ремонт оборудования, уровень потерь в производстве, связанных с неисправностью оборудования. Нормативы дифференцируются по группам оборудования и содержат последовательность проведения ремонтов и осмотров, объемы ремонтных работ, их трудоемкость и материалоемкость. Важнейшими нормативами системы ППР являются: 1) длительность межремонтного цикла; 2) Структура межремонтного цикла; 3) Длительность межремонтного и межосмотрового периода; 4) Категория сложности ремонта; 5) Нормативы трудоемкости; 6) Нормативы материалоемкости; 7) Нормы запаса деталей и оборотных узлов и агрегатов.
Под длительностью межремонтного цикла понимается период времени работы оборудования от момента ввода его в эксплуатацию до первого капитального ремонта или период времени между двумя последовательно выполняемыми капитальными ремонтами. Для легких и средних металлорежущих станков длительность межремонтного цикла (ТмB .ц.)B определяется по формуле:
где 24000 – нормативный ремонтный цикл, станко-ч;
коэффициент, учитывающий тип производства (для массового и
п
крупносерийного он равен 1.0, для серийного - 1.3, мелкосерийного и единичного
– 1.5);
коэффициент, учитывающий род обрабатываемого материала (при
м
обработке конструкционных сталей он равен 1.0, чугуна и бронзы –
0.8,
высокопрочных сталей – 0.7);у коэффициент, учитывающий условия эксплуатации оборудования
(при нормальных условиях механических цехов он равен 1.0, в запыленных и влажных помещениях – 0.7);
коэффициент, отражающий группу станков (для легких и средних
т
равен 1.0).
Под структурой межремонтного цикла понимается перечень и последовательность выполнения ремонтных работ и работ по техническому обслуживанию в период длительности межремонтного цикла. Например, для средних и легких металлорежущих станков:
К1 О1 Т1 О2 Т 2 О3 С1 О4 Т 3 О5 Т 4 О6 К 2
где К1B ,B К2B B – капитальный ремонт оборудования; Т1B ,B Т2B ,B Т3B ,B Т4B B – текущие малые ремонты оборудования; С1B B – средний ремонт оборудования; О1B ,B ОB2,B О3B ,B О4B B,B ОB 5B ,B О6B B – осмотр (техническое обслуживание).
Из структуры межремонтного цикла видно, сколько и в какой последовательности проводится тот или иной вид ремонта и осмотра.
Межремонтный период – период работы единицы оборудования между двумя очередными плановыми ремонтами. Например, период времени между К1B B и Т1B B или Т1B B и Т2B ,B или Т2B B и СB1.B Определяется длительность межремонтного периода (tмрB )B по формуле:
8
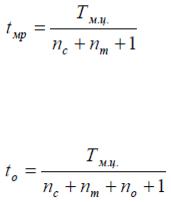
где ncB ,B nmB B – число средних и текущих ремонтов.
Межосмотровый период – период работы оборудования между двумя очередными осмотрами и плановыми ремонтами, расчет ведется по формуле:
где nоB B – число осмотров или другими словами число раз технического обслуживания на протяжении длительности межремонтного цикла.
Под категорией сложности ремонта понимается степень сложности ремонта оборудования и его особенности. Чем сложнее оборудование, чем больше его размер и выше точность обработки на нем, тем выше сложность ремонта, а следовательно, тем выше категория сложности.
Обозначается категория сложности ремонта буквой R и числовым коэффициентом перед ней. В качестве эталона для определенной группы металлорежущих станков, принят токарно-винторезный станок 1К62 с высотой центров 200мм и расстоянием между центрами 1000мм. Для этого станка установлена категория сложности по технической части 11R, а по электрической – 8,5R. Категорию сложности любого другого станка данной группы оборудования устанавливают путем сопоставления его с эталоном. Трудоемкость того или иного вида ремонтных работ определяется исходя из количества единиц ремонтной сложности и норм времени, установленных на одну ремонтную единицу. Количество единиц ремонтной сложности по механической части оборудования совпадает с категорией сложности. Следовательно, станок 1К62 имеет 11 ремонтных единиц по механической части, по электрической части установлено 8.5
ремонтных единиц.
Нормы времени устанавливаются на одну ремонтную единицу по видам ремонтных работ отдельно на слесарные, станочные и прочие работы (см. табл. 1).
|
|
|
|
|
Таблица 1 |
Нормы времени на ремонтную единицу для технического |
|||||
|
и подъемно-транспортного оборудования |
|
|||
Осмотр и |
Слесарные |
Станочные |
|
Прочие |
Всего, |
виды ремонта |
работы, |
работы, |
|
работы, |
нормо-ч. |
|
нормо-ч. |
нормо-ч. |
|
нормо-ч. |
|
|
|
|
|
|
|
О |
0.75 |
0.1 |
- |
|
0.85 |
Т |
4.00 |
2.0 |
0.1 |
|
6.10 |
С |
16.00 |
7.0 |
0.5 |
|
23.50 |
К |
23.00 |
10.0 |
2.0 |
|
35.00 |
Суммарная трудоемкость по отдельному виду ремонтных работ определяется по формуле:
9
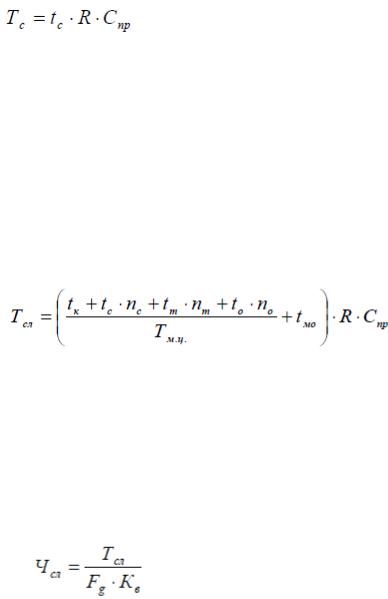
где ТсB B – трудоемкость среднего ремонта оборудования данной группы, нормо- ч; tсB B норма времени на одну ремонтную единицу по всем видам работ, нормо-ч;
R количество ремонтных единиц;
СпрB B количество единиц оборудования данной группы, шт.
Аналогично трудоемкость определяется по техническому обслуживанию, текущему и капитальному ремонтам.
Интерес представляет определение трудоемкости по видам работ (слесарным, станочным, прочим), так как результаты расчета позволяют определить численность ремонтных рабочих соответствующей профессии (слесарей, станочников т.д.). Расчет трудоемкости производится по формуле:
где tкB ,B tcB ,B tтB ,B tоB B - нормы времени на одну ремонтную единицу слесарных работ по капитальному, среднему и текущему ремонтам и техническому обслуживанию, нормо-ч.;
tмоB B - норма времени на одну ремонтную единицу по межремонтному обслуживанию за год, нормо-ч.
Расчет численности |
ремонтных рабочих |
(например, |
слесарных) производится по формуле:
где FgB B - годовой эффективный фонд времени работы одного ремонтного рабочего, ч.;
КвB B - коэффициент выполнения норм времени.
Материалоемкость на все виды ремонтов и техническое обслуживание определяется исходя из норм расхода материалов, установленных на единицу ремонтной сложности и количества единиц ремонтной сложности данной группы оборудования.
Нормы запаса деталей и оборотных узлов и агрегатов определяется аналогично потребности в материалах, исходя из количества единиц ремонтной сложности.
3.Контрольные вопросы
1.Значение, задачи и структура ремонтной службы предприятия.
2.Сущность и содержание системы ППР.
3.Ремонтные нормативы системы ППР и методика их расчета.
10