
1822
.pdf11
Содержание. Включает наименование всех разделов, подразделов с указанием номера страницы, на которой размещается начало раздела или подраздела.
Введение. Должно содержать краткую оценку современного состояния отрасли, Основные проблемы развития отрасли в целом и подотрасли (к которой относится реконструируемый цех) в частности. Должна быть приведена цель и пути достижения ее, принятые в проекте.
5. СОДЕРЖАНИЕ ГЛАВ ПОЯСНИТЕЛЬНОЙ ЗАПИСКИ
При реконструкции (все разделы) и проектировании цехов
(разделы 1.1 и 1.2)
1. ХАРАКТЕРИСТИКА ПРЕДПРИЯТИЯ И ЦЕХА
Раздел выполняется в период прохождения дипломником преддипломной практики.
1.1. Расположение и состав предприятия
Расположение и состав предприятия по отношению к жилой застройке, железнодорожным, автомобильным и водным магистралям, промышленным предприятиям. Здесь же приводится и состав предприятия: основные
ивспомогательные цеха, склады, сооружения и т.п.
1.2. Источники снабжения (сырьем, основными и вспомогательными мате-
риалами, рабочей силой)
Дается краткая характеристика сырья, основных и вспомогательных материалов и источники снабжения ими предприятия. Приводится краткая характеристика источников снабжения водой, паром, электроэнергией, сжатым воздухом (годовой расход предприятием воды, производительность артезианских скважин, тип и производительность котлов, годовое потребление
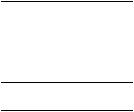
12
пара, давление пара, мощность трансформаторной подстанции, напряжение, годовое потребление электроэнергии силовой и осветительной нагрузками, тип и производительность компрессоров, давление воздуха в сети. Дается анализ обеспеченности реконструируемого цеха рабочей силой.
1.3 Характеристика здания реконструируемого объекта
Необходимо кратко описать конструкцию здания реконструируемого объекта (тип фундамента, несущих элементов, перекрытий, кровли и т.п.), дать оценку физическому состоянию, соответствие степени огнестойкости, указать площадь производственных и бытовых помещений, высоту и объем этих помещений. Делается вывод о соответствии здания строительным нормам и правилам.
1.4.Характеристика и качество выпускаемой цехом продукции
Результаты заносятся в табл. 1.
|
|
|
|
|
|
|
|
Таблица 1 |
|
|
.Характеристика и качество продукции |
|
|
|
|||||
|
|
|
|
|
|
|
|
|
|
|
|
|
|
|
Значение показателя |
|
|
||
№ |
Наименова- |
Ед. |
|
|
по |
данным |
|
||
|
по техниче- |
|
|||||||
п/п |
ние продукции |
изм. |
|
ским |
требо- |
предприятия |
|
Выводы |
|
|
|
|
|
ваниям |
|
|
|
|
|
|
|
|
|
|
|
|
5 |
|
|
1 |
2 |
|
3 |
|
4 |
|
|
6 |
|
|
|
|
|
|
|
|
|
|
|
В выводах указывается степень соответствия выпускаемой продукции требованиям ГОСТа, ТУ и т.п.
Кроме того, в этом подразделе дается анализ технологичности (трудоемкости, материалоемкости) продукции. Результаты технологичности продукции сравниваются с аналогичными показателями передовых предприятий отрасли.
1.5. Состояние технологической дисциплины Характеризуется соблюдением технологических режимов, организацией
подготовки инструмента, наличием на рабочих местах инструкций, журналов наблюдений за параметрами режима и т.д.
1.6. Анализ технико-экономических показателей цеха и предприятия
13
Производится путем сравнения практических данных предприятия с плановыми показателями этого же предприятия и с показателями ведущих предприятий родственного профиля или же подотрасли (отрасли) в целом.
1.7. Состояние безопасности жизнедеятельности (выполняется по методическим указаниям кафедры БЖД)
2. ОБОСНОВАНИЕ ТЕХНИЧЕСКИХ РЕШЕНИЙ И НАПРАВЛЕНИЙ РЕКОНСТРУКЦИИ
При реконструкции цехов
2.1. Анализ «узких» мест.
Под «узким» местом понимается место, где:
-существующие технологические параметры не соответствуют требуемым (по нормативно-технологической документации);
-установлено морально (или физически) устаревшее технологическое оборудование;
-существуют несовершенные технологические приемы.
2.1.1.Анализ соответствия существующих технологических параметров
требуемым.
Дипломник должен дать анализ по каждому технологическому участку степень соответствия технологических параметров требуемым. В анализе должно быть освещено: фактическая периодичность контроля параметра и его значение, допускаемая погрешность измерений, а также соответствие их требуемым. Анализ может быть произведен как в табличной, так и в описательной формах.
В результате анализа должны быть вскрыты причины несоответствия и даны рекомендации по устранению недостатков.
2.1.2. Анализ соответствия технологического оборудования и приемов требуемым
В данном разделе дипломник должен дать анализ степени соответствия оборудования и технологических приемов на каждом технологическом участке требуемым. Под требуемыми понимается новое, совершенное, серийно выпус-
14
каемое промышленностью оборудование или существующие на предприятиях отрасли передовые технологические приемы.
При анализе технологических режимов, приемов дипломник должен руководствоваться материалами не только учебной литературы, но и информацией журналов, брошюр и т.п. по специальности.
2.2.Вывод о целесообразности реконструкции и постановка задачи производится на основе рассмотренной характеристики реконструируемого объекта и выявления «узких мест». Здесь дается оценка, насколько данный объект соответствует современному уровню по всем рассмотренным показателям, делается вывод о необходимости реконструкции и одновременно ставятся задачи, которые необходимо решить в процессе реконструкции.
2.3.Обоснование предлагаемых проектных решений производится на основе поставленных в задании на реконструкцию задач, результатов характеристики реконструируемого объекта и выявления «узких мест». Дается основание по выбору того или иного варианта реконструкции.
При разработке проекта может быть принята многовариантность
предлагаемых решений. Наиболее целесообразный вариант подтверждается необходимыми расчетами.
При проектировании цехов
2. ОБОСНОВАНИЕ ТЕХНИЧЕСКИХ РЕШЕНИЙ И НАПРАВЛЕНИЙ ПРОЕКТИРОВАНИЯ
2.1.Вывод о целесообразности проектирования и постановка задачи производится на основе задания на проектирование, рассмотренной характеристики проектируемого объекта. Здесь делается вывод о необходимости проектирования и одновременно ставятся задачи, которые необходимо решить в процессе проектирования.
2.2.Обоснование предлагаемых проектных решений производится на основе поставленных в задании на проектирование задач, результатов характеристики проектируемого объекта. Дается основание по выбору того или иного варианта проектирования.
При разработке проекта может быть принята многовариантность предлагаемых решений. Наиболее целесообразный вариант подтверждается необходимыми расчетами.
15
3. ТЕХНОЛОГИЧЕСКАЯ ЧАСТЬ Выполняется при реконструкции и проектировании цехов
3.1. Характеристика выпускаемой продукции и ее соответствие техническим требованиям.
Производится с освещением номенклатуры, области применения и соответствия продукции техническим требованиям (по форме табл. 2).
|
|
|
|
|
|
Таблица 2 |
|
Соответствие продукции техническим требованиям |
|
||||
|
|
|
|
|
|
|
|
|
|
|
Значение показателя |
|
|
№ |
Показатель |
Ед. изм. |
|
|
Выводы |
|
по техниче- |
Фактическое |
|||||
п/п |
|
|
ским |
требо- |
значение |
|
|
|
|
ваниям |
|
|
|
|
|
|
|
|
|
|
1 |
2 |
3 |
|
4 |
5 |
6 |
|
|
|
|
|
|
|
Кроме этого дается экономическая оценка, перспективность выпуска продукции. При производстве фанеры различных марок целесообразно выбрать из них 2-3 наиболее перспективных.
3.2. Характеристика применяемого сырья и материалов.
Дается характеристика сырья, основных вспомогательных материалов, заложенных в технологический процесс производства продукции. При освещении этого раздела базовыми показателями сырья и материалов являются показатели, заложенные в ГОСТ, ТУ и т.п. на это сырье и материалы.
3.3. Установление календарного режима работы цеха или участка. Режим работы определяется после установления продолжительно-
сти смены, количества смен в сутки, количества рабочих дней с учетом праздничных и выходных дней, дней на капитальный и профилактический ремонт. После этого определяется эффективный фонд работы цеха или участка.
3.4. Разработка технологической схемы производства продукции, выбор технологического оборудования и описание технологического процесса. Разработка технологической схемы осуществляется после ознакомления с
нормативно-технологическими материалами на вид продукции, проработки литературы, патентного поиска.
Общая схема технологического процесса разрабатывается в соответствии с видом покрытий, установленных в техническом описании изделия. Составлению
16
схемы предшествует разработка технологических карт на каждый вид покрытия. В технологическую карту вносят операции, применяемые в каждой операции основные и вспомогательные материалы, основное технологическое оборудование, режимы выполнения операций.
Пример технологической карты приведен в [6].
Выбор оборудования следует производить, прежде всего, исходя из его технической характеристики, которая приведена в различной справочной литературе [1]. Но при этом следует иметь в виду, что в ходе проектирования может возникнуть необходимость выбора другого оборудования. Это становится ясным после выполнения расчетов загрузки оборудования. Причинами такого изменения могут быть низкая загрузка, недостаток производственной площади, недостаточная обеспеченность электроэнергией и др.
При выборе оборудования следует ориентироваться на применение отделочных линий с высокоэффективными методами отверждения покрытий. Однако это может показаться нерациональным в случае небольшой производственной программы. В случае необходимости студент может предусмотреть в проекте нетиповую линию. Тогда она может быть скомпонована из отдельных типовых устройств, но с обязательным расчетом основных параметров этой линии (скорости, размеров сушильных устройств и т.п.). Такой агрегатный метод построения линий очень важен, т.к. появление новых отделочных материалов ведет к изменению технологического процесса и, естественно, к изменению состава линии.
Описание технологического процесса производится в соответствии с принятой в проекте технологической схемой изготовления продукции, выбором материалов, оборудования и режимов на каждом технологическом участке. Подробные сведения о технологических процессах и режимах отделки различных изделий приведены в [1, 6].
Характеристику отечественного оборудования, на которое имеются данные в литературе, приводить в описании не следует. На зарубежное оборудование необходимо дать краткую характеристику по основным ее параметрам.
3.5. Расчет производительности, количества и коэффициента загрузки оборудования. Корректировка производственной программы.
17
Выбор формул для расчета производительности оборудования производится из соответствующей литературы. Для отдельных видов оборудования, при отсутствии на них расчетных формул, производительность необходимо принимать по паспортным данным. При этом расчетную производительность такого оборудования необходимо принимать как среднее значение между максимальным и минимальным значениями по паспорту. При расчете производительности необходимо стремиться к получению коэффициента загрузки оборудования, близкого к 1. Максимально допустимым является коэффициент загрузки, равный 1,2. Расчет производительности следует начинать с основного оборудования.
При отделке пневматическим или безвоздушным распылением решетчатой мебели (стульев, кресел), изделий в собранном виде (футляров телевизоров), брусковых деталей, кромок щитов производительность распылителя:
П = |
|
Тсмzk0 |
, шт/см |
(1) |
|
|
60Sk |
|
|||
|
|
|
|
|
|
|
|
|
|||
|
|
Q |
+tk m |
|
|
|
|
|
|
|
где Тсм - время смены, мин;
z - количества одновременно отделываемых деталей, шт. (z=1); k0 - коэффициент рабочего времени (k0 = 0,6 – 0,7);
S - площадь отделываемой детали, м2;
K - коэффициент, учитывающий форму отделываемого изделия (см. табл. 3);
Q - условная производительность распылителя, м2/ч (зависит от типа распылителя, см. табл. 4);
tк - дополнительные затраты времени на одно нанесение материала (см. табл. 5);
m - количество нанесения материалов распылением по техпроцессу. Таблица 3
Значение коэффициента k
№ |
Форма отделываемой поверхности |
K |
п/п |
|
|
|
|
|
1 |
2 |
3 |
|
|
|
1 |
Каркасы стульев, кресел |
3-5 |
|
|
|
2 |
Корпусные изделия, щитовые детали, |
1,1-1,2 |
|
кромки щитов (в стопах) |
|
|
|
|

18
|
|
|
|
|
Таблица 4 |
|
|
Условная производительность распылителей |
|
|
|||
|
|
|
|
|
|
|
Тип распы- |
КР-20 |
ЗИЛ |
КРУ-1 |
|
О-45 |
|
лителя |
|
|
|
|
|
|
|
|
|
|
|
|
|
1 |
2 |
3 |
4 |
|
5 |
|
|
|
|
|
|
|
|
Q, м2/ч |
160 |
460 |
400 |
|
540 |
|
Таблица 5
Затраты времени на дополнительные операции
Характер работы |
tk, мин |
1 |
2 |
|
0,6-0,8 |
Отделка каркасов стульев, кресел, |
|
брусков, ящиков |
|
|
0,15-0,3 |
То же при их механическом переме- |
|
щении |
|
|
0,02-0,03 |
Отделка кромок щитов в стопах |
|
|
0,2-0,4 |
Крашение щитов деталей |
|
|
|
При отделке наливом щитовых деталей мебели производительность лакокрасочной машины с ручным обслуживанием:
П = |
tсмzk0 60 |
, шт/см |
(2) |
|
rm |
||||
|
|
|
где r – ритм ручной подачи детали в лаконаливную машину; r=5-8 с, для деталей малого размера (площадью 1 м2); r=10-15 с, для деталей размером более 1 м2; k0=0,85-0,88, для машин с одной лаконаливной головкой;
k0=0,78-0,8, для машин с двумя головками (при нанесении парафиносодержащих лаков и эмалей);
m – количество нанесений материала наливом с обеих сторон. При отделке щитовых деталей наливом в автоматических линиях
производительность:
П = |
Тсмk0 zu |
, шт/см |
(3) |
|
(l + a)m |
||||
|
|
|
где l – длина обрабатываемой детали; а – промежуток между деталями, м.
19
Величина а зависит от скорости подачи линии. Для u=2-4 м/мин а=0,2-0,4 м, для u=5-10 м/мин а=1-1,2 м.
При отделке изделий в собранном виде пневмораспылением или ЭПВН производительность линии:
П = |
Тсмk0u |
, шт/см |
(4) |
|
Lm |
||||
|
|
|
где L - расстояние между подвесками конвейера, м; k0 – 0,65-0,75.
Далее необходимо найти норму времени, затрачиваемую на обработку
изделия (детали): |
|
|
|
|
Н = |
8n |
, ч/изд |
(5) |
|
П |
||||
|
|
|
где n - количество деталей в изделии (изделий); П - производительность оборудования, шт/см. Количество единиц отделочного оборудования:
m = |
|
QгодН |
, шт |
(6) |
|
|
|||
|
|
Тэф |
|
|
где Qгод - годовая программа выпуска изделий, шт/год; |
|
|||
Тэф - эффективный фонд расчета оборудования, ч. |
|
|||
Тэф |
=Тном ×с×8 ×k рем , |
(7) |
где Тном - число рабочих дней в году; с - количество рабочих смен в день; 8 - продолжительность смены, ч;
kрем - коэффициент, учитывающий простои оборудования при ремонте; kрем - 0,9 для автоматических линий или сложных станков;
kрем =0,95-0,97 для более простых станков. |
|
||
Загрузка оборудования вычисляется как: |
|
||
р = |
100mp |
, % |
(8) |
|
|||
|
m |
|
где mp - принятое количество единиц оборудования (округленное в сторону увеличения до целого числа расчетное значение m).
Допустимо значение р до 120 %.
3.6. Расчет расхода сырья и материалов на единицу продукции и производственную программу.
20
Вначале определяется S - площадь отделываемых поверхностей изделия (детали) в м2. Далее расчет ведут по нормативам расхода.
Они зависят от марки и вида лакокрасочного материла, метода нанесения, подложки, категории покрытия, группы сложности отделываемых поверхностей. Если материал (лак, эмаль и т.д.) состоит из нескольких компонентов, вычисляют расход каждого компонента в отдельности. Норма расхода вычисляется по формуле
Qp = g p ×S , кг |
(9) |
где gp - норматив расхода на деталь (изделие), кг/м2; S - площадь детали (изделия), м2.
В сводную ведомость вносят значение суммарных расходов по каждому материалу, затрачиваемых на отделку одного изделия и на заданную годовую программу выпуска изделий. Расчет можно выполнять на компьютере.
После проведения расчетов, при необходимости, производится корректировка производственной программы, предусмотренной заданием на проектирование. Корректировка производится по согласованию с руководителем дипломного проекта.
Площадь для межоперационного запаса определяют, исходя из производительности оборудования, времени хранения и размеров изделий. В частности, при хранении щитовых деталей в стопах на роликовых конвейерах площадь рассчитывают по формуле
S = |
Пτf |
, |
(10) |
|
nk |
||||
|
|
|
где П - цеховая программа, шт/ч; τ - время хранения (4-8 ч);
f - площадь, занимаемая одной деталью, м2; n - количество деталей в стопе (50-75 шт.);
k - коэффициент заполнения площади (0,4-0,5).
Количество межоперационных складов зависит от характера производства и вида применяемого оборудования. В частности, при отделке мебельных щитов деталей межоперационные склады организуют чаще всего перед началом отделки, после нанесения полиэфирных лаков, нитроцеллюлозных лаков.