
- •3. Посадки
- •3.1. Посадки с зазором
- •3.2. Посадки с натягом
- •3.3. Переходные посадки
- •6. Система допусков и посадок для подшипников качения
- •7. Задание на самостоятельную работу
- •7.1. Порядок выполнения работы
- •7.2. Пример выполнения работы
- •8. Вопросы для самоконтроля
- •Библиографический список
- •Приложение 1
- •Приложение 2
- •Приложение 3
Министерство образования и науки РФ Федеральное государственное бюджетное образовательное
учреждение высшего профессионального образования «Сибирская государственная автомобильно-дорожная академия (СибАДИ)»
Кафедра «Механика»
ВЗАИМОЗАМЕНЯЕМОСТЬ И СИСТЕМА
ДОПУСКОВ И ПОСАДОК
Учебно-методическое пособие по дисциплине «Детали машин и основы конструирования»
для студентов направления подготовки «Энергетическое машиностроение»
Составитель В.Н. Никитин
Омск
СибАДИ
2014
УДК 621.713 ББК 34.417.2
Рецензент канд. техн. наук, доц. В.И. Лиошенко
Работа одобрена научно-методическим советом направления «Энергетическое машиностроение» в качестве учебно-методического пособия для студентов, обучающихся по профилю «Двигатели внутреннего сгорания».
Взаимозаменяемость и система допусков и посадок : учебно-методическое пособие по дисциплине «Детали машин и основы конструирования» для студентов направления подготовки «Энергетическое машиностроение» / сост. В.Н. Никитин. – Омск : СибАДИ, 2014. – 39 с.
В учебно-методическом пособии приведены основные сведения о взаимозаменяемости деталей и узлов, допусках, предельных отклонениях и посадках. Рассмотрена единая система допусков и посадок (ЕСДП), а также особенности посадок подшипников качения. Подчеркивается связь излагаемого материала с курсовым проектом по дисциплине «Детали машин и основы конструирования». Пособие содержит задание на самостоятельную работу и пример её выполнения, а также вопросы для самоконтроля.
Ил. 18. Библиогр.: 4назв.
© ФГБОУ ВПО «СибАДИ», 2014
1.ПОНЯТИЕ О ВЗАИМОЗАМЕНЯЕМОСТИ
ИЕЁ ВИДАХ
Для проектирования, изготовления и ремонта машин большое техническое и экономическое значение имеет взаимозаменяемость деталей и узлов.
Взаимозаменяемостью называется свойство независимо изготовляемых деталей, узлов и агрегатов машин, позволяющее устанавливать их при сборке или ремонте без дополнительной обработки и выполнять при этом свои функции в соответствии с заданными техническими условиями. Под независимым изготовлением деталей или узлов понимается их изготовление в разное время и в разных местах (цехах, заводах, городах и даже странах). Другими словами, свойство взаимозаменяемости деталей и сборочных единиц позволяет изготавливать детали в одних цехах машиностроительных заводов серийного и массового производства, а собирать их
– в других.
Благодаря принципу взаимозаменяемости ускоряется проектирование машин, обеспечивается обработка деталей высокопроизводительными методами, значительно облегчается и ускоряется сборка, при ремонте машин детали, выбывшие из строя, быстро заменяются запасными и т.д.
Различают полную и ограниченную взаимозаменяемость. Полностью взаимозаменяемыми называются детали и узлы, которые
при сборке могут занимать определённые места в машине без пригонки, т.е. без каких-либо дополнительных операций подбора или регулирования при обеспечении необходимой работоспособности сборочной единицы. При полной взаимозаменяемости упрощается процесс сборки – он сводится к простому соединению деталей рабочими преимущественно невысокой квалификации; появляется возможность точно нормировать процесс сборки во времени, устанавливать необходимый темп работы, что особенно важно при сборке на конвейере. Полная взаимозаменяемость находит наиболее широкое применение.
Ограниченно взаимозаменяемыми называются такие детали и узлы,
при сборке или замене которых требуются дополнительные работы по подбору или регулированию, но без механической обработки.
При применении ограниченной взаимозаменяемости могут применяться компенсаторы, регулирующие положение некоторых частей маши-
~3 ~
ны относительно друг друга. В ряде случаев в сопряжении, где требуется обеспечить, например, очень малый зазор, полную взаимозаменяемость применять технологически нецелесообразно, так как это требует изготавливать детали сопряжения с очень большой точностью, что значительно удорожает производство. В этом случае для получения требуемой точности сборки применяют групповой подбор деталей, так называемую селективную сборку, т.е. переходят к ограниченной взаимозаменяемости. При этом после изготовления сопрягаемых деталей с достаточно большими колебаниями размеров их делят по размеру (сортируют) на несколько групп и собирают между собой, например, валы 1-й группы с втулкой 1-й группы, валы 2-й группы с втулкой 2-й группы и т.д., обеспечивая требуемый по чертежу очень малый зазор в сопряжении, и всё это при значительных колебаниях сопрягаемых размеров каждой из деталей при их изготовлении. Селективную сборку применяют, в частности, в сопряжении наружного и внутреннего кольца подшипников качения с шариками или роликами.
Как правило, ограниченную взаимозаменяемость применяют не по всем, а только по отдельным геометрическим параметрам.
Взаимозаменяемость может быть внешней и внутренней. Для заво- да-получателя важна только внешняя взаимозаменяемость. К примеру, завод по производству двигателей внутреннего сгорания собирает двигатели, получая при этом бензонасос с другого завода. В этом случае для завода по окончательной сборке двигателя важна взаимозаменяемость только по присоединительным размерам бензонасоса (фланцы с отверстиями), чтобы любой насос мог без всякой пригонки быть присоединен к любому двигателю.
Другой характерный пример внешней взаимозаменяемости – подшипники качения. Как известно, эти подшипники изготавливаются на специализированных подшипниковых заводах огромными партиями и поставляются на разные заводы по производству автомобилей, тракторов, самолетов, сельхозмашин и т.п. Для упомянутых заводов-получателей также важна только внешняя взаимозаменяемость, т.е. взаимозаменяемость по наружному и внутреннему диаметрам подшипника, которые определяют характер сопряжения подшипника соответственно с отверстием в корпусе и цапфой вала конкретного узла машины.
~4 ~

Для завода-изготовителя (в нашем примере по изготовлению бензонасосов или подшипников качения) важна как внешняя, так и внутренняя взаимозаменяемость. В подшипнике качения внутреннюю взаимозаменяемость имеют кольца и тела качения.
Взаимозаменяемость обеспечивается за счет строгого соблюдения допусков и посадок.
2.ОСНОВНЫЕ ПОНЯТИЯ И ОПРЕДЕЛЕНИЯ
ОДОПУСКАХ И ПРЕДЕЛЬНЫХ ОТКЛОНЕНИЯХ
Все сопряжения деталей машин делятся на подвижные и неподвижные. На рис. 1 показаны такие сопряжения на примере соединения вала и втулки.
|
|
|
|
|
|
|
|
|
|
|
|
|
|
|
|
|
|
|
|
|
|
|
|
|
|
|
|
|
|
|
|
|
|
|
|
|
|
|
|
|
|
|
|
|
|
|
|
|
|
|
|
|
|
|
|
|
|
|
|
|
|
|
|
|
|
|
|
|
|
|
|
|
|
|
|
|
|
|
|
|
|
|
|
|
|
|
|
|
|
|
|
|
|
|
|
|
|
|
|
|
|
|
|
|
|
|
|
|
|
|
|
|
|
|
|
|
|
|
|
|
|
|
|
|
|
|
|
|
|
|
|
|
|
|
|
|
|
|
|
|
|
|
|
|
|
|
|
|
|
|
|
|
|
|
|
|
|
|
|
|
|
|
|
|
|
|
|
|
|
|
|
|
|
|
|
|
|
|
|
|
|
|
|
|
|
|
|
|
|
|
|
|
|
|
|
|
|
|
|
|
|
|
|
|
|
|
|
|
|
а) |
|
|
|
|
|
|
|
|
|
|
|
|
|
|
|
|
|
|
|
б) |
|
|
|
|
|
Рис. 1. Виды сопряжений вала и втулки
Подвижное соединение (рис.1, а) характеризуется наличием зазора S, когда диаметр отверстия втулки D больше диаметра вала d. Неподвижное сопряжение (рис.1, б) характеризуется наличием натяга N, в этом случае диаметр отверстия втулки меньше диаметра вала и соединить вал и втулку можно или путем запрессовки на прессе, или нагревая втулку.
Сопрягаемая цилиндрическая поверхность вала, показанного на рис. 1, является охватываемой (наружной), а сопрягаемая поверхность отверстия втулки является охватывающей (внутренней). Принято все охватывающие поверхности деталей обозначать термином «отверстие», а все охватываемые поверхности термином «вал». То есть термины «отверстие»
и«вал» относятся не только к цилиндрическим деталям круглого сечения,
~5 ~
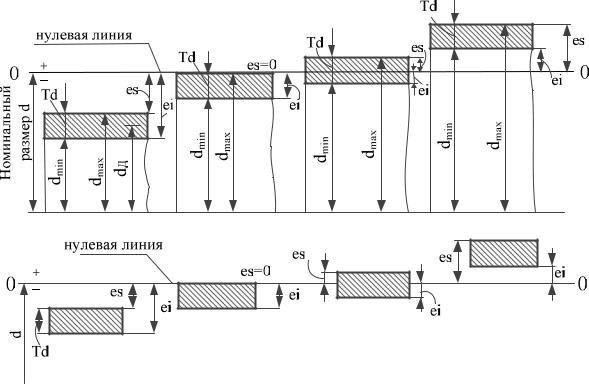
но и к поверхностям деталей другой формы, например ограниченным двумя параллельными плоскостями (паз, шпонка).
В процессе конструирования и изготовления деталей различают номинальный, действительный и предельный размеры (рис. 2 и 3).
Номинальный размер – размер детали, полученный из расчётов на прочность, жёсткость и по другим критериям работоспособности, а также выбранный из конструктивных или технологических соображений. Номинальный размер является одинаковым для сопрягаемых деталей и обозначается D (для отверстий) и d (для вала). Если речь идёт о сопряжении двух деталей, то номинальный размер обычно обозначают как Dном.
Рис. 2. Графическое изображение размеров, предельных отклонений и полей допусков вала
~6 ~
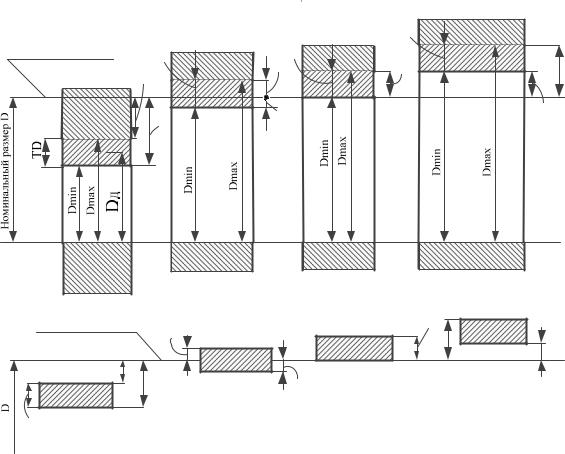
|
нулевая линия |
|
|
TD |
|
|
|
|
TD |
TD |
|
|
ES |
||
|
|
|
ES |
ES |
ES |
|
|
|
|
|
|
|
|||
0 |
+ |
|
|
|
|
|
|
|
EI |
EI |
EI=0 |
EI |
0 |
||
|
|
|
|
|
|
||
|
|
нулевая линия |
|
ES |
ES |
|
|
|
|
|
|
ES |
|
|
|
|
+ |
|
|
|
EI |
|
|
0 |
|
|
|
|
0 |
||
_ |
ES |
EI |
|
EI=0 |
|
||
|
|
|
EI |
|
|
|
|
|
TD |
|
|
|
|
|
|
|
|
|
Рис. 3. Графическое изображение размеров, |
|
|
предельных отклонений и полей допусков отверстия
Действительный размер – размер детали, полученный в результате непосредственного измерения с допустимой погрешностью. Обозначается
Dд и dд.
При изготовлении детали невозможно абсолютно точно выдержать однозначно установленный номинальный размер, так как в процессе производства неизбежны некоторые ошибки, зависящие от станка, режущего и мерительного инструмента, квалификации рабочего. Поэтому для определения возможного диапазона колебаний размеров изготавливаемых деталей устанавливают их предельные размеры – наибольший и наименьший, между которыми должен находиться действительный размер.
Наибольший предельный размер – размер, больше которого не должен быть действительный размер детали. Обозначается Dmax и dmax.
Наименьший предельный размер – размер, меньше которого не должен быть действительный размер детали. Обозначается Dmin и dmin.
~7 ~

Таким образом, сравнение действительного размера с предельными дает возможность судить о годности детали.
Допуск размера T – разность между наибольшим и наименьшим предельными размерами. Обозначается TD (для отверстия) и Td (для вала), т.е.
TD = Dmax |
Dmin; |
(1) |
Td = dmax |
dmin. |
(2) |
Допуск – абсолютная величина без знака.
Допуск определяет допустимое поле рассеивания действительных размеров годных деталей в партии, т.е. заданную точность изготовления. С увеличением допуска качество изделий, как правило, ухудшается, но стоимость изготовления уменьшается. Поэтому конструктор должен назначать допуски с учётом обоих этих факторов.
Для упрощения чертежей, чтобы не указывать в каждом случае два размера, характеризующих годность детали (наибольший и наименьший предельные размеры), введены предельные отклонения от номинального размера − верхнее и нижнее.
Верхнее предельное отклонение – алгебраическая разность между наибольшим предельным и номинальным размерами. Обозначается ES (для отверстия) и es – для вала.
ES = Dmax |
D; |
(3) |
es = dmax |
d. |
(4) |
Из формул (3) и (4) следует что |
|
|
Dmax = D + ES; |
(5) |
|
dmax = d + es, |
(6) |
т.е. наибольший предельный размер отверстия или вала есть сумма номинального размера и верхнего предельного отклонения.
Нижнее предельное отклонение – алгебраическая разность между наименьшим предельным и номинальным размерами. Обозначается EI
(для отверстия) и ei (для вала). |
|
EI = Dmin D; |
(7) |
~8 ~

ei =dmin d. |
(8) |
Из формул (7) и (8) следует, что
Dmin = D EI; |
(9) |
dmin = d + ei, |
(10) |
т.е. наименьший предельный размер отверстия или вала есть сумма номинального размера и нижнего отклонения.
Отклонение является положительным, если предельный размер больше номинального, и отрицательным, если предельный размер меньше номинального. Как видно из рис. 2 и 3, верхнее и нижнее отклонения могут быть оба положительными или отрицательными, одно из них может быть положительным, а другое отрицательным, или одно из них может быть равным нулю.
С введением предельных отклонений допуск можно определять как алгебраическую разность между верхним и нижним отклонениями, т.е.
TD = ES |
EI; |
(11) |
Td = es |
ei. |
(12) |
Для упрощения допуски изображают графически в виде полей допусков. Поле допуска – поле, ограниченное верхним и нижним отклонениями, определяемое величиной допуска и его положением относительно нулевой линии.
Нулевая линия − горизонтальная линия 0-0, соответствующая номинальному размеру, от которой откладывают отклонения размеров при графическом изображении. Положительные отклонения откладывают вверх от нулевой линии, а отрицательные – вниз.
Для наглядности поля допусков схематически показывают в виде прямоугольников без вычерчивания самих деталей, как показано в нижней части рис. 2 и 3.
3. ПОСАДКИ
Сборка деталей в узлы, узлов в агрегаты заключается в основном в надлежащем сопряжении парных поверхностей одинаковой формы, кото-
~9 ~
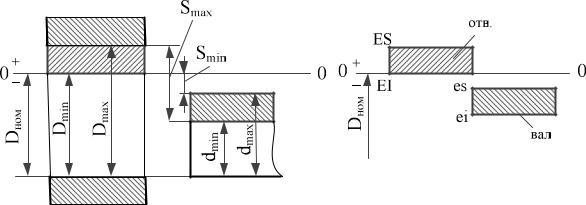
рые либо входят одна в другую, либо примыкают друг другу. Например, сопряжение поршень-цилиндр, в котором наружная цилиндрическая поверхность поршня представляет собой «вал», а внутренняя цилиндрическая поверхность цилиндра – «отверстие».
Характер сопряжения бывает различным в зависимости от функций, которые сопряжение выполняет в узле. Как уже было сказано, могут быть два вида соединений – подвижное и неподвижное. В первом случае во время работы машины детали перемещаются относительно друг друга (например вал и подшипник скольжения). Во втором случае во время работы машины детали относительно друг друга сохраняют неподвижность (например зубчатый венец и ступица червячного колеса).
Посадкой называется характер соединения двух деталей, обеспечивающий за счет разности действительных размеров их относительное перемещение или прочность неподвижного соединения.
Посадки разделяются на три группы: с зазором, натягом и переходные.
3.1. Посадки с зазором
Характерным признаком посадки с зазором является наличие в соединении гарантированного зазора S. Зазором называется положительная разность между размерами отверстия и вала, когда размер отверстия больше размера вала. Схема полей допусков посадки с зазором приведена на рис. 4. Поле допуска отверстия в этой посадке располагается над полем допуска вала.
Рис. 4. Схема полей допусков посадки с зазором
~10 ~

В связи с тем, что действительные размеры сопрягаемых деталей колеблются в пределах заданных допусков, зазоры, которые будут получаться при сборе этих деталей, также будут колебаться от своего наибольшего значения до наименьшего.
Наибольшим зазором Smax называется разность между наибольшим предельным размером отверстия и наименьшим предельным размером вала
Smax = Dmax dmin |
(13) |
или разность между верхним отклонением отверстия и нижним отклонением вала
Smax = ES–ei. |
(14) |
Наименьшим зазором Smin называется разность между наименьшим предельным размером отверстия и наибольшим предельным размером вала
Smin = Dmin dmax |
(15) |
или разность между нижним отклонением отверстия и верхним отклонением вала
Smin = EI es. |
(16) |
Действительный зазор в соединении определяется как разность между действительным размером отверстия и действительным размером вала.
3.2. Посадки с натягом
Характерным признаком посадки с натягом является наличие в соединении гарантированного натяга N. Натягом называется положительная разность между размерами вала и отверстия, когда размер вала больше размера отверстия.
Схема полей допусков посадки с натягом приведена на рис. 5. Поле допуска отверстия в этой посадке расположено под полем допуска вала.
~11 ~
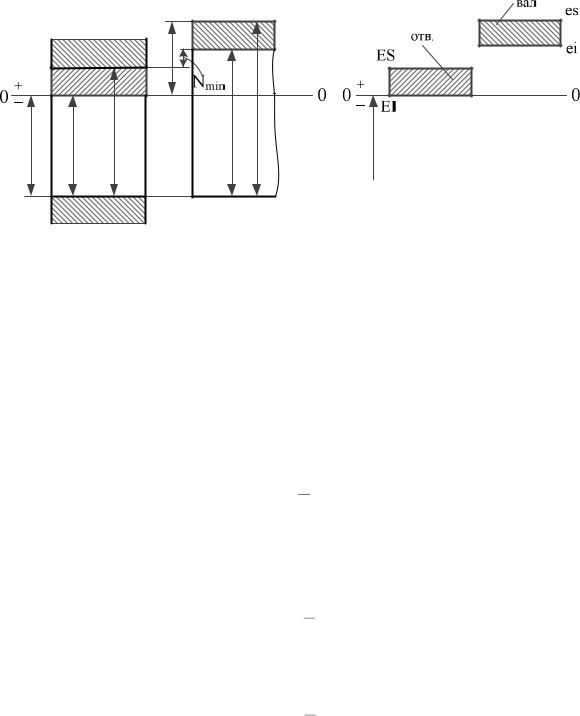
|
|
|
max |
|
|
|
|
|
N |
|
|
ном |
min |
max |
min |
max |
ном |
D |
D |
D |
d |
d |
D |
Рис. 5. Схема полей допусков посадки с натягом
Наибольшим натягом Nmax называется разность между наибольшим предельным размером вала и наименьшим предельным размером отверстия
Nmax = dmaxDmin |
(17) |
или разность между верхним отклонением вала и нижним отклонением отверстия
Nmax = es EI. |
(18) |
Наименьшим натягом Nmin называется разность между наименьшим предельным размером вала и наибольшим предельным размером отверстия.
Nmin = dmin Dmax |
(19) |
или разность между нижним отклонением вала и верхним отклонением отверстия
Nmin = ei ES. |
(20) |
Действительный натяг в соединении определяется как разность между действительным размером вала и действительным размером отверстия.
3.3.Переходные посадки
Впереходных посадках при различных сочетаниях действительных размеров отверстия и вала в пределах допусков возможны как зазоры, так
~12 ~
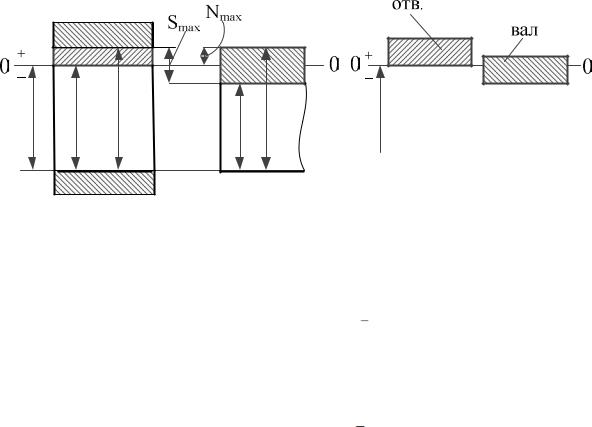
и натяги. Поля допусков отверстия и вала перекрываются частично или полностью (рис. 6).
ном |
min |
max |
min |
max |
D |
D |
D |
d |
d |
ном |
D |
Рис. 6. Схема полей допусков переходной посадки
Наибольший зазор получается при наименьшем предельном размере вала и наибольшем предельном размере отверстия, т.е.
Smax = Dmax dmin . |
(21) |
Наибольший натяг получается при наибольшем предельном размере вала и наименьшем предельном размере отверстия, т.е.
Nmax = dmax Dmin. |
(22) |
Допуск посадки, независимо от её вида, есть сумма допусков отверстия и вала, составляющих соединение.
На практике получение наибольших или наименьших зазоров или натягов в переходных посадках маловероятно, поскольку рассеивание размеров детали при обработке подчиняется закону нормального распределения. Реально имеют место относительно небольшие зазоры или натяги в зависимости от расположения полей допусков, что обеспечивает достаточно хорошее центрирование деталей. Переходные посадки предназначены для неподвижных соединений деталей, подвергающихся при ремонтах или по условиями эксплуатации сборке и разборке. Взаимная неподвижность деталей обеспечивается шпонками, штифтами и винтами.
Все посадки могут быть осуществлены по системе отверстия или по системе вала.
Посадки в системе отверстия – посадки, в которых требуемые зазоры и натяги получаются в сочетании различных полей допусков валов с
~13 ~
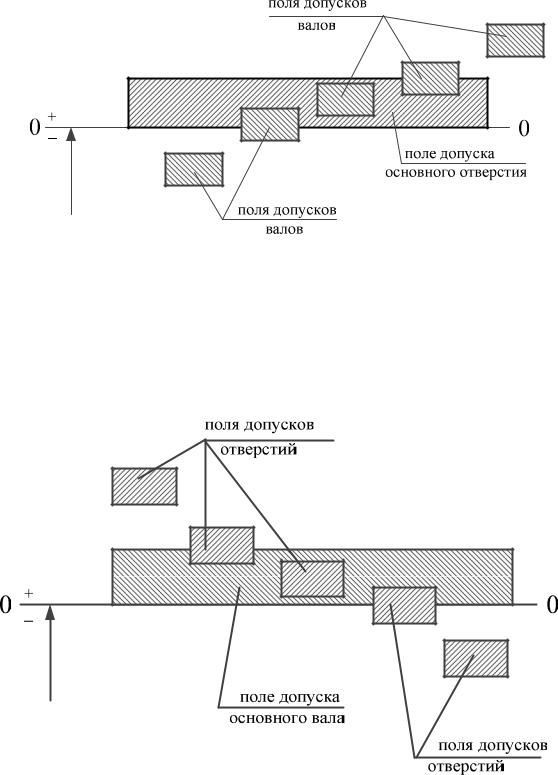
полем допуска основного отверстия, нижнее отклонение которого равно нулю (рис. 7).
Dном
Рис. 7. Схема полей допусков в системе отверстия
Посадки в системе вала − посадки, в которых требуемые зазоры и натяги получаются в сочетании различных полей допусков отверстий с полем допуска основного вала, верхнее отклонение которого равно нулю
(рис. 8).
Dном
Рис. 8. Схема полей допусков в системе вала
~14 ~
Выбор системы отверстия или системы вала для той или иной посадки определяется конструктивными, технологическими и экономическими соображениями. Точные отверстия обрабатываются дорогостоящим режущим инструментом (зенкерами, развертками, протяжками и т.п.). Каждый из них применяется для обработки только одного размера с определенным полем допуска. Валы независимо от их размера обрабатываются одним и тем же резцом или шлифовальным кругом. В системе отверстия различных по предельным размерам отверстий меньше, чем в системе вала, а следовательно, меньше номенклатура режущего инструмента, необходимого для обработки отверстий. В связи с этим преимущественное распространение получила система отверстия. Уменьшение номенклатуры позволяет увеличить партии изготавливаемого инструмента, применить производительное специализированное оборудование и тем самым увеличить выпуск инструмента с наименьшими затратами.
Однако в некоторых случаях по конструктивным соображениям приходится применять систему вала.
На рис. 9 показан узел двигателя внутреннего сгорания, состояний из поршня, шатуна и пальца, причем сопряжение пальца с шатуном должно осуществляться по посадке с зазором, а в сопряжении с поршнем – по посадке с натягом. Из схем полей допусков видно, что при применении системы отверстия палец должен иметь ступенчатую форму, что нерационально как с технологической, так и с конструктивной точек зрения. При применении системы вала палец будет гладким, а различные посадки будут обеспечены за счет изменения предельных размеров отверстия в поршне и шатуне.
При монтаже подшипников качения применяются одновременно обе системы. Как известно, подшипники качения стандартизованы и поля допусков их посадочных поверхностей (отверстия внутреннего кольца и внешней поверхности наружного кольца) заложены в стандарте. При установке подшипников в узлы самых разнообразных машин различные посадки в соединении внутреннего кольца с валом осуществляются путём изменения предельных размеров валов, т.е. по системе отверстия. В соединении наружного кольца с корпусом различные посадки осуществляются путём изменения предельных размеров отверстий в корпусе, т.е. по системе вала.
~15 ~
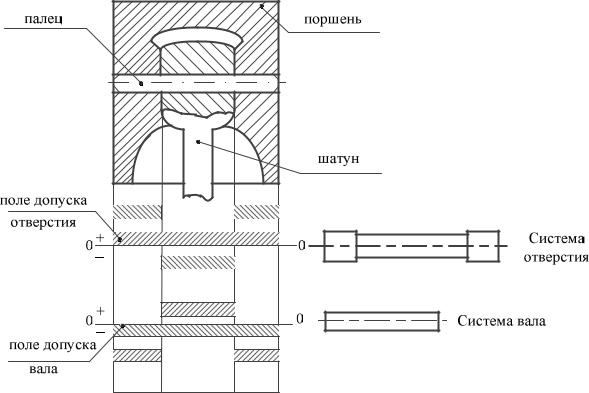
Рис. 9. Узел поршень-шатун-палец ДВС |
4. ЕДИНАЯ СИСТЕМА ДОПУСКОВ И ПОСАДОК (ЕСДП) ДЛЯ ГЛАДКИХ ЦИЛИНДРИЧЕСКИХ СОЕДИНЕНИЙ
ИСОЕДИНЕНИЙ
СПЛОСКИМИ ПАРАЛЛЕЛЬНЫМИ ПЛОСКОСТЯМИ
ЕСДП разработана на базе Международной организации по стандартизации ИСО (ISO – сокращение от английского названия организации
«International Organization for Standartization») и основывается на двух стандартах: ГОСТ 25346-89. Основные нормы взаимозаменяемости. Единая система допусков и посадок. Общие положения, ряды допусков и основных отклонений и ГОСТ 25347-89. Основные нормы взаимозаменяемости. Единая система допусков и посадок. Поля допусков и рекомендуемые посадки.
Система предназначена для выбора минимально необходимых, но достаточных для практики вариантов допусков и посадок типовых со-
~16 ~
единений деталей машин с различной точностью, даёт возможность стандартизировать режущие и мерительные инструменты, облегчает конструирование, производство и достижение взаимозаменяемости изделий и их частей, а также обуславливает повышение их качества.
Разные детали машин в зависимости от назначения и условий работы требуют разной точности изготовления. В ЕСДП предусмотрено несколько рядов точности, называемых квалитетами.
Квалитет – совокупность допусков, рассматриваемые как соответствующие одному уровню точности для всех номинальных размеров. Для номинальных размеров от 1 до 500 мм установлено 20 квалитетов: 01; 0; 1; 2; 3; 4; ..; 16; 17; 18. Допуски в каждом квалитете обозначаются двумя буквами латинского алфавита (IT) с добавлением номера квалитета. Например, IT6 означает допуск по 6-му квалитету, IT10 – допуск по 10-му квалитету. Квалитет определяет величину допуска – с возрастанием номера квалитета допуск увеличивается, т.е. точность убывает и наоборот.
Наиболее широко во всех отраслях машиностроения для ответственных сопряжений применяются 6-й и 7-й квалитеты, в случае относительно больших зазоров и натягов – 8...10-й квалитеты, 11-й 12-й квалитеты используются для грубых соединений. Остальные квалитеты (чаще всего 14-й) используются для несопрягаемых деталей. В таких случаях размеры называют свободными. Квалитеты от 01 до 5 предназначены для допусков средств измерения, в частности для калибров.
Для упрощения построения системы допусков и посадок весь диапазон номинальных размеров разбит на интервалы. Для наиболее широко используемых номинальных размеров от 1 до 500 мм предусмотрено 13 интервалов: от 1 до 3, свыше 3 до 6, свыше 6 до 10,…, свыше 400 до 500 мм. Для всех размеров, объединённых в один интервал, например для размеров свыше 6 до 10 мм, значения допусков приняты одинаковыми, поскольку назначать допуск для каждого номинального размера нецелесообразно − таблицы допусков в этом случае получились бы громоздкими, а сами допуски для смежных размеров отличались бы одним от другого незначительно.
Для образования посадок с различными зазорами и натягами предусмотрены 27 основных отклонений отверстий и валов (рис. 10).
~17 ~

Основные отклонения – это одно из двух отклонений (верхнее или нижнее), используемые для определения положения поля допуска относительно нулевой линии. Таким отклонением являются отклонения, ближайшие к нулевой линии. Для всех полей допусков, расположенных ниже нулевой линии, основным является верхнее отклонение (ES или es), а для расположенных над нулевой линией основным является нижнее отклонение (EI или ei). Основные отклонения отверстий обозначают прописными буквами латинского алфавита (A, B, C и т.д.), а для валов
– строчными (a, b, c и т.д.). Основное отверстие, т.е. отверстие в системе отверстия обозначают буквой H, основной вал (вал в системе вала) буквой h.
В системах отверстия и вала отклонения A-H (a-h) предназначены для образования полей допусков в посадках с зазором; отклонения Js-N (js- n) – в переходных посадках, отклонения P-ZC (p-zc) – в посадках с натягом.
Из рис. 10 видно, что каждому основному отклонению соответствует горизонтальная черта, от которой начинается поле допуска, а конец его, т.е. второе предельное отклонение не указано, поскольку оно зависит от того, с каким допуском (квалитетом) будет сочетаться данное основное отклонение. Из рис. 11 видно, что второе отклонение будет равно:
для валов
es = ei + IT |
(23) |
или
ei = es – IT; |
(24) |
для отверстий
ES = EI + IT |
(25) |
или
EI = ES IT. |
(26) |
~18 ~
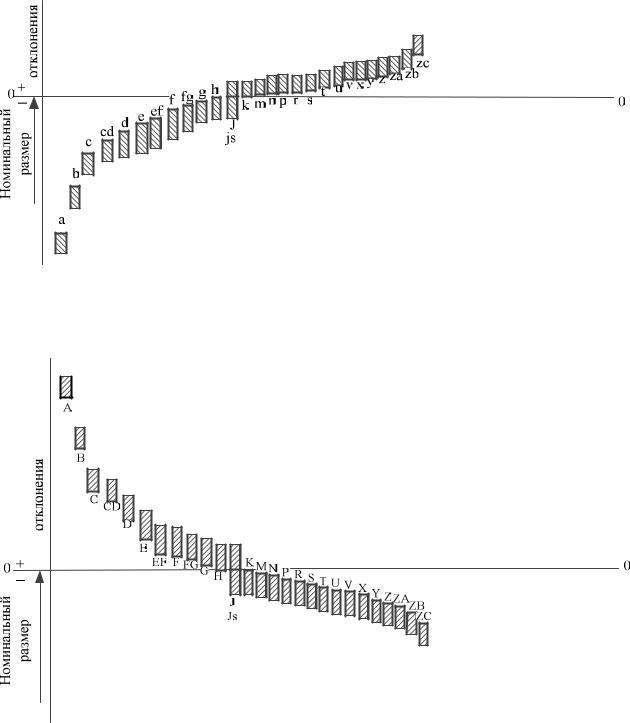
Положение полей допусков валов (основные отклонения)
Положение полей допусков отверстий (основные отклонения)
Рис. 10. Основные отклонения отверстий и валов, принятые в ЕСДП
~19 ~
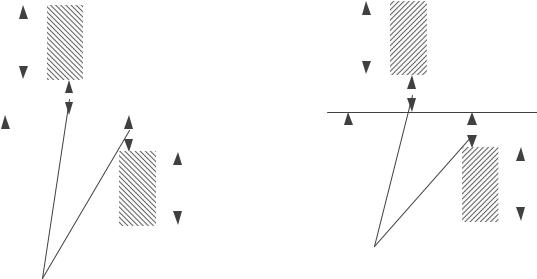
|
|
|
|
|
|
|
ES |
|
|
|
|
|
|
|
es |
|
|
|
|
|
|||||||||||
|
IT |
|
|
|
|
IT |
|
|
|
|
|
|
|
|
|
|
|
|
|||||||||||||
|
|
|
|
|
|
|
|
|
|
|
|
|
|
|
|
|
|
|
|
|
|
|
|
|
|
||||||
|
|
|
|
|
|
|
|
|
|
|
|
|
|
|
|
|
|
|
|
|
|
|
|
|
|||||||
|
|
|
|
|
|
|
|
|
|
|
|
|
|
|
|
|
|
|
|
|
|
|
|
|
|
|
|
|
|
|
|
|
|
|
|
|
|
|
|
|
|
|
|
|
|
|
|
|
|
|
|
|
|
|
|
|
|
|
|
|
|
|
|
|
|
|
|
|
|
|
|
|
|
|
|
|
|
|
|
|
|
|
|
|
|
|
|
|
|
|
|
|
|
|
|
|
|
|
|
|
|
|
|
|
|
|
|
|
|
|
|
|
|
|
|
|
|
|
|
ei |
|
|
|
|
|
||
|
+ |
|
|
|
|
|
EI |
+ |
|
|
|
|
|
|
|
|
|
|
|||||||||||||
|
|
|
|
|
|
|
|
|
|
|
|
|
|
|
|
|
|
|
|||||||||||||
|
|
|
|
|
|
|
|
|
|
|
|
|
|
|
|
|
|
|
|||||||||||||
0 |
|
|
|
|
|
|
|
|
|
|
|
|
|
|
0 |
0 |
_ |
|
|
|
|
|
|
|
|
|
|
|
|
0 |
|
|
|
|
|
|
|
|
|
|
|
|
|
|
|
|
|||||||||||||||||
D |
|
|
|
|
|
|
|
|
ES |
d |
|
|
|
|
|
|
|
|
es |
||||||||||||
|
|
|
|
|
|
|
|
|
|
|
|
|
|
|
|
||||||||||||||||
|
|
|
|
|
|
|
|
|
|
|
|
IT |
|
|
|
|
|
|
|
|
|
|
|
IT |
|||||||
|
|
|
|
|
|
|
|
|
|
|
|
|
|
|
|
|
|
|
|
|
|
|
|||||||||
|
|
|
|
|
|
|
|
|
|
|
|
|
|
|
|
|
|
|
|
|
|
|
|||||||||
|
|
|
|
|
|
|
|
|
|
|
|
|
|
|
|
|
|
|
|
|
|
|
|
|
|||||||
|
|
|
|
|
|
|
|
|
|
|
|
|
|
|
|
|
|
|
|
|
|
|
|
|
|
|
|||||
|
|
|
|
|
|
|
|
|
|
|
|
|
|
|
|
|
|
|
|
|
|
|
|
|
|
|
|
|
|
|
|
|
|
|
|
|
|
|
|
|
|
|
|
|
|
|
|
|
|
|
|
|
|
|
|
|
|
|
|
|
|
||
|
|
|
|
|
|
|
|
|
|
|
|
|
|
|
|
|
|
|
|
|
|
|
Основное |
|
ei |
|
|
||||
|
|
|
|
|
|
|
|
|
|
EI |
|
|
|
|
|
|
|
|
|
||||||||||||
|
а) |
|
|
Основное |
|
|
|
|
|
|
|
отклонение |
|
|
|
|
|
|
|||||||||||||
|
|
|
|
б) |
|
|
|
|
|
||||||||||||||||||||||
|
|
|
|
|
|
отклонение |
|
|
|
|
|
|
|||||||||||||||||||
|
|
|
|
|
|
|
|
|
|
|
|
|
|
|
|
|
|
|
|
|
Рис. 11. Схема к определению второго предельного отклонения: а) для отверстия; б) для вала
Величина основного отклонения не зависит от квалитета, а определяется только номинальным размером.
Основные отклонения подчиняются (за некоторым исключением) общему правилу – основное отклонение отверстия симметрично относительно нулевой линии основному отклонению вала, обозначенному той же буквой, т.е. EI = –es при основных отклонениях от A до H и ES = –ei при основных отклонениях от J до ZC. Это обеспечивает возможность образования посадок в системе вала, аналогичных посадкам в системе отверстия.
Как уже было сказано, поле допуска в ЕСДП образуется сочетанием одного из основных отклонений с допуском по одному из квалитетов. Условно поле допуска обозначается буквой основного отклонения и номером квалитета, например, для вала –h5, d7, d11, а для отверстия – H5, D7, D11.
Значения верхних и нижних предельных отклонений ES, EI, es, ei в соответствии с ГОСТ 25346-89 приведены в таблицах справочников [3; 4]
изадаются в микрометрах (мкм) в зависимости от номинального размера
иобозначения поля допуска, при этом в таблицах верхнее отклонение расположено вверху, а нижнее – под ним.
Так как сочетание 27 основных отклонений с 20 квалитетами даёт большое количество различных по величине и расположению полей допусков, то для практического пользования с целью унификации изделий и
~20 ~

инструмента отобрано оптимальное количество полей, удовлетворяющих требованиям промышлености. Из основного отбора полей допусков выделены поля допусков для предпочтительного применения, которые в таблицах справочников указаны в рамках, например g6 , H7 .
Посадки образуются путём сочетания полей допусков отверстия и вала. Обозначается посадка в виде дроби, при этом числителем является поле допуска отверстия, а знаменателем − поле допуска вала. Например, в системе отверстия H7/g6, H7/p6; в системе вала G7/h6, P7/h6.
Выбор различных посадок в соединениях производится на основе расчета, экспериментальных исследований или ориентируясь на аналогичные конструкции: выбор посадки и квалитета зависит как от точности соответствующего узла механизма или машины, так и от эксплуатационных требований, предъявляемых к соединению. При этом необходимо учитывать конкретные условия эксплуатации, требования к монтажу и демонтажу, технологический процессизготовления сопрягаемых деталей и т.д.
В связи с тем, что число сочетаний полей допусков отверстий и валов может быть достаточно большим, в ЕСДП введен ряд рекомендованных посадок. Из них выделены посадки предпочтительного применения, которые в соответствующих таблицах приведены в рамках.
При применении системы отверстия для номинальных размеров от 1 до 500 мм рекомендуется применять следующие предпочтительные по-
садки: с зазором − ,
,
,
,
,
,
,
,
,
,
; с натягом −
,
,
,
; переходные −
,
,
,
. Рекомендуемые посадки в системе вала:
, |
|
, |
|
, |
|
, |
|
, |
|
, |
|
|
, |
|
, |
|
|
. |
|
Существуют |
различные |
методики |
расчётов, которые определяют |
выбор конкретной посадки в сопряжении двух деталей. Например, посадки с натягом выбираются из условия нераскрытия стыка при действии определённой нагрузки. На основании проведенных расчётов разработаны рекомендации по выбору посадок типовых сопряжений деталей, которыми и руководствуются при конструировании.
При проектировании редуктора, которое является основой выполнения курсового проекта по дисциплине «Детали машин и основы конст-
~21 ~

руирования», студент должен на сборочном чертеже указать посадки основных сопряжений, а на рабочих чертежах – соответствующие предельные отклонения.
В соединении валов с зубчатыми или червячными колесами передача крутящего момента осуществляется обычно посредством шпонок. Чтобы в таком соединении избежать скольжения поверхности вала и отверстия, применение посадок по цилиндрическим поверхностям с зазором недопустимо, а посадок переходных − нежелательно. Поэтому на посадочных поверхностях вала и отверстия следует создавать натяг, гарантирующий нераскрытие стыка. При этом, что немаловажно, обеспечивается точное центрирование колеса на валу.
При передаче крутящего момента шпоночным соединением посадки для колес в редукторе можно принимать по следующим рекомендациям (в
скобках посадки с большим̀ натягом – для колес реверсивных передач):
цилиндрических прямозубых ;
цилиндрических косозубых и червячных (
) ;
конических (
) .
Всоединениях с валами зубчатых и червячных колес, полумуфт, шкивов, звездочек и других деталей (будем называть их втулкой) чаще применяются призматические шпонки, которые передают нагрузку своими боковыми гранями. ГОСТ 23360-78 регламентирует размеры шпонок и сечений пазов, допуски и посадки шпонок в сопряжении с пазом вала и пазом втулки. Указанный стандарт предусматривает поле допуска на ширину шпонки h9, что делает возможным их централизованное изготовление независимо от посадок, т.е. применять систему вала.
ГОСТ 23360-78 устанавливает поля допусков пазов вала и втулки для трех типов шпоночных соединений – свободное, нормальное и плотное. Для свободного соединения установлены поля допусков ширины паза вала H9 и для паза во втулке D10, что даёт посадку с зазором (H9/h9 или D10/h9); для нормального соединения – соответственно N9 и Js9; для плотного соединения – одинаковые поля допусков для паза на валу и паза во втулке P9, т.е. нормальные и плотные соединения имеют переходные посадки (N9/h9, Js9/h9, P9/h9). Однако вследствие нормального закона
~22 ~
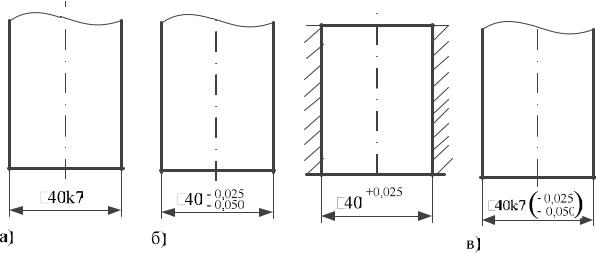
рассеивания размеров в пределах поля допуска при изготовлении шпоночных пазов на валу и втулке для нормального типа соединения возникает большая́ вероятность получения натяга в сопряжении шпонки с валом и зазора в сопряжении со втулкой, что не позволяет шпонке выпадать из паза вала при монтаже и компенсировать неизбежные неточности размеров, формы и расположения пазов и тем самым обеспечить собираемость в процессе сборки.
Для наблюдения за уровнем масла в корпусе редуктора среди других методов применяют контроль с помощью жезловых маслоуказателей (щупов). Если такой маслоуказатель имеет гладкую цилиндрическую шейку для сопряжения с отверстием в корпусе редуктора, то рекомендуется в указанном соединении посадка с зазором H9/d9.
Посадки подшипников качения на вал и в корпус рассмотрены в разделе 6 настоящего пособия.
5.ОБОЗНАЧЕНИЕ ПРЕДЕЛЬНЫХ ОТКЛОНЕНИЙ
ИПОСАДОК НА ЧЕРТЕЖАХ
Предельные отклонения линейных размеров указывают на чертежах деталей условными обозначениями полей допусков (рис. 12, а) или численными значениями предельных отклонений в миллиметрах (рис. 12, б), а также буквенными значениями полей допусков с одновременным указанием справа в скобках числовых значений предельных отклонений
(рис. 12, в)
~23 ~

Рис. 12. Примеры обозначения предельных отклонений
При записи предельных отклонений значения верхних отклонений помещают над нижними. Предельные отклонения, равные нулю, не указывают. При симметричном поле допуска абсолютная величина отклонения указывается в один ряд со знаком ±, при этом высота цифр, определяющих отклонения, должна быть равна высоте шрифта номинального размера, например 60 ± 0,23. Предельные отклонения, указываемые числовым значением, выраженным десятичной дробью, записывают до последней значащей цифры включительно, выравнивая количество знаков в
верхнем и нижнем отклонении добавлением нулей, например 10 ;
35 .
Посадки и предельные отклонения размеров деталей, изображенных на чертеже в сборе, указывают одним из следующих способов:
а) в виде дроби, в числителе которой указывается условное обозначение поля допуска отверстия, а в знаменателе − условное обозначение поля допуска вала (рис. 13, а);
б) в виде дроби, в числителе которой указывается числовое значение предельных отклонений отверстия, а в знаменателе − числовое значение предельных отклонений вала (рис. 13, б)
в) в виде дроби, в числителе которой указывают условное обозначение поля допуска отверстия с указанием справа в скобках его численного значения, а в знаменателе − условное обозначение поля допуска вала с указанием справа его численного значения (рис. 13, в).
|
|
|
|
|
|
|
|
|
50 |
|
|
|
50 |
+0.16 |
|
|
|
|||||||
|
|
|
|
|
|
|
|
|
|
|
|
|
|
|
|
|||||||||
50 |
H11 |
или 50H11/h11 |
+0.16 |
|
|
|
|
|
|
H11( |
) |
|
||||||||||||
|
|
h11 |
|
|
|
|
|
|
|
|
−0.16 |
|
|
|
|
|
h11(−0.16) |
|
||||||
|
|
|
|
|
|
|
|
|
|
|
|
|
|
|
|
|
|
|
|
|
|
|
|
|
|
|
|
|
|
|
|
|
|
|
|
|
|
|
|
|
|
|
|
|
|
|
|
|
|
|
|
|
|
|
|
|
|
|
|
|
|
|
|
|
|
|
|
|
|
|
|
|
|
|
|
|
|
|
|
|
|
|
|
|
|
|
|
|
|
|
|
|
|
|
|
|
|
|
|
|
|
|
|
|
|
|
|
|
|
|
|
|
|
|
|
|
|
|
|
|
|
|
|
|
|
|
|
|
|
|
|
|
|
|
|
|
|
|
|
|
|
|
|
|
|
|
|
|
|
~24 ~