
2588
.pdf200 г/л сернокислого аммония (NH4)2SO4, 5 г/л уксусно-кислого аммония CH3COONH4, 7 – 10 г/л декстрина C6H6O5. Режим электролиза: кислотность электролита рН = 8,9 – 9; температура t = 20 – 25 оС; катодная плотность тока Dк = 1 – 2 А/дм2. Процесс идет со скоростью наращивания 20 – 50 мкм/ч. Защищаемые детали являются при этом катодами. Аноды применяют растворимые марок Ц0, Ц1, Ц2. Периодически их очищают травлением или стальными щетками от шлама и пассивных пленок.
Контроль покрытия электролитического цинка в производственных условиях включает в себя внешний осмотр нарощенных поверхностей, определение прочности сцепления и толщины цинкового осадка. Внешний осмотр производится визуально при дневном или искусственном освещении (освещенность не менее 300 лк). Качественное цинковое покрытие должно быть светло-серого или серебри- сто-блестящего цвета с однородным оттенком, гладким, без шероховатости, дендритов и "подгара" на кромках. Прочность сцепления оценивается нанесением сетки царапин, изгибом контрольной пластины или легким ударом. Отбраковке подлежат оцинкованные изделия, имеющие непокрытые участки поверхности, шероховатость, дендриты, отслаивание осадка в виде отдельных вздутий (пузырей) или осыпающихся частиц, а также детали с темно-серым, губчатым цинковым осадком. Удаление недоброкачественных покрытий производится химическим травлением в 5 – 10 %-ном растворе серной или соляной кислоты. После удаления недоброкачественных покрытий детали повторно подвергаются цинкованию (см. рис. 27). Пористость цинковых покрытий обычно не контролируется, так как она, учитывая анодный характер защиты цинка, не регламентируется техническими условиями.
Толщина осадка цинка может быть проконтролирована химическими и физическими методами (специальными толщиномерами). Из химических методов наиболее простой – капельный метод. Он позволяет определить толщину цинкового покрытия на каком-либо участке поверхности (местную толщину). Точность его колеблется в пределах30 %. Этот метод основан на растворении покрытия последовательно наносимыми каплями раствора, содержащего 100 г/л кристаллического йода I и 200 г/л йодистого калия KI. Контроль производится следующим образом. На плоскую (ровную) тщательно промытую и высушенную поверхность цинкового покрытия капельницей c внутренним диаметром капилляра 1,8 – 2,0 мм наносят одну каплю рас-
111
твора и выдерживают 60 с. По истечении этого времени каплю удаляют фильтровальной бумагой, участок насухо вытирают и на то же место наносят следующую каплю свежего раствора. Нанесение капель продолжают до тех пор, пока не обнаружится сплошной участок основного металла. Толщину покрытия рассчитывают по формуле
ц = (n – 0,5) к, |
(27) |
где n – число капель раствора, расходуемых для обнажения основного металла; к – толщина покрытия, растворяемого одной каплей раствора в течение заданного времени (прил. 8).
6.3. Повышение антикоррозионных свойств цинковых покрытий
Для повышения антикоррозионных свойств цинковое покрытие в ряде случаев подвергают специальной обработке:
а) пассивированию и осветлению; б) фосфатированию;
в) окраске лаками и эмалями защитного назначения. Пассивирование проводят в растворе хромовой, азотной и сер-
ной кислот следующего состава, г/л:
хромовый ангидрит CrO3……………………………100 – 150; азотная кислота HNO3……………………………….10 – 20; серная кислота H2SO4………………………………..5 – 10.
Продолжительность обработки 20…30 с при t = 18…25 оС. В результате на поверхности цинкового покрытия образуются цветные (хроматные) пленки радужных оттенков. Они имеют пористую структуру и толщину порядка 0,25…0,5 мкм. После тщательной промывки водой и нейтрализации образовавшуюся на цинковом покрытии пассивную пленку осветляют в течение 25…30 с в растворе тринатрийфосфата Na3PO4 * 12H2O (50…60 г/л) при комнатной температуре. Затем детали промывают холодной водой и сушат.
Качество пассивной пленки на цинковых покрытиях определяют визуально. Цвет пленки может изменяться от светло-желтого, зеленоватого до розового и фиолетового. Коричневый цвет свидетельствует о низком ее качестве и на мелких деталях недопустим. Механическую прочность пленки проверяют стиранием ее пальцем с нажимом. Если она стирается, то ее механическая прочность считается недостаточной. Забракованную пассивную пленку удаляют в 3%-ном растворе азотной
112
кислоты HNO3 (время выдержки 2 – 15 с), после чего процесс пассивирования повторяют снова (см. рис. 27).
Фосфатирование цинковых покрытий – это обработка их в растворах фосфорной кислоты. Для этого чаще всего используют раствор следующего состава: окись цинка ZnO – 20…35 г/л; ортофосфорная кислота H3PO4 –20…30 г/л; натрий азотистокислый NaNO2 – 1,5…2,0 г/л. Продолжительность обработки 25…30 мин при температуре 28…30 оС. После фосфатирования покрытие цинка пассивируют в растворе бихромата натрия Na2Cr2O7 * 2H2O (50…80 г/л) при температуре 50…80 оС в течение 2…3 с.
6.4. Технология защитного цинкования
На практике находят применение следующие способы нанесения защитных цинковых покрытий:
-погружение изделий в расплавленный цинк (горячий способ);
-метод термической диффузии;
-металлизация;
-контактный метод осаждения цинка;
-электролитический метод.
Горячий способ цинкования является самым старым и благодаря своей простоте наиболее распространен в промышленности. При данном способе покрываемые изделия погружают в ванну с расплавленным цинком, выдерживают в ней короткий промежуток времени и вынимают с осевшим на них слоем цинка. Этот способ возможен благодаря способности расплавленного цинка равномерно покрывать поверхность детали.
Сущность диффузионного метода заключается в том, что детали, уложенные в соответствующие упаковочные приспособления и пересыпанные порошкообразным цинком, нагревают до температуры, при которой цинк осаждается на поверхности детали и диффундирует в глубину металла.
Металлизацией принято называть процесс получения покрытий распылением расплавленного метала. Этот метод довольно широко применяется для нанесения покрытий цинка, свинца, алюминия, олова, никеля, меди и стали. Метод основан на прилипании расплавленных частиц металла к поверхности детали, наслаивании их на соседние частицы и образовании довольно пористого чешуйчатого покрытия.
113
Контактный способ осаждения цинка осуществляется за счет работы гальванической пары, образующейся при погружении стальных изделий в контакте с алюминием в раствор цинковой соли. Цинк при этом вытесняется алюминием. Но покрытия, получаемые данным способом, отличаются незначительной толщиной и низкими защитными свойствами.
Электролитический метод цинкования является наиболее рациональным, благодаря чемунашел широкое распространение на практике. Содержание операций технологического процесса защитного электролитического цинкования крепежных деталей из аммонийного электролита (с учетом необходимости удаления забракованных покрытий и снятия некачественной пассивной пленки), требования к их выполнению приведены в табл. 7. При цинковании в аммиакатном электролите возможны следующие основныенеполадкиипричиныихвозникновения:
а) сильное газовыделение (недостаток сернокислого цинка в электролите);
б) низкий выход по току при нормальном составе электролита (температура электролита выше 40 °С);
в) покрытие имеет темный цвет, электролит прозрачен, пены нет (в электролите недостаточное содержание декстрина);
г) пригар и губчатые осадки на краях деталей (высокая катодная плотность тока, низкая температура электролита);
д) серые шероховатые осадки при нормальной Dк (недостаточное количество аммония в электролите);
е) темное губчатое покрытие цинка (загрязнение электролита медью и свинцом).
При наращивании цинковых покрытий на детали, имеющие сварные швы, в технологических процессах необходимо предусматривать:
-применение абразивной или гидроабразивной обработки для удаленния поверхности окалины и плотной корки окислов;
-использование во всех операциях процесса щелочных растворов (щелочь, попавшая в поры сварного шва, не воздействует на сталь, но после высыхания на стенках пор остается налет щелочных солей);
-увеличение продолжительности промывочных операций до 3 – 5 мин для более полного удаления остатков электролита из труднодоступных мест;
-форсированный режим сушки (t = 90 – 100 °С; = 1,0 – 1,5 ч), способствующий полному удалению влаги из пор, разрывов осадка и других дефектов.
114

115

116

117

118
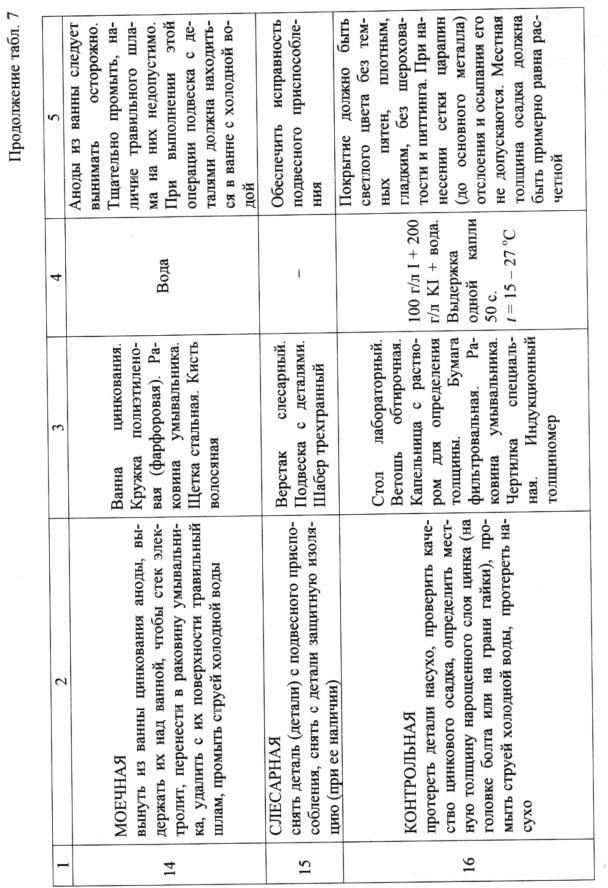
119

120