
1624
.pdf
электрическая лампочка 1, от которой пучок света через узкое щелевое отверстие диафрагмы 2 и объектив 3 падает на участок контролируемой поверхности 4. Световая полоска поверхности объективом 5 проецирует в фокальную плоскость окуляра 6. Наблюдательный микроскоп служит для рассматривания этого участка и измерения профиля контролируемой поверхности с помощью окуляра-микрометра.
б)
а)
Рис. 3. Двойной микроскоп Линника МИС-11: а) общий вид; б) оптическая схема
При работе с прибором контролируемую деталь кладут на предметный столик. Микроскопы устанавливают предварительно на нужном расстоянии от детали (образца), перемещая кронштейн по колонке. Винтом кремальеры и винтом тонкой наводки перемещают микроскопы, добиваясь четкого изображения световой щели на поверхности детали (образца). Поворотом винтового окулярного микрометра подводят горизонтальную линию перекрестия до касания ее с вершиной выступа неровности (рис. 4). В этом положении делают первый отсчет по окулярному микрометру. Затем смещают ту же линию до касания ее с дном впадины. В этом положении делают
11
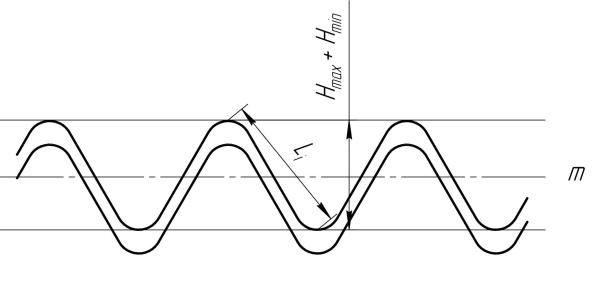
второй отсчет. Разность отсчетов, сделанных по выступу и впадине, дает величину Li.
Рис. 4. Схема замера микронеровностей
Для того чтобы выразить высоту неровности H в микрометрах, определяют цену деления Jµ круговой шкалы винтового окулярного микрометра с помощью объект-микрометра, представляющего собой металлическую пластинку со шкалой с делением через Т = 0,01 мм.
Объект-микрометр кладут на стол прибора. Включают освещение микроскопа. Кронштейн с корпусом микроскопов устанавливают на требуемой высоте. Производя подъем или опускание микроскопов с помощью винта 8 (рис. 3, а), получают изображение световой щели. Наблюдая изображение щели через визуальный микроскоп, добиваются, перемещая объект-микрометр по столику прибора, чтобы шкала попала в изображение щели и штрихи шкалы были бы перпендикулярны к ее изображению.
Отстопоривают винт, крепящий окулярный микрометр, последний поворачивают вокруг оси таким образом, чтобы направление винта окулярного микрометра было параллельно направлению изображения щели. Деления неподвижной шкалы окулярного микрометра при этом параллельны делениям шкалы объекта-микрометра (рис. 5, а).
Затем перекрестие окулярного микрометра совмещают с какимлибо штрихом объекта-микрометра и делают отсчет по барабану окулярного микрометра. Наблюдая в окуляр, переводят перекрестие на другой штрих объекта-микрометра, отстоящий на некоторое число
12
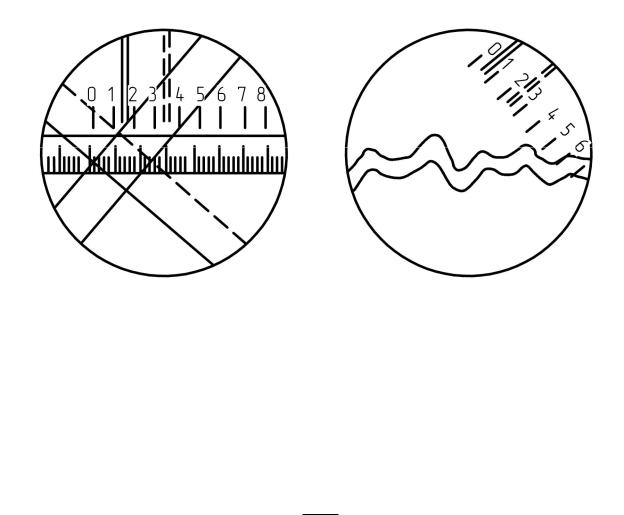
делений (чем больше расстояние между штрихами, тем больше точность определения масштаба), и делают второй отсчет по барабану окулярного микрометра. При подсчете разности следует помнить, что барабан может сделать несколько полных оборотов, и каждый полный его оборот соответствует 100 делениям. Отсчет полных оборотов барабана производят с помощью двойного штриха (см. рис. 5, а), перемещающегося относительно неподвижной шкалы окуляра одновременно с перекрестием.
а) |
б) |
|
|
Рис. 5. Положение перекрестия окулярного микрометра: а) определение цены деления по объекту-микрометру; б) измерение высоты неровностей
Цену деления барабана окулярного микрометра при измерении высоты профиля (горизонтальная линия перекрестия параллельна щели) определяют по формуле
z T J 2 A,
где z − число делений шкалы объекта-микрометра, пройденных перекрестием окуляра; Т − цена деления объекта-микрометра; А − разность отсчетов, полученных при двух совмещениях перекрестия, выраженная в делениях барабана.
Цифра 2 в знаменателе формулы учитывает наклон тубуса под углом 45°, а также то, что при измерении изделия окулярный микрометр поворачивают на 45°.
13
Высота неровности вычисляется по формуле
H J Lср
где Lср – среднее арифметическое значение разности отсчетов по шкале окулярного микрометра.
Используя полученные значения высоты неровностей можно определить значение параметра шероховатости Ra.
ТЕХНОЛОГИЧЕСКИЕ ФАКТОРЫ, ВЛИЯЮЩИЕ НА ШЕРОХОВАТОСТЬ ОБРАБОТАННОЙ ПОВЕРХНОСТИ
Все факторы, воздействующие на качество обрабатываемой поверхности детали, можно разбить на три группы. К первой группе относятся механические свойства материала и его структура. Ко второй группе – факторы, определяющие процесс взаимодействия обрабатываемого материала и режущего инструмента. Сюда входят скорость резания, подача и глубина резания, наличие смазочноохлаждающей жидкости, геометрические параметры режущего инструмента и его микрогеометрия. К третьей группе относятся параметры, влияющие на жесткость системы «станок – приспособление – инструмент – деталь».
В данной лабораторной работе исследуется влияние на качество обрабатываемой поверхности факторов второй группы, а именно: скорости резания, подачи и глубины резания. Качество поверхности будем оценивать параметрами шероховатости.
Для проведения лабораторной работы изготавливаются три образца с различными комбинациями режимов обработки (табл. 2). Для каждого образца фиксируются два режима обработки поверхности, а третий режим меняют 5 раз. В результате можно будет оценить изменения качества поверхности при варьировании значений одного фактора.
14

|
Режимы обработки образцов |
|
Таблица 2 |
|||
|
|
|
||||
|
|
|
|
|
|
|
Номер образца |
D, мм |
Номер пояска |
|
Режим обработки |
||
S, мм/об |
t, мм |
V, м/мин |
n, об/мин |
|||
|
|
1 |
0,206 |
|
|
|
1 |
32 |
2 |
0,320 |
0,5 |
71,30 |
710 |
3 |
0,390 |
|||||
|
|
4 |
0,452 |
|
|
|
|
|
5 |
0,520 |
|
|
|
|
|
1 |
|
0,5 |
|
|
2 |
32 |
2 |
0,32 |
1,0 |
71,30 |
710 |
3 |
1,5 |
|||||
|
|
4 |
|
2,0 |
|
|
|
|
5 |
|
2,5 |
|
|
|
|
1 |
|
|
9,05 |
90 |
3 |
32 |
2 |
0,32 |
0,5 |
28,20 |
250 |
3 |
45,25 |
450 |
||||
|
|
4 |
|
|
71,30 |
710 |
|
|
5 |
|
|
90,50 |
900 |
Замер следует начинать с первого пояска, в каждом пояске производиться три замера под углом 120° в соответствии со схемой
(рис. 6).
Частота вращения детали n связана со скоростью резания через диаметр детали D и является величиной, которая устанавливается на станке и определят режим обработки.
Рис. 6. Схема, иллюстрирующая места (точки) замеров
Данные замеров записывают в графы L1, L2, L3 табл. 3. Режимы обработки образцов приведены в табл. 2.
15
|
|
|
Результаты замеров опытных образцов |
Таблица 3 |
|||||||||
|
|
|
|
||||||||||
|
|
|
|
|
|
|
|
|
|
|
|
|
|
|
|
|
Условия |
|
Значения |
|
|
||||||
|
|
обработки |
Переменный |
|
|
||||||||
Номер |
D, |
замеров из |
Ra, |
Класс |
|||||||||
испытуемых |
фактор |
||||||||||||
образца |
мм |
поверхностей |
резания |
опыта, мкм |
мкм |
шероховатости |
|||||||
|
|
S |
t |
V |
n |
|
L1 |
L2 |
L3 |
Lср |
|
|
|
|
|
1 |
|
|
|
|
|
|
|
|
|
|
|
1 |
32 |
2 |
|
|
|
S |
|
|
|
|
|
|
|
3 |
|
|
|
|
|
|
|
|
|
||||
|
|
4 |
|
|
|
|
|
|
|
|
|
|
|
|
|
5 |
|
|
|
|
|
|
|
|
|
|
|
|
|
|
1 |
|
|
|
|
|
|
|
|
|
|
|
|
|
2 |
|
|
t |
|
|
|
|
|
|
|
2 |
32 |
|
3 |
|
|
|
|
|
|
|
|
||
|
|
|
4 |
|
|
|
|
|
|
|
|
|
|
|
|
|
5 |
|
|
|
|
|
|
|
|
|
|
|
|
|
|
1 |
|
|
|
|
|
|
|
|
|
|
|
|
|
2 |
|
V |
|
|
|
|
|
|
|
3 |
32 |
|
|
3 |
|
|
|
|
|
|
|
||
|
|
|
|
4 |
|
|
|
|
|
|
|
|
|
|
|
|
|
5 |
|
|
|
|
|
|
|
|
После замеров образцов и заполнения табл. 3 в каждой графе подсчитывают среднеарифметическое значение Lср, затем производят обработку результатов измерения.
При определении параметров микронеровностей методом светового свечения, необходимо учитывать особенности обработки результатов измерения высоты микронеровностей данным методом.
Высота микронеровностей находится по формуле
HСР |
|
LСР Е |
0,01 1000 |
LСР Е |
, |
|
5 |
||||
|
2 |
|
|
где Е – коэффициент увеличения (табл. 4).
Если шероховатость поверхности детали определялась при помощи профилографа, то принимаем значение высоты микронеровностей Hср равным Lср.
16
В условиях проведения лабораторной работы будем считать в первом приближении значение параметра Ra равным полученному значению средней высоты микрогеометрических отклонений Hср.
|
|
|
|
Таблица 4 |
|
Средние значения коэффициента увеличения |
|||
|
|
|
|
|
Объектив |
|
Число делений |
Среднее значение |
|
|
окулярного |
|
||
|
барабана |
коэффициента |
||
|
|
микрометра |
||
|
|
|
|
|
Fоб = 25,02 |
|
100 |
588 |
|
|
35 |
206 |
0,171 |
|
|
|
55 |
324 |
|
Fоб = 13,89 |
|
30 |
317,8 |
|
|
36 |
373 |
0,09411 |
|
|
|
30 |
319 |
|
Fоб = 8,16 |
|
20 |
352 |
0,05692 |
|
15 |
263 |
||
|
|
25 |
439 |
|
Fоб = 4,25 |
|
6 |
210 |
0,0287 |
|
9 |
312 |
||
|
|
|
Для многих поверхностей деталей в машиностроении задают не значение параметров шероховатости, а класс шероховатости. Для определения класса шероховатости каждой поверхности необходимо найти соответствие значения параметра шероховатости классу шероховатости по табл. 1.
ПОСТРОЕНИЕ ГРАФИКОВ
На основании данных, занесенных в табл. 3, строятся графики для каждого фактора (рис. 7). По оси ординат откладывается Ra, по оси абсцисс S, t, V. Графическое представление информации позволяет наглядно оценить изменение качества поверхности в результате влияния каждого фактора в отдельности. Кроме того, на графике визуально определяются точки, полученные с грубыми ошибками при измерении, что позволяет исключить их из графика.
17
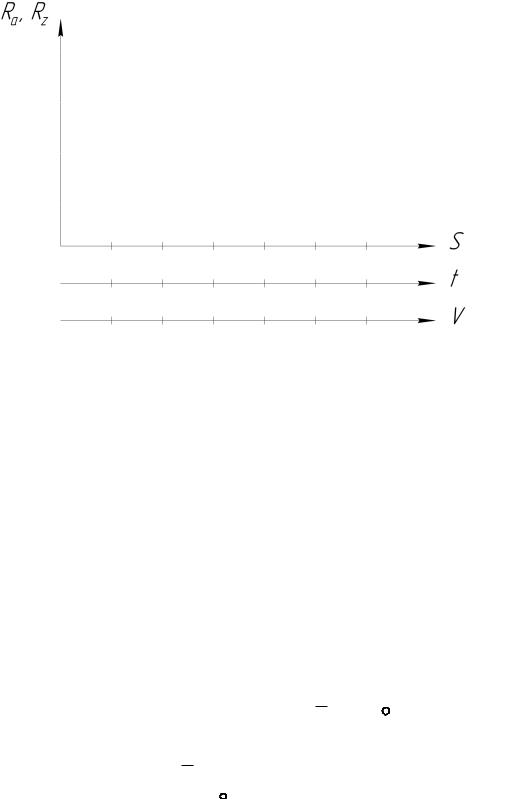
Рис. 7. Система координат для построения зависимостей шероховатости от режимов обработки деталей
График строят в одних координатах. По окончании работы составляется отчет и производится анализ построения кривых. Делается заключение о степени влияния каждого режима обработки на шероховатость обработанной поверхности.
ОБОЗНАЧЕНИЕ ШЕРОХОВАТОСТИ ПОВЕРХНОСТИ НА ЧЕРТЕЖАХ
На чертеже детали обозначается шероховатость только тех поверхностей, нормирование требований к которым является необходимым для обеспечения заданного функционирования детали.
Шероховатость поверхности, обрабатываемой по данному чертежу, обозначают одним из знаков ,
или
.
Знак применяют для поверхности, метод обработки которой не устанавливается; знак
– для поверхности, обрабатываемой со снятием слоя материала; знак
– для поверхности, обрабатываемой без снятия материала. Этим же знаком без указания числового значения обозначают поверхности, не подлежащие обработке по данному чертежу, шероховатость поверхности которых
18

обеспечивается состоянием поставки (например, изготовлением детали из сортамента).
При необходимости знак шероховатости выполняется с полкой, причем обозначения располагаются в последовательности, приведенной на рис. 8
Рис. 8. Условное обозначение шероховатости поверхности
Если шероховатость задаётся двумя предельными значениями параметра, то в обозначении указывают наибольшее и наименьшее значения параметра шероховатости.
ЗАКЛЮЧЕНИЕ ПО РЕЗУЛЬТАТАМ ВЫПОЛНЕННОЙ РАБОТЫ
После выполнения работы составляется отчет, в котором указываются оборудование, схема и метод проведения исследования влияния режимов резания на качество обработки поверхности.
На основании обработанных данных и построенных графиков дается заключение о степени влияния рассмотренных режимов обработки детали при продольном наружном точении на качество обрабатываемой поверхности. Даются параметры обработки поверхности для получения детали с заданным классом шероховатости.
19
КОНТРОЛЬНЫЕ ВОПРОСЫ
1.Какие факторы влияют на шероховатость поверхности при механической обработке?
2.Какие существуют методы определения шероховатости поверхности?
3.Какими приборами можно определить значение параметра шероховатости?
4.Какие параметры характеризуют шероховатость поверхности?
5.Каким образом влияет изменение режимов на шероховатость поверхности?
6Какой из параметров шероховатости (Ra или Rz) имеет большее значение для одной и той же поверхности и почему?
Библиографический список
1.Митрохин Н.Н. Основы технологии производства и ремонта автомобилей. Ч.1. Технология машиностроения: теория, справочные материалы, контрольные задания и примеры решения задач / Н.Н. Митрохин. – М.:МАДИ, 2002. – 203 с.
2.Баженов С. П. Основы эксплуатации и ремонта автомобилей и тракторов [Текст] : учебник / С. П. Баженов, Б. Н. Казьмин, С. В. Носов. − 4-е изд., стер. –
М.: Академия, 2010. − 330 с.
3.ГОСТ 2789-73. Шероховатость поверхности. Параметры и характеристики.
4.Егоров В.А. Оптические и щуповые приборы для измерения шероховатости поверхности / В.А Егоров. – М.: Машиностроение, 1965. – 82 с.
20