
3411
.pdf11
2.Образцы из дубовой, березовой и сосновой древесины в форме кубика со стороной 50 мм.
3.Шурупы диаметром 4 мм, длиной 60 мм.
4.Штангенциркуль с погрешностью измерения не более 0,1 мм; аналитические весы; электродрель; сверла диаметром 2; 2,5; 3 и 3,5 мм; отвертка; испытательная машина МР-05; приспособление для выдергивания шурупов по ГОСТ 10637 – 78.
Подготовка образцов к испытанию
Спомощью электродрели или сверлильного станка в образцах высверливаются отверстия в соответствии со схемой, изображенной на рис. 2.1. Диаметр отверстия под шуруп должен быть равным 2 мм для пород плотностью, меньшей 600 кг/м3, 3 мм – для пород плотностью 600…700 кг/м3 и 3,5 мм –для пород плотностью более 700 кг/м3. Глубина сверления должна быть равной 16±1 мм. Диаметр отверстия в образцах из ДСтП и МДФ должен быть равен 2,5 мм. Шурупы ввинчиваются отверткой на длину нарезной части шурупа, а при завинчивании в пласть ДСтП и МДФ на толщину плиты.
Проведение испытаний Образцы устанавливают в захваты приспособления на испыта-
тельной машине так, чтобы ось шурупа совпадала с осью приспособления (рис. 2.2). Выдергивание шурупа производят в направлении их оси со скоростью перемещения подвижного захвата испытательной машины 10 мм/мин.
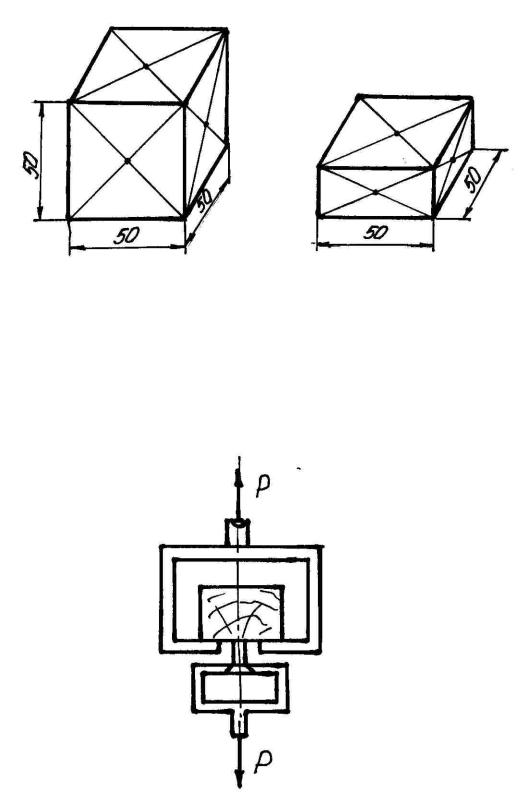
12
а) |
б) |
Рис. 2.1 Образцы для испытаний: а – образец из массивной древесины; б – образец из ДСтП и МДФ
Рис. 2.2 Схема испытаний Порядок выполнения работы
1.Ознакомиться с методическими указаниями, установкой и приспособлениями для испытаний.
13
2.Измерить образцы и определить плотность материала.
3.Подготовить образцы для испытания.
4.Провести испытания.
5.Вычислить удельное сопротивление выдергиванию шурупов и занести результаты в табл. 2.1.
6.Построить график зависимости удельного сопротивления выдергиванию шурупов от плотности материала.
7.Проанализировать полученные результаты и сделать выводы.
8.Написать отчет.
Содержание отчета
1.Общая характеристика способа соединения деталей на шурупах.
2.Методика испытаний.
3.Результаты испытаний.
4.Графики зависимости удельного сопротивления выдергивания шурупов от плотности материала.
5.Анализ результатов и выводы.
Таблица 2.1
Результаты испытаний
№ |
Материал образца |
Размеры образца , мм |
Масса |
Плот- |
L, |
Рmax, |
gш, |
||
обр. |
и направление за- |
длина |
шири- |
тол- |
образца, |
ность, |
мм |
Н |
Н/мм |
|
винчивания |
|
на |
щина |
г |
кг/м3 |
|
|
|
|
|
|
|
|
|
|
|
|
|
1 |
2 |
3 |
4 |
5 |
6 |
7 |
8 |
9 |
10 |
|
|
|
|
|
|
|
|
|
|
1 |
Дуб |
|
|
|
|
|
|
|
|
|
Рациональное |
|
|
|
|
|
|
|
|
|
Тангенциальное |
|
|
|
|
|
|
|
|
|
Торец |
|
|
|
|
|
|
|
|
|
|
|
|
|
|
|
|
|
|
2 |
Береза |
|
|
|
|
|
|
|
|
|
Рациональное |
|
|
|
|
|
|
|
|
|
Тангенциальное |
|
|
|
|
|
|
|
|
|
Торец |
|
|
|
|
|
|
|
|
|
|
|
|
|
|
|
|
|
|
14
Окончание табл. 2.1
1 |
2 |
3 |
4 |
5 |
6 |
7 |
8 |
9 |
10 |
|
|
|
|
|
|
|
|
|
|
3 |
Сосна |
|
|
|
|
|
|
|
|
|
Рациональное |
|
|
|
|
|
|
|
|
|
Тангенциальное |
|
|
|
|
|
|
|
|
|
Торец |
|
|
|
|
|
|
|
|
|
|
|
|
|
|
|
|
|
|
4 |
ДСтП |
|
|
|
|
|
|
|
|
|
Пласть |
|
|
|
|
|
|
|
|
|
Кромка |
|
|
|
|
|
|
|
|
|
|
|
|
|
|
|
|
|
|
5 |
МДФ |
|
|
|
|
|
|
|
|
|
Пласть |
|
|
|
|
|
|
|
|
|
Кромка |
|
|
|
|
|
|
|
|
|
|
|
|
|
|
|
|
|
|
Лабораторная работа №3
КОНТРОЛЬ ШЕРОХОВАТОСТИ ПОВЕРХНОСТИ
Цель работы: изучить влияние характера обработки поверхностей деталей из древесины и древесных материалов на шероховатость поверхности.
Общие сведения: Для оценки шероховатости поверхности древесины и древесных материалов применяют параметры: Rm max, Rm, Rz, R и Sz.
Параметр Rm max представляет собой среднее арифметическое из наибольших по высоте неровностей Hmax , найденных выборочно на контролируемой поверхности
|
|
1 |
n |
|
|
Rm max |
= |
∑Hmax i , |
(3.1) |
||
|
|||||
|
|
n i=1 |
|
где Hmax I - расстояние от высшей до низшей точки i-той неровности, мкм; n – число измерений.
Параметр Rm представляет собой наибольшую высоту неровностей профиля, вычисляемую по формуле
|
|
1 |
|
5 |
5 |
|
|
|
Rz |
= |
|
|
∑hmax i |
− ∑hmini , |
(3.3) |
||
5 |
||||||||
|
|
i=1 |
i=1 |
|
|
где hmax I ; hmin I - расстояние от пяти наивысших и пяти наинизших точек профиля до линии отсчета, проведенной параллельно средней линии и не пересекающей профиль.
Параметр R представляет собой среднее арифметическое отклонений профиля от его средней линии в пределах базовой длины ℓ и может быть определен путем измерения и последующего суммирования ряда ординат yi в
пределах базовой длины (рис. 3.1)
|
1 |
n |
|
|||||
Rα = |
∑ |
|
yi |
|
, |
(3.4.) |
||
|
|
|||||||
|
||||||||
|
n i=1 |
|
|
|
|
|
где n – число ординат yi.
Параметр Sz характеризует шаг неровностей, определяемый по впадинам профиля (рис. 3.1),
|
|
1 |
n |
|
|
Sz |
= |
∑Szi , |
(3.5) |
||
|
|||||
|
|
n i=1 |
|
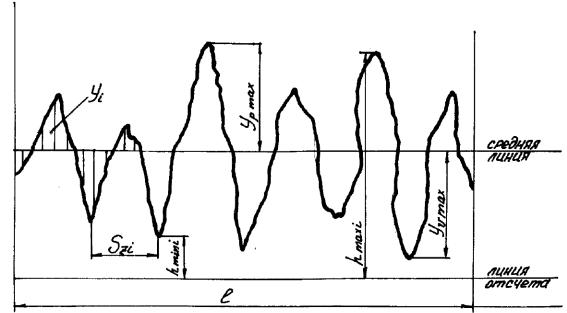
16
Рис. 3.1 Схематическое изображение профиля поверхности Согласно ГОСТ 7016-82 базовая длина выбирается в зависимости от
качества обработки поверхностей из следующих значений: 0,8; 2,5; 8 и 25 мм. Для контроля шероховатости поверхности древесины и древесных материалов принимаются индикаторные глубиномеры, допускающие выборочное измерение отдельных неровностей, оптические приборы МИС-11 и ТСП-
4, профилографы и профилометры.
Контроль шероховатости в производственных условиях может осуществляться путем визуального сравнения с эталонами.
Материалы, оборудование, приборы
1.Образцы из сосновой древесины, обработанные пилением, фрезерованием и шлифованием; образцы из ДСтП и МДФ, обработанные шлифованием. Шлифовальная шкурка различной зернистости.
2.Индикаторный глубиномер, микроскоп МИС-11, профилограф-
профилометр.
Порядок выполнения работы
1.Ознакомиться с методическими указаниями.
2.Ознакомиться с принципом действия измерительных приборов.
3.Подготовить образцы для измерений.

17
4.Провести измерения грубых неровностей с помощью индикаторного глубиномера.
5.Снять профилограммы поверхностей с помощью профилографапрофилометра и зафиксировать значения параметров Rm, Rz, R и Sz.
6.Отметить на одной из профилограмм участок с базовой длиной, вычисляемой по формуле
ℓ=LхVh,
где L –базовая длина по ГОСТ 7016-82,
Vh – горизонтальные увеличения профилографа.
7.Для определения параметра Rm провести параллельно общему направлению перемещения ленты линии наибольших выступов и впадин и измерить расстояние между ними. Параметр Rm в микрометрах вычислить по формуле
Rm = 1000 X ,
Vv
где X – расстояние между линиями выступов и впадин, измеренное
линейкой, мм;
Vv – вертикальное увеличение профилографа.
8.Для определения параметра Rz линейкой измерить пять максимальных hmax и пять минимальных hmin отклонений профиля от базовой линии в пределах выбранного участка. Параметр Rz вычислить по формуле
|
|
1 |
|
5 |
5 |
|
Rz |
= |
|
|
∑hmax i |
− ∑hmin i 103 , мкм. |
|
|
||||||
|
|
5Vv |
|
|
|
9.Для определения параметра R выбранный участок разделить на 10 равных частей, провести вертикальные линии из точек на средней линии до пересечения с линией профиля и измерить значения yi в мм. Параметр R
определить по формуле
|
1000 |
10 |
|
Rα = |
∑yi ,мкм. |
||
|
18
10.Для определения параметра Sz на выбранном участке профилограммы измерить линейкой шаги неровностей по впадинам Szi в мм.
Параметр Sz вычислить по формуле
|
|
1 |
n |
|
Sz |
= |
∑Szi , |
||
MV |
||||
|
|
1 |
||
|
|
h |
где М – число шагов неровностей.
11.Результаты измерений и расчетов занести в табл. 3.1; 3.2; 3.3. 12.Проанализировать результаты и сделать выводы. 13.Написать отчет.
Содержание отчета
1.Характеристика параметров шероховатости.
2.Способы контроля шероховатости.
3.Принципы работы приборов для контроля шероховатости.
4.Результаты определения параметров шероховатости.
5.Анализ результатов и выводы.
|
|
|
|
|
Таблица 3.1 |
|
Результаты измерений по определению параметра |
|
|||
|
Rm max индикаторным глубиномером |
|
|||
|
|
|
|
|
|
Наименование |
Марка инди- |
Цена деле- |
Номер изме- |
Показание |
Значение |
образца |
катора |
ния |
рения |
индикатора |
параметра |
|
|
|
|
Hmax I, мкм |
R m max, мкм |
|
|
|
|
|
|
|
|
|
|
|
|
|
|
|
|
|
|
|
|
|
|
|
|
|
|
|
|
|
|
19
Таблица 3.2
Результаты измерений по определению параметра
шероховатости прибором МИС – 11
Наименование |
Номер |
Показания окулярного |
Разность |
Значение |
Значение |
|
образца |
измере- |
микрометра |
показаний |
параметра |
параметра |
|
|
ния |
|
|
S |
Hmax i |
R m max |
|
Начальное |
Конечное |
||||
|
|
S1i |
S2i |
|
мкм |
мкм |
|
|
|
|
|
|
|
|
|
|
|
|
|
|
|
|
|
|
|
|
|
|
|
|
|
|
|
|
|
|
|
|
|
|
|
Таблица 3.3
Результаты измерений по определению параметров шероховатости
с помощью профилографа-профилометра
Наимено- |
Номер |
Увеличение |
Результаты измерений |
|
Значение параметра, |
|||||||||
вание |
измере- |
профило- |
|
|
|
|
|
|
|
мкм |
|
|
||
образца |
ния |
графа |
|
|
|
|
|
|
|
|
|
|
|
|
|
|
|
|
|
|
|
|
|
|
|
|
|
|
|
|
|
Vh |
Vv |
X |
hmax i |
hmin i |
yi |
|
Sz i |
Rm |
Rz |
|
R |
Sz |
|
|
|
|
|
|
|
|
|
|
|
|
|
|
|
|
|
|
|
|
|
|
|
|
|
|
|
|
|
|
|
|
|
|
|
|
|
|
|
|
|
|
|
|
|
|
|
|
|
|
|
|
|
|
|
|
|
|
|
|
|
|
|
|
|
|
|
|
|
|
|
|
|
|
|
20
Лабораторная работа № 4
ОПРЕДЕЛЕНИЕ ТОЧНОСТИ ОБРАБОТКИ ДЕТАЛЕЙ
Цель работы: Практическое ознакомление студентов с методом статистического контроля точности обработки деталей на деревообрабатывающих станках.
Работа проводится группами студентов по 3 человека в каждой. Каждая группа с помощью точного измерительного прибора (микрометра или штангенциркуля) определяет размеры деталей, указанные в задании.
Точность обработки - это степень соответствия обработанной детали ее номинальному размеру и заданной форме. То или иное отклонение от заданного размера или формы является характеристикой погрешностей обработки. Погрешности, которые обычно имеют место при обработке деталей, могут быть систематическими или случайными. Систематические погрешности делятся на два вида:
1.Погрешности, остающиеся постоянными в процессе обработки партии деталей.
2.Погрешности, закономерно изменяющиеся в процессе обработки.
Кпервым относят погрешности обработки, являющиеся следствием геометрических погрешностей станка, инструмента или приспособления.
Ко вторым относятся погрешности, вызванные постепенным износом режущего инструмента в процессе работы, нагревом станка и режущего инструмента.
Случайные погрешности характеризуются рассеиванием размеров деталей в партии. К числу случайных погрешностей могут быть отнесены погрешности, вызываемые неоднородностью материала, неодинаковой величиной припусков, колебанием режимов обработки.
При определении результирующей погрешности точности обработки используется статистический метод, основанный на законе больших чисел. Все случайные погрешности подчиняются определенной закономерности.