
- •ВВЕДЕНИЕ
- •1. ЗАДАЧИ НЕРАЗРУШАЮЩИХ МЕТОДОВ КОНТРОЛЯ
- •1.1. Цель и задачи технической диагностики
- •1.2. Виды дефектов
- •1.2.1. Классификация дефектов
- •1.2.2. Дефекты металлических заготовок
- •1.3. Виды неразрушающего контроля
- •1.4. Сравнение разрушающих и неразрушающих методов контроля
- •2. ОПТИЧЕСКИЙ КОНТРОЛЬ
- •2.1. Общие вопросы оптического неразрушающего контроля
- •2.2. Источники света и первичные преобразователи оптического излучения
- •2.3. Визуальный и визуально-оптический контроль качества
- •2.4. Приборы ВОК
- •2.5. Оптический контроль, использующий волновую природу света
- •3. КАПИЛЛЯРНЫЙ МЕТОД НЕРАЗРУШАЮЩЕГО КОНТРОЛЯ
- •3.1. Физическая основа метода
- •3.2. Классификация КНК и применяемые материалы
- •3.3. Технология капиллярного контроля
- •4. АКУСТИЧЕСКИЕ МЕТОДЫ КОНТРОЛЯ
- •4.1. Основные понятия волнового процесса
- •4.2. Излучение и прием акустических волн
- •4.3. Активные методы акустической дефектоскопии
- •4.4. Метод акустической эмиссии
- •4.5. Применение акустических методов в дефектоскопии
- •5. МАГНИТНЫЙ НЕРАЗРУШАЮЩИЙ КОНТРОЛЬ
- •5.1. Область применения и классификация
- •5.2. Способы намагничивания изделий
- •5.3. Способы регистрации дефектов при МНК
- •5.4. Магнитопорошковый метод неразрушающего контроля
- •5.5. Магнитографический метод контроля
- •5.6. Магнитные преобразователи
- •5.7. Размагничивание изделий
- •5.8. Дефектоскопия стальных канатов
- •6. ВИХРЕТОКОВЫЙ, ЭЛЕКТРИЧЕСКИЙ И ТЕПЛОВОЙ ВИДЫ КОНТРОЛЯ
- •6.1. Вихретоковый вид контроля
- •6.2. Электрический вид контроля
- •6.3. Тепловой вид контроля
- •7. ТЕЧЕИСКАНИЕ
- •7.1. Термины и определения течеискания, количественная оценка течей
- •7.2. Способы контроля и средства течеискания
- •7.3. Масс-спектрометрический метод
- •7.4. Галогенный и катарометрический методы
- •7.5. Жидкостные методы течеискания
- •7.6. Акустический метод
- •Библиографический список
Ресурс – наработка оборудования от начала эксплуатации или ее возобновления после капитального ремонта до наступления предельного состояния.
Из-за большого числа конструктивных, технологических и эксплуатационных факторов, влияющих на надежность, точно ее рассчитать или предсказать нельзя. Надежность можно оценить только приближенно путем расчета с использованием теории вероятностей и математической статистики или специально организованных испытаний, а также сбора эксплуатационных данных об отказах [1].
Для оценки фактического технического состояния и контроля надежности оборудования (его основных узлов) производится анализ данных по временным показателям надежности оборудования – ресурсу, сроку службы, наработке (суммарной – с начала эксплуатации, с момента проведения последнего капитального ремонта).
На основе анализа количественных показателей надежности принимается решение о необходимости проведения диагностики оборудования, его ремонта или замены. Уровень количественных оценок различается в зависимости от типа оборудования. Так, для магистральных насосно-перекачивающих станций при снижении величины средней наработки на отказ на 10%, вероятности безотказной работы на 3% оборудование, независимо от выработки назначенного ресурса, подлежит техническому освидетельствованию. Снижение коэффициента технического использования оборудования на 3–5% свидетельствует о необходимости проведения экономической оценки целесообразности его дальнейшей эксплуатации.
1.2.Виды дефектов
1.2.1.Классификация дефектов
Техническое состояние оборудования определяется числом дефектов и степенью их опасности [3, 4].
Дефектом называют каждое отдельное несоответствие продукции требованиям, установленным нормативной документацией (ГОСТ, ОСТ, ТУ и т.д.). К несоответствиям относятся нарушение сплошности материалов и деталей, неоднородность состава материала: наличие включений, изменение химического состава, наличие других фаз материала, отличных от основной фазы, и др. Дефектами являются также любые отклонения параметров материалов, деталей и
6
изделий от заданных, таких как размеры, качество обработки поверхности, влаго- и теплостойкость и ряд других физических величин.
Дефекты подразделяются на наружные (те, что выявляются глазами) и скрытые (внутренние, подповерхностные, неразличимые глазом).
В зависимости от возможного влияния на служебные свойства детали дефекты могут быть [3]:
критическими (дефекты, при наличии которых использование продукции по назначению невозможно или исключается по соображениям безопасности и надёжности);
значительными (дефекты, существенно влияющие на использование продукции и/или на её долговечность, но не являющиеся критическими);
малозначительными (не оказывают влияния на работоспособность продукции).
По происхождению дефекты изделий подразделяют на произ- водственно-технологические (металлургические, возникающие при отливке и прокатке, технологические, возникающие при изготовлении, сварке, резке, пайке, клепке, склеивании, механической, термической или химической обработке и т.п.); эксплуатационные (возникающие после некоторой наработки изделия в результате усталости материала, коррозии металла, изнашивания трущихся частей, а также неправильной эксплуатации и технического обслуживания) и конструктивные дефекты, являющиеся следствием несовершенства конструкции из-за ошибок конструктора. Такие дефекты обычно проявляются в начальный период работы оборудования – период приработки. Эксплуатационные дефекты возникают после некоторой наработки в результате износа, накопления усталостных и иных повреждений, а также из-за неправильного технического обслуживания и ремонта. Практика показывает, что можно выделить следующие основные причины накопления дефектов и повреждений, приводящих к отказам оборудования по мере его эксплуатации:
сквозные трещины, разрушения и деформации элементов оборудования, возникающие при превышении допускаемых напряжений;
механический износ, обусловленный трением сопрягаемых поверхностей;
7

эрозионно-кавитационные повреждения, вызванные воздействием потока жидкости или газа;
деградация свойств материалов с течением времени и под воздействием эксплуатационных факторов;
коррозия металлов и сплавов, коррозионно-механические повреждения, возникающие под влиянием коррозии, напряжений, трения и т.п.
Сцелью выбора оптимальных методов и параметров контроля производится классификация дефектов по различным признакам: по размерам дефектов, по их количеству и форме, по месту расположения дефектов в контролируемом объекте и т.д.
Размеры дефектов могут изменяться от долей миллиметров до сколь угодно большой величины. Практически размеры дефектов лежат в пределах 0,01 мм …. 1 см.
В ультразвуковой дефектоскопии, например, величина влияет на выбор рабочей частоты [3, 8].
При количественной классификации дефектов различают три случая (рис. 1.1): а – одиночные дефекты, б – групповые (множественные) дефекты, в – сплошные дефекты (обычно в виде газовых пузырей и шлаковых включений в металлах).
а б в
Рис. 1.1. Количественная классификация дефектов: а – одиночные; б – групповые; в – сплошные
По форме дефекты бывают объемные и плоскостные. Объемные проявляются в виде изменения (искажения) начальной формы или размеров объекта, плоскостные – в виде трещин или полос скольжения.
При классификации дефектов по форме различают три основных случая (рис. 1.2): а – дефекты правильной формы, овальные, близкие к цилиндрической или сферической форме, без острых краёв; б – дефекты чечевицеобразной формы, с острыми краями; в – дефекты произвольной, неопределённой формы, с острыми краями – трещины, разрывы, посторонние включения.
8
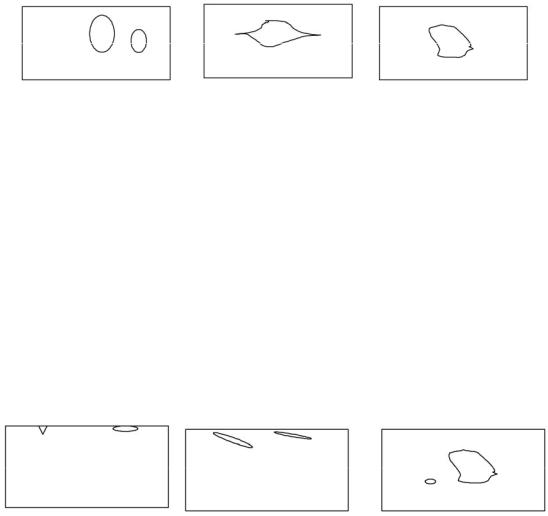
Форма дефекта определяет его опасность с точки зрения разрушения конструкции. Дефекты правильной формы, рис. 1.2, а, без острых краёв, наименее опасны, т.к. вокруг них не происходит концентрации напряжений. Дефекты с острыми краями, как на рис. 1.2, б и в, являются концентраторами напряжений. Эти дефекты увеличиваются в процессе эксплуатации изделия по линиям концентрации механических напряжений, что, в свою очередь, приводит к разрушению изделия.
а б в
Рис. 1.2. Классификация дефектов по форме: а – правильная форма; б – чечевицеобразная форма с острыми краями; в – произвольная, неопределённая форма с острыми краями
При классификации дефектов по положению различают четыре случая (рис. 1.3): а – поверхностные дефекты, расположенные на поверхности материала, полуфабриката или изделия, – это трещины, вмятины, посторонние включения; б – подповерхностные дефекты – это дефекты, расположенные под поверхностью контролируемого изделия, но вблизи самой поверхности; в – объёмные дефекты – это дефекты, расположенные внутри изделия. Наличие фосфовидных и нитридных включений и прослоек может привести к образованию дефектов четвертого вида – сквозных.
а б в
Рис. 1.3. Классификация дефектов по положению в контролируемом объекте: а – поверхностные; б – подповерхностные; в – объёмные
По форме поперечного сечения сквозные дефекты бывают круглые (поры, свищи, шлаковые включения) и щелевидные (трещины, непровары, дефекты структуры, несплошности в местах расположения оксидных и других включений и прослоек).
9
По величине эффективного диаметра (для дефектов округлого сечения) или ширине раскрытия (для щелей, трещин) сквозные дефекты подразделяются на обыкновенные (>0,5мм), макрокапиллярные (0,5...2–104 мм) и микрокапиллярные (<2–10~4 мм).
По характеру внутренней поверхности сквозные дефекты подразделяются на гладкие и шероховатые. Относительно гладкой является внутренняя поверхность шлаковых каналов. Внутренняя поверхность трещин, непроваров и вторичных поровых каналов, как правило, шероховатая.
Положение дефекта влияет как на выбор метода контроля, так и на его параметры. Например, при ультразвуковом контроле положение дефекта влияет на выбор типа волн: поверхностные дефекты лучше всего определяются рэлеевскими волнами, подповерхностные– головными волнами, а объёмные – объёмными (продольными) волнами [3].
Опасность влияния дефектов на работоспособность зависит от их вида, типа и количества. Классификация возможных дефектов в изделии позволяет правильно выбрать метод и средства контроля.
При определении степени опасности дефекта учитывают напряженное состояние контролируемого изделия, вид дефекта, его размеры и ориентацию относительно действующих напряжений. Основными факторами, определяющими степень опасности дефекта, являются величина утонения герметичных перегородок и коэффициент концентрации механических напряжений (в трещинах – коэффициент интенсивности напряжений), показывающий, во сколько раз максимальные местные напряжения в зоне дефекта выше, чем в бездефектной зоне. Виды допустимых дефектов и их величины приводятся в нормативной документации на контроль соответствующего изделия. Наиболее опасными являются плоскостные трещиноподобные дефекты, располагающиеся перпендикулярно действующим напряжениям. Основным параметром, характеризующим уровень концентрации напряжений в вершинах трещин, является критический коэффициент интенсивности напряжений [3].
Совокупность свойств, определяющих степень пригодности машины для использования по назначению, называется качеством. Эти свойства характеризуются эксплуатационными показателями (мощность, расход топлива, скорость, производительность и т.д.), экономической эффективностью, технологичностью, показателями эстетики и эргономики, надежностью.
10