
2483
.pdf1.4. Последовательность работы над расчетно-пояснительной запиской
Работу над расчетно-пояснительной запиской рекомендуется выполнять в следующей последовательности.
1.Ознакомление с техническим заданием. Подбор литературы, необходимой для проектирования. Анализ исходных данных. При этом обратить внимание на тип производства, материал детали. Ознакомиться с принципами выбора типа производства и материала детали.
2.Разработка технологического маршрута изготовления детали; выбрать оборудование, оснастку и инструмент, пользуясь справочной литературой.
3.Обоснование способа получения заготовки. Для этого необходимо учесть материал детали, тип производства, размеры и конструкцию детали, условия ее эксплуатации.
4.Выполнение необходимых расчетов для разработки чертежа заготовки и его вычерчивание.
5.Ознакомление и анализ видов термической обработки стальных деталей и обоснование выбранных видов термообработки.
6.Выбор технологического оборудования для термической операции, пользуясь литературой и справочными данными.
7.Окончательное оформление технологического процесса термообработки в виде операционной карты (ГОСТ 3.1405 – 86).
8.Окончательное выполнение чертежей, указанных в задании.
9.Окончательное оформление расчетно-пояснительной записки.
10.Подготовка к защите курсового проекта.
2.ОБЩИЕ МЕТОДИЧЕСКИЕ УКАЗАНИЯ К ВЫПОЛНЕНИЮ КУРСОВОЙ РАБОТЫ
2.1. Исходные данные
Исходные данные к курсовой работе указаны в прил. 1 в соответствии с индивидуальным вариантом.
Согласно техническому заданию, материал детали указывается в основной надписи эскиза детали. В прил. 4 приведены рекомендуе-
10
мые марки сталей, используемых для деталей автомобилей, строительных и дорожных машин.
При анализе материала детали, необходимо расшифровать марку и основные физико-механические характеристики материала, выявить основные факторы внешней среды, с которой контактирует деталь (температура, агрессивность окружающей атмосферы, условия смазки и т.д.), характер действующих нагрузок.
Материал должен удовлетворять эксплуатационным и экономическим требованиям [1-9].
Удовлетворение эксплуатационным требованиям
Выбранный материал должен обеспечивать длительную, эффективную работу детали в эксплуатационных условиях, то есть должен обеспечивать необходимую конструкционную прочность, выявленную расчетами инженера-конструктора. Он должен противостоять воздействию внешней окружающей среды (воздуха, воды, масла, кислоты, тепловым воздействиям и т.п.). Все это вместе определяет комплекс необходимых физико-механических свойств, которыми должен обладать материал, назначаемый для изготовления конкретной детали, т.е. предел прочности, предел текучести, показатели пластичности , , коэффициент ударной вязкости, предел выносливости, величина работы распространения трещин, контактная усталостная прочность, сопротивление износу, высоким и низким температурам и т.д.
Технологические требования
С этой точки зрения материал должен удовлетворять требованиям максимальной трудоемкости изготовления детали. В первую очередь он должен обладать хорошей обрабатываемостью режущим инструментом, различными методами обработки давлением. В ряде случаев для улучшения обрабатываемости приходится назначать предварительную термическую обработку заготовок (типа отжига). Выбранный материал должен иметь хорошую свариваемость, что обеспечит получение конструктивно прочной детали или узла при наименьших затратах.
Экономические требования
Материал должен обеспечить изготовление наиболее дешевой конструкции, способной эффективно и длительно работать в различных эксплуатационных условиях. В первую очередь нужно стремится к использованию менее дорогой стали – углеродистой или низколегированной. Применение легированной стали может быть технически и
11
экономически целесообразным и оправданным в том случае, если она дает экономический эффект за счет повышения долговечности деталей, уменьшения массы конструкции, уменьшения расхода запасных частей и, таким образом, экономии металла.
Ориентировочно экономическое обоснование выбора материала можно оценивать по коэффициенту экономической целесообразности:
Кэ=b/a,
где b – относительное повышение предела прочности материала по сравнению со сталью Ст3; а – относительное повышение стоимости данного материала по отношению к стоимости стали Ст3.
При решении вопроса о выборе стали важно установить также вариант предварительной и упрочняющей термообработки или ХТО. Как правило, правильно выбранный способ упрочняющей обработки позволяет повысить коэффициент экономической целесообразности использования выбранного материала в 1,2-1,3 раза.
Тип производства – это классификационная категория производства, выделяемая по признакам широты номенклатуры, регулярности, стабильности и объема выпуска изделий.
Вмашиностроении различают три типа производства: единичное, серийное и массовое.
Вединичном производстве выпускают изделия широкой номенклатуры в небольших количествах или индивидуально. Изготовление однотипных деталей совсем не повторяется или повторяется через определенные промежутки времени. При изготовлении деталей, как правило, используется универсальное оборудование.
Всерийном производстве изготавливают партии деталей, регулярно повторяющиеся через определенные промежутки времени. В зависимости от размера партии различают мелко-, средне- и крупносерийное производство. Используется специализированное оборудование.
Для массового производства характерно изготовление большого количества однотипных деталей на специальном оборудовании.
Тип производства указан в задании согласно рекомендациям производственных предприятий и обусловлен количеством деталей в партии (программой выпуска). Большинство деталей автомобильной
идорожной техники (валы, зубчатые колеса, шестерни, рычаги, оси, стаканы) изготавливаются партиями различных размеров, то есть тип производства – серийный [1, 2].
12
2.2. Введение
Во введении излагаются общие положения о состоянии, перспективах и основных направлениях развития машиностроения, а также о термической обработке материалов, ее целях и месте в технологическом процессе изготовления деталей.
2.3. Выбор заготовки и разработка чертежа заготовки
Правильный выбор вида заготовки оказывает непосредственное влияние на рациональное построение технологического процесса изготовления детали, способствует уменьшению отходов и экономии ресурсов. На выбор метода получения заготовки оказывают влияние назначение детали и технические требования на ее изготовление, материал детали, тип производства, форма поверхности и размеры детали. При выборе заготовки необходимо решить следующие задачи:
-установить способ получения заготовки;
-рассчитать припуски на обработку каждой поверхности;
-рассчитать размеры и назначить допуски на размеры заготовки;
-разработать чертеж заготовки.
Все решения должны учитываться одновременно, т.к. между ними существует тесная связь.
При выборе способа получения заготовки необходимо стремиться к максимальному приближению формы и размеров заготовки к параметрам готовой детали и снижению трудоемкости заготовительных операций.
В машиностроении и ремонтном производстве применяются следующие виды заготовок: сортовой прокат, штамповки, отливки, поковки а также комбинированные (штампосварные, литые в сочетании со сваркой).
Заготовки из сортового проката
Крепежные детали, пальцы, толкатели клапанов, ролики, шарики, мелкие ступенчатые валики и т.п. детали необходимо проектировать в массовом, серийном производстве из прутка соответствующего диаметра.
Штампованные заготовки
Одним из производительных способов получения заготовок является штамповка на горизонтально-ковочных машинах (ГКМ), про-
13

изводительность до 400 поковок в час. Штамповкой на ГКМ получают поковки массой 0,1 – 100 кг с максимальным диаметром 315 мм. Кроме ГКМ в качестве оборудования для штамповки применяют молоты и прессы [1].
Допуски и припуски на поковки регламентируются ГОСТ 7505-89. На ГКМ изготавливаются следующие поковки: зубчатые колеса, шестерни, конические шестерни с валом; цилиндрические шестерни с
валом, кольца, втулки, шестерни с фланцем и т. д. (рис. 5).
Рис. 5. Классификация поковок, получаемых на ГКМ
В том случае, когда поковку невозможно технологически выполнить на ГКМ, необходимо проектировать штамповку на кривошипных прессах. На прессах штампуют детали весом до 200 кг типа плоских поковок, шестерен, крестовин, ступенчатых валов, валовшестерен, поворотных кулаков, рычагов, шатунов, коленчатых валов и т.д. (рис. 6).
Штамповка на кривошипных прессах в 2-3 раза производительнее, а припуски и допуски на 20-35 % ниже по сравнению со штамповкой на молотах, расход металла поковки снижается на 10-15 %. Допуски и припуски заготовок, штампуемых на кривошипных прессах, принимают по ГОСТ 7505-95.
14

Рис. 6. Классификация поковок, штампуемых на молотах и горячештамповочных прессах
На рис. 5, 6 разделение деталей на группы I, II, III, IV произведено с учетом сложности поковок и точности их изготовления. Кроме того, к I группе относятся детали массового производства и высокой точности изготовления; ко II и III группам – детали серийного производства обычной и высокой точности.
Заготовки, полученные литьем (отливки)
При выборе литой заготовки в первую очередь следует определить класс точности в зависимости от типа производства и способа получения отливки.
15
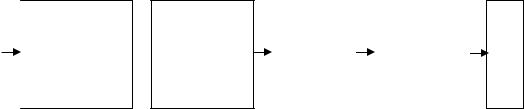
Чугунные детали рекомендуется выполнять литьем в песчаноглинистые формы. Стальные отливки сложной формы весом 50-500 г рекомендуется отливать по выплавляемым моделям. В металлических формах (кокилях) отливаются детали главным образом из алюминия массой от 5 г до 500 кг. Литье в металлических формах под давлением производится для цинковых, алюминиевых, магниевых и латунных сплавов. Под давлением отливают блоки цилиндров, поршни, корпусы коробок передач, втулки, кольца и др.
В данном курсовом проекте заготовки для автомобильных деталей серийного производства рекомендуется выполнять штамповкой. Методика проектирования и разработки чертежа штампованной заготовки представлена в [10].
2.4. Разработка технологического маршрута изготовления детали
Основной задачей этого этапа работы является составление общего плана (маршрута) получения детали, начиная с заготовительной операции и до окончательного получения детали с заданными размерами и техническими параметрами. Маршрут обработки можно представить в виде следующей общей схемы:
Загото- |
|
Предвари- |
ви- |
|
тельная |
тельная |
|
тер- |
опера- |
|
мическая |
ция |
|
обработка |
Черновая механиче- ская обра-
ботка
Окон- |
|
Чистовая |
чат. |
|
механич- |
термо- |
|
еская об- |
об- |
|
работка |
работка |
|
|
Контроль
В данной курсовой работе технологический маршрут изготовления детали необходимо представить в виде табл. 1.
Таблица 1. Технологический маршрут изготовления детали
№ |
Операция |
Цех (участок) |
Оборудование |
Инстру- |
п/п |
|
|
|
мент |
1 |
Заготовительная |
Заготовительный |
Пресс-ножницы |
Нож |
2 |
Изготовление заго- |
|
|
|
|
товки (ковка) |
Кузнечный |
Ковочный молот |
|
… |
|
|
|
|
N |
Контроль |
|
|
|
|
|
16 |
|
|
2.5. Разработка технологического процесса термической обработки
В рамках курсовой работы по дисциплинам «Материаловедение», «Материаловедение. ТКМ», наиболее важным является этап по разработке операций термической обработки детали с выбором необходимого оборудования, оснастки и инструмента.
Технологический процесс – это совокупность последовательных действий по изменению физико-механического состояния предметов труда с целью придания необходимых технических характеристик.
Разработка технологического процесса термообработки начинается с изучения технических условий на изделие. Обычно в технических условиях указывается твердость поверхности изделия, толщина слоя после термической обработки, величина допустимой деформации и другие показатели. После изучения технических условий выбирают основные операции термической обработки, тип оборудования, инструмент и т.д.
Технологический процесс термической обработки деталей включает в себя подготовительные, основные, отделочные и контрольные операции [1-3].
Подготовительные операции включают в себя комплекс мероприятий, направленных на предохранение изделий от образования трещин и других видов дефектов, например, обезжиривание деталей перед азотированием, укладку их в поддоны, защиту и изоляцию отдельных мест и т.д.
Основные операции включают в себя нагрев изделий для закалки, нормализации, отжига, отпуска, ХТО и т.д., выдержки и охлаждения. Выбор вида термической обработки обусловливается техническими требованиями к поверхностям деталей по физикомеханическим свойствам.
Отделочные операции состоят из очистки поверхности деталей, рихтовки и правки после коробления и т.д.
Контрольные операции являются заключительными в технологическом процессе. В них входят контроль твердости, толщины слоя после ХТО и закалки токами высокой частоты (ТВЧ) и т.п. Контроль осуществляется как представителями организации-изготовителя, так и заказчика.
17
Разработка технологических процессов термической обработки в общем случае включает в себя следующие работы: определение последовательности и содержания технологических операций; назначение и расчет режимов обработки; выбор оборудования; нормирование процесса; выбор средств контроля и испытаний; оформление рабочей документации на технологический процесс.
Выбор вида термической обработки
Все виды термической обработки в зависимости от назначения делятся на предварительные и окончательные.
Предварительная термообработка проводится для улучшения обрабатываемости материала режущим инструментом, повышения его пластичности, снятия внутренних напряжений и улучшения структуры.
Предварительной термообработке подвергаются заготовки деталей машин. К видам предварительной термической обработки, как правило, относятся: отжиг, нормализация, улучшение.
Краткая характеристика видов предварительной термической обработки и область их применения представлены в табл. 2.
Окончательная (упрочняющая) термообработка проводится для придания требуемых эксплуатационных характеристик (твердость, износостойкость и т.д.) поверхностям деталей машин.
Все детали, подвергаемые окончательной (упрочняющей) термообработке, можно разделить на две группы. К первой группе относятся детали, работающие на трение, поэтому проведенная термообработка должна обеспечить необходимую твердость, износостойкость поверхностного слоя. Ко второй группе относятся детали, испытывающие при работе значительные нагрузки различного характера: растягивающие, изгибающие, крутящие, контактные.
Вдеталях, испытывающих в процессе эксплуатации растягивающие и сжимающие нагрузки, напряжения по сечению распределены более или менее равномерно. Для таких деталей применяют сквозную закалку и отпуск.
Вдеталях, работающих на изгиб, кручение или при высоких контактных нагрузках, сквозное упрочнение сечения не обязательно, но, желательно поверхностное упрочнение при сохранении вязкой сердцевины.
Краткая характеристика видов окончательной термической обработки и область их применения представлены в табл. 3.
18
Таблица 2. Виды предварительной термической обработки
Наименование |
Краткая характеристика и применение |
|
Режим |
|
||||
обработки |
|
|
|
|
|
|
|
|
|
|
|
|
Скорость охла- |
||||
|
Медленное охлаждение нагретой стали |
ждения |
до |
50- |
||||
|
(с печью, в горячей золе, песке, цементе |
100 С/час |
для |
|||||
Отжиг |
и т.п.). В зависимости от температуры |
углеродистых и |
||||||
нагрева подразделяется на полный, не- |
20-60 С/час для |
|||||||
|
||||||||
|
полный, диффузионный и рекристалли- |
легированных |
||||||
|
зационный |
|
|
сталей, |
затем на |
|||
|
|
|
|
воздухе |
|
|
||
|
Выравнивает структуру по всей площади |
|
|
|
|
|||
|
сечения; снижает твердость и облегчает |
Температура на- |
||||||
|
обрабатываемость; снимает |
внутренние |
||||||
Полный отжиг |
напряжения; ликвидирует перегрев, из- |
грева на 30-50 С |
||||||
|
мельчая структуру. Применяется для по- |
выше АС3 |
|
|||||
|
ковок и отливок только из доэвтектоид- |
|
|
|
|
|||
|
ных сталей |
|
|
|
|
|
|
|
|
Обеспечивает |
получение |
зернистого |
Температура на- |
||||
Неполный отжиг |
перлита, обладающего лучшей обраба- |
|||||||
(сфероидизация) |
тываемостью, чем пластинчатый перлит. |
грева на 30-40 С |
||||||
|
Применяется только для эвтектоидных и |
выше АС1 |
|
|||||
|
заэвтектоидных сталей |
|
|
|
|
|
||
|
|
|
|
Температура на- |
||||
Диффузионный |
Выравнивает химический состав по все- |
грева |
на |
150- |
||||
отжиг (гомоге- |
му сечению. |
Отливки из легированных |
|
|
|
|
||
низационный) |
доэвтектоидных сталей |
|
200 С выше АС3, |
|||||
|
с |
длительной |
||||||
|
|
|
|
выдержкой |
|
|||
|
Снимает наклеп, увеличивая пластич- |
Температура на- |
||||||
Рекристаллиза- |
ность и уменьшая твердость, улучшает |
|||||||
обрабатываемость. Все стали после хо- |
грева на 20-50 С |
|||||||
ционный отжиг |
||||||||
|
лодной штамповки либо грубой механи- |
ниже АС1 |
|
|||||
|
ческой обработки |
|
|
|
|
|
||
|
Выравнивает и измельчает структуру; |
Нагрев |
на |
30- |
||||
|
улучшает механические свойства стали; |
80 С |
выше |
АС3 |
||||
Нормализация |
разрушает карбидную сетку у заэвтекто- |
|||||||
идных сталей. Применяется после горя- |
(Аст), охлажде- |
|||||||
|
чей или грубой механической обработки |
ние |
на |
спокой- |
||||
|
ном воздухе |
|
||||||
|
стали, перед цементацией и после нее |
|
||||||
|
|
|
|
|
Рекомендуемый вид окончательной термообработки для различных деталей автомобилей и дорожных машин представлен соответственно в прил. 5.
19