
1790
.pdfХлориды обеспечивают высокую гигроскопичность материала, металлический магний окисляется до оксида, оксиды магния и кальция частично гидратируются, частично – превращаются в карбонаты, хлориды растворяются в дождевой воде. После такой выдержки средний химический состав шлаков составляет MgO – 32,1 %, CaO – 2,4 %, SiO2 – 6,7 %, Al2O3 – 13,35 %, Fe2O3 – 1,7 %, SO3 – 0,6 %, поте-
ри при прокаливании – 43,8 %. Оптимальной температурой для обжига шлаков считается 900 – 1000 оС.
3.5.Сырье для жидкости затворения
Вкачестве жидкости затворения можно использовать чистую воду, гидрогель гидроксида магния или кремнезема. Но в большей степени вяжущие свойства магнезиального цемента проявляются при использовании в качестве жидкости затворения концентрированных растворов солей, таких как MgCl2, MgSO4, FeSO4, ZnCl2, Mg(NO3)2, Ca(NO3)2. Практика показывает, что наибольшую прочность удается достичь при использовании хлорида магния. В качестве сырья для производства хлорида магния используют минерал карналлит и рапу (сгущенную морскую или озерную воду). Карналлит MgCl2·KCl·6H2O
–белое кристаллическое вещество, из-за примесей иногда имеет желтый, розовый или серый цвет. Крупнейшие месторождения находятся на Урале (Соликамское) и в Германии (Страсфурское). Карналлит после дробления растворяют в холодной воде, механические примеси отделяют отстаиванием, затем фильтрацией. Фильтрат выпаривают, при этом образуется «искусственный карналлит». В табл. 8 приведены составы природного и искусственного карналлитов.
|
|
|
|
|
Таблица 8 |
Химический состав соликамских карналлитов |
|||||
Вид карналлита |
|
|
Содержание, % |
|
|
|
KCl |
MgCl2 |
NaCl |
H2O |
Нерастворимый |
|
|
|
|
|
остаток |
Природный карналлит |
19,7 |
26,1 |
23,9 |
28,5 |
1,8 |
Искусственный карналлит |
18,5 |
28,7 |
21,3 |
31,5 |
- |
Озерную рапу получают из соленых озер, таких как Сакское, Са- сык-Сивашское, озер Старое и Круглое на Перекопском перешейке в Крыму, озера Эльтон в Волгоградской области, озера Кара-Бугаз на востоке от Каспийского моря. В табл. 9 приводится состав рапы Сакского и Сасык-Сивашского озер.
33
|
|
Химический состав озерной рапы (мг/дм3) |
Таблица 9 |
|||||||
|
|
|
|
|||||||
Озеро |
Удель- |
Br- |
Cl- |
SO42- |
Ca2+ |
Mg2+ |
NaCl |
|
KCl |
Сухой |
|
ный |
|
|
|
|
|
|
|
|
остаток |
|
вес |
|
|
|
|
|
|
|
|
|
|
г/см3 |
|
|
|
|
|
|
|
|
|
Сакское |
1,101 |
0,020 |
6,15 |
1,16 |
0,08 |
0,88 |
7,76 |
|
0,409 |
12,77 |
Сасык- |
1,143 |
0,051 |
3,92 |
1,30 |
0,06 |
0,885 |
12,48 |
|
0.324 |
17,77 |
Сивашское |
|
|
|
|
|
|
|
|
|
|
Для извлечения солей рапу помещают в бассейны, вырытые на берегу. Под действием солнца вода испаряется, концентрация раствора увеличивается. При повышении плотности раствора до 1,06 г/см3 выделяется гидратированный оксид железа, до 1,12 г/см3 – хлорид кальция. Начиная с плотности 1,19 г/см3, выделяется сульфат кальция, а после достижения 1,25 г/см3 – остаток сульфата кальция и 80 % хлорида натрия. При дальнейшем испарении влаги начинается кристаллизация солей магния (хлорида, бромида и сульфата). Отделенный таким образом хлорид магния упаривается в выпарных котлах при температуре до 160 оС. Для удаления примесей (солей железа) и осветления материала в расплав вводится бертолетова соль. Конечный продукт – бишофит, имеет состав 94,5 % MgCl2, 3,5 % суммы хлоридов натрия и калия, до 1 % сульфата магния. Хлорид магния, необходимый для затворения магнезиального цемента, может быть получен и по реакции каустического магнезита с соляной кислотой. Соляную кислоту плотностью 1,086 г/см3 при постоянном перемешивании смешивают с небольшими порциями каустического магнезита. Для получения 1 кг раствора хлорида магния плотностью 1,25 – 1,30 г/см3 расходуется 1 кг соляной кислоты и 0,2 кг каустического магнезита.
Сульфат магния, как указывалось выше, также можно использовать для приготовления жидкости затворения. Эта соль входит в состав минералов кизерита, эпсомита, астраханита, лангбейнита, шенита, полигалита, а также вместе с хлоридом магния – в минерале каинит. В России имеются месторождения эпсомита в окрестностях озера Малое Кардуанское, расположенное восточнее устья Волги и на Северном Кавказе в Кубанской области. Сульфат магния также входит в состав озерной рапы озер Эльтон, малое Кардуанское, Баталапшинское (в районе Черкесска), Яровое (в районе г. Славгорода, Алтайский край). Из озерных месторождений сульфат магния добывается вместе с поваренной солью. При упаривании раствора до плотности 1,28 –
34
1,30 г/см3 из раствора выделяется MgSO4·7H2O с примесью хлорида натрия. Содержание семиводного сульфата составляет от 30 до 95 %. Кроме выпаривания, применяют способ получения сульфата магния, основанный на вымораживании растворов в открытых бассейнах. При температуре -5 оС сульфат магния выделяется в виде игольчатых кристаллов. Раствор сульфата магния может быть получен путем нейтрализации серной кислоты порошком каустического магнезита. В кислотоупорный сосуд сначала наливают необходимое для разбавления серной кислоты до плотности 1,085 – 1,090 г/см3 количество воды, затем небольшими порциями, не допуская сильного разогрева, добавляют серную кислоту. После этого при непрерывном перемешивании вводят порошок каустического магнезита. Этот способ, как и аналогичный способ получения раствора хлорида магния, более дорогостоящий. Некоторые исследователи предлагают в качестве жидкости затворения использовать раствор сульфата железа (II). Основной источник сульфата железа – железный купорос.
3.6. Сырье для заполнителей
Еще одним необходимым компонентом магнезиальных бетонов являются заполнители. В отличие от портландцемента, магнезиальный цемент не создает щелочную среду – растворимость гидроксида магния незначительна, а основные свойства выражены слабо. Органические заполнители не разрушаются в нейтральной среде. Кроме того, магнезиальный цемент препятствует развитию микроорганизмов, способных разрушить заполнитель. Применение растворов хлорида магния, являющихся хорошей огнестойкой пропиткой, делает эти материалы огнестойкими.
По данным А.П. Ваганова [3], количество отходов в процессе переработки древесины составляет 36 %, из них две трети приходится на опилки, стружку и мелкую щепу. Использование этих материалов в качестве заполнителя при производстве магнезиальных бетонов решит проблему загромождения заводских территорий огнеопасными отходами. При использовании опилок в качестве заполнителя, может быть получен строительный материал, превосходящий по своим качествам древесину. Такой материал получил название «ксилолит», что в переводе означает «окаменевшее дерево». Перед использованием опилки просеивают через сито с ячейками 5 мм. Влажность опилок не должна превышать 15 – 20 %.
35

4. ФИЗИКО–ХИМИЧЕСКИЕ СВОЙСТВА ПЛОТНОГО МАГНЕЗИАЛЬНОГО БЕТОНА
Магнезиальный бетон получают, используя в качестве вяжущего каустический магнезит, в качестве наполнителя – песок, жидкости затворения – раствор хлорида магния. По данным Мюллера составлена трехкомпонентная диаграмма каустический магнезит – раствор хлорида магния – песок (рис. 4). Треугольник АВС с изосклерами растяжения от 10 до 60 кг/см2 ограничивает практически используемые составы. Выше линии АС находятся составы слишком жидкой консистенции, ниже линии ВС – жесткие малопластичные составы.
Рис. 4. Трехкомпонентная диаграмма «каустический магнезит – раствор хлорида магния – песок»
36
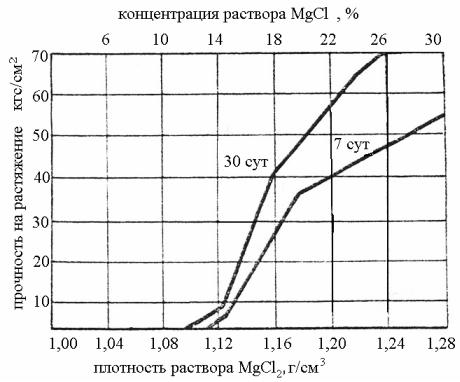
Из диаграммы следует, что с увеличением в составе раствора хлорида магния прочность цементного камня возрастает. Особенно резко в зависимости от количества раствора меняется прочность составов с соотношением оксида магния к песку от 1:1 до 1:3. Для этих систем даже небольшое увеличение количества раствора хлорида магния с 15 до 20 % приводит к повышению механической прочности
с10 до 50 кгс/см2. Оптимальными по прочности получаются составы
ссоотношением оксида магния к песку от 2:1 до 1:2,5 при затворении их 20 – 30 % раствором хлорида магния плотностью 1,15 г/см3.
4.1. Влияние жидкости затворения на свойства магнезиального бетона
А.П. Ваганов [3] приводит результаты исследования влияния плотности раствора хлорида магния на прочность цементного камня (рис. 5). Для растворов с плотностью более 1,12 г/см3 прочность при растяжении возрастает прямо пропорционально как для образцов в возрасте 7, так и 30 суток. Подобные зависимости получены для цементов, в которых вместо песка использовали кремниевую муку, тальк, опилки, асбест.
Рис. 5. Влияние плотности раствора хлорида магния на прочность цементного камня
37

Во всех случаях наблюдалось увеличение механической прочности с увеличением плотности (следовательно, и концентрации) раствора хлорида магния.
С.И. Килессо [6] приводит данные Бейтса и Юнга, согласно которым прочность магнезиального цемента зависит от концентрации раствора хлористого магния. При использовании растворов с концентрацией выше 18 % сопротивление раствора может быть увеличено в 3 и даже в 6 раз. Даже при низком содержании в смеси вяжущего, но при условии правильного соотношения между каустическим магнезитом и раствором хлорида магния можно получить цемент высокой прочности.
Мюллер [3] отметил, что как недостаток раствора хлорида магния, так и его избыток, приводят к падению механической прочности.
Рис. 6. Изменение прочности на |
Рис. 7. Изменение прочности на |
изгиб и растяжение, а также мо- |
изгиб и растяжение, а также мо- |
дуля упругости магнезиального |
дуля упругости в зависимости от |
цемента в зависимости от коли- |
плотности раствора MgCl2 |
чества раствора MgCl2 20 % |
|
38
На рис. 6 показано изменение прочности на изгиб и растяжение, а также модуля упругости магнезиального цемента в зависимости от количества раствора хлорида магния плотностью 1,18 г/см3 в смеси, а на рис. 7 – зависимость этих же свойств от плотности раствора хлорида магния, взятого в количестве 85 см3 на 100 г смеси.
Подавляющее большинство исследований по свойствам магнезиальных бетонов проводились с использованием химически чистого оксида магния, тогда как в производстве обычно используют отход производства огнеупоров – порошкообразный периклаз, который нестабилен по своим свойствам. Исследования, проведенные в 1996 – 1997 годах в лаборатории дорожно-строительных материалов СибАДИ Г.М. Погребинским и А.М. Сизиковым с сотрудниками [15], были направлены на поиск пути снижения негативного влияния нестабильного качества основного сырья – каустического магнезита. В качестве вяжущего использовался отход производства огнеупоров ПМК-75, содержащий 75 % оксида магния, 4,5 % оксида кальция, 3,5 % оксида алюминия и неразложившийся при прокаливании карбонат кальция. В качестве жидкости затворения использовали водные растворы бишофита – плавленого шестиводного хлорида магния, полученного путем сгущения раны залива Кара-Богаз-Гол.
Исследования зависимости физико-механических свойств от расхода и концентрации раствора затворения показали, что увеличение расхода раствора бишофита плотностью 1,2 г/см3 от 0,49 л/кг ПМК-75 до 0,9 л/кг приводит к снижению прочности при сжатии и изгибе до
40 % (табл.10)
Таблица 10
Зависимость прочности плотного магнезиального бетона от расхода раствора бишофита плотностью 1,2 г/см3
Отношение рас- |
Плотность об- |
Прочность образцов, кгс/см2 в возрасте, сут. |
|||
твор бишофита |
разцов в воз- |
|
|
|
|
|
При сжатии |
При изгибе |
|||
/ПМК-75 л/кг |
расте 3 сут. |
|
|||
|
|
|
|
||
|
кг/м3 |
1 |
|
3 |
1 |
0,49 |
1870 |
314 |
|
363 |
112 |
0,63 |
1850 |
264 |
|
290 |
76 |
0,76 |
1800 |
206 |
|
236 |
73 |
0,89 |
1810 |
178 |
|
212 |
120 |
1,00 |
1790 |
194 |
|
241 |
89 |
1,10 |
1700 |
176 |
|
257 |
74 |
39
Дальнейшее увеличение расхода раствора почти не сказывается на прочности при изгибе, а прочность при сжатии вновь начинает увеличиваться. Изменение расхода жидкости заметно сказывается на консистенции цементного теста. При расходе 0,49 л/кг тесто становится мало пластичным, при формовании требуется дополнительное уплотнение. На образцах, изготовленных при расходе раствора бишофита 1,1 л/кг, уже через сутки появляются высолы. На основании этого сделан вывод, что расход раствора затворителя плотностью 1,2 г/см3 с использованием в качестве вяжущего ПМК-75 должен составлять 0,55 – 0,80 л/кг.
Была исследована зависимость прочности магнезиального бетона от плотности раствора бишофита при расходе раствора 0,65 л/кг ПМК-75 (табл.11). Отмечено увеличение прочности на сжатие и изгиб всех образцов с увеличением плотности раствора бишофита. Наиболее быстрый рост прочности наблюдается при плотности раствора бишофита выше 1,17 г/см3. Использование растворов с плотностью выше 1,25 г/см3 ограничивает снижение периода текучего состояния цементного теста, уменьшается время начала схватывания.
Таблица 11
Зависимость прочности плотного магнезиального бетона от плотности раствора бишофита при расходе раствора 0,65 л/кг ПМК-75
№ |
Плотность |
Плотность бетона |
|
Прочность образцов, кгс/см2 |
|
||||||||
п/п |
раствора |
кг/м3 в возрасте, |
|
|
|
в возрасте, сут |
|
|
|
||||
|
бишофита |
|
сут. |
|
При сжатии |
|
При изгибе |
||||||
|
г/см3 |
|
|
|
|
|
|
|
|
|
|
|
|
|
1 |
|
28 |
1 |
|
3 |
|
28 |
|
1 |
|
3 |
|
|
|
|
|
|
|
|
|||||||
|
|
|
|
|
|
|
|
|
|
|
|
|
|
1 |
1,11 |
1800 |
|
1830 |
70 |
|
72 |
|
112 |
|
33 |
|
35 |
2 |
1,14 |
1820 |
|
1910 |
96 |
|
100 |
|
123 |
|
42 |
|
45 |
3 |
1,17 |
1840 |
|
1930 |
120 |
|
170 |
|
198 |
|
56 |
|
60 |
4 |
1,20 |
1820 |
|
1950 |
216 |
|
263 |
|
316 |
|
64 |
|
70 |
5 |
1,22 |
1840 |
|
1970 |
270 |
|
336 |
|
353 |
|
98 |
|
100 |
6 |
1.25 |
1910 |
|
2050 |
305 |
|
398 |
|
421 |
|
96 |
|
102 |
Кроме растворов хлорида магния в литературе есть данные по растворам сульфата магния, используемых в качестве жидкости затворения для магнезиального цемента. С.И. Килессо [6] установил зависимость прочности магнезиального цемента от количественного соотношения магнезита к раствору сульфата магния, аналогичную известной зависимости прочности растворов на портландцементе от во-
40
доцементного соотношения. Исследования, проведенные в СибАДИ, показали, что бетоны, полученные с применением сульфата магния, имеют меньшую прочность, но не настолько, чтобы можно было отказаться от их применения.
4.2. Влияние свойств обожженного магнезита на его активность
Еще академик А.А. Байков [8] установил, что удельный вес обожженного магнезита зависит как от содержания в нем оксида магния, так и от температуры, при которой проводили обжиг сырья. Активность обожженного магнезита тем выше, чем полнее удалена углекислота при обжиге (карбонат магния не обладает вяжущими свойствами и является инертной примесью в магнезиальном цементе), и чем ниже температура обжига. Определено, что физико-химические свойства каустического магнезита находятся в прямой зависимости от его удельного веса, который, в свою очередь, зависит от температуры и продолжительности обжига. Кроме того, активность каустического магнезита зависит от тонкости помола. Содержание в обожженном магнезите оксида магния также влияет на свойства магнезиального цемента, но это не единственный и не главный фактор, определяющий эти свойства. В Работах Бейтса и Юнга [3] приводится диаграмма (рис. 8) изменения прочности магнезиального цемента в зависимости от удельного веса обожженного магнезита.
С.И. Килессо [6] отмечает недопустимость использования показателя объемного веса вместо определения удельного веса и тонкости помола. Объемный вес возрастает, главным образом, не из-за увеличения содержания оксида магния, а из-за грубого помола. Чем крупнее частицы вяжущего, тем больше объемный вес. Но обожженный магнезит грубого помола менее активно вступает во взаимодействие с водой, что снижает прочностные качества цемента. При оценке качества обожженного магнезита обязательным условием является проведение ситового анализа на стандартных ситах с 900 отв./см2 и 4900 отв./см2. Только после оценки тонкости помола можно, с учетом величины удельного веса, делать заключение о качестве магнезита. При тонкости помола аналогичной для портландцемента, для получения качественного магнезиального цемента, удельный вес обожженного магнезита должен находиться в пределах от 3,25 до 3,45 г/см3.
41
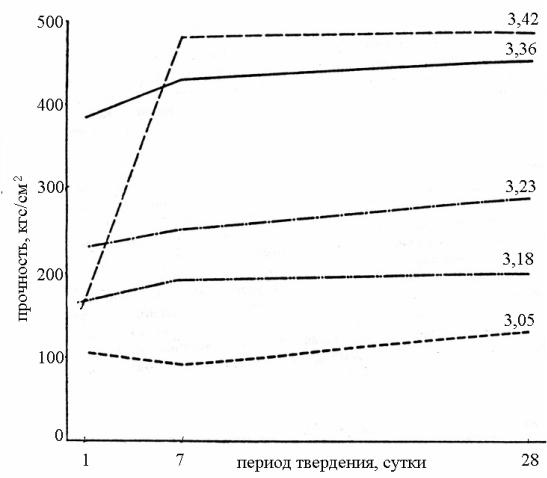
Рис. 8. Диаграмма изменения прочности магнезиального цемента в зависимости от удельного веса обожженного магнезита [17]
Для оценки влияния на прочность цементного камня качества вяжущего в лаборатории ДСМ СибАДИ [15] были проведены исследования зависимости прочности плотного магнезиального бетона от плотности ПМК-75 (табл.12). Расход раствора хлорида магния плотностью 1,2 г/см3 оставался постоянным и составлял 1,0 л/кг ПМК-75. Установлено, что на начальном этапе твердения (в возрасте 1 и 3 суток) прочность образцов при сжатии с возрастанием плотности ПМК-75 несколько снижается. Для образцов в возрасте 7 и 28 суток наблюдается возрастание прочности на сжатие с увеличением плотности вяжущего. Это объясняется диффузионными затруднениями при проникновении воды через малорастворимую поверхностную пленку гидроксида магния к непрореагировавшему оксиду. В возрасте 28 суток гидратация заканчивается и материал набирает прочность. Для прочности при изгибе четкой зависимости от плотности ПМК-75 не выявлено. Для об-
42